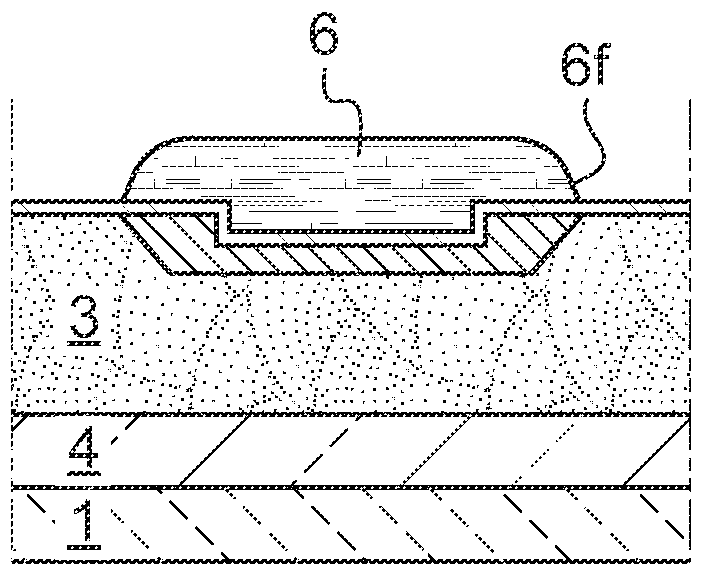
本发明目的在于一种导电支件、包含所述导电支件的电致变色设备及其制造法。以传统的方式,电致变色玻璃体的下电极是基于氧化铟(一般是以缩写ito而更为熟知的掺杂有锡的氧化铟(厚度为100nm至600nm的量级))的透明层,并且其方阻大于10欧姆—15欧姆。为了实现具有大于1米的两个金属接触之间的距离的大尺寸电致变色模块并且为了保持有色状态与无色状态之间的满意切换时间,希望的是在保持大于70%的透明度的同时将方阻降低到小于5ohm/sq的值。此外,制造处理有待于简化以及在工业规模上可靠化而不产生损坏,甚至是改善电致变色设备的光学和电学性能。为此,本发明提出一种用于电致变色设备的导电支件,包括:-玻璃衬底(透明的,如果在表面处纹理化,则有可能地尤其是半透明的),由有机或无机玻璃制成,具有从1.45到1.8的范围内的折射率n1,具有称为第一表面的第一主面,-电极,其包括被布置成栅格(称为金属栅格)的层,由(多个)金属材料(纯的或合金,优选地为单层甚至多层)制成,呈现小于10ω/□(更好的小于5ω/□)的方阻,所述金属栅格呈现至少100nm并且优选地至多1500nm的厚度e2,所述金属栅格由具有小于或等于50μm的宽度a的股线(另外称为轨道)形成并且被分离开小于或等于5000μm而且至少50μm的股线之间的距离b,这些股线被具有如下的表面的多个电绝缘的非导电域分离:所述表面最远离所述衬底而被称为高表面,各域优选地具有大于1.65的折射率。所述导电支件从第一表面侧起包括给定组分的优选地电绝缘的第一无机层,所述第一层直接在所述第一表面上或者在一下部层上,该下层尤其是阻挡层—无机物单层或多层—阻挡湿气(如果是塑料衬底的话)或阻挡碱性物质(如果是玻璃的话),所述第一层在厚度上被部分地或完全地构造而具有贯通孔或腔体,贯通孔或腔体具有宽度wc以用于至少部分地锚定所述金属栅格,所述高表面是所述第一层的表面或是上层—优选地具有小于或等于200nm的厚度的无机物—的表面。所述股线沿着其长度呈现在与高表面齐平的(平坦)旁侧区域之间的中心区域,并且所述中心区域的表面粗糙度大于(平滑的)所述旁侧区域的表面粗糙度,所述旁侧区域的粗糙度参数rq优选地至多是5nm。所述导电支件另外包括由无机材料(单个或多个材料)制成的导电涂层,该导电涂层优选地直接覆盖高表面,在所述旁侧区域之上并且与所述旁侧区域电连接,有可能地呈现在所述中心区域之上并且与所述中心区域电连接,具有小于或等于500mn—更好地小于或等于200nm—的厚度e5,具有小于20ω.cm并且大于所述金属栅格的电阻率的电阻率ρ5,并且其具有至少1.5—更好地至少1.55—并且甚至至少1.7的折射率n5。并且在所述中心区域中,当所述中心区域从所述高表面过齐平时,股线表面的中间和所述高表面相距如下的竖向距离h:该竖向距离h是正交于所述第一表面取得的并且小于或等于500nm,更好地小于或等于300nm并且甚至小于或等于100nm。所述金属栅格(其中心区域)优选地至少部分地被锚定在所述第一层中,并且有可能地被完全地锚定在所述第一层上的有可能的电绝缘上层(单层或多层)中。选取可能的最平滑的高表面—所述第一层的表面或有可能的上层的表面—以便减少泄漏电流。(所述第一层或所述上层的)所述高表面可以优选地呈现小于10nm、更好地小于5nm并且甚至小于2nm的粗糙度rq。rq可以是根据iso4287规范定义的,并且可以通过原子力显微镜来测量。在欠齐平情况下将h限制于500nm,以使得轮廓尽可能不陡峭。尽可能多地减少过齐平,以锚定层并且允许通过各非导电域进行栅格侧壁的钝化。优选地,(平坦)旁侧区域的(表面的)粗糙度参数rq至多是5nm并且甚至至多3nm并且甚至至多2nm或者还至多1nm。并且优选地,每个(平坦)旁侧区域中的rmax(最大高度)至多是20nm并且甚至至多10nm。通过液相法(如自动催化沉积(通过镀银等))特别是针对栅格材料的沉积而获得大于所述旁侧区域的表面粗糙度的所述中心区域的粗糙度。所述中心区域的粗糙度随所述金属栅格的厚度增加(所述旁侧区域的平滑性质独立于厚度)。所述中心区域中的粗糙度参数rq(或rms)可以是至少10nm并且甚至至少20nm并且优选地至多60nm。并且甚至所述中心区域中的粗糙度参数rmax(最大高度)可以是至少100nm并且甚至至少150nm并且优选地至多500nm。所述金属栅格的rmax和rq可以是根据iso4287规范定义的,并且可以通过原子力显微镜来测量。根据本发明,与高表面齐平的旁侧区域可以严格地处于与高表面相同的平面上,或可以从其偏离至多10nm并且更好地至多5nm。每个(平坦)旁侧区域与所述高表面齐平的事实还出自通过液相法(如基于reposer溶液中的金属盐的还原的自动催化(按英语的“electroless(无电)”)沉积)对金属的沉积,沉积是通过掩模层的开孔在通过湿法蚀刻(部分地或完全地)构造的层上执行的。该齐平现象独立于金属厚度。特别是,在自动催化沉积(如镀银(按英语的“silvering(镀银)”))的示例中,金属(如银)沉积在被(部分地或完全地)构造的层(单独的上层,或者上层和第一层)的孔中。由于在通过湿法蚀刻构造的层的形成期间产生的横向蚀刻,孔比掩模层的开孔更宽。银沉积在侧壁上并且沉积在位于每个孔之上的掩模层的被称为内表面的表面上,内表面在高表面的平面中并且因此超出每个孔的侧壁。由于旁侧区域与本身具有平滑内表面的掩模层接触,与高表面齐平的旁侧区域是平坦、平滑的。至于内表面,其再现高表面的平滑、平坦性质。湿法蚀刻在内表面和平滑侧壁以及腔体底部上不生成显著粗糙度(相对于在平滑表面上的沉积,这些潜在地生成的粗糙不增加栅格表面的粗糙度)。在物理气相沉积(“pvd”)(如磁控阴极溅射)期间,由于通过掩模层(如(光)树脂)的开孔的阴影效果,股线的旁侧区域呈盆形,形成具有等于在随后制造电致变色设备时易于生成短路的(部分地或完全地)所构造出的层的腔体的高度的深度的形态的破裂。在该类型的沉积中,对于欠齐平或过齐平的栅格而言,股线不具有平滑的并且与高表面齐平的旁侧区域。另外,镀银比物理气相沉积“pvd”更简单,更不复杂(没有真空设施等),并且适合于任何尺寸的金属栅格。此外,通过镀银沉积的银的电导率是足够的(典型地比通过pvd产生的银栅格的电导率低30%至40%)。在优选的实施方式中,因为对于制造是可靠的并且最简单,所以中心区域欠齐平于高表面,并且h大于100nm,甚至大于150nm。在测试期间,申请人确证了在中心区域的金属栅格的表面与高表面之间的足够的间隙的优点。实际上,在过齐平的金属栅格的情况下或者在具有更小h值的欠齐平的金属栅格的情况下,申请人观测到出现具有20nm至200nm的量级的高度h1以及具有沿着旁侧区域的内部边沿延伸的20nm至500nm的量级的半高宽w1的金属凸起。这些凸起是连续的或不连续的。这些凸起是有害的,因为易于增加泄漏电流。根据本发明的大于100nm、甚至大于150nm的间隙h允许显著减少这些凸起及其高度,甚至于抑制它们。