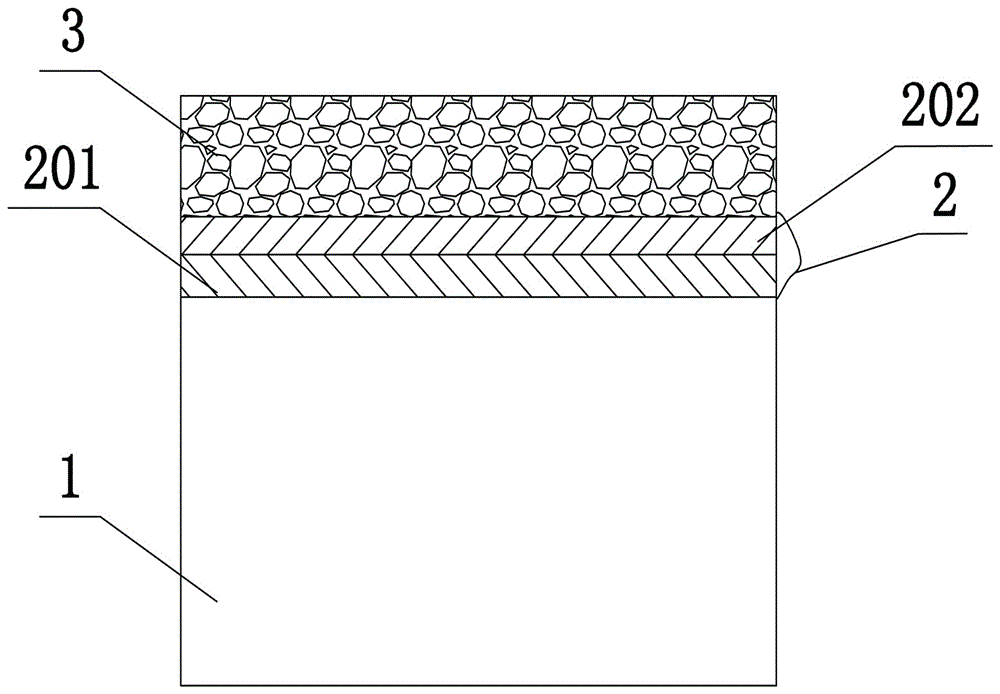
本发明涉及涂层刀具
技术领域:
,具体的说,涉及了一种超硬复合涂层刀具及其制备方法。
背景技术:
:随着现代机械加工工业的发展,对切削工具的使用性能提出了更高的要求。现有技术中,通常通过在刀具基体上涂覆一层或多层硬度高、耐磨性好的复合涂层,使得基体的高强度、高韧性和涂层的高硬度、高耐磨性相结合,从而达到降低切削工具与工件之间的摩擦因数,提高切削工具的耐磨性。其中,立方氮化硼涂层因具有高硬度、高耐磨性和良好的红硬性,对铁系金属元素有较大的化学惰性,因此立方氮化硼涂层被广泛用作涂层材料,然而立方氮化硼涂层与硬质合金基体之间存在硬度、弹性模量及热膨胀系数不匹配的现象,在热喷涂过程中,立方氮化硼涂层与基体的结合界面会产生残余应力,导致立方氮化硼涂层与硬质合金基体的结合力不强,在使用过程中易产生涂层剥离现象,影响了涂层切削工具质量和使用寿命。为了解决以上存在的问题,人们一直在寻求一种理想的技术解决方案。技术实现要素:本发明的目的是针对现有技术的不足,从而提供一种层间结合力强、内应力低、耐磨性能及抗冲击性能高的超硬复合涂层刀具及其制备方法。为了实现上述目的,本发明所采用的技术方案是:一种超硬复合涂层刀具,它包括硬质合金基体和依次喷涂在所述硬质合金基体表面的金属过渡层和掺杂有金属镍的立方氮化硼涂层,其中,在所述掺杂有金属镍的立方氮化硼涂层中,所述金属镍包覆在所述立方氮化硼晶体表面,且所述金属镍的总质量占所述表面包覆有金属镍的立方氮化硼晶体总质量的20%~50%。基于上述,所述金属过渡层为Ti层、Cr层、Nb层、Ta层和Zr层中的一种或几种的组合,且所述金属过渡层的厚度为30微米~50微米。基于上述,所述掺杂有金属镍的立方氮化硼涂层厚度为200微米~400微米。本发明还提供一种超硬复合涂层刀具的制备方法,它包括以下步骤:(1)第一次采用超音速火焰喷涂法在硬质合金基体表面喷涂金属过渡层,制得喷涂金属过渡基体,其中,所述金属过渡层为Ti层、Cr层、Nb层、Ta层和Zr层中的一种或几种的组合;(2)第二次采用超音速火焰喷涂法,以表面包覆有金属镍的立方氮化硼复合微粉为喷涂原料,在所述喷涂金属过渡层基体表面喷涂掺杂有金属镍的立方氮化硼涂层,从而制得超硬复合涂层刀具,其中,所述金属镍的总质量占所述表面包覆有金属镍的立方氮化硼复合微粉总质量的20%~50%。基于上述,所述步骤(1)中的超音速火焰喷涂法工艺参数为:燃料压力为0.75MPa~1.4MPa、燃料流量为5L/h~12L/h、氧气压力为0.45MPa~0.65MPa、氧气流量为9L/h~15L/h、送粉流量为3kg/h~6kg/h、送粉气体为氮气、喷涂距离为150mm~220mm。基于上述,所述步骤(2)中的超音速火焰喷涂法工艺参数为:燃料压力为0.75MPa~1.4MPa、燃气流量为7L/h~15L/h、氧气压力为0.75MPa~1.9MPa、氧气流量为12L/h~18L/h、送粉流量为6kg/h~10kg/h、送粉气体为氮气、喷涂距离为190mm~260mm。