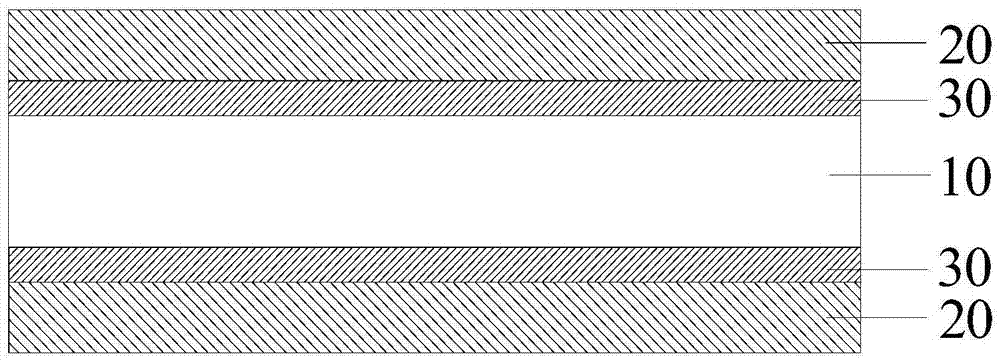
本发明涉及复合材料制备领域,具体而言,涉及一种玻璃钢、其制备方法及浮空器吊舱。
背景技术:
:玻璃钢是一种纤维强化塑料,其性质质轻而硬、不导电、性能稳定、回收利用少且耐腐蚀,可以代替钢材制造机器零件和汽车、船舶等外壳。目前,代替钢材应用于机器零件和汽车、船舶等外壳的玻璃钢需要具有更大的机械强度,以满足技术不断发展的需要。浮空器中的飞艇是一种轻于空气的航空器,由巨大的流线型舱体、位于舱体下面的吊舱、起稳定控制作用的尾面和推进装置组成。其中,吊舱供人员乘坐和装载货物。目前,如浮空器吊舱这类高空用产品的壳体通常为金属结构,从而使产品存在重量大的问题,难以满足航天航空领域中对产品重量的要求。因此,在目前的航天航空领域中如浮空器吊舱这类高空用产品的外壳需要在具有较大机械强度的同时,也能够具有更轻的重量。技术实现要素:本发明的主要目的在于提供一种玻璃钢、其制备方法及浮空器吊舱,以解决现有技术中的玻璃钢在保证具有较大机械强度的基础上重量较大的问题。为了实现上述目的,根据本发明的一个方面,提供了一种玻璃钢,玻璃钢包括至少两层纤维层、设置于两层纤维层之间的胶膜层以及设置于胶膜层的至少一侧的石墨烯层,石墨烯层位于胶膜层与纤维层之间。进一步地,每相邻的两层纤维层之间均设置有胶膜层。进一步地,胶膜层的两侧均设置有石墨烯层。进一步地,石墨烯层的厚度为0.35~35nm。进一步地,石墨烯层占胶膜层的重量比为20~55%,纤维层占胶膜层的重量比为30~55%。进一步地,胶膜层的原料包括树脂和固化剂。根据本发明的另一方面,提供了一种玻璃钢的制备方法,制备方法包括:将石墨烯层设置于胶膜预备层的表面;将胶膜预备层设置于至少两个纤维层中各相邻的两个纤维层之间,并将胶膜预备层固化以形成胶膜层。进一步地,在将石墨烯层设置于胶膜预备层表面的步骤之前,制备方法还包括在基材上形成石墨烯层的步骤,石墨烯层包括至少一层石墨烯预备层。进一步地,当至少一层石墨烯预备层仅为一层时,形成石墨烯层的步骤包括:S1、在金属层上生长石墨烯预备层,形成预制物;S2、将预制物中的石墨烯预备层覆盖于基材的表面;S3、刻蚀去除金属层,在基材的表面形成石墨烯层。进一步地,当石墨烯预备层为N层,且石墨烯层的厚度为0.35~35nm时,N为大于等于3的自然数,形成石墨烯层的步骤包括:S1、在金属层上生长石墨烯预备层,形成预制物;S2、重复步骤S1,直至形成N个预制物;S3、将其中一预制物中的石墨烯预备层覆盖于基材的表面,并刻蚀去除该预制物中的金属层,形成一石墨烯结构层;S4、将另一预制物的石墨烯预备层覆盖于所述石墨烯结构层,刻蚀去除所述另一预制物中的金属层,形成另一石墨烯结构层;S5、重复步骤S4,直至N个所述预制物的石墨烯预备层均形成为石墨烯结构层,从而在所述基材的表面形成层叠设置的N层石墨烯结构层。进一步地,各石墨烯预备层的厚度为0.35~0.45nm。进一步地,金属层由铜、镍和铂中的任一种或多种制成。进一步地,基材由聚对苯二甲酸乙二醇酯、聚丙烯、聚碳酸酯和聚甲基丙烯酸甲酯中的任一种或多种制成。