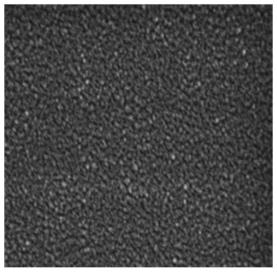
一种原子层沉积技术生长sns
x
薄膜的方法
技术领域
1.本发明属于纳米材料制备技术领域,尤其涉及一种原子层沉积技术生长sns
x
薄膜的方法。
背景技术:2.纳米结构的金属硫化物具有优良的磁性、电子和光学性质。其中sns
x
由于其具有优异广电特性以及低成本、无毒等优势在光伏、电化学催化等领域吸引了人们广泛的关注。传统制备sns
x
薄膜涂层的方法主要有电沉积、化学水浴沉积、物理气相沉积等。近年来,原子层沉积(ald)技术已经逐渐成为制备sns
x
薄膜涂层的前沿技术。ald的自限性表面化学反应,允许纳米材料沉积在各种复杂的表面或三维结构上,具有显着的重现性,且对薄膜厚度,材料成分等控制精确。在过去的几年里,ald一直在迅速发展。
3.ald过程的实质是基于前驱体的一系列表面化学反应过程,因此前驱体是ald制备相关纳米材料的基础原料,合适、匹配的前驱体组合是制备材料成功的关键。金属前驱体受ald技术特点限制,需要有好的挥发性、热稳定性以及与制备某种目标材料所需的另一种前驱体之间具备合适的反应活性。此外,不同的前驱体组合对所制备薄膜材料的种类和性能也具有非常重要的影响。目前已经有少量通过ald技术制备sns
x
薄膜的报道,然而所使用硫源基本都是硫化氢气体,不易存储运输,同时具有剧毒、易燃、腐蚀性,使用时不许遵守严格的操作步骤,存在较大安全隐患,这些问题在很大程度上阻碍了ald新型sns
x
制备方法的拓展与开发。因此,寻找出合适的、匹配性高的sn和s前驱体组合尤为重要。鉴于sns
x
材料的广泛和重要应用,迫切需要具有更多具有可行性的sns
x ald合成工艺,促进基于sns
x
的薄膜材料在上述领域的发展。
技术实现要素:4.为了解决上述技术问题,本发明提供一种原子层沉积技术生长sns
x
薄膜的方法,本发明的方法能够在纳米级的衬底上沉积形成sns
x
的沉积层。本发明通过大量实验,获得了一种液态、低(无)毒硫源替代硫化氢,用于ald工艺制备相关硫化物。通过在大量含硫有机物如硫醚(结构为r-s-r,其中r为c1-c4的烷烃,具体例如二甲硫醚ch
3-s-ch3)、二硫醚(结构为r-s-s-r,其中r为c1-c4的烷烃,具体例如二甲二硫醚ch
3-s-s-ch3)、硫醇(结构为r-sh,其中r为c1-c4的烷烃,具体例如异丙基硫醇i-pr-sh)中进行尝试,最终确定只有硫醇作为液态硫源才具有足够的反应活性与sn(acac)2通过ald技术制备sns
x
材料。同时,相对于传统ald硫源硫化氢,硫醇易存储运输、操作简便、毒性大大降低。
5.本发明的第一个目的是提供一种原子层沉积技术ald生长sns
x
薄膜的方法,包括以下步骤:
6.步骤一:将衬底置于反应腔中,在真空条件下,以脉冲形式向反应腔中通入sn源sn(acac)2进行沉积,得到沉积有sn源的衬底;
7.(2)向体系中充入惰性气体进行吹扫;
8.(3)将硫醇作为硫源,以脉冲形式通入反应腔,与沉积在衬底上的sn源进行单原子反应,得到纳米sns
x
薄膜;
9.(4)向体系中充入惰性气体进行吹扫,完成一个ald生长循环;
10.重复(1)~(4)若干次数,即可得到生长有一定厚度sns
x
沉积层;
11.可选的,所述衬底为钛、氧化硅、氧化钛、玻璃中的一种或一种以上。
12.可选的,为了进一步的保证原子层沉积设备中各管路及腔体内无水氧残留,在放置衬底前,本发明可对原子层沉积设备的管路及反应腔体进行抽空。
13.可选的,所述步骤(1)中以脉冲形式向反应腔中通入气相sn源的单个脉冲的持续时间为0.05~20s。
