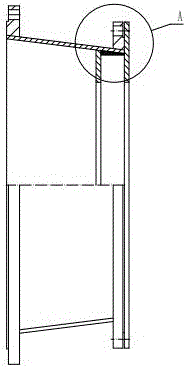
本发明涉及变径复合管制作技术领域,具体涉及一种由金属、陶瓷及高分子通过自蔓延高温合成技术(Self-propagatinghigh-temperaturesynthesis简称SHS)和真空离心浸渍浇注等特种方法复合加工而成的大口径耐磨耐蚀三元复合变径管的制作方法。
背景技术:我国近十几年来经济发展迅速,一系列与能源、环保相关的重大建设工程项目如烟气脱硫、煤炭变油、川气东送、油气净化、海水淡化等均在实施中。由于材料涉及腐蚀磨损和冲蚀磨损等相互作用工况,设备和管道出现过早泄漏现象频繁。尤其是沿海地区的火电厂,由于受到含颗粒泥沙海水的冲蚀磨损作用,大量灰渣输送管、冷却水循环海水管及废液处理管等,泄漏情况更为严重。据统计,我国输送管道、工艺管道和公用管道累计长达数千公里。每年管道因腐蚀、磨损、冲蚀等引起的泄漏相当频繁,维修更换量大,直接经济损失几十亿元。当今可用的管道有三类:金属类(不锈钢管、镍磷镀层管、高铬铸钢管、高铬稀土管、渗铝管、双金属管、碳钢管等);聚合物类(橡胶衬里钢管、塑料衬里钢管、喷塑钢管、玻璃钢管、塑料衬钢复合管、纤维增强塑料管等);陶瓷类(铸石衬里钢管、陶瓷复合钢管、搪玻璃钢管、水泥浇铸钢管等)。这些单质管道或二元复合管,由于性能单一,界面为物理粘接,结合力弱,仅适用单纯的磨损或腐蚀工况,在复杂工况下使用时寿命均很短,有的不到一个月就泄漏,对社会经济产生了很大的影响。这其中弯管、变径管的失效最快,原因是其在输送介质过程中,其受到的磨损相对比直管高几倍至几十倍,在磨损腐蚀的交互作用下,失效也远快于直管。
技术实现要素:本发明的目的在于提供一种适用于输送有腐蚀磨损、冲蚀磨损、磨损结垢及复合腐蚀等复杂介质工况,特别是火力、核发电行业汽轮机热交换使用海水循环冷却,存在海水腐蚀和泥沙磨损状况的大口径的由金属、陶瓷和高分子复合加工而成的大口径耐磨耐蚀三元复合变径管的制作方法。本发明提出的大口径耐磨耐蚀三元复合变径管的制作方法,具体步骤如下:(1)、采用梯度法分节分步进行自蔓延高温离心合成反应(SHS)根据变径管的长度及大小端直径差情况,在变径管内表面分别设置一定数量的挡环,使变径管沿轴向分成多个梯度过渡,即把变径管分成多个管节(管段),一般以直径差距4mm~30mm作为一个梯度,从小直径挡环开始,将挡环固定在变径管小直径端内;在挡环内填充铝热剂,将变径管装夹置于离心机上进行旋转,使铝热剂均匀分布于挡环内,用点火器点燃铝热剂,进行自蔓延高温离心合成反应(SHS),待冷却后去除挡环再以同样方法处理变径管大一节梯度,直至最后到大直径端;反应结束后生成TiB2/ZrB2-Al2O3陶瓷;(2)、在相邻的挡环间形成的梯度之间截面为三角的区域填充耐磨材料,耐磨材料由耐磨无机粒子和改性树脂复合粘接剂组成;(3):采用模型真空浇注工艺对变径管内表面进行拼混树脂浇注成型制作与变径管内表面相应的内模,内模与步骤(2)所得陶瓷和耐磨材料层间隔控制在3mm~10mm,内模与变径管端部密封使形成一密闭空间,留两个接口,一个接口用抽真空机抽真空,控制真空度为0.1-0.3大气压,另一个接口吸入配制好的有机/无机拼混树脂,直至填实,待时间大于或等于12小时固化结束,拆除内模完成制品。本发明中,步骤(1)中所述铝热剂主要成分是氧化铁粉Fe2O3和铝粉Al,还添加有二氧化锆ZrO2、二氧化钛TiO2、二氧化硅SiO2、三氧化二铝Al2O3和三氧化二硼B2O3,其中:按重量百分比计,氧化铁粉52-60%、铝粉18-24%、二氧化锆3-8%、二氧化钛3-5%、二氧化硅1-4%、三氧化二铝1-4%、三氧化二硼3-8%,,其总重量满足100%。