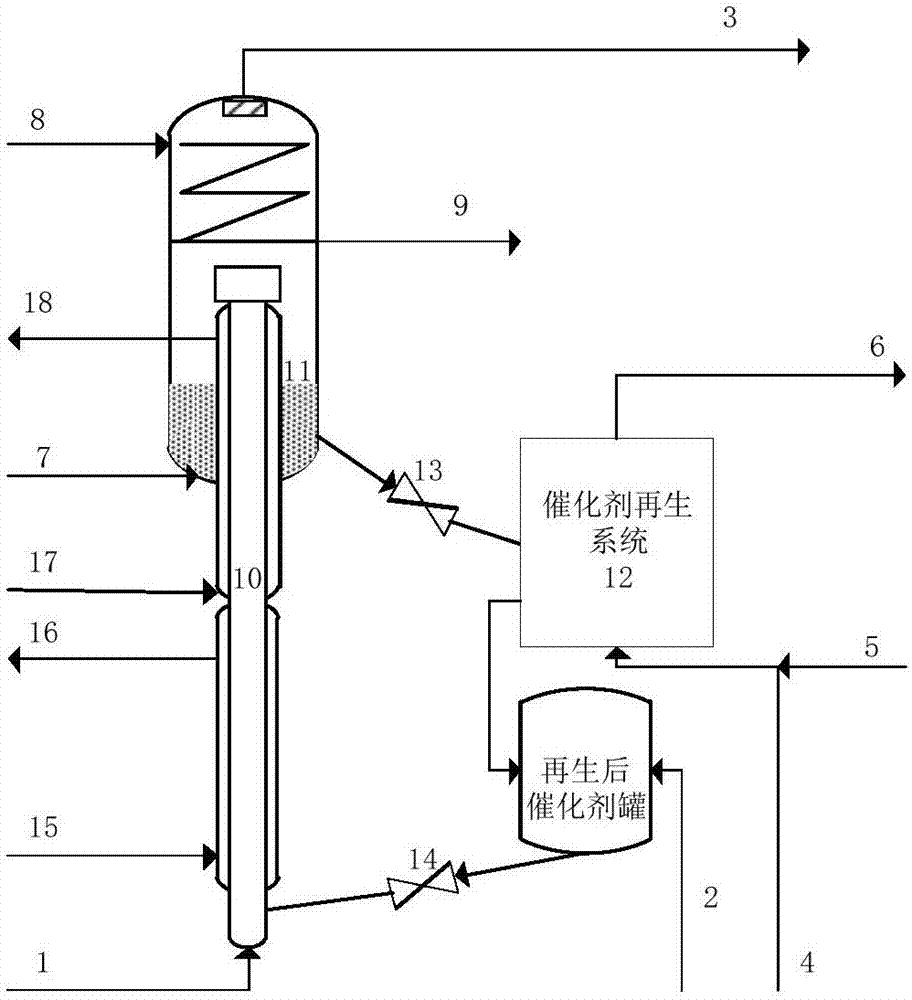
本发明涉及一种循环流化床工艺及在连续异构化应用,具体地说是一种环氧化物连续异构化的装置和方法,可用于环氧化物连续异构化制备相应的烯丙基醇产品。
背景技术:
:烯丙醇是一种重要的化工中间体和精细化工产品,由于分子结构中含有双键和羟基两种官能团,可参与氧化、还原、酯化、醚化和加成等,在化学品、医药、香料以及有机合成等方面具有广泛的用途。主要的衍生物及其用途为:用于合成环氧氯丙烷、甘油、1,4—丁二醇以及烯丙基酮等重要有机合成原料,其重要衍生物烯丙酯主要作为生产聚合物的单体或预聚体。此前烯丙醇合成主要采用烯丙基氯水解的方法合成,烯丙基氯水解工艺然会产生含大量氯废水、废液。烯丙醇目前的生产工艺产生大量废水、废液,随着人们对环境保护和化学反应原子经济性要求的逐渐提高,开发低成本、高收率、低污染的生产过程已成为未来化学工业发展的必然趋势,因此迫切需要一种更加绿色高效的方案。环氧化物异构化制备相应烯丙基醇具有工艺简单、收率高,对设备无腐蚀、无“三废”污染产生等优点。目前,作为催化环氧丙烷异构化反应最为有效的催化剂是磷酸锂,所以,目前它也得到了广泛的工业应用。环氧化物异构化制备相应烯丙基醇又有两种方法,分别为气相法和浆液反应法。气相法采用压片或挤条成型催化剂,固定床作为反应器,由于异构过程会生成大量活性中间体,易发生聚合导致催化剂积碳,催化剂寿命较短。美国专利us4720598公布了一种气相法合成及再生工艺,反应温度255-260℃,环氧丙烷在磷酸锂催化剂催化下异构生成烯丙醇,气相法采用固定床反应器,具有流程短、烯丙醇收率高的特点,但催化剂失活极快,催化剂使用30h,活性损失达到50%。需要频繁切换再生,生产效率低,不满足工业化生产要求。美国专利us3238264公布了浆液法制备烯丙醇的方法,其特点是,采用粉末磷酸锂催化剂,将催化剂悬浮在高沸点溶剂中进行反应,反应过程中需不断抽出并分离部分悬浮的失活催化剂,以分离出附着在油层上的焦油,其具备催化剂连续加入,连续采出的特点,但由于采用大量高沸点溶剂,存在溶剂损失,且由于高沸溶剂的存在,导致气液固扩散成为速控步骤,反应活性明显下降,导致反应停留时间长,副反应多。流化床反应器具有气固传质效率高,反应速率快,无溶剂损失的优点,由于催化剂强度等方面的原因,在环氧化物异构工艺中仍然未得到应用,本公司采用自制催化剂,成功开发了固定床流化床工艺生产烯丙醇小试工艺,但该异构化工艺中,催化剂仍然会快速失活,固定流化床工艺无法实现催化剂循环再生过程,且固定流化床反应器由于返混严重,导致烯丙醇选择性与环氧丙烷转化率收到影响,不利于进一步工业化放大。技术实现要素:针对上述现有技术中存在的问题,本申请发明人进行了深入研究,结果发现,采用耐磨催化剂,采用提升管流化床工艺,成功解决了目前工业化液相法工艺中存在溶剂损失,反应停留时间长,副反应多的问题,提高了反应活性,降低了失活速率,同时解决了固定床流化床工艺中返混高导致产品收率低与催化剂无法连续再生的问题,在本工艺中得到了较好的应用,反应速率及选择性均得到了有效的提高。本发明一个目的在于提供一种新的环氧化物异构工艺,采用循环流化床工艺,成功解决了目前液相法工艺中存在溶剂损失,反应停留时间长,副反应多的问题。