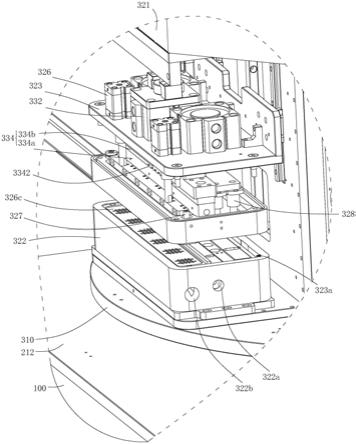
[0001]
本实用新型涉及电芯制造的技术领域,特别是涉及一种抽真空封装模具及设备、电芯制造系统。
背景技术:[0002]
电芯加工工序包括初定位、抽真空封装、切料、烫边、切边、弯折和烫边等工序。由于电芯中含有有毒有害物质,在完成注液工序后需要对锂电池进行封装,在注完电解液经过静置处理后,需要先将没有被电芯吸收的多余的电解液及生产过程中产生的气体抽出,然后在真空环境下将铝塑膜加热加压实现电芯的真空封装,以防止锂电池在投入市场上出售时不会出现漏液的情况。
[0003]
其中,抽真空封装工序作为电芯加工工序的关键工序,决定了电芯制造的良率是否达标。当抽真空封装工序对应的抽真空封装模具的工作过程为:首先刺破电芯,然后将多余的电解液及生产过程中产生的气体抽出,即进行抽真空操作,最后在真空环境下对电芯进行热封。
[0004]
然而,传统的抽真空封装模具在刺破电芯时,仅能让电芯内多余的电解液及电芯内的产生的气体通过刺破孔自然漏出,使电芯内排气的效率较低,甚至存在电芯内气体还没完全排出就被热封的情形。
技术实现要素:[0005]
本实用新型的目的是克服现有技术中的不足之处,提供一种解决上述技术问题的抽真空封装模具及设备、电芯制造系统。
[0006]
本实用新型的目的是通过以下技术方案来实现的:
[0007]
一种抽真空封装模具,包括:安装架;第一模座,所述第一模座设于所述安装架,所述第一模座开设有第一连接孔;第二模座,所述第二模座盖设于所述第一模座,且所述第二模座与所述第一模座之间围成容纳腔,所述第一连接孔与所述容纳腔连通,所述容纳腔的内壁上凸设有放置台;开合驱动组件,所述开合驱动组件设于所述安装架,且所述开合驱动组件的动力输出端与所述第二模座连接,所述开合驱动组件驱动所述第二模座相对于所述第一模座运动;刺破机构,所述刺破机构部分位于所述容纳腔内,所述刺破机构用于刺破电芯;热封机构,所述热封机构邻近所述刺破机构设置;压紧机构,所述压紧机构和所述刺破机构分别位于所述热封机构的两侧,所述压紧机构包括伸缩驱动件、压紧组件以及支撑板组件;所述伸缩驱动件设于所述第二模座,所述伸缩驱动件的动力输出端与所述压紧组件连接,以驱动所述压紧组件朝靠近或远离所述支撑板组件的方向运动;所述压紧组件和所述支撑板组件均位于所述第二容置槽内,所述压紧组件与所述支撑板组件相对设置;所述放置台用于放置所述支撑板组件,且所述支撑板组件用于支撑电芯;抽真空组件,所述抽真空组件与所述第一连接孔连通,所述抽真空组件用于对所述容纳腔进行抽真空。
[0008]
一种抽真空封装设备,包括固定座和上述任一实施例所述的抽真空封装模具,所
述安装架与所述固定座连接。
[0009]
一种电芯制造系统,包括机架、设于所述机架的输送装置及上述的抽真空封装设备,所述固定座与所述机架连接,所述输送装置用于在所述承载板上取出或放置电芯。
[0010]
与现有技术相比,本实用新型至少具有以下优点:
[0011]
1、由于开合驱动组件驱动第二模座朝靠近第一模座的方向运动,确保第二模座在抽真空组件抽真空时与第一模座围成的容纳腔的紧密性,使抽真空组件更好地对容纳腔进行抽真空,并使第二模座在电芯的抽真空封装工艺完毕后离开第一模座,以取出封装后的电芯;2、在封装时,首先开合驱动组件驱动第二模座相对于第一模座运动至与第一模座抵接,然后伸缩驱动件驱动压紧组件朝靠近支撑板组件的方向运动,直至压紧组件抵接于支撑板组件上的电芯,使电芯压紧定位于支撑板组件与压紧组件之间,避免电芯运动而影响后续的刺破精度;然后刺破机构刺破电芯,没有被电芯吸收的多余的电解液和产生的废气均通过电芯的刺破处排出,同时抽真空组件通过第一连接孔对容纳腔进行抽真空,同时将电芯静置过程中产生的气体抽出;最后热封机构对电芯进行热封,实现电芯的抽真空封装;3、由于在电芯刺破时,压紧组件将电芯压紧于支撑板组件,提高了电芯内排气的效率,同时确保电芯内气体完全排出。
附图说明
[0012]
为了更清楚地说明本实用新型实施例的技术方案,下面将对实施例中所需要使用的附图作简单地介绍,应当理解,以下附图仅示出了本实用新型的某些实施例,因此不应被看作是对范围的限定,对于本领域普通技术人员来讲,在不付出创造性劳动的前提下,还可以根据这些附图获得其他相关的附图。
[0013]
图1为一实施例中电芯制造系统的示意图;图2为图1所示电芯制造系统的局部示意图;图3为图1所示电芯制造系统的抽真空封装设备的另一视角的局部示意图;图4为图3所示抽真空封装设备的局部示意图;图5为图3所示抽真空封装设备的另一视角的局部示意图;图6为图5所示抽真空封装设备的局部爆炸示意图;图7为图5所示抽真空封装设备的局部示意图;图8为图7所示抽真空封装设备的热封组件的局部示意图;图9为图3所示电芯制造系统的另一局部示意图;图10为图9所示电芯制造系统的局部示意图;图11为图1所示电芯制造系统的另一视角的局部示意图;图12为图1所示电芯制造系统的局部示意图;图13为图1所示电芯制造系统的另一局部示意图;图14为图1所示电芯制造系统的再一局部示意图;图15为图14所示电芯制造系统的a处局部示意图。
具体实施方式
[0014]
为了便于理解本实用新型,下面将参照相关附图对本实用新型进行更全面的描述。附图中给出了本实用新型的较佳实施方式。但是,本实用新型可以以许多不同的形式来实现,并不限于本文所描述的实施方式。相反地,提供这些实施方式的目的是使对本实用新型的公开内容理解的更加透彻全面。需要说明的是,当元件被称为“固定于”另一个元件,它可以直接在另一个元件上或者也可以存在居中的元件。当一个元件被认为是“连接”另一个元件,它可以是直接连接到另一个元件或者可能同时存在居中元件。本文所使用的术语“垂直的”、“水平的”、“左”、“右”以及类似的表述只是为了说明的目的,并不表示是唯一的实施
方式。除非另有定义,本文所使用的所有的技术和科学术语与属于本实用新型的技术领域的技术人员通常理解的含义相同。本文中在本实用新型的说明书中所使用的术语只是为了描述具体的实施方式的目的,不是旨在于限制本实用新型。本文所使用的术语“及/或”包括一个或多个相关的所列项目的任意的和所有的组合。
[0015]
如图1与图2所示,一实施例的电芯制造系统10包括机架100、设于机架100的输送装置200和抽真空封装设备300。同时参见图3和图4,抽真空封装设备300包括固定座310和抽真空封装模具320。固定座310与机架100连接,抽真空封装模具320设于固定座310上。如图3和图5所示,具体地,抽真空封装模具320包括安装架321、第一模座322、第二模座323、开合驱动组件324、刺破机构326、热封机构330、压紧机构328以及抽真空组件(图未示)。安装架321与固定座310连接。如图3和图4所示,第一模座322设于安装架321,即第一模座322与安装架321连接。第一模座322开设有第一连接孔322a。第一模座322与第二模座323相对设置,第二模座323盖设于第一模座322,且第二模座323与第一模座322之间围成容纳腔323a。如图6所示,第一连接孔322a与容纳腔323a连通,容纳腔323a的内壁上凸设有放置台3232。开合驱动组件324设于安装架321,且开合驱动组件324的动力输出端与第二模座323连接,开合驱动组件324驱动第二模座323相对于第一模座322运动,使开合驱动组件324驱动第二模座323朝靠近或远离第一模座322的方向运动。在本实施例中,第二模座323滑动设置于安装架321,使开合驱动组件324驱动第二模座323更好地相对于安装架321滑动,从而使第二模座323朝靠近或远离第一模座322的方向更平稳地运动。可以理解,在其他实施例中,第二模座323也可以不与安装架321滑动连接,即第二模座323悬空安装于开合驱动组件324的动力输出端。
