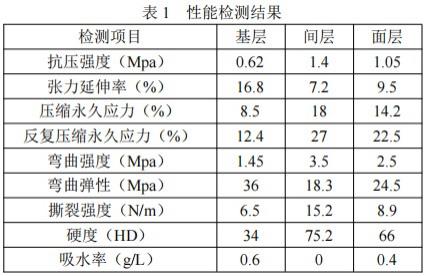
一种epp基复材抗震吸能汽车保险杠的制备方法
技术领域
1.本发明属于汽车发泡塑料部件技术领域,具体涉及一种epp基复材抗震吸能汽车保险杠的制备方法。
背景技术:2.汽车保险杠是吸收和缓和外界冲击力,防护车身前后部的安全装置。现在市场上大多数汽车采用塑料保险杠,汽车保险杠由外向内依次为外板、缓冲材料和横梁组成,外板和缓冲材料由塑料制成,横梁为冷轧薄板;其中,缓冲材料为缓冲撞击力防护车身的核心材料。塑料保险杠具有减轻车身重量、降低排放的优点,且具有良好的抗冲击性,还不易生锈,更加美观。
3.目前,塑料保险杠主要采用epp材质制成,epp是一种环保可降解的发泡塑料,通常为发泡聚丙烯珠粒,熔点在150℃左右,是一种新型抗压缓冲隔热材料,epp通过材料体积收缩和扩张,吸收并释放能量来达到抗压缓冲效果,epp的回弹性能够承受多次外力冲击。相比于其他材料还具有良好的耐应力开裂性能、隔热性能、隔音性能。
4.epp保险杠是多采用epp珠粒一体型腔模具冲压而成,主要依靠调节成型密度来控制产品质量,产品使用性能需要兼顾回弹性指标和硬度指标的平衡,即密度大硬度高,但回弹性差,变形修复能力差;而提高回弹性,则要降低密度,继而会降低硬度,影响耐磨性、耐刮擦、抗冲击抗撕裂强度。因此,单纯依靠epp制备保险杠,还具有材料特性的局限性,很难做性能上的综合突破。
5.但随着汽车行业技术水平的不断提高,人们对行驶安全的逐渐重视,对汽车保险杠的性能要求也不断的提出更高的要求。目前的epp保险杠在抗震吸能性能上的表现还有待提高,且长时间使用还易老化,会降低抗冲击的防护性,另外,整体压型由于要兼顾回弹性,因此其耐磨性能也较差,缩短使用寿命,耐撞性和耐冲击次数也有待提高。
技术实现要素:6.针对现有一体型腔模具冲压而成的epp保险杠存在着性能局限性,那以满足越来越高的使用安全性要求,其需要进一步提高抗震吸能性、抗老化、抗撞击和耐磨性的同时,还要兼顾回弹和修复性的问题,本发明提供一种epp基复材抗震吸能汽车保险杠的制备方法,分层制备,能够同时提高基层的回弹修复性,抗震吸能性和抗老化性;提高间层的强度,抗撞击性,抗震吸能性和抗老化性;提高面层的抗撞击性,耐磨性和抗老化性,进而达到综合提高保险杠的使用性能,延长使用寿命和撞击次数,提高保护效果。其具体技术方案如下:一种epp基复材抗震吸能汽车保险杠的制备方法,包括如下步骤:s1,预处理,以下s11、s12、s13为同时进行或先后进行:s11:基层epp珠粒预压膨胀:将基层epp珠粒进行四个阶段的预压,依次为:一次加压0.1~0.2bar,压时40~45min,泄压5~10min;二次加压2~3bar,压时5~5.5h,泄压5~10min;
三次加压3~3.5bar,压时40~50min,不泄压;四次降压1~2bar,压时70~80h,得到基层预压epp珠粒,备用;所述基层epp珠粒的球径为3~4mm;s12:面层epp珠粒预压膨胀:将面层epp珠粒进行五个阶段的预压,依次为:一次加压0.3~0.5bar,压时40~50min,泄压3~5min;二次加压3~3.5bar,压时6~7h,泄压3~5min;三次加压5~6bar,压时50~60min,不泄压;四次降压4~5bar,压时30~50min,不泄压;五次降压2~3bar,压时70~80h,得到面层预压epp珠粒,备用;所述面层epp珠粒的球径为1.5~2.5mm;所述面层epp珠粒在发泡制备时内含有纳米级纤维或微米级纤维,所述纳米级纤维和微米级纤维为玄武岩纤维、玻璃纤维和陶瓷纤维中的至少一种;所述纳米级纤维或微米级纤维在面层epp珠粒中的体积含量为5~10%;s13:间层eps珠粒预压膨胀:将间层eps珠粒进行六个阶段的预压,依次为:一次加压0.2~0.4bar,压时30~40min,泄压3~5min;二次加压2~3bar,压时4~5h,泄压10~20min;三次加压4~4.5bar,压时30~40min,不泄压;四次降压3.5~4bar,压时30~50min,不泄压;五次降压3~3.5bar,压时30~50min,不泄压;六次降压1.5~2.5bar,压时80~90h,得到间层预压eps珠粒,备用;所述eps珠粒为阻燃型eps,所述eps珠粒的球径为1~2mm;s2,初压成型,以下 s21、s22为同时进行或先后进行:s21:基层预压成型:将基层预压epp珠粒输送注入至基层模具中,并分布均匀充满基层模具型腔,然后锁膜并预热,之后对基层模具进行单面加热,使基层预压epp珠粒压融成型,得到基层型材;所述锁膜为锁紧固定基层模具,锁膜的压力为110~120bar;所述预热为通过蒸汽对基层模具进行预热,基层模具型腔的预热温度为50~60℃,预热时间2~5s;所述单面加热为通过蒸汽对基层模具进行穿透加热,基层模具型腔的加热温度为170~200℃,加热时间8~15s;所述单面加热为基层型材与间层型材的贴合面不充入蒸汽;s22:间层预压成型:将聚乙烯醇粉末与纤维分散于水中,加热至70~80℃,混合均匀得到浆料a;浆料a的成分质量配比为聚乙烯醇粉末∶纤维∶水=(8~10)∶(2~5)∶(10~12);再向浆料a中加入二氧化硅溶胶,混合得到浆料b,浆料b的成分质量配比为浆料a∶二氧化硅溶胶=20∶(3~8);将浆料b分散均匀注入至间层磨具中,然后将间层预压eps珠粒输送注入至基层模具中,并均匀浸渍于浆料b中,进行锁膜,锁紧固定基层模具挤压出多余浆料b后,进行加热,使间层预压eps珠粒压融成型,得到间层型材;所述纤维的直径为0.1~0.3mm,所述纤维长度为1~2mm;所述纤维为聚乙烯醇纤维、玄武岩纤维、玻璃纤维和陶瓷纤维中的至少一种;所述锁膜的压力为140~160bar;所述加热为通过电加热器对间层模具进行加热,加热温度为130~140℃,加热时间30~60s;s3,复压成型:将间层型材贴合于基层型材的前表面,进行组合型材,并将组合型材置于复压模具中,然后向间层型材前表面的复压模具型腔中输送注入面层预压epp珠粒,并分布均匀充满复压模具型腔的剩余空间,锁膜之后对复压模具进行局部面加热,使面层预压epp珠粒压融并与基层型材和间层型材进行熔接成型,得到保险杠型材;
