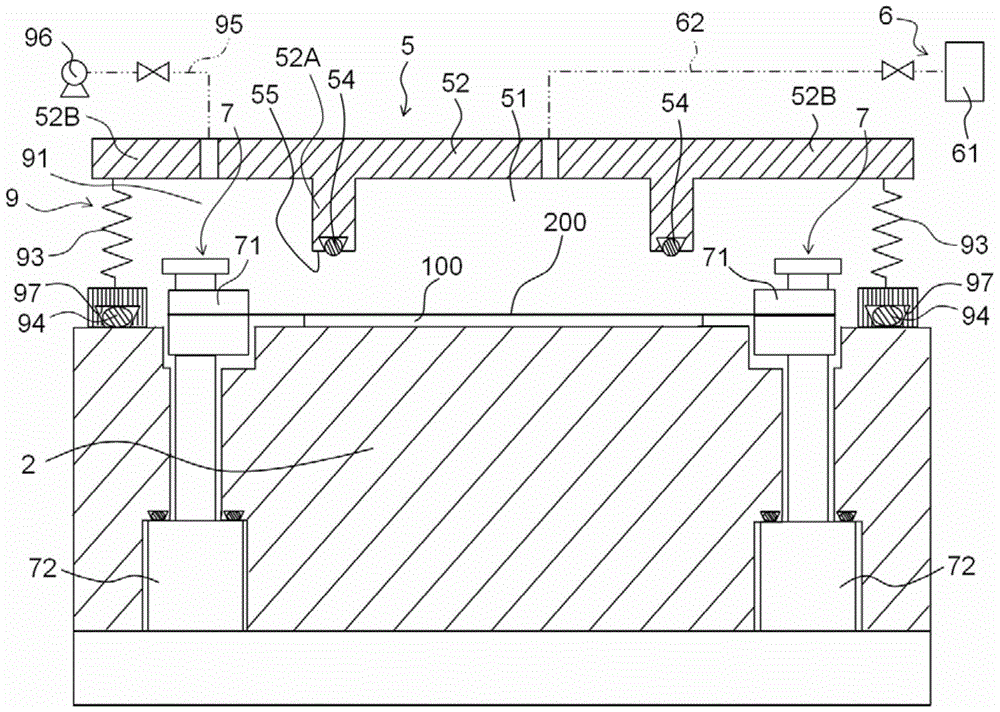
本发明涉及一种用于将模具的图案连续地转印到被成型物的压印装置以及压印方法。
背景技术:近年来,作为一种形成微指令、纳米指令的超微细的图案的方法,纳米压印技术受到注目。这是一种将具有微细图案的模具压向树脂等被成型物,并将该图案转印到被成型物的方法(例如,参照专利文献1)。在这种转印技术中,为了实现转印面积的扩大,考虑使用一种利用流体压力的压印装置(例如,参照专利文献2)。专利文献1:国际公开号WO2004/062886专利文献2:日本国特开2009-154393发明的内容(发明要解决的课题)这里,在以往的压印装置中,存在于模具与被成型物之间的气体在转印时形成气泡,存在转印不良的问题。因此,在所述专利文献2记载的压印装置中,设置有脱气机构,其用于对模具与被成型物的周围环境进行减压,从而除去模具与被成型物之间的气体。然而,在被成型物为转印面积大的物品或者是类似透镜的曲面这样的非平面状物的情况下,仅仅通过设置脱气机构,有时不能充分除去存在于模具与被成型物之间的气体。为此,本发明的目的在于提供一种能够确实地除去模具与被成型物之间的气体的压印装置以及压印方法。(用于解决课题的手段)为达成上述目的,本发明的压印装置是用于将模具的成型图案转印到被成型物的压印装置,其特征在于包括:加压部,其具有用于利用流体对所述模具与所述被成型物进行加压的加压室;载物台,其支撑受到所述加压部的压力的所述模具以及所述被成型物;加压机构,其用于调节所述加压室内的流体的压力;减压部,其具有用于对所述模具与所述被成型物的周围环境进行减压的减压室;以及分离机构,其用于在所述减压室内使所述模具与所述被成型物分离。在这种情况下,较佳的是,具有向空隙喷射流体的流体喷射机构,所述空隙通过所述分离机构在所述模具与所述被成型物的端部形成。另外,较佳的是,所述加压部包括:加压室用箱体,其与所述模具、所述被成型物一起形成所述加压室;密闭机构,其将所述加压室用箱体与所述模具、所述被成型物之间密闭;以及开闭机构,其用于使所述加压用箱体与所述模具之间或所述加压用箱体与所述被成型物之间开闭,或者,所述加压部也可以包括:具有可挠性的膜,其被配置于与所述模具或所述被成型物接触的面;以及加压室用箱体,其与所述膜一起形成所述加压室。另外,还存在具备用于调节所述模具或者所述被成型物的温度的调温机构、以及向所述被成型物照射规定波长的光的光照射机构的情况。另外,本发明的压印方法是用于将模具的成型图案转印到被成型物的压印方法,该压印方法的特征在于,包括:减压工序,用于在使所述模具与所述被成型物分离后的状态下,对所述模具与所述被成型物的周围环境进行减压;密接工序,用于使所述模具与所述被成型物之间紧密连接;以及加压工序,用于在将所述模具与所述被成型物之间紧密连接后的状态下,利用流体进行加压。附图说明图1是表示本发明的压印装置的局部剖视图。图2是表示本发明的压印装置的局部剖视图。图3是表示本发明的压印装置的局部剖视图。图4是表示涉及本发明的流体喷射机构的局部剖视图。图5是表示本发明的另一压印装置的局部剖视图。图6是表示本发明的另一压印装置的局部剖视图。符号的说明2载物台3流体喷射机构5加压部6加压机构7分离机构9减压部51加压室52加压室用箱体54密闭机构91减压室100模具200被成型物具体实施方式如图1至图3所示,本发明的压印装置为用于将模具100的成型图案转印到被成型物200的压印装置,该压印装置主要包括:加压部5,其具有通过流体对模具100与被成型物200进行加压的加压室51;载物台2,其用于支撑受到加压部5的压力的模具100以及被成型物200;加压机构6,其用于调节加压室51内的流体的压力;减压部9,其具有用于对模具100与被成型物200的周围环境进行减压的减压室91;以及分离机构7,其用于在减压室91内使模具100与被成型物200分离。