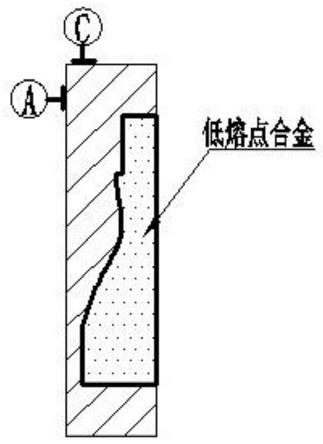
[0001]
本发明属于精密加工技术领域,涉及小尺寸叶片的三轴数铣加工方法。
背景技术:[0002]
叶片是工业制造中非常重要的一类零件,对产品的性能起着关键作用。产品的效率、使用寿命等指标的高低,都直接受叶片的设计和制造质量的影响,而且是主要影响。尤其精密加工领域中的叶片对产品的性能影响至关重要,这是因为该领域中的叶片大多形状不规则,且尺寸计算复杂,与普通零件有很大差异。
[0003]
目前,对于叶片,尤其是针对尺寸为叶身长度30mm以下,叶片弦宽20mm左右的小尺寸叶片,其制造主要通过以下工艺过程来实现:1)毛坯制造阶段,原材料经过锻造或铸造成型后,经热处理、理化检验、尺寸检验等过程,然后发往机械加工车间进行机械加工。2)叶片机械加工阶段,由叶片毛坯,经过机械加工,是叶片达到图纸设计尺寸。同时配合表面处理和特种检验工序,叶片经最终检验后发往装配车间装配。
[0004]
由于上述加工工艺需要设计制造专用精锻或精铸模具,投入成本高且制造周期长,制造工艺复杂。随着五轴数铣的发展,切削加工性能好的叶片可由五轴加工中心一次性加工成型,但需要配备综合性能良好的五轴加工中心,其加工成本高,对设备要求高,不利于小批量加工生产。
技术实现要素:[0005]
本发明解决的问题在于提供小尺寸叶片的三轴数铣加工方法,用于解决现有技术中使用五轴数铣加工工艺来制造小尺寸叶片而造成的加工成本高,对设备要求高,不利于小批量加工生产等的问题。
[0006]
本发明是通过以下技术方案来实现的:
[0007]
小尺寸叶片的三轴数铣加工方法,包括以下步骤:
[0008]
1)将毛坯铣加工为长方体,并以三轴数铣加工中心的轴为基准确定长方体毛坯的基准面a、基准面b和基准面c;其中,基准面a基准面b和基准面c两两相互垂直;
[0009]
2)将所述长方体毛坯的基准面a贴合置于工作台上,刀具垂直于所述基准面a设置且自所述基准面a的相对面上下刀,顺次进行粗铣、半精铣和精铣处理逐层加工出所述叶盆面;
[0010]
3)用辅助合金对所述叶盆面进行浇注,直至其完全填充整个所述叶盆面;待所述辅助合金凝固结晶后,将溢出所述叶盆面的辅助合金去除,以使浇注后形成的表面不影响加工定位精度为准;
[0011]
4)将所述长方体毛坯的基准面a的相对面贴合置于工作台上,刀具垂直于所述基准面a设置且自所述基准面a上下刀,顺次进行粗铣、半精铣和精铣处理逐层加工出所述叶背面;
[0012]
5)将所述长方体毛坯置于电阻炉上加热至150
°
,以去除所述叶盆面内的辅助合
金;
[0013]
6)线切割掉叶片型面上的余量部分并进行抛磨处理,再线切割掉工艺凸台,最终得到小尺寸叶片。
[0014]
所述步骤6)具体为,所述线切割是在保留打磨余量的前提下,自叶片型面沿切线方向向对两边的余量进行切割,然后再切除两边之间的余量,所保留有打磨余量为:单边余量厚度、两边之间的余量厚度为0.06mm~0.1mm;然后对打磨余量进行抛光打磨处理,以打磨出进气边和排气边;再线切割掉所述工艺凸台,最终得到所述小尺寸叶片。
[0015]
所述步骤6)的抛光打磨还包括:初抛:采用木轮对叶片的转接r以及前缘、后缘进行打磨以去除线切割后保留的余量;然后采用带柄百叶轮打磨头对所述叶片的叶盆、叶背上的铣加工残留纹路进行抛光处理;精抛:采用纤维轮对所述叶片的转接r、前缘、后缘以及叶背进行抛光处理;然后采用中硬型尼龙纤维轮对所述叶片的叶盆进行抛光处理后,采用软型尼龙纤维轮对所述叶片的叶盆进行抛光处理;其中,所述木轮的规格为exl轮、6
