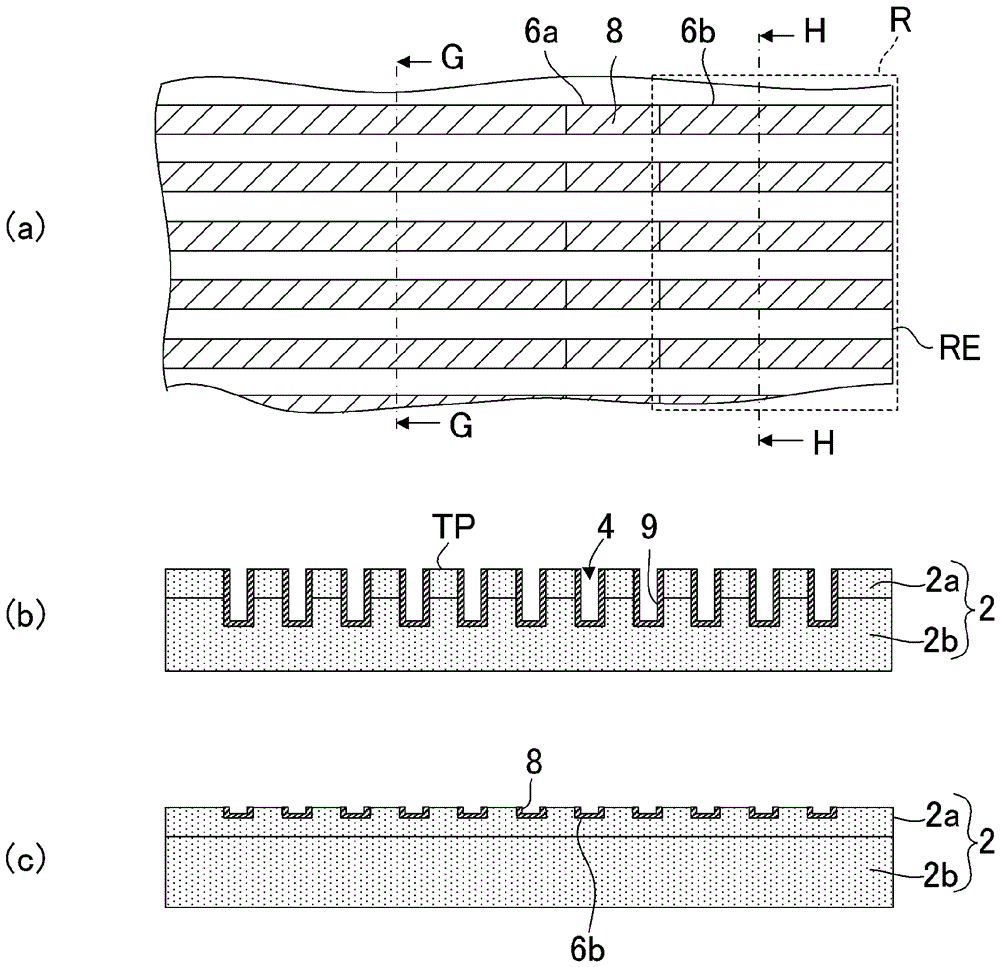
本发明涉及吐出液滴而在被记录介质进行记录的液体喷射头的制造方法、液体喷射头以及液体喷射装置。
背景技术:近年来,将墨滴吐出至记录纸等而记录字符或图形,或者将液体材料吐出至元件基板的表面而形成功能性薄膜的喷墨方式的液体喷射头得到利用。该方式将墨或液体材料(以下,称为液体)从液体罐经由供给管引导至通道,对填充于通道的液体施加压力而将液体从与通道连通的喷嘴吐出。在吐出液体时,使液体喷射头或被记录介质移动而记录字符或图形,或者形成既定形状的功能性薄膜。作为这种液体喷射头,已知剪切模式型。剪切模式型的液体喷射头在沿相对表面垂直的方向实施极化处理的压电性材料基板的表面形成多个并列的槽,沿邻接的槽之间的侧壁的厚度方向施加电场而使侧壁发生厚度滑移变形,从而对填充于槽的液体施加压力,将液滴从与槽连通的喷嘴吐出。近年来,伴随着记录点的高密度化的要求,槽的窄间距化、电极图案的细微化不断取得进展。在专利文献1中,记载有在压电性材料基板形成多个槽,并通过非电解镀敷法形成导电膜而制造液体喷射头的制造方法。首先,利用粘接剂将沿基板表面的垂直方向实施极化处理的2块压电性材料基板,极化方向彼此相反朝向地粘合。接着,利用液体抗蚀剂或干膜覆盖在压电性材料基板的上表面整个面并固化。接着,使用切割刀片形成槽宽为70μm、深度为300μm的平行的多列槽。接着,实施亲水化处理以改良压电性材料基板的表面,接着进行镀敷预处理使镀敷催化剂附着于压电性材料基板的整个面。接着,通过非电解镀敷法形成镀敷膜。接着,通过除去抗蚀剂膜(或干膜)的剥离法从驱动壁的上表面除去抗蚀剂膜(或干膜)和镀敷膜。图22是上述处理后的压电性材料基板101的立体图(专利文献1的图7)。在压电性材料基板101形成有包含多个平行的槽的通道部102。各通道部102由驱动壁103隔离。通过剥离法除去各驱动壁103的上表面的镀敷膜120而露出压电性材料基板101,其他表面被镀敷膜120覆盖。接着,使感光性电沉积抗蚀剂附着于压电性材料基板101而在镀敷膜120上形成抗蚀剂膜130。接着,通过遮光掩模对形成电极图案的区域进行遮光,并照射紫外线而曝光。接着,浸渍于显影液将除去镀敷膜120的区域的抗蚀剂膜130除去,使镀敷膜120露出。图23(a)~(c)表示通过曝光显影形成抗蚀剂膜130的图案的压电性材料基板101的表面(专利文献1的图9)。图23(a)表示压电性材料基板101的前端面,端面整个面的抗蚀剂膜130通过曝光显影而被除去,镀敷膜120露出至整个面。图23(b)表示压电性材料基板101的后端面,使各驱动壁103的后端面的镀敷膜120沿纵向露出。图23(c)表示压电性材料基板101的底面,使镀敷膜120以与露出于后端面的各镀敷膜120连续的方式露出。接着,进行蚀刻处理除去露出的镀敷膜120。图24(a)~(c)表示蚀刻处理后的压电性材料基板101的表面,分别与图23(a)~(c)对应。从压电性材料基板101的前端面除去镀敷膜120而露出压电性材料基板101,电极104残留于驱动壁103的侧面(图24(a))。压电性材料基板101的后端面形成有通过镀敷膜120的除去部140而电分离的电极图案150(图24(b))。压电性材料基板101的背面形成有与后端面的电极图案150电连接的电极图案150(图24(c))。接着,在压电性材料基板101的上表面以闭塞各槽的方式接合未图示的盖部件,在压电性材料基板101的前侧的除去镀敷膜120的表面粘接喷嘴板,并在压电性材料基板101的底面经由各向异性导电膜接合柔性印刷基板,使柔性印刷基板的布线和底面的各电极图案150电连接。专利文献1:日本特开2002-172789号公报。在浸渍于镀敷液而形成电极的情况下,为了确保压电性材料基板101与镀敷膜120之间的密合性,需要在进行镀敷处理前对压电性材料基板101的表面进行预处理。然而,抗蚀剂膜没有对预处理液的耐受性,由于预处理液,抗蚀剂膜130溶解并剥离。因此,如专利文献1所记载的那样,难以从驱动壁103的上表面均匀地除去镀敷膜120。因此,考虑不使用上述那样的非电解镀敷法而通过蒸镀法沉积导电膜,并通过剥离法形成电极图案。然而,近年来窄间距化得到推进,通道部102的槽宽不断变窄。在蒸镀时金属蒸汽难以进入狭窄的槽宽,因此为了在壁面形成必要厚度的驱动电极需要长时间的蒸镀。因此,沉积于驱动壁103的上端面的金属膜变厚,难以通过剥离法除去。另外,在专利文献1中,在镀敷膜120上形成抗蚀剂膜130,分别在压电性材料基板101的后端面和底面设置遮光掩模并进行曝光、显影,对镀敷膜120进行蚀刻而形成图案。因此,制造过程较长,电极图案的形成需要很多时间。另外,考虑不使用剥离法或光刻及蚀刻法,而通过激光加工形成镀敷膜120的图案的方法。然而,在激光加工中必须逐行加工电极图案,因此电极图案的形成同样需要很多时间。
