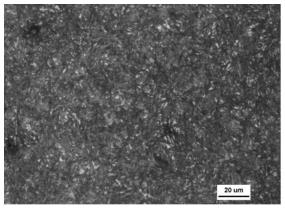
1.本发明属于齿轮钢技术领域,特别是提供了一种少残奥高硬度控制的齿轮钢及渗碳工艺;适用于汽车、轨道交通机车的齿轮箱用主、从动齿轮的生产及渗碳热处理,以及工程机械、风电齿轮等的生产及热处理,获得少残奥高表面硬度控制的齿轮工件。
背景技术:2.齿轮工件在常规渗碳后由于渗碳层碳含量偏高,在普通淬回火处理后其渗碳层残余奥氏体含量会比较高,达到20%左右或更高,而残余奥氏体是一种软相组织,导致渗碳层整体硬度偏低,无法满足齿轮高性能服役要求。
3.为了提高工件表面硬度,进行渗氮或碳氮共渗是一种可行的工艺。中国专利202210000400.7公开了一种拖拉机车桥用行星轴表面碳氮共渗处理方法,淬火后表面硬度可达59~63hrc。中国专利02157722.6公开了一种复合化学热处理工艺,将渗氮和渗碳结合,使工件表面层奥氏体的氮浓度提高到奥氏体渗氮层的水平,再进行直接淬火并在200~300℃范围内的时效处理或直接进行200~300℃温度区间中的等温淬火,可使工件硬度达到900hv以上。
4.但渗氮或碳氮共渗时,由于加入了氮的气氛使热处理受到一定限制,该处理必须在具备渗氮的装备中进行,而普通的渗碳炉不具备基本条件,很难完成处理。
5.本发明通过利用现有的渗碳炉设备,通过特定渗碳工艺设置以及后续热处理条件设置,可以获得渗碳后少残奥和高表面硬度的齿轮工件。
技术实现要素:6.本发明的目的是提供一种少残奥高硬度控制的齿轮钢及渗碳工艺,一种铌微合金化齿轮钢并经过成分控制保证渗碳后残余奥氏体分布及含量控制,另外,结合渗碳及热处理实现齿轮工件少残奥、高表面硬度控制。
7.本发明的少残奥高硬度控制的齿轮钢的成分为:c:0.16~0.22%,si:0.10~0.25%,mn:0.50~0.90%,cr:1.5~1.8%,ni:1.4~1.7%,mo:0.25~0.55%,nb:0.025~0.08%,al:0.02~0.035%,p:≤0.02%,s:≤0.02%,n:0.009~0.015%,cu:≤0.2%,余量为fe及不可避免的杂质;其中au=0.5c+mn+ni+30n+2cu,mu=cr+mo+si,且满足au在2.2~3.2%范围,mu在1.95~2.60%之间。
8.所述齿轮钢优选成分如下:c:0.19~0.22%,si:0.10~0.25%,mn:0.50~0.70%,cr:1.6~1.8%,ni:1.4~1.6%,mo:0.25~0.55%,nb:0.03~0.06%,al:0.02~0.035%,p:≤0.02%,s:≤0.02%,n:0.009~0.012%,cu:≤0.05%,余量为fe及不可避免的杂质,其中au=0.5c+mn+ni+30n+2cu,mu=cr+mo+si,且满足au在2.25~2.85%范围,mu在2.16~2.60%之间。
9.利用电炉或转炉+lf+vd/rh+连铸或模铸+轧制的工艺生产得到的齿轮钢棒材。
10.本发明钢中元素的主要作用如下:
11.c:作为钢中最基本合金元素,能够起到强化作用,为保证渗碳后工件心部硬度和韧性,c含量控制为0.16~0.22%。
12.si:作为脱氧剂,在钢铁冶炼中经常用到,同时si还是缩小奥氏体相区的元素,为保证脱氧效果及控制奥氏体相区,si不能低于0.10%,同时考虑到si对表面脱碳影响较大,si不能高于0.25%。
13.mn:能提高钢的淬透性,是保证心部硬度的重要元素,其不低于0.50%,另外,mn是扩大奥氏体相区的元素,为保证残余奥氏体控制,mn不高于0.90%。
14.cr:可以提高钢的淬透性及强度,是保证齿轮工件渗碳后心部硬度和韧性的重要元素,另外,cr具有缩小奥氏体相区的作用,其含量不低于1.5%,而过高的cr会影响钢的韧性,因此,cr不高于1.8%。
15.ni:能够提高渗碳后钢的心部韧性,具有扩大奥氏体相区的作用,综合考虑,ni含量控制为1.4~1.7%。
16.mo:是强碳化物形成元素,具有提高强韧性的作用,同时mo还可以起到细化组织和晶粒的作用,mo控制不低于0.25%,而过高的mo所起的作用有限,同时成本会明显增加,因此mo含量控制为0.25~0.55%。
