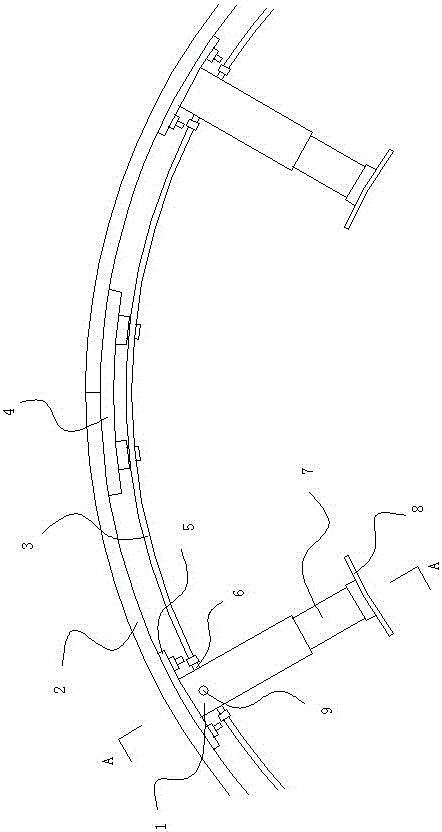
本发明涉及机动车轮胎爆胎应急装置领域,尤其涉及一种真空轮胎内置爆胎应急装置。
背景技术:安装真空轮胎的汽车在行驶过程中出现爆胎情况时,外胎会向轮辋的凹槽凹陷,甚至脱落,使得轮辋的轮缘取代外胎而支撑地面。一方面,由于外胎凹陷、甚至脱落,导致车身重心向爆胎车轮一侧倾斜,容易发生侧翻;另一方面,由于轮缘与地面间的摩擦系数小,无法实现车辆转弯,容易导致车辆失去方向控制。因此,对于行驶过程中的车辆,特别是高速行驶中的车辆,爆胎极易导致交通事故,甚至酿成车毁人亡的惨剧。在现有技术中,真空轮胎爆胎应急装置的设计思路可概括为三种。第一种是用爆胎应急装置封堵住轮辋凹槽,从而防止外胎脱落,避免轮缘支撑地面。专利号为01811431.8的发明专利所公开的一种环绕轮辋安装的组件便是采用这种思路设计而成的,但该组件存在发生爆胎后,车身重心倾斜程度较大的缺陷。第二种思路是将爆胎应急装置设计成包括一个形状与内胎相似的硬质轮胎,该硬质轮胎通过支撑件与车轮轮辋相连,当发生爆胎时,由该硬质轮胎支撑起车身,减少车身重心倾斜程度,避免车辆失去方向控制。采用第二种思路设计而成的爆胎应急装置包括公开号为101905628中国发明专利所公开的装置,但该装置存在须在车轮轮辋上加焊部件的缺陷。第三种设计思路是将爆胎应急装置的主体设计成一个圆筒,当发生爆胎时,由该圆筒顶起外胎,外胎胎唇提起轮毂,进而撑起车身,避免车身重心发生较大程度倾斜及车辆失去方向控制。体现第三种设计思路的有公告号为203713430的中国发明所公布的轮胎内置防爆轮辋,但该轮胎内置防爆轮辋存在难以为车辆提供动力的缺陷。如何设计出一种真空轮胎内置爆胎应急装置,使得安装它的车辆在发生爆胎时,车身重心不致发生大的倾斜,且爆胎车轮还能作为车辆的动力轮,同时,无需对车轮轮辋进行改造便可安装,是有待解决的技术问题。
技术实现要素:本发明所要解决的技术问题是提供一种带气缸的真空轮胎内置爆胎应急装置,安装它的车辆在发生爆胎时,车身重心倾斜程度小,且爆胎车轮还能作为车辆的动力轮,同时,无需对车轮轮辋进行改造便可安装。为解决上述技术问题,本发明采用的技术方案为:一种带气缸的真空轮胎内置爆胎应急装置,包括由两个或两个以上主体圆弧连接构成的一个圆筒,相邻所述主体圆弧之间通过连接结构可拆卸地固定连接;每一个所述主体圆弧上至少设有一个气缸,所述气缸包括缸筒、活塞、活塞杆、导向套,所述缸筒的后端为密闭端,缸筒的后端固定安装在主体圆弧上面向圆心的一侧;所述活塞安装在缸筒内,所述导向套固定安装在缸筒的前端,所述活塞杆的后端从导向套中穿过并伸入缸筒内与活塞相连,所述活塞杆的前端固定安装有摩擦垫片;所有气缸的缸筒上均设有气孔,相邻缸筒的气孔通过气管相连;至少有一个气缸的缸筒上设有一个气门嘴。进一步,所述主体圆弧上设有固定螺杆,所述固定螺杆位于主体圆弧上面向圆心的一侧;所述缸筒的后端设有与之一体铸造的固定座,所述固定座上设有与固定螺杆相对应的通孔;所述固定螺杆穿过所述通孔与固定螺母配合旋接,所述缸筒通过固定座、固定螺杆、固定螺母可拆卸地固定安装在主体圆弧上。