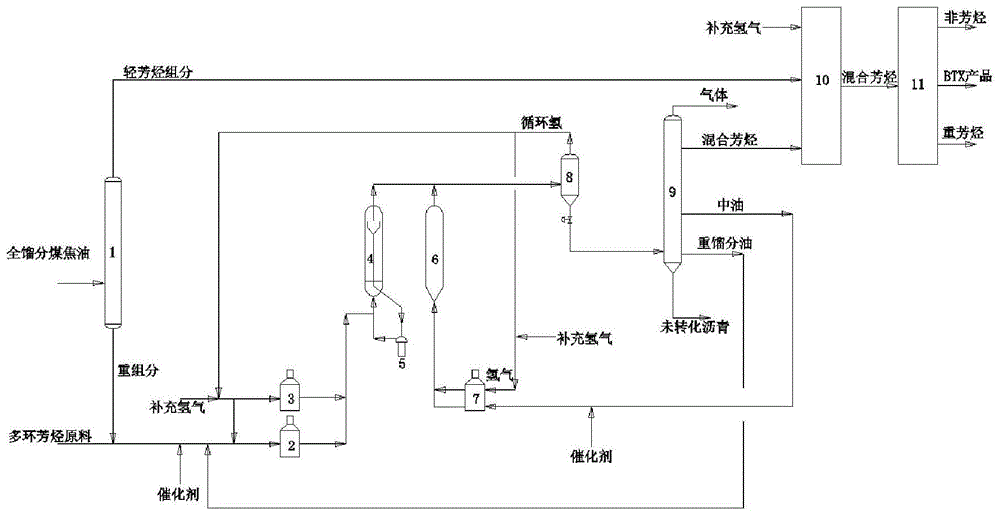
本发明属于轻质芳烃生产
技术领域:
,涉及一种富含多环芳烃的原料分级临氢热解制取轻质芳烃的生产系统及方法,尤其涉及一种富含多环芳烃原料高温高压分级临氢热解制轻质芳烃的生产系统及生产方法。
背景技术:
:随着世界经济的飞速发展,人们对各种各样化工原料的需求也不断增加,其中BTX(苯、甲苯、二甲苯)等轻质芳烃作为重要的基础化工原料,一直以来是全球市场长期旺盛需求的产品。目前的生产现状来看,BTX芳烃主要来自石脑油馏分催化重整和裂解汽油,由于原油价格上涨,石油芳烃生产原料供应紧张,开拓经济可行的芳烃生产新途径是增产芳烃亟需待解决的问题。煤焦油、催化油浆等一些富含多环芳烃原料采用轻质化技术可生产高芳潜值的石脑油馏分,也开始逐步成为生产BTX产品的来源。当前富含多环芳烃原料制取轻质芳烃均采用加氢精制/加氢裂化——石脑油催化重整——芳烃抽提工艺生产BTX产品。CN103865577A公开了一种由催化裂化柴油生产轻质芳烃及清洁燃料油品的方法,所述方法包括如下步骤:1)将催化裂化柴油与氢气混合,与裂化产物混合后同时进行加氢精制反应,以脱除硫氮杂质,并进行烯烃饱和及芳烃加氢饱和;2)加氢精制后催化柴油馏分油进行切割,其中>355℃的馏分油与氢气混合后返回进行加氢裂化;3)对于切割后馏分油进行抽提,得到富含多环芳烃的抽出油和富含烷烃的抽余油;4)富含烷烃抽余油作为清洁柴油调和组分;5)富含芳烃抽出油加氢裂化反应生产轻质芳烃及清洁汽油调和组分;6)抽出油加氢裂化产物经切割分离,>195℃的馏分油作为清洁柴油调和组分;<195℃的馏分油得到轻质芳烃产品和清洁汽油调和组分。在加氢精制/加氢裂化过程中,将部分多环芳烃裂化成小分子芳烃,同时进行芳烃加氢饱和反应生成单环环烷烃;随后再通过石脑油重整脱氢生产富含轻质芳烃的芳烃产品。此工艺流程长,为了生产BTX产品,在加氢和重整工艺中反复进行芳烃加氢饱和及环烷烃重整脱氢的反应,芳烃产率低、能效利用率低。CN106701181A公开了一种全馏分中低温煤焦油加氢制取轻质芳烃的方法及装置,该方法包括:(1)全馏分中低温煤焦油进入分馏塔进行分馏,得到从分馏塔底部分馏得到物流Ⅱ以及从分馏塔顶部分馏得到的物流Ⅰ;物流Ⅰ直接进入步骤(2);物流Ⅱ直接进入步骤(3);(2)将步骤(1)所得到的物流Ⅰ根据常规工艺制备得到轻质芳烃;(3)将步骤(1)得到的物流Ⅱ进行加氢裂化,并将加氢裂化后的物流输送至步骤(2)根据常规工艺制备轻质芳烃。CN104560174A公开了一种重油加氢转化方法,包括临氢热裂化、加氢裂化和加氢处理单元:重油先在第一反应器进行临氢热裂化反应;反应产物分离为轻馏分油、重馏分油和渣油;其中渣油与临氢热裂化催化剂、氢气进入第二反应器,进一步临氢热裂化反应;所述重馏分油和氢气进入加氢裂化反应器,与加氢裂化催化剂接触,在加氢裂化条件下进行加氢裂化反应得到轻质油;所述轻馏分油和氢气进入加氢精制反应器,与加氢精制催化剂接触并反应得到加氢精制后的轻馏分油;其中临氢热裂化第二反应器的反应温度比第一反应器的反应温度低5~50℃。针对当前的富含多环芳烃原料制轻质芳烃工艺技术流程长,芳烃产率低、能效低的不足,亟需对现有技术进行改进以解决上述技术问题。技术实现要素:针对现有技术存在的不足,本发明的目的在于提供一种富含多环芳烃的原料分级临氢热解制取轻质芳烃的生产系统及方法,以物质结构定向转化为原则,采用分子分割技术分级临解热解的方式,首先在一级临氢热解反应过程中将富含多环芳烃原料临氢热解生成2~4环芳烃为主的中油,然后在二级临氢热解反应过程中将中油裂化生成富含轻质芳烃的混合芳烃,随后通过混合芳烃加氢精制及芳烃抽提工艺生产单环轻质芳烃产品。本发明提供了一种富含多环芳烃原料,经过高温高压分级临氢热解后再经低压加氢精制,无需通过催化重整,可直接制取轻质芳烃。