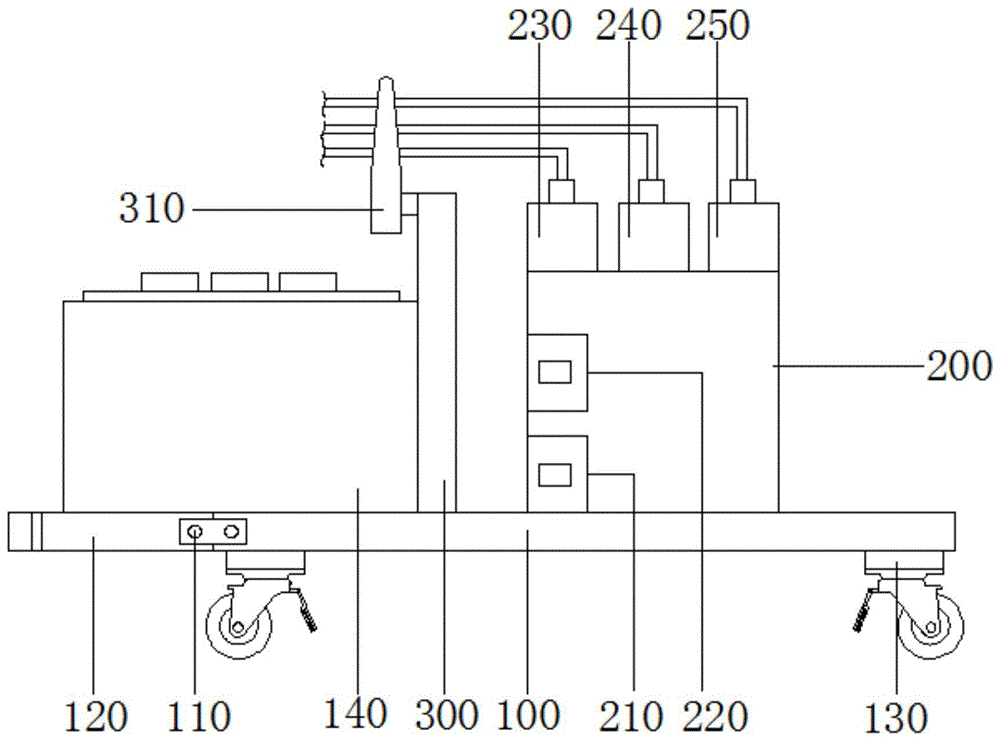
本发明涉及检测装置
技术领域:
,具体为一种车载锂离子动力电池检测设备的检测方法。
背景技术:
:电动汽车是指以车载电源为动力,用电机驱动车轮行驶,符合道路交通、安全法规各项要求的车辆,对环境影响相对传统汽车较小。而车载锂离子动力电池是配合电动汽车进行使用的,是混合动力汽车及电动汽车的动力电池,由于镍氢电池的一些技术性能如能量密度、充放电速度等已经接近到理论极限值,锂电池由于能量密度高、容量大、无记忆性等优点。现有车载锂离子动力电池在配合汽车安装和检修过程中,都需要进行检测,因为车载锂离子动力电池的内部结构复杂,需要检测的项目较多,在检测过程中,需要多人进行轮流检测,人员消耗大,检测速度较慢,效率较低,而且为了配合不同的检测项目,需要配备不同的检测装置,经济投入较高。技术实现要素:本发明的目的在于提供一种车载锂离子动力电池检测设备的检测方法,以解决上述
背景技术:
中提出的车载锂离子动力电池的内部结构复杂,需要检测的项目较多,在检测过程中,需要多人进行轮流检测,人员消耗大,检测速度较慢,效率较低,而且为了配合不同的检测项目,需要配备不同的检测装置,经济投入较高的问题。为实现上述目的,本发明提供如下技术方案:一种车载锂离子动力电池检测设备,包括底板、电能箱和支架,所述底板的顶部接触所述电能箱,所述底板的顶部焊接所述支架,所述底板的前侧壁通过螺丝固定连接有合页,所述合页的活动板通过螺丝固定连接有侧板,所述底板的底部通过螺栓固定连接有滚轮,所述侧板的顶部接触有锂电池,所述电能箱的前侧壁通过螺栓固定连接有容量检测器和DCR检测器,所述电能箱的顶部通过螺栓固定连接有BMS检测器、绝缘检测器和温度检测器,所述支架的顶部通过轴杆插接有线板,所述线板的顶部一体成型连接有顶板,所述顶板的右侧壁开设有凹槽,所述凹槽的圆周内壁镶嵌有圆板,所述圆板的右侧壁开设有圆板孔。优选的,所述电能箱的内腔底部通过螺栓固定连接有蓄电池,所述蓄电池的底部包括充电接口。优选的,所述支架的材质为空腔不锈钢板,所述空腔内部填充有膨胀石墨压缩板。一种车载锂离子动力电池检测设备的检测方法,该车载锂离子动力电池检测设备的检测方法包括如下步骤:S1:容量检测:利用所述电容检测器进行快速充电片段容量检测,电动汽车在SOC1至SOC2区间内进行充电,选取的SOC检测区间越广,测试的精度越高,检测区间定为20%SOC区间;充电可用容量检测:将电动汽车自然放电至厂商截止条件,即SOC=0%,静置一段时间后,通过检测设备将电动汽车进行正常充电至厂商截止条件,即SOC=100%,所述电容检测器即可通过安时积分获得汽车的充电可用容量,亦可通过电流电压与充电时间的积分获得电池的充电可用能量;放电容量检测:将电动汽车充电至厂商截止条件,即SOC=100%,静置一段时间后,通过所述电容检测器将电动汽车进行正常放电至厂商截止条件,即SOC=0%,检测设备即可通过安时积分获得汽车的放电可用容量,亦可通过电流电压与放电时间的积分获得电池的放电可用能量;S2:DCR检测:利用所述DCR检测器进行DCR快速检测,在1C倍率下充电,SOC显示值为50%时,所述DCR检测器的显示电压和电流分别为U1和I1;在0.1C倍率下充电,SOC显示值为50%时,所述DCR检测器的显示电压和电流分别为U0.1和I0.1,由于所述DCR检测器的显示电压即为电动汽车的电池电压U与DCR上的电压降之和,因此可得如下计算公式:U1=U+DCR·I1(1)U0.1=U+DCR·I0.1(2)(1)式—(2)式,即可算得DCR=(U1–U0.1)/(I1–