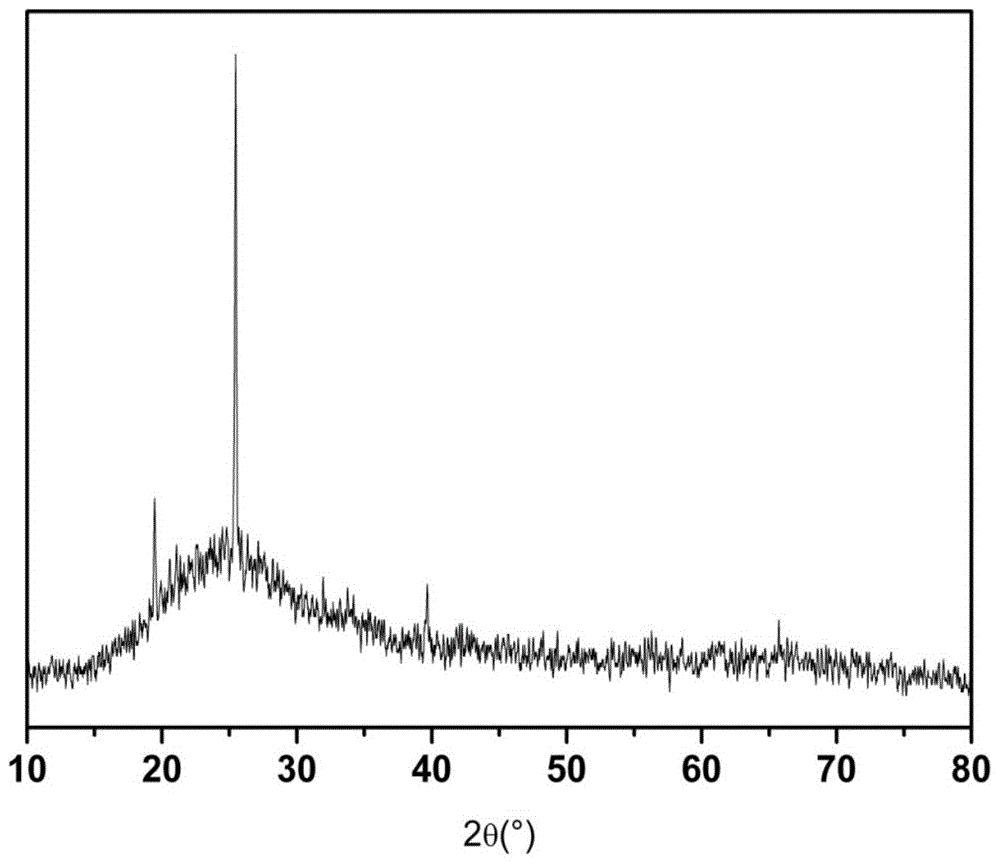
本发明涉及玻璃制备领域,具体涉及微晶玻璃及其生产方法和应用。
背景技术:
:微晶玻璃基于其中的晶粒能够造成裂纹尖端的弯曲和钝化,增加断裂能,从而减缓甚至阻止裂纹穿过晶相和可能的界面,提高玻璃抗冲击、抗跌落和耐划伤性等力学性能,可广泛应用于具有超薄、高透、超强等要求的移动终端显示设备屏幕保护领域。目前生产微晶玻璃的方法,一种是采用非连续生产方式,即通过高温熔融法将熔融玻璃液倒入模具浇注成玻璃锭,再将玻璃锭进行整体析晶处理,之后按照所需尺寸切割成玻璃薄片,最后还需对玻璃薄片进行双面磨削抛光处理。该方式各工艺步骤不连续,制成最终产品周期较长,且面临产能小、成本高等问题,难以满足市场需求。另一种是采用连续生产方式,即可以通过压延法、压制法、浮法等较为成熟的工艺制得,此种生产方式的优势是产能大,可实现规模量产。但是受工艺所限,目前通过压延或压制工艺均很难制得厚度1.5mm以下的电子级玻璃产品,无法直接用于智能移动终端。浮法工艺可以制得超薄微晶玻璃产品,但是其微晶化工艺主要是在锡槽内或退火窑内完成。锡槽内析晶对设备及每区温度场都有严格的要求,析晶过程难以精确控制,很难获得具备高透过率的微晶玻璃产品。退火窑内析晶所需产线较长,成本较高,且析晶在辊道上进行,容易发生翘曲等不良问题。cn104743884b公开了一种cao-mgo-al2o3-sio2系统微晶玻璃及其浮法生产工艺,提供了一种微晶玻璃的连续生产方式,具体地该工艺包括熔化、均化、玻璃摊平、抛光,随后进行拉薄或堆厚、冷却、进入热处理窑(在热处理窑中进行核化、晶化、退火处理),之后进行切割和抛光,但是该工艺仅限于生产3-18mm厚的建筑玻璃,并不适用于电子终端设备要求的超薄微晶玻璃。cn1896020a公开了一种可转变成玻璃陶瓷的浮法平板玻璃及其制备方法。该玻璃在浮浴过程中(即锡槽)完成核化和晶化,并通过控制温度调节玻璃的析晶,但是在锡槽内析晶对锡槽的结构要求较高,相应的设备需要进行改造,拉边机的材料也要相应的配套,特别是温度场的变化需要严格的要求,同时也要分区规划,才能完成在锡槽中的热处理过程。cn107857467a公开了一种建筑浮法微晶玻璃晶化方式及其晶化退火窑。在退火窑内进行晶化处理,同时对原有的退火窑进行了相应的改善,增加了相应的核化区和晶化区。但是退火、核化和晶化在同一窑内进行时,首先对窑的温度场控制条件要求较高,其次该窑采用的滚轴传动,在晶化的过程中由于温度较高可能迫使超薄玻璃变形产生翘曲不良等现象。因此,亟需一种微晶生产方法,在用于制备超薄微晶玻璃时能够克服上述问题,同时使得到的微晶玻璃具有透光率好、表面质量良好、不变形、外形完整度高等优点。技术实现要素:本发明的目的之一在于提供一种生产微晶玻璃的方法,由该方法制得的微晶玻璃具有透光率好、表面质量好、翘曲高度小、外形完整度高等优势。本发明的目的之二在于提供一种连续生产微晶玻璃的方法,该方法能够特别地用于简便地生产超薄微晶玻璃,使得到的超薄微晶玻璃不仅具有透光率好、表面质量好、翘曲高度小、外形完整度高等优势,而且翘曲高度特别小。为了实现上述目的,本发明第一方面提供一种生产微晶玻璃的方法,包括:将原玻璃体进行微晶化处理,所述微晶化处理包括:(1)升温:将原玻璃体从起始温度以升温速率vt1升温至核化温度;(2)核化:在核化温度下进行核化;(3)过渡期:从核化温度以升温速率vg升温至晶化温度;(4)晶化:在晶化温度下进行晶化;(5)降温:从晶化温度开始降温;其中,所述核化温度为550-640℃,所述晶化温度为640-750℃。优选地,所述原玻璃体的厚度t为0.3-1mm。优选地,所述原玻璃体的厚度t满足0.6mm≤t≤1mm,所述升温速率vt1满足vt1=n/(0.25t2)℃/min,其中n=3.5-4.5。优选地,所述原玻璃体的厚度t满足t<0.6mm,所述升温速率vt1为25-55℃/min。优选地,所述降温包括两个阶段,慢速降温阶段和快速降温阶段。优选地,所述原玻璃体的厚度t满足0.6mm≤t≤1mm,在慢速降温阶段的降温速率vm1满足vm1=m1/(0.25t2)℃/min,其中m1=2.5-3.5,在快速降温阶段的降温速率vm2满足vm2=m2/(0.25t2)℃/min,其中m2=5.5-6.5。