使反应产物α-Al2O3具有高韧性,能通过中间层Fe紧密贴合于大口径变径管内表面,不会出现开裂、鼓包、翘起、脱壳等现象。本发明中,自蔓延高温离心合成反应(SHS)是将配制的反应物料(铝热剂)置于管内,然后将金属管装在离心机上,使其高速旋转并引燃粉末物料,利用铝热反应所释放的热量,产生3000℃以上的高温,使反应在金属管内迅速蔓延,TiB2(熔点为2850℃)/ZrB2(熔点为3040℃)-Al2O3(熔点为2040℃)及Fe(熔点为1560℃)被加热使其处于熔融状态。同时钢管的内壁亦受热熔化一薄层,与生成物相融为一体,高温液相在离心力场的作用下而发生分离,密度大的Fe(7.8g/cm3)紧靠钢管内壁形成中间过渡层,并与钢管内壁呈冶金融合状态;密度小的TiB2(4.52g/cm3)/ZrB2(5.8g/cm3)-Al2O3(3.97g/cm3)则紧贴着铁层,形成均匀致密的陶瓷层。反应的化学方程式如下:Fe2O3+2Al——Al2O3+2Fe+836kJ3TiO2+3B2O3+10Al→3TiB2+5Al2O3(3ZrO2+3B2O3+10Al→3ZrB2+5Al2O3)α-Al2O3陶瓷具有高硬、不粘、抗蚀、隔热和耐温的特点,TiB2/Al2O3复合粉体具有良好的界面结合,这主要由TiB2在Al2O3颗粒表面进行非均相成核、结晶和长大的结晶过程所决定的,颗粒间良好结合的界面,能有效抑制晶粒生长,宏观上使α-Al2O3陶瓷具有高韧性,能通过中间层Fe紧密贴合于大口径钢管内表面,不会出现开裂、鼓包、翘起、脱壳等现象。本发明中,步骤(2)中所述耐磨无机粒子为金刚砂、石英砂或氧化铝陶瓷等中任一种,颗粒大小为250~710μm。本发明中,步骤(2)中所述改性树脂复合粘接剂由环氧树脂与聚酯树脂类高强粘合剂组成。本发明中,步骤(3)中所述填实是将聚合物树脂固化于陶瓷基孔隙内,并再形成一聚合物树脂内壁层。本发明中,步骤(3)中所述有机/无机拼混树脂中,所述有机树脂为环氧树脂﹑固化剂和改性剂,或者是不饱和聚酯树脂、引发剂和促进剂;无机填料为玻璃鳞片、二氧化硅、二氧化钛﹑滑石粉和石膏,它们的质量比是(1-2):(1-2):(0.2-0.5):(6-9):(4-6)。具体方法是:将有机树脂与无机填料按(2-4):(1-4)质量比在拼混树脂溶剂中混合而成有机/无机拼混树脂,拼混树脂溶剂采用混合溶剂,它们是二甲苯﹑丁酮或乙酸丁酯任意两种混合溶剂,拼混树脂混合溶剂的使用量为有机树脂总量的2-5%。本发明中,有机树脂中环氧树脂为双酚A型环氧树脂,不饱和聚酯树脂为乙烯基酯树脂;固化剂为聚酰胺,改性剂为聚硫橡胶,引发剂为过氧化甲乙酮,促进剂为辛酸钴液。本发明中,可使用直接涂覆方法直接在基体上涂覆有机/无机拼混树脂,浸涂或刷涂有机/无机拼混树脂,固化后形成聚合物树脂内壁层。本发明制作的三元复合变径管是由金属、陶瓷、聚合物等通过特种方法复合加工而成,主要技术有:梯度分节分步加工工艺技术;异种材料的反应复合成型技术;微纳米复相陶瓷的配混改性技术;拼混树脂的反应浸渍技术等。解决了自蔓延高温离心合成技术(SHS)中无法对变径管进行应用的难题,同时将金属承载连接性、陶瓷抗磨耐蚀性和聚合物耐蚀性等单一优异性能复合于一体,实现三元材料复合后性能最优化、协同化和功能化,不仅可以实现新型复合管综合性能的预设计以适应不同的介质工况,而且异种材料界面为化学结合,存在过渡层,使界面不同材料的热膨胀系数相匹配,粘接力强,赋予其优异的防磨损耐腐蚀抗疲劳的综合性能。