14.可选的,所述sn(acac)2的结构式如下:
[0015][0016]
可选的,所述步骤(1)中气相sn源在载气存在条件下以脉冲形式通入;所述载气的流量为10~200sccm。
[0017]
可选的,所述步骤(1)中的sn源的载气为高纯氮气或高纯氩气中的一种或者一种以上。
[0018]
可选的,所述步骤(1)中可以对sn源进行加热,使之气化,得到气相sn源。
[0019]
可选的,所述对sn源加热的温度为25~200℃。
[0020]
可选的,所述步骤(1)中的沉积温度为125~400℃。
[0021]
可选的,所述步骤(2)中吹扫时间为1~50s;惰性气体流量为10~300ml/min,维持体系压力为1.5
×
103~8
×
103pa。
[0022]
可选的,所述的惰性气体为高纯氮气或高纯氩气中的一种或者一种以上。
[0023]
可选的,所述步骤(3)中所述硫醇结构为r-sh,其中r为c1-c4的烷烃。
[0024]
可选的,所述步骤(3)中所述硫醇为叔丁基硫醇(t-bu-sh)、正丁基硫醇(n-bush)、异丙基硫醇(i-pr-sh)或者正丙基硫醇(n-pr-sh)中一种或者一种以上。
[0025]
可选的,所述步骤(3)中将硫源以脉冲形式通入反应腔的单个脉冲的持续时间为0.01~20s。
[0026]
可选的,所述步骤(3)中硫源在载气存在条件下以脉冲形式通入;所述载气的流量为10~200sccm。
[0027]
可选的,所述硫源的载气为高纯氮气或高纯氩气中的一种或者一种以上。
[0028]
可选的,所述步骤(3)中可以将所述的硫源加热,所述加热硫源的温度为15~150℃。
[0029]
可选的,重复步骤(1)~(4)的操作1~3000次;通过重复不同次数制备得到不同厚度的sns
x
沉积层。
[0030]
本发明的第二个目的是提供一种采用本发明的方法制备得到的snsx薄膜。
[0031]
有益效果:
[0032]
(1)本发明系第一次以液态硫醇为硫源通过原子层沉积(ald)的方法生长出含有
sns
x
的薄膜,对sns
x
纳米材料技术意义重大,且以异丙基硫醇作为硫源所沉积的sns
x
薄膜的速率较高,能有效提高纳米材料的制备效率。
[0033]
(2)相比较于传统的磁控溅射,化学水浴沉积、溶胶-凝胶法等制备纳米材料的方法,使用ald生长的sns
x
薄膜保型性良好,且对薄膜厚度,材料成分控制精确。
[0034]
(3)对多种衬底如钛、氧化硅、氧化钛、玻璃等均表现出兼容性。
[0035]
(4)硫醇作为硫源相对于传统硫源硫化氢易存储运输、操作简便、毒性大大降低。
附图说明
[0036]
图1为本发明实施例1中的sns
x
薄膜的平面sem图片;
[0037]
图2为本发明实施例1中的sns
x
薄膜的截面sem图片。
具体实施方式
[0038]
本发明提供了一种以硫醇为硫源通过原子层沉积技术(ald)生长sns
x
薄膜的方法,包括以下步骤;(1)将衬底置于反应腔中,在真空条件下,以脉冲形式向反应腔中通入气相sn源进行沉积,得到沉积有sn源的衬底,所述sn源为sn(acac)2;(2)向体系中充入惰性气体进行吹扫;(3)将硫醇作为硫源以脉冲形式通入反应腔,与沉积在衬底上的sn源进行反应,得到纳米sns
x
薄膜,所述硫醇结构为r-sh,其中r为c1-c4的烷烃;(4)向体系中充入惰性气体吹扫,完成一个ald循环;重复步骤(1)~(4)的操作1~3000次,即可得到生长有一定厚度sns
x
薄膜的沉积层。
[0039]