优选地,所述原玻璃体的厚度t满足t<0.6mm,在慢速降温阶段的降温速率vm1为20-45℃/min,在快速降温阶段的降温速率vm2为50-80℃/min。优选地,所述快速降温阶段的最终温度小于100℃。优选地,核化温度为560-620℃,核化时间为2-7h,优选为4-6h。优选地,晶化温度为650-720℃,晶化时间为0.2-4h,优选为0.5-2h。优选地,所述过渡期的升温速率vg为10-20℃/min。优选地,所述微晶化处理在析晶装置中进行,所述析晶装置至少包括升温区、核化区、过渡区、晶化区和降温区。优选地,将所述原玻璃体引入析晶装置在载板上进行微晶化处理。优选地,所述载板的材料选自石墨、氧化铝陶瓷、石英、碳化硅、氮化铝和堇青莫来石(本领域中也常称为高棚板)中的至少一种,优选为石墨或碳化硅。优选地,所述载板的表面粗糙度ra小于0.2μm,优选为小于0.05μm,更优选为小于0.025μm。优选地,所述微晶化处理在保护气体气氛下进行。优选地,所述保护气体为纯氦气、纯氮气,或者氦气与氮气的混合物。优选地,所述保护气体的纯净度大于99.999体积%,所述保护气体气氛中o2、so2、co2的体积含量之和小于10ppm。优选地,所述原玻璃体包含:52-62重量%的sio2,12-25重量%的al2o3,5-15重量%的na2o,0-4重量%的k2o,2-5重量%的mgo,0.5-5重量%的zro2,3-7重量%的li2o,0-4.5重量%的tio2,0-2重量%的b2o3,以及0-2重量%的澄清剂。优选地,所述原玻璃体的工作点粘度范围为1.2×103-9.5×105dpa·s。优选地,所述方法还包括对微晶化处理后的原玻璃体进行3d加工和/或化学强化处理。本发明第二方面提供了一种连续生产微晶玻璃的方法,包括:(1)将玻璃组合物通过浮法工艺制备得到原玻璃体;(2)将所述原玻璃体按照本发明第一方面所述的方法进行处理。优选地,所述浮法工艺包括将所述玻璃组合物引入浮法玻璃熔窑,经熔化、澄清、均化、自然摊平、抛光、拉薄成型、退火、切裁制备得到原玻璃体。优选地,步骤(2)中的微晶化处理在析晶装置中进行。优选地,所述析晶装置设置在浮法工艺冷端出口处。优选地,所述析晶装置的承接区与浮法工艺冷端出口连接。本发明第三方面提供了本发明第一、第二方面所述的方法制得的微晶玻璃。优选地,所述微晶玻璃的表面粗糙度ra≤15nm。优选地,所述微晶玻璃的透光率失效值q≤0.02,优选地q≤0.015,且在波长为380-780nm范围内,透光率为88%以上。优选地,所述微晶玻璃的雾度小于0.5%。优选地,所述微晶玻璃的表面质量缺陷率与所述原玻璃体的表面质量缺陷率的比值m小于1.05,优选为m≤1.03。优选地,所述微晶玻璃的厚度为0.3-1mm。优选地,所述微晶玻璃的翘曲高度小于0.3mm,优选为小于0.25mm。本发明第四方面提供了一种微晶玻璃,其包含:52-62重量%的sio2,12-25重量%的al2o3,5-15重量%的na2o,0-4重量%的k2o,2-5重量%的mgo,0.5-5重量%的zro2,3-7重量%的li2o,0-4.5重量%的tio2,0-2重量%的b2o3,以及0-2重量%的澄清剂。优选地,所述微晶玻璃的表面粗糙度ra≤15nm。优选地,所述微晶玻璃的透光率失效值q≤0.02,优选地q≤0.015,且在波长为380-780nm范围内,透光率为88%以上。优选地,所述微晶玻璃的雾度小于0.5%。优选地,所述微晶玻璃的表面质量缺陷率与所述原玻璃体的表面质量缺陷率的比值m小于1.05,优选为m≤1.03。优选地,所述微晶玻璃的厚度为0.3-1mm。优选地,所述微晶玻璃的翘曲高度小于0.3mm,优选为小于0.25mm。优选地,所述微晶玻璃是按照本发明第一、第二方面所述的方法制得的。本发明第五方面提供了本发明第三方面、第四方面所述微晶玻璃在移动电子终端设备前后盖保护玻璃中的应用。