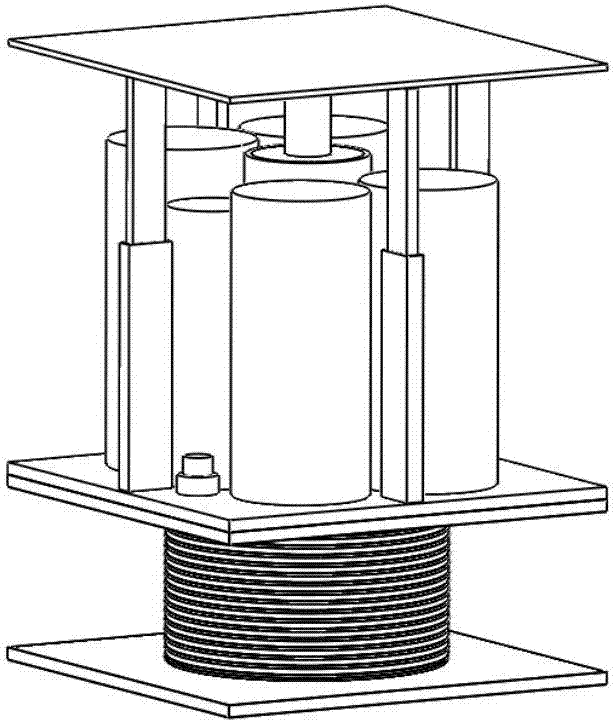
本发明属于土木工程以及机械工程振动控制领域和隔震
技术领域:
,涉及一种具有足够竖向承载力与竖向变刚度控制能力,同时水平向也具有适宜刚度的新型变刚度液压三维隔震装置及方法,适用于工业与民用建筑、桥梁、地铁工程等领域,同时,也可以用于机械设备、仪器等的隔震(振)。
背景技术:
:我国位于环太平洋地震带与欧亚地震带之间,是一个地震多发国。如何减振、隔震以提高建筑、桥梁的抗震性能是进行建筑、桥梁设计的重要问题。在相关
技术领域:
中,采用隔震支座是实现以上目的的有效方法。目前国内外隔震方面的研究主要集中在水平隔震上,隔震装置包括橡胶隔震支座、滑移隔震支座、摩擦摆支座、滚动隔震装置等。已有震害资料和试验表明,竖向地震对结构的动力响应以及非结构构件的破坏有着明显的影响。考虑到日益提高的结构性能化设计需求,研究新型多维隔震技术势在必行。地震作用下,结构的竖向振动控制相对于水平振动控制具有更大的难度。由于结构的竖向刚度一般较大,普通的减振措施(如各类阻尼器)较难发挥有效作用。另外,楼板的振动在结构的竖向振动中存在较大影响,但由于结构开敞空间的需求,较难对楼板施加减振措施。通过在现有的水平隔震基础上,开发三维隔震技术成为解决结构竖向振动的重要途径。在三维隔震方面,国外已有利用密封气体等流体介质实现三维隔震的相关研究,如采用橡胶隔震支座与密封型空气弹簧构成的组合式三维隔震装置。在这些研究中为实现隔震装置的长周期而采取的特别构造等使得支座造价昂贵,主要应用于核工业设施隔震,较难在工程结构领域进行广泛推广。在结构工程领域,国内三维隔震支座的研究主要以蝶形弹簧作为竖向隔震元件。目前,相关的研究还处于理论与试验阶段缺乏实际的工程运用。同时该类装置一般为弹性变形装置,较难实现复杂情况下的分阶段控制,无法兼顾不同周期地震作用下的隔震效果。竖向隔震要求结构竖向刚度尽可能低以延长结构周期,同时结构巨大的自重又完全依靠低刚度的竖向隔震装置承受,增大了隔震支座的设计难度,使得目前研究的三维隔震支座构造较为复杂。技术实现要素:本发明的目的在于提供一种具有足够竖向承载力与竖向变刚度控制能力,同时水平向也具有适宜刚度的新型变刚度液压三维隔震装置及方法,其旨在解决现有隔震支座的不足,即解决常规隔震支座无法隔离竖向地震的问题;解决现有组合式多维隔震装置构造复杂、造价昂贵等问题。同时利用阈值控制手段,实现支座竖向隔震的多级变刚度控制以兼顾不同周期地震作用下的隔震效果。该装置具有合理的连接构造措施防止三维隔震装置发生较大的水平向和竖向位移;同时由于竖向隔震装置的存在,使得支座所承受的竖向力减小,水平向叠层橡胶支座部分的竖向抗拉承载力足以保证三维隔震装置的整体稳定性和工作安全性。本发明的技术方案如下:一种变刚度液压三维隔震装置,包括上部的竖向隔震系统、下部的叠层橡胶支座、减压缸和增压缸及连接部件;竖向隔震系统包括竖向隔震器上联结板1、竖向导轨2、主缸活塞杆3、主缸限位导向套4、主缸底部活塞串联压簧5、主缸底部活塞串联拉簧6、竖向隔震器下联结板8、和主缸顶部封板24;叠层橡胶支座包括叠层橡胶支座上联结板10、钢板层11、橡胶层12、叠层橡胶支座下联结板13;减压缸包括活减压缸塞串联压簧14、减压缸缓冲垫层15、减压缸导向套16、减压缸活塞杆17、减压缸支撑环18和减压缸顶部封板25;增压缸包括增压缸活塞串联压簧19、增压缸缓冲垫层20、增压缸导向套21、增压缸活塞杆22、增压缸支撑环23和增压缸顶部封板26;竖向隔震器下联结板8和叠层橡胶支座上联结板10连接;导轨2顶部与竖向隔震器上联结板1连接,导轨2底部与竖向隔震器下联结板8连接;主缸活塞杆3顶部与竖向隔震器上联结板1连接,主缸顶部活塞下部直接接触液压油并进行密封,主缸底部活塞上部与压簧5串联,压簧5顶部与主缸