为达此目的,本发明采用以下技术方案:第一方面,本发明提供了一种富含多环芳烃的原料分级临氢热解制取轻质芳烃的生产系统,所述的生产系统按照工艺流程包括依次布置的原料分馏装置、一级临氢热解单元、二级临氢热解单元、分离装置、产物分馏装置、混合芳烃加氢精制反应单元和芳烃抽提装置。所述原料分馏装置顶部的轻组分出口连接所述混合芳烃加氢精制反应单元的轻组分入口,所述原料分馏装置底部的重组分出口连接所述一级临氢热解单元的进料口。所述一级临氢热解单元的出料口与二级临氢热解单元的出料口均连接所述分离装置的进料口;所述分离装置的底部出料口连接所述产物分馏装置的进料口;所述产物分馏装置的混合芳烃出口连接所述混合芳烃加氢精制反应单元的混合芳烃入口;所述混合芳烃加氢精制反应单元的出料口连接所述芳烃抽提装置的进料口。本发明提供了一种富含多环芳烃的原料分级临氢热解制取轻质芳烃的生产系统,采用高温高压分级临氢热解的方式,首先在一级临氢热解反应过程中将富含多环芳烃原料临氢热解生成2~4环芳烃为主的中油,然后在二级临氢热解反应过程中将中油裂化生成富含BTX(苯、甲苯、二甲苯)的混合芳烃,随后通过混合芳烃加氢精制及芳烃抽提工艺生产轻质芳烃BTX(苯、甲苯、二甲苯)产品。作为本发明一种优选的技术方案,所述的一级临氢热解单元包括依次串联的1~3台一级临氢热解装置。优选地,所述的一级临氢热解装置包括循环连接的一级临氢热解反应器和反应循环泵。优选地,所述的一级临氢热解反应器选自移动床反应器、沸腾床反应器、强制循环悬浮床反应器或无强制循环悬浮床反应器中的任意一种,进一步优选地,所述的一级临氢热解反应器为强制循环悬浮床反应器。优选地,所述的一级临氢热解反应器的壳体下部设置有循环出料口,所述的一级临氢热解反应器的壳体底部设置有回料口,所述反应循环泵的进料口连接一级临氢热解反应器的循环出料口,所述反应循环泵的出料口连接一级临氢热解反应器的回料口。优选地,所述一级临氢热解反应器的壳体底部还设置有进料口,所述进料口分别独立地连接一级临氢热解氢气进料管路和一级临氢热解原料进料管路。优选地,所述一级临氢热解氢气进料管路的出口和一级临氢热解原料进料管路的出口合并为一路后连接至一级临氢热解反应器的进料口。优选地,所述一级临氢热解氢气进料管路和一级临氢热解原料进料管路上分别独立地设置有加热炉,进一步优选地,所述一级临氢热解氢气进料管路上设置有氢气加热炉,所述一级临氢热解原料进料管路上设置有进料加热炉。优选地,所述一级临氢热解氢气进料管路的入口端通入氢气。优选地,所述一级临氢热解氢气进料管路上还设置有循环氢入口,所述循环氢入口连接所述分离装置顶部的循环氢出口,所述循环氢入口中通入的循环氢与入口端补充的氢气经过氢气加热炉加热后进入一级临氢热解反应器。优选地,所述一级临氢热解原料进料管路入口端通入富含多环芳烃原料。优选地,所述一级临氢热解原料进料管路上设置有至少四组入口,包括重组分入口、重馏分油入口、催化剂入口和补充氢气入口,所述重组分入口连接所述原料分馏装置底部的重组分出口,四组入口通入的物料经过进料加热炉加热后进入一级临氢热解反应器。优选地,所述一级临氢热解氢气进料管路的入口端设置有分支管路,所述分支管路的入口与所述一级临氢热解氢气进料管路共用同一入口,所述分支管路的出口连接所述一级临氢热解原料进料管路的补充氢气入口。作为本发明一种优选的技术方案,所述的二级临氢热解单元包括依次串联的1~2台二级临氢热解反应器。优选地,所述的二级临氢热解反应器为强制循环悬浮床反应器或非强制循环悬浮床反应器,进一步优选为非强制循环悬浮床反应器。优选地,所述的二级临氢热解反应器的壳体底部设置有进料口,所述进料口分别独立地连接二级临氢热解氢气进料管路和二级临氢热解原料进料管路。优选地,所述的二级临氢热解氢气进料管路和二级临氢热解原料进料管路上分别独立地设置有加热炉,进一步优选地,所述二级临氢热解氢气进料管路上设置有氢气加热炉,所述二级临氢热解原料进料管路上设置有进料加热炉。