技术实现要素:本发明是鉴于上述课题而做出的,其目的在于,提供不使用抗蚀剂等感光性树脂而能对金属膜形成图案的液体喷射头及其制造方法。本发明的液体喷射头的制造方法包括:槽形成工序,在致动器基板的表面的后端附近设定端子区域,沿从所述表面的前端至所述端子区域的方向形成并列的多个吐出槽;浅槽形成工序,在所述端子区域形成浅槽;导电膜形成工序,在所述表面和所述吐出槽及所述浅槽的侧面及底面形成导电膜;磨削工序,磨削并除去形成于所述表面的所述导电膜;盖板接合工序,以使所述端子区域露出并覆盖所述吐出槽的方式将盖板接合至所述表面;以及喷嘴板粘接工序,将喷嘴板粘接至所述致动器基板的所述吐出槽开口的侧面。另外,所述浅槽形成工序是在所述吐出槽与所述端子区域之间形成与所述吐出槽连续的第一浅槽,并在所述端子区域形成与所述第一浅槽连续的第二浅槽的工序。另外,所述槽形成工序是在邻接的所述吐出槽之间从所述前端直至所述后端,与所述吐出槽并列地形成虚设槽的工序;所述浅槽形成工序是沿与所述虚设槽交叉的方向形成所述第二浅槽,并且在相对所述第二浅槽而更靠近所述后端的一侧,与所述第二浅槽并列地形成第三浅槽的工序;包括:倒角工序,对所述第二浅槽与所述虚设槽交叉的交叉部的所述虚设槽的侧面与所述第二浅槽的侧面及底面之间的角部进行倒角。另外,包括:背面磨削工序,磨削所述致动器基板的与所述表面相反的一侧的背面,除去形成于所述虚设槽的底面的所述导电膜;以及基底基板接合工序,将基底基板接合至所述背面。另外,包括:柔性基板粘接工序,将形成有共用布线和个别布线的柔性基板以使所述共用布线与形成于所述第二浅槽的底面的所述导电膜电连接、使所述个别布线与形成于所述第三浅槽的底面的所述导电膜电连接的方式,粘接至所述端子区域。另外,所述槽形成工序是从所述前端直至所述后端形成吐出槽,并在邻接的所述吐出槽之间从所述前端直至所述后端,与所述吐出槽并列地形成虚设槽的工序;所述浅槽形成工序是在所述端子区域沿与所述吐出槽交叉的方向形成第二浅槽,并且在相对所述第二浅槽而更靠近所述后端的一侧,与所述第二浅槽并列地形成第三浅槽的工序;包括对所述第二浅槽与所述虚设槽交叉的交叉部的所述虚设槽的侧面与所述第二浅槽的侧面及底面之间的角部、以及所述第三浅槽与所述吐出槽交叉的交叉部的所述吐出槽的侧面与所述第三浅槽的侧面及底面之间的角部进行倒角的工序。另外,包括:背面磨削工序,磨削所述致动器基板的与所述表面相反的一侧的背面,除去形成于所述虚设槽的底面的所述导电膜;以及基底基板接合工序,将基底基板接合至所述背面。另外,包括:柔性基板粘接工序,将形成有共用布线和个别布线的柔性基板以使所述共用布线与形成于所述第二浅槽的底面的所述导电膜电连接、使所述个别布线与形成于所述第三浅槽的底面的所述导电膜电连接的方式,粘接至所述端子区域。另外,所述导电膜形成工序是通过镀敷法形成所述导电膜的工序。本发明的液体喷射头包括:致动器基板,在表面的后端附近设定有端子区域,从所述表面的前端朝向所述端子区域的方向形成有并列的多个吐出槽,并在所述吐出槽的侧面形成有驱动电极;盖板,以覆盖所述吐出槽并使所述端子区域露出的方式,接合于所述致动器基板的所述表面;喷嘴板,粘接于所述致动器基板的所述吐出槽开口的侧面;柔性基板,具有布线电极,并粘接于所述端子区域。在所述吐出槽与所述端子区域之间的所述表面形成有第一浅槽,在所述端子区域形成有与所述第一浅槽深度不同的第二浅槽,在所述第一及所述第二浅槽的侧面和底面形成有与所述驱动电极电连接的导电膜,所述导电膜与所述布线电极电连接。另外,包括:致动器基板,在表面的后端附近设定有端子区域,从所述表面的前端朝向所述端子区域的方向形成有并列的多个吐出槽,在邻接的所述吐出槽之间从所述前端直至所述后端,与所述吐出槽并列地形成有虚设槽,并在所述吐出槽及所述虚设槽各自的侧面形成有驱动电极;基底基板,接合于所述致动器基板的与所述盖板相反的一侧的背面;盖板,以覆盖所述吐出槽并使所述端子区域露出的方式,接合于所述致动器基板的所述表面;喷嘴板,粘接于所述致动器基板的所述吐出槽开口的侧面;柔性基板,具有布线电极,并粘接于所述端子区域。在所述端子区域形成有浅槽,在所述浅槽的侧面和底面形成有与所述驱动电极电连接的导电膜,所述导电膜与所述布线电极电连接。另外,所述基底基板露出至所述虚设槽的底面。另外,在所述吐出槽与所述端子区域之间的所述表面形成有第一浅槽,在所述端子区域,与所述第一浅槽连续地形成有所述浅槽所包含的第二浅槽。另外,所述浅槽包含第三浅槽,所述第二浅槽沿与所述虚设槽交叉的方向形成,所述第三浅槽与所述第二浅槽并列地形成于相对所述第二浅槽而更靠近所述后端的一侧,对所述第二浅槽与所述虚设槽交叉的交叉部的所述虚设槽的侧面与所述第二浅槽的侧面及底面的角部,进行倒角而除去所述导电膜。另外,所述布线电极包括共用布线和个别布线,形成于所述第二浅槽的底面的所述导电膜与所述共用布线电连接,形成于所述第三浅槽的底面的所述导电膜与所述个别布线电连接。另外,所述浅槽包含第二浅槽和第三浅槽,所述吐出槽从所述前端形成至所述后端,所述第二浅槽沿与所述吐出槽交叉的方向形成,所述第三浅槽与所述第二浅槽并列地形成于相对所述第二浅槽而更靠近所述后端的一侧,对所述第二浅槽与所述虚设槽交叉的交叉部的所述虚设槽的侧面与所述第二浅槽的侧面及底面之间的角部、以及所述第三浅槽与所述吐出槽交叉的交叉部的所述吐出槽的侧面与所述第三浅槽的侧面及底面之间的角部进行倒角而除去所述导电膜。另外,所述布线电极包括共用布线和个别布线,形成于所述第二浅槽的底面的所述导电膜与所述共用布线电连接,形成于所述第三浅槽的底面的所述导电膜与所述个别布线电连接。本发明的液体喷射装置包括:上述液体喷射头;移动机构,使所述液体喷射头往复移动;液体供给管,将液体供给至所述液体喷射头;以及液体罐,将所述液体供给至所述液体供给管。