所述锁膜为锁紧固定复压模具,锁膜的压力为140~160bar;所述局部面加热为通过电加热器对复压模具进行加热,加热温度为220~250℃,加热时间30~60s;所述局部面加热为基层型材的后表面不加热;s4,后处理:保险杠成型后再经降温冷却、脱模、烘烤定型后得到保险杠成品。
7.一种epp基复材抗震吸能汽车保险杠,采用上述方法进行制备,保险杠包括基层1、间层2和面层3,所述间层2夹设在基层1和面层3之间,所述间层2与基层1为组合扣接,所述基层1的前表面热压形成有若干列间隔排布的圆柱凹槽1.1和圆柱凸起1.2,所述面层3的内表面与圆柱凸起1.2的端面熔接,所述面层3的内表面与间层2为熔接;所述基层1的两端头直接与面层3的两端头熔接。
8.上述技术方案中,所述圆柱凹槽1.1和圆柱凸起1.2为两排以上。
9.上述技术方案中,所述圆柱凹槽1.1的直径小于圆柱凸起1.2的直径。
10.上述技术方案中,所述间层2的厚度为基层1厚度的1/(3~4)。
11.上述技术方案中,所述面层3的厚度大于等于间层2的厚度。
12.上述技术方案中,所述基层1的边缘和圆柱凸起1.2与面层3熔接,圆柱凸起1.2的高度大于等于间层2的厚度。
13.本发明的一种epp基复材抗震吸能汽车保险杠的制备方法,与现有技术相比,有益效果为:一、本发明方法基层采用四个阶段的预压方式对3~4mm的epp珠粒进行膨胀发泡,预压压力结合加压过程中进行泄压,有效提高大粒径epp珠粒的回弹性,针对基层的使用特性,提高保险杠的回弹修复性。
14.二、本发明方法面层采用1.5~2.5mm小粒径的epp珠粒,epp珠粒在发泡制备珠粒前参入适量的纳米级或微米级的增强纤维,能够有效提高面层的强度和抗撕裂性能,且不会影响成型均匀性;设计五个阶段的预压和泄压操作,能够提高小粒径的epp珠粒在热熔成型后的质量,结合增强纤维,进一步提高抗撞击性,整体面层为间层进行很好的分压,分散压力后,减少形变。
15.三、本发明方法间层采用1~2mm更小粒径的eps珠粒,提高整形硬度,设计六个阶段的预压和泄压操作,能够提高小粒径的eps珠粒在热熔成型后的质量,还能够较少吸水率。间层成型采用特殊成型工艺,制备纤维浆料,能够均匀分散纤维,防止纤维团聚造成质量不均;二氧化硅溶胶比表面积可达600m2/g,能够在热熔成型过程中黏连形成网膜结构,能够固定纤维,与纤维联合提高间层的强度和防撞性;二氧化硅溶胶与聚乙烯醇结合能够起到增稠、触变、补强作用,提高eps珠粒成型强度,且提高间层的耐高温性和耐低温性,提高抗老化性,延长使用保护寿命。本发明方法中设计的浆料配比是根据小粒径的eps珠粒和使用指标特性设计,过多或过少都会影响小粒径的eps珠粒的成型质量,过少会降低抗老化性、硬度和抗撞击性,过高则会影响eps珠粒的顺利成型,造成成型慢,易分层开裂的现象。
16.四、本发明设计填充小粒径的epp珠粒进行复压成型,面层热熔结合性更好,其中设计基层圆柱凸起穿过间层直接与面层融合,既能够实现间层与面层的结合,又能够实现基层与面层的结合,将间层很好的夹设在中间,整体结合度非常紧密,当受撞击后也不会发生分层断裂现象。在基层成型时,设计基层模具型腔的加热温度为170~200℃,温度较低,且
单面加热为基层型材与间层型材的贴合面不充入蒸汽,为了在结合面层时,基层前表面熔接性更好。
17.五、本发明设计间层的形状与基层前表面形状相适配,即间层填充了基层前表面的圆柱凹槽,使间层与基层的结合也更好,在受到撞击后不会发生两层分裂。间层的高强度能够很好提高抗撞击抗变形,也能够很好的分散撞击力,增大基层受理面积,减轻基层局部形变,进而基层恢复力更好,延长使用次数和寿命。
18.六、本发明方法在复压成型时,设计局部加热,基层型材的后表面不加热,能够在一定程度上保护基层型材的原始性能,减少降低回弹性修复性。
19.七、本发明设计间层对基层和面层进行一定程度的阻隔,相比于同材质的一体成型保险杠,能够大幅减少吸水率,提高抗老化性,延长使用保护寿命。
20.八、本发明设计保险杠的圆柱凹槽的直径小于圆柱凸起的直径,圆柱凸起的高度大于等于间层的厚度,能够提高基层与面层的接触面积,提高熔接质量,进而提高保险杠整体的抗拉强度和应力强度;设计间层的厚度为基层厚度的1/(3~4),能够很好的保证整体保险杠的回弹修复性,以及兼顾硬度和抗撞击性;面层的厚度大于等于间层的厚度,能后对间层起到很好的缓释作用力的作用;该保险杠的结构设计也是配合制备工艺进行设计,才能实现更好的使用性能。
21.九、本发明设计各层的成型压力和温度等参数,是根据层的厚度和材料性质以及需达到的指标要求而设计的,以实现层型材的品质以及层间结合品质,实现整体保险杠的使用效果,参数超范围会直接影响保险杠成型和使用性能,包括抗压强度、延伸率、压缩应力、弯曲强度、弹性、撕裂强度、硬度、吸水率等,以及成型的无过熟过生现象,有无缺料、是否多料、有无断裂现象。
22.综上,本发明保险杠整体检测结果及使用效果为:产品整体成型良好,无过熟过生现象,无缺料、多料、断裂现象;相比于现有基层同工艺一体成型的产品,使用性能大幅提高,具体表现在,基层和间层配合后提高了保险杠整体的抗震吸能性,间层的0吸水率阻隔辅助降低了基层吸水率,面层工艺也降低了面层的吸水率,配合间层阻隔,进一步减少吸水率,进而保险杠整体的抗老化性更好。间层工艺提高了保险杠核心强度、抗撞击性;面层工艺提高了保险杠表面的抗撞击性和耐磨性,与间层配合结构能够大幅提高保险杠强度。同时,基层工艺提高了基层的回弹和修复性,保证了保险杠的修复能力,增加使用次数,且不影响保险杠整体的强度、抗撞击性,延长使用寿命,具有良好的使用效果。