顶部封板24固定,主缸底部活塞下部与拉簧6串联,拉簧6底部与竖向隔震器下联结板8固定;主缸顶部活塞以下腔体与底部活塞以下腔体联通;主缸导向套4与主缸缸壁连接;钢板层11与橡胶层12形成叠层橡胶层、上部与叠层橡胶支座上联结板10连接,下部与联结板13连接;减压缸活塞上部与压簧14串联,底部支承于支撑环18;弹簧底部与活塞连接,弹簧顶部与减压缸顶部封板25连接;活塞下部腔体与主缸液压油腔体联通,活塞杆置于压簧14内部并且与减压缸导向套16协同工作,减压缸缓冲垫层15、减压缸导向套16均与减压缸顶部封板25固定;支撑环18与缸壁固定;增压缸活塞上部与压簧19串联,增压缸活塞杆22顶部支承于增压缸缓冲垫层20;弹簧底部与活塞连接,弹簧顶部与增压缸顶部封板26连接;活塞下部腔体与主缸液压油腔体联通,活塞杆置于压簧19内部并且与增压缸导向套21协同工作,增压缸缓冲垫层20、增压缸导向套21均与增压缸顶部封板26固定;支撑环23与缸壁固定。所述装置的竖向隔震器下联结板8和叠层橡胶支座上联结板10贴合连接采用高强螺栓或焊接方式连接;或者直接加工成一块联接板。所述装置的导轨2与竖向隔震器上联结板1、竖向隔震器下联结板8通过焊接直接连接或直接通过螺栓连接;主缸活塞杆3顶部与竖向隔震器上联结板通过焊接直接连接。所述装置的弹簧的固定方式为焊接或螺纹连接;或不固定压簧,仅让压簧与端板之间在弹簧内力作用下紧密接触连接;各液压缸腔体直接通过软油管或固定的硬管道连接;主缸导向套与主缸缸壁,减压缸与增压缸内部的导向套、缓冲垫层、支撑环均通过螺栓或螺纹连接。所述装置的主缸、增压缸、减压缸数量的组合比例通过多级变刚度的设计要求灵活布置,主缸、减压缸、增压缸的数量以及每个缸内部的腔体个数设为一个或多个。本发明的装置进行变刚度液压三维隔震方法,减压缸内腔均与主缸内腔联通,正常使用时减压缸活塞在压簧14与内部液压油压力的作用下被顶在支撑环18上,保持静止,不参与工作;当活塞杆17与缓冲垫层15相接触时,减压缸活塞运动到极限位置;通过控制减压缸活塞是否运动来控制液压缸内部液体压强的变化,从而起到变刚度作用;增压缸内腔均与主缸内腔联通,正常使用时活塞杆22在压簧19与内部液压油压力的作用下被压在缓冲垫层20上,保持静止,不参与工作;当增压缸活塞与支撑环23相接触时,增压缸活塞运动到极限位置;通过控制减压缸活塞是否运动来控制液压缸内部液体压强的变化,从而起到变刚度作用;在不同阶段控制不同数量的增压/减压缸参与工作实现竖向刚度的多级变化;导轨2用于限制竖向隔震器的水平运动。所述方法是利用增压缸/减压缸活塞的运动,增大主工作缸底部活塞的等效面积从而改变主工作缸顶部活塞出的刚度,达到变刚度控制效果;对主缸而言,其刚度通过下式进行计算:式中,keq1表示主缸顶部活塞的等效竖向刚度,aup表示主缸顶部活塞的面积,n表示主缸底部活塞腔体总数,adi表示第i个主缸底部活塞的面积,kdi表示第i个主缸底部活塞腔体中弹簧的总刚度;当仅主缸参与工作时,支座的竖向刚度等于主缸的等效竖向刚度;随着各阶段参与工作的增压/减压缸数量发生变化,支座的等效竖向刚度也发生改变,此时可根据下式计算支座的等效竖向刚度:式中,keq2表示有增压/减压缸参与工作时主缸顶部活塞的等效竖向刚度,aup表示主缸顶部活塞的面积,n表示主缸底部活塞腔体总数,adi表示第i个主缸底部活塞的面积,kdi表示第i个主缸底部活塞腔体中弹簧的总刚度,m表示增压/减压缸的个数,qj表示第j个增压/减压缸内部腔体数,ajk表示第j个增压/减压缸内第k个腔体中的活塞面积,kjk表示第j个增压/减压缸内第k个腔体中的弹簧总刚度。本发明的变刚度液压三维隔震装置安放于民用建筑、桥梁、地下建筑等的隔震层中,隔震装置以上的结构的自重以及增压/减压缸内部弹簧以及限位装置,实现在不同情况下隔震装置竖向的自复位;发生向下的位移时减压缸内部弹簧弹力克服自重作用,提供竖向向上的恢复力;发生向上的位移时结构自重克服增压缸内部弹簧弹力,提供竖向向下的恢复力。