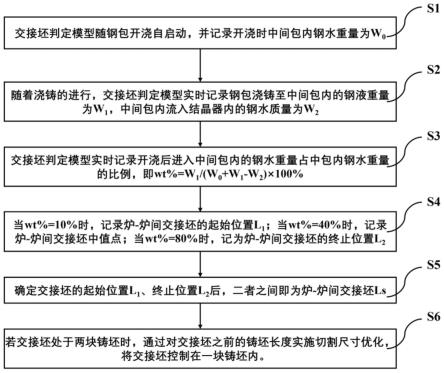
1.本发明涉及一种减少汽车板针眼缺陷发生率的方法,属于钢铁冶金连铸方法技术领域。
背景技术:2.汽车板钢对钢中非金属夹杂物要求非常严格。近年来,随着车企出于减重降本节能的需求,逐步减薄汽车板厚度。这使得能够导致汽车板针眼缺陷的夹杂物尺寸也相应减小,这显著加大了钢企生产汽车板钢时对夹杂物的控制难度。通过研究表明,多炉次连浇形成的炉-炉间交接坯(亦称之为过渡坯)在车企冲压加工时较多发生冲压开裂,主要原因在上炉次钢包结束浇铸后,下炉次钢包长水口下降浸入中间包内的钢液时,长水口会将钢液表面的中间包覆盖剂部分罩入其管内。在该炉次钢包开浇后,被钢水流股击碎成微小覆盖剂渣滴,由于尺寸较小而难以由钢液内部上浮至表面去除,因此会作为非金属夹杂物残留于钢液中。虽然此类夹杂物尺寸较小,但足以在厚度大幅减薄的汽车钢板经受大变形量冲压时导致“针眼”状微小开裂发生。
3.为了减少汽车板针眼缺陷发生率,钢铁厂只能采用将炉-炉间交接坯采取人为降级或改判的处理策略,而对于交接坯的判定,简单地即将上炉次最后一块铸坯和下炉次第一块铸坯降级,仅交接坯造成的降级品率就高达近40%。由于汽车板减薄是今后发展趋势,预计会有更多汽车板材部件厚度减薄至0.65mm,甚至更薄,因此在现有生产技术下,对其均必须采取交接坯降级策略。如不能减少交接坯降级量,将会极大提升钢铁厂汽车板钢的生产成本。
技术实现要素:4.本发明目的是提供一种减少汽车板针眼缺陷发生率的方法,通过精确识别板坯连铸炉炉间交接坯长度,并采用铸坯切割优化的方法,将铸坯的交接坯进行降级处理,成功地解决了由交接坯降级品量大而导致的生产成本增加的技术问题,同时有效地减少汽车板“针眼”缺陷的发生率,有效地解决了背景技术中存在的上述问题。
5.本发明的技术方案是:一种减少汽车板针眼缺陷发生率的方法,包含以下步骤:
6.步骤s1,钢包到达开浇位置后,交接坯判定模型随钢包开浇自动启动,并记录开浇时中间包内钢水重量为w0;
7.步骤s2,随着浇铸的进行,交接坯判定模型实时记录钢包浇铸至中间包内的钢液重量为w1,中间包内流入结晶器内的钢水重量为w2;
8.步骤s3,交接坯判定模型实时记录开浇后进入中间包内的钢水重量占中包内钢水重量的比例,即wt%=w1/(w0+w
1-w2)
×
100%;
9.步骤s4,经过对铸坯轧制情况的长期跟踪,确定当wt%=10%时,记录为炉-炉间交接坯的起始位置l1,显示在主控界面和铸坯切割界面;当wt%=40%时,记为炉-炉间交接坯的中值点,显示在主控界面及铸坯切割界面;当wt%=80%时,记为炉-炉间交接坯的
终止位置l2,显示在主控界面和铸坯切割界面;
10.步骤s5,确定交接坯的起始位置l1和终止位置l2后,l1与l2之间的铸坯即为炉炉间交接坯ls;
11.步骤s6,在炉炉间交接坯判定以后,显示在连铸切割车间的主界面,若交接坯只在一块铸坯内,则不需要进行尺寸优化;若交接坯处于两块铸坯时,通过增加和减少非交接坯的铸坯长度,将交接坯控制在一块铸坯内。
12.所述步骤s5中,由交接坯判定系统计算得到交接坯的起始时刻t1和终止时刻t2分别为:
[0013][0014][0015]
其中,a和b分别表示结晶器宽度为a,厚度为b,单位为m;v为铸坯拉速,单位为m/min;ρ为钢液密度,单位为kg/m3;w0为钢包开浇时,中间包内钢液的重量,单位为kg;q为钢包长水口流入中间包的通钢量,单位为kg/min。
[0016]
所述交接坯的长度为:
[0017]
ls=v(t
2-t1)
ꢀꢀꢀꢀ
(3)
[0018]
其中,ls为交接坯长度,单位为m;v为铸坯拉速,单位为m/min;t1、t2分别为交接坯判定的起止时刻。
[0019]
所述步骤s6中,交接坯距离火焰切割点45m,为五块铸坯的长度。
[0020]
所述步骤s6中,交接坯处于两块铸坯时,即位于前一炉第一块和后一炉最后一块。
[0021]
