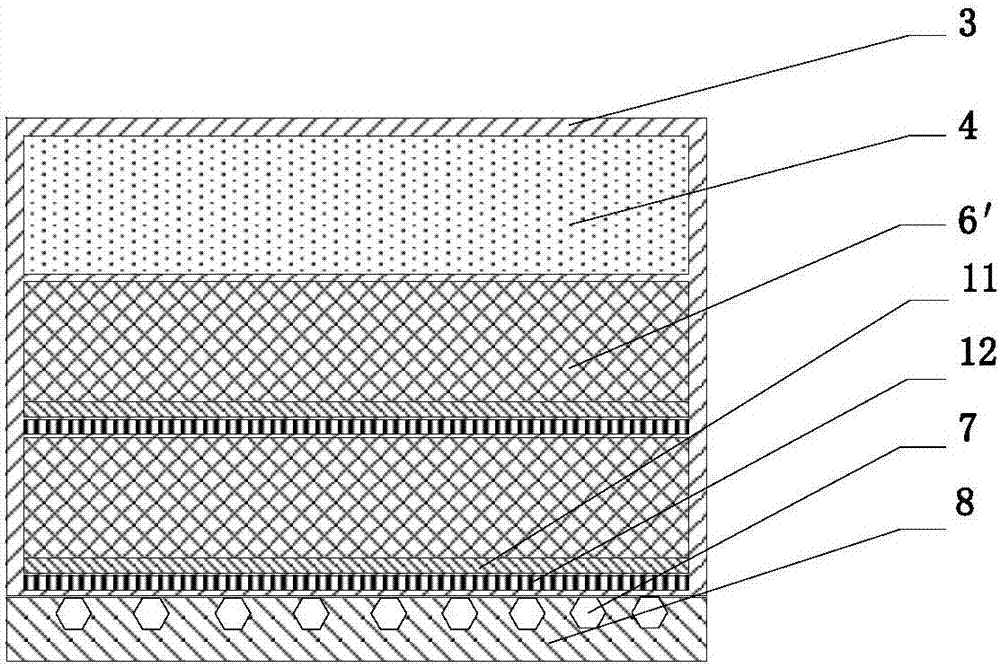
本发明属于材料
技术领域:
,特别涉及一种宝石级人造金刚石单晶用催化剂的制备方法及催化剂。
背景技术:
:在采用六面顶、bars(无压机分球式超高压合成装置)等超高压设备生长宝石级人造金刚石单晶时,一般采用图1所示的结构耗材组成的立方体(简称合成块)。其中包括碳化钨压砧1,叶蜡石传压介质2,石墨加热管3,mgo盖子4,碳源5,mgo管6,金属催化剂7,晶种8,mgo晶床9和导电钢帽10。工作时超高压设备的碳化钨压砧1受压力源推动,从上下、前后、左右六个方向均匀挤压合成块,合成块外围的叶蜡石传压介质9发生变形、流动,形成密封边。密封边与碳化钨压砧1内表面构成密封的合成腔体,并在合成腔体中心处达到金刚石单晶生长需要的5.5gpa左右的合成压强;设备外部的低压大电流电源,通过上、下碳化钨压砧1、导电钢帽10、导电垫片等构成的回路,对合成块中心处的石墨加热管施加数百-数千安培的加热电流,在合成腔体中心处达到金刚石单晶生长需要的1500℃左右的合成温度,使fe、ni等金属催化剂完全融化;并在图1中的碳源与晶种之间形成约5–40℃/mm的温度梯度。单晶生长时,低温端晶种上方催化剂熔体中溶解的碳原子在晶种表面析出,形成金刚石单晶;造成熔体中碳原子浓度降低。同时高温端碳源中的碳原子不断溶解到催化剂熔体中,在温度梯度的推动下运动到低温端,补充催化剂熔体中析出的碳原子,使单晶生长过程持续进行。一般情况下,碳源、催化剂中含有微量氮原子,在单晶生长过程中,氮杂质会进入金刚石单晶内部,形成缺陷,使金刚石单晶呈黄色。为了获得无色金刚石单晶,目前采取在金属催化剂中加入微量金属ti(或al),作为除氮剂。除氮剂具有较高的化学活性,在催化剂融化后,首先与氮反应生成不溶于催化剂的tin(aln)固体微颗粒。在金刚石单晶生长过程中,tin(aln)颗粒容易进入单晶内部,形成包裹体,影响单晶质量。为了减少tin(aln)包裹体,常在催化剂中加入少量cu。cu熔体对tin(aln)颗粒有一定的溶解作用,减少了tin(aln)固体微颗粒的形成。由于不存在商业化生产的fe-ni-ti(al)-cu合金,目前在生产宝石级人造金刚石单晶时常采用图2的催化剂及组装方式。图中,6′为feni合金,11为ti箔,12为铜箔。其中feni合金催化剂采用feni20或feni30牌号坡莫合金棒材原料,经车削获得预定的直径及高度;ti(cu)按其在合金中所占质量比,采用一定厚度的,商业化生产的ti(cu)箔裁剪而成。采用上述催化剂存在2个问题:第一个问题是:在催化剂融化后,金刚石单晶开始生长初期,由于催化剂中的fe-ni-cu-ti(al)合金中各元素微观分布不均匀,在低含量ti(al)微区,杂质氮原子不易去除,造成金刚石单晶颜色发黄;在ti(al)富集微区,易形成微量ti(al)碳化物,并进入金刚石单晶内部形成包裹体杂质。目前对上述问题的解决办法是在金属催化剂中加入一定过量的ti(al),如催化剂中ti质量百分比可达10%,同时通过降低温度梯度的方法降低单晶生长速度。这样可在单晶生长初期确保氮杂质的去除,同时又显著减少金刚石晶体中包裹体含量。但这样带来的弊端是在生长单晶的整个过程中,为了避免晶体中形成包裹体,只能采用较低的单晶生长速度。例如目前国内在六面顶高压设备上一次生长多颗0.1克拉/粒无色钻石时,单晶生长速度约为0.1克拉/30小时。第二个问题是:催化剂采用的坡莫合金棒材、ti(al)箔,在使用前必须采用机加工整形、裁剪。在整形与裁剪过程中,催化剂表面暴露在空气中,容易氧化,这样在单晶生长过程中带来了新的金属氧化物污染及金属氧化物包裹体。技术实现要素:为解决上述问题,本发明提供一种宝石级人造金刚石单晶用催化剂的制备方法及催化剂,所述方法制备的催化剂圆柱可以克服现有技术的上述问题,而提高金刚石单晶的生长速度和净度。本发明采用市售fe-ni催化剂合金粉末,与市售ti(al)cu合金粉末,通过混料-温压成型-高温氢还原处理工艺,合成出直径、高度、密度、公差符合要求,可直接组装使用的催化剂圆柱。