另外,在本说明书中,所谓的模具100是指采用“镍等金属”、“陶瓷”、“玻璃状碳等碳素材料”、“硅”等形成,且在该模具100的一端面(成型面)具有规定的图案。该图案能够通过在所述成型面实施精密机械加工形成。另外,该图案也能够通过以下方法形成:通过对硅基板等实施蚀刻等半导体微细加工技术来形成,或者采用电气铸造(电沉积)法、例如镀镍法在硅等基板等的表面实施金属喷镀并将该金属喷镀层剥离而形成。另外,也可以使用利用压印技术制作的树脂制成的模具。在这种情况下,模具也可以以成为相对于被成型物的被成型面具有可挠性的膜状的方式形成。当然,只要能够形成微细图案,模具100的材料及其制造方法并没有被特别限定。另外,形成于模具100的成型图案不仅仅是由凹凸形成的几何形状,也包括:例如用于类似具有规定的表面粗糙度的镜面状态的转印这样、将规定的表面状态进行转印的图案,以及用于转印具有规定的曲面的透镜等光学元件的图案。另外,成型图案的在平面方向上的凸部的宽度或凹部的宽度的最小尺寸形成为100μm以下、10μm以下、2μm以下、1μm以下、100nm以下、10nm以下等各种大小。另外,深度方向的尺寸形成为10nm以上、100nm以上、200nm以上、50nm以上、1μm以上、10μm以上、100μm以上等各种大小。另外,被成型物200是指,例如通过热塑性树脂或含有聚合反应性基的化合物类的聚合反应(热硬化、或者光硬化)制作的树脂。作为热塑性树脂,可以使用环状烯烃开环聚合/氢素添加体(COP)或环状烯烃共聚物(COC)等环状烯烃系树脂(cyclicolefinresin),丙烯酸树脂(acrylicresin)、聚碳酸酯(polycarbonate)、乙烯基醚树脂(vinyletherresin)、全氟烷氧基烷烃(PFA,Perfluoroalkoxyalkane)及聚四氟乙烯(PTFE,Polytetrafluoroethylene)等含氟树脂,以及聚苯乙烯(polystyrene),聚酰亚胺系树脂(polyimideresin),聚酯系树脂(polyesterresin)等。作为通过含有聚合反应性基的化合物类的聚合反应(热硬化或者光硬化)制作的树脂,可以使用包含环氧基(epoxide)的化合物、(甲基)丙烯酸酯化合物((meth)acrylicestercompound)、乙烯基化合物(vinylethercompound)、如双烯丙基纳迪克酰亚胺(bis-allyl-nadi-imide)化合物类含有乙烯(vinyl)基、丙烯(allyl)基等不饱和碳氢基德化合物类等。在这种情况下,也可以为了热聚合反应而单独使用含有聚合反应性基的化合物类,也可以为了提高热硬化性来添加使用热反应性的引发剂。进一步,也可以添加光反应性的引发剂并通过光照射进行聚合反应来形成成型图案。作为热反应性的自由基引发剂(radicalinitiator),可以适当使用有机过氧化物、偶氮化合物(azocompound),作为光反应性的自由基引发剂,可以适当使用苯乙酮(acetophenone)衍生物,二苯甲酮(benzophenone)衍生物,苯偶姻乙醚(benzoinether)衍生物,咕吨酮(xanthone)衍生物。另外,就反应性单体而言,也可以在无溶剂的情况下使用,也可以先溶解于溶媒中而在涂布后进行脱溶媒之后使用。另外,作为被成型物200,可以使用形成为具有可挠性的膜状的部件、或者在采用硅等无机化合物或金属制成的基板上形成为层状的部件。另外,被成型物200不限于平面状的部件,也包括例如透镜这样的被成型面为曲面的部件(参照图5、图6)。另外,在图1中,在载物台2侧配置有模具100,在加压部5侧配置有被成型物200,但也可以在载物台2侧配置被成型物200,在加压部5侧配置模具100。