优选地,所述二级临氢热解氢气进料管路和二级临氢热解原料进料管路共用同一个二级临氢热解加热炉。优选地,所述二级临氢热解氢气进料管路的入口端连接所述分离装置顶部的循环氢出口。优选地,所述二级临氢热解氢气进料管路上还设置有补充氢气入口,所述补充氢气入口通入的氢气经过二级临氢热解加热炉加热后进入二级临氢热解反应器。优选地,所述二级临氢热解原料进料管路的入口端连接产物分馏装置的中油出口,所述产物分馏装置分馏得到的中油经过二级临氢热解加热炉加热后进入二级临氢热解反应器。优选地,所述二级临氢热解原料进料管路上还设置有催化剂入口,所述催化剂入口通入的催化剂经过二级临氢热解加热炉加热后进入二级临氢热解反应器。作为本发明一种优选的技术方案,所述一级临氢热解反应器和二级临氢热解反应器的顶部产物出口分别独立连接一台的分离装置。优选地,所述一级临氢热解反应器和二级临氢热解反应器的顶部产物出口连接同一台分离装置。优选地,所述分离装置的壳体顶部设置有循环氢出口,所述循环氢出口分别独立地连接所述一级临氢热解氢气进料管路的循环氢入口和二级临氢热解氢气进料管路的入口端。优选地,所述分离装置的壳体底部设置有出料口,所述出料口连接所述产物分馏装置的进料口。优选地,所述分离装置为热高压分离罐、热中压分离罐、温高压分离罐、温中压分离罐、冷高压分离罐或冷低压分离罐中的任意一种或至少两种的组合。本发明对分离装置的具体组成形式不作特殊限定,可以是单独一组分离装置也可以是多组不同性质的分离装置的任意组合,当采用多组分离装置组合时,组合形式及各装置间的连接关系为本领域技术人员公知,本发明对此不作具体要求。一种可选的多级组合式分离装置包括热高压分离罐、温中压分离罐、冷高压分离罐和冷低压分离罐,其中,热高压分离罐的顶部出口连接温高压分离罐的入口,热高压分离罐的底部出口连接热中压分离罐的入口,温高压分离罐的顶部出口连接所述冷高压分离罐的入口,温高压分离罐的底部出口与热中压分离罐的顶部出口均连接所述温中压分离罐的入口,所述冷高压分离罐的出口与温中压分离罐的顶部出口均连接所述冷低压分离罐的入口。但本领域技术人员应理解的是,上述示例性描述的多级组合式分离装置为现有技术所公开,现有技术已公开或新技术中未公开的分离装置或多级组合式分离系统均可用于本发明,对本发明公开的分离装置进行常规变形或对结构进行适应性调整所得到的分离装置或分离系统仍落入本发明的保护范围和公开范围之内。作为本发明一种优选的技术方案,所述的一级临氢热解反应器的顶部产物出口和二级临氢热解反应器的顶部产物出口连接同一台产物分馏装置或分别独立连接不同的产物分馏装置。优选地,优选地,所述产物分馏装置的壳体上由上至下依次设置有气体出口、混合芳烃出口、中油出口、重馏分油出口和未转化沥青出口。优选地,所述的中油出口连接所述的二级临氢热解原料进料管路的入口端。优选地,所述的重馏分油出口连接所述一级临氢热解原料进料管路上的重馏分油入口。作为本发明一种优选的技术方案,所述的混合芳烃加氢精制反应单元包括依次串联的1~2台混合芳烃加氢精制反应器。优选地,所述的混合芳烃加氢精制反应器的壳体上设置有补充氢气入口、轻芳烃组分入口、混合芳烃入口和加氢产物出口,所述的轻芳烃入口连接所述原料分馏装置顶部的轻芳烃组分出口,所述的混合芳烃入口连接所述产物分馏装置的混合芳烃出口。优选地,所述的混合芳烃加氢精制反应器为固定床加氢反应器。优选地,所述的芳烃抽提装置的壳体上设置有非芳烃出口、BTX芳烃出口、重芳烃出口和加氢产物入口,所述加氢产物入口连接所述混合芳烃加氢精制反应器的加氢产物出口。