本发明的减压缸和增压缸均与主缸直接通过软油管或硬管道就近或远程连接,以满足不同大小隔震层空间的使用要求;同时减压缸和增压缸可水平或竖向放置。下面以主缸包含两个底部活塞腔体同时具有两个增压缸和两个减压缸的三维隔震装置为例,进一步阐述该发明:其包括竖向隔震器上联结板1、竖向导轨2、主缸活塞杆3、主缸限位导向套4、主缸底部活塞串联压簧5、主缸底部活塞串联拉簧6、联接螺栓垫层7、竖向隔震器下联结板8、高强螺栓9、叠层橡胶支座上联结板10、钢板层11、橡胶层12、叠层橡胶支座下联结板13、减压缸活塞串联压簧14、减压缸缓冲垫层15、减压缸导向套16、减压缸活塞杆17、减压缸支撑环18、增压缸活塞串联压簧19、增压缸缓冲垫层20、增压缸导向套21、增压缸活塞杆22、增压缸支撑环23、主缸顶部封板24、减压缸顶部封板25、增压缸顶部封板26。高强螺栓9将竖向隔震器下联结板8、叠层橡胶支座上联结板10可靠连接,或通过焊接方式连接或者直接加工成一块联接板。导轨2顶部与竖向隔震器上联结板1通过焊接或螺栓连接固定,导轨2底部与竖向隔震器下联结板8通过焊接或螺栓连接固定。主缸活塞杆3顶部与竖向隔震器上联结板1通过焊接固定,主缸顶部活塞下部直接接触液压油并进行密封,主缸底部活塞上部与压簧5串联,压簧5顶部与主缸顶部封板24固定,主缸底部活塞下部与拉簧6串联,拉簧6底部与竖向隔震器下联结板8固定;弹簧的固定方式为焊接或螺纹连接;或为方便更换,不固定压簧,仅让压簧与端板之间在弹簧内力作用下紧密接触。主缸顶部活塞以下腔体与底部活塞以下腔体联通,通过软油管或固定的硬管道连接;主缸内部腔体数量及活塞数量可根据需要进行设计。主缸导向套4通过螺栓或螺纹与主缸缸壁连接。钢板层11与橡胶层12共同形成叠层橡胶层、两者上部与叠层橡胶支座上联结板10,下部与叠层橡胶支座下联结板13连接。减压缸活塞上部与压簧14串联,底部支承于支撑环18;弹簧底部与活塞连接,弹簧顶部与减压缸顶部封板25连接;连接方式为焊接或螺纹连接,或为方便更换,仅让弹簧与两者在弹簧内力作用下紧密接触,在整个工作过程中不分离。活塞下部腔体与主缸液压油腔体通过软油管或固定的硬管道连接,其活塞杆置于压簧14内部并且与减压缸导向套16协同工作,减压缸缓冲垫层15、减压缸导向套16均与减压缸顶部封板25通过螺栓或螺纹连接固定;支撑环18通过焊接或螺纹与缸壁固定。减压缸内部腔体与活塞数量可根据设计设置为一个或多个,同时也可布置不同数量的减压缸与主缸协同工作。增压缸活塞上部与压簧19串联,增压缸活塞杆22顶部支承于增压缸缓冲垫层20;弹簧底部与活塞连接,弹簧顶部与增压缸顶部封板26连接;连接方式为焊接或螺纹连接,或为方便更换,仅让弹簧与两者在弹簧内力作用下紧密接触,在整个工作过程中不分离。活塞下部腔体与主缸液压油腔体通过软油管或固定的硬管道连接,其活塞杆置于压簧19内部并且与增压缸导向套21协同工作。增压缸各部件之间的连接方式与减压缸相同。增压缸内部腔体与活塞等数量可根据设计设置为一个或多个,同时也可布置不同数量的减压缸与主缸协同工作。减压缸内腔均与主缸内腔联通,正常使用时减压缸活塞在压簧14与内部液压油压力的作用下被顶在支撑环18上,保持静止,不参与工作;当活塞杆17与缓冲垫层15相接触时,减压缸活塞运动到极限位置。通过控制减压缸活塞是否运动来控制液压缸内部液体压强的变化,从而起到变刚度作用。增压缸内腔均与主缸内腔联通,正常使用时活塞杆22在压簧19与内部液压油压力的作用下被压在缓冲垫层20上,保持静止,不参与工作;当增压缸活塞与支撑环23相接触时,增压缸活塞运动到极限位置。通过控制减压缸活塞是否运动来控制液压缸内部液体压强的变化,从而起到变刚度作用。