根据本发明,当金属栅格欠齐平于高表面(其中h大于100nm,更好地大于150nm)时,根据本发明的金属股线中的大部分并且甚至每一金属股线没有这些凸起。根据本发明,当沿着旁侧区域的内部边沿延伸的这些凸起具有小于10nm的高度时,金属股线表面(优选地为银)被看作为没有凸起。在另一实施方式中,h小于或等于100nm,并且甚至优选地,中心区域欠齐平于高表面,优选地,金属股线表面没有沿着旁侧区域的内部边沿(中心区域侧)延伸的高度大于10nm的(金属)凸起。在小的间隙h的情况下,在去除掩模层期间生成凸起。假设当间隙h小(几乎齐平的股线)时,(部分地或完全地)构造的层的孔中所沉积的栅格金属(银)与掩模层的侧壁上的栅格金属之间的破裂归因于栅格金属与掩模层上的栅格金属之间的更大的接触区域而在实施上更为棘手。然而,可以通过化学侵蚀消除这些凸起。以有利的方式,导电支件可以包括如下的层,该层被称为不连续的钝化层,由电气材料制成,形成定位于中心区域之上并且有可能地定位于股线的旁侧区域之上的绝缘轨道的栅格,完全地覆盖中心区域并且有可能地部分地或完全地覆盖旁侧区域并且(高表面之上)不横向地超出股线的外部边沿或者(在高表面之上)横向地超出股线的外部边沿至多1μm,甚至至多500nm或者还至多200nm,甚至不超出中心区域。此外,根据本发明的绝缘栅格可以潜在地允许限制泄漏电流并且因此限制电致变色设备的寿命的劣化。此外,如果绝缘栅格的表面是平滑的(例如通过溶胶—凝胶法或其它液相法方法获得的层),则其可以使作为泄漏电流的来源的大的缺陷平坦化。金属栅格呈现可能甚至是不可见的小宽度a的股线并且优选地是不规则的并且更好地是随机的以消除可能的衍射现象。并且钝化被定位于股线之上。由于绝缘轨道不横向地延伸超过金属股线(或者稍微超出小于1μm),因此绝缘轨道不导致有源表面的损失(或者根据股线的宽度与按照本发明而可能的横向超出的比率来看,微小的损失)。出现比中心区域更平滑的旁侧区域另外地取得根据本发明的支件的主要优点。旁侧区域本身不需要被钝化(因为是平滑的)。根据本发明的制造处理允许将绝缘轨道部分地或完全地定位在旁侧区域上,并且因此完全地重新覆盖粗糙的中心区域。由于旁侧区域是平滑的并且不生成泄漏电流,因此仅可能是部分的对它们的覆盖并不是造成妨碍的。仅是部分的覆盖的可能性还允许通过在处理参数的选取上赋予容限来提供在制造处理方面的优点。中心区域越大,容限就越大。只要中心区域被完全覆盖,绝缘轨道就因此可以无差别地完全地或部分地覆盖旁侧区域。中心区域的宽度可以大于、等于或小于(在高表面处限定的)每个旁侧区域的宽度。这取决于e2、h以及容纳金属栅格的孔的宽度。优选地,钝化层在中心区域之上具有称为上表面的表面,其呈现小于10nm、更好地小于5nm并且甚至小于2nm的粗糙度参数rq以及甚至小于100nm、更好地小于50nm并且甚至小于20nm的粗糙度参数rmax。并且钝化层优选地具有侧壁,其呈现小于10nm、甚至小于5nm并且更好地小于2nm的粗糙度参数rq以及甚至小于100nm、更好地小于50nm并且甚至小于20nm的粗糙度参数rmax。钝化层可以是单层甚至多层的、透明的或不透明的(是或多或少吸收的),并且具有任何折射率。钝化层可以是有机的,特别是聚合物的。在钝化的第一实施方式中,电绝缘材料是正性(退火)光敏材料,具有如下的厚度e6:小于1000nm、甚至至多600nm并且在导电涂层之上甚至至多300nm。光敏材料传统上被以平版印刷方式利用于掩模层,并且按英语被命名为“photoresist(光致抗蚀剂)”。其一般涉及光树脂。“正性”光敏材料传统上是如下类型的光敏材料:对其而言暴露于uv光的部分变为可溶于显影剂(显影溶液)并且其中未被暴露的光敏材料部分保持不可溶。“负性”光敏材料传统上是如下的类型的光敏材料:对其而言暴露于光的部分变为不可溶于显影剂并且其中未被暴露的光敏材料部分保持可溶。钝化层可以是单层甚至多层的、透明的或不透明的(是或多或少吸收的),并且具有任何折射率。绝缘轨道呈现由于正性光敏材料的显影导致的倾斜侧壁。尤其是绝缘轨道的基部可能与高表面成至多60°、甚至在40°和50°之间的角度α,以至于绝缘轨道在远离第一表面的同时具有降低的宽度。钝化层的截面典型地呈圆顶形状而没有锐角。与所有预期相反,正性光敏材料与制造电致变色设备的以后的各步骤是兼容的。平坦化材料的厚度优选地是金属栅格的rmax值的量级。在该第一方式的优选实现中,钝化层是基于以下材料中的至少一个的层:聚酰亚胺、聚硅氧烷、苯酚甲醛(以名称“酚醛清漆(或者按英语的“novolac(酚醛清漆)”)树脂”而已知)或聚甲基丙烯酸甲酯(pmma)。在第二实施方式中,钝化层是无机的,并且更特别地是优选地通过溶胶—凝胶法的氧化物的层和/或作为金属的材料的氮化物和/或硅的氮化物的层,并且优选地是如下的层:氮化硅、或者氮化钛、或者氧化钛、氧化锆、氧化硅、氧化铌及其混合物。可以通过不同的方法(例如阴极溅射或溶胶—凝胶)来沉积绝缘轨道的材料。溶胶—凝胶处理归因于其更低的成本以及通过溶胶—凝胶的材料的平坦化性质而是有益的。两种配置对于钝化层而言是可能的。在第一配置中,钝化层处于(优选地无机的)导电涂层上。在第二配置中,钝化层处于(优选地无机的)导电涂层与中心区域(并且甚至旁侧区域)之间。在一种配置中,导电涂层(优选地基于铟的层)是不连续的并且缺少中心区域。导电涂层可以是不连续的,缺少中心区域,并且h于是被限定于股线表面的中间与导电涂层的表面之间。第一层可以是优选地通过溶胶—凝胶法的氧化物的层和/或作为金属的材料的氮化物和/或硅的氮化物的层,并且优选地是如下的层:氮化硅、氮化钛、或者氧化钛、氧化锆、氧化硅及其混合物,或者还有尤其基于锌的透明导体氧化物的层。根据本发明的有可能地被部分地构造的第一层可以处于大的表面(例如大于或等于0.005m2甚至大于或等于0.5m2或大于或等于1m2的表面)之上。根据本发明的栅格可以处于大的表面(例如大于或等于0.02m2甚至大于或等于0.5m2或大于或等于1m2的表面)之上。可以将阻挡湿气的下层添加到所选取的塑料衬底上。阻挡层可以基于氮化硅、碳氧化硅、氮氧化硅、氮碳氧化硅或二氧化硅、氧化铝、氧化钛、氧化锡、氮化铝、氮化钛,例如具有小于或等于10nm并且优选地大于或等于3nm甚至大于或等于5nm的厚度。其可能涉及多层。在本发明中,所有折射率是在550nm处定义的。关于金属栅格,股线是伸长的—未相连的或优选地互连的(至少在有源区中),尤其呈网格状。绝缘轨道具有相同的架构。以优选的方式,通过自动催化沉积并且优选地通过镀银来获得金属栅格。有利地,根据本发明的金属栅格可以呈现小于10ohm/carré、优选地小于或等于5ohm/carré并且甚至1ohm/carré的方阻。特别是,获得低的rcarré允许增加电致变色模块的常规尺寸并且降低有色状态/无色状态的切换时间。金属栅格的一种或多种材料是在由如下形成的组中选取的:银、铜、镍(尤其是纯的材料),或者可以是基于这些金属的合金。栅格优选地基于银。金属栅格可以优选地为单层(银)甚至多层(优选地具有至少80%、甚至90%的银)。