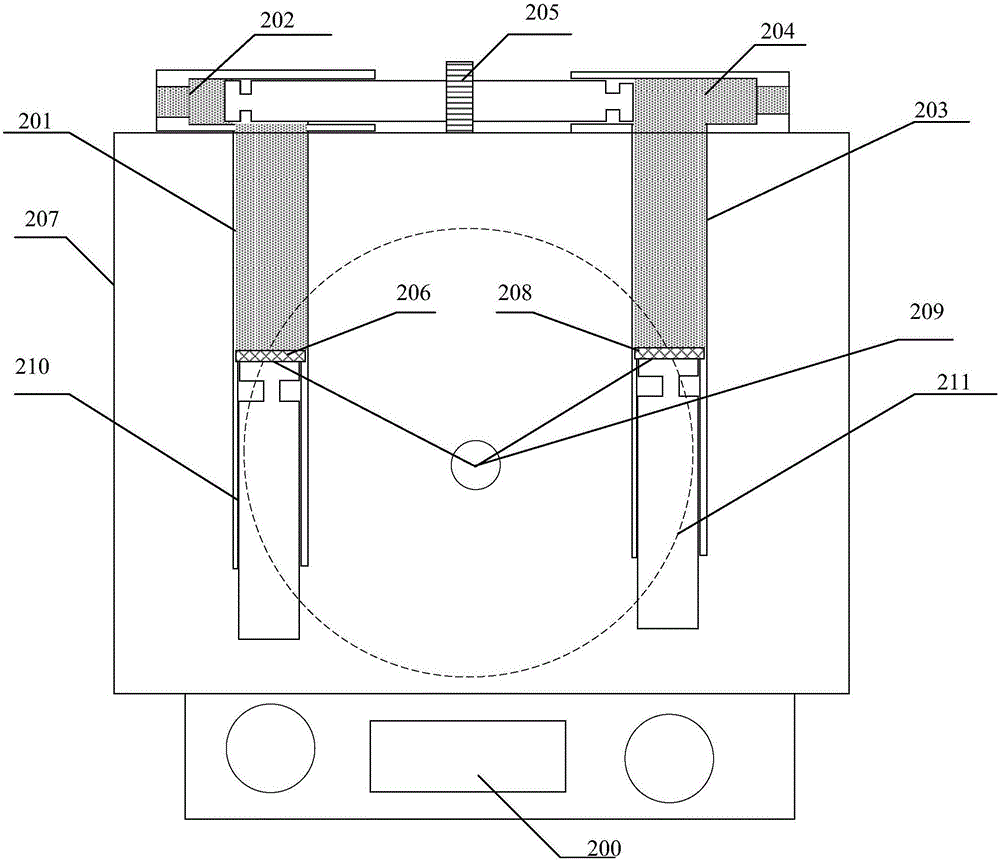
本发明涉及生物质固体燃料成型设备领域,具体而言涉及一种移动式生物质成型机。
背景技术:
:生物能源作为一种可再生能源,日益受到世界各国的重视,但是生物质存在堆积密度小且较松散,因而存在运输、储存和使用不方便等问题,而生物质致密成型能够有效的解决该问题。生物成型燃料可以提高生物质的使用效率、使用范围、有效减少直接燃烧造成的环境污染。生物质压缩成型工艺中,热压成型可将含水率18%的原料(秸秆)压缩成型,是国内外普遍研究和应用的成型工艺,其主要工艺流程为:原料粉碎——干燥——挤压成型——冷却包装。热压成型的主要工艺参数是温度、压力和物料在成型模具内的滞留时间。螺旋挤压成型是热压成型一种,工作原理是首先从进料口将粉碎的物料喂入压制室,靠物料与机筒、螺杆及物料自身间的摩擦力实现移动,通过模孔挤出,并在切割刀具的作用下,形成一定的产品。螺旋挤压成型生产工艺简单,但产量较低,每小时不到150Kg;能耗高,需要电加热,吨能耗90KWh以上;模具昂贵,寿命短,最高寿命不超过500h。冲压成型机是靠活塞的往复运动实现的,正常工作压强12MPa。冲压成型对原料适用范围广,但成型机设备结构复杂,生产过程中噪声大,振动大,故障率高,设备占地面积大,主机身长。压辊式颗粒成型机是目前国内最为普遍应用的一种成型工艺。压辊式成型机的主要工作部件由压辊和压模组成,在压制过程中,原料进入压辊和压模之间,压模上有成型孔,在压辊的作用下被压入成型孔内,最后用切断刀切成一定长度的成型燃料。压辊成型适应的原料范围广,可用于加工木屑、秸秆、稻壳等原料,不需要外部加热。压辊成型优点是产量较大、能耗相对较低,但使用维护复杂、模具昂贵,综合成本较高。为此,有必要提供一种新型生物质成型机机以解决上述现有技术中的问题。技术实现要素:在
发明内容部分中引入了一系列简化形式的概念,这将在具体实施方式部分中进一步详细说明。本发明的
发明内容部分并不意味着要试图限定出所要求保护的技术方案的关键特征和必要技术特征,更不意味着试图确定所要求保护的技术方案的保护范围。为解决现有技术中的问题,本发明提供一种移动式生物质成型机,所述移动式生物质成型机上一体集成有:上料粉碎系统,输送与除尘系统,以及造粒成型系统;其中,所述上料粉碎系统用于将物料粉碎并自喷入所述输送与除尘系统,所述输送和除尘系统用于除尘和气料分离,所述造粒成型系统用于将气料分离后的物料压缩成型。示例性地,所述上料粉碎系统包括无筛网粉碎机。示例性地,所述输送与除尘系统包括气力输送系统以及用于除尘的布袋。示例性地,所述造粒成型系统包括与所述输送和除尘系统连接的料箱、与所述料箱连接的成型模具系统和用于给所述成型模具系统提供动力的液压驱动系统。示例性地,所述成型模具系统包括预压室和成型室。示例性地,所述成型模具系统包括两个预压室,所述两个预压室对应设置有两个成型室。示例性地,所述成型模具系统还包括一个设置于所述两个成型室之间的主油缸,所述主油缸为双向油缸,用于驱动所述两个成型室。示例性地,所述成型模具系统还包括位于所述料箱中的拨料器,所述拨料器将所述物料推至所述预压室。示例性地,所述料箱中设置有两个拨料器,所述拨料器由一个圆盘给料器驱动。示例性地,所述预压室设置有推料油缸,所述推料油缸具有自锁功能。示例性地,所述上料粉碎系统、输送与除尘系统以及造粒系统集成在移动载体上。