进一步地,在将石墨烯层设置于胶膜预备层表面的步骤之前,制备方法还包括以下步骤:将包括树脂的原料混合形成混料,并将混料制备成胶膜预备层。进一步地,在将混料制备成胶膜预备层的步骤中,将混料放入涂膜机以制备胶膜预备层,涂膜机中的滚筒温度为70~95℃,滚筒速度为2.5~5.5m/min。进一步地,原料还包括固化剂,在原料中固化剂占树脂的重量比为2~15%。进一步地,在将胶膜预备层固化以形成胶膜层的步骤之前,制备方法还包括:将纤维层进行电晕处理。进一步地,在将胶膜预备层固化以形成胶膜层的步骤中,固化的温度为110~150℃,固化的时间为1~3h,固化的压力为0.85~0.1Mpa。根据本发明的另一方面,还提供了一种浮空器吊舱,形成浮空器吊舱的舱体的材料包括玻璃钢,玻璃钢为上述的玻璃钢。应用本发明的技术方案,本发明提供了一种玻璃钢,该玻璃钢包括至少两层纤维层、设置于两层纤维层之间的胶膜层以及设置于胶膜层的至少一侧的石墨烯层,所述石墨烯层位于胶膜层与所述纤维层之间。由于石墨烯为层状结构,从而能够直接将上述层状石墨烯设置于胶膜层的表面,无需将石墨烯混入胶膜层中,进而有效地避免了石墨烯在胶膜层中单独掺杂导致的掺杂不均匀的问题;并且,由于很薄的石墨烯层就能够具有较大的杨氏模量和断裂强度,进而使设置有石墨烯层的玻璃钢在厚度很小的情况下就能够具有很大的机械强度。附图说明构成本申请的一部分的说明书附图用来提供对本发明的进一步理解,本发明的示意性实施例及其说明用于解释本发明,并不构成对本发明的不当限定。在附图中:图1示出了本发明实施方式所提供的一种玻璃钢的剖面结构示意图;图2示出了本发明实施方式所提供的另一种玻璃钢的剖面结构示意图;以及图3示出了本发明实施方式所提供的玻璃钢的制备方法的流程示意图。具体实施方式需要说明的是,在不冲突的情况下,本申请中的实施例及实施例中的特征可以相互组合。下面将参考附图并结合实施例来详细说明本发明。需要注意的是,这里所使用的术语仅是为了描述具体实施方式,而非意图限制根据本申请的示例性实施方式。如在这里所使用的,除非上下文另外明确指出,否则单数形式也意图包括复数形式,此外,还应当理解的是,当在本说明书中使用术语“包含”和/或“包括”时,其指明存在特征、步骤、操作、器件、组件和/或它们的组合。为了便于描述,在这里可以使用空间相对术语,如“在…...之上”、“在…...上方”、“在…...上表面”、“上面的”等,用来描述如在图中所示的一个器件或特征与其他器件或特征的空间位置关系。应当理解的是,空间相对术语旨在包含除了器件在图中所描述的方位之外的在使用或操作中的不同方位。例如,如果附图中的器件被倒置,则描述为“在其他器件或构造上方”或“在其他器件或构造之上”的器件之后将被定位为“在其他器件或构造下方”或“在其他器件或构造之下”。因而,示例性术语“在…...上方”可以包括“在…...上方”和“在…...下方”两种方位。该器件也可以其他不同方式定位(旋转90度或处于其他方位),并且对这里所使用的空间相对描述作出相应解释。正如
背景技术:
中所介绍的,目前如浮空器吊舱这类高空用产品的壳体通常为金属结构,从而使产品存在重量大的问题,难以满足航天航空领域中对产品重量的要求。本申请的发明人针对上述问题进行研究,提出了一种玻璃钢,如图1所示,玻璃钢包括至少两层纤维层20、设置于两层纤维层20之间的胶膜层10以及设置于胶膜层10的至少一侧的石墨烯层30,石墨烯层30位于胶膜层10与纤维层20之间。在本申请的玻璃钢中,由于石墨烯是层状结构,从而能够直接将上述层状石墨烯设置于胶膜层的表面,无需将石墨烯混入胶膜层中,进而有效地避免了石墨烯在胶膜层中单独掺杂导致的掺杂不均匀的问题;并且,由于很薄的石墨烯层就能够具有较大的杨氏模量和断裂强度,进而使设置有石墨烯层的玻璃钢在厚度很小的情况下就能够具有很大的机械强度。在本申请上述的玻璃钢中,石墨烯层具有孔隙且非常薄,从而能够通过胶粘层将石墨烯层固定于胶粘层与纤维层之间。优选地,胶膜层10的两侧均设置有石墨烯层30,其结构如图 2所示。即每层胶膜层10设置于相邻的上层纤维层20和下层纤维层20之间,而两层石墨烯层30分别设置于胶膜层10与上层纤维层20之间以及胶膜层10与下层纤维层20之间。本申请上述的玻璃钢中可以包括多层胶膜层10、多层纤维层20和至少一层石墨烯层30,每相邻的两层所述纤维层20之间均设置有胶膜层10,且至少一对相邻的胶膜层10和纤维层20之间设置有石墨烯层30。在上述层叠设置的玻璃钢中,每层纤维层20的厚度可以为0.1~0.3mm,每层胶膜层10的厚度可以为0.1~0.2mm,多层胶膜层10、多层纤维层20以及至少一层石墨烯层30层叠之后形成的玻璃钢的厚度可以为5~30mm。由于胶膜层10、纤维层20和石墨烯层30均具有较小的厚度,从而使由多层胶膜层10和多层纤维层20叠加形成的玻璃钢能够在具有更高机械强度的基础上,也具有较小的厚度。在本申请上述的玻璃钢中,优选地,所述石墨烯层30的厚度为0.35~35nm。在上述优选地实施方式厚度范围内,上述石墨烯层30具有更大的杨氏模量和断裂强度,从而使设置有石墨烯层30的玻璃钢能够具有更大的机械强度。在本申请上述的玻璃钢中,优选地,石墨烯层30与胶膜层10的重量比为20~55%,纤维层20与胶膜层10的重量比为30~55%。上述优选的参数范围能够使石墨烯层30具有合适的比重,进一步地保证了设置有石墨烯层30的玻璃钢在厚度很小的情况下就能够具有很大的机械强度;并且,在保证石墨烯层30能够使玻璃钢具有较大机械强度的基础上,也保证不会由于石墨烯的厚度较大而导致胶膜层10与纤维层20之间的胶粘度降低,从而使胶膜层10能够与纤维层20良好地粘结。在本申请上述的玻璃钢中,优选地,胶膜层10的原料还包括树脂和固化剂。优选地,上述树脂为环氧树脂。由于固化后的环氧树脂具有良好的物理、化学性能,它对金属和非金属材料的表面具有优异的粘结强度,硬度高,柔韧性好,从而使后续形成的胶膜层10能够具有较高的粘附性和机械强度,进而在后续工艺中更好地与石墨烯层30以及纤维层20进行连接,提高了最终玻璃钢的机械强度;并且,由于固化剂能够使树脂等原料更好地混合并固化以形成胶膜层10,从而保证了胶膜层10的稳定性,进而使石墨烯能够更为稳定的设置于胶膜层10的表面上,保证了玻璃钢在厚度很小的情况下就能够具有很大的机械强度。根据本发明的另一方面,提供了一种玻璃钢的制备方法,如图3所示。