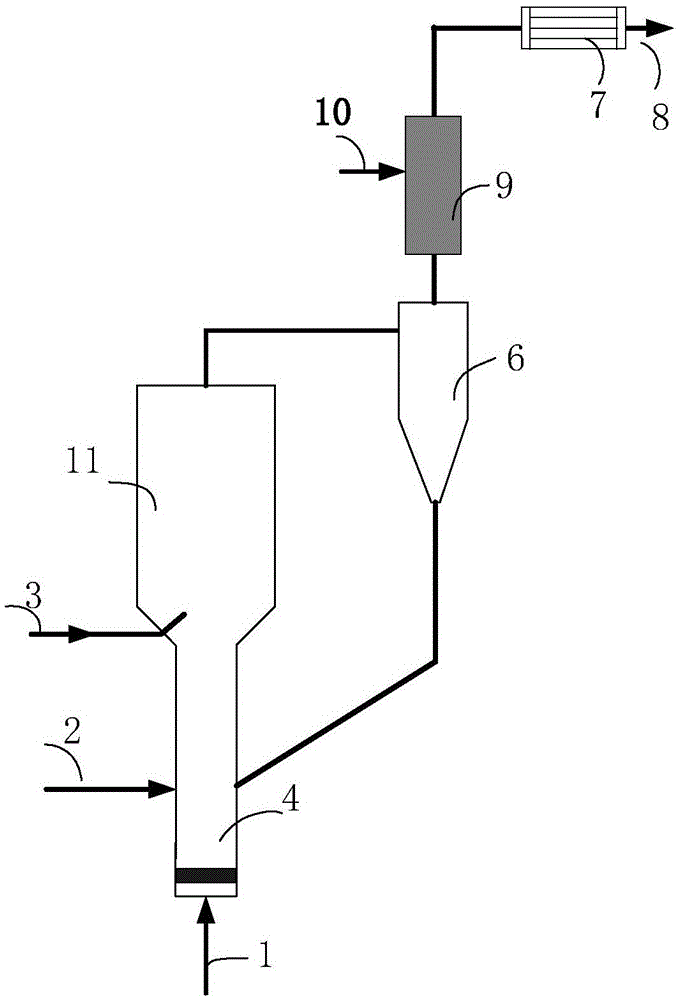
本发明属于能源
技术领域:
,具体涉及一种生物质热转化制取燃料油或其他化工品的方法,更特别地涉及用于由生物质热解或其热解衍生的热解油的催化脱氧而生产低氧生物质衍生的热解油的方法。
背景技术:
:快速热解是一种使用热解反应器将有机含碳生物质原料,即“生物质”,在无氧条件下快速加热至300-900℃,使其产生固体产物、液体产物和气态热解产物。气态热解产物的可冷凝部分(蒸气)冷凝成热解油。生物质热解油可作为燃料直接燃烧以用于某些锅炉和工业窑炉应用,并且还可作为催化方法中的潜在原料用于在炼油厂中生产燃料。然而,生物质热解油为复杂的高度氧合有机液体,其所具有的性质目前限制其作为生物燃料的使用。例如,生物质热解油具有高酸度和低能量密度,其大部分可归因于油中的氧合烃,其在储存期间经受次级反应。生物质热解油中的这类氧合烃包括羧酸、苯酚、甲酚、醇、醛等。常规生物质衍生的热解油包含30wt%以上的来自这些氧合烃的氧。生物质热解油转化成生物燃料和化学品需要生物质衍生的热解油的完全或部分脱氧。这种脱氧可经由两条主要路线,即水或CO2的消除而进行。然而将生物质热解油脱氧极易导致催化裂解、催化热解或催化加氢处理反应器中催化剂的快速积碳、堵塞、失活。显然,正是由于生物质热解油的各组分的热或酸催化聚合,例如油的各组分自身聚 合的二级反应。因此,理想的是提供用于生产低氧生物质热解油而不堵塞催化剂或减缓催化剂失活的方法,由此提高运行时间并改进生物质热解油的加工性。申请号为201280060991.1的专利申请发明了一种用于将生物质衍生的热解油脱氧的方法,利用含酚稀释剂稀释生物质衍生的热解油,进而与脱氧催化剂在加氢处理条件下在氢气接触。申请号为201380054271.9的专利申请发明了一种催化裂化源自包含生物质的材料的热解油的方法,其核心在于混合少部分脱氧后的热解油和预热的烃进料以制备进料混合物,然后将该混合物在不低于400℃的温度下在催化裂化反应器中与催化裂化催化剂接触以制备裂化产品。可见,目前国内外主要是采用催化加氢和催化裂解脱氧的方法。催化加氢过程中,生物油中的氧与氢气反应后以水分子的形式脱除,催化裂解脱氧,是在催化剂的作用下将氧以一氧化碳、二氧化碳等的形式脱除,缺点是脱氧的同时,也损失掉了部分碳,使得最终产品收率不高。因此,如何克服催化脱氧过程催化剂易于结焦、反应停留时间长的问题,以及提高最终产品收率等问题急需解决。因此,基于以上技术难点,迫切需要一种高效稳定并且相对简洁的生物油制备方法,在降低生物油含氧量、提高其热值的同时,保证过程的高效稳定,并且维持过程的技术经济性。技术实现要素:本发明的目的是提出一种生物质热解或催化裂解制备生物油并在线优化其品质的方法,利用廉价的活性自由基供体辅助生物质进行热裂解,优 化生物质的加工处理特性,在生物质裂解过程中提供活性氢和其他活性自由基等载体,大幅度降低生物质热解中间产物聚合度,降低其粘度和酸度等,并降低生物油中的含氧量,提高生物油产率,并且改善生物油的部分理化性质。本发明提出的生物质热解或催化裂解制备生物油并在线优化其品质的方法,根据几个示例性实施方案,将生物质热解的方法包括利用醇类物质或其溶液与生物质共热解或与生物质热解产物共催化裂解。