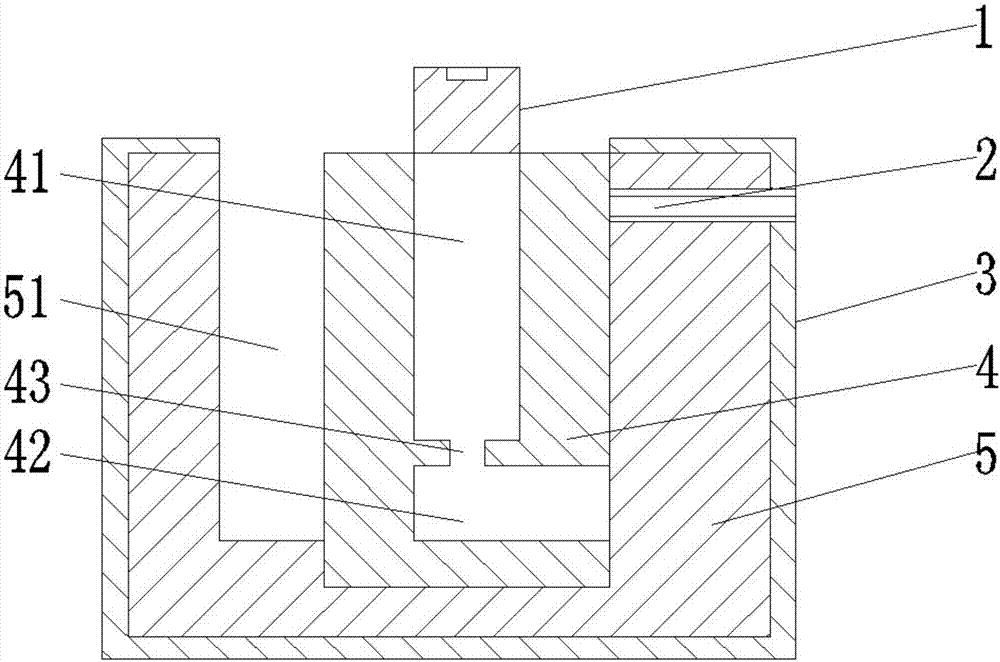
本发明涉及合金锻造挤压
技术领域:
,尤其涉及一种高强度镁合金的挤压模具及镁合金挤压方法。
背景技术:
:镁合金属于密排六方结构,在室温条件下具有较差的塑性,而近年来自镁合金在机械制造、交通运输、航天航空、信息产业的需求量逐渐增大,为了解决两者的矛盾常常需要对镁合金进行改性。作为稀土材料中重要的组成部分,nd元素的加入具有增强镁合金的高温强度、降低镁合金的热裂纹、增强镁合金的抗腐蚀性能的特点。另外,温度对于nd元素在镁合金中固溶度影响较大,此类镁合金可以通过固溶处理对合金进行增强。而mg-sn合金属于一种比较成熟的合金体系,在工业上已经得到了应用。现阶段在镁合金中采用zr元素进行细化的研究比较多,而ti对镁合金细化研究的比较少。本文采用加入ti元素也可以进一步提高镁合金抗腐蚀性能,此类材料的开发可以扩展镁合金的应用。近年来各种大塑性变形制备镁合金的方法已经得到了飞速的发展,比较普遍的有:大挤压比的正挤压、墩压、等通道挤压等。虽然这三两塑性变形方式都可以在一定程度上细化晶粒而增强镁合金,但这三种方式均存在工艺过程繁琐、细化程度不高、破坏合金形状的缺点。技术实现要素:本发明克服了上述现有技术的不足,提供了一种高强度镁合金的挤压模具及镁合金挤压方法。本发明能够直接获得超细的镁合金材料,具有操作简单,不破坏材料形状的特点,还可进行重复挤压,而且通过一次轧制过程就可以获得高强度的镁合金;同时,本发明是将正挤压、墩压、等通道挤压等轧制方式有效的结合在一起,在镁合金进行塑形变形的过程中进行叠加最大程度发挥各自的特点;极大的发挥了三种不同塑性变形均可以对镁合金进行细化的特点,使得镁合金在塑性变形的整个过程基本上均受到压应力的作用;另外在三种塑性变形的条件下均可以减少铸态镁合金中少量的孔洞,使得各种相可以均匀的混合在合金内部,减少合金内部的偏析现象,获得比较均匀的镁合金组织。本发明的技术方案:一种高强度镁合金的挤压模具,包括模具冲头、加热装置、模具套筒、可转动内部芯模和外部芯模;所述模具套筒内部设置有外部芯模,所述外部芯模内部设置有可转动内部芯模,所述可转动内部芯模内部设置待挤压镁合金,所述可转动内部芯模上端设置有模具冲头,所述模具套筒上端还设置有加热装置,加热装置分别为外部芯模、可转动内部芯模和待挤压镁合金供热,所述模具套筒下端还设置有一组热电偶测温装置,所述热电偶测温装置与一组温控系统数据连接,所述温控系统与所述加热装置电连接;所述可转动内部芯模内竖直方向上加工有一组墩压通道,所述墩压通道通过一组中间通道与挤压出口通道连通,所述挤压出口通道方向与所述墩压通道垂直设置;所述外部芯模上加工有一组最终挤压出口通道。进一步的,所述外部芯模和所述可转动内部芯模均为相互对称的两组模具组成。进一步的,所述外部芯模和所述可转动内部芯模表面均包裹有一层石棉。一种高强度镁合金的挤压模具的镁合金挤压方法,该方法包括如下步骤:步骤a、调整可转动内部芯模与外部芯模的相对位置,使可转动内部芯模的挤压出口通道与所述外部芯模中的最终挤压出口通道相背离。步骤b、将镁合金坯料的放入到模具可转动内部芯模中;步骤c、将加热装置放置在模具套筒中,接上电源后对模具芯模及加入其中的镁合金坯料进行加热;步骤d、开启连接控温系统的热电偶,监测到达实验温度后并对整个模具进行保温1h;步骤e、加热保温完成后,开启压力机进行挤压,直至冲头的下移量占镁合金长度的一半,关闭压力机;步骤f、开启芯模转动装置驱动可转动内部芯模转动,转动180°后关闭芯模转动装置,使得可转动内部芯模的挤压出口通道与外部芯模中的最终挤压出口通道连通。