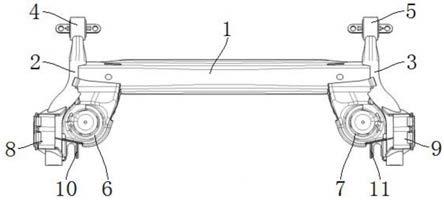
[0001]
本实用新型涉及汽车底盘,具体涉及一种汽车扭力梁后轴。
背景技术:[0002]
汽车扭力梁后轴具有结构平、重量轻、造价低、易于维护等优点,因此广泛应用于经济型车辆。但它的操控稳定性及乘坐舒适性差于独立悬架,因此较少应用于中高端车辆。
[0003]
绝大部分的汽车扭力梁后轴拥有相似的组成,是由衬套安装管、纵臂、横梁、弹簧托盘、车轮支架等焊接成的一个整体件。作为由多个零部件焊接构成的大件,扭力梁后轴难以实现平台化,其零部件难以通用于不同的后扭力梁轴。不同车型对扭力梁后轴的载荷、布置、性能等要求不同,因此需要为每款车型重新设计扭力梁后轴,并开发制作相应的模具工装。这种逐车设计扭力梁后轴的方法耗时长、花费高。
[0004]
如何使扭力梁后轴的零部件及模具工装能覆盖不同的轴载、布置及性能要求是本领域工程人员亟待解决的技术问题。
技术实现要素:[0005]
本实用新型的目的是提供一种汽车扭力梁后轴,其具有较高的通用性,即能够在通用大部分零部件的情况下,满足各种载荷、布置及性能要求;能够极大的缩短后轴的开发时间、缩减开发费用,且不用重开模具,能够大大降低生产成本。
[0006]
本实用新型所述的一种汽车扭力梁后轴,包括后轴本体,所述后轴本体包括横梁、中部与该横梁的左端焊接的左纵臂、中部与所述横梁的右端焊接的右纵臂、与所述左纵臂的前端配合连接的左衬套安装管、与所述右纵臂的前端配合连接的右衬套安装管、与所述横梁左端部和左纵臂中后部焊接的左弹簧托盘、与所述横梁右端部和右纵臂中后部焊接的右弹簧托盘、焊接在左纵臂后部的左车轮支架、焊接在右纵臂后部的右车轮支架,其特征在于:所述左纵臂具有依次相连的左前段、左中段、左连接段、左后段,所述左中段和左后段均为平直的管状结构,所述横梁的左端与左纵臂的左中段焊接,所述左车轮支架与左纵臂的左后段焊接;所述右纵臂具有依次相连的右前段、右中段、右连接段、右后段,所述右中段和右后段均为平直的管状结构,所述横梁的右端与右纵臂的右中段焊接,所述右车轮支架与右纵臂的右后段焊接。
[0007]
进一步,所述左纵臂的左前段、右纵臂的右前段均从后至前逐渐收窄。
[0008]
进一步,所述横梁为长条状,且其截面呈开口向下的u形;所述横梁的左端部内固定连接有左横梁加强板、右端部内固定连接有右横梁加强板。
[0009]
进一步,所述左横梁加强板的右端部高于其左端部,且其两侧分别设有翻边;所述左横梁加强板通过其右端部焊接在所述横梁左端部的顶部下面、通过其两侧的翻边焊接在所述横梁的左端侧面;所述右横梁加强板的左端部高于其右端部,且其两侧分别设有翻边;所述右横梁加强板通过其左端部焊接在所述横梁右端部的顶部下面、通过其两侧的翻边焊接在所述横梁的右端侧面。
[0010]
进一步,所述后轴本体还包括左减震器支架和右减震器支架,所述左减震器支架的外侧与左纵臂的左后段焊接、前部与左弹簧托盘焊接,所述右减震器支架的外侧与右纵臂的右后段焊接、前部与右弹簧托盘焊接。
[0011]
进一步,所述左纵臂和右纵臂均为管材预弯冲压成型。
[0012]
进一步,所述横梁为板材冲压成型,其中部高于其两端部。
[0013]
本实用新型有益的技术效果:
[0014]
1.能够实现不同轴载:后轴本体最高能承受1000kg的满载轴载,并向下兼容其它较小轴载。