附图说明
23.图1为本发明一种epp基复材抗震吸能汽车保险杠的俯视截面示意图;图2为本发明一种epp基复材抗震吸能汽车保险杠的基层型材的前表面示意图;图3为本发明一种epp基复材抗震吸能汽车保险杠的基层型材的俯视局部图;图4为本发明一种epp基复材抗震吸能汽车保险杠的俯视局部剖面图;图1-4中,1-基层,1.1-圆柱凹槽,1.2-圆柱凸起;2-间层;3-面层。
具体实施方式
24.下面结合具体实施案例和附图1-4对本发明作进一步说明,但本发明并不局限于
这些实施例。
25.实施例1一种epp基复材抗震吸能汽车保险杠的制备方法,方法包括如下步骤:s1,预处理,以下s11、s12、s13为同时进行:s11:基层epp珠粒预压膨胀:将球径为3.5mm的基层epp珠粒进行四个阶段的预压,依次为:一次加压0.15bar,压时42min,泄压8min;二次加压2.5bar,压时5h,泄压6min;三次加压3.2bar,压时45min,不泄压;四次降压1.5bar,压时75h,得到基层预压epp珠粒,备用;s12:面层epp珠粒预压膨胀:将球径为1.6mm的面层epp珠粒进行五个阶段的预压,依次为:一次加压0.35bar,压时42min,泄压3min;二次加压3.1bar,压时6h,泄压3min;三次加压5.2bar,压时52min,不泄压;四次降压4.2bar,压时35min,不泄压;五次降压2.2bar,压时73h,得到面层预压epp珠粒,备用;其中,面层epp珠粒在发泡制备时内含有纳米级纤维,即玄武岩纤维和纳米玻璃纤维;纳米级纤维在面层epp珠粒中的体积含量为7%;s13:间层eps珠粒预压膨胀:将阻燃型且球径为1.2mm的间层eps珠粒进行六个阶段的预压,依次为:一次加压0.25bar,压时32min,泄压3min;二次加压2.2bar,压时4h,泄压12min;三次加压4.1bar,压时32min,不泄压;四次降压3.6bar,压时34min,不泄压;五次降压3.2bar,压时32min,不泄压;六次降压1.8bar,压时83h,得到间层预压eps珠粒,备用;s2,初压成型,以下s21、s22为同时进行:s21:基层预压成型:将基层预压epp珠粒输送注入至基层模具中,并分布均匀充满基层模具型腔,然后锁膜并预热,锁膜为锁紧固定基层模具,锁膜的压力为115bar,预热为通过蒸汽对基层模具进行预热,基层模具型腔的预热温度为55℃,预热时间3s;之后对基层模具进行单面加热,单面加热为通过蒸汽对基层模具进行穿透加热,基层模具型腔的加热温度为185℃,加热时间10s;其中,基层型材与间层型材的贴合面不充入蒸汽;加热后使基层预压epp珠粒压融成型,得到基层型材;s22:间层预压成型:将聚乙烯醇粉末与纤维分散于水中,加热至75℃,混合均匀得到浆料a,浆料a的成分质量配比为聚乙烯醇粉末∶纤维∶水=9∶3∶11;再向浆料a中加入二氧化硅溶胶,混合得到浆料b,浆料b的成分质量配比为浆料a∶二氧化硅溶胶=20∶5;将浆料b分散均匀注入至间层磨具中,然后将间层预压eps珠粒输送注入至基层模具中,并均匀浸渍于浆料b中,进行锁膜,锁膜的压力为150bar,锁紧固定基层模具挤压出多余浆料b后,通过电加热器对间层模具进行加热,加热温度为135℃,加热时间50s;使间层预压eps珠粒压融成型,得到间层型材;其中,纤维的直径为0.1~0.3mm,纤维长度为1~2mm;纤维为聚乙烯醇纤维和玄武岩纤维;s3,复压成型:将间层型材贴合于基层型材的前表面,进行组合型材,并将组合型材置于复压模具中,然后向间层型材前表面的复压模具型腔中输送注入面层预压epp珠粒,并分布均匀充满复压模具型腔的剩余空间,锁紧固定复压模具,锁膜的压力为150bar,然后通过电加热器对复压模具进行局部面加热,加热温度为235℃,加热时间45s,其中局部面加热为基层型材的后表面不加热;使面层预压epp珠粒压融并与基层型材和间层型材进行熔接成型,得到保
险杠型材;s4,后处理:保险杠成型后再经降温冷却、脱模、烘烤定型后得到保险杠成品。
26.本实施例上述方法制备的保险杠,如图1-4所示,保险杠包括基层1、间层2和面层3,间层2的厚度为基层1厚度的1/4,面层3的厚度大于间层2的厚度,间层2夹设在基层1和面层3之间,间层2与基层1为组合扣接,面层3与基层1和间层2为熔接;基层1的前表面热压形成有若干列间隔排布的圆柱凹槽1.1和圆柱凸起1.2;基层1的边缘和圆柱凸起1.2与面层3熔接,圆柱凸起1.2的高度等于间层2的厚度。其中圆柱凹槽1.1和圆柱凸起1.2为两排;圆柱凹槽1.1的直径为圆柱凸起1.2直径的2/3;间层2的表面形状与基层1的前表面形状相适配。
27.本实施例方法制备出的保险杠经型材分层检测结果,见下表:
28.本实施例保险杠整体检测结果及使用效果为:产品整体成型良好,无过熟过生现象,无缺料、多料、断裂现象;相比于现有基层同工艺一体成型的产品,使用性能大幅提高,具体表现在,基层和间层配合后提高了保险杠整体的抗震吸能性,间层的0吸水率阻隔辅助降低了基层吸水率,面层工艺也降低了面层的吸水率,配合间层阻隔,进一步减少吸水率,进而保险杠整体的抗老化性更好。间层工艺提高了保险杠核心强度、抗撞击性;面层工艺提高了保险杠表面的抗撞击性和耐磨性,与间层配合结构能够大幅提高保险杠强度。同时,基层工艺提高了基层的回弹和修复性,保证了保险杠的修复能力,增加使用次数,且不影响保险杠整体的强度、抗撞击性,延长使用寿命,具有良好的使用效果。