金属栅格可以为多层,尤其是银的多层,并且按以下顺序包括(甚至构成自):-第一金属层(直接在腔体的底部或者最接近腔体的底部的金属层上),优选地由第一金属材料制成,第一金属材料优选地基于银甚至由银构成,第一金属层形成为小于栅格的总厚度e2的15%并且甚至10%和/或至少3nm、5nm、甚至至少10nm、并且优选地小于100nm甚至50nm,-第二金属层(在第一层上,远离于衬底),尤其具有可识别的与第一层的界面,基于第二金属材料,第二金属材料优选地选取自如下当中:银、铝或铜,第二金属层形成栅格的总厚度e2的至少70%、80%以及甚至90%,第二层优选地基于银,甚至尤其如第一层那样由银构成。可以尤其根据第一沉积方法(例如通过镀银沉积优选地至少20nm并且甚至至少30nm的厚度,或者通过真空沉积(溅射))形成基于银的第一金属层,并且根据第二沉积方法(其优选地为电沉积)形成基于银的厚度至少为3nm甚至5nm的第二金属层。电沉积的优点是与镀银相比银的利用率更高并且是较之溅射更不昂贵的处理。金属栅格可以是多层的,其中各层由不同的材料制成,例如具有抗腐蚀(水和/或空气)的(例如金属的)最终保护层,由与下面的金属层不同的(尤其是不同于银的)材料制成,具有小于10nm、更好地小于5nm或甚至3nm的厚度。该层特别是利用于基于银的栅格。另外,金属栅格可以是多层的,具有由不同材料制成的两个层(例如双层),并且由如下组成:-(单个)金属层,由(优选地甚至基于银的)前述材料制成,优选地具有至少100nm的厚度,例如是通过镀银或真空沉积(溅射)而沉积的,-以及(例如金属的)抗腐蚀(水和/或空气)的保护上层,由与金属层不同的(尤其与银不同的)材料制成,具有小于10nm、更好地小于5nm或甚至3nm的厚度。金属栅格可以是金属(如银)层,并且涂敷有(尤其是临时的、尤其是聚合物的)保护上层。金属栅格可以优选地直接沉积在所选取的被部分地构造的第一层上,甚至沉积在(尤其是进行扣接的)介电下层上(起扣接作用以促进栅格材料的沉积)。下层直接处于被部分地构造的层的腔体(底部并且优选地腔体的所有或部分侧壁)上,并且优选地缺少被部分地构造的层(优选地无机的扣接层、尤其是(多个)氧化物(例如透明导电氧化物))的表面。介电下层具有小于30nm甚至小于10nm的厚度ea。通过磁控阴极溅射来容易地沉积该扣接层。出于简单而优选金属栅格直接与所构造的层接触(栅格与腔体的底部之间没有层)。将a选取为小于或等于50μm以限制股线对于裸眼的可见性,并且将e2选取为至少100nm以更容易地实现低rcarré的目标。金属股线在电致变色设备的有源区中互连,或者(仅)经由其各端部连接到电接触。金属栅格可以采取如下的股线的形式:所述股线采取闭合图案或网格(限定闭合图案的彼此间互连的股线)的形式,闭合图案或网格具有不规则形状和/或不规则尺寸并且更好地甚至是随机的。厚度e2并非沿着股线的宽度在腔体中是必然恒定的。优选地,其是在股线的表面的中心处定义的。宽度a并非在给定的腔体中是必然恒定的。可以将b定义为股线之间的最大距离,该最大距离尤其对应于网格的两个点之间的最大距离。a和b可以从一个股线到另一股线而变化。由于金属栅格可能是不规则的,因此尺寸a优选地是各股线上的平均尺寸,正如e2是均值那样。如果所构造的层是溶胶—凝胶,则(在股线的表面的中心处定义的)厚度e2可以小于1500nm、更好地小于1000nm、尤其是在从100nm到1000nm的范围内,或者小于800nm并且特别是在从200nm到800nm的范围内,尤其是从100nm到500nm或甚至从100nm到300nm。宽度a优选地小于30μm,以还限制股线对裸眼的可见性。a优选地处于从1μm到20μm、还更优选地从1.5μm到20μm或甚至从3μm到15μm的范围内。b至少是50μm并且甚至至少是200μm,并且b小于5000μm、更好地小于2000μm、甚至小于1000μm。根据本发明的金属栅格的另一特性是覆盖比率t,其优选地小于25%、并且还更好地小于10%并且甚至小于6%或小于2%。并且优选地,绝缘栅格呈现小于或等于t、小于25%或小于10%并且甚至小于6%的覆盖比率t’。特别是,当e2处于800nm和1500nm之间并且a介于10μm和50μm之间时,可以期望在2000μm和5000μm之间的b。这对应于介于0.4%至6.0%之间的覆盖比率。特别是,当e2小于500nm并且a介于3μm和20μm之间或者在3μm到10μm之间时,可以期望在200μm和1000μm之间的b。这对应于介于0.5%和22%之间或者在0.5%到11%之间的覆盖比率。对于给定的rcarré而言,在高的股线宽度a处优先提供大的金属栅格厚度e2以获得透明性。特别是,与金属栅格在非导电域中的锚定有关的多个实施方式是可能的。在第一实施方式中,优选地电绝缘并且甚至优选地为溶胶—凝胶的第一层被在厚度上完全地进行构造而具有宽度wc的贯通孔,并且优选地未构造有可能的下阻挡层。在第二实施方式中,优选地电绝缘并且甚至优选地为溶胶—凝胶的第一层被电绝缘地在厚度上部分地进行构造而由如下形成:–在金属栅格之下的被称为低区域的区域,–被构造的区域,该区域形成非导电域并且具有宽度wc的腔体—因此具有未穿通的孔,优选地,旁侧区域与第一层毗邻并且具有宽度l1,l1大于腔体的高度ec并且l1≤2ec并且甚至l1≤1.4ec。在第三实施方式中,存在:-上层(单层或多层),由优选地为无机的、限定贯通孔的不连续的电绝缘材料制成,所述上层形成非导电域的一部分,高表面是上层的表面,具有至多500nm并且甚至300nm或至多100nm并且优选地至少20nm的厚度ez,–优选地为无机的、电绝缘的第一层,其是:–在厚度上被完全地进行构造而在上层与第一层之间的界面处具有宽度wc的贯通孔—至少容纳金属栅格的(中心区域的)下部分的腔体,金属栅格的中心区域的上部分有可能地在上层的贯通开孔中延伸,甚至超过高表面),-或者是在厚度上被部分地构造而由如下形成:-金属栅格之下的被称为低区域的区域,-在上层之下(并且在低区域之上)的被构造的区域,是具有面对贯通孔的宽度wc的腔体(因此未穿通的开孔)—尤其是至少容纳金属栅格的(中心区域的)下部的腔体(金属栅格的中心区域的上部可能地在上层的贯通开孔中延伸甚至超过高表面)—的区域。在上层与第一层之间的界面(上层—被构造的区域界面)处,贯通孔具有宽度w1,腔体具有宽度wc,优选地其中,wc≥w1,甚至wc>w1。当wc>w1时,股线的被称为边沿区域的区域与旁侧区域毗邻,比旁侧区域更处于外周并且处于上层之下的腔体中—因此与第一层的表面齐平(旁侧区域形成厚度ez的边沿区域的凹部)。当wc>w1时,旁侧区域具有被定义为点x’’与y’之间的距离的宽度l1,边沿区域具有被定义为点x’与y之间的距离的宽度l2,y’’是y在旁侧区域的表面的平面中的正交投影,l3是x’’与y’’之间的距离,l3大于总高度ec+e’c并且l3≤2(ec+e’c)并且甚至l3≤1.4(ec+e’c),其中ec是(在中间处取得的)腔体的高度并且e’c是孔的高度。