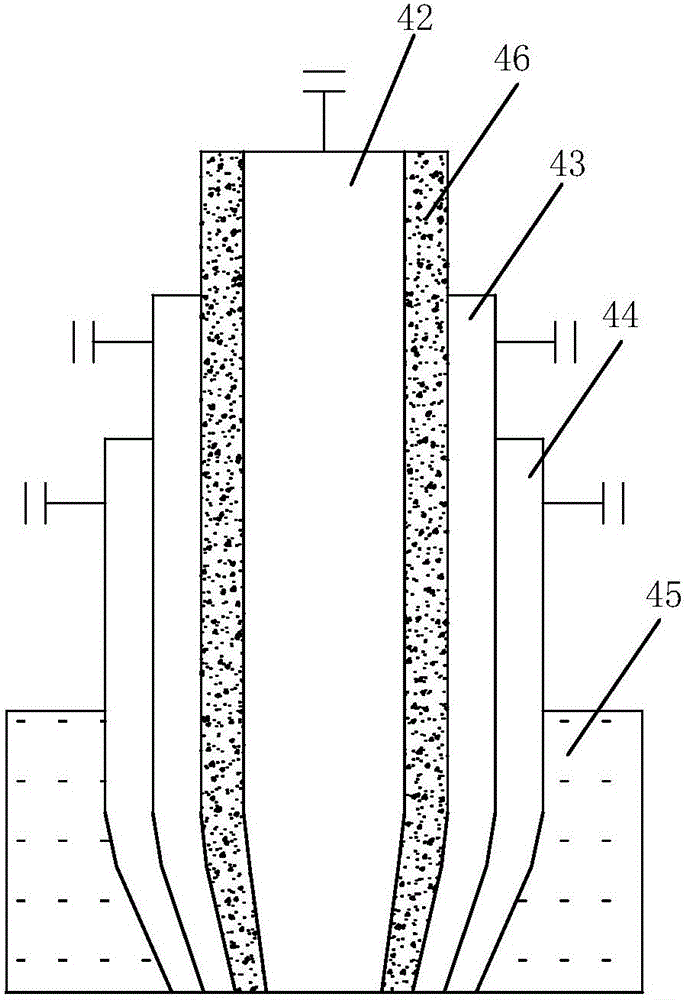
本发明涉及一种化工设备及反应方法,具体指一种煤加氢反应装置及反应方法。
背景技术:
:煤直接加氢工艺过程主要包括煤的破碎与干燥、煤浆制备、加氢液化、固液分离、气体净化、液体产品分馏和精制以及制氢等部分。主要流程为:在高温高压下,高浓度煤浆中的煤发生热解,在催化剂作用下进行加氢和分解,最终成为稳定的液体分子。液化过程中,将煤、催化剂和循环油制成的煤浆,与制得的氢气混合送入反应器。在液化反应器内,煤首先发生热解反应,生成自由基“碎片”,不稳定的自由基“碎片”再与氢在催化剂存在条件下结合,形成分子量比煤低得多的初级加氢产物。出反应器的产物构成十分复杂,包括气、液、固三相。气相的主要成分是氢气,分离后循环返回反应器重新参加反应;固相为未反应的煤、矿物质及催化剂;液相则为轻油(粗汽油)、中油等馏份油及重油。液相馏份油经提质加工(如加氢精制、加氢裂化和重整等)得到合格的汽油、柴油和航空煤油等产品。重质的液固淤浆经进一步分离得到重油和残渣,重油作为循环溶剂用于煤浆制备。现有的煤直接液化技术中,反应器反应压力高达17MPa-30Mpa,氢耗量高达6%-10%,流程复杂,投资成本高。工艺过程中不仅要补充大量新氢,还需要循环油作供氢溶剂,装置生产能力降低,出液化反应器的产物组成复杂,固液两相分离困难,产油率低。技术实现要素:本发明所要解决的技术问题是针对现有技术的现状提供一种反应条件温和且氢耗量小、产油率高的煤加氢反应装置。本发明所要解决的另一个技术问题是针对现有技术的现状提供一种反应条件温和且氢耗量小、产油率高的煤直接加氢反应方法。本发明解决上述技术问题所采用的技术方案为:该煤加氢反应装置,其特征在于包括气化室,所述气化室的侧壁上设有用于向所述气化室内加料的气化喷嘴;所述气化室的顶部通过管道连接旋风反应器,所述管道的侧壁上设有蒸汽喷嘴;所述旋风反应器的侧壁上设有用于向所述旋风反应器内加料的粉煤喷嘴,所述旋风反应器的顶部设有油气出口,所述旋风反应器的底部设有煤焦出口;所述气化室的底部出口连接下降管,所述下降管连通冷却室,所述冷却室的底部设有煤渣出口;所述下降管连接激冷装置,所述激冷装置连接设置在壳体侧壁上的激冷水入口。所述气化喷嘴包括第一本体,第一本体上由内而外依次设有燃料通道、氧气通道、蒸汽通道和第一冷却通道;燃料通道与氧气通道之间的隔层采用耐磨材料制备;所述煤焦出口通过气相输送装置连接所述燃料通道。所述气相输送装置包括依次连接的第一管道、放料罐、第二管道、给料罐和连接所述气化喷嘴的第三管道;所述第一管道连接所述旋风分离器的底部出口;所述第一管道和所述第二管道上分别设有第一控制阀和第二控制阀;所述放料罐、给料罐和所述第三管道均连接输送气源。