可根据设计在不同阶段控制不同数量的增压/减压缸参与工作可实现竖向刚度的多级变化。主缸内部液体与减压/增压缸内部通过软油管或固定的硬管道联通,在正常使用时仅主缸三个活塞运动即仅主缸参与工作。主缸底部活塞连接的拉簧与压簧能够提供足够的竖向承载能力和适宜的竖初始向刚度,主缸内部的压簧与主缸顶部封板和底部活塞连接,拉簧与竖向隔震器下联结板和活塞连接;弹簧的固定方式为焊接或螺纹连接;或为方便更换,不固定压簧,仅让压簧与端板之间在弹簧内力作用下紧密接触。主缸竖向内部有足够空间保证弹簧径向自由变形。竖向隔震器上联结板与主缸限位导向套共同作用限制突发情况下竖向隔震器向下运动的最大位移,主缸顶部活塞与主缸限位导向套共同作用提供抗拉措施,限制突发情况下竖向隔震器向上运动的最大位移,三者共同作用防止突发的较大竖向位移对隔震装置造成的破坏。对主缸而言,在整个过程中其刚度可以通过下式进行计算:式中,keq1表示仅主缸工作时主缸顶部活塞的等效竖向刚度,aup表示主缸顶部活塞的面积,ad表示主缸底部活塞的面积,kd表示一个主缸底部活塞腔体中弹簧的总刚度。当仅主缸参与工作时,支座的竖向刚度等于主缸的等效竖向刚度。减压缸下腔与主缸通过软油管或固定的硬管道联通,自重下减压缸活塞在弹簧弹力、液压油压力的作用下达到平衡位置,此时该活塞被弹簧顶在减压缸支撑环上。弹簧预压力通过设计施加,控制高压阈值,弹簧底部与活塞连接,弹簧顶部与减压缸顶部封板连接;弹簧的固定方式为焊接或螺纹连接;或为方便更换,不固定压簧,仅让压簧与端板之间在弹簧内力作用下紧密接触。弹簧刚度与减压缸活塞面积共同决定高压变刚度后竖向隔震器的竖向刚度。弹簧内圈设置减压缸导向套与缓冲垫层,两者均通过焊接或螺纹连接与减压缸顶部封板可靠连接。减压缸活塞杆运动到与缓冲垫层接触后减压缸活塞停止运动,减压缸退出工作。缓冲垫层用于防止过大的位移对装置以及隔震对象造成的破坏。减压缸缓冲垫层与减压缸活塞杆之间的距离控制减压位移阈值。减压缸参与工作之后,支座的等效竖向刚度可以通过下式计算:式中,keq2表示减压缸参与工作时主缸顶部活塞的等效竖向刚度,aup表示主缸顶部活塞的面积,ad表示主缸底部活塞的面积,kd表示一个主缸底部活塞腔体中弹簧的总刚度,aj表示减压缸活塞的面积,kj表示减压缸活塞腔体中弹簧的总刚度。增压缸下腔与主缸通过软油管或固定的硬管道联通,自重下增压缸活塞在弹簧弹力、液压油压力的作用下达到平衡位置,此时该活塞被液压油压力顶在缓冲垫层上。弹簧刚度与增压缸活塞面积共同决定低压变刚度后竖向隔震器的竖向刚度。弹簧预压力通过设计施加,控制低压阈值。弹簧底部与活塞连接,弹簧顶部与增压缸顶部封板连接;弹簧的固定方式可为焊接或螺纹连接;或为方便更换,不固定压簧,仅让压簧与端板之间在弹簧内力作用下紧密接触。弹簧内圈设置增压缸导向套与缓冲垫层,两者均通过焊接或螺纹连接与增压缸顶部封板可靠连接。增压缸活塞运动到与支撑环接触后增压缸活塞停止运动,增压缸退出工作。支撑环用于防止过大的位移对装置以及隔震对象造成的破坏。增压缸活塞与支撑环之间的距离控制增压位移阈值。增压缸参与工作之后,支座的等效竖向刚度可以通过下式计算:式中,keq3表示增压缸参与工作时主缸顶部活塞的等效竖向刚度,aup表示主缸顶部活塞的面积,ad表示主缸底部活塞的面积,kd表示一个主缸底部活塞腔体中弹簧的总刚度,ak表示增压缸活塞的面积,kk表示增压缸活塞腔体中弹簧的总刚度。该发明通过上部结构自重以及增压/减压缸内部弹簧以及限位装置,实现在不同情况下隔震装置竖向的自复位。发生向下的位移时减压缸内部弹簧弹力克服自重作用,提供竖向向上的恢复力;发生向上的位移时结构自重克服增压缸内部弹簧弹力,提供竖向向下的恢复力。与目前其他研究成果相比,自复位原理、构造简单,易于实施,造价低廉且更加安全可靠。同时其余缸体与主缸直接通过软油管或硬管道就近或远程连接。