步骤g、开启压力机,对镁合金进行进一步挤压;挤压结束后,关闭挤压机,取出挤压出的镁合金。进一步的,所述镁合金为mg-nd-sn-ti镁合金,其中各元素的质量百分比为:nd:2.9wt.%-3.1wt.%,sn:4.9wt.%-5.1wt.%,ti:0.5wt.%-0.7wt.%,其余的为纯mg。进一步的,所述步骤e中的挤压速度为1mm/s~30mm/s。进一步的,所述步骤d中试验温度为375℃~425℃。本发明相对于现有技术具有以下有益效果:本发明能够直接获得超细的镁合金材料,具有操作简单,不破坏材料形状的特点,还可进行重复挤压,而且通过一次轧制过程就可以获得高强度的镁合金;同时,本发明是将正挤压、墩压、等通道挤压等轧制方式有效的结合在一起,在镁合金进行塑形变形的过程中进行叠加最大程度发挥各自的特点;极大的发挥了三种不同塑性变形均可以对镁合金进行细化的特点,使得镁合金在塑性变形的整个过程基本上均受到压应力的作用;另外在三种塑性变形的条件下铸态镁合金中少量的孔洞,使得各种相可以均匀的混合在合金内部,减少合金内部的偏析现象,获得比较均匀的镁合金组织;本发明采用多次正挤压与墩压、等通道挤压相结合起来,与普通的正挤压、墩压及等通道挤压相比,实现了一次挤压多次塑性变形的效果;在多次正挤压后等通道挤压之前合金进行了墩粗,也可以细化晶粒;避免了合金材料需要多次预热、反复加热对合金产生缺陷的缺点;经过挤压变形后材料的形状及尺寸变化不大,可以反复多次挤压;本发明可以采用不同的等通道挤压的夹角调整镁合金变形的剧烈程度,进而改变调控镁合金的晶粒尺寸,以细化晶粒的方式提高镁合金的性能;本发明镁合金在模具中进行了多次不同挤压比的正挤压,进入等通道挤压阶段前的晶粒已经得到了明显的细化;经过正挤压后的镁合金材料的尺寸较小,在进入等通道挤压前会在拐角处受到挤压力而反复的压缩墩粗,进一步细化镁合金的晶粒;当镁合金墩粗结束后,在冲头的挤压力镁合金会进入等通道挤压的剪切带,在合金经过剪切带时受到模具的作用力而产生交叉、增殖,促进镁合金微观组织的进一步破碎;在合金进行多次大塑性变形的过程中有利于第二相的析出、弯曲直至破碎;破碎后的第二相可以成为镁合金结晶的形核点,改善合金的力学性能;将多次正挤压、墩压、等通道挤压三者相互结合,明显细化了镁合金晶粒,有效的强韧化镁合金,明显提高镁合金的细晶强化的作用;将多次正挤压、墩压、等通道挤压三者相互结合减少了挤压的次数,减少了多次反复加热引起合金挤压时产生的缺陷,本发明所用的模具制作简单,易于改装,加工具有低成本性;金属材料在其中进行塑性变形时具有连续性,细晶效果好,提高了镁合金的加工效率;本发明自带加热棒进行加热,能耗低,加热效率高,根据调整连接在硅棒上的控温系统的相关参数就可以根据工作实际需要改变模具中镁合金的温度;本发明进行挤压前的坯料与挤压后的形状相同,并不破坏合金的形状。一次挤压可以获得超细晶材料,多次挤压甚至可以获得纳米晶材料。附图说明图1是本发明的结构示意图;图2是本发明的可转动内部模芯旋转前的内部结构示意图;图3是本发明的可转动内部模芯旋转后的内部结构示意图;图4是本发明的俯视图;图5是图4的a-a面剖视图;图6是图4的b-b面剖视图;图7是本发明在400℃条件下一次挤压制备镁合金的微观组织示意图。图中1-模具冲头;2-加热装置;3-模具套筒;4-可转动内部芯模;5-外部芯模;41-墩压通道;42-挤压出口通道;43-中间通道;51-最终挤压出口通道。具体实施方式以下将结合附图对本发明进行详细说明。