本发明的有益效果是:通过精确识别板坯连铸炉炉间交接坯长度,并采用铸坯切割优化的方法,将铸坯的交接坯进行降级处理,成功地解决了由交接坯降级品量大而导致的生产成本增加的技术问题,同时有效地减少汽车板“针眼”缺陷的发生率。
附图说明
[0022]
图1为本发明的结构示意图;
[0023]
图2为本发明的流程图;
[0024]
图3为本发明实施例一未优化连铸实际炉-炉交接坯显示在切割车间主控界面的图形;
[0025]
图4为本发明实施例一优化后连铸实际炉-炉交接坯显示在切割车间主控界面的图形;
[0026]
图5为本发明实施例二未优化连铸实际炉-炉交接坯显示在切割车间主控界面的图形;
[0027]
图6为本发明实施例二优化后连铸实际炉-炉交接坯显示在切割车间主控界面的图形;
[0028]
图7为本发明汽车板钢的针眼缺陷发生率改善效果图;
[0029]
图8为本发明交接坯导致降级品率改善效果图;
[0030]
图中:钢液1、中间包2、结晶器3、交接坯4、l1起始位置5、l2终止位置6、中值点7、拉
坯方向8。
具体实施方式
[0031]
为了使发明实施案例的目的、技术方案和优点更加清楚,下面将结合实施案例中的附图,对本发明实施案例中的技术方案进行清晰的、完整的描述,显然,所表述的实施案例是本发明一小部分实施案例,而不是全部的实施案例,基于本发明中的实施案例,本领域普通技术人员在没有做出创造性劳动前提下所获得的所有其他实施案例,都属于本发明保护范围。
[0032]
一种减少汽车板针眼缺陷发生率的方法,包含以下步骤:
[0033]
步骤s1,钢包到达开浇位置后,交接坯判定模型随钢包开浇自动启动,并记录开浇时中间包内钢水重量为w0;
[0034]
步骤s2,随着浇铸的进行,交接坯判定模型实时记录钢包浇铸至中间包内的钢液重量为w1,中间包内流入结晶器内的钢水重量为w2;
[0035]
步骤s3,交接坯判定模型实时记录开浇后进入中间包内的钢水重量占中包内钢水重量的比例,即wt%=w1/(w0+w
1-w2)
×
100%;
[0036]
步骤s4,经过对铸坯轧制情况的长期跟踪,确定当wt%=10%时,记录为炉-炉间交接坯的起始位置l1,显示在主控界面和铸坯切割界面;当wt%=40%时,记为炉-炉间交接坯的中值点,显示在主控界面及铸坯切割界面;当wt%=80%时,记为炉-炉间交接坯的终止位置l2,显示在主控界面和铸坯切割界面;
[0037]
步骤s5,确定交接坯的起始位置l1和终止位置l2后,l1与l2之间的铸坯即为炉炉间交接坯ls;
[0038]
步骤s6,在炉炉间交接坯判定以后,显示在连铸切割车间的主界面,若交接坯只在一块铸坯内,则不需要进行尺寸优化;若交接坯处于两块铸坯时,通过增加和减少非交接坯的铸坯长度,将交接坯控制在一块铸坯内。
[0039]
所述步骤s5中,由交接坯判定系统计算得到交接坯的起始时刻t1和终止时刻t2分别为:
[0040][0041][0042]
其中,a和b分别表示结晶器宽度为a,厚度为b,单位为m;v为铸坯拉速,单位为m/min;ρ为钢液密度,单位为kg/m3;w0为钢包开浇时,中间包内钢液的重量,单位为kg;q为钢包长水口流入中间包的通钢量,单位为kg/min。
[0043]
所述交接坯的长度为:
[0044]
ls=v(t
2-t1)
ꢀꢀꢀꢀ
(3)
[0045]
其中,ls为交接坯长度,单位为m;v为铸坯拉速,单位为m/min;t1、t2分别为交接坯判定的起止时刻。
[0046]
所述步骤s6中,交接坯距离火焰切割点45m,为五块铸坯的长度。
[0047]
所述步骤s6中,交接坯处于两块铸坯时,即位于前一炉第一块和后一炉最后一块。
[0048]
在实际应用中,当钢包到达浇铸位置后,滑板打开,此时交接坯判定系统随开浇自启动,同时记录此时中间包的重量w0。随着浇铸的进行,交接坯判定模型实时记录钢包浇铸至中间包内的钢液重量为w1,中间包内流入结晶器内的钢水质量为w2。交接坯判定模型实时记录开浇后进入中间包内的钢水重量占中包内钢水重量的比例,即wt%=w1/(w0+w
1-w2)
×