其它缸体可以水平放置或者依据实际情况布置,配合使用油管等可以不与主缸布置在同一个地方,适用于不同的空间等。在液压缸外部设置竖向导轨,导轨上部与竖向隔震器上联结板通过焊接或螺栓连接,下部与竖向隔震器下联结板通过焊接或螺栓连接,限制竖向隔震器上联结板仅能沿竖向运动,同时竖向隔震器下联结板传递结构的水平剪力,保证液压缸的轴向受力。设置高强螺栓连接竖向隔震器以及叠层橡胶支座,有效地将上部的水平剪力传递给底部叠层橡胶支座。本发明中,叠层橡胶支座在传递竖向力的同时增大结构的水平周期,隔离水平向地震。橡胶部分有足够的竖向抗压、抗拉承载力以及刚度以承受竖向荷载,且能将上部结构的压力有效地传递给墩台或基础;有良好的弹性以适应上部结构的转动;有较大的剪切变形以满足上部结构的水平位移。当在地震作用下三维隔震装置受拉时,主缸顶部活塞将在主缸导向套4的作用下停止运动,同时通过导向套4将拉力传递给主缸缸壁继而传递给下部叠层橡胶支座。由于竖向隔震装置的存在,叠层橡胶支座部分在地震中所承受的竖向力大大减小,叠层橡胶支座的抗拉承载力足以满足三维隔震装置的整体稳定性和工作安全性的要求。发明的变刚度液压三维隔震装置具有以下优点:1、水平隔震措施采用研究和应用都较为成熟的叠层橡胶支座来满足水平隔震目的。适宜的水平刚度可以有效地隔离水平地震作用,避免强烈水平地震作用下结构及设备等发生严重破坏。同时由于上部竖向隔震装置的存在,叠层橡胶支座部分承受的竖向压力变化受到竖向隔震效果的控制,变化较小,竖向压力对其水平向隔震的力学性能影响较小,水平向隔震效果比传统叠层橡胶支座更加稳定;叠层橡胶支座的抗拉承载力足以满足三维隔震装置的整体稳定性和工作安全性的要求。2、本发明中液压缸部分承担竖向荷载并隔离竖向地震。在正常使用以及隔震时均具有足够的竖向承载力,同时具有很强的自复位能力。发生向下的位移时减压缸内部弹簧弹力克服自重作用,提供竖向向上的恢复力;发生向上的位移时结构自重克服增压缸内部弹簧弹力,提供竖向向下的恢复力。与目前其他研究成果相比,自复位原理、构造简单,易于实施,造价低廉且更加安全可靠。3、本发明中液压缸部分通过弹簧的预压力设置高压、低压控制阈值的被动控制手段,控制增压、减压缸的工作状态,实现竖向隔震的多级变刚度控制。可以通过简单调节活塞截面、增/减压缸的数量,调整各级刚度以及变刚度级数。该控制方式增加了装置隔震效果的同时还实现了类似于智能控制的效果。在高强度高频地震作用下,减压/增压缸与主缸共同工作,支座竖向处于低刚度隔震阶段,减小结构的动力响应。同时在长周期地震作用下,为防止支座处于低刚度阶段与地震作用产生共振,当支座位移达到一定程度时,限位装置(支撑环与缓冲垫层)开始工作,增压/减压缸退出工作,支座竖向刚度升高,减小长周期地震对隔震支座与结构的不利影响。4、在低幅值地震作用下,仅主缸参与工作,主缸内部弹簧刚度满足在正常使用下的初始刚度要求,使结构在活荷载、风荷载、低幅值地震等作用下不产生较大竖向位移和振动。5、其余缸体与主缸直接可以通过软油管或硬管道就近或远程连接。其它缸体可以水平放置或者依据实际情况布置,配合使用油管等可以不与主缸布置在同一个地方,适用于不同的空间等。6、通过设置竖向隔震器上联结板与主缸导向套的距离以及主缸导向套与主缸上部活塞的距离,可以灵活限制竖向隔震器的极限变形,避免其发生过大的竖向位移而破坏,提高了装置的整体工作安全性。7、主工作缸顶部活塞杆与支座端板串联,端板直接与上部结构连接。本发明中的液压缸部分仅传递和控制竖向力,水平力部分由端板传递到导轨,最后由导轨传递到下部叠层橡胶支座部分,装置中各部分分工更加明确,易于设计。8、该三维隔震装置构造较为简单,制作加工方便,具有同时完成三维隔震效果,并且具有良好的整体稳定性和工作安全性。附图说明图1(a)为发明的一种新型变刚度液压三维隔震支座的总体结构示意图,上部为竖向隔震部分,下部为叠层橡胶支座。