加压部5是具有用于通过流体直接地或间接地对模具100与被成型物200进行加压的加压室51的部件,例如可以包括:与模具100或被成型物200一起形成加压室51的加压室用箱体52、密闭该加压室用箱体52与模具100或被成型物200之间的密闭机构54、以及开闭所述加压用箱体52与所述模具100或所述被成型物200之间的开闭机构(未图示)。在图3中,表示通过加压室用箱体52与被成型物200形成加压室51的情况。加压室用箱体52形成为具有开口部的有底筒状,通过模具100或被成型物200来关闭开口部,由此,形成作为被密闭的空间的加压室51。该开口部形成为至少比被转印到被成型物200的图案区域更大。就材质而言,只要是相对于压印工艺中的成型条件具有耐压性、耐热性的材质即可,例如可以采用碳素钢等钢材或不锈钢SUS(StainlessSteel)等金属。密闭机构54是为了使加压室51密闭而将加压室用箱体52与模具100或被成型物200之间紧密连接的机构。例如,如图1所示,在作为密闭机构54来准备O型环的同时,只要在加压室用箱体52的侧壁52A的载物台侧端部形成比O型环的截面直径小的凹状的槽55,并将O型环配置于该槽即可。由此,利用加压室用箱体52与载物台2来夹持模具100或被成型物200,并且使加压室用箱体52与被成型物200紧密连接,因此能够将加压室51密闭。另外,即使加压室用箱体52与模具100或被成型物200之间存在倾斜,但只要其平行度在O型环的变形量以内,就能够切实地将加压室51密闭。虽然未图示,但开闭机构是通过使加压室用箱体52与模具100或被成型物200彼此接近或分离来使加压室51开闭的机构,可以使用例如利用液压式或空压式缸体来移动加压室用箱体52的机构、或者利用电气马达与滚珠丝杠来移动加压室用箱体52的机构等。另外,在这样来形成加压部5的情况下,优选形成加压室51的模具100或被成型物200是具有可挠性的膜状的部件。如此,能够对被成型面通过流体施加均匀的压力。另外,虽然未图示,但作为加压部5的另外一例,也可以以包括在与模具100或被成型物200接触的面配置的具有可挠性的膜、以及与该膜一起形成加压室的加压室用箱体的方式形成。由此,能够经由膜来间接地将加压室的压力施加到模具100或被成型物200。作为具有可挠性的膜的材料,可以使用例如树脂或薄的金属、橡胶等弹性体等。另外,在加压室侧设置相对于被成型物200来放射规定波长的光的光源的情况下,作为该膜,选择使用可供该光透过的材料。膜的厚度形成为10mm以下、较佳的是形成为3mm以下、更佳的是形成为1mm以下。与之前的例子相同,加压室用箱体形成为具有开口部的有底筒状。另外,通过粘合剂等使该加压室用箱体与膜紧贴,将加压室内密闭。另外,与上述的例子相同,也可以通过密闭机构来将该加压室用箱体与膜密闭。载物台2为用于支撑受到加压部5的压力的模具100及被成型物200的部件。载物台2的与模具100或被成型物200接触侧的面形成为足够宽且圆滑。材质只要相对于压印工艺的成型条件具有耐压性、耐热性即可,可以采用例如碳素钢等钢材或SUS等金属。另外,在自载物台2侧对模具100或被成型物200加热的情况下,优选使用金属等导热性高的材质。另外,在从加压室51侧对模具100或被成型物200加热的情况下,为了防止热量在载物台2侧散逸,也可以使用导热性低的材质,但为了防止出现加热不均,优选的是,载物台的表面使用导热性高的材质形成。另外,在光压印工艺中,在光源配置在载物台2侧的情况下,采用玻璃等透明材料即可。另外,为了防止在被成型物200产生不需要的转印痕迹,也可以使模具100与载物台2形成为一体。例如以往,在通过电气铸造形成图案后,仅切取出图案部分来使用,但也能够不用切取图案地维持原状来使用。加压机构6只要是能够将加压室51内的流体的压力调整到可将模具100的图案转印到被成型物200的压力的机构即可,例如,可以将加压室用气体给排流路62连接到加压室用箱体52,经由加压室用气体给排流路62来向加压室51供给或从加压室51排出空气或惰性气体等气体。