第二方面,本发明提供了一种富含多环芳烃的原料分级临氢热解制取轻质芳烃的方法,所述的方法在第一方面所述的富含多环芳烃的原料分级临氢热解制取轻质芳烃的生产系统中进行,所述方法包括:(Ⅰ)富含多环芳烃原料在原料分馏装置中分馏得到轻芳烃组分和重组分,将氢气、催化剂以及分馏得到的重组分和/或富含多环芳烃原料混合后通入一级临氢热解单元进行一级临氢热解反应得到一级临氢热解产物;(Ⅱ)氢气、催化剂以及步骤(Ⅰ)得到的一级临氢热解产物中的中油混合后通入二级临氢热解单元中进行二级临氢热解反应得到二级临氢热解产物;(Ⅲ)步骤(Ⅰ)得到的一级临氢热解产物与步骤(Ⅱ)得到的二级临氢热解产物混合后通入分离装置,分离得到高压气体和低压油气;(Ⅳ)步骤(Ⅲ)得到的低压油气进入产物分馏装置分离得到气体、混合芳烃、中油、重馏分油和未转化沥青;(Ⅴ)步骤(Ⅳ)得到的混合芳烃与氢气和/或步骤(Ⅰ)中得到的轻芳烃组分混合后通入混合芳烃加氢精制反应单元进行加氢精制得到精制混合芳烃,精制混合芳烃通入芳烃抽提装置中经芳烃抽提后得到所述的轻质芳烃。本发明提供了一种富含多环芳烃原料,经过高温高压分级临氢热解后再经低压加氢精制,无需通过催化重整,可直接制取轻质芳烃。具体地,将富含多环芳烃原料、催化剂、氢气、产物分馏装置分离得到的重馏分油以及原料分馏装置分离得到的重组分混合后通入一级临氢热解单元中进行临氢热解反应,反应流出物与二级临氢热解的反应流出物混合后经高低压分离装置分离得到氢气和油气,其中的氢气返回至一级临氢热解单元和二级临氢热解单元中供临氢热解反应循环使用,其中的油气进入产物分馏装置中进行轻重馏分的切割,分离得到气体、混合芳烃(<200℃馏分)、中油(200~430℃馏分)、重馏分油(430~530℃馏分)以及未转化沥青(≥530℃馏分),其中中油作为二级临氢热解的原料,加入少量催化剂与氢气分别加热后一同进入二级临氢热解单元进行裂化反应。如果原料中含有小于C10以下的碳氢化合物,比如全馏分煤焦油,将原料通过原料分馏塔分离出馏程<205℃的轻芳烃组分和≥205℃的重组分,其中的的重组分作为一级临氢热解反应的进料,轻芳烃组分、混合芳烃与氢气混合后通入混合芳烃加氢精制反应单元进行加氢精制反应得到清洁的混合芳烃,随后将清洁的混合芳烃通入芳烃抽提装置得到BTX(苯、甲苯、二甲苯)产品。示例性地,本发明提供了一种具体的轻质芳烃生产方法:(1)富含多环芳烃原料(如有分子量小于C10以下的碳氢化合物)经原料分馏塔蒸馏后,得到馏程<205℃的轻芳烃组分和馏程≥205℃的重组分;(2)富含多环芳烃原料,或者是步骤(1)中得到的≥205℃的重组分,与氢气和催化剂经加热炉升温后一起通入一级临氢热解反应器中进行一级临氢热解反应得到一级临氢热解产物;临氢热解产物中的中油馏分与氢气和催化剂经加热炉升温后一起通入二级临氢热解反应器中进行二级临氢热解反应得到二级临氢热解产物;(3)步骤(2)中得到的一级临氢热解产物与二级临氢热解产物混合后进入高低压分离装置,分离得到高压气体和低压油气;(4)步骤(3)中得到的高压气体作为循环氢返回至一级临氢热解反应器和二级临氢热解反应器中,低压油气进入产物分馏装置。产物分馏装置采用常压及减压蒸馏的方式,分离得到气体、混合芳烃、中油、重馏分油及未转化沥青;(5)步骤(4)中得到的重馏分油返回至一级临氢热解反应器中,与富含多环芳烃原料和/或步骤(1)中得到的馏程≥205℃的重组分混合作为一级临氢热解进料,进行一级临氢热解反应;步骤(4)中得到的中油通入二级临氢热解反应器进行一级临氢热解反应;(6)步骤(4)中得到的混合芳烃和/或步骤(1)得到的馏程<205℃轻芳烃组分混合后经混合芳烃加氢精制反应器脱除S、N、O及部分选择性加氢裂化后得到清洁的精制混合芳烃;(7)步骤(6)中得到的精制混合芳烃,经芳烃抽提装置抽提后得到BTX(苯、甲苯、二甲苯)产品。作为本发明一种优选的技术方案,步骤(Ⅰ)所述的多环芳烃原料为全馏分煤焦油、重质煤焦油馏分、催化油浆、煤、富含多环芳烃的重劣质原油、油砂、页岩油、重劣质常减压渣油或脱油沥青中的一种或至少两种的组合。优选地,所述的混合过程包括:(1)催化剂、部分氢气以及分馏得到的重组分和/或多环芳烃原料混合后经进料加热炉升温,其余氢气经氢气加热炉升温;(2)将上述升温后的氢气、催化剂以及分馏得到的重组分和/或多环芳烃原料混合后通入一级临氢热解反应器。