该制备方法包括:将石墨烯层30设置于所述胶膜预备层的表面;将至少两个纤维层20、设置于各相邻的两个所述纤维层20之间的所述胶膜预备层以及设置于所述胶膜预备层表面的所述石墨烯层30固化,以将所述胶膜预备层形成胶膜层10,并将所述石墨烯层30、所述胶膜层10和所述纤维层20形成所述玻璃钢。上述制备方法中由于时将石墨烯层设置于胶膜层的表面,从而有效地避免了石墨烯在胶膜层中单独掺杂导致的掺杂不均匀的问题;并且,由于很薄的石墨烯层就能够具有较大的杨氏模量和断裂强度,进而使设置有石墨烯层的玻璃钢在厚度很小的情况下就能够具有很大的机械强度。下面将结合图1和2更详细地描述根据本发明提供的玻璃钢的制备方法的示例性实施方式。然而,这些示例性实施方式可以由多种不同的形式来实施,并且不应当被解释为只限于这里所阐述的实施方式。应当理解的是,提供这些实施方式是为了使得本申请的公开彻底且完整,并且将这些示例性实施方式的构思充分传达给本领域普通技术人员。首先,将石墨烯层30设置于胶膜预备层表面。将上述石墨烯层30设置于胶膜层10的表面,能够有效地避免石墨烯在胶膜层10中单独掺杂导致的掺杂不均匀等问题;并且,由于形成的胶膜预备层表面设置有石墨烯,而石墨烯能够在厚度很小的情况下就具有较大的杨氏模量和断裂强度,进而使后续制备而成的玻璃钢在厚度很小的情况下就能够具有很大的机械强度。可以将包括树脂的原料混合形成混料,并将混料制备成胶膜预备层。优选地,上述树脂为环氧树脂。由于固化后的环氧树脂具有良好的物理、化学性能,它对金属和非金属材料的表面具有优异的粘结强度,硬度高,柔韧性好,从而保证了胶膜层10的稳定性,进而使石墨烯能够更为稳定的设置于胶膜层10的表面上,保证了玻璃钢在厚度很小的情况下就能够具有很大的机械强度。可以在高温条件下将包括树脂的原料混合形成混料,优选地,将包括树脂的原料在温度为30~55℃的条件下混合形成混料。在上述优选的参数范围内,形成的胶膜层10能够具有更高的稳定性,进而使石墨烯能够更为稳定的设置于胶膜层10的表面上,保证了玻璃钢在厚度很小的情况下就能够具有很大的机械强度。优选地,原料还包括固化剂,可以采用丙烯酸胺作为固化剂,在原料中固化剂占树脂的重量比为2~15%。在上述优选地实施方式中,固化剂能够使形成的胶膜层10具有更高的稳定性,进而使石墨烯能够更为稳定的设置于胶膜层10的表面上,保证了玻璃钢在厚度很小的情况下就能够具有很大的机械强度。制备上述胶膜预备层的方法可以有很多种,在一种优选的实施方式中,将混料放入涂膜机以制备成胶膜预备层,涂膜机中的滚筒温度为70~95℃,滚筒速度为2.5~5.5m/min。采用上述优选的工艺参数能够更为迅速有效地制备出胶膜预备层,并且使由胶膜预备层固化而成的胶膜层10具有均匀的厚度以及稳定的性质。优选地,在将石墨烯层30设置于胶膜预备层表面的步骤之前,制备方法还包括在基材上形成石墨烯层30的步骤,石墨烯层30包括至少一层石墨烯预备层。当上述至少一层石墨烯预备层仅为一层时,形成石墨烯层30的步骤包括:S1、在金属层上生长石墨烯预备层,形成预制物;S2、将预制物中的石墨烯预备层覆盖于基材的表面;S3、刻蚀去除金属层,以在基材的表面形成石墨烯层30。