29.实施例2一种epp基复材抗震吸能汽车保险杠的制备方法,方法包括如下步骤:s1,预处理,以下s11、s12、s13为同时进行:s11:基层epp珠粒预压膨胀:将球径为3mm的基层epp珠粒进行四个阶段的预压,依次为:一次加压0.1bar,压时40min,泄压5min;二次加压2bar,压时5h,泄压5min;三次加压3bar,压时40min,不泄压;四次降压1bar,压时70h,得到基层预压epp珠粒,备用;s12:面层epp珠粒预压膨胀:将球径为2.2mm的面层epp珠粒进行五个阶段的预压,依次为:一次加压0.45bar,压时48min,泄压5min;二次加压3.4bar,压时7h,泄压4min;
三次加压5.8bar,压时58min,不泄压;四次降压4.6bar,压时45min,不泄压;五次降压2.7bar,压时78h,得到面层预压epp珠粒,备用;其中,面层epp珠粒在发泡制备时内含有纳米级纤维,纳米级纤维为玻璃纤维和陶瓷纤维;纳米级纤维在面层epp珠粒中的体积含量为5%;s13:间层eps珠粒预压膨胀:将阻燃型且球径为1.8mm的间层eps珠粒进行六个阶段的预压,依次为:一次加压0.35bar,压时38min,泄压4min;二次加压2.8bar,压时5h,泄压18min;三次加压4.4bar,压时37min,不泄压;四次降压3.9bar,压时38min,不泄压;五次降压3.4bar,压时45min,不泄压;六次降压2.2bar,压时88h,得到间层预压eps珠粒,备用;s2,初压成型,以下 s21、s22为同时进行:s21:基层预压成型:将基层预压epp珠粒输送注入至基层模具中,并分布均匀充满基层模具型腔,然后锁膜并预热,锁膜为锁紧固定基层模具,锁膜的压力为110bar,预热为通过蒸汽对基层模具进行预热,基层模具型腔的预热温度为50℃,预热时间2s;之后对基层模具进行单面加热,单面加热为通过蒸汽对基层模具进行穿透加热,基层模具型腔的加热温度为170℃,加热时间8s;其中,基层型材与间层型材的贴合面不充入蒸汽;加热后使基层预压epp珠粒压融成型,得到基层型材;s22:间层预压成型:将聚乙烯醇粉末与纤维分散于水中,加热至70℃,混合均匀得到浆料a,浆料a的成分质量配比为聚乙烯醇粉末∶纤维∶水=8∶2∶10;再向浆料a中加入二氧化硅溶胶,混合得到浆料b,浆料b的成分质量配比为浆料a∶二氧化硅溶胶=20∶3;将浆料b分散均匀注入至间层磨具中,然后将间层预压eps珠粒输送注入至基层模具中,并均匀浸渍于浆料b中,进行锁膜,锁膜的压力为140bar,锁紧固定基层模具挤压出多余浆料b后,通过电加热器对间层模具进行加热,加热温度为130℃,加热时间30s;使间层预压eps珠粒压融成型,得到间层型材;其中,纤维的直径为0.1~0.3mm,纤维长度为1~2mm;纤维为玄武岩纤维和玻璃纤维;s3,复压成型:将间层型材贴合于基层型材的前表面,进行组合型材,并将组合型材置于复压模具中,然后向间层型材前表面的复压模具型腔中输送注入面层预压epp珠粒,并分布均匀充满复压模具型腔的剩余空间,锁紧固定复压模具,锁膜的压力为140bar,然后通过电加热器对复压模具进行局部面加热,加热温度为220℃,加热时间30s,其中局部面加热为基层型材的后表面不加热;使面层预压epp珠粒压融并与基层型材和间层型材进行熔接成型,得到保险杠型材;s4,后处理:保险杠成型后再经降温冷却、脱模、烘烤定型后得到保险杠成品。
30.本实施例上述方法制备的保险杠,如图1-4所示,保险杠包括基层1、间层2和面层3,间层2的厚度为基层1厚度的1/4,面层3的厚度大于间层2的厚度,间层2夹设在基层1和面层3之间,间层2与基层1为组合扣接,基层1的前表面热压形成有若干列间隔排布的圆柱凹槽1.1和圆柱凸起1.2,面层3的内表面与圆柱凸起1.2的端面熔接,面层3的内表面与间层2为熔接;基层1的两端头直接与面层3的两端头熔接;圆柱凸起1.2的高度等于间层2的厚度。其中圆柱凹槽1.1和圆柱凸起1.2为两排;圆柱凹槽1.1的直径为圆柱凸起1.2直径的2/3;间
层2的表面形状与基层1的前表面形状相适配。
31.本实施例方法制备出的保险杠经型材分层检测结果,见下表:
32.本实施例保险杠整体检测结果及使用效果为:产品整体成型良好,无过熟过生现象,无缺料、多料、断裂现象;相比于现有基层同工艺一体成型的产品,使用性能大幅提高,具体表现在,基层和间层配合后提高了保险杠整体的抗震吸能性,间层的0吸水率阻隔辅助降低了基层吸水率,面层工艺也降低了面层的吸水率,配合间层阻隔,进一步减少吸水率,进而保险杠整体的抗老化性更好。间层工艺提高了保险杠核心强度、抗撞击性;面层工艺提高了保险杠表面的抗撞击性和耐磨性,与间层配合结构能够大幅提高保险杠强度。同时,基层工艺提高了基层的回弹和修复性,保证了保险杠的修复能力,增加使用次数,且不影响保险杠整体的强度、抗撞击性,延长使用寿命,具有良好的使用效果。
33.实施例3一种epp基复材抗震吸能汽车保险杠的制备方法,方法包括如下步骤:s1,预处理,以下s11、s12、s13为先后进行:s11:基层epp珠粒预压膨胀:将球径为4mm的基层epp珠粒进行四个阶段的预压,依次为:一次加压0.2bar,压时45min,泄压10min;二次加压3bar,压时5.5h,泄压10min;三次加压3.5bar,压时50min,不泄压;四次降压2bar,压时80h,得到基层预压epp珠粒,备用;s12:面层epp珠粒预压膨胀:将球径为1.5mm的面层epp珠粒进行五个阶段的预压,依次为:一次加压0.5bar,压时40min,泄压5min;二次加压3bar,压时7h,泄压3min;三次加压5bar,压时60min,不泄压;四次降压4bar,压时50min,不泄压;五次降压2bar,压时80h,得到面层预压epp珠粒,备用;其中,面层epp珠粒在发泡制备时内含有微米级纤维,微米级纤维为玄武岩纤维和陶瓷纤维中的至少一种;微米级纤维在面层epp珠粒中的体积含量为10%;s13:间层eps珠粒预压膨胀:将阻燃型且球径为1mm的间层eps珠粒进行六个阶段的预压,依次为:一次加压0.4bar,压时30min,泄压5min;二次加压2bar,压时5h,泄压10min;三次加压4.5bar,压时30min,不泄压;四次降压4bar,压时30min,不泄压;五次降压3.5bar,压时30min,不泄压;六次降压2.5bar,压时80h,得到间层预压eps珠粒,备用;s2,初压成型,以下s21、s22为先后进行:
s21:基层预压成型:将基层预压epp珠粒输送注入至基层模具中,并分布均匀充满基层模具型腔,然后锁膜并预热,锁膜为锁紧固定基层模具,锁膜的压力为120bar,预热为通过蒸汽对基层模具进行预热,基层模具型腔的预热温度为60℃,预热时间5s;之后对基层模具进行单面加热,单面加热为通过蒸汽对基层模具进行穿透加热,基层模具型腔的加热温度为200℃,加热时间15s;其中,基层型材与间层型材的贴合面不充入蒸汽;加热后使基层预压epp珠粒压融成型,得到基层型材;s22:间层预压成型:将聚乙烯醇粉末与纤维分散于水中,加热至80℃,混合均匀得到浆料a,浆料a的成分质量配比为聚乙烯醇粉末∶纤维∶水=10∶5∶12;再向浆料a中加入二氧化硅溶胶,混合得到浆料b,浆料b的成分质量配比为浆料a∶二氧化硅溶胶=20∶8;将浆料b分散均匀注入至间层磨具中,然后将间层预压eps珠粒输送注入至基层模具中,并均匀浸渍于浆料b中,进行锁膜,锁膜的压力为160bar,锁紧固定基层模具挤压出多余浆料b后,通过电加热器对间层模具进行加热,加热温度为140℃,加热时间60s;使间层预压eps珠粒压融成型,得到间层型材;其中,纤维的直径为0.1~0.3mm,纤维长度为1~2mm;纤维为玻璃纤维和陶瓷纤维;s3,复压成型:将间层型材贴合于基层型材的前表面,进行组合型材,并将组合型材置于复压模具中,然后向间层型材前表面的复压模具型腔中输送注入面层预压epp珠粒,并分布均匀充满复压模具型腔的剩余空间,锁紧固定复压模具,锁膜的压力为160bar,然后通过电加热器对复压模具进行局部面加热,加热温度为220℃,加热时间60s,其中局部面加热为基层型材的后表面不加热;使面层预压epp珠粒压融并与基层型材和间层型材进行熔接成型,得到保险杠型材;s4,后处理:保险杠成型后再经降温冷却、脱模、烘烤定型后得到保险杠成品。
34.本实施例上述方法制备的保险杠,如图1-4所示,保险杠包括基层1、间层2和面层3,间层2的厚度为基层1厚度的1/4,面层3的厚度大于间层2的厚度,间层2夹设在基层1和面层3之间,间层2与基层1为组合扣接,基层1的前表面热压形成有若干列间隔排布的圆柱凹槽1.1和圆柱凸起1.2,面层3的内表面与圆柱凸起1.2的端面熔接,面层3的内表面与间层2为熔接;基层1的两端头直接与面层3的两端头熔接;圆柱凸起1.2的高度等于间层2的厚度。其中圆柱凹槽1.1和圆柱凸起1.2为两排;圆柱凹槽1.1的直径小于圆柱凸起1.2的直径;间层2的表面形状与基层1的前表面形状相适配。
35.本实施例方法制备出的保险杠经型材分层检测结果,见下表:
36.本实施例保险杠整体检测结果及使用效果为:产品整体成型良好,无过熟过生现象,无缺料、多料、断裂现象;相比于现有基层同工艺一体成型的产品,使用性能大幅提高,具体表现在,基层和间层配合后提高了保险杠整体的抗震吸能性,间层的0吸水率阻隔辅助降低了基层吸水率,面层工艺也降低了面层的吸水率,配合间层阻隔,进一步减少吸水率,进而保险杠整体的抗老化性更好。间层工艺提高了保险杠核心强度、抗撞击性;面层工艺提高了保险杠表面的抗撞击性和耐磨性,与间层配合结构能够大幅提高保险杠强度。同时,基层工艺提高了基层的回弹和修复性,保证了保险杠的修复能力,增加使用次数,且不影响保险杠整体的强度、抗撞击性,延长使用寿命,具有良好的使用效果。
37.实施例4一种epp基复材抗震吸能汽车保险杠的制备方法,方法包括如下步骤:s1,预处理,以下s11、s12、s13为同时进行:s11:基层epp珠粒预压膨胀:将球径为4mm的基层epp珠粒进行四个阶段的预压,依次为:一次加压0.1bar,压时45min,泄压5min;二次加压3bar,压时5h,泄压10min;三次加压3bar,压时50min,不泄压;四次降压1bar,压时80h,得到基层预压epp珠粒,备用;s12:面层epp珠粒预压膨胀:将球径为2.5mm的面层epp珠粒进行五个阶段的预压,依次为:一次加压0.3bar,压时50min,泄压3min;二次加压3.5bar,压时6h,泄压5min;三次加压5bar,压时60min,不泄压;四次降压4bar,压时50min,不泄压;五次降压2bar,压时80h,得到面层预压epp珠粒,备用;其中,面层epp珠粒在发泡制备时内含有微米级纤维,微米级纤维为玄武岩纤维;微米级纤维在面层epp珠粒中的体积含量为6%;s13:间层eps珠粒预压膨胀:将阻燃型且球径为2mm的间层eps珠粒进行六个阶段的预压,依次为:一次加压0.2bar,压时40min,泄压3min;二次加压3bar,压时4h,泄压20min;三次加压4bar,压时40min,不泄压;四次降压3.5bar,压时50min,不泄压;五次降压3bar,压时50min,不泄压;六次降压1.5bar,压时90h,得到间层预压eps珠粒,备用;s2,初压成型,以下s21、s22为先后进行:s21:基层预压成型:将基层预压epp珠粒输送注入至基层模具中,并分布均匀充满基层模具型腔,然后锁膜并预热,锁膜为锁紧固定基层模具,锁膜的压力为120bar,预热为