[0016]
如图4所示,刺破机构326部分位于容纳腔323a内,刺破机构326用于刺破电芯,使没有被电芯吸收的多余的电解液及产生的废气排出。热封机构330邻近刺破机构326设置。压紧机构328和刺破机构326分别位于热封机构330的两侧。如图5至图7所示,压紧机构328包括伸缩驱动件328a、压紧组件328b以及支撑板组件328c。伸缩驱动件328a设于第二模座323,伸缩驱动件328a的动力输出端与压紧组件328b连接,以驱动压紧组件328b朝靠近或远离支撑板组件328c的方向运动。压紧组件328b和支撑板组件328c均位于第二容置槽3233内,压紧组件328b与支撑板组件328c相对设置。放置台3232用于放置支撑板组件328c,且支撑板组件328c用于支撑电芯。输送装置200用于在支撑板组件328c上取出或放置电芯。在本实施例中,支撑板组件328c邻近热封机构330设置。抽真空组件与第一连接孔322a连通,抽真空组件用于对容纳腔323a进行抽真空。
[0017]
上述的抽真空封装模具320及设备、电芯制造系统,由于开合驱动组件324驱动第二模座323朝靠近第一模座322的方向运动,确保第二模座323在抽真空组件抽真空时与第一模座322围成的容纳腔323a的紧密性,使抽真空组件更好地对容纳腔323a进行抽真空,并使第二模座323在电芯的抽真空封装工艺完毕后离开第一模座322,以取出封装后的电芯;在封装时,首先开合驱动组件324驱动第二模座323相对于第一模座322运动至与第一模座322抵接,然后伸缩驱动件驱动压紧组件朝靠近支撑板组件328c的方向运动,直至压紧组件抵接于支撑板组件328c上的电芯,使电芯压紧定位于支撑板组件328c与压紧组件之间,避免电芯运动而影响后续的刺破精度;然后刺破机构326刺破电芯,没有被电芯吸收的多余的电解液和产生的废气均通过电芯的刺破处排出,同时抽真空组件通过第一连接孔322a对容
纳腔323a进行抽真空,同时将电芯静置过程中产生的气体抽出;最后热封机构330对电芯进行热封,实现电芯的抽真空封装;由于在电芯刺破时,压紧组件将电芯压紧于支撑板组件328c,提高了电芯内排气的效率,同时确保电芯内气体完全排出。
[0018]
如图7所示,在其中一个实施例中,伸缩驱动件328a包括伸缩气缸3282和固定板3284,伸缩气缸3282安装于第二模座323,第二模座323开设有与容纳腔323a连通的第二穿设孔(图未示),且伸缩气缸3282的动力输出端穿设于第二穿设孔并与压紧组件328b连接,使伸缩气缸3282通过固定板3284带动压紧组件328b运动。可以理解,在其他实施例中,伸缩驱动组件不仅限于是气缸驱动组件,还可以是电机驱动组件。
[0019]
如图5和图7所示,进一步地,压紧组件328b包括第一导向柱3283和压板件3285,第一导向柱3283滑动设置于固定板3284,且第一导向柱3283与压板件3285连接。压板件3285与第一导向柱3283连接,且压板件3285与支撑板组件328c对应设置,使压板件3285将电芯压紧抵接于支撑板组件328c,在第一导向柱3283的导向作用下,压板件3285抵接于支撑板组件328c的精度较高,实现电芯更好地定位于支撑板组件328c。此外,当压板件3285随固定板3284相对于支撑板组件328c运动至与电芯抵接的位置时,压板件3285随第一导向柱3283相对于固定板3284滑动,避免压板件3285刚性抵接于电芯而压坏电芯的问题,也就是说,第一导向柱3283相对于压板件3285滑动设置的方式使压板件3285具有较好的缓冲作用。
[0020]
如图6和图7所示,进一步地,第一导向柱3283包括导向杆3284和第一导柱套3286,第一导柱套3286套设于导向杆3284,且第一导柱套3286与固定板3284连接,导向杆3284的一端与压板件3285连接,使第一导向柱3283与压板件3285连接。固定板3284开设有伸缩孔3287,导向杆3284穿设于伸缩孔3287内并与固定板3284滑动连接,使导向杆3284分别相对于第一导柱套3286和固定板3284滑动连接,进而使导向杆3284更加平稳地滑动。进一步地,压板件3285与固定板3284平行设置,且压板件3285邻近固定板3284的一面与导向杆3284连接,由于导向杆3284的一端与压板件3285连接,且导向杆3284分别与第一导柱套3286和固定板3284滑动连接,使压板件3285相对于固定板3284平行运动,进而使压板件3285更好地压平支撑板组件328c上的电芯,实现电芯在刺破机构326刺破之后更好地排液和排气。进一步地,压板件3285包括压板件本体328d和弹性垫层328e,压板件本体328d与第一导向柱3283连接,弹性垫层328e设于压板件本体328d的背离第一导向柱3283的一面,使压板件3285抵接于电芯的部位具有较好的弹性及缓冲性,减小了压板件3285压坏电芯的几率。在本实施例中,弹性垫层328e为弹性胶层。
[0021]
如图6和图7所示,进一步地,支撑板组件328c包括第二导向柱3281、支撑板3288和调节板3289。放置台3232开设有导向孔3233,第二导向柱3281穿设于导向孔3233内并与放置台3232滑动连接,使第一导向柱3283较好地相对于放置台3232滑动。支撑板3288设于放置台3232邻近压紧组件的一面,且支撑板3288与第二导向柱3281连接,使支撑板3288随第二导向柱3281相对于放置台3232滑动,同时使支撑板3288较好地支撑电芯。调节板3289连接于支撑板3288的远离放置台3232的一面,使电芯定位于调节板3289与支撑板3288连接处所形成的槽内。进一步地,支撑板3288包括支撑板本体3292及导热板3294,支撑板本体3292分别与第二导向柱3281和调节板3289连接,支撑板本体3292开设有连接槽329a,导热板3294位于连接槽329a内并与支撑板本体3292连接,导热板3294与热封机构330抵接,使热封机构330产生的热量通过导热板3294传导至支撑板本体3292,如此热封机构330及导热板
3294的热量均能够作用于电芯,进而使抽真空封装模具320更好地对电芯进行热封。
[0022]
如图6所示,在其中一个实施例中,导热板3294开设有第一避位槽329b,第一避位槽329b的底部与支撑板本体3292的背离第二导向柱3281的一面平齐,使电芯更好地放置于导热板3294和支撑板本体3292上,同时增大了支撑板3288放置电芯的表面积。在本实施例中,第一避位槽329b的横截面呈l型,使导热板3294与热封机构330接触的面积较大,同时使导热板3294与支撑板本体3292连接形成的用于放置电芯的空间较大。同时参见图7,进一步地,调节板3289与支撑板本体3292的连接位置可调,使调节板3289、支撑板3288及热封机构330所围成的用于放置电芯的槽体的宽度可调,更好地适用于不同尺寸的电芯封装,提高了抽真空封装模具320的适用性及使用方便性。具体地,支撑板组件328c还包括调节固定件,调节板3289开设有第一调节孔3290,支撑板本体3292开设有多个并排分布的第二调节孔329c,调节固定件分别穿设于第一调节孔3290和其中一个第二调节孔329c内,使支撑板本体3292与调节板3289的连接位置可调。在本实施例中,调节固定件为螺钉,第一调节孔329c为腰型孔,第二调节孔3290为螺纹孔,使支撑板本体3292与调节板3289的连接位置可调。多个第二调节孔329c间隔设置,且多个第二调节孔329c的排布方向与热封机构330的延伸方向相垂直。
[0023]