根据本发明的生物质成型机将粉碎、输送、除尘和压缩成型等工艺集成为一体,有效简化系统设计,减少成型机占地面积;同时,设备可移动,操作方便灵活,节省一次运输。粉碎后的物料直接进入输送与除尘系统,成型过程不需要对原料进行烘干或其他预处理,成型过程不需要加热,成型后不需要对成型后的物料进行冷却即可包装,大大简化工艺,有效减少能耗和减少固定资产投资。同时设备具有自动化程度高,维护和操作简单,工作运行稳定,综合成本低等特点。附图说明本发明的下列附图在此作为本发明的一部分用于理解本发明。附图中示出了本发明的实施例及其描述,用来解释本发明的装置及原理。在附图中,图1为根据本发明实施例的生物质成型机的结构示意图;图2为根据本发明实施例的造粒成型系统的模具成型系统的结构示意图;图3为根据本发明实施例的造粒成型系统的液压系统工作原理示意图。具体实施方式在下文的描述中,给出了大量具体的细节以便提供对本发明更为彻底的理解,然而,对于本领域技术人员而言显而易见的是,本发明可以无需一个或多个这些细节而得以实施。在其他的例子中,为了避免与本发明发生混淆,对于本领域公知的一些技术特征为进行描述。为了彻底理解本发明,将在下列的描述中提出详细的步骤,以便阐释本发明提出的生物质成型机和成型方法的原理。显然,本发明的实施并不限定于本领域的技术人员所熟悉的特殊细节。本发明的较佳实施例详细描述如下,然而除了这些详细描述外,本发明还可以具有其他实施方式。应当理解的是,本发明能够以不同形式实施,而不应当解释为局限于这里提出的实施例。相反地,提供这些实施例将使公开彻底和完全,并且将本发明的范围完全地传递给本领域技术人员。在附图中,为了清楚,层和区的尺寸以及相对尺寸可能被夸大。自始至终相同附图标记表示相同的元件。在此使用的术语的目的仅在于描述具体实施例并且不作为本发明的限制。在此使用时,单数形式的“一”、“一个”和“所述/该”也意图包括复数形式,除非上下文清楚指出另外的方式。还应明白术语“组成”和/或“包括”,当在该说明书中使用时,确定所述特征、整数和/或部件的存在,但不排除一个或更多其它的特征、整数部件和/或组的存在或添加。在此使用时,术语“和/或”包括相关所列项目的任何及所有组合。为解决现有技术中存在的问题,本发明提供一种移动式生物质成型机,所述移动式生物质成型机上一体集成有:上料粉碎系统,输送与除尘系统,以及造粒成型系统;其中,所述上料粉碎系统用于将物料粉碎并自喷入所述输送与除尘系统,所述输送和除尘系统用于除尘和气料分离,所述造粒成型系统用于将气料分离后的物料压缩成型。根据本发明的生物质成型机将粉碎、输送、除尘和压缩成型等工艺集成为一体,有效简化系统设计,减少成型机占地面积;同时,设备可移动,操作方便灵活,节省一次运输。粉碎后的物料直接进入输送与除尘系统,成型过程不需要对原料进行烘干或其他预处理,成型过程不需要加热,成型后不需要对成型后的物料进行冷却即可包装,大大简化工艺,有效减少能耗和减少固定资产投资。同时设备具有自动化程度高,维护和操作简单工作运行稳定,综合成本低等特点。实施例一下面参考图1、图2和图3来描述本实施例提出的一种移动式生物质成型机,其中,图1为本实施例提出的一种移动式生物质成型机的结构示意图;图2为本实施例提出的生物质成型机的造粒成型系统中模具成型系统的结构示意图;图3为根据本发明实施例的造粒成型系统的液压系统工作原理示意图。