”×
1/4
”×
3/4”、杨树材质;所述带柄百叶轮打磨头的规格为30
×
25
×
6mm、80目;所述纤维轮的规格为exl轮、6
”×
1/4
”×
3/4”;所述中硬型尼龙纤维轮包括规格为20
×
20mm、10
×
10mm、硬度在6~7范围内的尼龙纤维轮;所述软型尼龙纤维轮包括规格为20
×
10mm、10
×
10mm、硬度在2~3范围内的尼龙纤维轮。
[0016]
在进行所述精抛处理之前,在所述的纤维轮、中硬型尼龙纤维轮和软型尼龙纤维轮上均匀涂抹上小白蜡抛光膏。
[0017]
所述精抛处理的操作为沿所述叶片的长度方向往复进行多次抛光处理。
[0018]
所述辅助合金的熔点小于等于150
°
。
[0019]
与现有技术相比,本发明的有益效果是:
[0020]
本发明提供的小尺寸叶片的三轴数铣加工方法,在叶片制造时选用三轴数铣:首先铣加工叶盆面,其次加工叶背面,但在加工叶背面时,因为叶盆面已加工,加之以叶身厚度小,容易导致叶片型面受切削力而变形,使得产品质量不合格。此外,在加工过程中容易将叶片表面啃伤,型面精度难以达到要求。为解决此变形问题,在加工叶背时在叶盆型腔浇满低于加工材料熔点的辅助合金,不会给叶片本身带来质量问题。待辅助合金凝固结晶后,叶背面加工完成后,加热去除辅助合金。另外,为防止轻微啃伤导致叶身表面缺陷,在加工叶片时为了提高制造效率,改进了叶片进排气边的加工余量,在加工时叶片型面单边加厚0.06mm~0.1mm余量,且沿切线方向向两边延伸,如此可以在不伤及进、排气边前后缘半径的情况下尽可能的减少抛磨余量,提高加工效。待叶片铣加工成型后用线切割将多余部分切除,将此余量抛磨去除。本发明提供的加工方法简单、效率高,且对设备要求低,由此能够降低生产成本低,尤其适用于小批量加工。
附图说明
[0021]
图1为本发明小尺寸叶片的立体图;
[0022]
图2为另一角度下本发明小尺寸叶片的立体图;
[0023]
图3为常规叶片进气边和排气边预留余量示意图;
[0024]
图4为本发明叶片进气边和排气边预留余量示意图;
[0025]
图5为本发明铣加工叶盆面示意图;
[0026]
图5a为图5的a-a剖视图;
[0027]
图6为本发明浇注辅助合金示意图;
[0028]
图6a为图6的a-a剖视图;
[0029]
图7为本发明铣加工叶背面示意图;
[0030]
图7a为图7的a-a剖视图;
[0031]
图8为本发明叶片的线性面;
[0032]
图9为本发明线切割后得到的小尺寸叶片示意图;
[0033]
图10为本发明小尺寸叶片的主视图;
[0034]
图11为本发明小尺寸叶片的侧视图;
[0035]
图12为本发明小尺寸叶片的后视图。
具体实施方式
[0036]
下面结合附图对本发明进行详细的说明。
[0037]
在本发明的描述中,需要理解的是,术语“中心”、“上”、“下”、“前”、“后”、“左”、“右”、“竖直”、“水平”、“顶”、“底”、“内”、“外”等指示的方位或位置关系为基于附图所示的方位或位置关系,仅是为了便于描述本发明和简化描述,而不是指示或暗示所指的装置或元件必须具有特定的方位、以特定的方位构造和操作,因此不能理解为对本发明的限制。
[0038]
术语“第一”、“第二”仅用于描述目的,而不能理解为指示或暗示相对重要性或者隐含指明所指示的技术特征的数量。由此,限定有“第一”、“第二”的特征可以明示或者隐含地包括一个或者更多个该特征。在本发明的描述中,除非另有说明,“多个”的含义是两个或两个以上。