本发明的液体喷射头的制造方法包括:槽形成工序,在致动器基板的表面的后端附近设定端子区域,沿从表面的前端至端子区域的方向形成并列的多个吐出槽;浅槽形成工序,在端子区域形成浅槽;导电膜形成工序,在表面和吐出槽及浅槽的侧面及底面形成导电膜;磨削工序,磨削并除去形成于表面的导电膜;盖板接合工序,以使端子区域露出并覆盖吐出槽的方式,将盖板接合至表面;以及喷嘴板粘接工序,将喷嘴板粘接至致动器基板的吐出槽开口的侧面。总之,由于通过磨削法将导电膜加工成电极图案,能够通过制造工时较少的简便的方法制造液体喷射头。附图说明图1是本发明的第一实施方式所涉及的液体喷射头的说明图;图2是表示本发明的第一实施方式所涉及的液体喷射头的制造方法的工序图;图3是用于说明本发明的第一实施方式所涉及的液体喷射头的各制造工序的图;图4是用于说明本发明的第一实施方式所涉及的液体喷射头的各制造工序的图;图5是用于说明本发明的第一实施方式所涉及的液体喷射头的各制造工序的图;图6是用于说明本发明的第一实施方式所涉及的液体喷射头的各制造工序的图;图7是用于说明本发明的第一实施方式所涉及的液体喷射头的各制造工序的图;图8是本发明的第二实施方式所涉及的液体喷射头的说明图;图9是表示本发明的第二实施方式所涉及的液体喷射头的制造方法的工序图;图10是用于说明本发明的第二实施方式所涉及的液体喷射头的各制造工序的图;图11是用于说明本发明的第二实施方式所涉及的液体喷射头的各制造工序的图;图12是用于说明本发明的第二实施方式所涉及的液体喷射头的各制造工序的图;图13是用于说明本发明的第二实施方式所涉及的液体喷射头的各制造工序的图;图14是用于说明本发明的第二实施方式所涉及的液体喷射头的各制造工序的图;图15是用于说明本发明的第二实施方式所涉及的液体喷射头的各制造工序的图;图16是用于说明本发明的第二实施方式所涉及的液体喷射头的各制造工序的图;图17是用于说明本发明的第二实施方式所涉及的液体喷射头的各制造工序的图;图18是本发明的第三实施方式所涉及的液体喷射头的截面示意图;图19是本发明的第三实施方式所涉及的液体喷射头的磨削工序之后的致动器基板的示意性的立体图;图20是本发明的第三实施方式所涉及的液体喷射头的倒角工序之后的致动器基板的示意性的立体图;图21是本发明的第四实施方式所涉及的液体喷射装置的示意性的立体图;图22是现有公知的通过剥离法将镀敷膜从驱动壁的上表面除去的压电性材料基板的立体图;图23表示现有公知的对抗蚀剂膜进行构图的压电性材料基板的表面;图24表示现有公知的蚀刻处理后的压电性材料基板的表面。附图标记说明1液体喷射头;2致动器基板;2a、2b压电体基板;4吐出槽;5虚设槽;6浅槽、6a第一浅槽、6b第二浅槽、6c第三浅槽;8导电膜;9、9a、9b驱动电极;10盖板;11液体供给室;12喷嘴板;13喷嘴;14基底基板;15柔性基板;16布线电极、17共用布线、18个别布线;19、19a、19b侧壁;20狭缝;21倒角部;23密封材料;24通道;TP表面、BP背面、FE前端、RE后端;R端子区域。具体实施方式(第一实施方式)图1~图7是用于说明本发明的第一实施方式所涉及的液体喷射头及其制造方法的图。图1是液体喷射头1的说明图,图2是表示液体喷射头1的制造方法的工序图,图3~图7是用于说明液体喷射头1的各制造工序的图。图1(a)是液体喷射头1的示意性的分解立体图。图1(b)是AA部分的截面示意图,图1(c)是BB部分的截面示意图的一部分,各自是从箭头方向观察的图。如图1所示,液体喷射头1包括:致动器基板2,包含压电体材料;盖板10,接合于致动器基板2的表面TP;喷嘴板12,粘接于致动器基板2及盖板10的前端FE;以及柔性基板15,粘接于在致动器基板2的表面TP的后端RE附近设定的端子区域R。致动器基板2具有层叠沿相对基板面垂直的方向极化、极化方向为彼此相反方向的2块压电体基板的构造。致动器基板2在表面TP的后端RE附近设定有端子区域,沿从表面TP的前端FE至端子区域R的方向形成有并列的多个吐出槽4,在该吐出槽4的侧面形成有驱动电极9。盖板10以覆盖多个吐出槽4并使端子区域R露出的方式接合于致动器基板2的表面TP。由盖板10闭塞吐出槽4的上部开口而构成通道24。在盖板10的后侧形成有液体供给室11,液体供给室11与各通道24连通并能进行液体的供给。喷嘴板12粘接于致动器基板2的吐出槽4开口的侧面。喷嘴13形成于喷嘴板12,并与在致动器基板2的侧面开口的吐出槽4(通道24)连通。如图1(b)及(c)所示,吐出槽4以一定的深度从前端FE形成至中间,从中间开始逐渐变浅地形成。从吐出槽4的后端RE侧的端部至端子区域R之间形成有与吐出槽4连续的第一浅槽6a。而且,在端子区域R形成有第一浅槽6a和与第一浅槽6a深度不同的第二浅槽6b。在第一浅槽6a及第二浅槽6b的侧面及底面形成有导电膜8,形成于吐出槽4的侧面的驱动电极9与形成于吐出槽4的底面的导电膜8连续并电连接。在柔性基板15的致动器基板2侧,在与各第二浅槽6b对应的位置形成有布线电极16。柔性基板15经由未图示的各向异性导电膜粘接于端子区域R。由此,布线电极16经由第一及第二浅槽6a、6b的导电膜8与驱动电极9电连接。液体喷射头1被如下地驱动。从未图示的液体罐供给的液体供给至液体供给室11,进一步供给至各吐出槽4。当驱动信号从柔性基板15的布线电极16传递至驱动电极9时,吐出槽4的两侧的侧壁19发生厚度滑移变形,两个侧壁19所夹着的通道24的容积瞬间增大,接着缩小。