由于ti(al)除氮剂是以微粉的形式均匀分布在催化剂中,并在氢还原过程中已预先除去催化剂中的部分杂质氮原子,因此ti(al)的除氮效率大大提高,只添加5%以下的除氮剂即可达到明显的除氮效果。由于ti(al)添加量较少,即使在较高的温度梯度与单晶生长速度下,包裹体的形成几率也明显降低。具体而言,本发明采用的技术方案如下:一种宝石级人造金刚石单晶用催化剂的制备方法,所述金属催化剂为fe-ni-ti-cu系催化剂合金或者fe-ni-al-cu系催化剂合金,所述方法包括如下步骤:s1:原料选择及配比:所述fe-ni-ti-cu系催化剂合金选取feni预合金粉末和ticu预合金粉末为原料,配料名义成分为fe:65%-75%,ni:20%-30%,ti:1%-5%,cu:0.5%-3%;所述fe-ni-al-cu系催化剂合金选取feni预合金粉末和alcu预合金粉末为原料,配料名义成分为:fe:65%-75%,ni:22%-33%,al:1%-3%,cu:0.5%-3%;s2:筛分:将feni预合金粉末、ticu预合金粉末或alcu预合金粉末进行粒度筛分分级,均分为100–80微米,80–60微米,60–40微米,40–20微米四个级别;s3:混料:feni预合金粉末和ticu预合金粉末或alcu预合金粉末按照s2步骤分级的不同粒度进行按比例选取级配;然后在三维混料机中混合均匀获得混合粉末;s4:温压成型:将s3步骤获得的混合粉末装入圆柱形温压成型模具,然后进行温压成型,控制温压工艺使得成型坯的相对密度为70-80%;s5:氢气高温还原烧结:将s4步骤获得的成型坯放入高温氢还原炉中,通入氢气和氩气混合保护气体,进行烧结成型,控制烧结工艺,使得烧结后的圆柱形催化剂的相对密度达到99%以上;s6:冷却,存储:s5步骤的烧结后的圆柱形催化剂随炉冷却,然后进行室温、干燥、惰性气体保护下的存储。进一步,所述feni预合金粉为feni20或feni30预合金触媒粉末,所述ticu预合金粉末或alcu预合金粉末中cu的质量百分比为35-50%。进一步,所述feni预合金粉末的级配为:(100–80微米):(80–60微米):(60–40微米):(40–20微米)=(5-10%):(20-35%):(40-60%):(10-20%);所述ticu预合金粉末或alcu预合金粉末的级配为(100–80微米):(80–60微米):(60–40微米):(40–20微米)=(5-10%):(40%):(30-35%):(15-25%)。进一步,所述温压温压工艺为,温压温度100–150℃,温压压力300–700mpa。进一步,所述烧结工艺为,烧结温度800-1150℃,保温时间2-8小时。一种宝石级人造金刚石单晶用催化剂,所述催化剂由上述制备方法得到。与现有技术相比,本发明的技术方案具有以下优点:在采用本催化剂后,可使目前国产六面顶设备生长宝石级无色金刚石单晶的生长速度提高到0.2克拉/20小时,0.5克拉/40小时,1克拉/72小时,2克拉/100小时;100小时后单晶生长速度超过15mg/hr,同时单晶净度可达到vvs级。附图说明通过阅读下文优选实施方式的详细描述,各种其他的优点和益处对于本领域普通技术人员将变得清楚明了。附图仅用于示出优选实施方式的目的,而并不认为是对本发明的限制。而且在整个附图中,用相同的参考符号表示相同的部件。在附图中:图1为现有技术中高温-高压温度梯度法合成宝石级人造金刚石单晶原理示意图。图2为现有技术中高温-高压温度梯度法合成宝石级人造金刚石单晶的催化剂组装方式示意图。具体实施方式下面将参照附图更详细地描述本公开的示例性实施方式。虽然本公开的示例性实施方式,然而应当理解,可以以各种形式实现本公开而不应被这里阐述的实施方式所限制。相反,提供这些实施方式是为了能够更透彻地理解本公开,并且能够将本公开的范围完整的传达给本领域的技术人员。实施例1:制备总质量1千克,质量百分比(名义成分)为75%fe,19%ni,4%ti,2%cu的催化剂合金。