本发明所述生产微晶玻璃的方法通过对微晶化处理的条件进行改进,实现原玻璃体(无论是现有产品还是上游工艺得到的中间体)的微晶化,使得到的微晶玻璃兼具透光率好(透光率失效值q≤0.02)、表面质量好(表面粗糙度ra≤10nm)、外形完整度高的优势;更特别地在用于制备超薄微晶玻璃时,使得到的超薄微晶玻璃不仅具有透光率好、表面质量好,而且具有翘曲影响小、外形完整度高等优势。在一种优选的实施方式中,得到的微晶玻璃厚度为0.3-1mm,透光率为88%以上,表面粗糙度ra≤15nm,翘曲高度小于0.25mm,雾度小于0.5%,所述微晶玻璃的表面质量缺陷率与所述原玻璃体的表面质量缺陷率的比值m小于1.05。附图说明图1是微晶玻璃b1的xrd测试图。具体实施方式在本文中所披露的范围的端点和任何值都不限于该精确的范围或值,这些范围或值应当理解为包含接近这些范围或值的值。对于数值范围来说,各个范围的端点值之间、各个范围的端点值和单独的点值之间,以及单独的点值之间可以彼此组合而得到一个或多个新的数值范围,这些数值范围应被视为在本文中具体公开。本发明第一方面提供一种生产微晶玻璃的方法,包括:将原玻璃体进行微晶化处理,所述微晶化处理包括:(1)升温:将原玻璃体从起始温度以升温速率vt1升温至核化温度;(2)核化:在核化温度下进行核化;(3)过渡期:从核化温度以升温速率vg升温至晶化温度;(4)晶化:在晶化温度下进行晶化;(5)降温:从晶化温度开始降温;其中,所述核化温度为550-640℃,所述晶化温度为640-750℃。在本文中,所述原玻璃体可以为现有的产品,也可以是通过上游工艺得到的中间体。原则地,本发明对原玻璃体的厚度不做限定,可以根据需要来调整。特别地,本发明所述方法能够用于超薄微晶玻璃的制备,得到透光率好、表面质量好、外形完整度高、翘曲高度特别小的超薄微晶玻璃。因此,为了得到超薄微晶玻璃,优选地,原玻璃体的厚度t为0.3-1mm。优选地,所述原玻璃体包含:52-62重量%的sio2,12-25重量%的al2o3,5-15重量%的na2o,0-4重量%的k2o,2-5重量%的mgo,0.5-5重量%的zro2,3-7重量%的li2o,0-4.5重量%的tio2,0-2重量%的b2o3,以及0-2重量%的澄清剂。进一步优选地,所述原玻璃体包含:52-60重量%的sio2,例如可以为52.5重量%、53重量%、56重量%、58重量%、59.5重量%以及上述数值中任意两个所组成范围中任意一值;14-25重量%的al2o3,例如可以为14.5重量%、14.8重量%、15重量%、20重量%、22重量%、24重量%、24.5重量%、24.8重量%以及上述数值中任意两个所组成范围中任意一值;7-14重量%的na2o,例如可以为7.5重量%、8重量%、12重量%、13重量%、13.5重量%以及上述数值中任意两个所组成范围中任意一值;0-4重量%的k2o,例如可以为0.2重量%、0.5重量%、1重量%、3重量%、3.5重量%、3.8重量%以及上述数值中任意两个所组成范围中任意一值;3-4.5重量%的mgo,例如可以为3.2重量%、3.5重量%、4重量%、4.2重量%以及上述数值中任意两个所组成范围中任意一值;0.5-4重量%的zro2,例如可以为0.6重量%、0.8重量%、1重量%、2重量%、3重量%、3.5重量%、3.8重量%以及上述数值中任意两个所组成范围中任意一值;4-7重量%的li2o,例如可以为4.2重量%、4.5重量%、5重量%、6重量%、6.5重量%、6.8重量%以及上述数值中任意两个所组成范围中任意一值;0-4.5重量%的tio2,例如可以为0.2重量%、0.5重量%、1重量%、2重量%、3重量%、4重量%、4.2重量%以及上述数值中任意两个所组成范围中任意一值;0-2重量%的b2o3,例如可以为0.2重量%、0.5重量%、1重量%、1.5重量%、1.8重量%以及上述数值中任意两个所组成范围中任意一值;以及0-1.5重量%的澄清剂,例如可以为0.1重量%、0.2重量%、0.8重量%、1.2重量%、1.4重量%1.48重量%以及上述数值中任意两个所组成范围中任意一值。在本发明中,所述澄清剂包括但不限于no3-、f-、cl-和so42-中的至少一种。优选地,所述原玻璃体的工作点粘度范围为1.2×103-9.5×105dpa·s。