优选地,所述分馏得到的轻芳烃组分的馏程<205℃。优选地,所述分馏得到的重组分的馏程≥205℃。优选地,所述一级临氢热解反应的温度为380~465℃,例如可以是380℃、390℃、400℃、410℃、420℃、430℃、440℃、450℃、460℃或465℃。优选地,所述一级临氢热解反应的压力为10~30MPaG,例如可以是10MPaG、11MPaG、12MPaG、13MPaG、14MPaG、15MPaG、16MPaG、17MPaG、18MPaG、19MPaG、20MPaG、21MPaG、22MPaG、23MPaG、24MPaG、25MPaG、26MPaG、27MPaG、28MPaG、29MPaG或30MPaG。优选地,所述一级临氢热解反应的氢油比500~2000,例如可以是500、600、700、800、900、1000、1100、1200、1300、1400、1500、1600、1700、1800、1900或2000,进一步优选地,所述一级临氢热解反应的氢油比为500~1000。作为本发明一种优选的技术方案,步骤(Ⅱ)所述的混合过程包括:(1)催化剂和一级临氢热解产物中的中油混合后经二级临氢热解加热炉升温,补充氢气经二级临氢热解加热炉升温;(2)将上述升温后的氢气、催化剂以及一级临氢热解产物中的中油混合后通入二级临氢热解反应器。优选地,所述二级临氢热解反应的温度为450~550℃,例如可以是450℃、460℃、470℃、480℃、490℃、500℃、510℃、520℃、530℃、540℃或550℃。优选地,所述二级临氢热解反应的压力为10~30MPaG,例如可以是10MPaG、11MPaG、12MPaG、13MPaG、14MPaG、15MPaG、16MPaG、17MPaG、18MPaG、19MPaG、20MPaG、21MPaG、22MPaG、23MPaG、24MPaG、25MPaG、26MPaG、27MPaG、28MPaG、29MPaG或30MPaG。优选地,所述二级临氢热解反应的氢油比为500~2000,例如可以是500、600、700、800、900、1000、1100、1200、1300、1400、1500、1600、1700、1800、1900或2000,进一步优选地,所述二级临氢热解反应的氢油比为1200~2000。作为本发明一种优选的技术方案,步骤(Ⅲ)所述的高压气体为氢气。优选地,将步骤(Ⅲ)分离得到的高压气体返回至步骤(Ⅰ)和步骤(Ⅱ)中作为补充氢气使用。优选地,将步骤(Ⅳ)分离得到的重油馏分返回步骤(Ⅰ)中作为多环芳烃原料使用。优选地,将步骤(Ⅳ)分离得到的中油返回步骤(Ⅱ)中作为二级临氢热解反应原料使用。优选地,步骤(Ⅳ)所述的产物分馏装置采用常压和减压蒸馏方式分离低压油气。优选地,步骤(Ⅳ)中对低压油气进行分馏,所述分馏过程中各温度对应馏分为:温度<200℃的馏分为混合芳烃,温度为200~430℃的馏分为中油,温度为430~530℃的馏分为重馏分油,温度≥530℃的馏分为未转化沥青。优选地,步骤(Ⅴ)所述加氢精制的反应温度为150~400℃,例如可以是150℃、200℃、250℃、300℃、350℃或400℃。优选地,步骤(Ⅴ)所述加氢精制的反应压力为2~6MPaG,例如可以是2MPaG、3MPaG、4MPaG、5MPaG或6MPaG。优选地,步骤(Ⅴ)所述加氢精制的氢油比为500~1000,例如可以是500、550、600、650、700、750、800、850、900、950或1000。本发明所述的数值范围不仅包括上述例举的点值,还包括没有例举出的上述数值范围之间的任意的点值,限于篇幅及出于简明的考虑,本发明不再穷尽列举所述范围包括的具体点值。与现有技术相比,本发明的有益效果为:本发明采用高温高压分级临氢热解的方式,首先在一级临氢热解反应过程中将富含多环芳烃原料临氢热解生成2~4环芳烃为主的中油,然后在二级临氢热解反应过程中将中油裂化生成富含BTX(苯、甲苯、二甲苯)的混合芳烃,随后通过混合芳烃加氢精制及芳烃抽提工艺生产轻质芳烃BTX(苯、甲苯、二甲苯)产品。