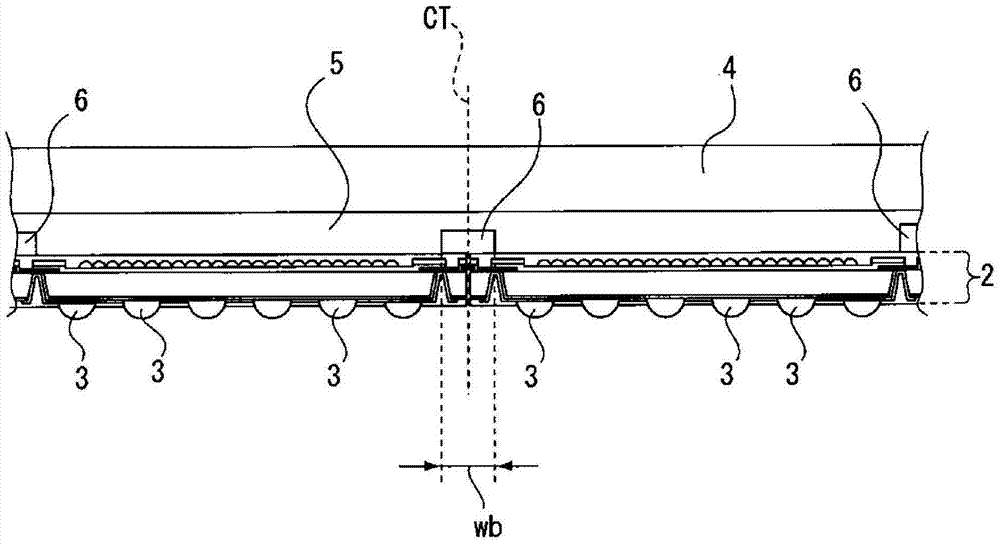
本技术涉及一种半导体器件和一种制造该半导体器件的方法,更具体地,涉及一个用来提供杨氏模量比切割部分中的透明树脂层高的防碎部件并防止切割中造成的半导体层的碎裂的技术领域。
背景技术:日本未经审查专利申请公开号2008-66679是相关技术的一个实例。近年来,固态成像元件(图像传感器)的PKG(封装)已以一种被称为芯片尺寸PKG(以下简称为CSP)的形式被大量生产。这样的CSP不同于由陶瓷或模制树脂形成的相关技术的空腔PKG。例如,随着其中相邻芯片之间的间隙通过晶片上的树脂壁被隔开的空腔配置被形成,传感器单元的保护层(例如,透明玻璃)和Si(硅)晶片被接合,硅通孔(以下简称为TSV)被形成,在与成像面相对的表面上进行重新布线,提供了焊接球,最后执行切割以用于分割。图12的A示出了具有上述空腔配置的CSP的固态成像元件(半导体器件)的配置的一个实例。在具有空腔配置的CSP中,如图12的A所示,半导体层100和保护层102由形成为粘接剂的树脂壁103接合。在这种情况下,由半导体层100、保护层102和树脂壁103划分的内部空间104充满空气。如图中所示,多个焊接球101被形成在半导体层100的成像面的背面侧上。在CSP中,通过TSV形成工艺来形成Deep-RIE或绝缘膜(SiO2)。然而,为了形成用于优异生产率的膜,有必要减小通孔直径与用于形成半导体层100的Si的厚度的纵横比。因此,通过背面研磨(以下简称为BGR)工艺,Si的厚度被减薄到,例如,约50μm至约100μm。然而,由于充满空气的内部空间104被形成在具有如图12的A所示的空腔配置的CSP中,支撑具有约50μm至约100μm的上述厚度的Si(半导体层100)的部分非常小。因此,特别是,在具有大尺寸的图像传感器中,存在一个问题,即,半导体层100会在BGR工艺中被弯曲,或者可能当在BGR工艺之后CSP被安装在基板上时由于产生的应力而相当大的弯曲。图12的B示出了在这种情况下半导体层100的弯曲(翘曲)的图像。当图像传感器的尺寸小时,Si的厚度与宽度的纵横比小。因此,Si的机械硬度比较高,并且很少会发生相当大的翘曲。然而,当图像传感器具有大的尺寸时,Si的厚度与宽度的纵横比很大。因此,随着Si的机械硬度被减弱,容易产生相当大的翘曲。半导体层100被翘曲的事实意味着成像面是弯曲的。因此,存在一个问题,即,由于成像面的弯曲,光学精度劣化。具体地,当发生上述翘曲时,透镜的光学聚焦位置在传感器的中心和边缘处偏离。因此,当在中心处实现聚焦时,存在一个问题,即,在边缘处产生模糊。为了解决由于具有所述空腔配置的CSP而造成的问题,已经提出了图13的A所示的具有无空腔配置的CSP。在具有无空腔配置的CSP中,如图13的A所示,半导体层100和由玻璃形成的保护层102之间的间隙填充有透明粘接剂树脂,并被形成为透明树脂层105。换句话说,相对于具有图12的A所示的空腔配置的前述CSP,内部空间104不是充满空气而是充满透明树脂。在这样的无空腔配置中,不仅Si(半导体层100)单体的机械硬度,而且由例如,约300μm至约800μm的相对厚的玻璃形成的保护层102的硬度被加入到翘曲中,如图12的B所示。因此,由于可以增加机械硬度,因此能够有效地防止发生翘曲。然而,在晶片级,为了实现上述的无空腔CSP结构,形成透明树脂层105的粘接性树脂被接合到整个晶圆表面上的玻璃(保护层102)。因此,在形成透明树脂层105的透明树脂中,引起的膜应力应尽可能小。否则,当Si和玻璃被接合时,可能会产生翘曲。此处,引起的应力小的事实意味着模量通常也降低(软化)。因此,为了实现如图13的A所示的无空腔配置,同时防止产生上述的翘曲,有必要减小形成透明树脂层105的透明树脂的弹性模量(降低杨氏模量)。