使用寿命长,性价比高,从而解决了现有的变径管道在复杂工况下的寿命短的问题,提高了管线整体运行寿命,减少非正常停机次数和维修频率,具有非常重要的工程应用价值。大口径耐磨耐蚀三元复合变径管系列制品,将直接应用于一些新建、改建、扩建等重大管路系统工程项目中,如火电厂烟气脱硫装置管路系统、灰渣湿态排放输送管线、凝汽器循环冷却水海水管线或淡水改海水管路系统,以及炼铁厂高炉水渣排放管等。有益效果:1、本发明提出了在变径钢管内耐磨耐蚀复合层(陶瓷层和树脂层)的加工方法,解决了大口径变径管内无法加工陶瓷层的难题。2、本发明可以有效地预防大口径输送管线输送颗粒腐蚀介质在变径处磨损腐蚀失效,延长变径乃至整条管线使用寿命。附图说明图1为变径管内第一节自蔓延反应离心旋转示意图。图2为变径管内第一节烧制TiB2/ZrB2-Al2O3金属陶瓷层示意图。图3为图2中变径管内第一节烧制TiB2/ZrB2-Al2O3金属陶瓷层的局部放大图。图4为变径管内第二节烧制TiB2/ZrB2-Al2O3金属陶瓷层示意图。图5为图4中变径管内第二节烧制TiB2/ZrB2-Al2O3金属陶瓷层的局部放大图。图6为变径管内完成烧制TiB2/ZrB2-Al2O3金属陶瓷层示意图。图7为图6中变径管内完成烧制TiB2/ZrB2-Al2O3金属陶瓷层的局部放大图。图8为变径管内耐磨材料填充部分示意图。图9为图8中变径管内耐磨材料填充部分局部放大图。图10为变径管内表面拼混树脂浇注部分示意图。图11为图10中变径管内表面拼混树脂浇注部分局部放大图。图12为变径管内表面拼混树脂浇注成型部分示意图。图13为图12中变径管内表面拼混树脂浇注成型部分局部放大图。图中标号:1.变径管,2.法兰,3.螺栓,4.反应原料,5.旋转模具,6.端盖,7.挡环,8.陶瓷,9.耐磨材料,10.拼混树脂,11.内模。具体实施方式下面结合具体实施例,进一步阐述本发明。应理解,这些实施例仅用于说明本发明而不用于限制本发明的范围。此外应理解,在阅读了本发明讲授的内容之后,本领域技术人员可以对本发明作各种改动或修改,这些等价形式同样落于本申请所附权利要求书所限定的范围。实施例1:对DN700-DN600长度200的变径管进行此方法制作(未注明单位均为mm,以下同)a.采用梯度法分节分步对变径管进行自蔓延高温离心合成反应,步骤如下:此大口径变径管大端外径为720,小端外径为630,壁厚14,大端内径为692,小端内径为602,大小端内径直径差90,以直径差18(单边差9)为梯度间隔,则可分为5节(段),则变径管轴向长度200,分成5段后每段为40,变径管内中间每段直径分别是:674、656、638、620,按上述直径分别制作四只挡环,挡环开孔内径400,厚度20,并制作大、小两端的封盖,封盖尺寸参照相应的法兰连接尺寸,封盖开孔内径400,厚度20。变径管大小两端装配法兰并电焊焊接,小端装上封盖,并固定在离心机上,同时安装620挡环,并固定牢固,准备对变径管第一节进行反应烧制TiB2/ZrB2-Al2O3金属陶瓷层。以配方为氧化铁粉58%、铝粉22%、氧化锆粉5%、氧化钛粉4%、氧化硅粉3%、氧化铝粉3%、氧化硼5%等组成1.8kg混合粉料。旋转变径管,加入混合粉料(见图1),点燃粉料,进行自蔓延离心反应复合成型,离心转速是800转/分,在钢管内壁第一节烧制一层具有高耐磨性能的TiB2/ZrB2-Al2O3金属陶瓷(见图2、图3)。拆除620挡环,安装638挡环,固定牢固,准备对变径管第二节进行反应烧制TiB2/ZrB2-Al2O3金属陶瓷层,加入1.85kg混合粉料,以同样方法烧制第二节金属陶瓷层(见图4、图5)。