本发明另一个目的在于将上述工艺用于环氧丙烷异构化制备相应烯丙基醇,该工艺具有原子经济性高、产品收率及选择性高、工艺无污染的特点,明显优于当前浆态床工艺。为实现以上技术目的,本发明采用的技术方案如下:一种环氧化物连续异构化的装置,该装置包括:二段提升管流化床反应器、位于提升管流化床反应器的第二段上方的沉降器、通过管道与沉降器底部连接的催化剂再生系统、通过管道与催化剂再生系统连接的再生后催化剂罐,再生后催化剂罐通过管道连接于二段提升管流化床反应器的第一段,其中,二段提升管流化床反应器的每一段单独控温(即具有单独的控温系统),二段提升管流化床反应器的第二段部分伸入沉降器内部,在伸入的二段提升管反应器的第二段部分与沉降器底部的内壁之间形成催化剂沉积区,沉降器顶部出口为反应产物出口,沉降器底部设有用于对沉降器底部积碳催化剂气提的待生催化剂气提管线。伸入沉降器内部的二段提升管反应器的第二段部分可以占第二段提升管(或二段提升管流化床反应器的第二段)总长度的1/5~4/5,优选2/5~3/5。优选地,沉降器底部通过斜管连接催化剂再生系统。关于二段提升管流化床反应器的每一段单独控温,优选地,二段提升管流化床反应器的第一段(一段提升管)和第二段(二段提升管)设有独立的夹套冷却器,第一段的夹套冷却器的热油温度为210~270℃,优选230~250℃,提升管流化床反应器下半段,物料浓度高,反应速率快,放热速率快,采用低温热油尽可能的移走热量;第二段的夹套冷却器的热油温度为250~290℃,优选270~280℃,提升管上半段,反应速率降低,通过高热油温度加热,保证上半段温度,提高转化率。所述沉降器顶部设置过滤器,优选800-1200目过滤器,例如1000目过滤器,大部分催化剂使用过程中磨损产生的细粉不会夹带进入沉降器顶部反应气中,减少催化剂与反应液进一步接触导致的串联副反应。进一步地,二段提升管流化床反应器采用细长型提升管反应器,纵横比为50~200:1,优选80~130:1,以减少物料返混。进一步地,在提升管流化床反应器的第二段(二段提升管)出口上方设置循环水冷却器,通过控制沉降器温度140~240℃,优选160~200℃而终止反应。本发明的另一个目的是提供一种环氧化物连续异构化的方法,将反应原料环氧化物与载气氮气预热至一定温度(例如220~350℃,优选250~290℃),让原料与进入二段提升管流化床反应器,与流化状态的催化剂(再生催化剂和/或新补充催化剂)接触,在一定的压力(例如0.1~5bar,优选,0.5~1.5bar;)下与停留时间(例如1~10s,优选2~5s)下在二段提升管流化床反应器内进行异构反应,提升管出口得到反应产物、原料、载气与催化剂的混合物,在设置于二段提升管流化床反应器的第二段上部的沉降器中分离得到反应气和积碳催化剂,其中,反应气上升经沉降器顶部反应液管线进入产物分离系统,沉降器底部积碳催化剂经氮气气提后,进入再生器再生烧炭(例如与贫氧气或空气接触),得到的再生烟气从再生器顶部烟气管线排出,得到的再生后催化剂输送至再生后催化剂储罐中,经催化剂管线返回提升管反应器。进一步地,新补充催化剂补充至催化剂储罐中,用于维持催化剂物料平衡。催化剂再生系统设有再生氮气进料管线和再生空气进料管线。