如图3与图4所示,进一步地,抽真空封装模具320还包括辅助压板组件327。第二模座323开设有安装孔(图未示),安装孔均与容纳腔323a连通。同时参见图5和图7,具体地,刺破机构326包括推动组件326a、刀架组件326b和承载板326c。推动组件326a设于第二模座323,推动组件326a部分位于容纳腔323a内。刀架组件326b位于容纳腔323a内,刀架组件326b与推动组件326a的动力输出端连接,使推动组件326a驱动刺刀3262朝靠近或远离电芯的方向运动,实现对电芯进行刺破。在本实施例中,承载板326c设于容纳腔323a内,用于支撑电芯。推动组件326a为气缸组件。在其他实施例中,推动组件326a还可以是电缸组件或液缸组件。承载板326c上开设有导向插槽3264。
[0024]
如图7所示,在其中一个实施例中,刀架组件326b包括刺刀3262,刺刀3262用于刺破承载板326c上的电芯。辅助压板组件327滑动设置于第二模座323,辅助压板组件327与承载板326c对应设置。辅助压板组件327开设有用于引导刺刀3262刺破电芯的第二避位槽327a,第二避位槽327a与导向插槽3264对应开设,第二避位槽327a与导向插槽3264对应连通。抽真空组件与第一连接孔322a连通,抽真空组件用于对容纳腔323a进行抽真空。由于辅助压板组件327滑动设置于第二模座323,使辅助压板组件327在刺刀3262相对于承载板326c上的电芯刺破操作时抵接压紧于电芯,避免电芯在刺破过程中相对于承载板326c活动而刺偏的问题,且刺刀3262在第二避位槽327a的引导下准确地插入导向插槽3264内,使刺刀3262能够对电芯进行准确刺破,避免了抽真空封装设备300在刺破过程中容易刺偏电芯的问题,有利于提高刺刀3262刺破电芯的精度。当刺破机构326的刺刀3262刺破电芯时,刺刀3262插入导向插槽3264内,没有被电芯吸收的多余的电解液流出至承载板326c,并由承载板326c的导向插槽3264流至容纳腔323a内,同时抽真空组件用于对容纳腔323a进行抽真空,使抽真空组件通过第一连接孔322a对容纳腔323a进行抽真空,同时将电芯静置过程中产生的气体抽出。此外,在承载板和支撑板3288共同支撑电芯的作用下,辅助压板组件对应于承载板设置,同时压紧组件对应于支撑板3288设置,使辅助压板组件及压紧组件共同作用于电芯表面,有利于电芯快速排液和排气,同时提高了电芯的刺破精度,进而提高了电芯
的抽真空封装的良率。
[0025]
如图7所示,进一步地,第一模座322的内壁上设有分隔筋板3222,分隔筋板3222将容纳腔323a分隔为第一容置槽3231和第二容置槽3233,分隔筋板3222支撑承载板326c,使承载板326c更好地设置于容纳腔323a内,同时提高了第一模座322的结构强度。第一容置槽3231与承载板326c对应,且第一容置槽3231与导向插槽3264连通。热封机构330部分位于第二容置槽3233内,第一连接孔322a与第二容置槽3233连通。当刺刀3262刺破电芯时,电芯流出多余的电解液通过导向插槽3264流入第一容置槽3231内,以免电解液流入第二容置槽3233内影响热封机构330的热封操作及抽真空组件的抽真空操作。进一步地,抽真空封装设备300还包括废液回收组件(图未示),第一模座322还开设有与第一容置槽3231连通的排液孔322b,废液回收组件与排液孔322b连通,废液回收组件用于抽取回收废液,以免第一容置槽3231内的储蓄的电解液溢出,使抽真空封装设备300能够持续对批量电芯进行抽真空封装操作。在本实施例中,废液回收组件包括回收泵和抽液管道,回收泵通过抽液管道与排液孔322b连通,使回收泵能够抽取回收第一容置槽3231内的废液。进一步地,第一容置槽3231的底部设有倾斜面3232,倾斜面3232延伸至邻近排液孔322b的位置,有利于废液通过倾斜面3232引导快速流出第一容置槽3231内,实现快速排液的效果。在本实施例中,倾斜面3232的数目为两个,且两个倾斜面3232朝相互远离的方向倾斜。排液孔322b的数目为两个,两个排液孔322b与两个倾斜面3232的倾斜方向一一对应设置,使第一容置槽3231内的废液能够分别通过两个排液孔322b快速排出,进一步地提高了废液的排出效率。废液回收组件分别与两个排液孔322b连通。在本实施例中,两个倾斜面3232的夹角为120度~150度,使第一容置槽3231内的废液具有较好的排液效果。具体地,两个倾斜面3232的夹角为140度。
[0026]
再次参见图4,在其中一个实施例中,承载板326c邻近辅助压板组件327的一面开设有引导槽3265,引导槽3265与导向插槽3264连通,使电芯刺破后流至承载板326c上的废液能够通过引导槽3265快速流入导向插槽3264内,进而使废液快速汇集至第一容置槽3231内并排出排液孔322b。在本实施例中,引导槽3265的延伸方向与导向插槽3264的延伸方向垂直,使废液通过引导槽3265能够快速流入导向插槽3264内。进一步地,引导槽3265的延伸方向与导向插槽3264的延伸方向相垂直,使废液通过引导槽3265能够更快速地引流入导向插槽3264内。具体地,引导槽3265的数目为多个,多个引导槽3265并排设置,有利于废液快速流入导向插槽3264内,提高了废液的汇集效率。进一步地,承载板326c开设有定位凹槽3261,定位凹槽3261分别与导向插槽3264和引导槽3265连通,定位凹槽3261用于定位电芯,避免电芯在定位压紧过程中相对于承载板326c滑动,使辅助压板组件327更好地将电芯压紧定位于承载板326c上。
[0027]
如图4和图7所示,进一步地,辅助压板组件327包括滑套3271、滑动杆3273和辅助压板本体3275,第二模座323开设有定位槽323a,滑套3271位于定位槽内并与第二模座323连接,且滑套3271套设于滑动杆3273并与滑动杆3273滑动连接,辅助压板本体3275与承载板326c对应设置,辅助压板本体3275与滑动杆3273连接,且辅助压板本体3275位于第二模座323邻近第一模座322的一侧,使辅助压板本体3275在刺刀3262相对于承载板326c上的电芯刺破操作时能够有效地抵接压紧于电芯。第二避位槽327a开设于辅助压板本体3275。第二避位槽327a开设于辅助压板本体3275。进一步地,刀架组件326b还包括刀架主体3266,刺刀3262设于刀架主体3266,且刀架主体3266与推动组件326a的动力输出端连接,使刺刀
3262通过刀架主体3266连接于推动组件326a的动力输出端,进而使刺刀3262与推动组件326a的动力输出端连接。在本实施例中,刺刀3262和导向插槽3264的数目均为多个,多个刺刀3262与多个导向插槽3264一一对应设置,多个刺刀3262并排设置于刀架主体3266,使刀架组件326b能够同时对多个电芯进行刺破操作,提高了电芯的刺破效率。
[0028]
如图3和图5所示,在其中一个实施例中,抽真空封装模具320还包括热封机构330,热封机构330位于容纳腔323a内,热封机构330用于对电芯进行热封。刺破机构326邻近热封机构330设置,热封机构330用于对电芯进行热封,热封机构330开设有与容纳腔323a连通的抽真空孔331,抽真空孔331分别与容纳腔323a和第一连接孔322a连通。
[0029]
如图4所示,进一步地,热封机构330开设有与容纳腔323a连通的抽真空孔331,抽真空孔331分别与容纳腔323a和第一连接孔322a连通。抽真空组件与第一连接孔322a连通,抽真空组件用于对容纳腔323a进行抽真空,使抽真空组件通过第一连接孔322a对容纳腔323a进行抽真空,同时将电芯静置过程中产生的气体抽出,使热封机构330在真空环境下将铝塑膜加热加压实现电芯的真空封装。在本实施例中,刺破机构326邻近热封机构330设置。在一个实施例中,第一连接孔322a与抽真空孔331对应设置,有利于对抽真空孔331进行快速抽真空。可以理解,在其他实施例中,第一连接孔322a与抽真空孔331也可以错开设置。