实施例一:结合图1-图7示,本实施例公开的一种高强度镁合金的挤压模具,模具冲头1、加热装置2、模具套筒3、可转动内部芯模4和外部芯模5;所述模具套筒3内部设置有外部芯模5,所述外部芯模5内部设置有可转动内部芯模4,所述可转动内部芯模4内部设置待挤压镁合金,所述可转动内部芯模4上端设置有模具冲头1,所述模具套筒3上端还设置有加热装置2,加热装置2分别为外部芯模5、可转动内部芯模4和待挤压镁合金供热,所述模具套筒3下端还设置有一组热电偶测温装置,所述热电偶测温装置与一组温控系统数据连接,所述温控系统与所述加热装置2电连接;所述可转动内部芯模4内竖直方向上加工有一组墩压通道41,所述墩压通道41通过一组中间通道43与挤压出口通道42连通,所述挤压出口通道42方向与所述墩压通道41垂直设置;所述外部芯模5上加工有一组最终挤压出口通道51。具体的,所述外部芯模5和所述可转动内部芯模4均为相互对称的两组模具组成。一种高强度镁合金的挤压模具的镁合金挤压方法,该方法包括如下步骤:步骤a、调整可转动内部芯模4与外部芯模5的相对位置,使可转动内部芯模4的挤压出口通道42与所述外部芯模5中的最终挤压出口通道51相背离。步骤b、将镁合金坯料的放入到模具可转动内部芯模4中;步骤c、将加热装置2放置在模具套筒中,接上电源后对模具芯模及加入其中的镁合金坯料进行加热;步骤d、开启连接控温系统的热电偶,监测到达实验温度后并对整个模具进行保温1h;步骤e、加热保温完成后,开启压力机进行挤压,直至冲头的下移量占镁合金长度的一半,关闭压力机;步骤f、开启芯模转动装置驱动可转动内部芯模4转动,转动180°后关闭芯模转动装置,使得可转动内部芯模4的挤压出口通道42与外部芯模5中的最终挤压出口通道51连通。步骤g、开启压力机,对镁合金进行进一步挤压;挤压结束后,关闭挤压机,取出挤压出的镁合金。具体的,所述镁合金为mg-nd-sn-ti镁合金,其中各元素的质量百分比为:nd:2.9wt.%-3.1wt.%,sn:4.9wt.%-5.1wt.%,ti:0.5wt.%-0.7wt.%,其余的为纯mg。具体的,所述步骤e中的挤压速度为1mm/s~30mm/s。具体的,所述步骤d中试验温度为375℃~425℃。实施例二:一种高强度镁合金的挤压模具的镁合金挤压方法,该方法包括如下步骤:镁合金的坯料选择为mg-4sn-3nd-1ti,经过固溶处理后采用线切割将镁合金坯料制成所需的尺寸,放置在模具芯模中,将模具冲头放置在坯料的上方。设置好控温系统的参数并然后开启加热装置的开关,为了促进装置的温度稳定,减少热损失;在模具表面包裹一层石棉进行阻热。调整模具内部模芯与外部模芯的位置。将直径为25mm,长度为135mm的镁合金坯料的放入到可转动内部芯模4中。将加热装置2连接模具套筒3中,接上电源后对可转动内部芯模4及加入其中的镁合金坯料进行加热。当整个模具的温度达到稳定温度375℃时,为了使得整个模具以及镁合金坯料的温度均匀,将整个模具保温1h。开启压力机进行挤压,直至冲头的下移量占合金尺寸的一半,关闭压力机。开启内部模芯转动装置,转动180°后关闭转动装置,使得内部模芯的出口与外部模芯底部正好连接。开启压力机,对镁合金进行进一步挤压;挤压结束后,关闭挤压机。关闭加热装置并将镁合金脱模,将脱模后的镁合金放在水中进行水淬,取出挤压出的镁合金,进行下一次挤压。将获得的镁合金采用标准的制样方式进行制样,然后抛光、腐蚀,在晶相显微镜下观察镁合金的晶粒尺寸。将试样重新打磨,采用维氏硬度仪对合金的硬度进行测量,其平均硬度为73.2hv。