技术实现要素:然而,当形成透明树脂层105的透明树脂的弹性模量减小时,如上所述,用于分割的切割时可能产生半导体层100的碎裂(Si碎裂)。图13的B示出了切割时的状态。如图所示,在切割时,预定位置(切割部分)被分割前的层结构中的切割刀片110切割。在切割时,半导体层100不是固定的,且当形成透明树脂层105的透明树脂的弹性模量小时发生摇动。产生所谓的抖振。在传感器活性表面上,即,与透明树脂层105接触的半导体层100的表面上,发生碎裂(破裂)。具有小的弹性模量的透明树脂堵塞切割刀片110并因此剪切力被削弱的事实,是传感器活性表面上的碎裂的原因之一。期望提供一种半导体器件以及一种制造半导体器件的方法,能够防止切割时发生半导体层的抖振或切割刀片的堵塞,以及防止在切割中引起的半导体层的碎裂发生。根据本技术的一个实施方式,提供了一种半导体器件,其是作为固态成像元件的半导体器件,该半导体器件包括半导体层、包括透明材料的保护层,以及密封半导体层和保护层之间的间隙的透明树脂层。杨氏模量比透明树脂层更高的防碎部件被形成为与分割前的层结构的切割部分中的半导体层接触,并且在用于所述分割的所述切割部分中执行切割。此外,根据本技术的一个实施方式的半导体器件的另一种配置,透明树脂层被插入在防碎部件和保护层之间。此外,切割前的防碎部件的宽度被设置为在用于切割防碎部件的切割刀片的厚度B的1.5倍至3.0倍的范围内,而分割后的防碎部件的宽度被设置为在(1.5B/2-B/2)至(3B/2-B/2)的范围内。此外,透明树脂层的杨氏模量被设置为等于或小于1.5Gpa,而防碎部件的杨氏模量被设置为等于或大于2.5Gpa。此外,防碎部件包括树脂。此外,防碎部件包括任何硅氧烷基树脂、丙烯酸基树脂和环氧基树脂。此外,防碎部件的树脂材料包含填充物。此外,保护层包含玻璃。根据本技术的一个实施方式,提出了以下方法,作为一种制造半导体器件的方法。即,根据本技术的一个实施方式,提供了一种制造半导体器件的方法,其为一种制造半导体器件作为固态成像元件的方法,该方法包括,形成分割前的层结构,其中,半导体层和包括透明材料的保护层之间的间隙以晶片级由透明树脂所密封,以使杨氏模量比透明树脂层高的防碎部件被形成为与用于所述分割的切割部分中的半导体层接触;以及在切割部分中对所述分割前的层结构进行切割,所述切割部分在形成所述分割前的层结构的步骤中形成。根据本技术的实施方式,半导体器件具有一种配置,其中,半导体层和保护层之间的间隙被透明树脂密封,如在相关技术的无空腔配置那样。即,在这方面,能够防止在背面研磨(BGR)工艺中引起的半导体层的翘曲发生。此外,根据本技术的实施方式,杨氏模量比透明树脂层高的防碎部件被形成为与分割前的层结构的切割部分中的半导体层接触。因此,与其中具有相对低的杨氏模量的透明树脂层与半导体层接触的相关技术的无空腔配置相比,通过形成具有更高的杨氏模量的防碎部件以与半导体层接触,能够防止切割时半导体层的抖振(摇动),并防止切割刀片的堵塞。结果,能够有效地防止切割中引起的半导体层的碎裂的产生。根据本技术的上述实施方式,在被设计为通过用透明树脂层密封保护层和半导体层之间的间隙来防止发生在BGR工艺中引起的半导体层的翘曲的用作固态成像元件的半导体器件中,可以防止半导体层的抖振的发生,并防止在切割时切割刀片的堵塞,因此可以有效地防止切割中引起的半导体层的碎裂。