图1示出了本发明涉及的一种移动式生物质成型机的结构示意图,所述移动式生物质成型机一体集成有上料粉碎系统101,输送与除尘系统102,造粒成型系统103;所述上料粉碎系统101用于将物料粉碎并自喷入所述输送与除尘系统102,所述输送和除尘系统102用于除尘和气料分离,所述造粒成型系统103用于将气料分离后的物料压缩成型。根据本发明的生物质成型机粉碎后的物料以自喷方式进入输送与除尘系统,而不需要加引风机,简化设备构造;经过粉碎后的物料不需要经过烘烤或晒干直接进入输送与除尘系统,经由输送与除尘系统除尘后,输送至造粒成型系统成型,从而形成将粉碎、输送、除尘和压缩成型等工艺集成为一体,有效简化系统设计,简化成型机构造;同时,设备可移动,操作方便灵活,节省一次运输。粉碎后的物料直接进入输送与除尘系统,成型过程不需要对原料进行烘干或其他预处理,成型过程不需要加热,成型后不需要对成型后的物料进行冷却即可包装,大大简化工艺,简化工作人员操作,仅需进行喂料和出料操作,且工艺过程流畅稳定,保证设备稳定运行,有效减少能耗和减少固定资产投资,减少综合成本。示例性地,所述上料粉碎系统包括无筛网粉碎机。无筛网粉碎机代替现有粉碎机内部筛网结构,可处理含水量25%以下的生物质原料,相对于现有技术一般要求含水率18%以下的粉碎机,有效增加原料使用范围,粉碎前不需要对原料进行预处理,进一步减少生产成本。如图1所示,上料粉碎系统101为无筛网粉碎机,粉碎后的物料直接进入输送与除尘系统102,不需要经过烘干和人工晾晒费用,进一步减少生产成本。示例性的,所述输送与除尘系统包括气力输送系统以及用于除尘的布袋。所述气力输送系统利用气流的能量,在密闭管道内将有粉碎系统粉碎的颗粒输送至造粒成型系统,其输送量大,输送距离长,输送速度高,可实现一处装料,多处卸料。因而可提高生物质成型机的系统集成率和效率。示例性的,所述输送和除尘系统包括用于除尘的布袋。粉碎后的物料在气力输送过程中,与除尘的布袋发生碰撞,其中颗粒大、比重大的粉尘物料,由于重力的作用沉降下来,落入灰斗或料箱,较细小的粉尘通过滤料。使用布袋除尘方式进行气料分离,工艺简单,进一步简化系统设计。示例性地,所述造粒成型系统包括与所述输送和除尘系统连接的料箱、与所述料箱连接的成型模具系统和用于给所述成型模具系统提供动力的液压驱动系统。如图1所示,所述造粒成型系统103包括料箱104,成型模具系统105以及液压驱动系统106。料箱103设置于输送与除尘系统102的下方,经输送与除尘系统102除尘后的物料落入料箱104;料箱104与成型模具系统105相连,料箱103将经由输送与除尘系统102落入其中的物料推送至成型模具系统105;成型模具系统105经液压驱动系统106提供动力驱动,完成生物质压制成型。成型模具系统105在液压驱动系统106的驱动下将料箱103中的物料压制成型,成型过程不需要加热,成型后不需要对成型后的物料进行冷却即可包装,大大简化工艺,有效减少能耗和减少固定资产投资;采用成型模具压缩成型工艺,相较于现有技术中的螺旋挤压和压辊成型工艺,磨具成本低,进一步减少综合成本;同时液压驱动完成压制成型,自动化程度高,使得设备操作方便灵活,进一步减少人工成本,在一个示例中,仅需两人就可完成操作。示例性的,所述成型模具系统包括预压室和成型室。