[0015]
2.能够实现不同扭转刚度:通过改变左横梁加强板和右横梁加强板的长度、厚度等几何尺寸,能够改变后轴本体的扭转刚度,实现不同的扭转刚度。
[0016]
3.能够实现不同轮距:通过激光切割出不同长度的横梁、更换不同横向长度的左车轮支架和右车轮支架,能够实现不同轮距的调节。
[0017]
4.能够实现不同衬套安装点距离:通过激光切割出不同长度的横梁,能够实现对左衬套安装点和右衬套安装点的距离调节。
[0018]
5.能够实现不同拖距:该拖距指衬套安装点及轮心点在车辆纵轴方向的距离。通过对左纵臂和右纵臂进行激光切割实现其长度的调节、调节左车轮支架在左纵臂左后段上的安装位置和右车轮支架在右纵臂右后段上的安装位置,能够实现不同的拖距。
[0019]
6.能够实现不同扭转中心位置:后轴本体扭转中心位置主要受横梁剪切中心位置的影响,通过对左纵臂左前段和右纵臂右前段进行激光切割实现其长度的调节,并进一步调节横梁在左纵臂左中段和右纵臂右中段上的安装位置,能够实现不同的扭转中心位置。
[0020]
7.能够实现不同衬套布置形式:通过对左纵臂、右纵臂的前端进行激光切割形成不同大小和方向的切口,能够与多种衬套搭配,安装在不同下车体中。
附图说明
[0021]
图1是本实用新型的结构示意图;
[0022]
图2是横梁的结构示意图之一;
[0023]
图3是横梁的结构示意图之二;
[0024]
图4是左纵臂的结构示意图;
[0025]
图5是左横梁加强板的结构示意图;
[0026]
图6是右横梁加强板的结构示意图。
[0027]
图中:1-横梁,2-左纵臂,3-右纵臂,4-左衬套安装管,5-右衬套安装管,6-左弹簧托盘,7-右弹簧托盘,8-左车轮支架,9-右车轮支架,10-左减震器支架,13-右减震器支架;
[0028]
11-左横梁加强板,12-右横梁加强板;
[0029]
21-左前段,22-左中段,23-左连接段,24-左后段。
具体实施方式
[0030]
以下结合附图和实施例对本实用新型做详细说明。
[0031]
参见图1至图6所示的一种汽车扭力梁后轴,包括后轴本体,所述后轴本体包括横梁1、中部与该横梁1的左端焊接的左纵臂2、中部与所述横梁1的右端焊接的右纵臂3、与所
述左纵臂2的前端配合连接的左衬套安装管4、与所述右纵臂3的前端配合连接的右衬套安装管5、与所述横梁1左端部和左纵臂2中后部焊接的左弹簧托盘6、与所述横梁1右端部和右纵臂3中后部焊接的右弹簧托盘7、焊接在左纵臂2后部的左车轮支架8、焊接在右纵臂3后部的右车轮支架9,其特征在于:所述左纵臂2具有依次相连的左前段21、左中段22、左连接段23、左后段24,所述左中段22和左后段24均为平直的管状结构,所述横梁1的左端与左纵臂2的左中段22焊接,所述左车轮支架8与左纵臂2的左后段24焊接;所述右纵臂3具有依次相连的右前段、右中段、右连接段、右后段,所述右中段和右后段均为平直的管状结构,所述横梁1的右端与右纵臂3的右中段焊接,所述右车轮支架9与右纵臂3的右后段焊接。左弹簧托盘6、右弹簧托盘7用于支撑减震器弹簧的下端;左车轮支架8的内侧下部与左纵臂2的左后段24焊接、外侧用于连接制动器总成,右车轮支架9的内侧下部与右纵臂3的右后段焊接、外侧用于连接制动器总成。将左纵臂2的左中段22、右纵臂3的右中段设计成平直段,能够使得横梁1在焊接时,可根据需求选择其相对于左纵臂2和右纵臂3的前后焊接位置。