优选地,如果w1>wc,则a被定义在高表面处,并且如果w1≤wc,则a被定义在第一层的表面处。优选地,如果w1>wc,则b被定义在高表面处,并且如果w1≤wc,则b被定义在第一层的表面处。当第一层在厚度上被部分地构造并且优选地具有大于200nm的高度ec的腔体优选地由喇叭口形侧壁界定时,腔体在远离塑料衬底的同时变宽。可以限定大于ec的水平距离l并且其中l≤2ec。l在点x和y之间,使得x是侧壁的最高点并且y是腔体的底部的端部处的点。高度为e’c的上层的孔可以由喇叭口形侧壁界定,在远离塑料衬底的同时变宽,具有大于e’c的水平距离l’,并且其中l’≤2e’c。当第一层是在厚度上被部分地构造的层(该层的上表面可能地形成高表面)时,腔体越深,旁侧区域越大。上层是透明的,具有最小可能的吸收。优选地,上层是无机的,尤其包括金属和/或硅的氧化物、金属和/或硅的氮化物、金属和/或硅的氮氧化物(sion)的层。其厚度ez可以小于200nm、小于150nm、小于100nm并且甚至从5nm或20nm到80nm。其可以尤其是金属氧化物或金属氧化物和金属氮化物(如sio2/si3n4)的单层或多层。上层是例如(保护)阻挡物层或者酸(例如王水,其为用于导电涂层的ito的常用蚀刻溶液)蚀刻停止层。优选地,上层包括如下的氧化物的至少一个层:ti、zr、al及其混合物或者还有sn并且可能地包括硅。这些氧化物可以是通过气相沉积,尤其是磁控溅射或者还通过溶胶—凝胶法沉积的。优选地,上层具有大于1.7的折射率。在多层的情况下,限定优选地大于1.7的平均折射率。在多层的情况下,优选的是具有小于1.7的折射率的任何层具有小于50nm的厚度。上层具有未穿通的孔或优选地具有贯通的孔。孔可以具有大于20nm并且甚至至少50nm或100nm并且优选地小于300nm的高度e’c以及小于或等于30μm的宽度a’c。e’c是在孔的中心处取得的。孔可以形成任何形状(例如直形或弯曲)的规则地或不规则地间隔开的尤其是(至少在有源区中)未相连的(线形)沟槽。孔可以形成栅网,也就是说,任何形状(尤其是(方形、矩形、蜂窝形)几何形状)的规则或不规则网格的周期性或非周期性的(二维)互连的开孔网。网格可以由网格的两个点之间的最大宽度来定义。优选地由金属栅格来部分地填充(形成为栅格,限定金属栅格的布置的)第一层的腔体或贯通孔。腔体由最常见地形成盆形的底部和侧壁界定。对非导电域进行分离的第一层的腔体或贯通孔可以具有大于200nm并且甚至至少250nm或500nm并且优选地小于1500nm或1200nm的高度ec以及小于或等于30μm的宽度ac。ec是在腔体的中心处取得的。优选地在腔体的底部处取得ac。第一层的腔体或贯通孔可以形成任何形状(例如直形或弯曲)的规则地或不规则地间隔开尤其是(至少在有源区域中)未相连的(线形)沟槽。第一层的腔体或贯通孔可以形成栅网,也就是说,任何形状(尤其是(方形、矩形、蜂窝形)几何形状)的规则或不规则网格的周期性或非周期性的(二维)互连的开孔网。网格可以由网格的两个点之间的最大宽度bc定义。优选地,ec大于200nm、甚至大于250nm或大于500nm。ec优选地为亚微米级。优选地,e’c大于100nm、甚至大于250nm并且小于或等于500nm。e’c优选地为亚微米级。在本发明的意义内,当明确为层或(包括一个或多个层的)涂层的沉积是直接在另一沉积之下或直接在另一沉积之上执行的时,是指这两个沉积之间不能存在任何层的插入。在本发明中,所有折射率是在550nm下定义的。导电涂层具有小于20ω.cm、甚至小于10ω.cm或小于1ω.cm并且甚至小于10-1ω.cm并且大于金属栅格的电阻率的电阻率ρ5,并且具有至少1.55、更好地1.6并且还更好地1.7的给定的折射率n5。优选的是根据各股线之间的距离调整电阻率。电阻率由于b大而更小。例如,对于b=1000μm以及e5=100nm而言,优选小于0.1ω.cm的电阻率。对于200μm的b以及e5=100nm而言,优选小于1ω.cm的电阻率。根据本发明的导电涂层贡献于更好的电流分布。导电涂层优选地是单层而非多层。涂层的表面可以再现尤其是通过气相沉积获得的栅格的表面粗糙度。中心区域之上的涂层可以欠齐平于高表面。导电涂层可以因此包括(或优选地由如下构成):具有介于1.7和2.3之间的折射率na的无机层,优选地其为(距衬底最远的)涂层的最终层并且甚至仅为单个的,优选地具有小于150nm的厚度,基于:透明导电氧化物、简单的或混合的氧化物:–尤其是基于有可能掺杂的以下金属氧化物中的至少一个:氧化锡、氧化铟、氧化锌、氧化钼moo3、氧化钨wo3、氧化钒v2o5,-(优选地)基于ito,例如基于氧化锡锌snzno或基于氧化铟锌(被命名为izo)或基于氧化铟锡锌(被命名为itzo)的(尤其是无定形的)层。优选地,基于氧化锌的层被掺杂有铝和/或镓(azo或gzo)。由zno的氧化物制成的层优选地被掺杂有al(azo)和/或ga(gzo),具有如下的按zn+al或zn+ga或zn+ga+al或zn+优选地选取自b、sc或sb或还选取自y、f、v、si、ge、ti、zr、hf并且甚至选自in的其它掺杂剂的重量的百分比总和:该百分比总和按金属的总重量至少为90%、更好地至少为95%并且甚至至少97%。对于根据本发明的azo层而言,可能优选的是按铝的重量的百分比对于按铝和锌的重量的百分比之和(又称为al/(al+zn))小于10%,优选地小于或等于5%。为此,可以优选地使用氧化铝和氧化锌的陶瓷靶,使得按氧化铝的重量的百分比对于按氧化锌和氧化铝的重量的百分比之和(典型地为al2o3/(al2o3+zno))小于14%,优选地小于或等于7%。对于根据本发明的gzo层而言,可能优选的是按镓的重量的百分比对于按锌和镓的重量的百分比之和(又称为ga/(ga+zn))小于10%,并且优选地小于或等于5%。为此,可以优选地使用氧化锌和氧化镓的陶瓷靶,使得按氧化镓的重量的百分比对于按氧化锌和氧化镓的重量的百分比之和(典型地为ga2o3/(ga2o3+zno))小于11%,优选地小于或等于5%。在所选取的基于氧化锡锌(snzno)的层中,按sn的总金属重量的百分比优选地从20%到90%(并且优选地对于zn而言从80%到10%),并且特别是从30%到80%(并且优选地对于zn而言从70%到20%);尤其是,按sn/(sn+zn)重量的比率优选地从20%到90%并且特别是从30%到80%。优选地为ito或基于氧化锌的无机层优选地呈现小于或等于60nm、50nm甚至40nm或甚至30nm并且甚至小于10nm的厚度,并且具有小于10-1ω.cm的电阻率。优选地,选取通过物理气相沉积、尤其是通过磁控溅射而沉积的选取自ito和zno(azo、gzo、agzo)、甚至moo3、wo3、v2o5的层。氧化铟锡(又或是掺杂锡的氧化铟或对于英语名称“indiumtinoxide(氧化铟锡)”而言的ito)优选地理解为表示混合氧化物或从铟(iii族)的氧化物(in2o3)和锡(iv族)的氧化物(sno2)获得的混合物,优选地在质量比例上对于第一氧化物而言介于70%和95%之间并且对于第二氧化物而言介于5%和20%之间。