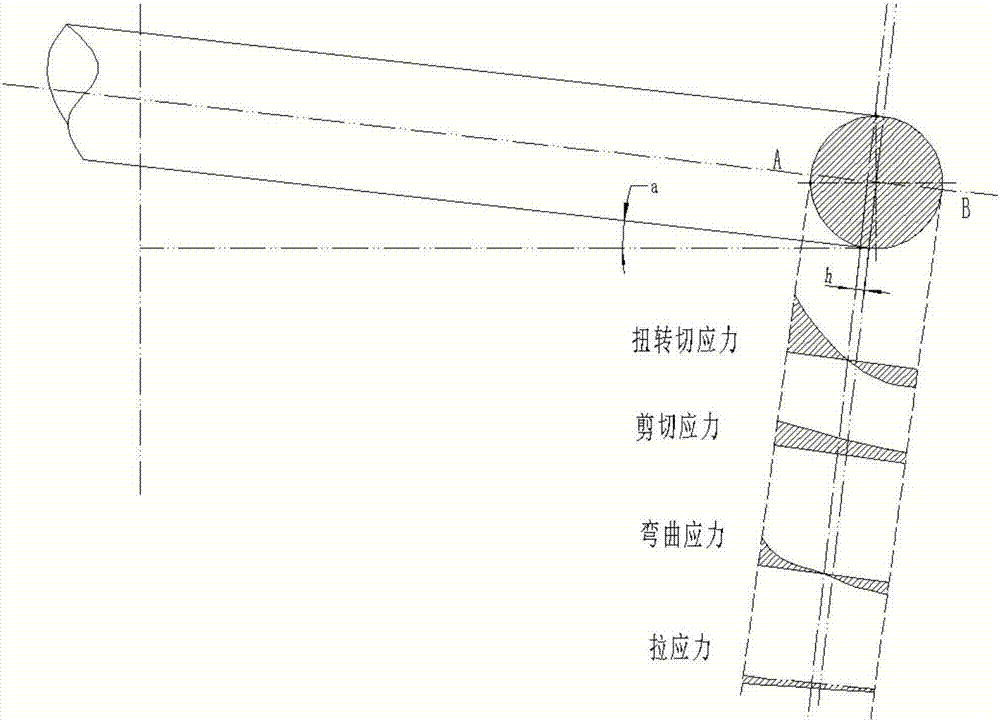
本实用新型涉及弹簧的疲劳试验
技术领域:
,具体涉及一种弹簧钢丝扭转疲劳试验装置。
背景技术:
:弹簧产业是国家工业经济中十分重要的基础产业。在汽车、电器电子、铁路、航空航天、能源等产业中,弹簧都是不可或缺的关键基础件。在实际工作条件下,多数弹簧在交变载荷作用下工作,其工作应力低于材料的屈服强度。弹簧在交变载荷下工作,经过长时间运行而发生失效的现象为疲劳破坏。据统计,约有80%以上弹簧失效是由疲劳引起的,其中大多数是突然断裂。随着现代机械向高速化和大型化方向发展,弹簧产品在高温、高压、重载和腐蚀等恶劣工况下运行,疲劳破坏事故更是层出不穷,造成的经济损失无法估量。因此,弹簧产品的疲劳强度与寿命设计对提高弹簧产品质量有着十分重要的意义。弹簧的抗疲劳性能是保证弹簧强度与使用寿命的重要指标,不论是弹簧生产商,还是弹簧用户,通常都使用疲劳试验机对弹簧进行疲劳检测。目前广泛采用的是基于弹簧产品的拉压疲劳寿命测试方法,其试验载荷与波形参数接近弹簧实际工作参数。然而弹簧的服役条件决定了弹簧疲劳属于高周疲劳。弹簧高寿命高可靠性的特点,导致疲劳试验时间长,甚至出现无限寿命的结果。弹簧的疲劳强度与可靠性直接影响设备的工作性能及安全性。由于弹簧产品存在设计缺陷在恶劣工况下突然疲劳断裂而导致设备发生重大事故的事例屡见不鲜,带来的经济损失及危害更是无法估量,因此测试弹簧的疲劳寿命非常重要。然而,目前广泛使用的拉压疲劳测试方法测试周期长,试验成本高,不能完全满足现阶段弹簧产品可靠性设计与质量保障的要求。因此,一种高效率低成本的弹簧疲劳寿命试验方法是本行业亟待解决的问题。技术实现要素:针对上述技术问题,本实用新型公开一种弹簧钢丝扭转疲劳试验装置,通过将钢丝试件与制成弹簧的钢丝同尺寸,可满足基于疲劳试验中尺寸效应的要求;其快速高效的特点又完全满足基于弹簧材料的疲劳试验要求。本实用新型的技术方案是这样实现的:一种弹簧钢丝扭转疲劳试验装置,所述的试验装置包括驱动系统,液压夹具系统,静止端和试验台架四个部分,驱动机构被配置为试验装置的动力执行机构,包括直驱电机和输出主轴;液压夹具系统包括液压夹头及液压泵站;静止端包括扭矩传感器和支撑架;试验台架被配置为支撑整个扭转装置,它包括导轨,导轨滑块,定位块及试验台面,液压夹具系统之间夹持钢丝试件,通过PLC控制系统将计算机与动力执行机构连接,PLC控制系统在接收到计算机的参数信息后,控制动力执行机构,对钢丝试件加载作用力,使得钢丝试件做往复的扭转运动,扭矩传感器采集钢丝试件在试验时的扭矩值,PLC记录钢丝试件的扭转次数并将获得的试验参数传递给计算机,计算机保存试验的扭转次数及试验参数,使得钢丝扭转试验等效为弹簧拉压疲劳试验。