通过上述优选的实施方式能够有效地制备出石墨烯层30,且使形成的石墨烯层30具有较大的杨氏模量和断裂强度。当上述石墨烯预备层为N层,且石墨烯层30的厚度为0.35~35nm时,N为大于等于3的自然数,形成石墨烯层30的步骤包括:S1、在金属层上生长石墨烯预备层,形成预制物;S2、 重复步骤S1,直至形成N个预制物;S3、将其中一预制物中的石墨烯预备层覆盖于基材表面,并刻蚀去除该预制物中的金属层,形成一石墨烯结构层;S4、将另一预制物的石墨烯预备层覆盖于石墨烯结构层,刻蚀去除第一预制物中的金属层,形成另一石墨烯结构层;S5,重复步骤S4,直至N个预制物的石墨烯预备层均形成为石墨烯结构层,从而在基材表面形成层叠设置的N层石墨烯结构层。上述实施方式是将金属层上生长的石墨烯预备层进行多层叠加,使叠加后形成的石墨烯层30的厚度达到机械强度达到所需的数值(0.35~35nm)后,再将上述石墨烯层30转移至胶膜预备层的表面。优选地,每层石墨烯预备层的厚度为0.35~0.45nm。上述优选的厚度参数能够使各层石墨烯预备层具有较大的杨氏模量和断裂强度,从而可以使玻璃钢达到所需机械强度的同时,厚度和重量尽量地小。优选地,金属层由铜、镍和铂中的任一种或多种制成,基材由聚对苯二甲酸乙二醇酯、聚丙烯、聚碳酸酯和聚甲基丙烯酸甲酯中的任一种或多种制成。利用上述材料制成的金属层能够更为快速有效地生长石墨烯预备层,且使叠加而成的石墨烯层30具有较大的机械强度;选择上述材料制成的基材能够更为有效地使金属层被刻蚀掉,并更为有效地将石墨烯层30转移至胶膜预备层的表面。在完成将石墨烯层30设置于胶膜预备层的表面的步骤之后,将胶膜预备层设置于至少两个纤维层20中各相邻的两个纤维层20之间,并将胶膜预备层固化以形成胶膜层10,上述石墨烯层30、胶膜层10和纤维层20形成玻璃钢。由于上述玻璃钢是由将胶膜预备层固化之后的胶膜层10、纤维层20与石墨烯层30形成的,且设置有石墨烯层30的胶膜层10在石墨烯层30的作用下能够具有较大的杨氏模量和断裂强度,从而使制备而成的玻璃钢在厚度很小的情况下就能够具有很大的机械强度。上述纤维层20可以为纤维束或纤维织物,且纤维体为麻纤维、碳纤维、玻璃纤维、丙纶、芳纶、玄武岩纤维和超高分子聚乙烯中的任一种或多种。更为优选地,纤维层20为超高分子聚乙烯。上述优选地纤维层20材料具有较高的韧性与机械强度,从而采用上述优选地纤维层20材料能够使形成的玻璃钢具有更高的机械强度。优选地,在将胶膜预备层固化以形成胶膜层10的步骤中,固化的温度为110~150℃,固化的时间为1~3h,固化的压力为0.85~1.0Mpa。采用上述优选的工艺参数能够更为快速有效地对胶膜预备层、纤维层20以及石墨烯层30进行固化处理,从而使玻璃钢快速有效地固化成型,并且能够进一步提高玻璃钢的机械性能。在一种优选的实施方式中,在将胶膜预备层固化以形成胶膜层10的步骤之前,制备方法还包括:将纤维层20进行电晕处理。由于电晕处理是一种电击处理,它使承印物的表面具有更高的附着性,从而使经过电晕处理的纤维层20能够具有更高的附着性,进而更为牢固地与墨烯层30和胶膜层10进行连接。