图1(b)为该新型装置的三维立体图。图2为该装置竖向隔震器部分的平面布置图。图3(a)为该装置减压缸未进入工作状态时的剖面图,图3(b)是减压缸运动到极限位置的剖面图。图4(a)为该装置增压缸未进入工作状态时的剖面图,图4(b)是增压缸运动到极限位置的剖面图。图中:1竖向隔震器上联结板、2竖向导轨、3主缸活塞杆、4主缸限位导向套、5主缸底部活塞串联压簧、6主缸底部活塞串联拉簧、7联接螺栓垫层、8竖向隔震器下联结板、9高强螺栓、10叠层橡胶支座上联结板、11钢板层、12橡胶层、13叠层橡胶支座下联结板、14减压缸活塞串联压簧、15减压缸缓冲垫层、16减压缸导向套、17减压缸活塞杆、18减压缸支撑环、19增压缸活塞串联压簧、20增压缸缓冲垫层、21增压缸导向套、22增压缸活塞杆、23增压缸支撑环、24主缸顶部封板、25减压缸顶部封板、26增压缸顶部封板。具体实施方式下面结合附图以主缸包含两个底部活塞腔体同时具有两个增压缸和两个减压缸的三维隔震装置为例:详细说明。以主缸包含两个底部活塞腔体同时具有两个增压缸和两个减压缸的三维隔震装置在50m跨度的单层球面网壳中进行三维隔震为例,结合技术方案和附图详细叙述本发明的具体实施例,以使本发明的优点和特征能更易于被本领域技术人员理解。该50m跨度的单层球面网壳水平向和竖向基本周期分别为0.318s以及0.284s。使用本发明对该结构进行三维隔震,竖向基本周期均隔震到原本周期的3倍;采取竖向三阶段变刚度控制机制进行设计,取第一阶刚度与第三阶段刚度对应结构竖向周期为1.5倍基本周期,第二阶段刚度对应竖向周期为3倍基本周期。通过有限元计算,对竖向而言,每个支座的三阶段竖向刚度分别取为1500kn/m、345kn/m以及1500kn/m。同时根据结构在活荷载、风荷载、低幅值地震等作用下不产生较大竖向位移和振动,通过有限元计算,确定三阶段变刚度控制机制的高压控制阈值与抵押控制阈值所对应的竖向力分别为55kn和65kn。所以减压缸和增压缸内部弹簧的预压力分别为65kn和55kn。根据工程经验,取最大竖向隔震位移为100mm(包含第三阶段限位阶段20mm)。对主缸进行设计,根据其高度要求1500kn/m,又下式反算出主缸内部一个底部活塞腔内弹簧的总刚度:然后根据传统工业用弹簧设计方法弹簧即可。以主缸顶部活塞直径200mm,底部活塞直径160mm的主缸为例,则通过螺旋弹簧设计方法,得出主缸顶部活塞需配置的弹簧参数如下表。表1主缸弹簧参数表位置弹簧外径d/mm簧丝直径d/mm有效圈数n总圈数nl弹簧刚度k/kn/m主缸拉簧15028612557主缸压簧1402546634材料:油回硅锰a(60si2mn)主缸拉簧与活塞以及主缸底部直接通过拉簧两端的非有效簧丝进行连接。压簧直接与活塞以及主缸端盖接触,在预压力作用下协调工作。主缸各腔体直接通过m42的油口外接软油管进行连接。主缸壁厚取10mm,缸壁上加工有螺栓丝扣,丝扣高度长度20mm。主缸顶部封板、导向套、底板均加工有相应丝扣,通过丝扣与缸壁连接。对减压缸进行设计,根据其高度要求345kn/m,又下式反算出减压缸内部弹簧的总刚度:然后根据传统工业用弹簧设计方法弹簧即可。以减压缸活塞直径250mm为例,则通过螺旋弹簧设计方法,得出主缸顶部活塞需配置的弹簧参数如下表。表2减压缸弹簧参数表位置弹簧外径d/mm簧丝直径d/mm有效圈数n总圈数nl弹簧刚度k/kn/m减压缸压簧240483.55.52116材料:油回硅锰a(60si2mn)减压缸弹簧与活塞以及减压缸顶部封板直接接触,在预压力作用下协调工作。减压缸与主缸内腔通过m60的油口外接油管进行连接。减压缸弹簧内部设置有导向套与缓冲垫层,导向套的厚度为10mm,直接为弹簧内径减去5mm。