在所述气体的供给中,可以使用带有被压缩的气体的气瓶(Bombe)或者压缩机等气体供给源61。另外,在气体的排气中,虽未图示,但通过脱气阀的开闭来排放气体即可。另外,也可以适当地设置安全阀等。减压部9具有用于对模具100与被成型物200的周围环境、尤其是模具100与被成型物200之间的环境进行减压的减压室91,由此,能够除去存在于模具100、被成型物200以及载物台2之间的气体,能够均匀地按压模具100与被成型物200。作为减压部9,可以使用将模具100及被成型物200中的任一方或双方包含在内的减压室91、与减压室连接的减压室用气体给排流路95、以及经由减压室用气体给排流路95来排放减压室91内的气体的减压用泵96。例如,如图1所示,减压室91包括加压室用箱体52、从加压室用箱体52的上部水平延伸的凸缘部52B、从凸缘部52B垂下来覆盖加压室用箱体52的蛇纹管93、将该蛇纹管93与载物台2之间密闭的密封部件94、以及载物台2。因此,加压室51也成为减压室的一部分。另外,密封部件94配置在蛇纹管93的形成于载物台2侧的凹状的槽97。而且,减压用泵96只要是能够将减压室减压到在将被成型物200压向模具100的情况下不会发生转印不良的范围内的部件即可。另外,毋庸赘言,蛇纹管93、密封部件94具有能够耐受减压时的外力的强度。另外,能够使上述加压室用气体给排流路62与减压室用气体给排流路95通用。在这种情况下,首先,在开放了加压室51的状态下,将减压室91及加压室51的气体排出并除去减压室91内的气体,接着,在闭锁了加压室51后,只要将气体供给到加压室51并相对于模具100来按压被成型物200即可。另外,在利用加压室用箱体与具有可挠性的膜形成加压部5且利用粘合剂等将该加压室用箱体与膜之间紧贴的情况下,也可以设置减压用压力调节机构(未图示),该减压用压力调节机构用于在减压时使加压室51内与减压室91内压力相同。作为减压用压力调节机构,可以设置例如经由开闭阀连接加压室51与减压室91的连通路。由此,通过在减压时开放开闭阀,能够使加压室51与减压室91压力相同。分离机构7用于在减压室91内使模具100与被成型物200之间在减压时分离,并切实地除去模具100与被成型物200之间的气体。由此,即使转印面积变大,也能够切实地除去气体。分离机构7只要是在模具100与被成型物200之间形成空隙150的部件即可,例如,如图1所示,可以采用用于夹持模具100或被成型物200的端部的夹持部71、以及使该夹持部71在使模具100与被成型物200分离的方向上移动的升降机构72形成。作为夹持部71,能够使用例如施加弹簧等的弹性力来进行夹持的夹子等。作为升降机构72,可以使用液压式或空压式的缸体来使该夹持部71进行移动的部件、或使用电动马达与滚珠丝杠来使该夹持部71进行移动的部件等。而且,如图4所示,本发明的压印装置也可以设置朝向模具100与被成型物200的端部喷射流体的流体喷射机构3。由此,能够利用分离机构7在转印后紧密连接的模具100与被成型物200的端部形成空隙,并朝向该空隙喷射流体,由此来进行脱模。流体喷射机构3主要包括:向模具100与被成型物200之间喷射流体的喷射口31、调节从喷射口31喷射出的流体的流速的流速调节机构(未图示)、以及向喷射口31供给流体的流体供给源(未图示)。喷射口31能够形成为例如沿被成型物200的端部形成的缝隙状。缝隙的宽度可以根据模具100与被成型物200的接合力等来调节,只要采用例如宽度为0.2mm至0.5mm的缝隙即可。另外,也可以使用沿被成型物200的端部以适当的间隔设置有多个孔的多喷嘴。另外,喷射口31可以与分离机构7独立地设置,也可以例如与上述夹持部11的下部形成为一体。而且,如图4所示,喷射口31优选设置在隔着被成型物200相向的位置。