I0.1);在电池SOC两端,受SOC算法修正影响不作为DCR测试起点,在50%SOC范围内DCR较为稳定,故选取50%SOC作为DCR测试起点,测试循环过程中每次测试间静置30s,利用DCR标准检测,将电动汽车与所述DCR检测器连接,放电至厂商截止条件,即SOC=0%,静置30min,充电至BMS显示SOC=50%,将电动汽车进行短时间恒流1C倍率放电,记录第0s,0.1s,2s,10s以及18s对应的电压和电流值,分别记为U0,U0.1,U2,U10,U18以及I0,I0.1,I2,I10,I18;静置40s后,对电动汽车进行短时间恒流0.75C倍率充电,记录第58s,58.1s,60s,68s以及108s累计时间对应的电压和电流值,分别记为U58,U58.1,U60,U68,U108以及I58,I58.1,I60,I68,I108,其中第18s至第58s区间为电流绝对值降至0的区间,第68s至108秒区间为电流绝对值降至0的区间;S3:BMS精度检测:利用所述BMS检测器检测SOC精度,每隔1秒记录SOCn及累计容量Cn,充电和放电终止时测得累计容量为C0,系统容量Cap参考容量测试结果,检测电流精度,测试过程中获取BMS电流读数,并记录同一时刻所述BMS检测器电流读数,检测电压精度,测试过程中获取BMS电压读数,并记录同一时刻检测设备电压读数;S4:外观检测:确保箱体外观良好,未见明显变形及锈蚀;箱体无刺激性气味液体;箱体螺栓无缺失、无松动、无螺纹露出;箱体高、低压线束无金属部分裸露,无明显破损;箱体连接器无明显破损、松脱;箱体的铭牌、安全警示标识清晰可见,无破损;S5:绝缘检查:利用所述绝缘检测器在标准充电法和放电法测试系统容量过程中,BMS关闭绝缘检测,由所述绝缘检测器完成测试获取绝缘阻值,全程的测试阻值要求电池动力系统与车壳绝缘阻抗>500Ω/V;S6:充电接口温度检查:利用所述温度检测器在容量测试过程中实时检测充电枪连接位置的温度,全程记录动态温度数据,统计最高和最低温度,充电插头和车辆底座非金属部分允许温度不超过85℃,端子温升不超过50K。与现有技术相比,本发明的有益效果是:该种车载锂离子动力电池检测设备及其检测方法,通过配件的组合运用,可使车载锂离子动力电池在检测过程中实现容量、DCR、BMS、绝缘和充电接口温度的统一检测,只要单人操作即可进行多项的检测工作,简化了检测步骤,检测过程快速有效,降低了检测的时间,加快了工作效率,也有效避免了不同检测设备的选用而造成的经济浪费。附图说明图1为本发明结构示意图;图2为本发明线板示意图;图3为本发明电动汽车充电等效电路图示意图。图中:100底板、110合页、120侧板、130滚轮、140锂电池、200电能箱、210容量检测器、220DCR检测器、230BMS检测器、240绝缘检测器、250温度检测器、300支架、310线板、320顶板、330圆板、340圆板孔。具体实施方式下面将结合本发明实施例中的附图,对本发明实施例中的技术方案进行清楚、完整地描述,显然,所描述的实施例仅仅是本发明一部分实施例,而不是全部的实施例。基于本发明中的实施例,本领域普通技术人员在没有做出创造性劳动前提下所获得的所有其他实施例,都属于本发明保护的范围。