本发明公开了一种醇类物质与生物质共热解的方法,其主要特征在于,在生物质热解或热解产物催化裂解反应过程中,加入一定量醇类物质作为活性自由基及氢的供体,使得醇类裂解产生的活性自由基与热解自由基结合,从而起到稳定热解中间产物、降低热解积碳量、降低热解产品粘度的作用;同时,作为氢供体,醇类物质在热解或催化裂解过程可为反应体系提供氢源,以起到热解产物加氢、脱氧等作用。本发明所述生物质热解反应包括在无氧或缺氧条件下将生物质热转化为液体或气体产物的过程(具体可包括旋转锥闪速热解、流化床快速热解、固定床热解、移动床热解、微波热解);所述催化裂解是将热解产物在催化剂存在下进行二次催化裂解的过程(具体可包括热解产物二次催化裂解、热解气相产物在线连续催化裂解)。本发明所述醇类物质至少包括甲醇、乙醇、丙醇、丁醇或它们的同系物的纯物质或溶液中的一种。本发明所述醇类物质参与热解反应方式至少包括以下方式其中一种:与生物质原料混匀后进入热解反应器4参与热解反应、随热解载气进入热 解反应器4、独立进入热解反应器4;所述醇类物质参与催化裂解反应方式至少包括以下方式其中一种:随载气进入催化重整反应段5或催化重整反应器9、独立进入热解反应段5或催化重整反应器9、与生热解液相产物混匀后进共同进入催化裂解反应器。根据一示例性实施方案,本发明提供将生物质热解或催化裂解制备生物油并在线优化其品质的方法,所述方法包括使包含生物质的原料与含醇类物质以预定比例混匀,然后将含醇类物质和生物质的原料输入含有脱氧催化剂或热固载体的热解反应器4中,快速完成热解反应,所生成的热解产物即为初级热解油。根据另一示例性实施方案,本发明提供将生物质热解或催化裂解制备生物油并在线优化其品质的方法,所述方法包括使包含生物质的原料连续输入以获取液相产物为目的的热解反应器4中,进行快速热解,同时在原料的热解区域连续按照预设比例输入醇类物质,预定的醇类物质加入比例由含醇类物质的纯品或溶液的质量流速与生物质原料的质量流速确定。根据另一示例性实施方案,本发明提供将生物质热解或催化裂解制备生物油并在线优化其品质的方法,所述方法包括使包含生物质的原料连续输入以获取液相产物为目的的热解反应器中,进行快速热解,将热解气相产物经旋风分离器6分离出灰分后引入另一催化重整反应器9,在催化剂存在下进行催化裂解,以实现脱氧为目的。在催化重整反应器9内,连续按照预设比例输入醇类物质,预定的醇类物质加入比例由含醇类物质的纯品或溶液的质量流速与生物质热解气相产物和催化剂的质量流速确定。本发明所述醇类物质与生物质共热解的方法,其特征在于:所述醇类 物质用量(或质量流率)为原料质量(或质量流率)的1%-200%。本发明所述热解过程中所用载气为惰性气体或能在热解过程提供氢源或改变反应体系饱和蒸汽压的气体,至少包括水蒸气、N2、CO、CH4、H2、乙醇(气)、甲醇(气)中的一种。在热解或催化裂解反应中添加促进醇类物质分解产生活性自由基的催化剂(如Cu/ZrO2,CuO/ZrO2等)。本发明所述热解过程采用热载体,包括石英砂、微球催化剂等。本发明所述催化热解过程采用填料负载型催化剂,所用填料为惰性硬质骨架材料,至少包括多孔陶瓷、蜂窝陶瓷、磁环中的一种;所述催化剂包括各类分子筛、改性分子筛、负载型金属催化剂等中的一种或它们的复合。