[0030]
抽真空封装设备300的工作过程为:首先开合驱动组件324驱动第二模座323相对于第一模座322升降运动,确保第二模座323压紧于第一模座322;然后压紧组件压紧电芯位于支撑板组件328c的部位;然后辅助压板组件压紧电芯位于承载板的部位;然后刺破机构326刺破电芯,使没有被电芯吸收的多余的电解液排出;然后抽真空组件通过第一连接孔322a对容纳腔323a进行抽真空操作;最后热封机构330对电芯进行热封,实现在真空环境下将铝塑膜加热加压,进而实现电芯的真空封装。
[0031]
如图4所示,进一步地,热封机构330包括第一驱动组件332、第一热封头334和第二热封头336。第一驱动组件332固定于第二模座323背离第一模座322的一面。第二模座323开设有第一穿设孔,第一驱动组件332通过第一穿设孔与第一热封头334连接。第一热封头334与第二热封头336对应设置,第一热封头334和第二热封头336共同对电芯进行热封,使第一驱动组件332驱动第一热封头334对应于第二热封头336运动,进而使第一热封头334和第二热封头336同时作用于电芯上实现电芯的热封。在本实施例中,第一驱动组件332为气缸组件,第一驱动组件332驱动第一热封头334相对于第二热封头336靠近或远离移动。在其他实施例中,第一驱动组件332还可以是电缸或液缸组件。
[0032]
如图8所示,进一步地,抽真空孔331包括第一抽真空孔331a、第一抽风支孔331b、第二抽真空孔331c和第二抽风支孔331d。第一抽真空孔331a和第一抽风支孔331b均开设于第一热封头334,第一抽真空孔331a与第一抽风支孔331b连通,有利于抽真空组件通过第一抽真空孔331a对第一热封头334邻近的空间区域进行快速抽真空操作。第二抽真空孔331c和第二抽风支孔331d均开设于第二热封头336,第二抽真空孔331c与第二抽风支孔331d连通,有利于抽真空组件通过第而抽真空孔331对第二热封头336邻近的空间区域进行快速抽真空操作。进一步地,第一抽真空孔331a沿第一热封头334的轴向延伸,第一抽风支孔331b与第一抽真空孔331a连通,且第一抽风支孔331b贯穿第一热封头334,有利于抽真空组件在第一热封头334抵接热封电芯的过程中对电芯的周围进行快速地抽真空。具体地,第一抽风支孔331b的延伸方向与第一抽真空孔331a的延伸方向垂直。第一抽风支孔331b的数目为多
个,多个第一抽风支孔331b间隔分布且均与第一抽真空孔331a连通。进一步地,第二抽真空孔331c沿第二热封头336的轴向延伸,第二抽风支孔331d与第二抽真空孔331c连通,且第二抽风支孔331d贯穿第二热封头336,有利于抽真空组件在第二热封头336抵接热封电芯的过程中对电芯的周围进行快速地抽真空。具体地,第二抽风支孔331d的延伸方向与第二抽真空孔331c的延伸方向垂直。第二抽风支孔331d的数目为多个,多个第二抽风支孔331d间隔分布且均与第二抽真空孔331c连通。
[0033]
如图5所示,进一步地,第一热封头334包括相连接的热封头主体334a和放置座334b,第一抽真空孔331a和第一抽风支孔331b均开设于热封头主体334a。放置座334b与第一驱动组件332的动力输出端连接,热封头主体334a设于放置座334b邻近第二热封头336的一侧,使第一热封头334与第一驱动组件332的动力输出端连接,且第一热封头334与第二热封头336相对设置,进而使第一驱动组件332驱动第一热封头334相对于第二热封头336运动。为使第一热封头334沿第一驱动组件332的动力输出方向运动,进一步地,第一热封头334还包括辅助导杆334c,第二模座323开设有导孔,辅助导杆334c位于导孔内并与第二模座323滑动连接,且辅助导杆334c的延伸方向与第一驱动组件332的动力输出方向平行,使第一热封头334沿第一驱动组件332的动力输出方向准确运动,提高了第一热封头334相对于第二模座323运动的精度,进而提高了电芯的热封精度。在本实施例中,辅助导杆334c和导孔的数目均为两个,每一辅助导杆334c位于相应的导孔内,两个辅助导杆334c分别位于第一驱动组件332的两侧,可以更好地引导第一热封头334沿第一驱动组件332的动力输出方向运动。
[0034]
然而,热封头主体334a的热量直接依次传导至放置座334b和第二模座323上,使抽真空封装设备300存在过热的问题,进一步地,放置座334b与热封头主体334a连接处开设有多个导风槽3342,多个导风槽3342并排开设。当抽真空组件工作时,对容纳腔323a进行抽真空,使容纳腔323a内的空气在多个导风槽3342内流动,以对放置座334b的热量进行散热,使热封头主体334a的热量不易传导至放置座334b上,提高了放置座334b的散热速率,避免了抽真空封装设备300存在过热的问题。
[0035]
如图3和图5所示,在其中一个实施例中,固定座310转动连接于机架100,安装架321连接于固定座310的背离机架100的一面,使安装架321通过固定座310转动连接于机架100。抽真空封装设备300还包括旋转驱动机构(图未示),旋转驱动机构安装于机架100,且旋转驱动机构的动力输出端与固定座310连接,使旋转驱动机构驱动固定座310相对于机架100转动,进而使固定座310能够周期性地转动至邻近输送装置200的位置处。在本实施例中,抽真空封装模具320的数目为多个,多个抽真空封装模具320沿固定座310的周向间隔分布,由于每一抽真空封装模具320能够对多个电芯进行抽真空封装,提高了抽真空封装设备300对电芯进行抽真空封装的效率。当旋转驱动机构驱动固定座310旋转,使其中一个抽真空封装模具320转动至与第一滑动座220对应的位置,位于电芯的上料位与抽真空封装设备300之间的取放机构240刚好运动至与该抽真空封装模具320对应的位置,并将待真空封装的电芯放置于抽真空封装模具320内的容纳槽内,进而对电芯进行抽真空封装操作,同时位于抽真空封装放置与切料机构400之间的取放机构240将真空封装后的电芯放置于切料机构400上,同时位于切料机构400与精封机构500之间的取放机构240将电芯放置于精封机构500上,同时位于精封机构500与测电压机构600之间的取放机构240将电芯放置于测电压机
构600上,同时位于测电压机构600与定位机构700之间取放机构240将电芯放置于定位机构700。
[0036]
为提高抽真空封装设备300对电芯的封装效率,并巧妙利用位于抽真空封装放置与切料机构400之间的取放机构240往复运动的时间差与固定座310转动的时间差实现无缝对接,进一步地,每一抽真空封装模具320随固定座310旋转一周的时间等于抽真空封装模具320对电芯进行抽真空封装的时间。在本实施例中,每一抽真空封装模具320随固定座310旋转一周的时间等于位于抽真空封装放置与切料机构400之间的取放机构240往复运动的时间之和的两倍。同理,当位于抽真空封装放置与切料机构400之间的取放机构240在上料位取到电芯时,同时位于抽真空封装放置与切料机构400之间的取放机构240在抽真空封装放置的抽真空封装模具320上取出电芯,同时位于切料机构400与精封机构500之间的取放机构240在取料机构取出电芯,同时位于精封机构500与测电压机构600之间的取放机构240将电芯取出于精封机构500上,同时位于测电压机构600与定位机构700之间取放机构240将电芯取出于测电压机构600,这样不仅提高了抽真空封装设备300对电芯的封装效率,并巧妙利用位于抽真空封装放置与切料机构400之间的取放机构240往复运动的时间差与固定座310转动的时间差实现无缝对接。
[0037]