附图说明图1为示出了根据一个实施方式的半导体器件的截面配置的示图;图2为示出了在分割半导体器件的先前的步骤中的分割前的层结构的截面配置的示图;图3的A和B为示出了相关技术的无空腔配置的第一步骤的切割状态的示图;图4的A和B为示出了相关技术的无空腔配置的第二步骤的切割状态的示图;图5的A和B为示出了根据所述实施方式的分割前的层结构中的第一步骤的切割状态的示图;图6的A和B为示出了根据所述实施方式的分割前的层结构中的第二步骤的切割状态的示图;图7为示出了其中包含填充物的防碎部件的示图;图8为示出了关于碎片防止部件的弹性模量和碎片大小之间的关系的实验的图示结果的示图;图9的A至C为示出了根据所述实施方式的制造半导体器件的方法的示图;图10为示出了如图9的A至C中的根据实施方式的半导体器件的制造方法的示图;图11是示出了使用根据本实施方式的半导体器件的成像光学单元的配置的一个实例的截面图;图12的A和B为示出了根据相关技术的具有空腔配置的固态成像元件(半导体器件)的配置和问题的实例的示图;图13的A和B示出了根据相关技术的具有无空腔配置的固态成像元件(半导体器件)的配置和问题的实例的示图。具体实施方式在下文中,将参考附图详细描述本公开的优选实施方式。请注意,在本说明书和附图中,用相同的参考标号表示具有基本相同的功能和结构的结构元件,并且省略对这些结构元件的重复解释。在下文中,对与本技术有关的实施方式进行说明。将按以下顺序进行描述。<1.根据实施方式的半导体器件><2.根据实施方式的制造半导体器件的方法><3.根据实施方式的使用固态成像元件的成像光学单元的配置实例><4.变形例><1.根据实施方式的半导体器件>图1为示出了根据本技术的实施方式的半导体器件1的截面配置的示图。首先,假设根据本实施方式的半导体器件1为用作固态成像元件的半导体器件。在附图中,半导体层2例如,用作固态成像元件的传感器单元。虽然没有被详细地示出,但是例如,多个光接收元件或用于R、G和B的微型滤色器形成在半导体层2的表面(成像面)侧上。保护层4形成在半导体层2的表面侧(正面侧)上。保护层4被形成以保护半导体层2的成像面,并使用具有相对高的硬度的材料。在这个实例中,透明玻璃被用于保护层4。根据本实施方式的半导体器件1具有这样一种配置作为整体配置,其中,半导体层2和保护层4被具有相对较小的杨氏模量的透明树脂(透明粘接树脂)接合,如图13的A和B的上述无空腔配置那样。由被配置用于接合的透明树脂形成的层被称为透明树脂层5。使透明树脂层5具有低杨氏模量(导致弹性模量小的)的目的与根据相关技术的无空腔配置的情况相同。根据本实施方式的半导体器件1以芯片尺寸PKG(以下简称为CSP)的上述形式被成批生产,所述芯片尺寸PKG不同于由陶瓷或模制树脂形成的相关技术的空腔PKG。半导体器件1以这样的方式形成,即,保护层4和传感器单元的Si晶片(半导体层2)被接合,在半导体层2中形成硅通孔(以下简称为TSV),在与成像面相对的表面上进行重新布线,设置如图中所示的多个焊接球3,并且最后执行切割以用于分割。在根据本实施方式的半导体器件中,在通过执行用于分割的切割而形成的半导体器件的侧壁表面的内侧上的最外围区域内,由杨氏模量比透明树脂层5高的材料(更大的弹性模量)形成的防碎部件6被形成为与半导体层2接触,如图中所示。从下面的描述中将会理解,图中所示的防碎部件6变成其中在分割之前以晶片级执行切割的切割部中的片段。换句话说,通过预先以晶片级形成宽度充分大于切割刀片的厚度的防碎部件6并对其中形成了防碎部件6的部分执行切割来分割这种情况下的半导体器件1。从前面的描述可以理解,根据本实施方式的图1所示的半导体器件1在其中进行切割的部分中具有空腔配置,并具有其中由透明树脂进行接合作为无空腔配置的整体配置。