采用本发明所述方法所制得的液相热解产品或催化裂解产品可用于深度加氢制取高级烃燃料、直接用作燃料油或用于合成或直接提取其他化学品。附图说明图1为一种实施例的流化床快速热解反应器结构示意图。图2为另一种实施例的流化床快速热解反应器结构示意图。其中:1、载气进入管路,2、螺旋输料器,3、醇类物质进入管路,4、热解反应器,5、催化重整反应段,6、旋风分离器,7、冷凝器,8、产物排出管路,9、催化重整反应器,10、醇类物质进入口,11、热解反应扩大段。具体实施方式以下详述在性质上仅为示例性的,且不限制本发明或本发明的应用和使用。实施例1:将100g干燥后玉米芯粉末原料(粒径0.5-1mm)由螺旋输料器2连续送入流化床快速热解反应器4,如图1所示,输料速率为7-8g/min,流化床床料为石英砂。热解反应器4上部为陶瓷负载的ZSM-5催化剂,用于催化裂解热解反应所产生的气体产物。热解载气为20%乙醇溶液蒸汽,由热解反应器4底部进入,质量流量为10g/min。流化床反应器内热解和催化裂解温度为500℃。所得热解液相产品组成如表1所示。表1生物质与乙醇溶液共热解有机液相产品结果载气条件有机酸酮呋喃酚烃苯并呋喃其他20wt%乙醇3.0%16.2%3.2%33.1%33.0%6.9%4.6%5wt%乙醇4.2%24.5%4.6%52.0%4.5%10.2%0.0%显然,随热解气氛下乙醇量的增大,热解产品中烃类组分大幅增加,并其导致热解油产品稳定性差的呋喃、酮以及有机酸的组分大幅减少。实施例2:将100g干燥后玉米芯粉末原料(粒径0.5-1mm)由螺旋输料器2连续送入流化床快速热解反应器4,如图2所示,输料速率为7-8g/min,流化床床料为石英砂。热解反应器4上部催化重整反应段5为陶瓷负载的ZSM-5催化剂,用于催化裂解热解反应所产生的气体产物。热解载气为氮气,由热解反应器4底部进入,体积流量为30L/min,无水乙醇由热解反应扩大段11的下部进入,质量流率为2g/min。流化床反应器内热解和催化裂解温度为500℃。所得热解液相产品组成如表2所示。表2生物质与乙醇溶液共催化裂解有机液相产品结果载气条件有机酸酮呋喃酚烃苯并呋喃其他无水乙醇1.2%36.07%12.7%1.7%46.9%00.6%实施例3:将100g玉米秸秆稀酸水解后粉末原料(水解过程去除半纤维素,粒径0.5-1mm,纤维素含量53%,木质素含量40%,其他杂质7%)由螺旋输料器2连续送入流化床快速热解反应器4,如图1所示,输料速率为7-8g/min,流化床床料为石英砂。热解反应器4上部催化重整反应段5为陶瓷负载的ZSM-5催化剂,Si/Al=25,用于催化裂解热解反应所产生的气体产物。热解载气为10%乙醇水溶液加热所产生的过热蒸汽,由热解反应器4底部进入,体积流量为33L/min。流化床反应器内热解和催化裂解温度为550℃。所得热解液相产品组成如表3所示。表3生物质与乙醇溶液共催化裂解有机液相产品结果载气条件有机酸酮呋喃酚烃苯并呋喃其他无水乙醇013.5%8.7%21.7%40.1%7.4%8.6%上述实施例只为说明本发明的技术构思及特点,其目的在于让熟悉此项技术的人士能够了解本发明的内容并据以实施,并不能以此限制本发明的保护范围。凡根据本发明精神实质所作的等效变化或修饰,都应涵盖在本发明的保护范围之内。当前第1页1 2 3