如图1、图2和图9所示,在其中一个实施例中,电芯制造系统10还包括切料机构400、精封机构500、测电压机构600、定位机构700、切边机构800、双折边机构900以及热封机构1100。抽真空封装设备300、切料机构400、精封机构500、测电压机构600、定位机构700、切边机构800、双折边机构900以及热封机构1100沿输送装置200的输送方向依次设置于机架100上。输送装置200用于依次输送电芯至抽真空封装设备300、切料机构400、精封机构500、测电压机构600、定位机构700、切边机构800、双折边机构900以及热封机构1100,使电芯分别运送至抽真空封装设备300、切料机构400、精封机构500、测电压机构600、定位机构700、切边机构800、双折边机构900以及热封机构1100对应的工位。进一步地,切料机构400用于切除真空封装后的电芯的毛边。精封机构500用于对切除毛边的电芯进行精封,即对电芯的毛边切除处进行精封。测电压机构600用于对精封后的电芯的电压进行测量,以检测精封后的电芯的电压是否合格。若电芯的电压合格,则通过输送机构将电芯输送至定位机构700。若电芯的电压不合格,则将电芯丢弃。定位机构700用于对电压测量合格的电芯进行定位调整。切边机构800用于切除定位后的电芯的多余的封边。双折边机构900用于对切除封边后电芯的外壳进行双折边处理,以分别对电芯的外壳两侧进行折边。热封机构1100用于对双折边处理后的电芯的边角进行封烫。
[0038]
由于抽真空封装设备300、切料机构400、精封机构500、测电压机构600、定位机构700、切边机构800、双折边机构900以及热封机构1100沿输送装置200的输送方向依次设置,使输送装置200能够将电芯依次输送至各个机构对应的工位上进行加工,在对电芯进行精封工序时,电芯容易损坏形成不合格产品,在精封机构500之后设置测电压机构600对精封后的电芯的电压进行测量,若电芯的电压合格,才将电芯依次输送至定位机构700、切边机构800、双折边机构900以及热封机构1100对应的工位上进行继续加工,否则将电芯丢弃,以及时丢弃不合格的电芯,避免不合格电芯进行接下来的定位机构700、切边机构800、双折边机构900以及热封机构1100对应的工位上进行继续加工而浪费合格电芯的加工效率,解决了电芯的生产效率较低的问题;经测电压机构600检测合格的电芯,先通过输送装置200输
送至定位机构700进行定位调整,然后再将电芯依次输送至切边机构800、双折边机构900以及热封机构1100进行加工,使电芯输送至切边机构800、双折边机构900以及热封机构1100上进行精确地加工,解决了电芯加工的次品率较高的问题。
[0039]
如图2和图9所示,具体地,输送装置200包括基座组件210、第一滑动座220、水平驱动机构230、取放机构240、第二滑动座250和夹紧机构260。基座组件210设于机架100,第一滑动座220和第二滑动座250均滑动连接于基座组件210。第一滑动座220的滑动方向与第二滑动座250的滑动方向相互平行。水平驱动机构230设于基座组件210,水平驱动组件的动力输出端分别与第一滑动座220和第二滑动座250连接,水平驱动组件用于驱动第一滑动座220相对于基座组件210分别滑动至与抽真空封装设备300、切料机构400、精封机构500、测电压机构600和定位机构700对应的位置,水平驱动组件还用于驱动第二滑动座250相对于基座组件210分别滑动至定位机构700、切边机构800、双折边机构900以及热封机构1100对应的位置。取放机构240设于第一滑动座220,使取放机构240随第一滑动座220相对于基座组件210滑动。取放机构240用于放置或取出电芯,使电芯能够依次输送至抽真空封装设备300、切料机构400、精封机构500、测电压机构600以及定位机构700,以对电芯进行真空封装、切除毛边、精封、测电压以及定位调整工序。夹紧机构260设于第二滑动座250,使夹紧机构260随第二滑动座250相对于基座组件210滑动。夹紧机构260用于将定位机构700定位调整后的电芯进行夹紧,以使电芯分别精确地输送至与切边机构800、双折边机构900以及热封机构1100对应的位置,实现分别对电芯进行精确地切边、双折边和热封操作。同时参见图1,在本实施例中,抽真空封装设备300、切料机构400、精封机构500、测电压机构600和定位机构700沿输送装置200的输送方向依次间隔设置,即抽真空封装设备300与切料机构400之间的距离、切料机构400与精封机构500之间的距离、精封机构500与测电压机构600之间的距离、测电压机构600与定位机构700之间的距离均相等,有利于简化第一滑动座220及取放机构240的设置方式,同时缩短第一滑动座220相对于基座组件210往复滑动的位移。
[0040]
如图9和图10所示,进一步地,基座组件210包括第一基座212和第二基座214,第一基座212与第二基座214平行设置于机架100,第一滑动座220滑动设置于第一基座212,第二滑动座250滑动设置于第二基座214。如图11和图12所示,水平驱动机构230包括第一水平驱动机构230a和第二水平驱动机构230b。其中,第一水平驱动机构230a安装于第一基座212,且第一水平驱动机构230a的动力输出端与第一滑动座220连接。第二水平驱动机构230b安装于第二基座214,且第二水平驱动机构230b的动力输出端与第二滑动座250连接。第一水平驱动机构230a的动力输出方向与第二水平驱动机构230b的动力输出方向相互平行。在本实施例中,第一滑动座220的滑动方向与第二滑动座250的滑动方向相互平行,且第一滑动座220的滑动轨迹与第二滑动座250的滑动轨迹平行且邻近设置。第一水平驱动机构230a和第二水平驱动机构230b为两个相互独立的动力驱动源,不仅使第一滑动座220和第二滑动座250均能够运动至与定位机构700对应的位置,而且使第一滑动座220和第二滑动座250各自运动至与定位机构700对应的位置的时间差错开,避免取放机构240与夹紧机构260发生机械干涉的问题。夹紧机构260在定位机构700定位调整之后将电芯夹紧,使夹紧机构260将电芯夹紧并随第二滑动座250依次输送至与切边机构800、双折边机构900以及热封机构1100对应的位置,保证电芯在切边机构800、双折边机构900以及热封机构1100的加工精度,同时使电芯制造系统10的结构更加简单。
[0041]
如图11所示,具体地,第一水平驱动机构230a包括第一电机232、丝杆(图未示)和螺母234。第一电机232安装于第一基座212,第一电机232的动力轴与丝杆的一端连接,丝杆的另一端与第一基座212转动连接。螺母234套设于丝杆并与丝杆螺纹连接,螺母234与第一滑动座220连接。当第一电机232驱动丝杆相对于第一基座212转动连接时,丝杆带动螺母234水平移动,由于螺母234与第一滑动座220连接,使螺母234带动第一滑动座220相对于第一基座212滑动,使第一水平驱动机构230a驱动第一滑动座220相对于第一基座212滑动。可以理解,在其他实施例中,第一水平驱动机构230a不仅限于是电机驱动丝杆传动机构,还可以是电机驱动带传动机构。
[0042]
如图12所示,具体地,第二水平驱动机构230b包括第二电机233、第一带轮235、第二带轮237和传送皮带(图未示)。第二电机233安装于第二基座214,且第二电机233的动力输出轴与第一带轮235连接。第二带轮237转动连接于第二基座214。传送皮带分别套设于第一带轮235和第二带轮237,且传送皮带与第二滑动座250连接。当第二电机233驱动第一带轮235转动时,第一带轮235通过传送皮带带动第二带轮237相对于第二基座214转动,使传送皮带带动第二滑动座250相对于第二基座214分别滑动与定位机构700、切边机构800、双折边机构900以及热封机构1100对应的位置。