也就是说,从这个观点来看,半导体器件1的配置可以说是一种空腔配置和无空腔配置的混合配置(混合无空腔配置)。图2示出了分割前的层结构的截面配置,其为分割半导体1的前一步骤中的多个半导体器件1的集合。如上所述,在分割前的层结构中,与半导体层2接触的防碎部件6被形成在其中执行用于分割的切割的切割部分(在图中由CT表示)中。如图2所示,分割前的层结构上的防碎部件6的宽度wb,即,切割之前的防碎部件6的宽度wb,可以被设置为小于上述图12中所示的空腔配置的树脂壁103的宽度w1。在图12的空腔配置中,必须确保Si(半导体层100)和玻璃(保护层102)通过空腔的树脂壁103粘接的粘接强度。因此,必须确保宽度w1在一定程度上(例如,至少为0.3mm或以上)。然而,在图2的配置中,没有必要扩大防碎部件6的宽度wb以确保其中半导体层2和保护层4整体由无空腔侧上的透明树脂层5粘接的配置的粘接力。因此,宽度wb可被设置为切割刀片的厚度+α。宽度wb为至少约0.1mm就足够了。因此,当宽度wb可以被设置为小时,应力低。此外,由于不执行与保护层4的接合,防碎部件6可能不具有粘接力。由于使用具有较高弹性的透明树脂进行接合,所以防碎部件6可能不会有足够的弹性来吸收材料的高度、翘曲和平坦度的变化。从该观点来看,防碎部件6的弹性模量可以被设置为高的。在此实例中,例如,树脂被用作防碎部件6。当透明树脂层5的弹性模量高时,在不设置防碎部件6的情况下也可以抑制切割时的碎裂。然而,由于上述翘曲的问题,透明树脂层5的弹性模量必须被设置为是低的。在本实施方式中,切割时的碎裂被设计为通过提供能够增加对应于切割部分的弹性模量的树脂而被抑制。如下面将描述的那样,上述用于分割的切割以两个分离的工艺进行,即,在正面侧上进行切割的工艺和从背面侧进行切割的工艺。将参照图3的A至图4的B来描述相关技术的无空腔配置中的两个步骤的切割状态和为什么由于切割而产生碎裂的原因。在这种情况下,如图3的A所示,首先,通过从分割前的层结构的正面侧(在该图的情况下,在保护层102的一侧)插入用于玻璃切割的切割刀片111来进行切割。如图3的B所示,当切割刀片111到达透明树脂层105时,从正面侧的切割(第一步骤的切割)结束。接着,用于Si(硅)切割的切割刀片112从其中第一步骤的切割结束的分割前的层结构的背面侧插入,如图4的A所示,半导体层100和透明树脂层105的剩余部分被切割,如图4的B所示。通过在分割前的层结构的多个预定部分(切割部分)中进行切割,进行半导体器件的分割。在这种情况下,传感器活性表面上的上述碎裂在从背面侧切割时发生,如图4的A和B所示。具体而言,在从背面侧切割时,只有具有小弹性模量的透明树脂存在于相关技术的无空腔配置中的切割部分附近。因此,当切割刀片112旋转时,半导体层100可能不是固定的,从而可能会抖振(被摇动)(附图中的X)。因此,破裂(附图中的Y)可能会出现在传感器活性表面上(其为与半导体层100中的透明树脂层表面105接触的表面)。在相关技术的无空腔配置中,在从背面侧切割时,具有小弹性模量的透明树脂会很容易地堵塞切割刀片112,由于堵塞,因此切割刀片112的剪切力会被减弱。这一点也是在传感器活性表面发生碎裂的原因之一。图5的A至图6的B示出了以同样的方式对根据该实施方式的分割前的层结构执行两部分割的情况。在该实施方式的情况下,首先,通过从保护层4(图5的A)的正面侧插入用于玻璃切割的切割刀片111,向第一步骤那样执行从正面侧的切割。此时,如图5的A的放大图所示,当切割刀片111到达防碎部件6时,第一步骤的切割结束。图5的B示出了第一步骤的切割结束时分割前的层结构的状态。