所述粉煤烧嘴包括第二本体,所述第二本体上设有粉煤通道,所述粉煤通道外设有第二冷却通道。所述旋风反应器的下部设有用于储存煤焦的储焦室,所述煤焦出口设置在所述储焦室的底部。所述的煤加氢反应装置的煤加氢反应方法,其特征在于包括下述步骤:燃料、氧气和水蒸汽自所述气化喷嘴进入所述气化室,在1000~1700℃、1~9MPa下进行反应,生成以CO+H2为主要组成的高温高压合成气;温度为1000~1700℃、压力为1~9MPa的高温高压合成气从所述气化室的顶部出口进入所述管道,与来自所述蒸汽喷嘴的蒸汽反应,进一步增加合成气中的氢含量;煤粉通过所述粉煤喷嘴进入所述旋风反应器,与来自所述管道的温度为1000~1700℃、压力为1~9MPa高温高压合成气在600~1500℃、1~9MPa下进行煤加氢反应,生成油气和煤焦;油气从所述油气出口排出,煤焦储存在所述煤焦室内,定期从所述煤焦出口排出,煤焦通过气相输送装置加压后送入气化喷嘴4;控制所述进入气化喷嘴的煤焦与进入粉煤喷嘴的煤粉质量比例为0.4~0.7:1;进入所述气化室的合成气流速为0.5~1.5m/s;进入所述旋风分离器内的氢气占干基煤粉的质量比为4~10%;控制所述旋风分离器内气速为1~3m/s。所述燃料选自甲烷、液化石油气或生物质燃料。与现有技术相比,本发明所提供的煤加氢反应装置及反应方法能够在相对温和的条件下对煤粉进行分级利用;将煤中的轻组分直接热解加氢,无需催化剂和制浆,得到的挥发份用来制备合成油,煤中的重组分即煤焦进行燃烧为装置提供热量和氢;本发明将煤制氢和加氢集成在一起,系统不需要外设煤制氢装置,简化了反应流程,煤的利用充分、合理,能耗低,减少环境污染,工艺流程简单,煤加氢反应是通过气相反应实现的,反应速率快,转化率高,油收率高。附图说明图1为本发明实施例示意图;图2为本发明实施例中气化喷嘴的剖视示意图;图3为本发明实施例中粉煤喷嘴的剖视示意图。具体实施方式以下结合附图实施例对本发明作进一步详细描述。如图1至图3所示,该一种煤加氢反应装置包括气化室1,气化室1的侧壁上设有用于向气化室内加料的气化喷嘴4;气化喷嘴可以是一个,也可以是多个。气化室1的顶部通过管道2连接旋风反应器3,管道2的侧壁上设有蒸汽喷嘴6;旋风反应器3的侧壁上设有用于向旋风反应器3内加料的粉煤喷嘴5,旋风反应器3的顶部设有油气出口31,旋风反应器3的底部设有煤焦出口32;气化室1的底部出口连接下降管7,下降管7连通冷却室8,冷却室8的底部设有煤渣出口81;壳体的侧壁上设有激冷水入口12激冷水入口连接激冷装置9,通过激冷装置9向下降管7的侧壁通激冷水,保护下降管,同时控制激冷室内温度(壳体为何表示出两层:壳体为常规水冷壁结构。内层是指水冷壁,外层是指外壳)。