在本文中,粘度是按照sj/t11040-1996所述方法测得的。为了进一步减少微晶化处理对原玻璃体质量的影响,优选地,当所述原玻璃体的厚度t满足0.6mm≤t≤1mm时,所述升温速率vt1满足vt1=n/(0.25t2)℃/min,其中n=3.5-4.5(例如当t=1mm时,vt1=14-18℃/min,当t=0.8mm时,vt1=21.9-28.1℃/min),优选地,n=3.8-4.2,例如可以为3.85、3.9、4、4.1、4.15以及上述数值中任意两个所组成范围中的任意一值。当所述原玻璃体的厚度t满足t<0.6mm时,所述升温速率vt1为25-55℃/min。为了进一步提高成核效率并进一步获得理想的晶体尺寸,优选地,核化温度为560-620℃,核化时间为2-7h,优选为4-6h。优选地,所述过渡期的升温速率vg为10-20℃/min。为了进一步得到理想的晶体尺寸,优选地,晶化温度为650-720℃,晶化时间为0.2-4h,优选为0.5-2h。优选地,所述降温包括两个阶段,慢速降温阶段和快速降温阶段。在一种优选的实施方式中,所述降温的方式为先进行慢速降温阶段之后进行快速降温阶段。为了进一步减少玻璃降温过程的应力残留以及提高生产效率,优选地,当所述原玻璃体的t满足0.6mm≤t≤1mm时,在慢速降温阶段的降温速率vm1满足vm1=m1/(0.25t2)℃/min,其中m1=2.5-3.5(例如当t=1mm时,vt1=10-14℃/min;当t=0.8mm时,vt1=15.62-21.87℃/min),优选地m1=2.8-3.2,例如可以为2.85、2.9、3、3.1、3.15以及上述数值中任意两个所组成范围中的任意一值;在快速降温阶段的降温速率vm2满足vm2=m2/(0.25t2)℃/min,m2=5.5-6.5(例如当t=1mm时,vt1=22-26℃/min;当t=0.8mm时,vt1=34.37-40.62℃/min),优选地m2=5.8-6.2,例如可以为5.85、5.9、6、6.1、6.15以及上述数值中任意两个所组成范围中的任意一值。当所述原玻璃体的t满足t<0.6mm,在慢速降温阶段的降温速率vm1为20-45℃/min,在快速降温阶段的降温速率vm2为50-80℃/min。优选地,所述慢速降温阶段的最终温度为415-430℃。优选地,所述快速降温阶段的最终温度小于100℃,例如可以为25℃或者40℃。优选地,所述微晶化处理在析晶装置中进行,所述析晶装置至少包括升温区、核化区、过渡区、晶化区和降温区。优选地,所述析晶装置为析晶窑。在一种优选的实施方式中,所述析晶装置至少包括承接区、升温区、核化区、过渡区、晶化区、降温区和卸载区。在本文中,承接区用于接收原玻璃体以将其引入析晶装置进行微晶化处理。承接方式可以为本领域常用的技术手段,例如可以是使用机械手抓取放入析晶装置中的传输载板之上,也可以是采用过渡辊道进行转移。在本文中,升温区用于将所述原玻璃体从起始温度升至核化温度。所述起始温度可以为当时的环境温度,例如可以为-10℃至40℃。在本文中,卸载区用于将微晶玻璃进行铺纸堆垛、包装入库。卸载方式可以为本领域常用的技术手段,例如可以是机械手抓取方式。优选地,所述原玻璃体的微晶化处理在载板上进行。载板材料要求耐高温、表面光滑易加工,且高温下不与原玻璃体发生反应和粘结。优选地,所述载板的材料选自石墨、氧化铝陶瓷、石英、碳化硅、氮化铝和堇青莫来石(本领域也常称为高棚板)中的至少一种,优选为石墨或碳化硅。采用石墨作为载板材料,由于石墨自身的润滑性,石墨载板不仅不会与原玻璃体发生粘结,且原玻璃体能够在微晶化处理过程中保持良好的表面状态。为了进一步提高制得的微晶玻璃的表面质量,优选地,所述载板的表面粗糙度ra小于0.2μm,优选为小于0.05μm,更优选为小于0.025μm。在本文中,表面粗糙度指表面(载板、原玻璃体或制得的微晶玻璃)具有的较小间距和微小峰谷的不平度,通过gb/t10610-1998方法测得。为了进一步保证微晶玻璃的表面质量、晶粒尺寸,优选地,所述微晶化处理在保护气体气氛下进行。