当第一步骤的切割结束时,防碎部件6的一部分处于切割状态,如图所示。如图6的A所示,通过从半导体层2的背面侧插入用于Si切割的切割刀片112,执行第二步骤中的从后表面侧的切割。如图6的B所示,半导体层2与防碎部件6的其余部分通过此切割被切断。在本实施方式中,在图6的A和B所示的切割时,具有高杨氏模量的防碎部件6与切割部分附近的半导体层2接触。因此,在这种情况下,即使当切割刀片112旋转时,半导体层2可以是固定的。因此,如上所述,能够有效地防止半导体层2的抖振的发生。在本实施方式的配置中,当半导体层2被切割刀片112切割时,具有小弹性模量的透明树脂没有与切割刀片112接触。此外,能够防止切割刀片112的上述堵塞的发生。从这个观点出发,在本实施方式中,可以有效地防止分割中引起的传感器活性表面上的碎裂。例如,甚至当仅通过从正面侧或背面侧的切割进行分割时,同样也可以同样地获得这样的碎裂防止效果。在这个实例中,如上面的图1和2中所示,防碎部件6被形成为不与相对硬的保护层4接触。换句话说,透明树脂层5被配置为在防碎部件6和保护层4之间。当防碎部件6与保护层4接触时,几乎没有理由使用具有小弹性模量的透明树脂接合半导体层2和保护层4。因此,可能无法获得防止在接合时引起的翘曲的效果。因此,通过不使防碎部件6与保护层4接触,能够提高防止由于接合造成的翘曲的效果。从避免碎裂的观点来看,防碎部件6的弹性模量优选为大。在这个实例中,树脂被用作防碎部件6。然而,在这种情况下,如图7所示,通过包含填充物6a以进一步硬化树脂,可以增加模量。随着防碎部件6的模量增加(杨氏模量增加),能够强有力地防止切割刀片112的旋转引起的半导体层2中抖振或切割刀片112的堵塞发生,如上所述。因此,可以提高切割特性并强有力地防止破裂的发生。图8为示出了防碎部件6的模量和碎片大小之间的关系的一个实验的图示结果的示图。在实验中,通过使用具有不同模量的三种防碎部件6,多次执行切割来测量每个碎片的大小。在图中,三种防碎部件6的每一个的碎片大小的测定结果,由两个●标记和一个▲标记表示。两个●标记表示每个碎片大小的最大值和最小值,而▲标记表示碎片大小的平均值。从图8所示的实验结果来看,可以理解的是,通过增加防碎部件6的模量,可以进一步防止碎裂的发生。透明树脂层5和防碎部件6的模量(杨氏模量)最好被设置为至少如下。即,透明树脂层5的模量等于1.5Gpa(千兆帕斯卡),而防碎部件6的模量等于或大于2.5Gpa。在下文中,将给出透明树脂层5和防碎部件6的材料的实例。例如,硅氧烷基粘接剂或丙烯酸基粘接剂可以被用作透明树脂层5的材料。也可以用环氧基粘接剂、酯基粘接剂或聚酰亚胺基粘接剂。当使用这种材料时,杨氏模量如下所示。硅氧烷基粘接剂:0.1Gpa至0.8Gpa丙烯酸基粘接剂:0.1Gpa至0.5Gpa环氧基粘接剂:1.8Gpa至2.5Gpa酯基粘接剂:0.1Gpa至0.5Gpa聚酰亚胺基粘接剂:0.1Gpa至0.5Gpa关于由树脂形成的防碎部件6,例如,可以使用光敏硅氧烷基粘接剂、光敏丙烯酸基粘接剂或光敏环氧基粘接剂。通过这些材料获得的杨氏模量如下所示。光敏硅氧烷基粘接剂:0.3Gpa至0.7Gpa光敏丙烯酸基粘接剂:2.0Gpa至3.5Gpa光敏环氧基粘接剂:1.8Gpa至3.0Gpa当使用硅氧烷基树脂时,模量优选地通过包含填充物6a而增加。丙烯酸基粘接剂加上环氧系粘接剂的混合树脂可以被用于由树脂形成的防碎部件6。此外,考虑到耐热性和耐化学性,优选选择实际的材料。顺便提及,如上所述,防碎部件6的宽度(wb)可以被设置为至少大于切割防碎部件6的切割刀片112的厚度。