典型的质量比例为针对于sno2的质量近似为10%,in2o3的质量近似为90%。导电涂层可以构成自具有介于1.7和2.3之间的从而等于n5的折射率na的无机层。导电涂层可以是多层,并且(优选地直接)包括:在上述无机层(尤其是最终层)之下的第一层,该第一层直接在金属栅格(单层或多层栅格)上,由透明导电氧化物制成,具有小于200nm的厚度e’5,具有介于1.7和2.3之间的折射率n’5,尤其是选取自如下当中:-优选地基于尤其是掺杂有铝和/或镓的氧化锌(azo或gzo)或可能地或者itzo的层,-和/或例如基于优选地具有小于100nm的厚度的氧化锡锌snzno或基于氧化铟锌(命名为izo)或基于氧化铟锡锌(命名为itzo)的(尤其是无定形的)层。azo或gzo层可以例如允许将无机层(尤其是ito层)的厚度减少到小于50nm。特别是,可以具有ito/a(g)zo或gzo双层或者还具有(a)gzo或azo/ito双层。衬底可以是平坦的或弯曲的,并且此外可以是刚性的、柔性的或半柔性的。衬底的各主面可以是矩形的、方形的或甚至任何其它形状(圆形的、椭圆形的、多边形的…)。该衬底可以在尺寸上是大的,例如具有大于0.02m2、甚至0.5m2或1m2的表面,并且具有几乎占据表面(除了构造区域之外)的下电极。由塑料材料制成的衬底可以实质上是透明的,是聚碳酸酯pc或聚甲基丙烯酸甲酯pmma或者还是pet、聚乙烯醇缩丁醛pvb、聚氨酯pu、聚四氟乙烯ptfe等…。衬底的厚度可以是至少0.1mm,优选地在从0.1mm到6mm、尤其是从0.3mm到3mm的范围内。如先前所定义的支件可以另外包括(优选地直接)沉积在导电涂层和钝化层上的电致变色系统。本发明还有关于包含有如先前所定义的导电支件的电致变色设备、具有形成被称为下电极的电极的金属栅格的电极,该下电极最靠近第一表面,通常为阳极,尤其是被电致变色系统覆盖,被上电极—常规的厚ito层—覆盖。对于上电极而言,在液体电解质的情况下,还可以替换地或累积地使用如先前根据本发明所定义的导电支件。最后,本发明涉及一种制造如先前定义的导电支件的方法,该方法按此顺序包括以下步骤:-提供包括如下的衬底:-在第一表面上的可能的下层(阻挡湿气等),-由所述第一层的组分制成的被称为“锚定”层的连续的层,-在所述锚定层中形成腔体或贯通孔,因此形成在厚度上被构造的所述第一层,所述第一层的表面是高表面,所述形成包括:-尤其是通过如下来在所述锚定层上实现具有给定的贯通开孔布置的由(负性或正性)光敏材料制成的不连续的掩模层,并且具有侧壁:-将所述光敏材料沉积为实心层,-借助于紫外线源使第一表面侧暴露于紫外线,–通过所述掩模层的贯通开孔而对所述锚定层进行湿法蚀刻,创建所述掩模层的悬置于所述腔体或贯通孔之上的区域,并且因此限定所述掩模层的面对所述腔体或贯通孔的被称为内表面的表面的部分—所述开孔的宽度w0小于所述腔体或贯通孔的在所述高表面处的宽度wc,-形成所述金属栅格包括:在所述腔体或贯通孔中通过优选地自动催化的液相法沉积所述栅格的第一金属材料,所述第一材料沉积在所述腔体的(第一界定层的)侧壁上并且完全地在所述掩模层的所述内表面上,因此形成股线的与所述高表面齐平并且与股线的中心区域相比更不粗糙的旁侧区域,–尤其是通过液相法去除掩模层,-优选地,例如通过物理气相沉积来沉积优选地无机的导电涂层,–有可能地形成呈绝缘栅格状的钝化层—优选地在存在于所述中心区域上的所述导电涂层上的钝化层,所述钝化层形成自在所述股线的所述中心区域之上的绝缘轨道。蚀刻是通过湿法蚀刻处理实现的。通过溶液的浓度、溶液的类型、蚀刻的持续时间和/或溶液的温度来调节所述腔体的深度。(光)敏掩模层于是耐受蚀刻溶液。在蚀刻溶液在所有方向上进行侵蚀(凿空)的意义上,利用湿法溶液的蚀刻是竖向的并且是横向的。蚀刻轮廓可以呈半球类型的盆形。腔体具有在与衬底相对的方向上进行扩口的侧壁(在远离衬底的同时变宽)。截面可以呈甚至为半球(类型)的盆形。下文描述运用构造于第一层上的上层(其表面形成高表面的该上层已经被描述)的相似的制造处理。本发明因此还涉及一种制造如先前限定的(具有在第一层上的上层的)导电支件的方法,其按此顺序包括如下步骤:-提供包括如下的衬底:-在第一表面上的可能的下层(阻挡湿气等),-由所述第一层的组分制成的被称为锚定层的连续的层,-(直接)在所述锚定层上的由所述上层的材料制成的被称为附加层的连续的电绝缘层,-在所述附加层中形成未穿通的或贯通的开孔,因此形成在厚度上被完全地或部分地构造的所述上层,所述形成包括:–尤其是通过如下来在所述附加层上实现具有给定的贯通开孔布置的由(负性或正性)光敏材料制成的不连续的掩模层,并且具有侧壁:-将所述光敏材料沉积为实心层,-借助于紫外线源使第一表面侧暴露于紫外线,-利用第一蚀刻溶液通过所述掩模层的贯通开孔而对所述附加层进行湿法蚀刻,创建所述掩模层的悬置于未穿通的或贯通的孔之上的区域,并且因此限定所述掩模层的面对未穿通的或贯通的孔的被称为内表面的表面的部分,-在所述锚定层中形成腔体或贯通孔,因此形成其中wc>w1的被部分地构造的第一层,所述形成包括:-利用优选地与所述第一溶液不同并且优选地不蚀刻所述上层的第二蚀刻溶液通过所述掩模层的贯通开孔、所述上层的贯通孔而对所述锚定层进行湿法蚀刻,创建所述掩模层和所述上层的悬置于所述第一层的所述腔体或贯通孔之上的区域,并且因此限定所述上层的面对所述第一层的所述腔体或贯通孔的被称为另外的内表面的表面的部分,-形成所述金属栅格包括:在所述第一层的所述腔体或贯通孔中并且在所述上层的贯通孔中通过优选地自动催化的液相法沉积所述栅格的第一金属材料,因此形成所述股线的在所述内表面之下与所述高表面齐平同时与股线中心区域相比更不粗糙的旁侧区域,所述第一材料沉积在所述上层的贯通孔的侧壁上、完全地在所述上层的所述另外的内表面上、在所述掩模层的所述内表面上,因此形成所述边沿区域以及股线的旁侧区域,–尤其是通过液相法去除掩模层,-优选地,例如通过物理气相沉积来沉积优选地无机的导电涂层,-优选地形成呈绝缘栅格状的所述钝化层,所述钝化层形成自优选地在存在于所述中心区域之上的导电涂层上的在股线的中心区域之上的绝缘轨道。通过溶液的浓度、溶液的类型、蚀刻的持续时间和/或溶液的温度来调节腔体(和/或上层的孔)的深度。(光)敏掩模层耐受蚀刻溶液(第一蚀刻溶液和第二蚀刻溶液)。腔体(和/或上层的孔)在与衬底相对的方向上进行扩口(在远离衬底的同时变宽)。在蚀刻溶液在所有方向上进行侵蚀(凿空)的意义上,利用湿法溶液的蚀刻是竖向的并且是横向的。蚀刻轮廓可以呈半球类型的盆形。这种在所有方向上的侵蚀是掩模层的悬置于腔体或未穿通的或贯通的孔之上的区域的来源。优选wc>w1,因为因此更容易创建与高表面齐平的平滑的外周旁侧区域。优选导电涂层是无机的,因为无机的导电涂层更好地耐受在由光敏材料制成的层的化学显影步骤和/或由光敏材料制成的层的部分的移除的步骤期间所使用的水性化学溶液。