替代地,所述缸筒的后端与所述主体圆弧焊接连接或一体铸造。进一步,所述气孔、气门嘴均设于缸筒上靠近其后端的一侧。进一步,所述主体圆弧的两端设有连接螺杆,所述连接螺杆设于所述主体圆弧面向圆心一侧,所述连接螺杆与主体圆弧一体铸造或焊接连接;所述连接结构包括所述连接螺杆、连接圆弧、连接螺母,所述连接圆弧上设有供所述连接螺杆穿过的通孔;相邻主体圆弧通过所述连接螺杆、连接圆弧、连接螺母固定连接。进一步,所述主体圆弧包括位于中部的支撑段和位于两个端部的连接段;所述主体圆弧的径向厚度于所述连接段与所述支撑段的连接处有阶跃,所述连接段的径向厚度比所述支撑段的径向厚度薄;所述连接螺杆设于所述连接段面向圆心一侧,所述连接螺杆与连接段一体铸造或焊接连接。本发明的积极效果在于:(1)该真空轮胎内置爆胎应急装置的圆筒可以制作得足够大,使得在发生爆胎时,车身重心倾斜程度较小。(2)该真空轮胎内置爆胎应急装置采用气缸作为连接圆筒和车轮轮辋的部件,向缸筒内充入高压气体后,高压气体推动活塞、活塞杆向前运动,活塞杆将摩擦垫片挤压在车轮轮辋上,使得整个爆胎应急装置与车轮轮辋间不至发生相对滑动,从而使得爆胎车轮仍然能作为车辆的动力轮。(3)该真空轮胎内置爆胎应急装置采用气缸连接圆筒和车轮轮辋,整个爆胎应急装置的安装和拆卸通过充气和放气来实现,无需对车轮轮辋进行任何改造。(4)安装该爆胎应急装置的车辆发生爆胎后,由气缸内的高压气体撑起车身,这使得车辆行驶更平稳舒适。附图说明图1为实施例一的结构示意图。图2为图1所示实施例一的局部放大图。图3为图1所示实施例一沿A-A的剖视图。图4为实施例二的结构示意图。图5为图4所示实施例二的局部放大图。图6为图4所示实施例二沿B-B的剖视图。具体实施方式以下结合附图及实施例对本发明作进一步说明。实施例一如图1、图2、图3所示,本实施例包括由三个主体圆弧2连接构成的一个圆筒,相邻主体圆弧2之间通过连接结构可拆卸地固定连接。主体圆弧2的两端设有连接螺杆(未标示),连接螺杆(未标示)设于主体圆弧2面向圆心一侧,连接螺杆(未标示)与主体圆弧2一体铸造;所述连接结构包括连接螺杆(未标示)、连接圆弧4、连接螺母(未标示),连接圆弧4上设有供连接螺杆(未标示)穿过的通孔(未画出);相邻主体圆弧2通过连接螺杆(未标示)、连接圆弧4、连接螺母(未标示)固定连接。每一个主体圆弧2上设有两个气缸1,气缸1包括缸筒10、活塞11、活塞杆7、导向套12,缸筒10的后端为密闭端,缸筒10的后端设有与之一体铸造的固定座5,固定座5上设有通孔(未画出);主体圆弧2上设有固定螺杆(未标示),固定螺杆(未标示)位于主体圆弧2上面向圆心的一侧;固定螺杆(未标示)穿过固定座5上的通孔(未画出)与固定螺母(未标示)配合旋接,缸筒10通过固定座5、固定螺杆(未标示)、固定螺母(未标示)可拆卸地固定安装在主体圆弧2上。