然而,当防碎部件6的宽度wb和切割刀片112的厚度之间的差过小时,可能会导致切割性能的劣化。例如,在切割时半导体层2的阻尼特性可能会减小,或者刀片的堵塞发生的概率可能会增加。因此,防碎部件6的宽度wb最好被设定为在切割刀片112的厚度的约1.5倍至约3.0倍的范围内。当防碎部件6的宽度wb被设置为切割刀片112的厚度的1.5倍至3.0倍时,如上所述,如图1所示,通过切割进行的分割后的半导体器件1中的防碎部件6的宽度wr,如在图6的B中,考虑到切割,是在(1.5B/2-B/2)至(3B/2-B/2)的范围内。在这里,“B”表示切割刀片112的厚度。<2.根据实施方式的制造半导体器件的方法>接着,将参照图9的A至图10对根据本实施方式的如上所述的半导体器件1的制造方法进行说明。在图9的A至C中,图9的A是示出了作为多个半导体层2的集合的硅晶片2'的透视图和截面图。在根据实施方式的制造方法中,防碎部件6形成在硅晶片2'上,如图9的B所示。从前面的描述可以理解,防碎部件6形成在硅晶片2'的用于分割的切割部分上。因此,形成了格子状,如图所示。在这个实例中,由于光敏树脂粘接剂被用作防碎部件6的材料,图9的B所示的形成防碎部件6的工艺是通过曝光和显影图案化光敏树脂粘接剂来进行的。在防碎部件6形成后,如图9的C所示,在等于或小于透明树脂5'的交联温度高温下,作为用于形成透明树脂层5的材料的透明树脂5'被真空层压在硅晶片2'上,防碎部件6形成在其中。通过在真空状态下层压这样的透明树脂5',如图9的C的剖视图所示,透明树脂5'可以以保形方式暂时附着到防碎部件6形成在其中的硅晶片2'的表面形状上。在透明树脂5'被层压后,如图10所示,作为保护层4的材料的玻璃材料4',在真空状态下被加压粘接在透明树脂5'被层压在其上的硅晶片2'上,同时被加热。因此,通过在真空状态下对玻璃材料4'进行加压,根据防碎部件6形成在其中的位置的图9的C的层压工艺中的透明树脂5'中形成的阶梯部分被平面化。此时,通过上述加压,透明树脂5'流向高的部分或低的部分,并且因此玻璃材料4'最终可以被接合而没有空隙(气泡)。在其中作为树脂粘接剂的透明树脂5'的交联没有太多的进展的范围内,接合工艺中的加热温度最好是尽可能高。这是因为由于透明树脂5'被熔融并且因此很容易被移动的事实所以可以更很好地防止空隙的混合。可以通过至少完成图10中所示的接合工艺并以晶片级用透明树脂5'密封半导体层2和保护层4之间的间隙,来获得其中与半导体层2接触的防碎部件6形成在切割部分中的作为分割之前的层结构的结构。虽然参照附图的描述被省略,但是通过图中10所示的接合工艺后的加热工艺执行透明树脂5'的交联。光敏树脂粘接剂也可以被用作透明树脂5'。在这种情况下,通过曝光执行交联。在透明树脂5'的交联后,半导体层2的背面侧通过背面研磨(BGR)工艺被减薄,TSV被处理,并在背面上进行重新布线。此后,作为最终工艺,通过由切割部分对经过上述工艺的分割前的层结构进行切割来分割半导体器件1。从上述的制造工艺可以理解,根据本实施方式的混合无空腔配置可以相对容易地实现,并且添加了较少的工艺。因此,在不增加成本的情况下,具有相对较大的尺寸的传感器CSP可以以较低的成本来实现。<3.使用根据实施方式的固态成像元件的成像光学单元的配置实例>图11是示出了使用根据本实施方式的半导体器件1(固态成像元件)的成像光学单元10的配置的实例的截面图。如图所示,这种情况下的成像光学单元10被安装在透镜镜筒(透镜筒)11中,以便容纳多个透镜。具体地,在这种情况下的成像光学单元10中,透镜12被安装为使得透镜12的一部分相对于在物体侧的透镜镜筒11形成的开口部分突出。