[0043]
如图1和图2所示,为减小第一滑动座220相对于基座组件210往复滑动的位移,进一步地,取放机构240的数目为五个,五个取放机构240并排设置于第一滑动座220,且相邻两个取放机构240之间的距离相等。在电芯的上料位与抽真空封装设备300之间、抽真空封装放置与切料机构400之间、切料机构400与精封机构500之间、精封机构500与测电压机构600之间、以及测电压机构600与定位机构700之间均设有一取放机构240,且五个取放机构240的放置或取出电芯的节拍相同,确保五个取放机构240能够随第一滑动座220相对于基座组件210往复滑动的步调一致性。在电芯的上料位与抽真空封装设备300之间、抽真空封装放置与切料机构400之间、切料机构400与精封机构500之间、精封机构500与测电压机构600之间、以及测电压机构600与定位机构700之间均设有一取放机构240,可以减小第一滑动座220相对于基座组件210往复滑动的位移,并缩短电芯在各个工位加工的周转周期,提高了电芯的加工效率。如图13所示,在本实施例中,每一取放机构240包括固定架241、设于固定架241的吸盘组件243以及气控机构(图未示)。固定架241与第一滑动座220连接。气控机构与吸盘组件243连通,气控机构用于对吸盘组件243进行抽气或吹气控制,使吸盘组件243能够吸附或松开电芯。
[0044]
可以理解,在电芯的上料位处的电芯可以由人工手动对电芯进行上料,也可以由上料机构对电芯进行上料。在其中一个实施例中,电芯制造系统还包括上料机构,上料机构用于对电芯进行上料。上料机构对应设置于电芯的上料位。上料机构、抽真空封装设备300、切料机构400、精封机构500、测电压机构600和定位机构700沿输送装置200的输送方向依次间隔设置。具体地,上料机构为半自动弹匣式上料机构。
[0045]
如图14所示,具体地,测电压机构600包括支撑架610、固定治具620、连接座组件630、第二升降组件640、第一探针组件650和第二探针组件660。支撑架610和固定治具620均与机架100连接。固定治具620邻近输送装置200设置,固定治具620用于定位电芯。第二升降组件640设于支撑架610,且第二升降组件640的动力输出端与连接座组件630连接。第二升降组件640驱动连接座组件630相对于固定治具620升降运动。第一探针组件650和第二探针
组件660均设于连接座组件630上,且第一探针组件650和第二探针组件660均与固定治具620对应设置。第一探针组件650用于检测电芯的电压,第二探针组件660用于检测电芯的铝塑膜的边电压,使测电压机构600同时对电芯的电压及铝塑膜的边电压进行测量,综合判定电芯是否合格。在本实施例中,第二升降组件640为气缸组件,在其他实施例中,第二升降组件640还可以为液缸组件或电缸组件。
[0046]
如图15所示,在其中一个实施例中,第一探针组件650包括设置座652、探针本体654和刺破钻头656。设置座652与连接座组件630连接,探针本体654和刺破钻头656并排安装于设置座652,刺破钻头656用于刺破电芯的铝塑膜的溶胶封边区,探针本体654用于检测电芯的电压。同时参见图11,在本实施例中,探针本体654包括第一滑件654a、探针杆体654b、与探针杆体654b的一端连接的凸柱部654c,设置座652开设有第一安装通孔652a,第一滑件654a位于第一安装通孔652a内并与设置座652连接。第一滑件654a套设于探针杆体654b并与探针杆体654b滑动连接。凸柱部654c用于抵接于电芯,以检测电芯的电压。由于探针杆体654b滑动连接于第一滑件654a,当探针杆体654b与电芯抵接时,探针杆体654b相对于设置座652滑动,避免探针杆体654b由于惯性作用冲撞折断或撞伤固定治具620的问题,延长了第一探针组件650的使用寿命。进一步地,刺破钻头656包括钻头杆体656a和第三滑件656b,设置座652开设有第二安装通孔652b,第三滑件656b位于第二安装通孔652b内并与设置座652连接。第三滑件656b套设于钻头杆体656a并与钻头杆体656a滑动连接。在本实施例中,钻头杆体656a邻近凸柱部654c的位置设有刺刃部6562,刺刃部6562用于刺破电芯的铝塑膜的溶胶封边区。由于钻头杆体656a滑动连接于第三滑件656b,当钻头杆体656a刺破铝塑膜并与固定治具620抵接时,钻头杆体656a受阻力作用相对于设置座652滑动,避免钻头杆体656a折断或刺刃部6562刺伤固定治具620的问题,延长了第二探针组件660的使用寿命。
[0047]
进一步地,刺刃部6562与固定治具620之间的距离为第一距离,凸柱部654c与固定治具620的距离为第二距离,第一距离小于第二距离,使探针本体654和刺破钻头656均相对于设置座652朝固定治具620同步靠近的方向运动时,刺刃部6562与电芯首先接触刺破,有利于测电压机构600同时实现对电芯的电压及铝塑膜的边电压进行电压检测,进而提高了测电压机构600的检测效率。在本实施例中,凸柱部654c呈圆柱状。根据电芯的电压及铝塑膜的边电压的电压检测数据,综合判定当前检测的电芯是否合格。若电芯不合格,则挑出丢弃;否则,通过输送装置200将电芯输送至下一工位即定位机构700工位进行操作,以达到及时剔除不合格的电芯的效果,避免不合格的电芯和合格的电芯一起排队进入下一个工位即定位机构700工位进行加工,大大提高了电芯的制造效率。
[0048]
如图14所示,在其中一个实施例中,固定治具620包括固定治具本体623和辅助检测块625,固定治具本体623与机架100连接,固定治具本体623开设有相连通的第一放置槽623a和第二放置槽623b,第一放置槽623a用于放置定位电芯,第二放置槽623b用于放置辅助检测块625,辅助检测块625用于与电芯的铝塑膜抵接,以检测电芯的铝塑膜的边电压,通过设置辅助检测块625,有利于提高电芯的铝塑膜的边电压的测量效率及精度。同时参见图15,在其中一个实施例中,连接座组件630包括连接座631、第一安装块633和第二安装块635,连接座631与第二升降组件640的动力驱动杆连接,第一安装块633和第二安装块均滑动设置于连接座631,第一探针组件650安装于第一安装块633,第二探针组件660安装于第
二安装块635,使第一探针组件650和第二探针组件660均安装于连接座组件630上。进一步地,连接座631开设有第一腰型孔631a,第一安装块633开设有第一固定孔(图未示)。连接座组件630还包括第一固定件(图未示),第一固定件分别穿设于第一腰型孔631a和第一固定孔内,使第一安装块633通过第一固定件固定于连接座631上。当需调节第一安装块633与连接座631的连接位置时,松开第一固定件,调节第一安装块633与连接座631的相对位置至适当位置,锁紧第一固定件,进而使第一安装块633与连接座631的连接位置可调,提高了测电压机构600的使用方便性。
[0049]
如图14所示,进一步地,连接座631开设有第二腰型孔631b,第二安装块635开设有第二固定孔。连接座组件630还包括第二固定件(图未示),第二固定件分别穿设于第二腰型孔631b和第二固定孔内,使第二安装块635通过第二固定件固定于连接座631上。当需调节第二安装块635与连接座631的连接位置时,松开第二固定件,调节第二安装块635与连接座631的相对位置至适当位置,锁紧第二固定件,进而使第二安装块635与连接座631的连接位置可调,提高了测电压机构600的使用方便性。进一步地,连接座组件630还包括连接板637和至少两个引导柱639,连接板637与每一引导柱639连接。至少两个引导柱639平行设置。每一引导柱639滑动设置于支撑架610。至少两个引导柱639均与连接座631连接,当第二升降组件640驱动连接座631相对于支撑架610运动时,由于连接板637与每一引导柱639连接,使连接座631能够带动所有引导柱639同时相对于支撑架610滑动,进而使连接座631相对于支撑架610始终平行运动,提高了连接座631的运动精度,避免第一探针组件650偏离作用到电芯,进而提高了第一探针组件650检测到电芯的电压精度。同理,提高了第二探针组件660检测到电芯的电压精度。
