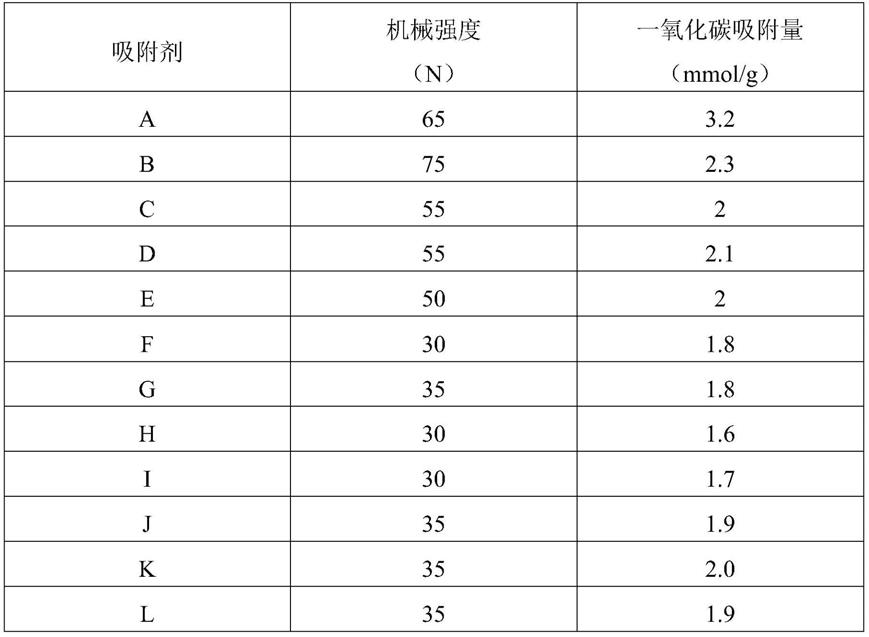
一种用于co变压吸附的吸附剂的制备方法
技术领域
1.本发明涉及化工技术领域,具体涉及一种用于co变压吸附的吸附剂的制备方法。
背景技术:2.在现代工业中,n2、ch4和co是重要的基础化工原料。n2在化工、电子、冶金、饰品、机械等领域早已获得了广泛的应用,现代工业对氮的需求量每年以大于10%的速度增加;ch4除作为合成原料外,当前更多的是作为能源实用,而co是羟基合成有机化学食品的重要原料,还可以生产多种邮寄化学品,如甲酸、草酸、醋酸、甲基甲酰胺dmf、二异氰酸酯tdl等。
3.变压吸附(pressure swing adsorption,psa)是近几十年在工业上新崛起的气体分离技术,其基本原理是利用混合气体组分在固体材料上吸附特性的差异以及吸附量随压力变化而变化的特性,通过周期性的压力变换过程实现气体的分离或提纯。该技术是在上世纪六十年代迅速发展起来的。由于最早的吸附剂吸附能力较低、选择性较差,吸附分离仅用在吸湿干燥、脱色、除臭、饮用水净化上,吸附剂往往是一次性使用,使用时能耗不高,而吸附剂的选择是spa能否实现的关键。
4.cn201410770801.6涉及用于回收co的吸附剂,尤其是涉及一种从工业尾气中回收co的吸附剂及其制备方法和应用,属于化工分离技术领域。以活性炭为载体,负载活性组分和活性助剂,所述活性组分为氯化亚铜,所述活性助剂为fe、co中的一种或两种,加入成型助剂制备而成;制备方法采用浸渍法或者混合成型法;应用于富含co工业尾气的变压吸附提浓co气体,得到浓度大于99%的co产品气,co收率大于90%。
5.cn201210163603.4公开了一种一氧化碳吸附剂,以重量比例为氯化亚铜38~42%、13x分子筛18~23%、氢氧化铝8~10%和凹凸棒石提纯粉28~35%为原料,按以下步骤制得:a、将13x分子筛在200℃烘箱烘烤120分钟~150分钟;b、将四种原料混合后得混料,将混料入捏合机,向捏合机加入混料重量10%的纯净水进行捏合,捏合时间20~25分钟;得捏合物料;c、随即将捏合物料用挤条机加工成ф3mm
×
8mm~ф3mm
×
15mm的条形物品;d、将条形物放入烘箱,在300℃~320℃烘烤180~200分钟取出,待自然冷却后,制成一氧化碳吸附剂。加入了经过粉碎、提纯、超微化与活化处理的200目凹凸棒石提纯粉,从而提高了一氧化碳吸附剂的吸附能力,大幅降低成本,价格为同类产品的2/3。
6.现有技术中均未对载体进行处理,所制得的吸附剂机械强度低,消耗高。
技术实现要素:7.鉴于上述现有技术中存在的问题,本发明的目的在于提供一种从含有一氧化碳的气体混合物中分离一氧化碳的高选择性吸附剂及其制备方法,解决了常规吸附剂机械强度低,co吸附效率不高的问题。与现有技术相比,有益效果是:吸附剂活性组分氯化亚铜稳定性好,不易氧化,吸附剂使用前无需活化;吸附剂吸附容量大,常温即可解析;吸附剂分离系数大,产品co纯度高;制备方法简单,适合大规模工业化应用。