所述预压室将经所述上料粉碎系统粉碎、所述输送和除尘系统输送和除尘后的物料进行预压缩,物料经过预压缩后由松散粉碎物料成型为预压缩料块,预压缩料块密度较低,一方面提供进入成型室物料的前级较低密度料块,使得物料经过经成型室压缩成密度较高的料块,另一方面,不影响其进入成型室的流动性,推进喂料。所述成型室将所述经过预压缩后的物料进行压制成型,形成高密度成型料块。生物质原料经过两次压制成型,有效提高物料压制后的成型密度,提高压制效率。如图2,示出了本发明的一个实施例的造粒成型系统中模具成型系统的的示意性结构示意图。所述成型模具系统设置在料箱207下方,可将由料箱207提供的物料压制成型。所示造粒成型系统设置有预压室201和成型室202。所示由料箱207提供的物料经过预压室201进行预压缩后进入成型室202进行压制成型。示例性的,所述成型模具系统包括两个预压室,所述两个预压室对应设置有两个成型室。继续参看图2,所述成型模具系统包括两个预压室,分别为左预压室201和右预压室203;左预压室201对应设置有左成型室202,右预压室203对应设置有右成型室204。在所述造粒成型系统上同时集成两个预压室和两个成型室,一方面有效提升生物质成型机的集成度,增加设备空间利用率,简化系统设计,进一步缩小成型机占地面积;另一方面可有效提升生物质原料压制成型的效率,提升设备产率。示例性地,所述成型模具系统还包括一个设置于所述两个成型室之间的主油缸,所述主油缸为双向油缸,用于驱动所述两个成型室。继续参看图2,成型模具系统中还包括一个主油缸204,主油缸204为双向油缸,所述左成型室202与右成型室204共同由所述主油缸204驱动。具体的,在运行过程中,油缸顺序驱动所述两个成型室,继续参看图2,油缸向左运动,驱动左成型室202进行压制成型,左成型室202进行压制的过程中,右成型室完成物料的输送;左成型室完成压制,油缸向右运动,驱动右成型室204进行压制成型,右压制成型室进行压制的过程中,左成型室202完成物料的输送。如此设计,将油缸驱动压制室压制的进程和回程相结合,驱动左成型室的进程成为驱动右成型室的回程,驱动左成型室的回程成为驱动右成型室的进程,一方面节省提高系统设计集成度,进一步缩小成型机占地面积,另一方面提升系统产能,减少能耗。优选的,所述主油缸缸径280mm,额定压力设定为31.5MPa,从而可产生100吨推力,以提升成型室压制成型的密度,提升压制效率。在一个示例中,所述主油缸采用一个功率为45Kw的高压泵(柱塞泵),使主油缸一个工作循环控制6s,从而节省油缸一个工作循环时间,提升压制效率,提升产能。示例性的,所述成型模具系统还包括位于所述料箱中的拨料器,所述拨料器将所述物料推至所述预压室。继续参看图2,料箱207内设置有拨料器206和208,所述拨料器206和208用来将料箱207中的物料推送至预压室201和203。所述拨料器设置有左拨料器206和右拨料器208,分别对应左预压室201和右预压室203。在一个示例中,所述拨料器206和208集成到一个圆盘给料器209上,进一步增加系统的集成度,简化系统设计。示例性的,所述预压室设置有推料油缸,所述推料油缸具有自锁功能。所述推料油缸驱动预压室进行物料的预压缩,继续参看图2,所述造粒成型系统包括两个推料油缸210和211两个预压室分别对应左预压室201和右预压室203,所述推料油缸210和211在液压动力系统的驱动下顺序驱动预压室201和203,配合主油缸完成成型室202和204的压制成型。