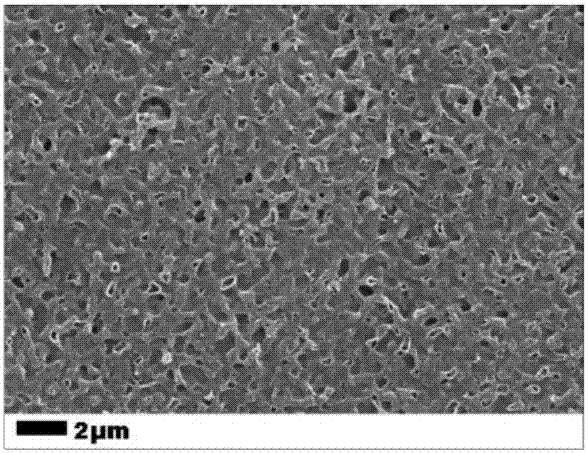
本发明涉及一种用人造石废弃物制备多孔陶瓷的方法,属于建筑材料技术和废弃物利用
技术领域:
。
背景技术:
:人造石,顾名思义就是通过人工的方法,将无机矿物材料及部分辅料加有机粘合剂混合后进行搅拌、定型、干燥、切割、抛光等加工而成的具有一定强度、花色的人工石材,将人工石材按照客户的需要再加工成用于厨房台面、卫生间台面,甚至是墙面、地面的材料。它是一种由天然矿石粉,高性能树脂和天然颜料经过真空浇铸或模压成型的矿物填充高分子复合材料(简称实体面材或实心板材,俗称人造石),主要分为聚酯板类、复合亚克力类、美玉石类和石英石类几种,按照组成主要分为钙铝板和石英石板。相较于传统的木质台面、天然大理石台面等其他材质的台面,应用范围更加广泛。由于人造石材的可塑性强、花色丰富且色差小等特点,现广泛用于家装、楼堂馆所、公共建筑的装饰装修中。人造石废弃物是生产人造石时产生的废弃物,其成分含有30%左右的树脂,一般树脂含有苯等化合物,而且这些有机物在自然环境中降解非常缓慢;废弃物中还含有一些碱性的无机添加物,重金属盐类等,这些化合物都会对环境产生严重的污染而且堆积占用了大量的土地。人造石加工的过程中需要湿磨和抛光,因此废弃物中含有大量的水分。由于废弃物中大量树脂和水分的存在,而且树脂燃烧产生的气体严重污染大气,因此对其无污染煅烧处理难以实现。人造石含水率高(一般在40%以上),但其表观含水少,难挥发,烘干困难是制约其工业化应用的根本原因,且其完全烘干后易出现颗粒团聚导致无法均匀分散,同时在烘干的过程中(70℃)树脂开始挥发出刺激性的气味,因此一般企业只能是不作处理任意排放、填埋。目前人造石废弃物已经成为环境的一大威胁,小规模企业众多,产品质量良莠不齐;生产率和产品合格率较低,据不完全统计全国生产人造石板的企业一年所产生的废料是2000多万吨,由于废弃物中大量树脂和水分的存在,且树脂燃烧产生的气体严重污染大气,降解缓慢,因此对其无污染处理难以实现。多孔陶瓷是一种新型的陶瓷材料,自19世纪70年代作为细菌过滤体被实用化以来,由于它具有均匀透过性,较大的比表面积,低密度以及耐高温、抗腐蚀、耐热冲击、机械强度高、原料来源广泛,使用寿命长等优良特性而越来越受到人们的重视,己被广泛应用于化工,能源、环保、冶金、电子及生物等各个部门,作为过滤、分离、布气、吸音、催化剂载体及生物陶瓷等材料,引起了材料学界的高度关注,成为一个非常活跃的研究领域。随着大量研究成果的取得,多孔陶瓷的应用范围仍在不断地进一步发展。多孔陶瓷是一种经高温烧成,材料中含有大量彼此相通并与材料表面相贯通的多孔结构的陶瓷材料,多孔陶瓷由于其特殊的材质及结构,具有以下一些共同特性:化学稳定性好;热学稳定性能好;几何表面积与体积比高;多孔陶瓷制品的孔道尺寸分布范围较宽。用人造石固体废弃物研究开发一种生产成本低,兼具轻质、保温、隔热功能的环保型多孔陶瓷,实现资源化综合利用,既可以解决环境污染问题,又使资源得到了有效利用,符合我国环境可持续发展战略实施的要求,具有广阔的应用前景。技术实现要素:本发明针对现有人造石板行业存在的废料浪费、污染环境以及多孔陶瓷应用广泛但生产成本高的问题,提供了一种用人造石废弃物制备多孔陶瓷的方法,达到节能减排,废物利用的目的。为了实现上述目的,本发明采用以下技术方案:一种用人造石废弃物制备的多孔陶瓷,由按重量份比60-80份人造石废弃物、20-40份飞灰、5-10份碳酸氢钠、0.01-0.03份外加剂和40-50份水混合,加入1-5份发泡剂发泡,烘干,在不高于800℃条件下低温烧结而成;外加剂其质量百分比组成为:5%-10%烷基醇酰胺、40%-50%聚羧酸减水剂、10%-15%的焦磷酸钠和25%-35%的聚丙烯酸钠。