通过蒸汽对基层模具进行预热,基层模具型腔的预热温度为50℃,预热时间5s;之后对基层模具进行单面加热,单面加热为通过蒸汽对基层模具进行穿透加热,基层模具型腔的加热温度为170℃,加热时间15s;其中,基层型材与间层型材的贴合面不充入蒸汽;加热后使基层预压epp珠粒压融成型,得到基层型材;s22:间层预压成型:将聚乙烯醇粉末与纤维分散于水中,加热至70℃,混合均匀得到浆料a,浆料a的成分质量配比为聚乙烯醇粉末∶纤维∶水=10∶2∶12;再向浆料a中加入二氧化硅溶胶,混合得到浆料b,浆料b的成分质量配比为浆料a∶二氧化硅溶胶=20∶3;将浆料b分散均匀注入至间层磨具中,然后将间层预压eps珠粒输送注入至基层模具中,并均匀浸渍于浆料b中,进行锁膜,锁膜的压力为160bar,锁紧固定基层模具挤压出多余浆料b后,通过电加热器对间层模具进行加热,加热温度为130℃,加热时间60s;使间层预压eps珠粒压融成型,得到间层型材;其中,纤维的直径为0.1~0.3mm,纤维长度为1~2mm;纤维为聚乙烯醇纤维和陶瓷纤维;s3,复压成型:将间层型材贴合于基层型材的前表面,进行组合型材,并将组合型材置于复压模具中,然后向间层型材前表面的复压模具型腔中输送注入面层预压epp珠粒,并分布均匀充满复压模具型腔的剩余空间,锁紧固定复压模具,锁膜的压力为140bar,然后通过电加热器对复压模具进行局部面加热,加热温度为250℃,加热时间30s,其中局部面加热为基层型材的后表面不加热;使面层预压epp珠粒压融并与基层型材和间层型材进行熔接成型,得到保险杠型材;s4,后处理:保险杠成型后再经降温冷却、脱模、烘烤定型后得到保险杠成品。
38.本实施例上述方法制备的保险杠,如图1-4所示,保险杠包括基层1、间层2和面层3,间层2的厚度为基层1厚度的1/3,面层3的厚度大于间层2的厚度,间层2夹设在基层1和面层3之间,间层2与基层1为组合扣接,基层1的前表面热压形成有若干列间隔排布的圆柱凹槽1.1和圆柱凸起1.2,面层3的内表面与圆柱凸起1.2的端面熔接,面层3的内表面与间层2为熔接;基层1的两端头直接与面层3的两端头熔接;圆柱凸起1.2的高度大于间层2的厚度。其中圆柱凹槽1.1和圆柱凸起1.2为两排;圆柱凹槽1.1的直径小于圆柱凸起1.2的直径;间层2的表面形状与基层1的前表面形状相适配。
39.本实施例方法制备出的保险杠经型材分层检测结果,见下表:
40.本实施例保险杠整体检测结果及使用效果为:产品整体成型良好,无过熟过生现象,无缺料、多料、断裂现象;相比于现有基层同工艺一体成型的产品,使用性能大幅提高,具体表现在,基层和间层配合后提高了保险杠整体的抗震吸能性,间层的0吸水率阻隔辅助降低了基层吸水率,面层工艺也降低了面层的吸水率,配合间层阻隔,进一步减少吸水率,进而保险杠整体的抗老化性更好。间层工艺提高了保险杠核心强度、抗撞击性;面层工艺提高了保险杠表面的抗撞击性和耐磨性,与间层配合结构能够大幅提高保险杠强度。同时,基层工艺提高了基层的回弹和修复性,保证了保险杠的修复能力,增加使用次数,且不影响保险杠整体的强度、抗撞击性,延长使用寿命,具有良好的使用效果。
41.实施例5一种epp基复材抗震吸能汽车保险杠的制备方法,方法包括如下步骤:s1,预处理,以下s11、s12、s13为先后进行:s11:基层epp珠粒预压膨胀:将球径为3mm的基层epp珠粒进行四个阶段的预压,依次为:一次加压0.2bar,压时40min,泄压10min;二次加压2bar,压时5.5h,泄压5min;三次加压3.5bar,压时40min,不泄压;四次降压2bar,压时70h,得到基层预压epp珠粒,备用;s12:面层epp珠粒预压膨胀:将球径为2.5mm的面层epp珠粒进行五个阶段的预压,依次为:一次加压0.5bar,压时50min,泄压5min;二次加压3.5bar,压时7h,泄压5min;三次加压6bar,压时60min,不泄压;四次降压5bar,压时50min,不泄压;五次降压3bar,压时80h,得到面层预压epp珠粒,备用;其中,面层epp珠粒在发泡制备时内含有纳米级纤维,纳米级纤维为陶瓷纤维;纳米级纤维在面层epp珠粒中的体积含量为7%;s13:间层eps珠粒预压膨胀:将阻燃型且球径为2mm的间层eps珠粒进行六个阶段的预压,依次为:一次加压0.4bar,压时40min,泄压5min;二次加压3bar,压时5h,泄压20min;三次加压4.5bar,压时40min,不泄压;四次降压4bar,压时50min,不泄压;五次降压3.5bar,压时50min,不泄压;六次降压2.5bar,压时90h,得到间层预压eps珠粒,备用;s2,初压成型,以下s21、s22为同时进行:s21:基层预压成型:将基层预压epp珠粒输送注入至基层模具中,并分布均匀充满基层模具型腔,然后锁膜并预热,锁膜为锁紧固定基层模具,锁膜的压力为110bar,预热为
通过蒸汽对基层模具进行预热,基层模具型腔的预热温度为60℃,预热时间2s;之后对基层模具进行单面加热,单面加热为通过蒸汽对基层模具进行穿透加热,基层模具型腔的加热温度为200℃,加热时间8s;其中,基层型材与间层型材的贴合面不充入蒸汽;加热后使基层预压epp珠粒压融成型,得到基层型材;s22:间层预压成型:将聚乙烯醇粉末与纤维分散于水中,加热至80℃,混合均匀得到浆料a,浆料a的成分质量配比为聚乙烯醇粉末∶纤维∶水=8∶5∶10;再向浆料a中加入二氧化硅溶胶,混合得到浆料b,浆料b的成分质量配比为浆料a∶二氧化硅溶胶=20∶8;将浆料b分散均匀注入至间层磨具中,然后将间层预压eps珠粒输送注入至基层模具中,并均匀浸渍于浆料b中,进行锁膜,锁膜的压力为140bar,锁紧固定基层模具挤压出多余浆料b后,通过电加热器对间层模具进行加热,加热温度为140℃,加热时间30s;使间层预压eps珠粒压融成型,得到间层型材;其中,纤维的直径为0.1~0.3mm,纤维长度为1~2mm;纤维为聚乙烯醇纤维、玄武岩纤维和玻璃纤维;s3,复压成型:将间层型材贴合于基层型材的前表面,进行组合型材,并将组合型材置于复压模具中,然后向间层型材前表面的复压模具型腔中输送注入面层预压epp珠粒,并分布均匀充满复压模具型腔的剩余空间,锁紧固定复压模具,锁膜的压力为160bar,然后通过电加热器对复压模具进行局部面加热,加热温度为250℃,加热时间60s,其中局部面加热为基层型材的后表面不加热;使面层预压epp珠粒压融并与基层型材和间层型材进行熔接成型,得到保险杠型材;s4,后处理:保险杠成型后再经降温冷却、脱模、烘烤定型后得到保险杠成品。