100%。当wt%=10%时,认为后一炉钢水到达中间包出口,记录为炉-炉间交接坯的起始位置l1。当wt%=40%时,认为中间包出口处前一炉钢水和后一炉钢水的质量分数各占50%,记为炉-炉间交接坯的中值点。当wt%=80%时,认为中间包出口处几乎都为后一炉钢水,记为炉-炉间交接坯的终止位置l2。
[0049]
由交接坯判定系统可以计算得到交接坯的起始时刻t1和终止时刻t2分别为:
[0050][0051][0052]
其中,a和b分别表示结晶器宽度为a,厚度为b,单位为m;v为铸坯拉速,单位为m/min;ρ为钢液密度,单位为kg/m3;w0为钢包开浇时,中间包内钢液的重量,单位为kg;q为钢包长水口流入中间包的通钢量,单位为kg/min。
[0053]
计算出交接坯的起止时刻后,就可以计算出交接坯的长度为:
[0054]
ls=v(t
2-t1)
ꢀꢀꢀꢀ
(3)
[0055]
其中,ls为交接坯长度,单位为m;v为铸坯拉速,单位为m/min;t1、t2分别为交接坯判定的起止时刻。
[0056]
交接坯判定系统计算出交接坯的长度后,交接坯的位置就会显示在铸坯切割的控制系统内。
[0057]
实施例一:
[0058]
在本实施例中,结晶器的宽度为1.5m,厚度为0.237m,拉速为1.3m/min,钢液密度为7200kg/m3,钢包开浇时中间包内钢液的重量为55t,钢包长水口流入中间包的通钢量为6.7t/min。通过计算可知:交接坯的起始时刻为开浇后的0.8min,终止时刻为开浇后的6.6min,通过式(3)可以计算出,本实施例中,交接坯长度为7.52m。
[0059]
在本实施例中,交接坯判定系统可以通过记录交接坯的起止时刻,将交接坯的整个位置信息及长度记录在铸坯切割的操作平台上,如图3,交接坯位于前一炉最后一块铸坯和后一炉第一块铸坯内,且交接坯的起始位置距离铸坯的切口位置为1.02m,为了将交接坯放置于一块铸坯内,就需要优化前面几块铸坯的长度。
[0060]
在本实施例中,按照规定,铸坯的尺寸处于7.82-10.58m即满足产品要求。为了将交接坯放置于一块铸坯内,只需将1号铸坯的长度优化调整至8.5m,其他几块铸坯长度不变,即可将交接坯优化至后一炉的第一块铸坯内,如图4。因此,只需降级一块铸坯,提高了汽车板钢的降级品率。
[0061]
实施例二:
[0062]
在本实施例与实施例一基本相同,特别之处在于:
[0063]
结晶器的宽度为1.8m,厚度为0.237m,拉速为1.1m/min,钢液密度为7200kg/m3,钢包开浇时中间包内钢液的重量为53t,钢包长水口流入中间包的通钢量为6.8t/min。通过计
算可知:交接坯的起始时刻为开浇后的0.78min,终止时刻为开浇后的6.26min,通过式(3)可以计算出,本实施例中,交接坯长度为6.04m。
[0064]
在本实施例中,交接坯判定系统可以通过记录交接坯的起止时刻,将交接坯的整个位置信息及长度记录在铸坯切割的操作平台上,如图5,交接坯位于前一炉最后一块铸坯和后一炉第一块铸坯内,且交接坯的起始位置距离铸坯的切口位置为3.02m,为了将交接坯放置于一块铸坯内,就需要优化前面几块铸坯的长度。
[0065]
在本实施例中,按照规定,铸坯的尺寸处于7.82-10.58m即满足产品要求。为了将交接坯放置于一块铸坯内,只需将1号铸坯的长度优化调整至8.5m,其他几块铸坯长度不变,即可将交接坯优化至后一炉的第一块铸坯内,如图6。
[0066]
通过采用本发明提供的方法,汽车板钢的针眼缺陷发生率和铸坯降级量都明显减少。经过数据统计175个浇次,采用本发明提供的方法与未采用本发明提供的方法,针眼缺陷发生率与铸坯降级量的对比情况分别如图7和图8所示。
[0067]
上面对本发明实施例结合附图进行了说明,但本发明不限于上述实施例,还可以根据本发明的发明创造的目的做出多种变化,凡依据本发明技术方案的精神实质和原理下做的改变、修饰、替代、组合或简化,均应为等效的置换方式,只要符合本发明的发明目的,只要不背离本发明的技术原理和发明构思,都属于本发明的保护范围。