上述电晕处理是利用高频率交流电压在纤维层20欲与胶膜层10进行连接的表面进行电晕放电,优选地,高频率交流电压为5000~15000V/m2。根据本发明的另一方面,提供了一种浮空器吊舱,形成浮空器吊舱的舱体的材料包括玻璃钢,玻璃钢由上述的制备方法制备而成。其中,上述浮空器可以包括高空气球和飞艇等。由于上述玻璃钢包括石墨烯层,而石墨烯层具有较大的杨氏模量和断裂强度,从而使设置有石墨烯层的玻璃钢在厚度很小即重量很轻的情况下就能够具有很大的机械强度。下面将结合实施例进一步说明本申请提供的玻璃钢的制备方法。实施例1本实施例提供的玻璃钢的制备方法的步骤包括:首先,将双酚A的环氧树脂和作为固化剂的丙烯酸胺在温度为30℃的条件下混合形成混料,其中,固化剂占树脂的重量比为2%,并将上述混料放入涂膜机以制备成胶膜预备层,涂膜机中的滚筒温度为70℃,滚筒速度为2.5m/min;其次,在金属镍层上生长石墨烯预备层,将连接金属层的石墨烯预备层覆盖于基材的表面,并刻蚀掉金属层,重复上述步骤以在PET基材的表面形成厚度为0.35nm的石墨烯层;最后,选用超高分子聚乙烯作为纤维层,对纤维层在高频率交流电压为5000V/m2的条件下进行电晕处理,将石墨烯层设置于胶膜预备层的表面,并将设置有石墨烯层的胶膜预备层设置于两层纤维层之间并固化,形成玻璃钢,结构如图1所示,其中,固化的温度为110℃,固化的时间为1h,固化的压力为0.85Mpa。实施例2本实施例提供的玻璃钢的制备方法的步骤包括:首先,将双酚A的环氧树脂和作为固化剂的丙烯酸胺在温度为40℃的条件下混合形成混料,其中,固化剂占树脂的重量比为7%,并将上述混料放入涂膜机以制备成胶膜预备层,涂膜机中的滚筒温度为80℃,滚筒速度为4m/min;其次,在金属镍层上生长石墨烯预备层,将连接金属层的石墨烯预备层覆盖于基材的表面,并刻蚀掉金属层,重复上述步骤以在PET基材的表面形成厚度为10nm的石墨烯层;最后,选用超高分子聚乙烯作为纤维层,对纤维层在高频率交流电压为10000V/m2的条件下进行电晕处理,将石墨烯层设置于胶膜预备层的表面,并将设置有石墨烯层的胶膜预备层设置于两层纤维层之间并固化,形成玻璃钢,结构如图1所示,其中,固化的温度为130℃,固化的时间为2h,固化的压力为0.9Mpa。实施例3本实施例提供的玻璃钢的制备方法的步骤包括:首先,将双酚A的环氧树脂和作为固化剂的丙烯酸胺在温度为55℃的条件下混合形成混料,其中,固化剂占树脂的重量比为15%,并将上述混料放入涂膜机以制备成胶膜预备层,涂膜机中的滚筒温度为95℃,滚筒速度为5.5m/min;其次,在金属镍层上生长石墨烯预备层,将连接金属层的石墨烯预备层覆盖于基材的表面,并刻蚀掉金属层,重复上述步骤以在PET基材的表面形成厚度为35nm的石墨烯层;最后,选用超高分子聚乙烯作为纤维层,对纤维层在高频率交流电压为15000V/m2的条件下进行电晕处理,将石墨烯层设置于胶膜预备层的表面,并将设置有石墨烯层的胶膜预备层设置于两层纤维层之间并固化,形成玻璃钢,结构如图1所示,其中,固化的温度为150℃,固化的时间为3h,固化的压力为1.0Mpa。