由此,从相向的位置喷射的流体在模具100与被成型物200之间的中央部相冲撞。这样,流体失去速度且从动压变为静压,冲击部的静压比被成型物200的上表面的压力要高,因此能够托起被成型物200。这样一来,由于喷出的高速流体的能量变换为静压,在瞬间会消除流体在壁面产生的剥落、涡流以及剪切力,因而能够防止被转印到被成型物200的图案受到损坏。另外,如果流体压力在模具100与被成型物200之间抵消,那么喷射口31当然也能够被设置在从3个方向或4个方向喷射流体的位置。流速调节机构只要是能够调节从喷射口31喷射的流体的流速的机构即可,例如可以使用通过压力与喷出时间来调节流速的部件。具体而言,可以是以50ms至300ms的脉宽喷射利用储压器(accumulator)储压至0.2至0.5MPa的流体的方式构成。作为流体供给源,可以使用将气体向喷射口31输送的空气压缩机或贮留被压缩的气体的气瓶等。调温机构未被图示,其通过加热或冷却被成型物来调节被成型物的温度。调温机构可以使用对被成型物直接地或间接地进行加热的加热机构、或者对被成型物直接地或间接地进行冷却的冷却机构。加热机构只要是能够将模具100及被成型物200中的任一方或双方加热到规定温度、例如被成型物200的玻璃转化温度以上或熔融温度以上的机构即可。而且,可以从载物台2侧加热被成型物200,也可以从加压室51侧加热被成型物200。例如,也可以在载物台2内设置加热器来从载物台2侧加热模具100或被成型物200。另外,也可以在加压室51设置通过例如陶瓷加热器或卤素加热器这样的、利用电磁波的放射来进行加热的放射热源,对模具100或被成型物200进行加热。而且,也可以使用加热后的液体或气体来进行加热。冷却机构只要是能够将模具100及被成型物200中的任一方或双方冷却到规定温度、例如低于被成型物200的玻璃转化温度的温度或低于熔融温度的温度即可。而且,可以从载物台2侧冷却被成型物200,也可以从加压室51侧冷却被成型物200。例如,可以使用在载物台2内设置冷却用水路来从载物台2侧冷却模具100或被成型物200的方式。另外,在用于光压印工艺的情况下,只要将能够对被成型物200放射规定波长的电磁波的光源配置于加压室51内即可。接着,对本发明的压印方法与本发明的压印装置的动作一起进行说明。本发明的压印方法为用于将模具100的成型图案转印到被成型物200的压印方法,该压印方法主要包括:在使模具100与被成型物200已分开的状态下,对模具100与被成型物200的周围环境进行减压的减压工序;将模具100与被成型物200之间紧密连接密接工序;以及在已将模具100与被成型物200之间紧密连接的状态下,通过流体进行加压的加压工序。在减压工序中,通过开闭机构来移动加压室用箱体52,使减压部9的密封部件94抵接于载物台2,并使减压室91密闭。另外,利用分离机构7使被成型物200脱离模具100。在这种状态下,使减压用泵96动作,对减压室91内进行减压来除去被成型物200与模具100之间的气体(参照图1或图5)。在密接工序中,利用分离机构7将被成型物200叠加至模具100上(参照图2)。接着,通过开闭机构来移动加压室用箱体52,使加压部5的密封部件54抵接于被成型物200来消除模具100与被成型物200之间的空隙(参照图3)。在加压工序中,从气体供给源61向加压室51供给气体,从而对被成型物200与模具100加压。此时,在热压印中,通过调温机构对被成型物200进行加热、冷却,并将模具100的成型图案转印到被成型物200。而且,在光压印中,将光源的光照射到被成型物200,来将模具100的成型图案转印到被成型物200。最后,进行脱模,使模具100从被成型物200脱离。由此,即使转印面积变大,也能够切实地除去模具100与被成型物200之间的气体,且能够切实地防止因气泡造成的转印不良的问题。