8.本发明一方面提供一种吸附剂的制备方法,包括:
9.a)将载体与模板剂、任选地铝源溶液及任选地磷酸溶液混合,并在混合后进行晶化处理,制得第一改性载体;
10.b)采用有机胺对所述第一改性载体进行气固相处理,制得第二改性载体;
11.c)将所述第二改性载体与铜源混合并成型,制得吸附剂前驱体;以及
12.d)对所述吸附剂前驱体进行焙烧处理,制得所述吸附剂。
13.本申请的发明人经研究发现,在使用模板剂、任选地铝源溶液及任选地磷酸溶液对载体进行改性处理之后,再采用有机胺对所述第一改性载体进行气固相处理,能够显著提高吸附剂的机械强度,并有效提高吸附量,还能够提高载体结晶度,增加载体与金属之间的协同作用。
14.在本发明的一些优选的实施方式中,所述铝源溶液选自硫酸铝,铝酸钠和异丙醇铝中的至少一种。
15.在本发明的一些优选的实施方式中,所述模板剂为氢氧化钠、正丙胺、四丙基溴化铵、四丙基氢氧化铵、四甲基溴化铵、四乙基溴化铵、四丁基溴化铵、四甲基氢氧化铵、四乙基氢氧化铵和四丁基氢氧化铵中的至少一种。
16.在本发明的一些优选的实施方式中,所述铝源溶液的质量浓度为35%-50%,所述磷酸溶液的质量浓度为5%-10%,所述模板剂的质量浓度为1%-10%;优选地,所述载体与所述铝源溶液的质量比为(0-0.1):1,所述载体与所述模板剂的质量比为(0.01-0.1):1;所述载体与所述磷酸溶液的质量比为(0.01-0.2):1。
17.根据本发明,所述载体与所述铝源溶液的质量比为(0.03-0.1):1。
18.在本发明的一些优选的实施方式中,步骤a)中,所述晶化处理的条件包括:晶化温度为100℃-150℃,优选为110℃-130℃;晶化时间为2h-12h。
19.在本发明的一些优选的实施方式中,所述载体选自多孔氧化硅、a型沸石分子筛、x型沸石分子筛、y型沸石分子筛、zsm型沸石分子筛、丝光沸石和磷酸铝分子筛中至少一种。
20.根据本发明,可以在对步骤a)制得的第一改性载体进行冷却、洗涤和干燥处理后再进行步骤b)。
21.在本发明的一些优选的实施方式中,步骤b)中,所述有机胺选自乙胺、正丙胺、正丁胺、乙二胺和己二胺中至少一种。
22.在本发明的一些优选的实施方式中,步骤b)中,将所述第一改性载体置于水中,进行所述气固相处理;优选地,所述第一改性载体与所述水的质量比为(0.01-1):1,优选为(0.01-0.4):1;和/或所述水与所述有机胺的质量比为(0.01-20):1,优选为(0.1-10):1。
23.在本发明的一些优选的实施方式中,步骤b)中,所述气固相处理的条件包括:温度为150℃-200℃,时间为10h-120h。
24.根据本发明,可以在对步骤b)制得的第二改性载体进行水洗和干燥处理后再进行步骤c)。
25.在本发明的一些优选的实施方式中,步骤c)中,所述铜源为氯化亚铜、硝酸铜、氯化铜和乙酸铜中的至少一种;优选地,以所述第二改性载体的质量为计算基准,所述铜源的用量为13wt%-50wt%。