一种用人造石废弃物制备多孔陶瓷的方法:按重量份比将60-80份人造石废弃物、20-40份飞灰、5-10份碳酸氢钠、0.01-0.03份外加剂和适量水混合均匀制成固含量浓度为30%-40%的料浆,将料浆加入发泡剂1-5份发泡,烘干,在不高于800℃条件下低温烧结;所述的外加剂由烷基醇酰胺、聚羧酸减水剂、焦磷酸钠和聚丙烯酸钠组成。上述的用人造石废弃物制备多孔陶瓷的方法,优选包括步骤如下:(1)将人造石废弃物过筛;(2)按重量份比60-80份人造石废弃物、20-40份飞灰、5-10份碳酸氢钠、0.01-0.03份外加剂和适量水混合均匀制成固含量浓度为30%-40%的料浆,加入发泡剂1-5份发泡;所述的外加剂其质量百分比组成为:5%-10%烷基醇酰胺、40%-50%聚羧酸减水剂、10%-15%的焦磷酸钠和25%-35%的聚丙烯酸钠;(3)烘干;(4)在不高于800℃条件下低温烧结6-10小时。上述方法中,所述的人造石废弃物是钙铝板废弃物,其重量百分比组成如下(干基):al2o32.48%-2.50%、cao39.05%-41.49%、mgo0.24%-0.30%、k2o0.08%-0.10%、na2o0.15%-0.17%、杂质余量;其中杂质为废弃物中含有的树脂和水分;废弃物粒度为10-100微米。所述的飞灰,其重量百分比组成如下(干基):al2o338.5%-40.3%、sio233.5%-35.9%、cao10.1%-12.3%、杂质余量;杂质为其它氧化物或水分;飞灰粒度为1-100微米。所述的过筛筛目大小为140-200目。所述的发泡为搅拌自然发泡,发泡好的混合料在温度20±2℃湿度大于等于50%的环境中养护8-10小时。使得混合料中水份的分布趋于均匀化,同时也带动了混合料内部粘接剂等物质在混合料内部的均匀化。上述方法中,外加剂的优选质量百分比组成为:8%烷基醇酰胺、45%聚羧酸减水剂、12%的焦磷酸钠和35%的聚丙烯酸钠。所述的发泡剂优选双氧水。所述的烘干优选在90±5℃的烘干设备中烘干3-5小时。为了保证多孔陶瓷孔结构和陶瓷莫来石相的形成,防止温度过高结构坍塌,采取低温长时间保温的烧结工艺,优选采用每分钟升温3℃,300℃保温30-40分钟,500℃保温60-80分钟,800℃保温3小时的烧结工艺。上述方法制得的多孔陶瓷材料。本发明的有益效果:(1)本发明原料中人造石废弃物中含有的大量树脂高温下分解都会产生大量的气体形成多孔的结构,废料中的al2o3、sio2和cao,形成陶瓷中需要的骨架莫来石相,双氧水发泡剂可以引入大量气孔,碳酸氢钠助熔剂的使用可以大幅降低多孔陶瓷的出现液相的温度,有利用低温烧成;(2)本发明外加剂的使用,可以有效的释放出人造石里面的吸附水转化成自由水,降低了外加水的用量,节约了成本;释放出的水所留下的空间,形成气孔;烷基醇酰胺在体系里面具有稳定和促进气泡的作用,聚羧酸减水剂和焦磷酸钠复合作用具有分散废弃物和释放吸附水的作用,聚丙烯酸钠作为体系稳定剂,防止沉淀;(3)本发明采用的烧结工艺可保证多孔陶瓷孔结构和陶瓷莫来石相的形成,防止温度过高结构坍塌;(4)本发明方法实现了废弃物的利用,利用大量工业垃圾,降低环境负荷和多孔陶瓷的制造成本;(5)本发明方法制得的多孔陶瓷具有较好的抗折强度,隔热性好、密度小、自重轻。附图说明图1为本发明方法制得的陶瓷xrd图谱;图2为本发明方法制得的陶瓷扫描电镜照片。具体实施方式下面结合实施例对本发明作进一步说明。本发明实施例使用的人造石废弃物是钙铝板废弃物,其重量百分比组成如下(干基):al2o32.48%-2.50%、cao39.05%-41.49%、mgo0.24%-0.30%、k2o0.08%-0.10%、na2o0.15%-0.17%、杂质余量;其中杂质为废弃物中含有的树脂和水分;废弃物粒度为10-100微米。飞灰,其重量百分比组成如下(干基):al2o338.5%-40.3%、sio233.5%-35.9%、cao10.1%-12.3%、杂质余量;杂质为其它氧化物或水分;飞灰粒度为1-100微米。