一方面由于气氛会对析晶效果和析晶过程存在一定影响,例如析晶环境中游离氧的含量会影响晶粒生长,通过充入保护气体降低析晶环境中的游离氧,在一定程度上可以阻碍晶粒长大,保证玻璃在微晶化过程中不受气氛影响干扰,以至于达到细化晶粒的效果;另一方面,充入保护气体可以防止如石墨等载板材料在高温或其他气氛条件下被氧化、腐蚀。优选地,所述保护气体为纯氦气、纯氮气,或者氦气与氮气的混合物。若所述保护气体为氦气与氮气的混合物,两种气体的混合比例可以任意调节,例如体积比为1:1等。优选地,所述保护气体的纯净度大于99.999体积%,所述保护气体气氛中o2、so2、co2的体积含量之和小于10ppm。原则上,本申请并不限定制备原玻璃体的方法。而特别地用于制备超薄微晶玻璃时,优选地使用浮法工艺制备原玻璃体。优选地,所述方法还包括对微晶化处理后的原玻璃体进行3d加工和/或化学强化处理。本发明中的核化温度、核化时间、晶化温度和晶化时间统称为热处理制度,具体的热处理制度与原玻璃体的组成有关,不同组成对应的最优热处理制度有差异。由于原玻璃体在微晶化处理过程处于高内能亚稳态,在转变为晶体过程中会放出热量,应用差热分析仪(如德国耐驰dsc404f3)可以分析出原玻璃体的转变温度(tg)和析晶速度最大的温度(tp),从而确定热处理制度。在原玻璃体的微晶化处理过程中,原玻璃体的软化点温度是影响最终产品的重要因素。特别地,本发明所述的生产微晶玻璃的方法优选地适用于具有上述组成的原玻璃体。这是因为本申请所述的微晶化处理温度(核化温度和晶化温度)都低于具有上述组成的原玻璃体的软化点温度。而如果微晶化处理温度(核化温度和晶化温度)接近甚至高于软化点温度,那么原玻璃体在微晶化处理过程中会发生变形,同时可能造成不必要的多晶转变或某些晶核重新溶解,从而影响微晶玻璃的最终质量。采用本发明所述的上述方法制备的微晶玻璃,表面质量良好,表面粗糙度ra≤15nm(甚至ra≤10nm),翘曲高度较小,微晶玻璃表面质量缺陷率与对应原玻璃体表面质量缺陷率的比值m小于1.05,透光率失效值q≤0.02;特别地,制得的超薄微晶玻璃(厚度为0.3-1mm),翘曲高度非常小,都小于0.3mm。透光率失效值q表示微晶化处理过程对原玻璃体透光率的影响效果,通过下式计算得到:q=1-t1/t0其中,t0表示原玻璃体的透光率,t1表示微晶玻璃的透光率。在本文中,表面质量缺陷率表示按照gb/t30020-2013方法通过全自动缺陷检测仪检测出的玻璃的缺陷个数,例如全自动缺陷检测仪可采用德国申克2558125缺陷检测仪。翘曲高度测试时,可采用如下方法进行:选定样品尺寸(长×宽)为1300×1100mm,样品厚度可为0.3-1mm,将样品平放大理石平台,保持船翘状态,选定合适规格塞尺对玻璃四角以及边部分别进行塞入测试,逐渐增加塞尺厚度至玻璃样品刚好不发生移动,此时塞尺厚度即为该样品翘曲高度值。透光率为按照iso13468-1:1996方法测得的,例如采用uv-2450紫外可见分光光度计测试。表面粗糙度为按照gb/t10610-1998方法测得的,例如采用sv-3100表面粗糙度测试仪。雾度为按照iso14782:1999方法测得的,例如可采用德国byk4775透射雾影仪进行测试。本发明第二方面提供了一种连续生产微晶玻璃的方法,包括:(1)将玻璃组合物通过浮法工艺制备得到原玻璃体;(2)将所述原玻璃体按照本发明第一方面所述的方法进行处理。优选地,所述浮法工艺包括将所述玻璃组合物引入浮法玻璃熔窑,经熔化、澄清、均化、自然摊平、抛光、拉薄成型、退火、切裁制备得到原玻璃体。根据本发明,制备原玻璃体可以采用常规浮法工艺生产线,也可以根据玻璃组合物的组成做相应调整。原则地,本发明对原玻璃体的厚度不做限定,可以根据需要来调整。特别地,本发明所述方法能够用于制备超薄微晶玻璃,得到透光率好、表面质量好、外形完整度高、翘曲高度特别小的超薄微晶玻璃。因此,为了得到超薄微晶玻璃,优选地,原玻璃体的厚度t为0.3-1mm。优选地,所述玻璃组合物包含:52-62重量%的sio2,12-25重量%的al2o3,5-15重量%的na2o,0-4重量%的k2o,2-5重量%的mgo,0.5-5重量%的zro2,3-7重量%的li2o,0-4.5重量%的tio2,0-2重量%的b2o3,以及0-2重量%的澄清剂。