[0039]
在本发明的描述中,需要说明的是,除非另有明确的规定和限定,术语“安装”、“相连”、“连接”应做广义理解,例如,可以是固定连接,也可以是可拆卸连接,或一体地连接;可以是直接相连,也可以通过中间媒介间接相连,可以是两个元件内部的连通。对于本领域的普通技术人员而言,可以具体情况理解上述术语在本发明中的具体含义。
[0040]
本发明提供小尺寸叶片的三轴数铣加工方法,其中,小尺寸叶片的结构如图1、图2所示,可以看出该叶片扭转角大,叶片型面复杂,叶身厚度小且叶身前、后缘半径小。其加工包括以下步骤:
[0041]
1)将毛坯铣加工为长方体,并以三轴数铣加工中心的轴为基准确定长方体毛坯的基准面a、基准面b和基准面c;其中,基准面a基准面b和基准面c两两相互垂直;
[0042]
2)在所述基准面a的相对面上铣加工出叶盆面:参照图5、图5a,将所述长方体毛坯的基准面a贴合置于工作台上,刀具垂直于所述基准面a设置且自所述基准面a的相对面上下刀,顺次进行粗铣、半精铣和精铣处理逐层加工出所述叶盆面;
[0043]
3)用辅助合金对所述叶盆面进行浇注,如图6、图6a所示,直至其完全填充整个所述叶盆面;待所述辅助合金凝固结晶后,将溢出所述叶盆面的辅助合金去除,以使浇注后形成的表面不影响加工定位精度为准;
[0044]
4)在所述基准面a上铣加工出叶背面:如图7、图7a所示,将所述长方体毛坯的基准面a的相对面贴合置于工作台上,刀具垂直于所述基准面a设置且自所述基准面a上下刀,顺次进行粗铣、半精铣和精铣处理逐层加工出所述叶背面;
[0045]
5)去除所述叶盆面内的辅助合金;
[0046]
6)参照图8、图9,线切割掉叶片型面上的多余部分并进行抛磨处理,再线切割掉工艺凸台,最终得到小尺寸叶片。
[0047]
本发明提供的小尺寸叶片的三轴数铣加工方法,在叶片制造时选用三轴数铣:首先铣加工叶盆面,其次加工叶背面,但在加工叶背面时,因为叶盆面已加工,加之以叶身厚度小,容易导致叶片型面受切削力而变形,使得产品质量不合格。此外,在加工过程中容易将叶片表面啃伤,型面精度难以达到要求。为解决此变形问题,在加工叶背时在叶盆型腔浇满低于加工材料熔点的辅助合金,不会给叶片本身带来质量问题。待辅助合金凝固结晶后,叶背面加工完成后,加热去除辅助合金。另外,为防止轻微啃伤导致叶身表面缺陷,在加工叶片时为了提高制造效率,改进了叶片进排气边的加工余量,在加工时叶片型面单边加厚0.06mm~0.1mm余量,且沿切线方向向两边延伸,如此可以在不伤及进、排气边前后缘半径的情况下尽可能的减少抛磨余量,提高加工效。待叶片铣加工成型后用线切割将多余部分切除,将此余量抛磨去除。本发明提供的加工方法简单、效率高,且对设备要求低,由此能够降低生产成本低,尤其适用于小批量加工。本发明提供的小尺寸叶片的三轴数铣加工方法在工业生产的应用过程中,大大缩短了此类航空叶片的制造周期,节省了设备成本,取得了一定的经济效益。
[0048]
所述步骤6)具体为,所述线切割是在保留打磨余量的前提下,自叶片型面沿切线方向向对两边的余量进行切割,然后再切除两边之间的余量,所保留有打磨余量为:单边余量厚度、两边之间的余量厚度为0.06mm~0.1mm;然后对打磨余量进行抛光打磨处理,以打磨出进气边和排气边;再线切割掉所述工艺凸台,最终得到所述小尺寸叶片。如图3所示,常规加工叶片进排气边余量向两边加厚延伸,给后续抛磨等工序带来很大的困难,而本发明加工叶片时为了提高制造效率,改进了叶片进气边和排气边上留有的加工余量方式。