气化喷嘴4包括第一本体,第一本体上由内而外依次设有燃料通道42、氧气通道43、蒸汽通道44和第一冷却通道45;燃料通道42与氧气通道43之间的隔层46采用耐磨材料制备;所述煤焦出口32通过气相输送装置8连接燃料通道42。气相输送装置8包括按煤焦输送方向依次连接第一管道81、放料罐84、第二管道82、给料罐85和连接所述气化喷嘴4的第三管道83;第一管道81连接旋风分离器1的底部出口;所述第一管道81和所述第二管道82上分别设有第一控制阀86和第二控制阀87;放料罐84、给料罐85和第三管道83均连接输送气源。粉煤烧嘴5包括第二本体51,所述第二本体51上设有粉煤通道52,所述粉煤通道52外设有第二冷却通道53。所述旋风反应器3的下部设有用于储存煤焦的储焦室33,所述煤焦出口32设置在所述储焦室33的底部。使用上述煤加氢反应装置的煤加氢反应方法,包括下述步骤:燃料、氧气和水蒸汽自所述气化喷嘴4进入所述气化室1,在1300℃、4MPa下进行反应,生成以CO+H2为主要组成的高温高压合成气;温度为1300℃、压力为4MPa的高温高压合成气从气化室1的顶部出口进入所述管道2,与来自蒸汽喷嘴6的蒸汽在1500℃、4MPaG下反应:CO+H2O=CO2+H2;进一步增加合成气中的氢含量;煤粉通过所述粉煤喷嘴5进入所述旋风反应器3,与来自管道2的温度为1000~1700℃、压力为3.8MPa高温高压合成气在1300℃、3.8MPa下进行煤加氢反应,生成油气和煤焦;油气从所述油气出口31排出,煤焦储存在煤焦室33内,定期从煤焦出口排出。当旋风式反应器下部的煤焦储存到焦放料罐容积的85%左右后,将放料罐84泄压至与旋风式反应器压力相同,打开第一阀门86将煤焦排放至放料罐84,放料完毕后关闭第一阀门86。然后用氮气或二氧化碳向放料罐84内充压至与给料罐85内压力相同;打开第二阀门87,煤焦进入给料罐85。给料罐85内的煤焦通过惰性输送气气相输送至气化烧嘴4,给料罐85内压力比气化室1内的压力高1.0MPa。放料罐下部、给料罐下部和输焦管线均连接气体输入装置(图中未示出)。正常情况下不需要添加燃料,进入气化室的燃料仅仅是煤焦;装置开车时可以根据需要添加其它燃料;燃料选自甲烷、液化石油气、生物质燃料等。进入气化喷嘴4的煤焦与进入粉煤喷嘴5的干基煤粉的质量比例为0.6。控制气化室1合成气流速为1m/s,温度为1500℃,压力4MPa;旋风分离器3内气速2m/s,温度1300℃,压力3.8MPa。本实施例和现有技术的对比如表1所示。表1煤炭直接液化煤炭间接液化煤炭干馏实施例耗煤量3.5吨/吨油品4吨/吨油品25吨/吨油品3.34吨/吨油品氢气来源制氢装置制氢装置-------不需外加氢气当前第1页1 2 3