26.根据本发明,在将改性载体和铜源混合并成型时,可以根据需要添加适量的水。水的添加量以便于混合和成型为准。
27.根据本发明,可以在步骤c)制得的吸附剂前驱体静置干燥后再进行步骤d)。
28.在本发明的一些优选的实施方式中,步骤d)中,所述焙烧处理的温度为100℃-400℃,优选为200℃-300℃。
29.根据本发明,所述焙烧处理的时间为2h-24h,优选为3h-12h。
30.根据本发明,可以采用盐酸溶液对步骤d)制得的吸附剂进行浸泡处理,并在浸泡处理之后进行水洗和干燥处理。
31.本发明再一方面提供一种根据上述的制备方法制得的吸附剂。
32.本发明再一方面提供一种上述吸附剂在co的吸附领域中的应用。
33.当将本发明所提供的制备方法制得的吸附剂应用于co的吸附领域时,能够使co的吸附量达到3.2mmol/g以上。并且,本发明所提供的吸附剂的机械强度能够达到65n以上。
具体实施方式
34.以下通过实施例对本发明进行详细说明,但本发明的保护范围并不限于下述说明。
35.在下述实施方式中,采用颗粒强度测试仪测定吸附剂的强度。
36.实施例1
37.称取1gx分子筛,并加入17g质量浓度为40%的铝酸钠溶液,20g质量浓度为6%的四丙基溴化铵溶液,之后在120℃晶化5h,经冷却、水洗和干燥制得第一改性载体。
38.之后,将第一改性载体置于水中,使第一改性载体与水的质量比为3:7,之后加入乙二胺,使水与乙二胺的质量比为5:1。然后在160℃气固相处理15h,经水洗和干燥制得第二改性载体。
39.称取10g第二改性载体与3g氯化亚铜及适量水混合,搅拌均匀后挤条,静置后干燥,制得吸附剂前驱体。
40.将制得的吸附剂前驱体置于马弗炉内,在200℃焙烧5h,之后采用质量分数5%盐酸溶液浸泡,水洗、干燥即得吸附剂a。
41.测试吸附剂a的机械强度和在18℃、一氧化碳压力为760mmhg下的一氧化碳吸附量,结果如表1所示。
42.实施例2
43.称取1gsapo-34分子筛,并加入25g质量浓度为40%的硫酸铝溶液,15g质量浓度为5%的正丙胺溶液和12g质量浓度为5%的磷酸溶液,之后在110℃晶化4h,经冷却、水洗和干燥制得第一改性载体。
44.之后,将第一改性载体置于水中,使第一改性载体与水的质量比为3:7,之后加入正丁胺,使水与乙二胺的质量比为6:1。然后在150℃气固相处理12h,经水洗和干燥制得第二改性载体。
45.称取10g第二改性载体与3g氯化亚铜及适量水混合,搅拌均匀后挤条,静置后干燥,制得吸附剂前驱体。
46.将制得的吸附剂前驱体置于马弗炉内,在200℃焙烧5h,之后采用质量分数5%盐酸溶液浸泡,水洗、干燥即得吸附剂b。
47.测试吸附剂b的机械强度和在18℃、一氧化碳压力为760mmhg下的一氧化碳吸附
量,结果如表1所示。
48.实施例3
49.按照实施例1中的方式制备吸附剂c,不同之处仅在于使用乙酸铝替换实施例1中的铝酸钠。
50.测试吸附剂c的机械强度和在18℃、一氧化碳压力为760mmhg下的一氧化碳吸附量,结果如表1所示。
51.实施例4