优选地,二段提升管流化床反应器采用细长型提升管反应器,纵横比为50~200:1,优选80~130:1,减少物料返混。通过采用两段提升管反应器合一,精确控制反应温度,并简化了系统,提高了可靠性。优选地,二段提升管流化床反应器的第一段(一段提升管)冷却器热油温度为210~270℃,优选230~250℃,提升管反应器下半段,物料浓度高,反应速率快,放热速率快,采用低温热油尽可能的移走热量;二段提升管流化床反应器的第二段的冷却器热油温度为250~290℃,优选270~280℃,提升管上半段,反应速率降低,通过高热油温度加热,保证上半段温度,提高转化率。本发明方法中,所述二段提升管流化床反应器的第二段出口上方设置循环水冷却器,通过控制沉降器温度在140~240℃,优选160~200℃而终止反应。本发明方法中,沉降器下部采用氮气进行气提,是沉降器下部催化剂沉积部位为氮气气氛,减少沉降器死体积内副反应的进一步发生,气提氮气用量与环氧化物比例为0.5~2:1,优选0.8~1.2:1(mol)。本发明方法中,所述沉降器顶部设置过滤器,采用800-1200目,优选1000目过滤器,大部分催化剂使用过程中磨损产生的细粉不会夹带进入沉降器顶部反应气中,减少催化剂与反应液进一步接触导致的串联副反应。优选地,所述预热温度为220~350℃,优选250~290℃。优选地,反应压力为0.1~5bar,优选,0.5~1.5bar。优选地,所述物料及催化剂在提升管反应器中接触时间为1~10s,优选2~5s。优选地,新补充催化剂的补充比例为0.02~1%/h,优选0.05~0.2%/h。优选地中,氮气与环氧化物的摩尔比为1~5:1,优选2~3:1。优选地,所述环氧化物进料与催化剂质量比为0.5~3:1,优选1~2:。环氧化物选自环氧丙烷、环氧丁烷、环氧己烷、环氧环己烷中的一种或多种。本发明方法中催化剂采用二氧化硅担载的二氧化钛/氧化锌/氢氧化钾/磷酸锂催化剂。本发明中所述的压力均为绝压。本发明的积极效果在于:本发明的催化剂用于催化环氧丙烷异构化制备烯丙醇,产品收率明显提高,单程收率达到50%以上,选择性高达94%以上;催化剂可以原位再生添加,又不引入溶剂,相比浆液法工艺减少了溶剂损耗,提高了工艺经济性;反应失活催化剂直接由斜管进入再生器中,即使催化剂失活快,仍然实现连续生产;采用提升管式流化床反应器,物料与催化剂接触时间固定,停留时间分布窄,通过外夹套控制温度,反应温度稳定,副反应控制可以达到固定床反应器水平;该工艺绿色无污染,原子经济性高,主反应原子经济性达到100%。提升管反应器移热系统,沉降器撤热终止反应系统,改变了原有提升管反应器无撤热,反应终止效果不佳的缺点,部分催化剂夹带至反应气体中的缺点,进一步提高了产品收率。附图说明图1为不同催化剂补加量对反应性能影响。图2为本发明的环氧化物连续异构化的装置示意图。1.反应原料进料管线,2.新鲜催化剂补充进料,3.反应气出气管线,4.再生氮气进料管线,5.再生空气进料管线,6.再生后尾气出料管线,7.待生催化剂气提管线,8.冷却器循环水进料,9.冷却器循环水出料,10.二段提升管流化床反应器,11.沉降器,12.催化剂再生系统(再生器),13.失活催化剂输送管线,14.再生后催化剂输送管线,15.一段提升管冷却器热油进料,16.