由此,液体从液体供给室11引入至通道24,并作为液滴从喷嘴13吐出。图1所示的情况是通过3周期驱动(3サイクル駆動)从各吐出槽4依次吐出液滴。在此,致动器基板2能够使用由钛锆酸铅(PZT)构成的压电陶瓷基板。预先沿相对板面垂直的方向对2块压电陶瓷基板实施极化处理,并使极化方向为彼此相反朝向地粘合而形成致动器基板2。通过溅射法、上蒸镀法或者非电解镀敷法能够将导电膜8形成为0.1μm~5μm的厚度。如果通过非电解镀敷法形成Ni-P,进一步层叠Au,则能够以低成本且在短时间内形成导电膜8。使用在外周端部埋入金刚石的切割刀片(金刚石砂轮)能够连续地形成吐出槽4、第一浅槽6a及第二浅槽6b。盖板10使用线膨胀系数与致动器基板2接近的材料。例如,能够使用与致动器基板2相同的钛锆酸铅陶瓷。喷嘴板12能够使用聚酰亚胺薄膜。吐出槽4的深度为300μm~400μm,吐出槽4的宽度及侧壁19的厚度为40μm~100μm。第一浅槽6a与第二浅槽6b深度不同。例如,能够比第二浅槽6b更浅地形成第一浅槽6a。第一浅槽6a通过将盖板10经由粘接剂接合至其上部而被密封。在该情况下,优选形成于第一浅槽6a的底面的导电膜8的上表面与盖板10的致动器基板2侧的表面之间的间隙较小的方式。这是为了防止供给至吐出槽4的液体滞留于第一浅槽6a。另一方面,柔性基板15能够通过使布线电极16经由各向异性导电膜嵌合于第二浅槽6b而牢固地粘接。因此,优选比第一浅槽6a更深地形成第二浅槽6b。此外,也能比第二浅槽6b更深地形成第一浅槽6a。在该情况下,在第一浅槽6a与盖板10之间充分地供给粘接材料,对形成于第一浅槽6a的底面的导电膜8的上表面与盖板10之间进行密封即可。另外,能够根据需要在盖板10的后端与致动器基板2的角部模制密封材料而完全地密封第一浅槽6a。第一浅槽6a及第二浅槽6b具有0.1μm~30μm的深度,并全都具有与吐出槽4相同的槽宽。这样,在致动器基板2的表面TP的端子区域R形成第二浅槽6b,并在该第二浅槽6b和吐出槽4形成导电膜8即可,因此能够通过简便的方法形成液体喷射头1。使用图2对本发明的第一实施方式所涉及的液体喷射头1的制造方法进行说明。如图2所示,首先,在基板形成工序S0中,形成包含压电体材料的致动器基板2。接着,在槽形成工序S1中,在致动器基板2的表面TP的后端RE附近设定端子区域R,沿从表面TP的前端FE至端子区域R的方向形成并列的多个吐出槽4。接着,在浅槽形成工序S2中,在致动器基板2的端子区域R形成与吐出槽4连通的第一浅槽6a。接着,在导电膜形成工序S3中,在致动器基板2的表面TP和吐出槽4及第一浅槽6a的侧面及底面形成导电膜。此外,如果通过非电解镀敷法形成导电膜,则能够以低成本在短时间内形成膜,因此特别地有效。接着,在磨削工序S4中,磨削并除去形成于致动器基板2的表面TP的导电膜8。由此,在致动器基板2的表面TP形成导电图案。接着,在盖板接合工序S5中,以使致动器基板2的端子区域R露出并覆盖吐出槽4的方式,将盖板10接合至表面TP。接着,在喷嘴板粘接工序S6中,将喷嘴板12粘接至致动器基板2的吐出槽4开口的侧面。接着,在柔性基板粘接工序S10中,以使布线电极16与形成于第二浅槽6b的底面的导电膜8电连接的方式将形成有布线电极16的柔性基板15粘接至端子区域R。这样,在本发明的液体喷射头1的制造方法中,在致动器基板2的表面形成浅槽,接着在整个面形成导电膜之后,磨削基板表面而留下沉积于浅槽的导电膜的图案,以此代替在形成导电膜的前后涂敷感光性树脂,并在形成感光性树脂的图案后通过剥离法或者蚀刻法形成导电膜的图案。因此,能够图案形成工时较少地、不需要反复地进行抗蚀剂膜的涂敷、显影、曝光、蚀刻的复杂的光学加工地形成导电膜的图案。以下,依据图3~图7具体地进行说明。以下,对相同的部分或具有相同功能的部分标记了相同的标号。图3是用于说明基板形成工序S0的致动器基板2的截面示意图。在基板形成工序S0中,通过粘接剂使沿与基板表面垂直的方向实施极化处理的压电体基板2a、以及沿相反方向实施极化处理的压电体基板2b粘合而形成致动器基板2。比压电体基板2a更厚地形成压电体基板2b,在形成吐出槽4时压电体基板2a与压电体基板2b的边界位于槽的深度的中间位置。虽然致动器基板2使用PZT陶瓷,但也能够使用PZT陶瓷以外的钛酸钡等其他压电体基板。另外,也可以在绝缘体基板上必要的区域形成压电体基板2a、2b的层叠体作为致动器基板2。图4是用于说明槽形成工序S1及浅槽形成工序S2的图,图4(a)是致动器基板2的局部的平面示意图,图4(b)是CC部分的截面示意图,图4(c)是DD部分的截面示意图,图4(d)是EE部分的截面示意图。如图4(a)及(b)所示,在槽形成工序S1中,在致动器基板2的表面TP形成吐出槽4,接着在浅槽形成工序S2中,形成与吐出槽4连续的第一浅槽6a及比第一浅槽6a更深的第二浅槽6b。吐出槽4使用切割刀片从致动器基板2的表面TP的前端FE形成至端子区域R的跟前。切割刀片具有圆盘形状,因此如图4(b)所示,吐出槽4的后端RE侧的端部成为圆弧形状。在形成吐出槽4后,使切割刀片上升而形成第一浅槽6a,接着与第一浅槽6a连续地形成第二浅槽6b。由于在之后的磨削工序中将磨削表面TP,吐出槽4以及第一及第二浅槽6a、6b的最终形状比在槽形成工序S1及浅槽形成工序S2中磨削的深度更浅。因此,优选在浅槽形成工序中比最终形状更深地形成。