以有利的方式,制造方法包括:形成呈绝缘栅格状的、形成自在股线的中心区域上的绝缘轨道的钝化层,并且包括:–以实心方式沉积覆盖所述导电涂层的所述钝化层的正性光敏材料的层,–借助于紫外线源使第二主面侧暴露于紫外线,-在溶液中显影,直到使所述正性光敏材料的层呈现为不连续,所述正性光敏材料保持被定位在所述金属栅格之上以用于形成所述钝化层。钝化处理包括平版印刷步骤,但既不借助于平版印刷掩模也不借助于对准步骤(这些将产生额外的成本和复杂度)。在使第二面侧暴露于uv时,每个(不透明的)金属股线形成对uv的屏障,因而股线之上的正性光敏材料未被暴露并且不可溶于显影溶液。绝缘栅格因此在金属栅格上自对准。依照显影,侧壁将一般地是或多或少倾斜的,使得绝缘股线的宽度随着厚度而降低。可以经由正性光敏材料的层的uv照射和显影的条件来控制绝缘轨道的宽度,从而绝缘轨道的宽度大于股线中心区域的宽度,以便使泄漏电流得到更有效的抑制,避免边沿效应。可以经由钝化光敏材料的溶液的浓度以及还有uv照射条件和或显影条件(时间和浓度)来控制绝缘轨道的高度。形成钝化层是特别简单并且快速的,因为不需要沉积随后必需被完全移除的另外的牺牲材料的步骤。在另一实现中,形成呈绝缘栅格的、形成自在股线的中心区域上的绝缘轨道的钝化层包括:–以实心方式沉积覆盖所述导电涂层的所述钝化层的材料的层,-通过如下来在实心层上实现具有给定的贯通开孔布置的由正性光敏材料制成的另外的不连续的掩模层:-沉积覆盖所述钝化层的材料的实心层的正性光敏材料,-借助于紫外线源使第二主面侧暴露于紫外线,-在溶液中显影,直到使被暴露的正性光敏材料的层呈现为不连续,所述层于是定位于所述金属栅格的股线之上,-通过另外的掩模层的贯通开孔对所述实心层进行湿法蚀刻,创建绝缘轨道,-通过液相法移除该另外的掩模层。尤其是,当h至多是100nm时,(在沉积导电涂层之前)去除掩模层创建沿着金属栅格的旁侧区域的内部边沿延伸的至少10nm高的金属凸起,并且方法包括:在去除掩模层之后并且在沉积导电涂层之前,进行湿法蚀刻以消除凸起的步骤。通过液相法沉积第一金属材料优选为镀银,并且栅格优选地是单层。以有利的方式,通过液相法沉积(优选地针对金属栅格的独特的沉积)可以是镀银,并且优选地栅格是单层并且甚至(基于银的)第一材料被直接沉积在腔体或未穿通的孔的底部中。用于镀银步骤的溶液可以包括银盐、银离子的还原剂并且甚至螯合剂。可以根据镜的制造领域中通常使用的并且在例如由mallory;glenno.;hajdu,juanb.编辑的作品“electrolessplating-fundamentalsandapplications”((1990),williamandrewpublishing/noyes)的章节17中描述的传统操作方式来实施镀银步骤。在优选的实施方式中,镀银步骤包括:(通过在池中浸润或通过溶液溅射)利用两种水性溶液(一个包含金属盐(例如硝酸银),并且另一个包含金属离子(ag+离子)的还原剂(例如钠、钾、醛、酒精、糖))的混合物来实现对如下的衬底的接触:该衬底具有可能的下层、第一层、可能的上层和具有贯通开孔的掩模层。最经常使用的还原剂是罗谢尔盐(酒石酸钾钠knac4h4o6∙4h2o)、葡萄糖、葡萄糖钠和甲醛。优选地,在实现该接触之前,镀银步骤包括(上层的腔体和/或孔的表面的)敏化步骤,该步骤优选地包括通过锡盐进行的处理,和/或(上层的腔体和/或孔的表面的)活化步骤,该步骤优选地包括通过钯盐进行的处理。这些处理为此本质上具有(通过银)促进后续金属化并且增大(在上层的腔体和/或孔中)形成的银金属层的粘附力的功能。针对这些敏化和活化步骤的详细描述,可以例如参照us申请2001/033935。更明确地,可以通过如下来进行镀银:将衬底(该衬底具有可能的下层、第一层、可能的上层以及由(光)树脂制成的具有贯通开孔的掩模层)按此顺序浸没在每个具有以下三种溶液之一的池中:-第一水性(敏化)sncl2溶液,优选地进行搅拌(优选地在小于5分钟的时间期间内,例如0.5分钟至3分钟),然后进行(蒸馏)水清洗,-第二水性(活化)pdcl2溶液,优选地进行搅拌(优选地在小于5分钟的时间期间内,例如0.5分钟至3分钟),然后进行(蒸馏)水清洗,-第三,其为银盐(优选地氮化银)溶液和银还原剂(优选地葡萄糖钠)溶液的混合物,优选地进行搅拌(优选地在小于15分钟并且甚至5分钟的时间期间内,例如从0.5分钟到3分钟),然后进行(蒸馏)水清洗。被涂敷并且因此镀银的衬底随后被从最后的池收回并且进行(蒸馏)水清洗。另一实施方式在于:按与前面相同的顺序溅射前述的三种溶液而不是浸没衬底(该衬底具有可能的下层、第一层、可能的上层以及由(光)树脂制成的具有贯通开孔的掩模层)。优选地通过液相法,特别是通过在溶剂(丙酮等)中的超声来实现(在沉积导电涂层之前的)掩模层的去除。直接在栅格上并且(直接)在第一层或可能的上层、单层或多层和/或单一或多种材料的涂层上沉积导电涂层可以是通过物理气相沉积(尤其是通过阴极溅射)进行的,其中进行snzno或azo的可能的第一沉积以及第二或最终或优选地独特的ito沉积或基于(掺杂的)zno、甚至moo3、wo3或v2o5的沉积。处理可以包括:在沉积导电涂层之前的加热步骤,优选地介于150°c和550°c之间,优选地在介于5分钟和120分钟之间的持续时间期间,特别是在介于15分钟和90分钟之间的持续时间期间,和/或在沉积无机导电涂层之后的加热步骤,在沉积钝化层之前或之后,在优选地介于150°c和550°c之间的温度下,优选地在介于5分钟和120分钟之间的持续时间期间、特别是在介于15分钟和90分钟之间的持续时间期间。现在将借助于非限制性示例和各图来更详细地描述本发明:-图1是根据本发明第一实施方式的其中股线中心区域与高表面欠齐平的用于电致变色设备的导电支件的示意性截面图,-图1a图解在没有钝化层的情况下的图1的详细视图,-图1b图解在由申请人实现的比较示例中的具有通过pvd沉积的栅格的股线的被部分地构造的第一层的腔体的截面的详细的示意性视图,-图2是根据本发明第二实施方式的其中第一层被完全地构造的用于电致变色设备的导电支件的示意性截面图,-图3是根据本发明第三实施方式的其中在中心区域与导电涂层之间进行钝化的用于电致变色设备的导电支件的示意性截面图,-图4是根据本发明第四实施方式的其中栅格与高表面齐平的用于电致变色设备的导电支件的示意性截面图,-图5是根据本发明第五实施方式的其中栅格与缺少中心区域的导电涂层的表面齐平的用于电致变色设备的导电支件的示意性截面图,-图6是根据第六实施方式的其中栅格被锚定在被构造的第一层和上层中的用于电致变色设备的导电支件的示意性截面图,-图6’是图6的细节的视图,图7a至图7i是与第一实施方式相关的制造导电支件的方法的步骤的示意性视图。明确的是,出于清楚的考虑,所表示的对象的不同要素并非是按比例再现的。示意性的图1以侧向截面表示用于电致变色设备的导电支件100。