进一步优选地,所述玻璃组合物包含:52-60重量%的sio2,例如可以为52.5重量%、53重量%、56重量%、58重量%、59.5重量%以及上述数值中任意两个所组成范围中任意一值;14-25重量%的al2o3,例如可以为14.5重量%、14.8重量%、15重量%、20重量%、22重量%、24重量%、24.5重量%、24.8重量%以及上述数值中任意两个所组成范围中任意一值;7-14重量%的na2o,例如可以为7.5重量%、8重量%、12重量%、13重量%、13.5重量%以及上述数值中任意两个所组成范围中任意一值;0-4重量%的k2o,例如可以为0.2重量%、0.5重量%、1重量%、3重量%、3.5重量%、3.8重量%以及上述数值中任意两个所组成范围中任意一值;3-4.5重量%的mgo,例如可以为3.2重量%、3.5重量%、4重量%、4.2重量%以及上述数值中任意两个所组成范围中任意一值;0.5-4重量%的zro2,例如可以为0.2重量%、0.5重量%、1重量%、2重量%、3重量%、4重量%、4.2重量%以及上述数值中任意两个所组成范围中任意一值;4-7重量%的li2o,例如可以为4.2重量%、4.5重量%、5重量%、6重量%、6.5重量%、6.8重量%以及上述数值中任意两个所组成范围中任意一值;0-4.5重量%的tio2,例如可以为0.2重量%、0.5重量%、1重量%、2重量%、3重量%、4重量%、4.2重量%以及上述数值中任意两个所组成范围中任意一值;0-2重量%的b2o3,例如可以为0.2重量%、0.5重量%、1重量%、1.5重量%、1.8重量%以及上述数值中任意两个所组成范围中任意一值;以及0-1.5重量%的澄清剂,例如可以为0.1重量%、0.2重量%、0.8重量%、1.2重量%、1.4重量%1.48重量%以及上述数值中任意两个所组成范围中任意一值。在本发明中,所述澄清剂包括但不限于no3-、f-、cl-和so42-中的至少一种。在采用浮法工艺的玻璃成形过程中,粘度是一个重要指标,要求粘度适中,以适用于超薄玻璃的制备。优选地,所述玻璃组合物制备的原玻璃体的工作点粘度范围为1.2×103-9.5×105dpa·s,此粘度对应的温度之间的差值可以表征浮法玻璃的硬化速度。优选地,原玻璃体的硬化速度为250℃-350℃,如原玻璃体的硬化速度低于250℃,则硬化速度太快,无法进行超薄拉引;如高于350℃,则硬化速度过慢,不利于提高浮法生产效率。优选地,步骤(2)中的微晶化处理在析晶装置中进行。优选地,所述析晶装置设置在浮法工艺冷端出口处。优选地,所述析晶装置的承接区与浮法工艺冷端出口连接。在一种具体的实施方式中,按照上述玻璃组合物的组成计算对应原料用量,原料选择各自对应的氧化物、碳酸盐或硝酸盐等,将原料充分混合均匀后送入浮法玻璃熔窑,经熔化、澄清、均化后形成均匀玻璃液,玻璃液经流道进入充满氮气保护气的锡槽,经自然摊平、抛光、徐冷、拉薄等,之后进入退火窑退火以消除玻璃内应力,后经冷端切割后形成原玻璃体。通过机械手抓取冷端出口辊道上的原玻璃体放置于载板上,载板材料例如为石墨,原玻璃体随载板被运输入析晶窑内,调整载板数量以及运行速度,以适应浮法产线原玻璃体的生产节拍。本发明第三方面提供了本发明第一、第二方面所述的方法制得的微晶玻璃。优选地,所述微晶玻璃的表面粗糙度ra≤15nm,优选地ra≤10nm。优选地,所述微晶玻璃的透光率失效值q≤0.02,优选地q≤0.015,且在波长为380-780nm范围内,透光率为88%以上。优选地,所述微晶玻璃的雾度小于0.5%。优选地,所述微晶玻璃的表面质量缺陷率与所述原玻璃体的表面质量缺陷率的比值m小于1.05,优选地m≤1.03。优选地,所述微晶玻璃的厚度为0.3-1mm。优选地,所述微晶玻璃的翘曲高度小于0.3mm,优选为小于0.25mm。本发明第四方面提供了一种微晶玻璃,其包含:52-62重量%的sio2,12-25重量%的al2o3,5-15重量%的na2o,0-4重量%的k2o,2-5重量%的mgo,0.5-5重量%的zro2,3-7重量%的li2o,0-4.5重量%的tio2,0-2重量%的b2o3,以及0-2重量%的澄清剂。