减压缸活塞杆长度与缸内缓冲垫层之间的距离为减压位移阈值,可通过所选取的最大隔震位移以及限位段位移确定。活塞杆的长度与导向套的长度可以通过实际导向需求确定,只需满足活塞杆与缓冲垫层之间的距离要求即可。缓冲垫层与导向套均事先焊接在减压缸顶部封板上,顶部封板于缸壁之间通过高度为20mm的螺栓丝扣连接。对增压缸进行设计,根据其高度要求345kn/m,又下式反算出减压缸内部弹簧的总刚度:然后根据传统工业用弹簧设计方法弹簧即可。以增压缸活塞直径220mm为例,则通过螺旋弹簧设计方法,得出主缸顶部活塞需配置的弹簧参数如下表。表3增压缸弹簧参数表位置弹簧外径d/mm簧丝直径d/mm有效圈数n总圈数n1弹簧刚度k/kn/m增压缸压簧21038351348材料:油回硅锰a(60si2mn)增压缸弹簧与活塞以及增压缸顶部封板直接接触,在预压力作用下协调工作。增压缸与主缸内腔通过m60的油口外接油管进行连接。增压缸弹簧内部设置有导向套与缓冲垫层,导向套的厚度为10mm,直接为弹簧内径减去5mm。增压缸活塞与缸内支撑环之间的距离为增压位移阈值,可通过所选取的最大隔震位移以及限位段位移确定。活塞杆的长度与缓冲垫层的长度和等于初始状态时增压缸弹簧的长度,两者的具体值可以通过实际导向需求确定。缓冲垫层与导向套均事先焊接在增压缸顶部封板上,顶部封板于缸壁之间通过高度为20mm的螺栓丝扣连接。通过m30摩擦型高强螺栓9将竖向隔震器下联结板8、叠层橡胶支座上联结板10可靠连接。导轨2顶部与竖向隔震器上联结板1以及竖向隔震器下联结板8通过一级对接焊缝连接。主缸活塞杆3顶部与竖向隔震器上联结板1通过螺栓连接固定,主缸顶部活塞下部直接接触液压油并进行密封,主缸底部活塞上部与压簧5串联,下部与拉簧6串联;通过拉簧两端的非有效簧丝进行连接。为方便更换,不固定压簧,仅让压簧与端板之间在弹簧内力作用下紧密接触。主缸顶部活塞以下腔体与底部活塞以下腔体联通,通过m42油口以及软管连接。主缸导向套4通过螺栓丝扣与主缸缸壁连接。钢板层11与橡胶层12共同形成叠层橡胶层、两者之间通过胶合粘接等方式连接。减压缸活塞上部与压簧14串联,底部支承于支撑环18;为方便更换,仅让弹簧与活塞和减压缸顶部封板在弹簧内力作用下紧密接触,在整个工作过程中不分离。活塞下部腔体与主缸液压油腔体通过m60油口软管连接,其活塞杆置于压簧14内部并且与减压缸导向套16协同工作,减压缸缓冲垫层15、减压缸导向套16均与减压缸顶部封板25通过提前焊接固定;支撑环18通过螺栓与缸壁固定。增压缸活塞上部与压簧19串联,增压缸活塞杆22顶部支承于增压缸缓冲垫层20;为方便更换,仅让弹簧与活塞和减压缸顶部封板在弹簧内力作用下紧密接触,在整个工作过程中不分离。活塞下部腔体与主缸液压油腔体通过m60油口软管连接,其活塞杆置于压簧19内部并且与增压缸导向套21协同工作。增压缸各部件之间的连接方式与减压缸相同。减压缸内腔均与主缸内腔联通,正常使用时减压缸活塞在压簧14与内部液压油压力的作用下被顶在支撑环18上,保持静止,不参与工作;当活塞杆17与缓冲垫层15相接触时,减压缸活塞运动到极限位置。通过控制减压缸活塞是否运动来控制液压缸内部液体压强的变化,从而起到变刚度作用。增压缸内腔均与主缸内腔联通,正常使用时活塞杆22在压簧19与内部液压油压力的作用下被压在缓冲垫层20上,保持静止,不参与工作;当增压缸活塞与支撑环23相接触时,增压缸活塞运动到极限位置。通过控制减压缸活塞是否运动来控制液压缸内部液体压强的变化,从而起到变刚度作用。可根据设计在不同阶段控制不同数量的增压/减压缸参与工作可实现竖向刚度的多级变化。如图1(a)所示,竖向隔震器上联结板1与结构底部相连,主缸活塞杆2直接承受结构竖向力,内部液压油通过油路与减压缸以及增压缸相通。如图3(a)、4(a)所示,减压与增压缸在正常使用时均不参与工作。此时减压缸活塞被弹簧的预压力紧紧顶在支撑环18上,保持静止。