支件100包括具有1.45至1.8的折射率ns的玻璃衬底—平滑的,具有称为第一表面的第一主面11,按此顺序远离衬底而承载:–可能的阻挡湿气的层4,如氮化硅41或薄层堆叠,–在厚度上被部分地构造的第一层3,其是无机的,优选地为电绝缘材料,具有优选地微米或亚微米的厚度e3,包括:-被称为低区域的(连续)区域30,其在此直接在下层之上,具有(优选地微米的)给定的厚度e’3,覆盖下层的表面,-呈现为凸起部以及呈现为凿空部的被构造的区域31,凸起部限定平坦的高表面34,腔体或凿空部由(限定低表面的)底部33和侧壁32界定,腔体具有在高表面34处的宽度wc并且具有在中间处取得的高度ec,其优选地至多为1500nm并且优选地大于100nm,腔体根据规则的或不规则的给定的布置(非连接的条带、栅网等)延伸,高表面是局部平坦的,-电极2,包括布置成称为金属栅格的栅格2的层,由通过自动催化沉积获得的(多个)金属材料制成,优选地为(通过镀银获得的)银单层,栅格在此是由锚定在腔体中的股线—又称为轨道20—形成的单层,股线在高表面34处具有小于50μm、更好地小于或等于30μm(并且至少1μm)的宽度a,并且在高表面34处分离开小于或等于5000μm并且至少50μm的距离b,栅格具有在股线的中间处定义的至少100nm并且优选地小于1500nm的厚度e2,金属栅格呈现小于10ω/□并且甚至小于5ω/□或小于1ω/□的方阻,–优选地为单层的无机导电涂层5,具有小于或等于500nm或小于或等于100nm并且更好地小于或等于60nm的厚度e5,具有小于20ω.cm并且大于金属栅格的电阻率的电阻率ρ5,并且具有至少1.5并且更好地1.7的给定折射率n5,在此由在栅格2和高表面34之上由ito(或azo或gzo、agzo)制成的无机层构成,-钝化层6,直接在导电涂层5之上,所述钝化层6是不连续的,优选地由正性光树脂制成,具有小于1000nm的(在腔体的中间取得的)厚度e6。由于在形成稍后详细描述的被部分地构造的第一层时进行的对连续层的湿法蚀刻处理,因此腔体具有喇叭口形的侧壁。股线20沿着它们的长度呈现在与高表面34齐平的旁侧区域22、22’之间的中心区域21,并且中心区域21的表面粗糙度大于旁侧区域22、22’的表面粗糙度。为了表征金属栅格2,如图1a(在没有钝化层的情况下的图1的细节视图)所示,表示出a、b、e2并且还有中心区域的宽度am,并且对于腔体而言的在腔体的底部处的宽度ac以及ec是从腔体的底部的中心起的高度。侧壁是喇叭口形的(在远离衬底1的同时变宽),定义x与y之间的水平距离l,使得x是侧壁的最高点并且y是腔体的底部的端部处的点。l大于ec,l≤2ec并且甚至l≤1.4ec。在中心区域21中,股线表面的中间和高表面相距正交于第一表面取得的竖向距离h并且竖向距离h小于或等于500nm。在此,中心区域21欠齐平于高表面34。由于自动催化沉积(如镀银)以及宽度l1的平滑的旁侧区域22、22’,因此股线呈现比旁侧区域更粗糙的中心区域21。中心区域的宽度am不一定大于l1,这取决于a、h和ec的值。中心区域和平坦的旁侧区域的粗糙度参数的示例按照厚度e2记录在以下表中。股线的表面e2(nm)rq(nm)rmax(nm)旁侧区域300210中心区域30030300旁侧区域2001.58中心区域20020200旁侧区域450210中心区域45035450优选地通过磁控阴极溅射沉积ito涂层5,其表面于是符合于在下方的表面:被部分地构造的第一层3的表面;平坦和平滑的旁侧区域22、22’;比旁侧区域更粗糙的中心区域21。钝化层6形成定位在中心区域21之上并且定位在股线的旁侧区域22、22’之上的绝缘轨道的栅格,覆盖中心区域并且部分地或完全地覆盖旁侧区域,并且不横向超出股线的外部边沿,或者横向地超出股线的外部边沿至多1μm。在此,每个绝缘轨道的侧壁6f是倾斜的,具有与高表面34的45°的量级的角度α。每个绝缘轨道的截面是圆顶形状的,没有锐角。由于每个绝缘轨道的上表面6s和每个绝缘轨道的侧壁6f是平滑的,因此钝化层6使中心区域21平坦化,并且保持旁侧区域22、22’的平滑性质。为了随后制造电致变色设备,添加电致变色系统、在液体电解质的情况下可以相同的上电极。金属栅格优选地具有随机图案。在与(图1的)第一实施方式相关的示例nº1中,选取以下特性。玻璃衬底1是平坦、平滑的,具有1.5的折射率,例如,具有2mm的厚度并且具有至少90%的tl。阻挡层是金属或硅的氮化物或金属或硅的氧化物的薄层堆叠。第一层是具有400nm的厚度的tiox溶胶—凝胶层。可以替换地通过阴极溅射来沉积该层。厚度ec为350nm。通过蚀刻获得第一层3的腔体,如随后详细描述的那样。被部分地构造的第一层3是局部平坦的。高表面34的粗糙度被由小于4nm的rq定义。栅格2是通过镀银直接沉积在腔体中的银单层,如随后详细描述的那样。银在此部分地填充腔体,具有等于大约300nm的e2。h因此等于50nm。作为栅网的栅格的图案是六边形的。宽度a等于12μm,并且最大距离b为560μm。覆盖比率t为4.5%。导电涂层5由50nm的氧化铟锡ito的层构成,具有大约2的折射率,具有小于10-1ω.cm的电阻率ρ5。由传统4点方法测量的(在150°c下在30分钟时间的退火之后的)整体的rcarré大约为2.5ohm/carré。至于形成局部化绝缘栅格的钝化层,其为具有300nm量级的量级的e6的正性光敏聚酰亚胺层。随后,添加具有由400nm厚度的ito制成的上电极的电致变色系统。图7a至图7i是特别是与示例nº1相关的根据第一实施方式的导电支件的制造的示意性视图(未按比例),其中通过化学蚀刻制造被部分地构造的第一层,并且通过镀银制造银栅格。图7a所图解的第一步骤在于从涂敷有下层的玻璃衬底1开始:-在下层上形成锚定层3a,其包括第一层的材料,-通过“旋转涂敷”在层3a上施加液态的掩模材料(正性光敏材料,树脂的az®1505)的层60。所沉积的光敏材料随后在对流炉中在100°c下烘培20分钟的时间。光敏材料的厚度是800nm。图7b所图解的第二步骤在于生成光树脂图案。为了做到这点,在树脂60上施加具有不连续性71的平版印刷掩模70,并且利用(在365nm处)20mw/cm2的hg灯通过根据不规则的(更好地随机的)布置的不连续性71在10秒的时间期间从第一主面11侧使树脂60受辐射于uv。图7c所图解的第三步骤在于在光敏材料60中创建贯通开孔。通过在基于四甲基氢氧化铵(按英语的“tmah”)的特定显影溶液中进行溶解来消除被辐射的区域并且通过去离子水清洗,由此形成通过光树脂的贯通开孔。界定贯通开孔的光敏材料的侧壁61在远离衬底的同时扩口。因此,在光敏材料60的外部表面或上表面63处,每个贯通开孔的宽度大于在高表面34处的宽度w0。替换地,可以使用负性光敏材料以及逆向光蚀刻掩模(去除非辐射区域以形成开孔)。图7d所图解的第四步骤在于在优选地为介电的连续锚定层3a(如tiox层)的中创建腔体。优选在环境温度下通过湿法蚀刻而非干法蚀刻来形成被部分地构造的第一层。所选取的树脂60因此耐受蚀刻溶液,蚀刻溶液在此是基于nh3和h2o2的溶液。蚀刻形成深度ec的腔体,侧壁32和腔体在远离玻璃1时扩口。对于示例nº1而言,ec等于350nm。