本发明提供一种车载锂离子动力电池检测设备,通过配件的组合运用,可提高电池检测范围和速度,一体化程度高,请参阅图1-3,包括底板100、电能箱200和支架300;请再次参阅图1,底板100的前侧壁具有合页110,具体的,底板100的前侧壁通过螺丝固定连接有合页110,合页110的活动板通过螺丝固定连接有侧板120,底板100的底部通过螺栓固定连接有滚轮130,侧板120的顶部接触有锂电池140;请再次参阅图1,电能箱200底部与底板100的顶部固定安装,具体的,底板100的顶部通过螺栓固定连接有电能箱200,电能箱200的前侧壁通过螺栓固定连接有容量检测器210和DCR检测器220,电能箱200的顶部通过螺栓固定连接有BMS检测器230、绝缘检测器240和温度检测器250;请再次参阅图1-2,支架300底部与底板100的顶部固定安装,具体的,底板100的顶部焊接支架300,支架300的顶部通过轴杆插接有线板310,线板310的顶部一体成型连接有顶板320,顶板320的右侧壁开设有凹槽,凹槽的圆周内壁镶嵌有圆板330,圆板330的右侧壁开设有圆板孔340,圆板330的材质为绝缘橡胶板;请再次参阅图1,为对确保电能箱200的供电能力,具体的,电能箱200的内腔底部通过螺栓固定连接有蓄电池,蓄电池的底部包括充电接口。请再次参阅图1,为了使支架300具备保护能力和阻燃性,具体的,支架300的材质为空腔不锈钢板,空腔内部填充有膨胀石墨压缩板,膨胀石墨压缩板遇热会膨胀,继而阻隔空气,降低燃烧几率。请参阅图1-2,本发明还提供一种车载锂离子动力电池检测设备的检测方法,该车载锂离子动力电池检测设备的检测方法包括如下步骤:S1:容量检测:利用电容检测器210进行快速充电片段容量检测,片段检测是利用SOC区间的数据快速估算被检测电动汽车可用容量的方法,电动汽车在SOC1至SOC2区间内进行充电,选取的SOC检测区间越广,测试的精度越高,检测区间定为20%SOC区间,在多次测试结果表明,40%~60%SOC区间检测结果对电动汽车可用容量的估算最为接近标定值,故而选取该区间作为快速充电片段检测的SOC区间;充电可用容量检测:将电动汽车自然放电至厂商截止条件,即SOC=0%,静置一段时间后,通过检测设备将电动汽车进行正常充电至厂商截止条件,即SOC=100%,电容检测器210即可通过安时积分获得汽车的充电可用容量,亦可通过电流电压与充电时间的积分获得电池的充电可用能量;放电容量检测:将电动汽车充电至厂商截止条件,即SOC=100%,静置一段时间后,通过电容检测器210将电动汽车进行正常放电至厂商截止条件,即SOC=0%,检测设备即可通过安时积分获得汽车的放电可用容量,亦可通过电流电压与放电时间的积分获得电池的放电可用能量,由于国标规定,充电桩内安装反光二极管导致无法放电,在测试开始前短接反光二极管,未来实际应用检测工作时,应在充电桩内安装放电继电器保护内部电路,对被检测电动车进行放电,需要被检测电动车BMS进入测试模式,在此之前需要更新BMS软件内容,使BMS具备测试模式功能,充电法可用容量检测终点条件,即放电容量检测方法起点条件,放电至单体最低截止电压2.8V即BMS二级警报时停止放电,在停止放电前,切换至小电流再停止放电,保护被测电动车继电器;S2:DCR检测:利用DCR检测器220进行DCR快速检测,在1C倍率下充电,SOC显示值为50%时,DCR检测器220的显示电压和电流分别为U1和I1;在0.1C倍率下充电,充电电流由1C切换成0.1C目的在于快速测试大电流和小电流情况下直流内阻的差异和数值,SOC显示值为50%时,DCR检测器220的显示电压和电流分别为U0.1和I0.1,由于DCR检测器220的显示电压即为电动汽车的电池电压U与DCR上的电压降之和,因此可得如下计算公式:U1=U+DCR·I1(1)U0.1=U+DCR·I0.1(2)(2)式—(2)式,即可算得DCR=(U1–U0.1)/(I1–I0.1);在电池SOC两端,受SOC算法修正影响不作为DCR测试起点,在50%