直至最后装上大端封盖,将第5节金属陶瓷层烧好(见图6、图7)。b.变径管内表面陶瓷层梯度之间截面为三角形的区域使用耐磨材料填充耐磨材料主要由耐磨无机粒子和改性树脂复合粘接剂组成,耐磨材料无机粒子选择高硬度金刚砂,粒度为420μm,改性树脂复合粘接剂选用环氧树脂与聚酯树脂组成高强粘合剂,耐磨无机粒子和改性树脂复合粘接剂重量配比为3:2,配制总量1.8kg,用刮刀填充于陶瓷层梯度之间截面为三角形的区域内(见图8、图9)。c.采用模型真空浇注工艺对变径管内表面进行拼混树脂浇注成型以厚度4的钢板依照变径管内腔卷制做好内模,内模与变径管内陶瓷耐磨层之间留有5毫米间隙,端部用橡胶圈封堵,用抽真空机抽出管内空气,达到0.02MPa,加入约7.6kg经配混的环氧基拼混树脂(配混比例为:环氧树脂30%,聚酰胺10%,聚硫橡胶10%,玻璃鳞片6%,二氧化硅6%,二氧化钛1%,滑石粉20%,石膏粉13%,二甲苯2%,乙酸丁酯2%)直至填满,缓慢恢复管内压力到常压(见图10、图11)。拼混树脂固化12小时左右,固化后的拼混树脂层厚度为5,拆开内模、封盖完成制备(见图12、图13)。实施例2:对DN1200-DN1000长度400的变径管进行此方法制作(未注明单位均为mm,以下同)a.采用梯度法分节分步对变径管进行自蔓延高温离心合成反应,步骤如下:此大口径变径管大端外径为1220,小端外径为1020,壁厚14,大端内径为1192,小端内径为992,大小端内径直径差200,以直径差25(单边差12.5)为梯度间隔,则可分为8节(段),变径管轴向长度400,分成8段后每段长度为50,变径管内中间每段直径分别是:1167、1142、1117、1092、1067、1042、1017,以上述直径分别制作7只挡环,挡环开孔内径800,厚度20,并制作大、小两端的封盖,封盖尺寸参照相应的法兰连接尺寸,封盖开孔内径800,厚度20。变径管大小两端装配法兰并电焊,小端装上封盖,并固定在离心机上,同时安装1017挡环,并固定牢固,准备对变径管第一节进行反应烧制TiB2/ZrB2-Al2O3金属陶瓷层。以配比为氧化铁粉58%、铝粉22%、氧化锆粉5%、氧化钛粉4%、氧化硅粉3%、氧化铝粉3%和氧化硼5%组成3.72kg混合粉料。旋转变径管,加入混合粉料(见图1),点燃粉料,进行自蔓延离心反应复合成型,离心转速是600转/分,在钢管内壁第一节烧制一层具有高耐磨性能的TiB2/ZrB2-Al2O3金属陶瓷(见图2、图3)。拆除1017挡环,安装1042挡环,固定牢固,准备对变径管第二节进行反应烧制TiB2/ZrB2-Al2O3金属陶瓷层,加入3.81kg混合粉料,以同样方法烧制第二节金属陶瓷层(见图4、图5)。直至最后装上大端封盖,将第8节金属陶瓷层烧好(见图6、图7)。b.变径管内表面陶瓷层梯度之间截面为三角形的区域使用耐磨材料填充耐磨材料主要由耐磨无机粒子和改性树脂复合粘接剂组成,耐磨材料无机粒子选择高硬度金刚砂,粒度为500μm,改性树脂复合粘接剂选用环氧树脂与聚酯树脂组成高强粘合剂,耐磨无机粒子和改性树脂复合粘接剂重量配比为3:2,配制总量3.5kg,用刮刀填充于陶瓷层梯度之间截面为三角形的区域内(见图8、图9)。c.采用手工浸涂方法对变径管内表面进行树脂层涂覆成型表面分批浸涂经配混拼混树脂,总量15.4kg,(配混比例为:乙烯基酯树脂60%,过氧化甲乙酮1.5%,辛酸钴液1.5%,玻璃鳞片4%,二氧化硅4%,二氧化钛1%,滑石粉15%,石膏粉10%,二甲苯2%,丁酮1%),涂覆后拼混树脂固化12小时左右,树脂层厚度为5(见图10、图11)。拆开内模、封盖完成制备(见图12、图13)。