42.本实施例上述方法制备的保险杠,如图1-4所示,保险杠包括基层1、间层2和面层3,间层2的厚度为基层1厚度的1/4,面层3的厚度大于间层2的厚度,间层2夹设在基层1和面层3之间,间层2与基层1为组合扣接,基层1的前表面热压形成有若干列间隔排布的圆柱凹槽1.1和圆柱凸起1.2,面层3的内表面与圆柱凸起1.2的端面熔接,面层3的内表面与间层2为熔接;基层1的两端头直接与面层3的两端头熔接;圆柱凸起1.2的高度大于间层2的厚度。其中圆柱凹槽1.1和圆柱凸起1.2为两排;圆柱凹槽1.1的直径小于圆柱凸起1.2的直径;间层2的表面形状与基层1的前表面形状相适配。
43.本实施例方法制备出的保险杠经型材分层检测结果,见下表:
44.本实施例保险杠整体检测结果及使用效果为:产品整体成型良好,无过熟过生现象,无缺料、多料、断裂现象;相比于现有基层同工艺一体成型的产品,使用性能大幅提高,具体表现在,基层和间层配合后提高了保险杠整体的抗震吸能性,间层的0吸水率阻隔辅助降低了基层吸水率,面层工艺也降低了面层的吸水率,配合间层阻隔,进一步减少吸水率,进而保险杠整体的抗老化性更好。间层工艺提高了保险杠核心强度、抗撞击性;面层工艺提高了保险杠表面的抗撞击性和耐磨性,与间层配合结构能够大幅提高保险杠强度。同时,基层工艺提高了基层的回弹和修复性,保证了保险杠的修复能力,增加使用次数,且不影响保险杠整体的强度、抗撞击性,延长使用寿命,具有良好的使用效果。
45.实施例6一种epp基复材抗震吸能汽车保险杠的制备方法,方法包括如下步骤:s1,预处理,以下s11、s12、s13为同时进行:s11:基层epp珠粒预压膨胀:将球径为3.8mm的基层epp珠粒进行四个阶段的预压,依次为:一次加压0.2bar,压时43min,泄压8min;二次加压2.8bar,压时5.3h,泄压8min;三次加压3.3bar,压时47min,不泄压;四次降压1.8bar,压时78h,得到基层预压epp珠粒,备用;s12:面层epp珠粒预压膨胀:将球径为1.5mm的面层epp珠粒进行五个阶段的预压,依次为:一次加压0.3bar,压时40min,泄压3min;二次加压3bar,压时6h,泄压3min;三次加压5bar,压时50min,不泄压;四次降压4bar,压时30min,不泄压;五次降压2bar,压时70h,得到面层预压epp珠粒,备用;其中,面层epp珠粒在发泡制备时内含有微米级纤维,微米级纤维为玄武岩纤维和陶瓷纤维;微米级纤维在面层epp珠粒中的体积含量为7.5%;s13:间层eps珠粒预压膨胀:将阻燃型且球径为1mm的间层eps珠粒进行六个阶段的预压,依次为:一次加压0.2bar,压时30min,泄压3min;二次加压2bar,压时4h,泄压10min;三次加压4bar,压时30min,不泄压;四次降压3.5bar,压时30min,不泄压;五次降压3bar,压时30min,不泄压;六次降压1.5bar,压时80h,得到间层预压eps珠粒,备用;s2,初压成型,以下s21、s22为同时进行:s21:基层预压成型:将基层预压epp珠粒输送注入至基层模具中,并分布均匀充满
基层模具型腔,然后锁膜并预热,锁膜为锁紧固定基层模具,锁膜的压力为118bar,预热为通过蒸汽对基层模具进行预热,基层模具型腔的预热温度为58℃,预热时间4s;之后对基层模具进行单面加热,单面加热为通过蒸汽对基层模具进行穿透加热,基层模具型腔的加热温度为190℃,加热时间14s;其中,基层型材与间层型材的贴合面不充入蒸汽;加热后使基层预压epp珠粒压融成型,得到基层型材;s22:间层预压成型:将聚乙烯醇粉末与纤维分散于水中,加热至78℃,混合均匀得到浆料a,浆料a的成分质量配比为聚乙烯醇粉末∶纤维∶水=9.5∶4∶11;再向浆料a中加入二氧化硅溶胶,混合得到浆料b,浆料b的成分质量配比为浆料a∶二氧化硅溶胶=20∶7;将浆料b分散均匀注入至间层磨具中,然后将间层预压eps珠粒输送注入至基层模具中,并均匀浸渍于浆料b中,进行锁膜,锁膜的压力为155bar,锁紧固定基层模具挤压出多余浆料b后,通过电加热器对间层模具进行加热,加热温度为138℃,加热时间55s;使间层预压eps珠粒压融成型,得到间层型材;其中,纤维的直径为0.1~0.3mm,纤维长度为1~2mm;纤维为玄武岩纤维;s3,复压成型:将间层型材贴合于基层型材的前表面,进行组合型材,并将组合型材置于复压模具中,然后向间层型材前表面的复压模具型腔中输送注入面层预压epp珠粒,并分布均匀充满复压模具型腔的剩余空间,锁紧固定复压模具,锁膜的压力为140bar,然后通过电加热器对复压模具进行局部面加热,加热温度为220℃,加热时间30s,其中局部面加热为基层型材的后表面不加热;使面层预压epp珠粒压融并与基层型材和间层型材进行熔接成型,得到保险杠型材;s4,后处理:保险杠成型后再经降温冷却、脱模、烘烤定型后得到保险杠成品。
46.本实施例上述方法制备的保险杠,如图1-4所示,保险杠包括基层1、间层2和面层3,间层2的厚度为基层1厚度的1/3,面层3的厚度等于间层2的厚度,间层2夹设在基层1和面层3之间,间层2与基层1为组合扣接,基层1的前表面热压形成有若干列间隔排布的圆柱凹槽1.1和圆柱凸起1.2,面层3的内表面与圆柱凸起1.2的端面熔接,面层3的内表面与间层2为熔接;基层1的两端头直接与面层3的两端头熔接;圆柱凸起1.2的高度等于间层2的厚度。其中圆柱凹槽1.1和圆柱凸起1.2为两排;圆柱凹槽1.1的直径小于圆柱凸起1.2的直径;间层2的表面形状与基层1的前表面形状相适配。