优选地,所述微晶玻璃的表面粗糙度ra≤15nm。优选地,所述微晶玻璃的透光率失效值q≤0.02,优选地q≤0.015,且在波长为380-780nm范围内,透光率为88%以上。优选地,所述微晶玻璃的雾度小于0.5%。优选地,所述微晶玻璃的表面质量缺陷率与所述原玻璃体的表面质量缺陷率的比值m小于1.05,优选为m≤1.03。优选地,所述微晶玻璃的厚度为0.3-1mm。优选地,所述微晶玻璃的翘曲高度小于0.3mm,优选为小于0.25mm。优选地,所述微晶玻璃是按照本发明第一、第二方面所述的方法制得的。本发明第五方面提供了本发明第三方面、第四方面所述微晶玻璃在移动电子终端设备前后盖保护玻璃中的应用。根据本发明,所述移动电子终端设备包括但不限于平板、手机、电脑、智能手表等。本发明所述方法能够结合生产线直接对原玻璃体进行微晶化处理,故不再需要进行额外磨、抛等加工工序,同时通过控制微晶化工艺,得到综合性能优异的微晶玻璃,具有透光率好(透光率失效值q≤0.02)、表面质量好(表面粗糙度ra≤15nm)、翘曲高度小、外形完整度高等优点;特别地制得的超薄玻璃(厚度为0.3-1mm),除具有上述优势,而且翘曲高度也非常小,都小于0.3mm,甚至小于0.25mm。以下将通过实施例对本发明进行详细描述。应当理解的是,此处所描述的具体实施例仅用于说明和解释本发明,并不用于限制本发明。实施例1采用同一种玻璃组合物,通过控制熔化、成型等工艺,制备不同厚度的原玻璃体a1-a5,将原玻璃体经过冷端出口进入析晶窑后进行微晶化处理。具体地,首先,按照如下组成计算对应原料用量:59.34重量%的sio2,15.16重量%的al2o3,9.25重量%的na2o,2.14重量%的k2o,3.39重量%的mgo,3.81重量%的zro2,5.34重量%的li2o,1.05重量%的tio2,澄清剂(cl-与so42-)合计0.5重量%,将各原料充分混合均匀后送入浮法玻璃熔窑,经熔化、澄清、均化后形成均匀玻璃液,玻璃液经流道进入充满氮氢气保护气的锡槽,经自然摊平、抛光、徐冷、拉薄等,之后进入退火窑退火以消除玻璃内应力,后经冷端切割后形成不同厚度的原玻璃体a1-a5,按照gb/t30020-2013以及iso13468-1:1996方法测试原玻璃体a1-a5的表面质量缺陷率、透光率。通过机械手抓取冷端出口辊道上的原玻璃体放置在载板(石墨板)上,原玻璃体随石墨载板被运输至析晶窑内。析晶窑内各区的对应气氛以及工艺条件如表1所示。表1微晶化处理完成后,在慢速降温区m1降至适当温度(例如为430℃)之后在快速降温区m2降温至100℃以下(例如25℃),在卸载区通过机械手取出得到微晶玻璃b1-b5,而石墨载板紧接着被运送至入口处形成生产闭环。对得到的微晶玻璃进行xrd测试,测试显示微晶玻璃b1-b5具有明显的晶相和玻璃相,如图1示出了微晶玻璃b1的xrd测试图。采用与原玻璃体相同的方法,测试微晶玻璃b1-b5的表面质量缺陷率及透光率,并计算质量缺陷率比值m以及透光率失效值q。采用gb/t10610-1998方法测试微晶玻璃b1-b5的表面粗糙度ra。采用如下方法测试微晶玻璃b1-b5的翘曲高度:选定样品尺寸(长×宽)为1300×1100mm,样品厚度可为0.3-1mm,将样品平放大理石平台,保持船翘状态,选定合适规格塞尺对玻璃四角以及边部分别进行塞入测试,逐渐增加塞尺厚度至玻璃样品刚好不发生移动,此时塞尺厚度即为该样品翘曲高度值。上述测试结果如表2所示。表2微晶玻璃b1b2b3b4b5m1.011.001.001.011.03t0/%91.691.591.591.691.7t1/%90.590.390.890.490.4q0.0120.0130.0080.0130.014翘曲高度/mm0.150.120.250.180.15表面粗糙度ra/nm8981010对比例1参照实施例1所述方法制备微晶玻璃,不同的是,在浮浴过程中(锡槽内)按照cn1896020a实施例1所述方法进行微晶化处理,最终得到对比玻璃d1。对比例2参照实施例1所述方法制备微晶玻璃,不同的是,在退火窑按照cn107857467a实施例1所述方法进行微晶化处理,最终得到对比玻璃d2。