吐出槽4形成为深度300μm~400μm,宽度40μm~100μm;第一浅槽6a与吐出槽4连续并形成为深度10μm~40μm,宽度与吐出槽4相同;第二浅槽6b与第一浅槽6a连续并形成为深度30μm~40μm,宽度与第一浅槽6a相同。如图4(c)所示,构成通道24的区域的吐出槽4具有一定的深度。如图4(d)所示,形成于端子区域R的第二浅槽6b作为浅槽6形成于压电体基板2a的表面TP。此外,如已经说明的那样,可以比第二浅槽6b更深地形成第一浅槽6a,也可以形成为相同的深度。图5是用于说明导电膜形成工序S3的图,图5(a)是致动器基板2的局部的平面示意图,图5(b)是FF部分的截面示意图。在导电膜形成工序S3中,通过非电解镀敷法在致动器基板2的表面TP和吐出槽4、第一浅槽6a及第二浅槽6b的侧面及底面形成导电膜8。首先,对致动器基板2的表面实施镀敷预处理,接着,通过非电解镀敷法使Ni-P析出至表面,接着使Au析出而形成由Au和Ni-P构成的导电膜8。导电膜8形成为厚度0.1μm~5μm。通过实施镀敷预处理能够提高导电膜8的密封性。图6是用于说明磨削工序S4的图,图6(a)是致动器基板2的局部的平面示意图,图6(b)是GG部分的截面示意图,图6(c)是HH部分的截面示意图。如图6(a)所示,在磨削工序S4中,磨削并除去沉积于致动器基板2的表面TP的导电膜8,在表面TP形成导电膜8的图案。磨削使用宽度较宽的磨削刀片等,除去导电膜8和表面TP的表层。接着,使用研磨平台使表面TP平坦化。由此,如图6(b)及(c)所示,导电膜8残留于吐出槽4的底面和侧面、第一及第二浅槽6a、6b的底面及侧面。沉积于吐出槽4的侧壁的导电膜8成为驱动电极9。第二浅槽6b的导电膜8作为与外电路的连接用端子起作用。各第二浅槽6b的导电膜8分别与对应的吐出槽4的驱动电极9电连接。图7(a)是表示在盖板接合工序S5中,将盖板10接合至致动器基板2的表面TP的状态的截面示意图。盖板10以使致动器基板2的端子区域R露出并覆盖吐出槽4的方式,通过粘接剂接合于表面TP。在磨削工序S4中,形成于第一浅槽6a的导电膜8的上端面形成为与表面TP相同程度的高度,因此能够共面地接合盖板10和表面TP。即使在盖板10和表面TP不共面的情况下,由于盖板10经由粘接剂接合于致动器基板2,也能通过粘接剂密封第一浅槽6a。在盖板10形成有液体供给室11,液体供给室11与各吐出槽4连通。此外,也能够在将盖板10接合至致动器基板2之后,在盖板10的后端与致动器基板2的角部模制密封材料而完全地密封第一浅槽6a。图7(b)是表示在喷嘴板粘接工序S6中,通过粘接剂将喷嘴板12粘接至致动器基板2的吐出槽4开口的前端FE的侧面的状态的截面示意图。在喷嘴板12形成有喷嘴13,喷嘴13与吐出槽4连通。图7(c)是表示将柔性基板15粘接至致动器基板2的端子区域R的状态的截面示意图。在柔性基板15形成有布线电极16,布线电极16与第二浅槽6b的导电膜8经由未图示的各向异性导电膜电连接。在浅槽形成工序S2中,比导电膜8的厚度和布线电极16的厚度的总计的厚度更浅地形成第二浅槽6b。由此,能够使导电膜8与布线电极16之间电连接。如上所述,在致动器基板2的表面TP形成第一浅槽6a及第二浅槽6b,通过非电解镀敷法使导电膜8沉积于该第一及第二浅槽6a、6b,其后,通过除去表面TP的导电膜8形成导电膜8的图案,因此制造工序较短,并能够不使用光刻及蚀刻法而简便地形成电极图案。此外,虽然在导电膜形成工序S3中通过非电解镀敷法形成了导电膜8,但本发明不限于此,也可以用溅射法或蒸镀法代替非电解镀敷法形成导电膜8。(第二实施方式)图8~图17是用于说明本发明的第二实施方式所涉及的液体喷射头及其制造方法的图。图8是液体喷射头1的说明图,图9是表示液体喷射头1的制造方法的工序图,图10~图17是用于说明液体喷射头1的各制造工序的图。对与第一实施方式相同的部分或具有相同功能的部分标记了相同的标号。图8(a)是液体喷射头1的示意性的分解立体图,图8(b)是沿着吐出槽4的长度方向的截面示意图,图8(c)是沿着虚设槽5的长度方向的截面示意图。如图8所示,液体喷射头1包括:致动器基板2,包含压电体材料;盖板10,接合于致动器基板2的表面TP;喷嘴板12,粘接于致动器基板2及盖板10的前方的侧面;以及柔性基板15,粘接于致动器基板2的后端RE附近的表面TP的端子区域R。致动器基板2由压电体材料构成,包括极化方向与基板面垂直并彼此朝向相反方向的2块压电体基板2a、2b。在致动器基板2的与盖板10相反的一侧的背面接合有基底基板14。在致动器基板2的表面TP的后端RE附近设定有端子区域R,沿从表面TP的前端FE至端子区域R的方向形成有并列的多个吐出槽4,在邻接的吐出槽4之间,从前端FE至后端RE,与吐出槽4并列地形成有虚设槽5。在吐出槽4的侧面形成有驱动电极9,在吐出槽4的底面形成有导电膜8。在虚设槽5的侧面形成有驱动电极9,基底基板14露出至虚设槽5的底面。盖板10以覆盖多个吐出槽4及多个虚设槽5并使端子区域R露出的方式,接合于致动器基板2的表面TP。在盖板10的后侧形成有液体供给室11,在液体供给室11中与吐出槽4对应的位置形成有狭缝20。由盖板10闭塞吐出槽4的上部开口而构成通道24,该通道24经由狭缝20与液体供给室11连通。虚设槽5由盖板10闭塞上部开口而与液体供给室11不连通。喷嘴板12粘接于致动器基板2及盖板10的前端FE。