蚀刻溶液在所有方向上(竖向地并且横向地)进行侵蚀(凿空)。蚀刻轮廓是盆形的。锚定层3a的湿法蚀刻创建掩模层的如下区域:该区域悬置在腔体之上并且因此限定掩模层60的面对腔体32的被称为内表面62、62’的表面的部分。每个腔体具有大于宽度w0的(在高表面处的)宽度wc。内表面62、62’具有几乎等于l的宽度l0。腔体的底部33是平坦的。图7e所图解的第五步骤在于通过液相法并且更确切地自动催化沉积(因此优选地通过镀银)来沉积栅格材料2。在腔体中通过(耐受蚀刻的)光敏材料60的开孔实现沉积以优选地部分地填充腔体,如在此所图解那样。银沉积于腔体的底部中、腔体的侧壁上、光敏材料的内表面62、62’上、光敏材料的侧壁上(并且没有在层3的高表面上)、并且在不连续上表面63上。更确切地,镀银部分地填充每个腔体并且沉积于底部中、侧壁上并且完全地在掩模层的内表面62、62’上,因此形成与高表面齐平并且比面对贯通开孔的股线中心区域21更不粗糙的股线旁侧区域22、22’。每个旁侧区域22、22’的宽度l1几乎等于l0+e2。对于示例nº1而言,银层被根据以下的针对大约300nm的厚度e2的操作方式沉积在被部分地构造的第一层3中(其中h等于50nm并且中心区域欠齐平):-根据以下来稀释镀银溶液(由dr.-ing.schmitt,gmbh公司(dieselstr.16,64807迪堡/德国)提供的待稀释溶液):○250cm3管瓶中的100μl的miraflex®1200(sncl2溶液)(溶液nº1),○250cm3管瓶中的200μl的miraflex®pd(pdcl2溶液)(溶液nº2),○250cm3管瓶中的15ml的miraflex®rv(还原剂的溶液,葡萄糖钠)(溶液nº3),○250cm3管瓶中的15ml的miraflex®s(硝酸银溶液)(溶液nº4);-在环境温度下使用上述溶液,-将(具有层4、3)的衬底放置在其中倾注了溶液nº1的内容物的池中,在1分钟的时间期间进行搅拌然后用蒸馏水清洗;-将(具有层4、3)的衬底放置在其中倾注了溶液nº2的内容物的第二池中,在1分钟的时间期间进行搅拌然后用蒸馏水清洗;-将(具有层4、3)的衬底放置在其中倾注了溶液nº3和nº4的内容物的最终池中,在两分钟的时间期间进行搅拌然后用蒸馏水清洗。图7f所图解的第六步骤在于通过利用丙酮溶剂的液相法并且使用超声来去除光敏材料。导电支件随后优选地在环境温度下浸没在h2o:h2o2:nh3(500:20:1)溶液中3至5分钟的时间以消除银凸起。在具有小于100nm的h的欠齐平栅格的情况下或当栅格为过齐平时,这种化学处理是特别推荐的。图7g所图解的第七步骤在于通过阴极溅射沉积导电涂层5。对于示例nº1而言,其涉及氧化铟锡ito的层。利用由氧化铟(按重量90%)和氧化锡(按重量10%)制成的陶瓷靶在2×10-3mbar的压力下在1%的氩气和氧气的混合物(o2/(ar+o2))下通过磁控阴极溅射来沉积ito。在变形中,选取azo、gzo或agzo。随后在250°c下在30分钟的时间期间执行第一退火。第八步骤在于:-通过旋转涂敷来沉积对于示例nº1而言由作为光敏聚酰亚胺(pimeltmtm系列i-700聚酰亚胺)的正性光敏材料制成的层6a,覆盖导电涂层5,随后是在对流炉中的退火步骤(100°c,20分钟),–借助于紫外线源(其对于示例nº1而言是(在365nm)20mw/cm2的hg灯)使第二主面12侧暴露于如图7h图解的紫外线。图7i所图解的第九步骤在于在基于四甲基氢氧化铵(按英语的tmah)的溶液中的正性光敏材料的显影的结果,以及用去离子水清洗直到使得聚酰亚胺层6呈现为不连续为止的步骤,使(由于银股线的屏蔽而)未曝光的聚酰亚胺留在导电涂层5的定位于银股线20之上的区域中。形成局部化绝缘栅格6的由聚酰亚胺制成的钝化层具有300nm量级的厚度。随后在300°c下在60分钟的时间期间实现第二退火(摒弃或不摒弃第一退火)。在该第二退火之后,由聚酰亚胺制成的钝化层的厚度从380nm下降到300nm。根据本发明的导电支件因此允许制造具有更好的切换时间(经由更小的方阻的获得)的大尺寸的电致变色设备,并且由于金属栅格的钝化的原因,这不会产生泄漏电流劣化。图1b图解在申请人实现的比较性示例中的具有通过pvd沉积的栅格的股线的被部分地构造的第一层的腔体的截面的细节的示意性视图,示出被构造的第一层中的高表面34和所锚定的股线(如示例1中那样)。利用银靶在8×10-3mbar的压力下在氩气下通过磁控阴极溅射来沉积银。通过归因于掩模层的遮蔽效应,股线的旁侧区域22’’a和22’’b呈盆形。这些盆形生成泄漏电流。旁侧区域22’’a和22’’b创建生成泄漏电流的形态的破裂。图2是根据本发明第二实施方式的其中第一层3被完全地构造并且消除了下层的用于电致变色设备的导电支件的示意性截面图。通过第一锚定层的蚀刻持续时间来修改示例1的制造条件以使ec从350nm降低到400nm。图3是根据本发明第三实施方式的其中钝化6处于中心区域21与导电涂层5之间的用于电致变色设备的导电支件的示意性截面图。图4是根据本发明第四实施方式的用于电致变色设备的导电支件的示意性截面图,第四实施方式与第一方式不同在于股线中心区域过齐平于高表面34。通过第一锚定层的蚀刻持续时间来修改示例1的制造条件以使ec从350nm降低到250nm。图5是根据本发明第五实施方式的其中通过栅格在中心区域21缺失从而栅格与不连续的导电涂层的表面齐平的用于电致变色设备的导电支件的示意性截面图。在形成金属栅格和钝化层之前沉积涂层,不连续性可以是通过湿法蚀刻实现的。图6是根据本发明第六实施方式的用于电致变色设备的导电支件的示意性截面图,第六实施方式与第一实施方式不同在于总是通过自动催化沉积(如镀银)而沉积的栅格2被锚定在被部分地构造的第一层中并且还锚定在第一层3之上的被构造的上层3’中。银股线之间的非导电域的高表面是上层34’的表面,于是h被限定于股线的中心区域21的表面与上层34’的表面之间。由优选地无机的电绝缘材料制成的上层3’是被不连续构造的,限定贯通孔,具有20nm至100nm的厚度ez。在界面34(上层3’与第一层3之间的界面)处,贯通孔具有宽度w1,其中wc>w1。被称为边沿区域的股线区域22a、22’a与旁侧区域22、22’毗邻,比旁侧区域更处于外周并且在腔体中处于上层之下,因此与第一层3的表面34齐平。如图6’的细节图中示出那样:-旁侧区域22、22’具有限定如点x’’与y’之间的距离的宽度l1,-边沿区域22a、22’a具有限定如点x’与y之间的距离的宽度l2,-l3是x’’与y’’之间的距离,y’’是y在旁侧区域22、22’的表面的平面中的正交投影。l3大于总高度ec+e’c并且l3≤2(ec+e’c),其中ec是腔体的高度并且e’c是上层3的孔的高度。在示例中,第一层是400nm的氧化钛的层,并且上层是如下的层:例如通过pvd或溶胶—凝胶沉积的具有等于30nm的厚度ez的二氧化硅氧化物的层,或者替换地可能地最微细的二氧化硅层。其可以为多层。一般地,ec大于e’c(ez)。当前第1页12