17.nb:是强碳化物形成元素,可以与碳结合形成nbc析出相,起到细化晶粒和组织的作用,为了保证残余奥氏体分布及硬度控制,nb含量不少于0.025%,而过高的nb会在钢中形成偏析,生成大颗粒nbc夹杂物,对齿轮疲劳性能不利,因此,nb含量不高于0.08%。
18.al:是强脱氧元素,与氧结合形成氧化铝夹杂物,为保证脱氧效果及夹杂物控制,al含量控制为0.02~0.035%。
19.p:是杂质元素,会导致钢的脆性,因此p含量不高于0.02%。
20.s:在钢中会形成mns夹杂物,对冲击性能不利,钢中s应不高于0.02%。
21.n:可与钢中al形成aln,起到细化晶粒的作用,为保证晶粒控制效果,n含量不低于0.009%,而过高含量的n会导致其在晶界偏聚,从而导致钢的脆性加剧,同时n还具有扩大奥氏体相区的作用,因此n含量不应高于0.015%。
22.cu:具有扩大奥氏体相区的作用,为降低渗碳后残余奥氏体和提高渗碳后表面硬度,cu含量不高于0.2%。
23.au和mu参数的控制,可以保证渗碳后残余奥氏体含量控制在较好水平,从而为最终少残奥的齿轮工件控制提供条件。
24.根据本发明钢成分范围,利用电炉或转炉+lf+vd/rh+连铸或模铸+轧制的工艺生产得到相应成分的齿轮钢棒材。
25.将齿轮钢棒材加工成齿轮工件,齿轮工件经清洗干燥后放置于真空渗碳炉中进行渗碳处理;渗碳时采用强渗+扩散+次强渗+再扩散的模式,
26.第1步强渗期温度910~950℃、碳势1.05~1.35%,
27.第2步扩散期温度910~930℃、碳势0.85~0.95%,
28.第3步次强渗期温度910~950℃、碳势1.00~1.15%,
29.第4步再扩散期温度880~910℃、碳势0.75~0.85%,强渗时间与次强渗时间比在2.0~4.5之间,扩散期与再扩散期时间比在0.2~1.0之间,且再扩散时间不低于90min;渗碳结束后进行油冷,冷速控制50~150℃/s,淬火前油初始温度25~40℃,油冷结束后,油温
应低于120℃,保证工件最终的冷却温度,油冷时间t依据工件厚度d按照如下公式进行设置,
[0030][0031]
其中:t为油冷时间,min;d为工件厚度,mm。
[0032]
渗碳结束后,齿轮工件表面碳含量在0.85%以下,表面以下0.3mm内金相组织为针状或板块状马氏体+残余奥氏体,残余奥氏体含量≤20%,渗碳层晶粒度≥8.0级,在组织和晶粒细化的同时,使残余奥氏体弥散分布在马氏体基体中,且实现小尺寸残奥控制,残余奥氏尺寸≤5μm,平均残余奥氏体尺寸在3μm以下。
[0033]
将油冷结束后的齿轮工件表面的油渍清洗干净,随后进行回火处理,回火温度180~220℃,回火时间在90~360min,回火结束后,将工件置于低温环境中进行低温冷却处理,温度-85℃~-140℃,低温处理时间50~180min,冷却结束后置于室温环境中,待温度达到室温时,再进行回火处理,回火温度170~220℃,回火时间90~360min。
[0034]
渗碳后的热处理保证了残余奥氏体向马氏体的转变,使渗碳层残余奥氏体尺寸减小,含量降低到3~14%之间,从而提升齿轮工件表面硬度达到760hv以上,并保证硬度均匀稳定。
附图说明
[0035]
图1为通过本发明获得的工件渗层金相组织结果图。
[0036]
图2为实施例和对比例残奥含量和表面硬度对比结果图。
具体实施方式
[0037]
下面通过具体实施例,对本发明的具体实施方法进行进一步的说明。
[0038]
实施例1:
[0039]
利用电炉+lf+vd+连铸+轧制的工艺生产获得如下化学成分的齿轮钢棒材:c:0.20%,si:0.16%,mn:0.65%,cr:1.75%,ni:1.51%,mo:0.29%,nb:0.036%,al:0.024%,p:0.009%,s:0.005%,n:0.011%,cu:0.02%,au=2.63%,mu=2.2%。
[0040]