实施例4本实施例提供的玻璃钢的制备方法的步骤包括:首先,将双酚A的环氧树脂和作为固化剂的丙烯酸胺在温度为55℃的条件下混合形成混料,其中,固化剂占树脂的重量比为15%,并将上述混料放入涂膜机以制备成重量相同的两个胶膜预备层,涂膜机中的滚筒温度为95℃,滚筒速度为5.5m/min;其次,在金属镍层上生长石墨烯预备层,将连接金属层的石墨烯预备层覆盖于基材的表面,并刻蚀掉金属层,重复上述步骤以在PET基材的表面形成厚度为35nm的石墨烯层,重复上述步骤以制备出与上述石墨烯层尺寸相同的第二个石墨烯层;最后,选用超高分子聚乙烯作为纤维层,提供三个纤维层并对纤维层在高频率交流电压为15000V/m2的条件下进行电晕处理,将石墨烯层一一对应设置于胶膜预备层的表面,并将表面设置有石墨烯层的每个胶膜预备层分别设置于相邻的两个纤维层之间并固化,形成玻璃钢,结构如图2所示,其中,固化的温度为150℃,固化的时间为3h,固化的压力为1.0Mpa。对比例1本对比例提供的玻璃钢的制备方法的步骤包括:首先,将双酚A的环氧树脂和作为固化剂的丙烯酸胺在温度为55℃的条件下混合形成混料,其中,固化剂占树脂的重量比为15%,并将上述混料放入涂膜机以制备成重量相同的两个胶膜预备层,涂膜机中的滚筒温度为95℃,滚筒速度为5.5m/min;然后,选用超高分子聚乙烯作为纤维层,提供三个纤维层并对纤维层在高频率交流电压为15000V/m2的条件下进行电晕处理,将每个胶膜预备层分别设置于相邻的两个纤维层之间并固化,形成玻璃钢,结构如图2所示,其中,固化的温度为150℃,固化的时间为3h,固化的压力为1.0Mpa。对比例2本对比例提供的金属层的制备方法的步骤包括:利用铝合金材料制备金属层,使金属层与上述实施例1至4中的玻璃钢具有相同的尺寸。对上述实施例1至4和对比例1提供的玻璃钢进行拉伸强度和重量的测试,测试结果如下表所示。项目重量g拉伸强度MPa实施例133415实施例235440实施例336450实施例445465对比例156390对比例2100175从上表可以看出,本申请实施例1至4中玻璃钢的拉伸强度可以达到415~465MPa,远大于对比例1和2中玻璃钢的拉伸强度;并且,与对比例1和2中制备玻璃钢相比,实施例1至4中玻璃钢也具有更轻的重量,即实施例1至4中的玻璃钢在重量很轻的情况下具有很大的机械强度。从以上的描述中,可以看出,本发明上述的实施例实现了如下技术效果:1)由于玻璃钢中的胶膜层以石墨烯为原料制备而成,从而使很薄的胶膜层就能够具有较大的杨氏模量和断裂强度,进而使设置有胶膜层的玻璃钢在厚度很小即重量很轻的情况下就能够具有很大的机械强度;2)由于石墨烯为层状结构,从而能够直接将上述层状石墨烯设置于胶膜层的表面,无需将石墨烯混入胶膜层中,进而有效地避免了石墨烯在胶膜层中单独掺杂导致的掺杂不均匀的问题;3)由于玻璃钢是透明的,人在浮空器上还能够透过玻璃钢看到天空或地上广阔的风景。以上所述仅为本发明的优选实施例而已,并不用于限制本发明,对于本领域的技术人员来说,本发明可以有各种更改和变化。凡在本发明的精神和原则之内,所作的任何修改、等同替换、改进等,均应包含在本发明的保护范围之内。当前第1页1 2 3