将左纵臂2的左后段24、右纵臂3的右后段设计成平直段,能够使得左车轮支架8和右车轮支架9在焊接时,可根据需求选择其相对于左纵臂2和右纵臂3的前后焊接位置。有利于在不同布置及性能要求下实现车轮支架、横梁及纵臂的通用化。横梁1的两端通过激光切割成型,相比传统的落料,激光切割具有更好的精度,使搭接的焊缝具有更好的耐久性能;同时,仅需使用同一套横梁模具,横梁的长度通过激光切割便能够灵活控制,即能够切割出不同长度的横梁,进一步实现不同的轮距、不同衬套安装点距离。
[0032]
所述左纵臂2的左前段21、右纵臂3的右前段均从后至前逐渐收窄。左衬套安装管4焊接在左纵臂2的前端,即左衬套安装管4通过其后部焊接在左前段21的前端部;右衬套安装管5焊接在右纵臂3的前端,即右衬套安装管5通过其后部焊接在右前段的前端部。左衬套安装管4和右衬套安装管5的内部压入衬套,后轴本体通过衬套与下车体相连。原有的左纵臂和右纵臂为冲压落料成型,不同的车型需新开模具。本申请的左纵臂2和右纵臂3不用新开模具,仅需对左纵臂2、右纵臂3的前端和后端均采用激光切割,通过激光切割的方式能够得到不同长度的左纵臂2和右纵臂3;由于左纵臂2的左前段21、右纵臂3的右前段均从后至前逐渐收窄,通过对不同位置的左前段21和右前段进行切割,能够实现与不同尺寸衬套安装管的搭接;同时通过对左纵臂2、右纵臂3前端切口角度的调节,能够实现衬套安装管不同的安装角度,进一步实现不同的操控稳定性及乘坐舒适性。
[0033]
所述横梁1为长条状,且其截面呈开口向下的u形;所述横梁1的左端部内固定连接有左横梁加强板11、右端部内固定连接有右横梁加强板12。左横梁加强板11、右横梁加强板12能够增加横梁1的刚度。
[0034]
所述左横梁加强板11的右端部高于其左端部,且其两侧分别设有翻边;所述左横梁加强板11通过其右端部焊接在所述横梁1左端部的顶部下面、通过其两侧的翻边焊接在所述横梁1的左端侧面;所述右横梁加强板12的左端部高于其右端部,且其两侧分别设有翻边;所述右横梁加强板12通过其左端部焊接在所述横梁1右端部的顶部下面、通过其两侧的翻边焊接在所述横梁1的右端侧面。横梁1通过左横梁加强板11与左纵臂2构成三角形的加强结构,横梁1通过右横梁加强板12与右纵臂3构成三角形的加强结构,能够提高后轴本体的整体强度和刚度。通过改变左横梁加强板和右横梁加强板的长度、厚度等几何尺寸,能够改变后轴本体的扭转刚度,实现不同的扭转刚度。
[0035]
所述后轴本体还包括左减震器支架10和右减震器支架13,所述左减震器支架10的外侧与左纵臂2的左后段24焊接、前部与左弹簧托盘6焊接,所述右减震器支架13的外侧与右纵臂3的右后段焊接、前部与右弹簧托盘7焊接。左减震器支架10和右减震器支架13用于支撑减震器下端。
[0036]
所述左纵臂2和右纵臂3均为管材预弯冲压成型。左纵臂2和右纵臂3主要起到车轮到车身之间的受力传递作用。
[0037]
所述横梁1为板材冲压成型,其中部高于其两端部。横梁1能够实现悬架的扭转性能。
[0038]
本实用新型能够具有较高的通用性,即在通用大部分零部件的情况下,满足各种载荷、布置及性能要求,涵盖a0、a及b级车辆;极大的缩短了后轴的开发时间、缩减了开发费用,且不用重开模具,大大降低了生产成本。