取齿轮钢棒材,加工成齿轮工件,齿轮工件截面厚度d=150mm,齿轮工件经清洗干燥后放置于真空渗碳炉中进行渗碳处理;渗碳时采用强渗+扩散+次强渗+再扩散的模式,其中第1步强渗期温度930℃、碳势1.25%,第2步扩散期温度915℃、碳势0.90%,第3步次强渗期温度930℃、碳势1.05%,第4步再扩散期温度890℃、碳势0.80%,强渗时间与次强渗时间比为2.5,扩散期与再扩散期时间比为0.5,且再扩散时间120min;渗碳结束后进行油冷,淬火前油初始温度35℃,油冷结束后,油温低于120℃,油冷时间t=45min。
[0041]
渗碳结束后,表面碳含量为0.78%,表面以下0.3mm内金相组织为针状马氏体+残余奥氏体,残余奥氏体含量17%,晶粒度9.5级。
[0042]
将油冷结束后的齿轮工件表面的油渍清洗干净,随后进行回火处理,回火温度200℃,回火时间120min,回火结束后,将工件置于低温环境中进行低温冷却处理,温度-130℃,低温处理时间85min,冷却结束后置于室温环境中,待温度达到室温时,再进行回火处理,回
火温度175℃,回火时间120min。
[0043]
最后取样测试,渗碳层残余奥氏体含量为9%,表面硬度782~795hv。
[0044]
实施例2:
[0045]
利用电炉+lf+vd+模铸+轧制的工艺生产获得如下化学成分的齿轮钢棒材:c:0.18%,si:0.21%,mn:0.72%,cr:1.66%,ni:1.60%,mo:0.36%,nb:0.042%,al:0.031%,p:0.005%,s:0.003%,n:0.010%,cu:0.06%,au=2.83%,mu=2.23%。
[0046]
取齿轮钢棒材,加工成齿轮工件,齿轮工件截面厚度d=360mm,齿轮工件经清洗干燥后放置于真空渗碳炉中进行渗碳处理;渗碳时采用强渗+扩散+次强渗+再扩散的模式,其中第1步强渗期温度940℃、碳势1.20%,第2步扩散期温度915℃、碳势0.90%,第3步次强渗期温度940℃、碳势1.10%,第4步再扩散期温度900℃、碳势0.78%,强渗时间与次强渗时间比为2.0,扩散期与再扩散期时间比为0.5,且再扩散时间120min;渗碳结束后进行油冷,淬火前油初始温度25℃,油冷结束后,油温低于120℃,油冷时间t=60min。
[0047]
渗碳结束后,表面碳含量为0.76%,表面以下0.3mm内金相组织为针状马氏体+残余奥氏体,残余奥氏体含量15%,晶粒度10.5级。
[0048]
将油冷结束后的齿轮工件表面的油渍清洗干净,随后进行回火处理,回火温度200℃,回火时间120min,回火结束后,将工件置于低温环境中进行低温冷却处理,温度-96℃,低温处理时间125min,冷却结束后置于室温环境中,待温度达到室温时,再进行回火处理,回火温度200℃,回火时间120min。
[0049]
最后取样测试,渗碳层残余奥氏体含量为7%,表面硬度788~802hv。
[0050]
对比例:
[0051]
利用电炉+lf+vd+连铸+轧制的工艺生产获得如下化学成分的齿轮钢棒材:c:0.19%,si:0.10%,mn:0.78%,cr:1.56%,ni:1.65%,mo:0.27%,al:0.028%,p:0.006%,s:0.003%,n:0.013%,cu:0.12%,au=3.16%,mu=1.93%。
[0052]
取齿轮钢棒材,加工成齿轮工件,齿轮工件截面厚度d=150mm,齿轮工件经清洗干燥后放置于真空渗碳炉中进行渗碳处理;渗碳时采用强渗+扩散的模式,其中第1步强渗期温度930℃、碳势1.25%,第2步扩散期温度900℃、碳势0.90%,扩散时间120min;渗碳结束后进行油冷,淬火前油初始温度55~60℃,油冷结束后,油温低于120℃,油冷时间t=25min。
[0053]
渗碳结束后,表面碳含量为0.92%,表面以下0.3mm内金相组织为板条马氏体+残余奥氏体,残余奥氏体含量26%,晶粒度7.0级。
[0054]
将油冷结束后的齿轮工件表面的油渍清洗干净,随后进行回火处理,回火温度200℃,回火时间120min。
[0055]
最后取样测试,渗碳层残余奥氏体含量为23%,表面硬度693~721hv。