[0050]
如图9和图10所示,进一步地,第一基座212的背离机架100的一面设有第一导向轨(图中仅示出第一导向轨的安装槽212a),第一滑动座220滑动设置于第一导向轨,使第一滑动座220更好地滑动设置于第一基座212。第二基座214的背离机架100的一面设有第二导向轨214a,第二滑动座250滑动设置于第二导向轨214a,使第二滑动座250更好地滑动设置于第二基座214。在本实施例中,第一导向轨与第二导向轨214a平行设置,且第一导向轨的延伸方向与第二导向轨214a的延伸方向不共线。定位机构700、切边机构800、双折边机构900和热封机构1100均沿第二导向轨214a的延伸方向布设。
[0051]
进一步地,定位机构700包括定位调节组件、第一夹紧组件和第二夹紧组件。定位调节组件包括手轮、调节丝杆和固定座310,固定座310安装于第二基座214。手轮与调节丝杆的一端连接。调节丝杆转动连接于固定座310上,且调节丝杆的周壁上设有螺向相反的第一螺接部和第二螺接部。第一夹紧组件套设于第一螺接部并与调节丝杆螺纹连接,且第一夹紧组件滑动设置于第二基座214。第二夹紧组件套设于第二螺接部并与调节丝杆螺纹连接,且第二夹紧组件滑动设置于第二基座214。第一夹紧组件和第二夹紧组件分别位于第二导向轨214a的两侧。当沿正向转动手轮时,手轮带动调节丝杆正向转动,使第一夹紧组件与第二夹紧组件相互靠近;相反,当沿反向转动手轮时,手轮带动调节丝杆反向转动,使第一夹紧组件与第二夹紧组件相互远离。如此,对第一夹紧组件与第二夹紧组件之间的间隙进行调节,实现第一夹紧组件和第二夹紧组件的相对位置的调节,以适用于不同尺寸的电芯进行调整。
[0052]
可以理解,由于第一导向轨和第二导向轨错开设置,且第一夹紧组件与第二夹紧
组件之间的间隙需适应不同尺寸的电芯进行调节,位于测电压机构与定位机构之间的取放机构在测电压机构取出电芯的位置与第一滑动座之间的距离,与取放机构在定位机构放置电芯的位置与第一滑动座之间的距离不同,为提高取放机构适用性,进一步地,位于测电压机构与定位机构之间的取放机构的固定架241与第一滑动座220滑动连接,使吸盘组件与第一滑动座的相对位置可以灵活调节,以适应于不同位置的第一夹紧组件与第二夹紧组件之间的间隙。在本实施例中,固定架相对于第一滑动座滑动的方向垂直于第一滑动座相对于第一基座滑动的方向。在本实施例中,第一滑动座220包括滑动座主体222、与滑动座主体连接的升降架224、以及与升降架滑动连接的滑套座226。固定架与滑套座滑动连接,使固定座310与第一滑动座滑动连接。具体地,滑套座相对于升降架滑动的方向、固定套相对于滑套座滑动的方向、以及第一滑动座相对于第一基座滑动的方向,三者两两相互垂直。在一个实施例中,固定架与滑套座滑动连接的部位为杆体结构。
[0053]
如图14和图15所示,进一步地,取放机构240还包括升降驱动机构245,升降驱动机构安装于升降架,且升降驱动机构的动力输出端与滑套座连接,使升降驱动机构驱动滑套座相对于升降架滑动,以调节吸盘组件相对于第一基座升降的高度,提高了取放机构的适用性。在本实施例中,升降驱动机构为气缸机构。进一步地,取放机构240还包括位置调节驱动组件247,位置调节驱动组件安装于第一滑动座,位置调节驱动组件的动力输出端与固定架连接,以驱动固定架相对于第一滑动座滑动。在本实施例中,位置调节驱动组件为气缸组件。为提高位置调节驱动组件驱动固定架相对于第一滑动座滑动的精度,进一步地,滑套座上设有并排的第一感应器226b和第二感应器226c,固定架上设有感应片241a。感应片还与位置调节驱动组件的控制端通信连接。当感应片运动至与第一感应器对应的位置时,感应片随固定架运动至第一极限位置。当感应片运动至与第二感应器对应的位置时,感应片随固定架运动至第二极限位置。如此,实现位置调节驱动组件驱动感应片随固定架相对于第一滑动座的精确滑动。为减小取放机构占用空间,进一步地,滑套座开设有避位孔226a,避位孔用于避开位置调节驱动组件247,且位置调节驱动组件247位于升降架与滑动座主体连接的位置之间,大大减小了取放机构占用空间。
[0054]
进一步地,第一夹紧组件包括第一安装座、第一螺母、第一驱动源和第一夹持板。第一安装座滑动设置于第二基座214,且第一安装座与第一螺母连接。第一螺母套设于第一螺接部并与第一螺接部螺纹连接。第一驱动源安装于第一安装座背离第二滑动座250的一面,且第一驱动源的动力输出端与第一夹持板连接,使第一驱动源驱动第一夹持板运动。第二夹紧组件包括第二安装座、第二螺母、第二驱动源和第二夹持板。第二安装座滑动设置于第二基座214,且第二安装座与第二螺母连接。第二螺母套设于第二螺接部并与第二螺接部螺纹连接。第二驱动源安装于第二安装座背离第二滑动座250的一面,且第二驱动源的动力输出端与第二夹持板连接,使第二驱动源驱动第二夹持板运动。在本实施例中,第一夹持板与第二夹持板平行且相对设置,且第一夹持板与第二夹持板朝相互靠近或远离的方向运动,以松开或夹紧电芯。第一驱动源和第二驱动源均为气缸组件。在其他实施例中,第一驱动源和第二驱动源均还可以为电缸组件或液缸组件。
[0055]
需要说明的是,第一夹持板与第二夹持板共同夹持电芯的夹持力方向为第一方向,夹紧机构260夹持于电芯的夹持力方向为第二方向,第一方向与第二方向之间存在夹角。当第一夹持板与第二夹持板夹持电芯时,夹紧机构260随第二滑动座250相对于第二基
座214运动至与定位机构700对应的位置,夹紧机构260夹紧作用于电芯上。当夹紧机构260夹紧电芯后,第一夹持板朝与第二夹持板相互远离的方向运动,实现电芯较好定位夹具于电芯上,提高了电芯的定位夹紧精度。在本实施例中,第一方向与第二方向垂直,且第一方向和第二方向均垂直于第二导向轨214a的延伸方向,使第一夹持板与第二夹持板共同对电芯进行横向的预轻压夹持,以先调整电芯至预定位置,并使夹紧机构260对电芯进行纵向的重压夹持,通过两个不同方向的夹持定位能够避免电芯的夹持定位不到位的问题,同时提高了电芯的定位夹持精度。
[0056]
为提高第一夹持板和第二夹持板共同夹持电芯的效果,同时减小了第一夹持板和第二夹持板的重量,进一步地,第一夹持板包括相连接的第一夹持板主体和第一夹块,第一夹持板主体设置于第一安装座。第一夹块邻近第二夹持板设置。第一驱动源的动力轴与第一夹持板主体连接。第二夹持板包括相连接的第二夹持板主体和第二夹块,第二夹持板主体设置于第二安装座。第二夹块邻近第一夹持板设置。第二驱动源的动力轴与第二夹持板主体连接。在本实施例中,第一夹块与第二夹块平行且相对设置。第一夹块的横截面和第二夹块的横截面均呈l型,使第一夹持板与第二夹持板共同夹持于电芯的面积较大,同时减小了第一夹持板和第二夹持板的重量。为进一步提高第一夹持板和第二夹持板共同夹持电芯的效果,在一个实施例中,第一夹块设有朝向第二夹持板主体倾斜的第一避位面,第二夹块设有朝向第一夹持板主体倾斜的第二避位面,当第一夹块与第二夹块朝相互靠近的方向运动时,第一避位面与第二避位面均能够避开与电芯抵接夹持,并使电芯夹持于第一夹块与第二夹块的过程中具有一定的活动空间,进而使第一夹块与第二夹块更好地夹持电芯。进一步地,第一夹持板还滑动设置于第一安装座,第二夹持板还滑动设置于第二安装座,使第一夹持板相对于第一安装座的滑动更加平稳,并使第二夹持板相对于第二安装座的滑动更加平稳,进而使第一夹持板与第二夹持板之间的夹持精度更高。在本实施例中,第一安装座和第二安装座均通过设有滑轨的方式来实现相应的夹持板滑动设置。在其他实施例中,第一安装座和第二安装座均还可以通过设置导向杆3284的方式来实现相应的夹持板滑动设置。