喷嘴13形成于喷嘴板12,并与在致动器基板2的前侧的侧面开口的吐出槽4(通道24)连通。如图8(b)所示,吐出槽4从致动器基板2的前端FE形成至端子区域R的跟前。吐出槽4的后侧的端部具有转印切割刀片的外形形状的圆弧形状。从吐出槽4的后侧的端部至端子区域R之间形成有与吐出槽4连续的第一浅槽6a。而且,在端子区域R中,形成有与第一浅槽6a连续并与虚设槽5交叉的第二浅槽6b,在相对第二浅槽6b而更靠近后端RE的一侧,与第二浅槽6b并列地形成有第三浅槽6c。比第二及第三浅槽6b、6c深度更浅地形成第一浅槽6a。图14是表示之后说明的倒角工序后的致动器基板2的局部立体图,参照该图14对第一~第三浅槽6a~6c和导电膜8进行说明。在第一~第三浅槽6a~6c的侧面及底面形成有导电膜8。形成于第二浅槽6b的底面及侧面的导电膜8经由形成于第一浅槽6a的导电膜8与形成于吐出槽4的侧面的驱动电极9电连接。形成于第三浅槽6c的导电膜8与形成于虚设槽5的侧面的驱动电极9电连接。在此,在第二浅槽6b与虚设槽5交叉的交叉部的虚设槽5的侧面与第二浅槽6b的侧面及底面的角部形成有倒角部21,导电膜8被除去。其结果是,第二浅槽6b的导电膜8与第三浅槽6c的导电膜8电独立。如图8(b)所示,在端子区域R粘接有柔性基板15。在柔性基板15中,与第二浅槽6b对应地形成有共用布线17,与第三浅槽6c对应地形成有个别布线18。柔性基板15经由未图示的各向异性导电膜粘接于端子区域R。其结果是:第二浅槽6b的底面的导电膜8与吐出槽4的侧面的驱动电极9和共用布线17电连接;第三浅槽6c的底面的导电膜8与形成于夹着吐出槽4的2个虚设槽5的吐出槽4侧的侧面的2个驱动电极9和个别布线18电连接。液体喷射头1被如下地驱动。从未图示的液体罐供给的液体供给至液体供给室11,并经由狭缝20填充至各吐出槽4(通道24)。当在柔性基板15的共用布线17与个别布线18之间供给驱动信号时,该驱动信号传递至第二浅槽6b的导电膜8和第三浅槽6c的导电膜8。进一步,驱动信号供给至吐出槽4的侧面的2个驱动电极9和夹着吐出槽4的2个侧壁19的虚设槽5侧的驱动电极9,电场沿与侧面垂直的方向施加于侧壁19a和侧壁19b(参照图14)而发生厚度滑移变形。由此,两个侧壁19a、19b所夹着的吐出槽4(通道24)的容积瞬间增大,接着缩小并从喷嘴13吐出液滴。该情况能够通过1周期驱动而从各吐出槽4依次吐出液滴。致动器基板2的材料、吐出槽4、第一浅槽6a的深度和宽度、通过非电解镀敷法的导电膜8的形成、盖板10及喷嘴板12等与第一实施方式相同,因此省略说明。能够比吐出槽4和第一浅槽6a宽度更宽地形成第二浅槽6b及第三浅槽6c的宽度。第二及第三浅槽6b、6c的深度可以是20μm~30μm。比导电膜8和共用布线17或个别布线18的总计厚度更浅地形成第二及第三浅槽6b、6c。参照图9~图17对本发明的第二实施方式所涉及的液体喷射头1的制造方法进行说明。图10是用于说明基板形成工序S0的致动器基板2的截面示意图。在基板形成工序S0中,经由粘接剂使沿相对基板面垂直的方向实施极化处理、极化方向彼此相反朝向的2块压电体基板粘合而形成致动器基板2。比压电体基板2a更厚地形成压电体基板2b,之后在形成吐出槽4、虚设槽5时将侧壁固定于压电体基板2b。致动器基板2的材料等与第一实施方式相同,因此省略说明。图11是用于说明槽形成工序S1和浅槽形成工序S2的说明图。图11(a)是致动器基板2的局部平面示意图,图11(b)是II部分的截面示意图,图11(c)是JJ部分的截面示意图。在槽形成工序S1中,在致动器基板2的表面TP的后端RE附近设定端子区域R,沿从表面TP的前端RE至端子区域R的方向形成并列的多个吐出槽4直至端子区域R的跟前,并在邻接的吐出槽4之间,从前端FE至后端RE,与吐出槽4并列地形成虚设槽5。然后,在浅槽形成工序S2中,在吐出槽4与端子区域R之间形成第一浅槽6a,在端子区域R中,沿与第一浅槽6a连续并与虚设槽5交叉的方向形成第二浅槽6b,进一步在相对第二浅槽6b而更靠近后端RE的一侧,与第二浅槽6b并列地形成第三浅槽6c。吐出槽4、虚设槽5及第一~第三浅槽6a、6b、6c能够使用切割刀片磨削而形成。在实际中,连续地形成吐出槽4和与其连续的第一浅槽6a。即,在形成吐出槽4的槽形成工序S1之后,在浅槽形成工序S2中连续地形成与该吐出槽4连续的第一浅槽6a,或以与此相反的顺序形成。另外,比吐出槽4更深地形成虚设槽5。吐出槽4形成为深度300μm~400μm,宽度40μm~100μm。由于在之后的磨削工序中将磨削表面TP,吐出槽4、虚设槽5及第一~第三浅槽6a、6b、6c的最终形状相对在槽形成工序S1及浅槽形成工序S2中磨削的深度变浅。因此,优选在浅槽形成工序中比最终形状更深地形成。例如,假设在之后的磨削工序中将表面TP磨削约10μm,则第一浅槽6a与吐出槽4连续并形成为深度10μm~40μm,宽度与吐出槽4相同,第二浅槽6b与第一浅槽6a连续并形成为深度30μm~40μm,宽度比第一浅槽6a更宽。能够以与第二浅槽相同的深度、相同程度的宽度形成第三浅槽6c。虚设槽5形成为与吐出槽4相同程度的宽度或比吐出槽4的宽度更窄,深度比吐出槽4深10μm~100μm。此外,如已经说明的那样,也可以比第二浅槽6b或第三浅槽6c更深地形成第一浅槽6a,也能形成为相同的深度。图12是用于说明导电膜形成工序S3的图。