为了进一步的保证原子层沉积设备中各管路及腔体内无水氧残留,在放置衬底前,本发明可选对原子层沉积设备的管路及反应腔体进行抽空。
[0040]
在本发明中,衬底可选包括钛、氧化硅、氧化钛、玻璃中的一种或一种以上。
[0041]
本发明可选对所述sn源进行加热,使之气化,得到气相sn源,所述对sn源加热的温度可选为25~200℃,更可选为50~180℃,具体的,可以是75℃、120℃、150℃或180℃。
[0042]
在本发明中,所述气相sn源的单个脉冲的持续时间可选为0.05~20s,更可选为1~18s,最可选为3~15s,具体的,在本发明的实施例中,可以是2s、6s、8s或12s;所述沉积的温度可选为125~400℃,更可选为150~350℃,最可选为200~300℃,具体的,在本发明的实施例中,可以是200℃、240℃、265℃或315℃;所述气相sn源的载气可选为高纯氮气或高纯氩气,所述载气的流量可选为10~200sccm,更可选为20~160sccm,最可选为60~120sccm,具体的,可以是20sccm、80sccm、120sccm或150sccm。
[0043]
完成一次sn源的沉积后,本发明可选采用高纯氮气或高纯氩气对反应腔体进行吹扫清洗,清洗的时间可选为5~50s,更可选为10~45s,最可选为15~40s。
[0044]
然后,本发明将硫源以气相脉冲形式通入反应腔内,与沉积在衬底上的sn源进行反应,得到沉积有含sns
x
沉积层的衬底,在本发明中,所述硫醇结构为r-sh,其中r为c1-c4的烷烃,具体的,在本发明的实施例中,硫源可采用n-pr-sh、i-pr-sh、n-bu-sh、t-bu-sh。本发明可选将所述硫源加热,使之气化,形成气态硫源。所述加热硫源的温度可选为15~150℃,具体的,在本发明的实施例中,可以是60℃、40℃、80℃或25℃。
[0045]
在本发明中,所述通入硫源的单个脉冲持续时间可选为0.01~20s,更可选为1~15s,更可选为5~10s,具体的,在本发明的实施例中,可以是5s、15s、20s或10s;所述硫源的
载气可选为高纯氮气或高纯氩气,所述载气的流量可选为10~200sccm,更可选为20~160sccm,最可选为60~120sccm。
[0046]
完成一次还原后,本发明可选采用高纯氮气或高纯氩气对反应腔体进行吹扫清洗,所述清洗的时间可选为5~50s,更可选为10~45s,最可选为15~40s。
[0047]
本发明可选重复上述气相sn源沉积-吹扫清洗-硫源沉积-吹扫清洗这一过程,重复循环的次数视实际需求而定,在本发明中,所述循环的次数可选为100~2500次,更可选为300~2000次,具体的,在本发明的实施例中,可以是100次、500次、1000次或2000次。
[0048]
以下对本发明的优选实施例进行说明,应当理解实施例是为了更好地解释本发明,不用于限制本发明。
[0049]
实施例1
[0050]
一种以sn(acac)2为sn源,以异丙基硫醇(i-pr-sh)为硫源的snsx薄膜原子层沉积方法,包括以下过程:
[0051]
(1)以ti为衬底,沉积温度为240℃,sn源sn(acac)2的加热温度为75℃,使之气化,以高纯氮气为载气,通入气相sn(acac)2,载气流量为20sccm;脉冲时间为12s,等待时间为10s;
[0052]
(2)完成一个脉冲后使用高纯氮气进行清洗,清洗时间为25s;
[0053]
(3)硫源i-pr-sh加热温度为60℃,使之气化,以高纯氮气为载气,载气流量为60sccm,以脉冲形式通入i-pr-sh,脉冲时间为5s,等待时间为20s;
[0054]