[0049]
参照图4,所述步骤6)具体为,在叶片型面上留有沿切线方向向两边延伸、单边厚度为0.06mm~0.1mm的余量后,两边之间也留有0.06mm~0.1mm的余量。如此可以在不伤及进气边、排气边前后缘半径的情况下尽可能的减少抛磨余量,提高加工效率。待叶片铣加工成型后用线切割将多余部分切除,将此余量抛磨去除,最终得到所述小尺寸叶片。
[0050]
参见图10、图11及图12,所述步骤6)的抛光打磨还包括:
[0051]
初抛:采用木轮对叶片的转接r以及前缘、后缘进行打磨以去除线切割后保留的余量;然后采用带柄百叶轮打磨头对所述叶片的叶盆、叶背上的铣加工残留纹路进行抛光处理;
[0052]
精抛:采用纤维轮对所述叶片的转接r、前缘、后缘以及叶背进行抛光处理;然后采用中硬型尼龙纤维轮对所述叶片的叶盆进行抛光处理,再采用软型尼龙纤维轮对所述叶片的叶盆进行抛光处理。
[0053]
其中,所述木轮的规格为exl轮、直径
×
厚度
×
圆心为6
”×
1/4
”×
3/4”,单位为英寸(即直径为15.2cm、厚度为0.6cm、圆心为1.9cm)、硬度可以为中硬型、杨树材质。所述带柄百叶轮打磨头的规格为,直径
×
高度
×
柄径为30
×
25
×
6mm、目数为80目。所述纤维轮的规格为exl轮、直径
×
厚度
×
圆心为6
”×
1/4
”×
3/4”,单位为英寸(即直径为15.2cm、厚度为0.6cm、圆心为1.9cm)、硬度可以为软型,其硬度与软型尼龙纤维轮一致;所述中硬型尼龙纤维轮包括规格为20
×
20mm、10
×
10mm、硬度在6~7范围内的两种尼龙纤维轮;所述软型尼龙
纤维轮包括规格为20
×
10mm、10
×
10mm、硬度在2~3范围内的两种尼龙纤维轮。木轮、纤维轮可以选用3m牌。
[0054]
具体的,初抛为:使用韧性好、耐磨的木轮对叶片的转接r以及前缘、后缘的多余量进行抛光,再使用适用于对加工过程中产生刀纹进行前处理抛光的带柄百叶轮打磨头对所述叶片的叶盆、叶背上的刀纹进行抛光处理。
[0055]
精抛为:使用不易造成叶片的过热的纤维轮对叶片的转接r、前缘、后缘以及叶背进行抛光,并使用软、硬规格不同的尼龙纤维轮对叶片的叶盆进行抛光。通过使用不同的抛光工具在叶片抛光的不同需求阶段进行专项处理,能够保证在达到抛光需求的同时减少对叶片的损伤。
[0056]
优选的,在进行所述精抛处理之前,在所述的纤维轮、中硬型尼龙纤维轮和软型尼龙纤维轮上均匀涂抹上小白蜡抛光膏。该抛光膏颗粒细、油腻,有良好的光饰作用,在精抛时将小白蜡抛光膏涂抹在抛光工具上可以提高叶片表面的光洁度。
[0057]
更优选的,所述精抛处理的操作为沿所述叶片的长度方向往复进行多次抛光处理。一般地,往复操作3-5次即可满足要求。
[0058]
在抛光处理完成后,使用三坐标检测设备对利用该抛光方法加工得到的叶片按截面进行检测并与理论模型进行对比,得出叶片为合格产品。可以看出,该抛光方法大大缩短了此类叶片的抛光周期、节省了成本;并且,还有效地提升了抛光质量,降低了不合格品率。
[0059]
所述辅助合金的熔点小于等于150
°
,远低于加工材料熔点。加工好叶背后,将其整个置于电阻炉上加热至150
°
,然后去除该辅助合金。不会在加工过程中给该小尺寸叶片带来质量问题。其中,所述的辅助合金一般为锡铋辅助合金。
[0060]
本发明的内容不限于实施例所列举,本领域普通技术人员通过阅读本发明说明书而对本发明技术方案采取的任何等效的变换,均为本发明的权利要求所涵盖。