活塞11安装在缸筒10内,导向套12固定安装在缸筒10的前端,活塞杆7的后端从导向套12中穿过并伸入缸筒10内与活塞11相连,活塞杆7的前端固定安装有摩擦垫片8,摩擦垫片8的形状与车轮轮辋形状相适应,使得摩擦垫片8能与车轮轮辋紧密贴合。所有气缸1的缸筒10上均设有气孔6,相邻缸筒10的气孔6通过气管3固定相连;所有气缸1中有一个的缸筒10上设有一个气门嘴9。气孔6、气门嘴9均设于缸筒10上靠近其后端的一侧。实施例二如图4、图5、图6所示,本实施例包括由三个主体圆弧2连接构成的一个圆筒,相邻主体圆弧2之间通过连接结构可拆卸地固定连接。主体圆弧2包括位于中部的支撑段2-1和位于两个端部的连接段2-2;主体圆弧2的径向厚度于连接段2-2与支撑段2-1的连接处有阶跃,连接段2-2的径向厚度比支撑段2-1的径向厚度薄;连接段2-2面向圆心一侧设有连接螺杆(未标示),连接螺杆(未标示)与连接段2-2一体铸造而成。所述连接结构包括连接螺杆(未标示)、连接圆弧4、连接螺母(未标示),连接圆弧4上设有供连接螺杆(未标示)穿过的通孔(未画出);相邻主体圆弧2通过连接螺杆(未标示)、连接圆弧4、连接螺母(未标示)固定连接。每一个主体圆弧2上设有两个气缸1,气缸1包括缸筒10、活塞11、活塞杆8、导向套6,缸筒10的后端为密闭端,缸筒10的后端固定安装在主体圆弧2上面向圆心的一侧;缸筒10的后端与主体圆弧2一体铸造而成。活塞11安装在缸筒10内,导向套6固定安装在缸筒10的前端,活塞杆8的后端从导向套6中穿过并伸入缸筒10内与活塞11相连,活塞杆8的前端固定安装有摩擦垫片7,摩擦垫片7的形状与车轮轮辋形状相适应,使得摩擦垫片7能与车轮轮辋紧密贴合。所有气缸1的缸筒10上均设有气孔5,相邻缸筒10的气孔5通过气管3固定相连;所有气缸1中有一个的缸筒10上设有一个气门嘴9。气孔5、气门嘴9均设于缸筒10上靠近其后端的一侧。下面结合实施例二说明本发明的工作原理及使用方法。安装时,首先将气缸1中的气体放出,使活塞杆8尽量缩入缸筒10内,并将气管3拆下,然后,将三个主体圆弧2逐次放入外胎内,并在外胎内用连接圆弧4将三个主体圆弧2连接成一个圆筒,而后再用气管3将相邻气孔5连接起来。待将外胎一侧的胎唇安装到车轮轮辋上后,通过气门嘴9向气缸1内充气。由于所有的气缸1均由气管3串联起来了,故所有气缸1内的气压相同,充气时,所有气缸1的活塞杆8均被向前推出。待摩擦垫片7被挤压得与车轮轮辋结合得足够紧密,气缸1内的气压达到预定值后,停止充气。最后,将外胎的另一侧胎唇安装到车轮轮辋上。拆卸时,先将外胎内的气体放出,将外胎一侧胎唇卸出,然后,通过气门嘴对所有气缸1进行放气,同时,通过外胎挤压气缸1,使得所有气缸1的活塞杆8缩入缸筒10内,最后,拆下气管3,将主体圆弧2逐个拆卸下来。由于受缸筒10内高压气体的作用,摩擦垫片7能与车轮轮辋结合得十分紧密,整个爆胎应急装置十分牢靠地固定在车轮轮辋的外侧,如此,当发生爆胎时,该爆胎应急装置撑起车身,避免车子发生危险。