[0057]
进一步地,定位机构700还包括校准组件,校准组件包括刻度尺,刻度尺与第一夹块连接。刻度尺设有多个并排的刻度线,且刻度线的排列方向与第一夹块的运动方向平行。在本实施例中,第一夹块邻近第二夹块的一面平齐于刻度尺上的0刻度线。第二夹块邻近第一夹块的一面随第二夹块运动至与刻度尺的其中一个刻度线对应的位置,使用者可直观读取到第一夹块与第二夹块之间的夹持间隙,并配合需求转动手轮,如此,有利于使用者快速得知第一夹块与第二夹块之间的夹持间隙的调节是否到位,提高了夹持间隙的调节效率,避免直接目测判断调节出现误判的情形,提高了定位机构700的使用方便性。
[0058]
进一步地,切边机构800包括两个对称设置的切边组件,分别为第一切边组件和第二切边组件。第一切边组件设置于第一安装座,第二切边组件设置于第二安装座上。两个切边组件分别对电芯的两边的多余的封边进行剪切,实现对电芯的两边的多余的封边同时进行切除,提高了电芯的封边的切除效率。具体地,第一切边组件包括第一滑座、第一调节座、第一切边驱动源、第一导向件及第一滚刀件,第一调节座与第一滑座连接,第一安装座连接于第一调节座的背离第一滑座的一面。第一切边驱动源设于第一安装座。第一导向件和第一滚刀件均转动连接于第一调节座。第一导向件和第一滚刀件沿第二导向轨214a的延伸方
向并排设置,且第一导向件位于第一滚刀件邻近定位机构700的一侧,使电芯在切边之前先经过第一导向件的引导,进而使电芯的多余的封边展平,有利于提高第一滚刀件更好地切除电芯多余的封边。第一切边驱动源的动力输出端与第一滚刀件连接,以驱动第一滚刀件相对于第一调节座转动。在本实施例中,第一滚刀件和第一导向件的数目均为两个,两个第一滚刀件相对设置,且两个第一滚刀件通过齿轮组件啮合传动,使两个第一滚刀件更好地同步啮合传动,进而使两个第一滚刀件更好地切除电芯多余的封边。两个第一导向件相对设置。在本实施例中,第一切边驱动源为电机,且第一切边驱动源的动力输出端与其中一个第一滚刀件连接。例如,第一切边驱动源的动力输出端通过带传动与其中一个第一滚刀件连接。
[0059]
具体地,第二切边组件包括第二滑座、第二调节座、第二切边驱动源、第二导向件及第二滚刀件。第二调节座与第二滑座连接,第二安装座连接于第二调节座的背离第二滑座的一面。第二切边驱动源设于第二安装座。第二导向件和第二滚刀件均转动连接于第二调节座。第二导向件和第二滚刀件沿第二导向轨214a的延伸方向并排设置,且第二导向件位于第二滚刀件邻近定位机构700的一侧,使电芯在切边之前先经过第二导向件的引导,进而使电芯的多余的封边展平,有利于提高第二滚刀件更好地切除电芯多余的封边,提高切除的精度。第二切边驱动源的动力输出端与第二滚刀件连接,以驱动第二滚刀件相对于第二调节座转动。在本实施例中,第二滚刀件和第二导向件的数目均为两个,两个第二滚刀件相对设置,且两个第二滚刀件通过齿轮组件啮合传动,使两个第二滚刀件更好地同步啮合传动,进而使两个第二滚刀件更好地切除电芯多余的封边。两个第二导向件相对设置。在本实施例中,第二切边驱动源为电机,且第二切边驱动源的动力输出端与其中一个第二滚刀件连接。例如,第二切边驱动源的动力输出端通过带传动与其中一个第二滚刀件连接。由于第一调节座和第一夹持板主体均设置于第一安装座,使第一调节座和第一夹持板主体均随第一安装座同时调整,同理,第二调节座和第二夹持板主体均随第二安装座同时调整,提高了电芯制造系统的调节的方便性。进一步地,第一滑座滑动设置于第一安装座,第二滑座滑动设置于第二安装座,使第一滑座与第二滑座的相对位置可调,进而使第一调节座与第二调节座的相对位置可调,使切边机构800能够适用于不同尺寸的电芯的多余封边的切除,提高了切边机构800的适用性。
[0060]
进一步地,双折边机构900包括两个相对设置的折边组件,两个折边组件分别设于第一滑座和第二滑座,使两个折边组件之间的间距能够通过第一滑座和第二滑座之间的相对位置的调节而调节,以使两个折边组件同时对不同尺寸的电芯的两边进行折边,又由于第一调节座连接于第一安装座,使第一调节座和与第一调节座位于同一第一安装座的折边组件均能够随第一安装座而调整,同理,第二调节座和与第二调节座位于同一第二安装座的折边组件均能够随第二安装座而调整,提高了电芯制造系统10的适应性。进一步地,热封机构1100设于第二基座214上,且热封机构1100设于第二导向轨214a的一侧。热封机构1100用于对双折边处理后的电芯的边角进行封烫。在本实施例中,热封机构1100位于双折边机构900的背离切边机构800的一侧,使电芯经双折边处理后的边角进一步地热封处理。
[0061]
上述的电芯制造系统10制造电芯的步骤包括:首先,通过输送装置200将电芯从上料位输送至真空封装装置;然后,通过抽真空封装设备300对电芯进行真空封装;然后,通过输送装置200将真空封装后的电芯输送至切料机构400;然后,通过切料机构400切除真空封
装后的电芯的毛边,以切除真空封装后的电芯的多余的毛边;然后,通过输送装置200将切除毛边后的电芯输送至精封机构500;然后,通过精封机构500对电芯的毛边切除处进行精封;然后,通过输送装置200将精封后的电芯输送至测电压机构600;然后,通过测电压机构600对精封后的电芯的电压进行测量。然后,判断电芯的电压是否合格,若电芯的电压合格,则通过取放机构将电压合格的电芯输送至定位机构;否则,将电芯丢弃;然后,通过定位机构700对电芯的输送方向进行定位调整;然后,通过输送装置200将定位调整的电芯输送至切边机构800;然后,通过切边机构800切除定位后的电芯的多余的封边;然后,通过输送装置200将切除封边后的电芯输送至双折边机构900;然后,通过双折边机构900对切除封边后电芯的外壳进行双折边处理;然后,通过输送装置200将双折边处理后的电芯输送至热封机构1100;最后,通过热封机构1100对双折边处理后的电芯的边角进行封烫。
[0062]
与现有技术相比,本实用新型至少具有以下优点:
[0063]
1、由于开合驱动组件324驱动第二模座323朝靠近第一模座322的方向运动,确保第二模座323在抽真空组件抽真空时与第一模座322围成的容纳腔323a的紧密性,使抽真空组件更好地对容纳腔323a进行抽真空,并使第二模座323在电芯的抽真空封装工艺完毕后离开第一模座322,以取出封装后的电芯;2、在封装时,首先开合驱动组件324驱动第二模座323相对于第一模座322运动至与第一模座322抵接,然后伸缩驱动件驱动压紧组件朝靠近支撑板组件328c的方向运动,直至压紧组件抵接于支撑板组件328c上的电芯,使电芯压紧定位于支撑板组件328c与压紧组件之间,避免电芯运动而影响后续的刺破精度;然后刺破机构326刺破电芯,没有被电芯吸收的多余的电解液和产生的废气均通过电芯的刺破处排出,同时抽真空组件通过第一连接孔322a对容纳腔323a进行抽真空,同时将电芯静置过程中产生的气体抽出;最后热封机构330对电芯进行热封,实现电芯的抽真空封装;3、由于在电芯刺破时,压紧组件将电芯压紧于支撑板组件328c,提高了电芯内排气的效率,同时确保电芯内气体完全排出。
[0064]
以上所述实施例仅表达了本实用新型的几种实施方式,其描述较为具体和详细,但并不能因此而理解为对实用新型专利范围的限制。应当指出的是,对于本领域的普通技术人员来说,在不脱离本实用新型构思的前提下,还可以做出若干变形和改进,这些都属于本实用新型的保护范围。因此,本实用新型专利的保护范围应以所附权利要求为准。