47.本实施例方法制备出的保险杠经型材分层检测结果,见下表:
48.本实施例保险杠整体检测结果及使用效果为:产品整体成型良好,无过熟过生现象,无缺料、多料、断裂现象;相比于现有基层同工艺一体成型的产品,使用性能大幅提高,具体表现在,基层和间层配合后提高了保险杠整体的抗震吸能性,间层的0吸水率阻隔辅助降低了基层吸水率,面层工艺也降低了面层的吸水率,配合间层阻隔,进一步减少吸水率,进而保险杠整体的抗老化性更好。间层工艺提高了保险杠核心强度、抗撞击性;面层工艺提高了保险杠表面的抗撞击性和耐磨性,与间层配合结构能够大幅提高保险杠强度。同时,基层工艺提高了基层的回弹和修复性,保证了保险杠的修复能力,增加使用次数,且不影响保险杠整体的强度、抗撞击性,延长使用寿命,具有良好的使用效果。
49.实施例7一种epp基复材抗震吸能汽车保险杠的制备方法,方法包括如下步骤:s1,预处理,以下s11、s12、s13为先后进行:s11:基层epp珠粒预压膨胀:将球径为3.2mm的基层epp珠粒进行四个阶段的预压,依次为:一次加压0.12bar,压时41min,泄压6min;二次加压2.2bar,压时5h,泄压7min;三次加压3.1bar,压时42min,不泄压;四次降压1.2bar,压时72h,得到基层预压epp珠粒,备用;s12:面层epp珠粒预压膨胀:将球径为2mm的面层epp珠粒进行五个阶段的预压,依次为:一次加压0.4bar,压时45min,泄压4min;二次加压3.2bar,压时6.5h,泄压4min;三次加压5.5bar,压时55min,不泄压;四次降压4.5bar,压时40min,不泄压;五次降压2.5bar,压时75h,得到面层预压epp珠粒,备用;其中,面层epp珠粒在发泡制备时内含有纳米级纤维,纳米级纤维为玄武岩纤维、玻璃纤维和陶瓷纤维的混合纤维;纳米级纤维在面层epp珠粒中的体积含量为9%;s13:间层eps珠粒预压膨胀:将阻燃型且球径为1.5mm的间层eps珠粒进行六个阶段的预压,依次为:一次加压0.3bar,压时35min,泄压4min;二次加压2.5bar,压时4.5h,泄压15min;三次加压4.2bar,压时35min,不泄压;四次降压3.7bar,压时40min,不泄压;五次降压3.3bar,压时40min,不泄压;六次降压2bar,压时85h,得到间层预压eps珠粒,备用;s2,初压成型,以下s21、s22为先后进行:s21:基层预压成型:将基层预压epp珠粒输送注入至基层模具中,并分布均匀充满基层模具型腔,然后锁膜并预热,锁膜为锁紧固定基层模具,锁膜的压力为113bar,预热为
通过蒸汽对基层模具进行预热,基层模具型腔的预热温度为52℃,预热时间2s;之后对基层模具进行单面加热,单面加热为通过蒸汽对基层模具进行穿透加热,基层模具型腔的加热温度为175℃,加热时间9s;其中,基层型材与间层型材的贴合面不充入蒸汽;加热后使基层预压epp珠粒压融成型,得到基层型材;s22:间层预压成型:将聚乙烯醇粉末与纤维分散于水中,加热至72℃,混合均匀得到浆料a,浆料a的成分质量配比为聚乙烯醇粉末∶纤维∶水=8.5∶2.5∶10;再向浆料a中加入二氧化硅溶胶,混合得到浆料b,浆料b的成分质量配比为浆料a∶二氧化硅溶胶=20∶4;将浆料b分散均匀注入至间层磨具中,然后将间层预压eps珠粒输送注入至基层模具中,并均匀浸渍于浆料b中,进行锁膜,锁膜的压力为145bar,锁紧固定基层模具挤压出多余浆料b后,通过电加热器对间层模具进行加热,加热温度为132℃,加热时间35s;使间层预压eps珠粒压融成型,得到间层型材;其中,纤维的直径为0.1~0.3mm,纤维长度为1~2mm;纤维为陶瓷纤维;s3,复压成型:将间层型材贴合于基层型材的前表面,进行组合型材,并将组合型材置于复压模具中,然后向间层型材前表面的复压模具型腔中输送注入面层预压epp珠粒,并分布均匀充满复压模具型腔的剩余空间,锁紧固定复压模具,锁膜的压力为150bar,然后通过电加热器对复压模具进行局部面加热,加热温度为230℃,加热时间45s,其中局部面加热为基层型材的后表面不加热;使面层预压epp珠粒压融并与基层型材和间层型材进行熔接成型,得到保险杠型材;s4,后处理:保险杠成型后再经降温冷却、脱模、烘烤定型后得到保险杠成品。
50.本实施例上述方法制备的保险杠,如图1-4所示,保险杠包括基层1、间层2和面层3,间层2的厚度为基层1厚度的1/4,面层3的厚度大于间层2的厚度,间层2夹设在基层1和面层3之间,间层2与基层1为组合扣接,基层1的前表面热压形成有若干列间隔排布的圆柱凹槽1.1和圆柱凸起1.2,面层3的内表面与圆柱凸起1.2的端面熔接,面层3的内表面与间层2为熔接;基层1的两端头直接与面层3的两端头熔接;圆柱凸起1.2的高度等于间层2的厚度。其中圆柱凹槽1.1和圆柱凸起1.2为两排;圆柱凹槽1.1的直径小于圆柱凸起1.2的直径;间层2的表面形状与基层1的前表面形状相适配。
51.本实施例方法制备出的保险杠经型材分层检测结果,见下表:
52.本实施例保险杠整体检测结果及使用效果为:产品整体成型良好,无过熟过生现象,无缺料、多料、断裂现象;相比于现有基层同工艺一体成型的产品,使用性能大幅提高,具体表现在,基层和间层配合后提高了保险杠整体的抗震吸能性,间层的0吸水率阻隔辅助降低了基层吸水率,面层工艺也降低了面层的吸水率,配合间层阻隔,进一步减少吸水率,进而保险杠整体的抗老化性更好。间层工艺提高了保险杠核心强度、抗撞击性;面层工艺提高了保险杠表面的抗撞击性和耐磨性,与间层配合结构能够大幅提高保险杠强度。同时,基层工艺提高了基层的回弹和修复性,保证了保险杠的修复能力,增加使用次数,且不影响保险杠整体的强度、抗撞击性,延长使用寿命,具有良好的使用效果。