(4)完成一个脉冲后采用高纯氮气进行清洗,清洗时间为15s;
[0055]
将上述(1)~(4)步骤重复循环100次,所得sns
x
薄膜厚度为41nm,速率为0.41nm/循环,速率较高。
[0056]
图1和图2分别为实施例1制备的sns
x
薄膜的平面和截面sem图;从图1和图2中可以直观地看出所得sns
x
薄膜制备成功,且所制备薄膜涂层保形性好,连续均匀,无裂纹,进一步推断对应工艺可以用于以复杂3d结构为衬底的ald纳米材料制备之中。
[0057]
实施例2:不同硫源制备snsx薄膜
[0058]
将实施例1中的硫源分别替换成正丁基硫醇(n-bu-sh)、叔丁基硫醇(t-bu-sh)、正丙基硫醇(n-pr-sh),其他操作步骤和参数保持不变。
[0059]
结果显示,重复循环100次,所得snsx薄膜厚度分别为3.9nm、5.4nm、4.9nm。
[0060]
实施例3
[0061]
一种以sn(acac)2为sn源,以正丁基硫醇(n-bu-sh)为硫源的sns
x
薄膜原子层沉积方法,包括以下过程:
[0062]
(1)以氧化硅为衬底,沉积温度为265℃,sn源sn(acac)2的加热温度为120℃,使之气化,以高纯氩气为载气,通入气相sn(acac)2,载气流量为80sccm;脉冲时间为6s,等待时间为20s;
[0063]
(2)完成一个脉冲后使用高纯氩气进行清洗,清洗时间为45s;
[0064]
(3)硫源n-bu-sh加热温度为40℃,以高纯氩气为载气,载气流量为20sccm,以脉冲形式通入n-bu-sh,脉冲时间为15s,等待时间为15s;
[0065]
(4)完成一个脉冲后采用高纯氩气进行清洗,清洗时间为35s;
[0066]
将上述(1)~(4)步骤重复循环500次,所得sns
x
薄膜厚度为19.1nm。
[0067]
实施例4
[0068]
一种以sn(acac)2为sn源,以异丙基硫醇(t-bu-sh)为硫源的sns
x
薄膜原子层沉积方法,包括以下过程:
[0069]
(1)以氧化钛为衬底,沉积温度为315℃,sn源sn(acac)2的加热温度为150℃,使之气化,以高纯氩气为载气,通入气相sn(acac)2,载气流量为120sccm。脉冲时间为8s,等待时间为5s;
[0070]
(2)完成一个脉冲后使用高纯氩气进行清洗,清洗时间为15s;
[0071]
(3)硫源t-bu-sh加热温度为80℃,使之气化,以高纯氩气为载气,载气流量为160sccm,以脉冲形式通入t-bu-sh,脉冲时间为20s,等待时间为10s;
[0072]
(4)完成一个脉冲后采用高纯氩气进行清洗,清洗时间为5s;
[0073]
将上述(1)~(4)步骤重复循环1000次,所得snsx薄膜厚度为43nm。
[0074]
实施例5
[0075]
一种以sn(acac)2为sn源,以正丙基硫醇(n-pr-sh)为硫源的snsx薄膜原子层沉积方法,包括以下过程:
[0076]
(1)以玻璃为衬底,沉积温度为200℃,sn源sn(acac)2的加热温度为180℃,使之气化,以高纯氮气为载气,通入气相sn(acac)2,载气流量为150sccm,脉冲时间为2s,等待时间为15s;
[0077]
(2)完成一个脉冲后使用高纯氮气进行清洗,清洗时间为35s;
[0078]
(3)硫源n-pr-sh加热温度为25℃,使之气化,以高纯氮气为载气,载气流量为90sccm,以脉冲形式通入n-pr-sh,脉冲时间为10s,等待时间为10s;
[0079]
(4)完成一个脉冲后采用高纯氮气进行清洗,清洗时间为15s;