增压缸活塞在液压油压力作用下也被顶在缓冲垫层20上,保持静止。减压与增压缸中的弹簧预压力控制支座的高压和低压控制阈值。当液体内部压力即支座的支座反力高于低压控制阈值而低于高压控制阈值时,两控制缸的活塞将始终保持静止,使得控制缸不参与工作。此时支座的竖向隔震部分只有主缸参与工作,主缸底部活塞与主缸底部活塞串联压簧5、主缸底部活塞串联拉簧6连接提供正常使用时结构所需的竖向刚度以及全过程竖向所必要的承载力,支座的竖向刚度为较大的初始刚度即一级刚度,确保结构在活荷载、风荷载、低幅值地震等作用下不产生较大竖向位移和振动。此时支座的竖向刚度可通过权力要求书中对应的公式计算。当地震中结构的支座反力过大即液压缸内部液压油压力超过高压控制阈值时,减压控制缸的活塞将在液压油压力作用下,克服弹簧14的弹力开始运动,此时主工作底部活塞的等效面积发生改变,使得支座的竖向刚度大大减小。此时支座的竖向刚度为减压二级刚度,可通过权力要求书中对应的公式计算。该刚度由主缸底部活塞串联的主缸底部活塞串联压簧5、主缸底部活塞串联拉簧6和减压缸活塞串联的弹簧14共同提供;可根据设计,灵活调整控制缸活塞面积以得到不同的控制效果。该阶段支座的竖向刚度的减小主要是为了延长结构竖向周期,降低地震作用下结构包括加速度、内力在内的各种响应,实现结构基于性能的抗震设计目标。当与减压缸活塞杆17运动到与缓冲垫15接触的时候,活塞将停止运动,此后减压控制缸退出工作。此时减压缸的剖面图如图3(b)所示。同样由于主缸底部等效活塞面积发生变化,支座竖向刚度发生改变,变为减压三级刚度。该刚度主要是为了避免共振、减小隔震层位移,防止支座发生破坏。减压缸缓冲垫层15与减压缸活塞杆17之间的距离控制减压位移阈值。高压控制阈值与减压位移阈值可根据隔震需要灵活设计,实现竖向减压的多级变刚度控制。当地震中结构的支座反力过小即液压缸内部液压油压力低于低压控制阈值时,增压控制缸的活塞将在弹簧19的弹力作用下,克服液压油压力开始运动,此时主工作底部活塞的等效面积发生改变,使得支座的竖向刚度大大减小。此时支座的竖向刚度为增压二级刚度可通过权力要求书中对应的公式计算。该刚度由主缸底部活塞串联的主缸底部活塞串联压簧5、主缸底部活塞串联拉簧6和减压缸活塞串联的弹簧19共同提供;可根据设计,灵活调整控制缸活塞面积以得到不同的控制效果。该阶段支座的竖向刚度的减小主要是为了延长结构竖向周期,降低地震作用下结构包括加速度、内力在内的各种响应,实现结构基于性能的抗震设计目标。当与增压缸活塞运动到与支撑环23接触的时候,活塞将停止运动,此后增压控制缸退出工作。此时增压缸的剖面图如图4(b)所示。同样由于主缸底部等效活塞面积发生变化,支座竖向刚度发生改变,变为减压三级刚度。该刚度主要是为了避免共振、减小隔震层位移,防止支座发生破坏。增压缸支撑环23与减压缸活塞之间的距离控制增压位移阈值。低压控制阈值与增压位移阈值可根据隔震需要灵活设计,实现竖向增压的多级变刚度控制。叠层橡胶支座由叠层橡胶支座上联结板10、叠层橡胶支座下连接板13以及中间的钢板层11和橡胶层12组成。由于竖向隔震部分的存在,使得整个隔震过程中水平隔震部分承受的竖向压力变化幅值较小,使得其水平隔震性能更加稳定。叠层橡胶支座的抗拉承载力足以满足三维隔震装置的整体稳定性和工作安全性的要求。导轨2与上联结板1和下联结板8固定,且通过高强螺栓9将上部竖向隔震器与叠层橡胶支座可靠连接。结构底部承受的剪力传递到竖向隔震器上联结板1,然后通过导轨2直接传递到下联结板8,然后通过高强螺栓9传递到下部的叠层橡胶支座部分。以上所述仅为本发明的实施例,并非因此限制本发明的专利范围,凡是利用本发明说明书原理及附图内容所作的等效结构或等效流程变换,或直接或间接运用在其他相关的
技术领域:
,均同理包括在本发明的专利保护范围内。当前第1页12