经过高温高压分级临氢热解后再经低压加氢精制,无需通过催化重整,直接制取轻质芳烃的工艺。附图说明图1为本发明一个具体实施方式提供的轻质芳烃生产系统的工艺流程图。其中,1-原料分馏塔;2-一级临氢热解进料加热炉;3-一级临氢热解氢气加热炉;4-一级临氢热解反应器;5-反应循环泵;6-二级临氢热解反应器;7-二级临氢热解进料加热炉;8-高低压分离装置;9-产物分馏装置;10-混合芳烃加氢精制反应器;11-芳烃抽提装置。具体实施方式下面结合附图并通过具体实施方式来进一步说明本发明的技术方案。在一个具体实施方式中,本发明提供了一种富含多环芳烃的原料分级临氢热解制取轻质芳烃的生产系统,所述的生产系统如图1所示按照工艺流程包括依次布置的原料分馏塔1、一级临氢热解单元、二级临氢热解单元、高低压分离装置8、产物分馏装置9、混合芳烃加氢精制反应单元和芳烃抽提装置11。所述原料分馏塔1顶部的轻组分出口连接所述混合芳烃加氢精制反应单元的轻组分入口,所述原料分馏塔1底部的重组分出口连接所述一级临氢热解单元的进料口。所述一级临氢热解单元的出料口与二级临氢热解单元的出料口均连接所述高低压分离装置8的进料口;所述高低压分离装置8的底部出料口连接所述产物分馏装置9的进料口;所述产物分馏装置9的混合芳烃出口连接所述的混合芳烃加氢精制反应单元的混合芳烃入口;所述混合芳烃加氢精制反应单元的出料口连接所述芳烃抽提装置11的进料口。所述的一级临氢热解单元包括依次串联的1~3台一级临氢热解反应装置,所述的一级临氢热解反应装置包括循环连接的一级临氢热解反应器4和反应循环泵5,所述一级临氢热解反应器4的壳体下部设置有循环出料口,所述一级临氢热解反应器4的壳体底部设置有回料口,所述反应循环泵5的进料口连接所述一级临氢热解反应器4的循环出料口,所述反应循环泵5的出料口连接所述一级临氢热解反应器4的回料口。所述一级临氢热解反应器4的壳体底部还设置有进料口,所述进料口分别独立地连接一级临氢热解氢气进料管路和一级临氢热解原料进料管路,所述一级临氢热解氢气进料管路的出口和一级临氢热解原料进料管路的出口合并为一路后连接至所述一级临氢热解反应器4的进料口。所述一级临氢热解氢气进料管路的入口端通入氢气,所述一级临氢热解氢气进料管路上还设置有循环氢入口,所述循环氢入口连接所述高低压分离装置8顶部的循环氢出口。所述一级临氢热解氢气进料管路上还设置有一级临氢热解氢气加热炉3,所述循环氢入口中通入的循环氢与入口端补充的氢气经过一级临氢热解氢气加热炉3加热后进入一级临氢热解反应器4。所述一级临氢热解原料进料管路入口端通入富含多环芳烃原料,所述一级临氢热解原料进料管路上设置有至少四组入口,包括重组分入口、重馏分油入口、催化剂入口和补充氢气入口,所述重组分入口连接所述原料分馏塔1底部的重组分出口。所述一级临氢热解原料进料管路上还设置有一级临氢热解进料加热炉2,四组入口通入的物料经过一级临氢热解进料加热炉2加热后进入一级临氢热解反应器4。所述一级临氢热解氢气进料管路的入口端设置有分支管路,所述分支管路的入口与所述一级临氢热解氢气进料管路共用同一入口,所述分支管路的出口连接所述一级临氢热解原料进料管路的补充氢气入口。所述的二级临氢热解单元包括依次串联的1~2台二级临氢热解反应器6。所述二级临氢热解反应器6的壳体底部设置有进料口,所述进料口分别独立地连接二级临氢热解氢气进料管路和二级临氢热解原料进料管路。所述二级临氢热解氢气进料管路和二级临氢热解原料进料管路共用一个二级临氢热解进料加热炉7。所述二级临氢热解氢气进料管路的入口端连接所述高低压分离装置8顶部的循环氢出口,所述二级临氢热解氢气进料管路上还设置有补充氢气入口,所述补充氢气入口通入的氢气经过二级临氢热解加热炉7加热后进入二级临氢热解反应器6。