[0080]
将上述(1)~(4)步骤重复循环2000次,所得snsx薄膜厚度为91nm。
[0081]
需要说明的是,在本文中,而且,术语“包括”、“包含”或者其任何其他变体意在涵盖非排他性的包含,从而使得包括一系列要素的过程、方法、物品或者设备不仅包括那些要素,而且还包括没有明确列出的其他要素,或者是还包括为这种过程、方法、物品或者设备所固有的要素。
[0082]
尽管已经示出和描述了本发明的实施例,对于本领域的普通技术人员而言,可以理解在不脱离本发明的原理和精神的情况下可以对这些实施例进行多种变化、修改、替换和变型,本发明的范围由所附权利要求及其等同物限定。
[0083]
对比例1:
[0084]
和实施例1相比,其他参数不变,改变所使用sn源为sn((ch3)2n)4。
[0085]
以sn((ch3)2n)4为sn源,以异丙基硫醇(i-pr-sh)为硫源的snsx薄膜原子层沉积方法,包括以下过程:
[0086]
(1)以ti为衬底,沉积温度为240℃,sn源sn((ch3)2n)4的加热温度为75℃,使之气化,以高纯氮气为载气,通入气相sn(acac)2,载气流量为20sccm;脉冲时间为12s,等待时间为10s;
[0087]
(2)完成一个脉冲后使用高纯氮气进行清洗,清洗时间为25s;
[0088]
(3)硫源i-pr-sh加热温度为60℃,使之气化,以高纯氮气为载气,载气流量为60sccm,以脉冲形式通入i-pr-sh,脉冲时间为5s,等待时间为20s;
[0089]
(4)完成一个脉冲后采用高纯氮气进行清洗,清洗时间为15s;
[0090]
将上述(1)~(4)步骤重复循环100次,所得snsx薄膜厚度为10.1nm。
[0091]
对比例1所制备薄膜材料的沉积速率为0.101nm/循环,且所沉积薄膜存在不连续现象。同实施例1所得结果对比可知,实施例1所制备的薄膜材料具有更高的生长速率、更光滑的表面以及更好的薄膜保型性。对比例1所得结果较差的原因在于所使用sn源sn((ch3)2n)4与所使用硫源之间的反应活性不匹配,导致对比例1所沉积薄膜材料不连续、表面粗糙以及生长速率低。
[0092]
对比例2
[0093]
和实施例1相比,其他参数不变,改变所使用硫源为叔丁基二硫。
[0094]
以sn(acac)2为sn源,以叔丁基二硫(
t
bu-s-s-t
bu)为硫源的snsx薄膜原子层沉积方法,包括以下过程:
[0095]
(1)以ti为衬底,沉积温度为240℃,sn源sn(acac)2的加热温度为75℃,使之气化,以高纯氮气为载气,通入气相sn(acac)2,载气流量为20sccm;脉冲时间为12s,等待时间为10s;
[0096]
(2)完成一个脉冲后使用高纯氮气进行清洗,清洗时间为25s;
[0097]
(3)硫源叔丁基二硫(
t
bu-s-s-t
bu)加热温度为60℃,使之气化,以高纯氮气为载气,载气流量为60sccm,以脉冲形式通入叔丁基二硫(
t
bu-s-s-t
bu),脉冲时间为5s,等待时间为20s;
[0098]
(4)完成一个脉冲后采用高纯氮气进行清洗,清洗时间为15s;
[0099]
将上述(1)~(4)步骤重复循环100次,无薄膜产生。
[0100]
实施例1所得结果要明显优于对比例2,这是因为实施例1所使用硫源中具有硫氢键的存在,具有更优良的反应活性,使得sn(acac)2和i-pr-sh的前驱体组合之间具有更合适匹配的反应活性,更利于沉积出性能优良的薄膜材料。而对比例2所使用的sn(acac)2和
t
bu-s-s-t
bu之间反应活性不匹配,导致无薄膜材料沉积。