首先按表1称量不同粒径的feni20合金粉末表1不同粒度feni20合金粉末称取质量粒度(微米)100-8080-6060-4040-20合计质量百分比(%)10%20%60%10%100%称量质量(克)93.85187.7563.193.85938.5随后按表2称量不同粒径的35%cu-65%ti合金粉末。表2不同粒度35%cu-65%ti合金粉末称取质量粒度(微米)100-8080-6060-4040-20合计质量百分比(%)5%40%30%25%100%称量质量(克)3.07524.618.4515.37561.5用3维混料机将总质量为1千克的上述8种不同粒径合金粉末均匀混合后,每次称取2.5克合金粉末,装填入温压成型模具。在120℃,600mpa下压制成相对密度80%的圆柱。将制成的合金圆柱放入氢还原炉内,在10%氢气-90%氩气气氛,1000℃下保温0.5小时,然后在纯氩气气氛,900℃下保温1小时。随炉冷却后,获得直径10mm,高度4mm,相对密度大于99%的催化剂合金圆柱。储存、备用。使用上述催化剂,在bars(无压机分球式超高压合成装置)设备上,当合成压强为5.5gpa,晶种上端面温度为1420℃,温度梯度为15℃/mm时,保温时间40小时,可生长出0.6–0.8克拉/粒,净度为si的无色金刚石单晶。实施例2:制备总质量1千克,质量百分比为65.8%fe,28.2%ni,3%al,3%cu的催化剂合金。首先按表3称量不同粒径的feni30合金粉末表3不同粒度feni30合金粉末称取质量粒度(微米)100-8080-6060-4040-20合计质量百分比(%)5%35%40%20%100%称量质量(克)47329376188940随后按表4称量不同粒径的50%cu-50%ti合金粉末。表4不同粒度50%al-50%ti合金粉末称取质量粒度(微米)100-8080-6060-4040-20合计质量百分比(%)10%40%35%15%100%称量质量(克)3.07524.618.4515.37560用3维混料机将总质量为1千克的上述8种不同粒径合金粉末均匀混合后,每次称取2.4克合金粉末,装填入温压成型模具。在110℃,550mpa下压制成相对密度80%的圆柱。将制成的合金圆柱放入氢还原炉内,在10%氢气-90%氩气气氛,1150℃下保温0.5小时,然后在纯氩气气氛,800℃下保温2小时。随炉冷却后,获得直径10mm,高度4mm,相对密度大于99%的催化剂合金圆柱。储存、备用。使用上述催化剂,在bars(无压机分球式超高压合成装置)设备上,当合成压强为5.5gpa,晶种上端面温度为1410℃,温度梯度为8℃/mm时,保温时间40小时,可生长出0.4–0.5克拉/粒,净度为vvs的无色金刚石单晶。实施例3:制备总质量1千克,质量百分比(名义成分)为78%fe,18%ni,2.5%ti,1.5%cu的催化剂合金。采用feni20预合金粉末和35%cu-65%ti合金粉末。级配方式与实施例1相同。用3维混料机将总质量为1千克的8种不同粒径合金粉末均匀混合后,每次称取2.5克合金粉末,装填入温压成型模具。在150℃,300mpa下压制成相对密度70%的圆柱。将制成的合金圆柱放入氢还原炉内,在10%氢气-90%氩气气氛,1000℃下保温0.5小时,然后在纯氩气气氛,900℃下保温1小时。随炉冷却后,获得直径10mm,高度4mm,相对密度大于99%的催化剂合金圆柱。储存、备用。使用上述催化剂,在bars(无压机分球式超高压合成装置)设备上,当合成压强为5.5gpa,晶种上端面温度为1420℃,温度梯度为10℃/mm时,保温时间40小时,可生长出0.6–0.8克拉/粒,净度为vs级无色金刚石单晶。以上所述,仅为本发明较佳的具体实施方式,但本发明的保护范围并不局限于此,任何熟悉本
技术领域:
的技术人员在本发明揭露的技术范围内,可轻易想到的变化或替换,都应涵盖在本发明的保护范围之内。因此,本发明的保护范围应以所述权利要求的保护范围为准。当前第1页12