所述二级临氢热解原料进料管路的入口端连接产物分馏装置9的中油出口。所述二级临氢热解原料进料管路上还设置有催化剂入口,所述催化剂入口通入的催化剂经过二级临氢热解加热炉7加热后进入二级临氢热解反应器6。所述高低压分离装置8的壳体顶部设置有循环氢出口,所述循环氢出口分别独立地连接所述一级临氢热解氢气进料管路的循环氢入口和二级临氢热解氢气进料管路的入口端。所述高低压分离装置8的壳体底部设置有出料口,所述出料口连接所述产物分馏装置9的进料口。所述产物分馏装置9的壳体上由上至下依次设置有气体出口、混合芳烃出口、中油出口、重馏分油出口和未转化沥青出口。所述的中油出口连接所述的二级临氢热解氢气进料管路的入口端。所述的重馏分油出口连接所述一级临氢热解原料进料管路上的重馏分油入口。所述的混合芳烃加氢精制反应单元包括依次串联的1~2台混合芳烃加氢精制反应器10。所述的混合芳烃加氢精制反应器10的壳体上设置有补充氢气入口、轻芳烃组分入口、混合芳烃入口和加氢产物出口,所述的轻芳烃入口连接所述原料分馏塔1顶部的轻芳烃组分出口,所述的混合芳烃入口连接所述产物分馏装置9的混合芳烃出口。所述的芳烃抽提装置11的壳体上设置有非芳烃出口、轻质芳烃出口、重芳烃出口和加氢产物入口,所述加氢产物入口连接所述混合芳烃加氢精制反应器10的加氢产物出口。在另一个具体实施方式中,本发明提供了一种富含多环芳烃的原料分级临氢热解制取轻质芳烃的生产方法,所述的生产方法具体包括如下步骤:(1)富含多环芳烃原料(如有分子量小于C10以下的碳氢化合物)经原料分馏塔1蒸馏后,得到馏程<205℃的轻芳烃组分和馏程≥205℃的重组分;(2)富含多环芳烃原料,或者是步骤(1)中得到的≥205℃的重组分,与氢气和催化剂经加热炉升温后一起通入一级临氢热解反应器4中进行一级临氢热解反应得到一级临氢热解产物;临氢热解产物中的中油馏分与氢气和催化剂经加热炉升温后一起通入二级临氢热解反应器6中进行二级临氢热解反应得到二级临氢热解产物;(3)步骤(2)中得到的一级临氢热解产物与二级临氢热解产物混合后进入高低压分离装置8,分离得到高压气体和低压油气;(4)步骤(3)中得到的高压气体作为循环氢返回至一级临氢热解反应器4和二级临氢热解反应器6中,低压油气进入产物分馏装置9。产物分馏装置9采用常压及减压蒸馏的方式,分离得到气体、混合芳烃、中油、重馏分油及未转化沥青;(5)步骤(4)中得到的重馏分油返回至一级临氢热解反应器4中,与富含多环芳烃原料和/或步骤(1)中得到的馏程≥205℃的重组分混合作为一级临氢热解进料,进行一级临氢热解反应;步骤(4)中得到的中油通入二级临氢热解反应器6进行二级临氢热解反应;(6)步骤(4)中得到的混合芳烃和/或步骤(1)得到的馏程<205℃轻芳烃组分混合后经混合芳烃加氢精制反应器10脱除S、N、O及部分选择性加氢裂化后得到清洁的精制混合芳烃;(7)步骤(6)中得到的精制混合芳烃,经芳烃抽提装置11抽提后得到BTX(苯、甲苯、二甲苯)产品。实施例1本实施例提供了一种富含多环芳烃原料——中低温煤焦油分级临氢热解制备轻质芳烃的方法,所述方法具体包括如下步骤:(1)中低温煤焦油经原料分馏塔1蒸馏后,得到馏程<205℃的轻芳烃组分和馏程≥205℃的重组分,其中,中低温煤焦油的理化特性见表1,煤焦油实沸点切割馏出百分数见表2;(2)步骤(1)中得到的≥205℃的重组分,与氢气和催化剂经加热炉升温后一起通入一级临氢热解反应器4中进行一级临氢热解反应得到一级临氢热解产物;一级临氢热解反应条件为:反应温度440℃,反应压力22MPaG,氢油比700;反应器型式:强制循环悬浮床反应器(带循环泵),数量2台,一级临氢热解反应各参数汇总见表3;(3)临氢热解产物中的中油馏分与氢气和催化剂经加热炉升温后一起通入二级临氢热解反应器6中进行二级临氢热解反应得到二级临氢热解产物;二级临氢热解反应条件为:反应温度500℃,反应压力22MPaG,氢油比1700;反应器型式:一次通过式悬浮床反应器(无强制循环),数量1台,二级临氢热解反应各参数汇总见表3;(4)步骤(2)中得到的一级临氢热解与步骤(3)中得到的二级临氢热解产物混合后进入高低压分离装置8,分离得到高压气体和低压油气;(5)步骤(4)中得到的高压气体作为循环氢返回至一级临氢热解反应器4和二级临氢热解反应器6中,低压油气进入产物分馏装置9。