SOC范围内DCR较为稳定,故选取50%SOC作为DCR测试起点,测试循环过程中每次测试间静置30s,利用DCR标准检测,将电动汽车与DCR检测器220连接,放电至厂商截止条件,即SOC=0%,静置30min,充电至BMS显示SOC=50%,将电动汽车进行短时间恒流1C倍率放电,记录第0s,0.1s,2s,10s以及18s对应的电压和电流值,分别记为U0,U0.1,U2,U10,U18以及I0,I0.1,I2,I10,I18;静置40s后,对电动汽车进行短时间恒流0.75C倍率充电,记录第58s,58.1s,60s,68s以及108s累计时间对应的电压和电流值,分别记为U58,U58.1,U60,U68,U108以及I58,I58.1,I60,I68,I108,其中第18s至第58s区间为电流绝对值降至0的区间,第68s至108秒区间为电流绝对值降至0的区间;其中,放电内阻计算表和充电内阻计算表分别为:0.1s放电内阻(U0.1–U0)/(I0.1–I0)2s放电内阻(U2–U0)/(I2–I0)10s放电内阻(U10–U0)/(I10–I0)18s放电内阻(U18–U0)/(I18–I0)全过程放电内阻(U58–U18)/(I58–I18)58.1s充电内阻(U58.1–U58)/(I58.1–I58)60s充电内阻(U60–U58)/(I60–I58)68s充电内阻(U68–U58)/(I68–I58)全过程充电内阻(U108–U68)/(I108–I68)测试中包含充电与放电,目的在于检测电池充电内阻与放电内阻,由于充电过程中热启动等原因,故充电电阻会高于放电电阻,选择1C进行放电,0.75C进行充电;S3:BMS精度检测:利用BMS检测器230检测SOC精度,每隔1秒记录SOCn及累计容量Cn,充电和放电终止时测得累计容量为C0,系统容量Cap参考容量测试结果,检测电流精度,测试过程中获取BMS电流读数,并记录同一时刻BMS检测器230电流读数,检测电压精度,测试过程中获取BMS电压读数,并记录同一时刻检测设备电压读数;S4:外观检测:确保箱体外观良好,未见明显变形及锈蚀;箱体无刺激性气味液体;箱体螺栓无缺失、无松动、无螺纹露出;箱体高、低压线束无金属部分裸露,无明显破损;箱体连接器无明显破损、松脱;箱体的铭牌、安全警示标识清晰可见,无破损;S5:绝缘检查:利用绝缘检测器240在标准充电法和放电法测试系统容量过程中,BMS关闭绝缘检测,由绝缘检测器240完成测试获取绝缘阻值,全程的测试阻值要求电池动力系统与车壳绝缘阻抗>500Ω/V;S6:充电接口温度检查:利用温度检测器250在容量测试过程中实时检测充电枪连接位置的温度,全程记录动态温度数据,统计最高和最低温度,充电插头和车辆底座非金属部分允许温度不超过85℃,端子温升不超过50K。综合以上所述,本发明通过配件的组合运用,可使车载锂离子动力电池在检测过程中实现容量、DCR、BMS、绝缘和充电接口温度的统一检测,只要单人操作即可进行多项的检测工作,简化了检测步骤,检测过程快速有效,降低了检测的时间,加快了工作效率,也有效避免了不同检测设备的选用而造成的经济浪费。虽然在上文中已经参考实施例对本发明进行了描述,然而在不脱离本发明的范围的情况下,可以对其进行各种改进并且可以用等效物替换其中的部件。尤其是,只要不存在结构冲突,本发明所披露的实施例中的各项特征均可通过任意方式相互结合起来使用,在本说明书中未对这些组合的情况进行穷举性的描述仅仅是出于省略篇幅和节约资源的考虑。因此,本发明并不局限于文中公开的特定实施例,而是包括落入权利要求的范围内的所有技术方案。当前第1页1 2 3