按照实施例1所述方法,对对比玻璃d1、d2进行测试,测试结果如表3所示。表3由表2和表3可知,相比于其他微晶玻璃生产方法,本发明所述方法不仅能够生产出超薄(厚度为0.3-1mm)微晶玻璃,同时所得微晶玻璃产品还具有透光率失效值q≤0.02、析晶前后表面质量缺陷率比值m≤1.03、表面粗糙度ra≤10nm、翘曲高度≤0.25mm等优异性能。实施例2-13采用如表4所示的玻璃组合物,参照实施例1所述方法制备微晶玻璃,具体工艺条件如表4所示。采用n2作为保护气体,保护气体的纯净度为99.9999体积%,保护气体气氛中o2+so2+co2体积含量为8ppm,在石墨载板上进行微晶化处理。实施例14采用实施例2所述的玻璃组合物,参照实施例2所述方法制备微晶玻璃,不同的是,设置升温区的升温速率为40℃/min,其余与实施例2相同,最终得到微晶玻璃b14。实施例15采用实施例2所述的玻璃组合物,参照实施例2所述方法制备微晶玻璃,不同的是,设置升温区的升温速率为25℃/min,其余与实施例2相同,最终得到微晶玻璃b15。实施例16采用实施例2所述的玻璃组合物,参照实施例2所述方法制备微晶玻璃,不同的是,设置慢速降温区m1的降温速率vm1为15℃/min,快速降温区m2的降温速率vm2为40℃/min其余与实施例2相同,最终得到微晶玻璃b16。实施例17采用实施例2所述的玻璃组合物,参照实施例2所述方法制备微晶玻璃,不同的是,设置慢速降温区m1的降温速率vm1为35℃/min,快速降温区m2的降温速率vm2为60℃/min,其余与实施例2相同,最终得到微晶玻璃b17。实施例18采用实施例2所述的玻璃组合物,参照实施例2所述方法制备微晶玻璃,不同的是,析晶装置的降温区不区别慢速降温区和快速降温区,在降温区的降温速率一直为24℃/min,其余与实施例2相同,最终得到微晶玻璃b18。按照实施例1所述方法,对微晶玻璃b14-b18进行相关性能测试,测试结果如表5所示。表5实施例所得的微晶玻璃实施例14实施例15实施例16实施例17实施例18m1.031.021.021.0410.2t0/%91.591.791.691.691.5t1/%89.890.490.490.190.5q0.0180.0140.0130.0160.011翘曲高度/mm0.450.180.180.50.15雾度/%0.470.430.420.410.37表面粗糙度ra/nm1010101010其中实施例2-9采用本发明所述组成的玻璃组合物以及本发明所述的微晶玻璃制备方法,实施例10、实施例11以及实施例14-18为采用本发明所述组成的玻璃组合物但微晶玻璃制备方法不同于本发明,实施例12、实施例13中使用的玻璃组合物不同于本发明,但是采用本发明所述的微晶玻璃制备方法。将最终得到的玻璃参照实施例1所述方法进行相关测试,测试结果如表4和表5所示。由表4的结果可知,采用本发明所述组成的玻璃组合物,本发明所述的制备方法制得的微晶玻璃,如实施例1-9,具有透光率高(在可见光380-780nm范围内大于88%),透光率失效值低(q≤0.015),雾度低(<0.5%),翘曲高度小(<0.25mm),粗糙度小(ra≤10nm)等优点。采用本发明所述组成的玻璃组合物,但制备工艺中析晶温度不同于本发明,如实施例10、实施例11,所制备的微晶玻璃的雾度、翘曲高度,透过率失效值q,表面粗糙度ra较大,难以满足终端前后盖保护玻璃的使用要求。采用本发明所述组成的玻璃组合物,但制备工艺中升、降温速率不同于本发明,如实施例14-18,玻璃升、降温速率大于本发明限定速率时,其所制玻璃翘曲高度较大;玻璃升、降温速率小于本发明限定速率时,虽对玻璃性能无明显影响,但速率过慢势直接导致产量过低生产成本过高。采用组成不同于本发明的玻璃组合物,但使用本发明所述的制备方法,如实施例12、实施例13,所制备的微晶玻璃透过率较低,雾度以及表面粗糙度均较大。以上详细描述了本发明的优选实施方式,但是,本发明并不限于此。在本发明的技术构思范围内,可以对本发明的技术方案进行多种简单变型,包括各个技术特征以任何其它的合适方式进行组合,这些简单变型和组合同样应当视为本发明所公开的内容,均属于本发明的保护范围。当前第1页12