实施例1(1)将人造石废弃物取出,过200目的筛子;(2)配料:按重量份将60份人造石废弃物、40份飞灰、7份碳酸氢钠、0.03份外加剂和45份水混合均匀,制成浓度为30%-40%的料浆;外加剂质量百分比组成为:8%烷基醇酰胺、45%聚羧酸减水剂、12%的焦磷酸钠和35%的聚丙烯酸钠。将上述浆料加入4份发泡剂,自然发泡,发泡好的混合料在温度20℃、湿度50%的环境中放置10小时,使得混合料中水份的分布趋于均匀化,同时也带动了混合料内部粘接剂等物质在混合料内部的均匀化;(3)烘干:将发泡好的样品放在90℃左右的烘干设备中烘干4小时;(4)烧结:为了保证多孔陶瓷孔结构和陶瓷莫来石相的形成,防止温度过高结构坍塌,采取低温长时间保温的烧结工艺,即采用每分钟升温3℃,300℃保温30分钟,500℃保温80分钟,800℃保温3小时的烧结工艺。实施例2(1)将人造石废弃物取出,过200目的筛子;(2)配料:按重量份将70份人造石废弃物、30份飞灰、10份碳酸氢钠、0.02份外加剂和45份水混合均匀,制成浓度为30%-40%的料浆,外加剂质量百分比组成为:8%烷基醇酰胺、45%聚羧酸减水剂、12%的焦磷酸钠和35%的聚丙烯酸钠。将上述浆料加入3份发泡剂,自然发泡,发泡好的混合料在温度20℃、湿度50%的环境中放置10小时,使得混合料中水份的分布趋于均匀化,同时也带动了混合料内部粘接剂等物质在混合料内部的均匀化;(3)烘干:将发泡好的样品放在90℃左右的烘干设备中烘干4小时;(4)烧结:为了保证多孔陶瓷孔结构和陶瓷莫来石相的形成,防止温度过高结构坍塌,采取低温长时间保温的烧结工艺,即采用每分钟升温3℃,300℃保温40分钟,500℃保温60分钟,800℃保温3小时的烧结工艺。实施例3(1)将人造石废弃物取出,过200目的筛子;(2)配料:按重量份将80份人造石废弃物、20份飞灰、5份碳酸氢钠、0.01份外加剂和45份水混合均匀,制成浓度为30%-40%的料浆,外加剂质量百分比组成为:8%烷基醇酰胺、45%聚羧酸减水剂、12%的焦磷酸钠和35%的聚丙烯酸钠。将上述浆料加入2份发泡剂,自然发泡,发泡好的混合料在温度20℃、湿度50%的环境中放置10小时,使得混合料中水份的分布趋于均匀化,同时也带动了混合料内部粘接剂等物质在混合料内部的均匀化;(3)烘干:将发泡好的样品放在90℃左右的烘干设备中烘干4小时;(4)烧结:为了保证多孔陶瓷孔结构和陶瓷莫来石相的形成,防止温度过高结构坍塌,采取低温长时间保温的烧结工艺,即采用每分钟升温3℃,300℃保温35分钟,500℃保温80分钟,800℃保温3小时的烧结工艺。实施例4(1)将人造石废弃物取出,过200目的筛子;(2)配料:按重量份将70份人造石废弃物、30份飞灰、10份碳酸氢钠、0.02份外加剂和45份水混合均匀,制成浓度为30%-40%的料浆,外加剂质量百分比组成为:10%烷基醇酰胺、50%聚羧酸减水剂、10%的焦磷酸钠和30%的聚丙烯酸钠。将上述浆料加入3份发泡剂,自然发泡,发泡好的混合料在温度20℃、湿度50%的环境中放置10小时,使得混合料中水份的分布趋于均匀化,同时也带动了混合料内部粘接剂等物质在混合料内部的均匀化;(3)烘干:将发泡好的样品放在90℃左右的烘干设备中烘干4小时;(4)烧结:为了保证多孔陶瓷孔结构和陶瓷莫来石相的形成,防止温度过高结构坍塌,采取低温长时间保温的烧结工艺,即采用每分钟升温3℃,300℃保温40分钟,500℃保温60分钟,800℃保温3小时的烧结工艺。表1实验数据统计表实施例表观密度/g.cm-3吸水率/%抗折强度/mpa抗压强度/mpa10.9232.44.520.420.8438.74.822.530.9035.74.321.641.128.94.223.1在相同条件下测得各实施例产品的性能数据如表1。实施例2为优选的配比,图1为其所形成的莫来石陶瓷相,图2为其扫描电镜照片。以上是结合具体实施例对本发明的详细介绍,本发明的保护范围不限于此。当前第1页12