产物分馏装置9采用常压及减压蒸馏的方式,分离得到气体、混合芳烃、中油、重馏分油及未转化沥青;(6)步骤(5)中得到的重馏分油返回至一级临氢热解反应器4中,与步骤(1)中得到的馏程≥205℃的重组分混合作为一级临氢热解进料,进行一级临氢热解反应;步骤(5)中得到的中油通入二级临氢热解反应器6进行二级临氢热解反应;(7)步骤(5)中得到的混合芳烃和步骤(1)得到的馏程<205℃轻芳烃组分混合后经混合芳烃加氢精制反应器10脱除S、N、O及选择性加氢裂化后得到清洁的精制混合芳烃;混合芳烃加氢精制反应条件为:反应温度310℃,反应压力3MPaG,氢油比600;反应器型式:固定床反应器,数量2台;(8)步骤(7)中得到的精制混合芳烃,经芳烃抽提装置11抽提后得到BTX(苯、甲苯、二甲苯)产品,BTX产品的收率为57.34%,产物中其余组分含量见表4。表1表2组分重量,%对干基焦油轻芳烃组分,<205℃馏分5%重组分,≥205℃馏分95%总计100%表3表4实施例2本实施例提供了一种富含多环芳烃原料——减压渣油分级临氢热解制备轻质芳烃的方法,所述方法具体包括如下步骤:(1)减压渣油与氢气和催化剂经加热炉升温后一起通入一级临氢热解反应器4中进行一级临氢热解反应得到一级临氢热解产物;一级临氢热解反应条件为:反应温度440℃,反应压力20MPaG,氢油比600;反应器型式:强制循环悬浮床反应器(带循环泵),数量2台;其中,减压渣油的理化特性见表5,一级临氢热解反应各参数汇总见表6;(2)临氢热解产物中的中油馏分与氢气和催化剂经加热炉升温后一起通入二级临氢热解反应器6中进行二级临氢热解反应得到二级临氢热解产物;二级临氢热解反应条件为:反应温度500℃,反应压力20MPaG,氢油比1500;反应器型式:一次通过式悬浮床反应器(无强制循环),数量1台;二级临氢热解反应各参数汇总见表6;(3)步骤(1)中得到的一级临氢热解产物与步骤(2)中得到的二级临氢热解产物混合后进入高低压分离装置8,分离得到高压气体和低压油气;(4)步骤(3)中得到的高压气体作为循环氢返回至一级临氢热解反应器4和二级临氢热解反应器6中,低压油气进入产物分馏装置9。产物分馏装置9采用常压及减压蒸馏的方式,分离得到气体、混合芳烃、中油、重馏分油及未转化沥青;(5)步骤(4)中得到的重馏分油返回至一级临氢热解反应器4中,与减压渣油混合作为一级临氢热解进料,进行一级临氢热解反应;步骤(4)中得到的中油通入二级临氢热解反应器6进行二级临氢热解反应;(6)步骤(4)中得到的混合芳烃经混合芳烃加氢精制反应器10脱除S、N、O及选择性加氢裂化后得到清洁的精制混合芳烃;混合芳烃加氢精制反应条件为:反应温度310℃,反应压力3MPaG,氢油比600;反应器型式:固定床反应器,数量2台;(7)步骤(6)中得到的精制混合芳烃,经芳烃抽提装置11抽提后得到BTX(苯、甲苯、二甲苯)产品,BTX产品的收率为27.93%,产物中其余组分含量见表7。表5表6表7产物重量收率,%对干基减压渣油气体(H2S、NH3、C1~C4)23.50%生成水0.27%BTX27.93%非芳烃38.85%重芳烃6.58%未转化沥青6.10%合计103.23%申请人声明,以上所述仅为本发明的具体实施方式,但本发明的保护范围并不局限于此,所属
技术领域:
的技术人员应该明了,任何属于本
技术领域:
的技术人员在本发明揭露的技术范围内,可轻易想到的变化或替换,均落在本发明的保护范围和公开范围之内。当前第1页1 2 3