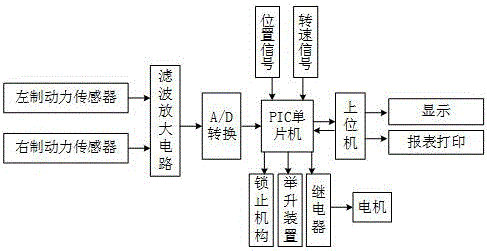
本发明涉及一种检测装置,具体涉及一种新型全时四驱汽车制动力检测装置。
背景技术:
:当前轻型车的汽车制动性能主要由滚筒反力式制动检验台和平板式制动检验台检测,国内大部分机动车安检机构普遍采用滚筒反力式制动检验台。其实际为一个机械模拟路面,被测汽车开上去后,可模拟在道路上制动的状态,同时制动力及其他相关参数被安置在“路面”上的传感器测出,作为判断汽车制动性能的依据。然而,随着汽车工业的不断发展,不少高端汽车都采用了全时全轮驱动(AWD),部分AWD车辆在滚筒反力式制动检验台上检测时,会造成车辆差速器或变速箱的损坏。现阶段部分检测站采用平板制动检验台对AWD车辆进行制动线内检验,但相比于滚筒反力式制动检验台,平板制动检验台存在重复性差,对操作、环境要求较高等缺点。技术实现要素:本发明的目的在于改善上述现有技术存在的缺陷,在传统滚筒反力式制动检验台的基础上加以改进,对更好地测得车轮最大制动力给出了合理的方法,能够更加快速、准确、安全地检测AWD车辆,并且具有较高的测量精度和可靠性。本发明解决技术问题所采取的技术方案为:全时四驱汽车制动力检验装置,包括制动检验台机械装置、单片机及电路控制系统。单片机及电路控制系统对制动检验台机械装置的制动力进行数据采集、数据处理及输出,从而实现全时四驱汽车汽车制动力的高精度及高可靠性检验。所述的制动检验台机械装置包括一组制动台,沿检测线纵向在制动台两侧设置的两组自由滚筒组,制动台上设置有轮胎顶紧装置,自由滚筒组上设置锁止机构。当对前轮进行检测时,前轮在制动滚筒组上,轮胎顶紧装置进入工作状态将轮胎顶紧,防止其位移影响检测结果,后轮在自由滚筒组上一起转动;同样,检测后轮时则前轮在自由滚筒组上,后轮在制动滚筒组上。所述的制动台由结构完全相同的左右两套车轮制动力测试单元和一套指示、控制装置组成。每一套车轮制动力测试单元由框架、驱动装置、滚筒组、举升装置、测量装置等构成。所述的前后自由滚筒装置通过锁止机构来控制,当需要使用自由滚筒时将锁止机构解除,滚筒可自由滚动,当不需要使用时则锁死机构,使自由滚筒无法滚动。所述的轮胎顶紧装置,包括安装在制动台机架上的气缸,通过曲臂连接滑轮,气缸不工作时整个顶紧装置与地面平行,气缸工作时通过曲臂将滑轮顶紧,且滑轮可跟随汽车轮胎一起自由转动。所述的单片机及电路控制系统包括数据采集模块、通讯模块、PIC单片机控制模块、调试显示模块。其特征在于:制动力系统检测时,汽车行驶上制动检验台,左右轮触发位置开关,此时单片机控制系统采集信号后启动滚筒电机,驾驶员踩下踏板,车轮在制动器作用下开始减速,制动力经滚筒、扭力箱及测力臂,传给测力传感器,当持续上升的制动力出现峰值下降10%或者滑移率达到设定值10%时,基本上认为已测得最大制动力值,此时单片机发出指令。本发明的有益效果:1、有效解决传统制动力检验台检测时会对四驱车辆造成变速器损坏等的问题,规避了被检车辆的损坏风险。2、能够更加快速、准确、安全地检测AWD车辆,更好地测得车轮最大制动力,具有较高的测量精度和可靠性。3、操作简单,并且能满足四驱模式和二驱模式的任意切换,解决了机动车安全检测机构对各种车型制动力的检测问题。附图说明图1为本发明制动检验台机械装置结构示意图。图2为本发明单片机及电路控制系统框图。图中:1、电动机;2、减速器;3、机架;4、主滚筒;5、顶紧装置;6、车轮挡盖板;7、举升装置;8、第三滚筒;9、传感器总成;10、边盖板;11、副滚筒;12、中间盖板;13、链轮及滚子轮;14、自由滚筒架;15、自由滚筒。具体实施方式以下结合附图对本发明作进一步说明。如图1所示,制动检验台机械装置包括一组制动台,沿检测线纵向在制动台两侧设置的两组自由滚筒组,每组自由滚筒组由自由滚筒架14和自由滚筒架14,自由滚筒架14中的多个自由滚筒15组成。制动台上设置有轮胎顶紧装置5,轮胎顶紧装置5一侧装有车轮挡盖板6,自由滚筒组上设置锁止机构。当对前轮进行检测时,前轮在制动滚筒组上,轮胎顶紧装置进入工作状态将轮胎顶紧,防止其位移影响检测结果,后轮在自由滚筒组上一起转动;同样,检测后轮时则前轮在自由滚筒组上,后轮在制动滚筒组上。所述的制动台由结构完全相同的左右两套车轮制动力测试单元和一套指示、控制装置组成,两套车轮制动力测试单元由中间盖板隔开,中间盖板下方是一些链轮及滚子轮13。