图12(a)是致动器基板2的局部平面示意图,图12(b)是LL部分的截面示意图。在导电膜形成工序S3中,通过非电解镀敷法在致动器基板2的表面TP和吐出槽4、虚设槽、第一~第三浅槽6a~6c的底面及侧面形成导电膜8。镀敷预处理、非电解镀敷法、材料等与第一实施方式相同,因此省略说明。图13是用于说明磨削工序S4的图。图13(a)是致动器基板2的局部平面示意图,图13(b)是NN部分的截面示意图。在磨削工序S4中,磨削并除去形成于致动器基板2的表面TP的导电膜8。磨削使用宽度较宽的磨削刀片等,除去导电膜8和表面TP的表层,并使用研磨平台使表面TP平坦化。由此,能够在表面TP附近形成导电膜8的图案。此外,形成于吐出槽4的侧面的导电膜8,即驱动电极9经由第一浅槽6a与第二浅槽6b电连接。另外,形成于虚设槽5的侧面的导电膜8,即驱动电极9经由沉积于虚设槽5的侧面与第二浅槽6b的底面及侧面的角部的导电膜8与吐出槽4的驱动电极9导通。另外,形成于虚设槽5的侧面的驱动电极9经由沉积于虚设槽5的侧面与第三浅槽6c的底面及侧面的角部的导电膜8,与第三浅槽6c的底面的导电膜8导通。因此,在该状态下吐出槽4的驱动电极9与虚设槽5的驱动电极9电连接。图14是用于说明倒角工序S7的图,是致动器基板2的后端RE的局部立体图。在倒角工序S7中,对第二浅槽6b与虚设槽5交叉的交叉部的虚设槽5的侧面与第二浅槽6b的侧面及底面之间的角部进行倒角。例如,能够使用比形成虚设槽5的切割刀片的厚度稍厚的刀片容易地进行倒角。其结果是:虚设槽5的侧面的驱动电极9与吐出槽4的侧面的驱动电极9电分离;第二浅槽6b的导电膜8和第三浅槽6c的导电膜8作为端子电极起作用。图15是用于说明盖板接合工序S5的截面示意图。在盖板接合工序S5中,以使端子区域R露出并覆盖吐出槽4及虚设槽5的方式将盖板10经由粘接剂接合至表面TP。通过粘接剂密封第一浅槽6a。在盖板10形成有液体供给室11,液体供给室11与吐出槽4经由狭缝20连通,由盖板10闭塞虚设槽5的上部开口。其结果是,供给至液体供给室11的液体流入吐出槽4但不流入虚设槽5。图16是用于说明背面磨削工序S8及基底基板接合工序S9的图,图16(a)是背面磨削工序S8之后的截面示意图,图16(b)是基底基板接合工序S9之后的截面示意图。在背面磨削工序S8中,磨削致动器基板2的与表面TP相反的一侧的背面BP,除去虚设槽5的底面,留下吐出槽4的底面。由此,形成于虚设槽5的底面的导电膜8被除去,形成于虚设槽5的两侧面的驱动电极9a、9b电分离。接着,在基底基板接合工序S9中,在磨削的背面BP接合基底基板14,闭塞在背面BP开口的虚设槽5。基底基板14使用相对介电常数较小的绝缘体。其结果是:驱动电极9a与驱动电极9b之间的电容耦合比相对介电常数较大的压电体存在于虚设槽5的底面的情况更小,驱动电极9a与驱动电极9b之间的串扰降低。图17是用于说明喷嘴板粘接工序S6及柔性基板粘接工序S10的液体喷射头1的截面示意图。在喷嘴板粘接工序S6中,将喷嘴板12接合至致动器基板的吐出槽4开口的侧面。接着,在柔性基板粘接工序S10中,以使共用布线17与形成于第二浅槽6b的底面的导电膜8电连接,使个别布线18与形成于第三浅槽6c的底面的导电膜8电连接的方式,将形成有共用布线17和个别布线18的柔性基板15粘接至端子区域R。这样,在通过非电解镀敷法形成导电膜的前后,不使用感光性树脂(抗蚀剂膜)、光刻及蚀刻法形成电极图案,并且通过磨削法成批地分离形成于虚设槽的两侧面的驱动电极,因此能够通过制造工时较少的简便的方法制造液体喷射头。(第三实施方式)图18是本发明的第三实施方式所涉及的液体喷射头1的截面示意图。图18(a)是吐出槽4的槽方向的截面示意图,图18(b)是虚设槽5的槽方向的截面示意图。与第一及第二实施方式不同的部分是:吐出槽4和虚设槽5从致动器基板2的前端FE形成至后端RE,在盖板10的后端通过密封材料23密封吐出槽4和虚设槽5。以下,主要对与第二实施方式不同的部分进行说明。对与第一实施方式或第二实施方式相同的部分或具有相同功能的部分标记了相同的标号。在致动器基板的表面TP的后端RE附近构成有端子区域R,从表面TP的未图示的前端直至后端RE交替并列地形成有吐出槽4和虚设槽5。如图18(a)所示,在吐出槽4的底部形成有基底基板14和较薄地残留于基底基板14上的致动器基板2b。在吐出槽4的底面及侧面形成有导电膜8及驱动电极9。吐出槽4经由狭缝20与盖板10的液体供给室11连通,在盖板10的后端由密封材料23密封。在端子区域R中形成有第二浅槽6b和第三浅槽6c,第二浅槽6b沿与吐出槽4交叉的方向形成,第三浅槽6c在相对第二浅槽6b而更靠近后端RE的一侧,与第二浅槽6b并列地形成。形成于吐出槽4的后端RE侧的侧面的导电膜8与形成于第二浅槽6b的底面及侧面的导电膜8电连接。对第三浅槽6c与吐出槽4交叉的交叉部的吐出槽4的侧面与第三浅槽6c的侧面及底面之间的角部进行倒角而形成倒角部21b。从而使形成于吐出槽4的侧面的导电膜8与形成于第三浅槽6c的底面和侧面的导电膜8电分离。如图18(b)所示,在未图示的致动器基板2的与盖板10相反的一侧的背面接合有基底基板14,基底基板14露出至虚设槽5的底部。在虚设槽5的侧面形成有导电膜8及驱动电极9。虚设槽5与盖板10的液体供给室11不连通,在盖板10的后端由密封材料23密封。