基于上述,所述表面包覆有金属镍的立方氮化硼复合微粉的粒径为10微米~45微米。基于上述,所述步骤(1)还包括在对所述预涂覆基体表面喷涂金属过渡层前,依次对所述预涂覆基体进行超声清洗、毛化和采用丙酮清洗的步骤。本发明相对现有技术具有突出的实质性特点和显著的进步,具体的说,本发明在硬质合金基体上依次喷涂金属过渡层和掺杂有金属镍的立方氮化硼涂层,利用金属过渡层与硬质合金基体间良好的润湿性,缓解了单一的氮化硼涂层及掺杂有金属镍的立方氮化硼涂层与硬质合金基体结合力较弱的问题,同时通过具有较高喷射速度的超音速火焰喷涂工艺,使得各涂层之间及金属过渡层涂层与硬质合金基体有较强的界面结合力。另一方面,在喷涂所述掺杂有金属镍的立方氮化硼涂层时,热喷涂材料采用金属镍包覆立方氮化硼微粉形成的复合微粉,避免了喷涂过程中立方氮化硼复合微粉发生六方晶型相变,同时包覆在氮化硼晶体表面的金属镍连同所述金属过渡层,可有效吸收界面间的残余应力,缓解了掺杂有金属镍的立方氮化硼涂层与硬质合金基体存在的界面物理性能突变,避免了温差工况条件下涂层的脱落和碎裂,显著改善了超硬涂层与硬质合金基体的结合性能。本发明所提供的超硬复合涂层刀具结构设计合理、耐磨性能优异、层间结合力强、使用寿命长;本发明所提供的制备方法工艺简单,设备可自动化操作,易于实现工业化。附图说明图1是本发明实施例1提供的超硬复合涂层刀具结构示意图。图2是本发明实施例3提供的超硬复合涂层刀具结构示意图。图中:1、硬质合金基体;2、金属过渡层;3、掺杂有金属镍的立方氮化硼涂层;201、金属Cr层;202、金属Nb层。具体实施方式下面通过具体实施方式,对本发明的技术方案做进一步的详细描述。实施例1本实施例提供一种超硬复合涂层刀具,其结构如图1所示,它包括用于承载所述超硬复合涂层的硬质合金基体1,以及依次喷涂在所述硬质合金1表面的金属过渡层2和掺杂了金属镍的立方氮化硼涂层3。其中,在所述掺杂有金属镍的立方氮化硼涂层中,所述金属镍包覆在所述立方氮化硼晶体表面,且所述金属镍的总质量占表面包覆有金属镍的所述立方氮化硼晶体总质量的20%。本实施例中,所述金属过渡层2为金属钛层,所述金属钛层的厚度为50微米,所述掺杂了金属镍的立方氮化硼涂层厚度为400微米。本实施例还提供一种上述超硬复合涂层刀具的制备方法,它包括以下步骤:(1)首先对硬质合金基体进行超声清洗和毛化处理,并采用丙酮对所述硬质合金表面进行清洗;然后第一次采用超音速火焰喷涂法在硬质合金基体表面喷涂厚度为50微米的金属钛层,制得喷涂金属过渡基体;其中,超音速火焰喷涂法的工艺参数为:燃料压力为1.4MPa、燃料流量为12L/h、氧气压力为0.65MPa、氧气流量为15L/h、金属钛粉送粉流量为6kg/h、送粉气体为氮气、喷涂距离为220mm。(2)第二次采用超音速火焰喷涂法在所述喷涂金属过渡基体表面喷涂厚度为400微米的掺杂有金属镍的立方氮化硼涂层,从而制得超硬复合涂层刀具;其中,喷涂原料选取粒度为10微米~45微米的表面包覆有金属镍的立方氮化硼复合微粉,且所述金属镍的总质量占表面包覆有金属镍的所述立方氮化硼复合微粉总质量的20%。