一段提升反应器热油出料,17.二段提升管冷却器热油进料,18.二段冷却器热油出料。具体实施方式下面结合附图和实施例对本发明作进一步的说明,需要说明的是,实施例并不构成对本发明要求保护范围的限制。如图1所示,本发明的环氧化物连续异构化的装置包括:二段提升管流化床反应器10、位于提升管流化床反应器10的第二段上方的沉降器11、通过失活催化剂输送管线13与沉降器11底部连接的催化剂再生系统12、通过管道与催化剂再生系统12连接的再生后催化剂罐,再生后催化剂罐通过再生后催化剂输送管线14(斜管)连接于二段提升管流化床反应器10的第一段,其中,二段提升管流化床反应器10的第一段的下部设有反应原料进料管线1,每一段单独控温,二段提升管流化床反应器10的第二段部分伸入沉降器11内部,在伸入的二段提升管反应器的第二段部分与沉降器底部的内壁之间形成催化剂沉积区,沉降器11顶部设有反应气出气管线3,沉降器11底部设有用于对沉降器底部积碳催化剂气提的待生催化剂气提管线7。伸入沉降器内部的二段提升管反应器的第二段部分可以占第二段提升管(或二段提升管流化床反应器的第二段)总长度的1/5~4/5,优选2/5~3/5。二段提升管流化床反应器的第一段(一段提升管)和第二段(二段提升管)设有独立的夹套冷却器,第一段的夹套冷却器分别设有一段提升管冷却器热油进料15和一段提升反应器热油出料16,热油温度为210~270℃,优选230~250℃,提升管流化床反应器下半段,物料浓度高,反应速率快,放热速率快,采用低温热油尽可能的移走热量;第二段的夹套冷却器设有二段提升管冷却器热油进料17和二段冷却器热油出料18,热油温度为250~290℃,优选270~280℃,提升管上半段,反应速率降低,通过高热油温度加热,保证上半段温度,提高转化率。所述沉降器顶部设置1000目过滤器,大部分催化剂使用过程中磨损产生的细粉不会夹带进入沉降器顶部反应气中,减少催化剂与反应液进一步接触导致的串联副反应。二段提升管流化床反应器采用细长型提升管反应器,纵横比为50~200:1,优选80~130:1,以减少物料返混。在提升管流化床反应器的第二段(二段提升管)出口上方设置循环水冷却器,其具有冷却器循环水进料8和冷却器循环水出料9,通过控制沉降器温度140~240℃,优选160~200℃而终止反应。催化剂再生系统12设有再生氮气进料管线4和再生空气进料管线5,积碳催化剂经氮气气提后进入催化剂再生系统12与通过再生空气进料管线5进入的空气(贫氧气)接触再生烧炭,得到的再生烟气从催化剂再生系统12顶部再生后尾气出料管线6排出。再生后催化剂罐设有新鲜催化剂补充进料2。在以下实施例中,如无特别注明,所采用的“%”均为“wt%”。产品组成采用岛津gc-2010型气相色谱仪(pona型毛细管色谱柱,氢火焰检测器,氮气作为载气)进行分析。采用乙醇溶剂、汽化室温度250℃、载气流速1ml/min、进样量1μl、色谱柱程序升温:首先50℃保持2min,然后以5℃/min升温至80℃,保持5min,然后以20℃/min升温至260℃,保持15min。