成型过程中,推料油缸的自锁功能,从而使液压系统传动稳定的同时保证压缩效率,以完成两个推料油缸协同动作。参看图3,描述了根据本发明的实施例的造粒成型系统工作原理图。表1示出了图3中各元件对应的功能。表1:元件功能YV1液压站启动YV2主油缸左推YV3主油缸右推YV4左给料油缸推YV5左给料油缸回YV6右给料油缸推YV7右给料油缸回表2示出了造粒成型系统工作过程中各油缸动作顺序。表2:继续参看图2、图3、表1和表2,进一步描述所述液压驱动的造粒成型系统的工作流程。首先,启动液压站电机;接着,左推料油缸210推,驱动左预压室201对原料进行预压缩成型,同时,完成左推料油缸210保,以保持推料状态完成左预压室预压缩成型;接着,主油缸205左推,驱动左左成型室202进行压制成型;接着,右推料油缸209推,驱动右预压室203对原料进行预压缩成型,同时,完成右推料油缸209保,以保持推料状态完成右预压室预压缩成型;接着,主油缸205右推,驱动右成型室204进行压制成型;接着,左推料油缸210回;接着,左推料油缸210推,驱动左预压室201对原料进行预压缩成型,同时,完成左推料油缸210保,以保持推料状态完成左预压室203预压缩成型;接着,主油缸205左推,驱动左成型室202进行压制成型;接着,右推料油缸209回;接着,右推料油缸209推,驱动右预压室203对原料进行预压缩成型,同时,完成右推料油缸209保,以保持推料状态完成右预压室204预压缩成型;至此完成一个循环。在一个示例中,所述主油缸采用一个功率为45Kw的高压泵(柱塞泵),使主油缸一个工作循环控制6s,进一步提升压制效率,提升产能。在一个示例中,根据本发明的生物质成型机和成型方法,经过第一预压室预压缩形成块料的密度为350~450Kg每立方米,经过成型室压缩成型后形成的成型料密度不小于800Kg每立方米,根据本发明提供的生物质成型机和成型方法每小时产能可达500kg。示例性的,所述上料粉碎系统、输送与除尘系统以及造粒系统集成到移动载体上。参看图1,上料粉碎系统101、输送与除尘系统102以及造粒系统103集成到底盘100上,所述底盘100可以是可移动的载体,或者是可以放置到可移动载体上的任何载体。将上料粉碎系统、输送与除尘系统以及造粒系统集成到移动载体上从而实现生物质成型机可移动,方便设备管理与存放,适用于不同场合使用。根据本发明的生物质成型机将粉碎、输送、除尘和压缩成型等工艺集成为一体,有效简化系统设计,减少成型机占地面积;同时,设备可移动,操作方便灵活,节省一次运输。粉碎后的物料直接进入输送与除尘系统,成型过程不需要对原料进行烘干或其他预处理,成型过程不需要加热,成型后不需要对成型后的物料进行冷却即可包装,大大简化工艺,有效减少能耗和减少固定资产投资。同时设备具有自动化程度高,维护和操作简单,工作运行稳定,综合成本低等特点。本发明已经通过上述实施例进行了说明,但应当理解的是,上述实施例只是用于举例和说明的目的,而非意在将本发明限制于所描述的实施例范围内。此外本领域技术人员可以理解的是,本发明并不局限于上述实施例,根据本发明的教导还可以做出更多种的变型和修改,这些变型和修改均落在本发明所要求保护的范围以内。本发明的保护范围由附属的权利要求书及其等效范围所界定。当前第1页1 2 3