本步骤中,超音速火焰喷涂法的工艺参数为:燃料压力为0.75MPa、燃气流量为10L/h、氧气压力为1.5MPa、氧气流量18L/h、金属镍包覆立方氮化硼复合微粉送粉流量为10kg/h、送粉气体为氮气、喷涂距离为190mm。实施例2本实施例提供一种超硬复合涂层刀具,具体结构同实施例1中的超硬复合涂层刀具结构。本实施例还提供一种上述超硬复合涂层刀具的制备方法,具体步骤与实施例1中的步骤大致相同,不同之处在于:本实施例的所述步骤(1)中在硬质合金基体表面涂覆的金属过渡层为厚度为45微米的金属铬层;本实施例的所述步骤(1)中超音速火焰喷涂法的工艺参数为:燃料压力为1.0MPa、燃料流量为10L/h、氧气压力为0.5MPa、氧气流量为10L/h、送粉流量为5kg/h、送粉气体为氮气、喷涂距离为200mm。实施例3本实施例提供一种超硬复合涂层刀具,具体结构如图2所示,它包括用于承载所述超硬复合涂层的硬质合金基体1,以及依次涂覆在所述硬质合金1表面的金属Cr层201、金属Nb层202和掺杂了金属镍的立方氮化硼涂层3。其中,在所述掺杂有金属镍的氮化硼涂层中,所述金属镍包覆在所述氮化硼晶体表面,且所述金属镍的总质量占表面包覆有金属镍的所述立方氮化硼晶体总质量的50%。所述金属Cr层201和所述金属Nb层202厚度均为25微米,所述掺杂了金属镍的立方氮化硼涂层3的厚度为300微米。本实施例提供一种超硬复合涂层刀具的制备方法,具体步骤与实施例1中的步骤大致相同,不同之处在于:本实施例的所述步骤(1)中在硬质合金基体表面涂覆的金属过渡层厚度为50微米,包括厚度为25微米的金属Cr层和涂层在所述金属Cr层上的厚度为25微米的金属Nb层。本实施例的所述步骤(2)中超音速火焰喷涂法的工艺参数为:超音速火焰喷涂法的工艺参数为:燃料压力为0.9MPa、燃气流量为9L/h、氧气压力为0.8MPa、氧气流量为15L/h、送粉流量为8kg/h、送粉气体为氮气、喷涂距离为250mm。性能测试分别对实施例1~3所提供的超硬复合涂层刀具进行维氏硬度、层间结合力、掺杂有金属镍的立方氮化硼涂层中的六方氮化硼进行检测,检测结果如表1所示。由表中可以看出,实施例1~3所提供的超硬复合涂层刀具均具有较高的维氏硬度和较强的层间结合力,同时在涂层中均未发现有六方氮化硼成分,从而验证了热喷涂材料采用金属镍包覆立方氮化硼复合微粉,表面包覆的金属镍可以防止立方氮化硼微粉在喷涂过程中发生六方晶型相变。表1、实施例1~3提供的超硬复合涂层刀具性能检测维氏硬度层间结合力六方氮化硼含量实施例1318069Mpa无实施例2321572Mpa无实施例3320070Mpa无最后应当说明的是:以上实施例仅用以说明本发明的技术方案而非对其限制;尽管参照较佳实施例对本发明进行了详细的说明,所属领域的普通技术人员应当理解:依然可以对本发明的具体实施方式进行修改或者对部分技术特征进行等同替换;而不脱离本发明技术方案的精神,其均应涵盖在本发明请求保护的技术方案范围当中。当前第1页1 2 3