实施例中使用的催化剂如下制备:将1000g磷酸锂催化剂原粉、4000g硅溶胶(电子级硅溶胶,平均粒径10~20nm,金属离子含量<20ppm,固含量25%,ph=8,山东百特新材料有限公司)、33.3g二氧化钛、16.7g氧化锌,2.5g氢氧化钾混合,加入1000g去离子水,充分搅拌均匀,获得未喷雾干燥浆料,浆料固含34%。将浆料打入喷雾干燥机中喷雾干燥,喷雾干燥温度250℃。将喷雾干燥后颗粒放入马弗炉中360℃焙烧6h,获得成品催化剂iso-1。催化剂组成如下:(tio2)1.62(zno)0.82(koh)0.12(li3po4)48.72(sio2)48.72。实施例1本工艺中采用的反应器为如图1所示的二段提升管流化床反应器,其内径为40毫米,高度为4米;提升管反应器的第二段出口位于沉降器内,实现催化剂与反应物及产物快速分离,反应产物送入后续分离系统。首先将氮气、环氧丙烷加热到280℃进入提升管与再生催化剂及新补充催化剂接触反应,氮气流量10l/min,环氧丙烷进料速率为7.8kg/h,循环催化剂3.9kg/h,补充催化剂进料速率3.9g/h,提升管外加套导热油温度280℃,物料与催化剂在提升管反应器中接触时间为3秒,提升管出口温度为290℃,出口反应液与催化剂混合物经换热器能却至180℃,反应终止。提升管出口的积碳催化剂在重力作用下进入沉降器,沉降器内径为200毫米,高度为1.5米;积碳催化剂在沉降器中经氮气气提,气提氮气用量为5l/min,催化剂沉降后进入再生器再生,再生后的催化剂返回到提升管反应器;反应气上升至沉降器顶部反应气出口冷凝后进入后续分离系统。冷凝后反应液取样,经gc分析,分析结果见表1。表1:实施例1产品液分析结果反应组别po/%aa/%其它/%xpo/%saa/%r-143.2553.673.0856.7594.57注:实施例2与实施例1不同的是,考察了不同预热温度下异构化性能。见表2。表2:不同温度反应性能结果预热温度/℃po/%aa/%其它/%xpo/%saa/%25068.1230.511.3731.8895.7026060.5437.531.9339.4695.1127051.3146.122.5748.6994.7228043.2553.673.0856.7594.5729027.4566.715.8472.5591.95实施例3与实施例1不同的是考察了不同冷却温度对最终反应性能的影响,见表3。表3:不同冷却温度反应性能实施例4与实施例1不同的是考察了不同接触时间对最终反应性能的影响,见表4。表4不同接触时间反应性能接触时间/spo/%aa/%其它/%xpo/%saa/%255.7642.711.5344.2496.54343.2553.673.0856.7594.57436.4159.234.3663.5993.14531.6662.535.8168.3491.50实施例5与实施例1不同的是考察了不同环氧化物与催化剂质量比对最终反应性能的影响,见表5。表5不同催化剂用量环氧/催化剂po/%aa/%其它/%xpo/%saa/%165.7633.320.9234.2497.311.356.2541.891.8643.7595.751.847.2350.232.5452.7795.19243.2553.673.0856.7594.57注:环氧/催化剂为进料质量比。实施例6与实施例1不同的是考察了不催化剂补加量对反应性能的影响,见图1。当前第1页12