52.按照实施例1中的方式制备吸附剂d,不同之处仅在于铝酸钠的用量为30wt%。
53.测试吸附剂d的机械强度和在18℃、一氧化碳压力为760mmhg下的一氧化碳吸附量,结果如表1所示。
54.实施例5
55.按照实施例1中的方式制备吸附剂d,不同之处仅在于铝酸钠的用量为60wt%。
56.测试吸附剂d的机械强度和在18℃、一氧化碳压力为760mmhg下的一氧化碳吸附量,结果如表1所示。
57.实施例6
58.按照实施例1中的方式制备吸附剂e,不同之处仅在于焙烧处理的温度为450℃。
59.测试吸附剂e的机械强度和在18℃、一氧化碳压力为760mmhg下的一氧化碳吸附量,结果如表1所示。
60.对比例1
61.按照实施例1中的方式制备吸附剂f,不同之处仅在于未采用铝源(实施例1中为铝酸钠溶液)和模板剂(实施例1中为四丙基溴化铵溶液)对载体进行处理。
62.测试吸附剂f的机械强度和在18℃、一氧化碳压力为760mmhg下的一氧化碳吸附量,结果如表1所示。
63.对比例2
64.按照实施例1中的方式制备吸附剂g,不同之处仅在于不含有铝酸钠。
65.测试吸附剂g的机械强度和在18℃、一氧化碳压力为760mmhg下的一氧化碳吸附量,结果如表1所示。
66.对比例3
67.按照实施例1中的方式制备吸附剂h,不同之处仅在于不含有四丙基溴化铵。
68.测试吸附剂h的机械强度和在18℃、一氧化碳压力为760mmhg下的一氧化碳吸附量,结果如表1所示。
69.对比例4
70.按照实施例2中的方式制备吸附剂i,不同之处仅在于不含有磷酸。
71.测试吸附剂i的机械强度和在18℃、一氧化碳压力为760mmhg下的一氧化碳吸附量,结果如表1所示。
72.对比例5
73.按照实施例1中的方式制备吸附剂j,不同之处仅在于未进行晶化处理。
74.测试吸附剂j的机械强度和在18℃、一氧化碳压力为760mmhg下的一氧化碳吸附量,结果如表1所示。
75.对比例6
76.按照实施例1中的方式制备吸附剂k,不同之处仅在于未进行气固相处理。
77.测试吸附剂k的机械强度和在18℃、一氧化碳压力为760mmhg下的一氧化碳吸附量,结果如表1所示。
78.对比例7
79.按照实施例1中的方式制备吸附剂l,不同之处仅在于未进行焙烧处理。
80.测试吸附剂l的机械强度和在18℃、一氧化碳压力为760mmhg下的一氧化碳吸附量,结果如表1所示。
81.表1
[0082][0083]
根据上表可知,采用本发明的技术方案所制备的吸附剂具有更高的机械强度和一氧化碳吸附量。
[0084]
应当注意的是,以上所述的实施例仅用于解释本发明,并不构成对本发明的任何限制。通过参照典型实施例对本发明进行了描述,但应当理解为其中所用的词语为描述性和解释性词汇,而不是限定性词汇。可以按规定在本发明权利要求的范围内对本发明作出修改,以及在不背离本发明的范围和精神内对本发明进行修订。尽管其中描述的本发明涉及特定的方法、材料和实施例,但是并不意味着本发明限于其中公开的特定例,相反,本发明可扩展至其他所有具有相同功能的方法和应用。