实施例三:一种高强度镁合金的挤压模具的镁合金挤压方法,该方法包括如下步骤:镁合金的坯料选择为mg-4sn-3nd-1ti,经过固溶处理后采用线切割将镁合金坯料制成所需的尺寸,放置在模具芯模中,将模具冲头放置在坯料的上方。设置好控温系统的参数并然后开启加热装置的开关,为了促进装置的温度稳定,减少热损失。在模具表面包裹一层石棉进行阻热。调整模具内部模芯与外部模芯的位置,外部芯模的出口与内部芯模的开口朝向完全相同。将直径为25mm,长度为135mm的镁合金坯料的放入到可转动内部芯模4中。将加热装置2连接模具套筒3中,接上电源后对可转动内部芯模4及加入其中的镁合金坯料进行加热。当整个模具的温度达到稳定温度400℃时,为了使得整个模具以及镁合金坯料的温度均匀,将整个模具保温1h。开启压力机进行挤压,直至冲头的下移量占合金尺寸的一半,关闭压力机。开启内部模芯转动装置,转动180°后关闭转动装置,使得内部模芯的出口与外部模芯底部正好连接。开启压力机,对镁合金进行进一步挤压;挤压结束后,关闭挤压机。关闭加热装置并将镁合金脱模,将脱模后的镁合金放在水中进行水淬,取出挤压出的镁合金,进行下一次挤压。关闭加热装置并将镁合金脱模,将脱模后的镁合金放在水中进行水淬。将获得的镁合金采用标准的制样方式进行制样,然后抛光、腐蚀,在晶相显微镜下观察镁合金的晶粒尺寸。将试样重新打磨,采用维氏硬度仪对合金的硬度进行测量,其平均硬度为82.6hv。实施例四:镁合金的坯料选择为mg-4sn-3nd-1ti,经过固溶处理后采用线切割将镁合金坯料制成所需的尺寸,放置在模具芯模中,将模具冲头放置在坯料的上方。设置好控温系统的参数并然后开启加热装置的开关,为了促进装置的温度稳定,减少热损失。在模具表面包裹一层石棉进行阻热。调整模具内部模芯与外部模芯的位置,外部芯模的出口与内部芯模的开口朝向完全相同。将直径为25mm,长度为135mm的镁合金坯料的放入到可转动内部芯模4中。将加热装置2连接模具套筒3中,接上电源后对可转动内部芯模4及加入其中的镁合金坯料进行加热。当整个模具的温度达到稳定温度375℃时,为了使得整个模具以及镁合金坯料的温度均匀,将整个模具保温1h。开启压力机进行挤压,直至冲头的下移量占合金尺寸的一半,关闭压力机。开启内部模芯转动装置,转动180°后关闭转动装置,使得内部模芯的出口与外部模芯底部正好连接。开启压力机,对镁合金进行进一步挤压。挤压结束后,关闭挤压机。关闭加热装置并将镁合金脱模,将脱模后的镁合金放在水中进行水淬,取出挤压出的镁合金,进行下一次挤压。将获得的镁合金采用标准的制样方式进行制样,然后抛光、腐蚀,在晶相显微镜下观察镁合金的晶粒尺寸。将试样重新打磨,采用维氏硬度仪对合金的硬度进行测量,其平均硬度为79.3hv。实施例五:本对比例与实施方式一、二、三、四的区别仅在于:对比例中的镁合金材料为熔炼均匀的镁合金坯料,只进行固溶处理而未进行任何的热挤压;采用维氏硬度仪对合金的硬度进行测量,其平均硬度为59.6hv。按照gb/t4338-2006标准对制得的镁合金材料进行维氏硬度的测试,(单位为hv)结果如表1所示。测试实施例二实施例二实施例二实施例五硬度(hv)73.282.679.359.6表1由表1中实施例测试结果对比可知,本发明将在400℃对mg-4sn-3nd-1ti合金进行挤压,采用正挤压-墩压-等通道挤压三种技术相结合的方式制备高强镁合金。以上实施例只是对本专利的示例性说明,并不限定它的保护范围,本领域技术人员还可以对其局部进行改变,只要没有超出本专利的精神实质,都在本专利的保护范围内。当前第1页12