形成于虚设槽5的后端RE侧的侧面的导电膜8与形成于第三浅槽6c的底面及侧面导电膜8电连接。对第二浅槽6b与虚设槽5交叉的交叉部的虚设槽5的侧面与第二浅槽6b的侧面及底面之间的角部进行倒角而形成倒角部21a。从而使形成于虚设槽5的侧面的导电膜8与形成于第二浅槽6b的底面和侧面的导电膜8电分离。图20是此后说明的液体喷射头1的制造方法中的倒角工序之后的致动器基板2的立体图,参照该图对第二浅槽6b及第三浅槽6c进行说明。在致动器基板2的表面交替地形成有吐出槽4和虚设槽5。而且,在第二浅槽6b与虚设槽5交叉的交叉部的虚设槽5的侧面与第二浅槽6b的侧面及底面之间的角部形成有倒角部21a。同样地,在第三浅槽6c与吐出槽4交叉的交叉部的吐出槽4的侧面与第三浅槽6c的侧面及底面之间的角部形成有倒角部21b。倒角部21a的导电膜8被除去,使虚设槽5的侧面的驱动电极9与第二浅槽6b的底面的导电膜8电分离。另外,倒角部21b的导电膜8被除去,使吐出槽4的侧面的驱动电极9与第三浅槽6c的底面的导电膜8电分离。由此,形成于吐出槽4的侧面的驱动电极9与形成于虚设槽5的侧面的驱动电极9电分离。再次返回图18,在端子区域R粘接有包括共用布线17和个别布线18的柔性基板15。柔性基板15的共用布线17经由未图示的各向异性导电膜与第二浅槽6b的导电膜8电连接,个别布线18经由未图示的各向异性导电膜与第三浅槽6c的导电膜8电连接。其他结构与第二实施方式相同。第三实施方式所涉及的液体喷射头1的制造方法基本上与第二实施方式所涉及的液体喷射头1的制造方法相同,以下,对不同点进行说明。在槽形成工序S1中,从致动器基板2的表面TP的前端FE至后端RE形成吐出槽4,并在邻接的吐出槽4之间,从前端FE至后端RE,与吐出槽4并列地形成虚设槽5。在该情况下,与第二实施方式同样地,比吐出槽4更深地形成虚设槽5。接着,进行浅槽形成工序S2、导电膜形成工序S3及磨削工序S4,这些工序与第二实施方式相同,因此省略说明。图19是本发明的第三实施方式所涉及的液体喷射头1的磨削工序S4之后的致动器基板2的示意性的立体图。如图所示,吐出槽4和虚设槽5从前端FE形成至后端RE,在端子区域R沿与吐出槽4及虚设槽5交叉的方向形成有第二浅槽6b和第三浅槽6c。在吐出槽4、虚设槽5、第二浅槽6b及第三浅槽6c的侧面及底面形成有导电膜8。接着,如图20所示,在倒角工序S7中,对第二浅槽6b与虚设槽5交叉的交叉部的虚设槽5的侧面与第二浅槽6b的侧面及底面之间的角部进行倒角而形成倒角部21a,使虚设槽5的驱动电极9与第二浅槽6b的底面的导电膜8电分离。另外,对第三浅槽6c与吐出槽4交叉的交叉部的吐出槽4的侧面与第三浅槽6c的侧面及底面之间的角部进行倒角而形成倒角部21b,使吐出槽4与第三浅槽6c的底面的导电膜8电分离。接着,进行盖板接合工序S5、背面磨削工序S8、基底基板接合工序S9、喷嘴板粘接工序S6及柔性基板粘接工序S10。这些工序与第二实施方式相同,因此省略说明。此外,通过未图示的密封材料23密封吐出槽4的后侧的开口。这样,由于从前端FE至后端RE笔直地形成吐出槽4和虚设槽5,在吐出槽4中没有转印切割刀片的外形的区域,能大幅度地缩短前端FE与后端RE之间的长度,从而能够使液体喷射头1小型化。另外,如已经说明的那样,在形成导电膜8的前后不需要形成感光性树脂膜并进行光刻及蚀刻处理,能够通过制造工时较少的简便的方法进行制造。(第四实施方式)图21是本发明的第四实施方式所涉及的液体喷射装置50的示意性的立体图。液体喷射装置50包括:移动机构40,使液体喷射头1、1’往复移动;流路部35、35’,将液体供给至液体喷射头1、1’,并从液体喷射头1、1’排出液体;液体泵33、33’,将液体供给至流路部35、35’;以及液体罐34、34’。各液体喷射头1、1’包括多个头基片,各头基片包括多个通道,并从与各通道连通的喷嘴吐出液滴。液体喷射头1、1’使用已经说明的第一~第三实施方式的任一个。液体喷射装置50包括:一对输送单元41、42,沿主扫掠方向输送纸等被记录介质44;液体喷射头1、1’,将液体吐出至被记录介质44;滑架单元43,承载液体喷射头1、1’;液体泵33、33’,将存积于液体罐34、34’的液体按压供给至流路部35、35’;以及移动机构40,沿与主扫掠方向正交的副扫掠方向扫掠液体喷射头1、1’。未图示的控制部控制并驱动液体喷射头1、1’、移动机构40、以及输送单元41、42。一对输送设备41、42沿副扫掠方向延伸,包括接触辊面且旋转的栅格辊(gridroller)和夹送辊(pinchroller)。由未图示的马达使栅格辊和夹送辊围绕轴转移,将夹入辊间的被记录介质44沿主扫掠方向输送。移动机构40包括:一对导轨36、37,沿副扫掠方向延伸;滑架单元43,能沿着一对导轨36、37滑动;无接头带38,连结滑架单元43并使其沿副扫掠方向移动;以及马达39,经由未图示的滑轮(pulley)使该无接头带38旋转。滑架单元43承载多个液体喷射头1、1’,吐出例如黄色、品红、青色(cyan)、黑色的4种液滴。液体罐34、34’存积对应的颜色的液体,并经由液体泵33、33’、流路部35、35’供给至液体喷射头1、1’。各液体喷射头1、1’按照驱动信号吐出各色液滴。在使液体从液体喷射头1、1’吐出的时刻,能够通过对驱动滑架单元43的马达39的旋转及被记录介质44的输送速度进行控制,在被记录介质44上记录任意的图案。