透镜13和14被安装为比透镜12更接近成像面侧。用作根据本实施方式的半导体器件1的固态成像元件被布置为占据在透镜镜筒11的成像面侧上形成的开口部分。用作半导体器件1的固态成像元件作为CSP的尺寸小,因此有助于成像光学单元10的小型化。<4.变形例>已对本技术的实施方式进行了说明,但是本技术的实施方式不局限于上述的具体实例。可以考虑各种变形例。例如,在前面的描述中,防碎部件6已经由树脂形成。然而,例如,无机材料,如SiO2或SiN也可以被使用。在这种情况下,形成防碎部件6的工艺通过形成并图案化无机材料来进行。在前面的描述中,保护层4已由玻璃形成。代替玻璃,保护层4可以由另一种透明材料例如透明树脂形成。例如,考虑到以下情况,保护层4可以由Si基材料形成。在图12所示的空腔配置中,必要的会聚率(condensingpower)被配置为通过片上透镜(OCL)的折射率“折射率=约1.6”和内部空间104中的空气的“折射率=1”之间的差来获得。在本技术的实施方式中,由于保护层4和传感器之间的间隙被填充以透明树脂层5(例如,折射率=约1.5),透镜的会聚率会被削弱。因此,担心传感器的灵敏度可能会降低。因此,考虑到这一点,用作OCL的保护层4由具有高折射率(折射率=约1.7至约2.1)的诸如SiN的材料形成。在以上描述中,例如,其中防碎部件6被形成为接触切割部分中的半导体层2的分割前的层结构,已经通过在半导体层2的侧面上形成防碎部件6,然后在一个晶片级的任务中用透明树脂5'粘接保护层4(图9的A到图10)而形成。然而,其中形成了防碎部件6的分割前的层结构可以通过在保护层4的侧面上形成防碎部件6,然后用透明树脂5'将保护层4粘接到半导体层2的侧面上而被制造。至于图9的A到图10,在半导体层2的侧面上形成防碎部件6的方法是有利的,在于防碎部件6很容易与半导体层2接触。此外,本技术也可以被配置如下。(1)1.一种半导体器件,包括:半导体层;保护层,包括透明材料;以及透明树脂层,密封半导体层和保护层之间的间隙,其中,杨氏模量比透明树脂层高的防碎部件被形成为与分割前的层结构的切割部分中的半导体层接触,并且在用于所述分割的所述切割部分中执行切割。(2)根据(1)的半导体器件,其中,透明树脂层被插入在防碎部件和保护层之间。(3)根据(1)或(2)的半导体器件,其中,切割前的防碎部件的宽度被设置为在用于切割防碎部件的切割刀片的厚度B的1.5倍至3.0倍的范围内,以及其中,分割后的防碎部件的宽度被设置为在(1.5B/2-B/2)至(3B/2-B/2)的范围内。(4)根据(1)至(3)中任一项的半导体器件,其中,透明树脂层的杨氏模量被设置为等于或小于1.5Gpa,以及其中,防碎部件的杨氏模量被设置为等于或大于2.5Gpa。(5)根据(1)至(4)中任一项的半导体器件,其中,防碎部件包括树脂。(6)根据(5)的半导体层,其中,防碎部件包括任何硅氧烷基树脂、丙烯酸基树脂和环氧基树脂。(7)根据(5)或(6)的半导体器件,其中,防碎部件的树脂材料包含填充物。(8)根据(1)至(7)中的任一项的半导体器件,其中,保护层包括玻璃。(9)一种制造半导体器件的方法,该方法包括:形成分割前的层结构,其中,半导体层和包括透明材料的保护层之间的间隙以晶片级被透明树脂密封,从而使得杨氏模量比透明树脂层高的防碎部件被形成为与分割的切割部分中的半导体层接触;在切割部分中对分割前的层结构进行切割,所述切割部分在形成分割前的层结构的步骤中形成。本公开包含的主题涉及于2012年8月28日提交至日本专利局的日本在先专利申请JP2012-187927中所公开的主题,其全部内容通过引用结合于此。