每一套车轮制动力测试单元由机架3、驱动装置、滚筒组、举升装置7、测量装置等构成,其中电动机1和减速器2组成驱动装置,电动机1和减速器2由边盖板10侧封,滚筒组包括主滚筒4、副滚筒11和第三滚筒8,测量装置主要是指传感器总成9。所述的前后自由滚筒装置通过锁止机构来控制,当需要使用自由滚筒时将锁止机构解除,滚筒可自由滚动,当不需要使用时则锁死机构,使自由滚筒无法滚动。所述的轮胎顶紧装置,包括安装在制动台机架上的气缸,通过曲臂连接滑轮,气缸不工作时整个顶紧装置与地面平行,气缸工作时通过曲臂将滑轮顶紧,且滑轮可跟随汽车轮胎一起自由转动。所述的单片机及电路控制系统,如图2所示,包括数据采集模块、通讯模块、PIC单片机控制模块、调试显示模块。制动力系统检测时,汽车行驶上制动检验台,左右轮触发位置开关,此时单片机控制系统采集信号后启动滚筒电机,驾驶员踩下踏板,车轮在制动器作用下开始减速,制动力经滚筒、扭力箱及测力臂,传给测力传感器,当持续上升的制动力出现峰值下降10%或者滑移率达到设定值10%时,基本上认为已测得最大制动力值,此时单片机发出指令。实施例一本实施例对全时四驱汽车制动力检测装置进行试验,在某地检测站A安装全时四驱汽车制动力检测装置,选择三种车型全时四驱汽车斯巴鲁翼豹、大众途观、奥迪Q5作为试验车辆,分别驶上全时四驱汽车制动力检测装置进行三次制动力检测。根据GB7258-2012《机动车运行安全技术条件》以及GBT13564-2005《滚筒反力式汽车制动检验台》,按以下步骤进行对比试验:1)根据指示要求,安装机械台体以及系统仪表,检查无误后在试验道路限宽标记内停放试验车辆。2)启动电源,开启计算机,启动上位机测试软件,登陆界面进入测试界面,调试软件获取串口信息以及端口通道。3)输入基本参数。输入车牌号、整车的重量、选择车轴数、选择系数,按下上位机界面上的“检测”按钮。4)将被检车辆正直居中驶入制动台主副滚筒之间,轮胎顶紧装置进入工作状态将轮胎顶紧,防止其位移影响检测结果。非检车轮在自由滚筒组上,自由滚筒会跟着汽车轮胎一起自由转动。5)制动力检测。接通电源,启动滚筒电机,滚筒带动被测车辆的左右轮转动,操作人员按照显示屏指示在5s~8s内,将制动踏板逐渐踩到底,测得左右轮制动力增长全过程的数值以及左、右车轮最大制动力。数据采集完停止电机,按下上位机界面上的“换至下一车轴”,进行下一轴制动力的检测。6)停止检测。按下上位机界面上“结束检测”按钮,制动力检测停止,待车辆制动停稳后,操作人员松开制动踏板,将被检车辆开出制动台。通过三次制动力检测,得出相应制动率(制动率:制动力/整车重量100%)的值如表1表2、表3所示。表1斯巴鲁翼豹的制动率斯巴鲁翼豹第一次第二次第三次平均值极差前轴79.9%79.1%80.0%79.7%0.9%后轴71.7%71.9%71.4%71.7%0.5%表2大众途观的制动率大众途观第一次第二次第三次平均值极差前轴64.5%64.3%64.7%64.5%0.4%后轴69.4%69.2%69.3%69.3%0.2%表3奥迪Q5的制动率奥迪Q5第一次第二次第三次平均值极差前轴79.8%79.4%79.2%79.5%0.6%后轴74.8%74.5%74.3%74.5%0.5%通过对比试验,三种车型在全时四驱制动力检测台上测试的制动率值其重复性误差、示值误差均小于国标GBT13564-2005所要求的“不大于1%”。实施例二本实施例对全时四驱汽车制动力检验装置进行标定,在某地厂家B安装全时四驱汽车制动力检验装置,将标定架固定在滚筒上,按JJG906-2009国标用砝码进行制动力标定。使用专用的标定装置依次加载砝码质量(mi)至满量程,再依次减载砝码质量(mi)至零,测出设定的各标定点所对应的左右轮制动力AD的示值,每个标定点重复测两三次,取其算术平均值。本装置实际标定中,L/R为10,测量数据如表4所示。表4制动力标定测量数据加载砝码值/kg50100150200250300350400制动力值/daN490980147019602450294024303920AD值5601132168022562810339439504506制动力为y,AD值为x,根据公式利用最小二乘法拟合可得,系数a1为0.87,a0为-6.96。也即y=0.87x-6.96。由此,可根据相应的AD值就可换算得到制动力的大小。当前第1页1 2 3