所述的动力执行机构采用直驱电机进行动力加载,所述的直驱电机包括转子、定子以及绝对正弦编码器,所述的转子通过压紧联轴器与机器轴承固定相连,电机外壳与机框通过螺栓固定相连,在机框上的螺栓连接处设置法兰连接面。所述的动力执行机构采用CDDR系列C063C电机及配套的AKD-P01206驱动单元作为动力加载单元。所述的液压夹头采用弹簧夹头夹持,夹头的瓣数为3~5个,液压泵站通过配套的夹头座为夹头输入液压动力。所述的输出主轴通过滚动轴承安装在机架上,滚动轴承工作时内外套圈间有相对运动,滚动体既自转又围绕轴承中心公转,滚动轴承的内套圈随输出主轴一起往复旋转,滚动轴承的外套圈静止不动。所述的输出主轴与法兰盘通过圆头平键实现联接,圆头平键的侧面是工作面,工作时靠键与键槽的互压传递转矩。所述的试验装置的主体通过电路连接实现电路控制,所述的试验装置的主体电路包括主电路,控制电路,报警电路,电磁制动电路以及与PLC连接电路。所述试验装置在实验过程中,包含两种试验模式,所述的试验模式包括基于弹簧产品的疲劳寿命试验和基于弹簧材料的疲劳寿命试验,其中,基于弹簧产品的疲劳寿命试验中,在第七步中输入参数包括设定试验编号及日期,便于以后查找试验数据;用户输入弹簧产品的基本参数及工作参数,所述的基本参数及工作参数包括钢丝直径d、中径D、试验最大载荷F1、试验最小载荷F2、标定长度L、螺旋升角ɑ,点击参数计算后,计算机可以给出将弹簧实际工况等效转换为钢丝扭转疲劳试验的相应参数,等效的相应参数为预扭角最小扭转角循环特性系数r、最大负载扭矩T、转角幅长径比n;基于弹簧产品的疲劳寿命试验中,在第七步中输入参数包括设定试验编号及日期,通过输入数据钢丝直径d、最大切应力τmax、循环特性系数r、以及标定长度L,得到输出数据预扭角转角幅最小扭转角最大负载扭矩T,试验结束后,点击数据保存选项,可以存储此次计算结果,下次试验时可以提取此次结果,也可直接点击进入试验选项。所述直驱电机的控制模式采用PLC脉冲发生模式,通过计算机将换算的工作参数传递给PLC,PLC根据这些参数,发出脉冲信号给伺服驱动器,伺服驱动器根据脉冲信号的频率和脉冲个数控制电机的转速和转角,同时,电机尾部设置的旋转编码器将电机的转角及转速反馈给伺服驱动器,伺服驱动器对比发出脉冲与反馈脉冲调整电机转角,完成伺服控制,PLC记录发出脉冲列的个数,当试件扭转断裂时,安装在固定端的扭矩传感器采集不到扭矩信号,PLC停止给伺服驱动器发送脉冲信号,电机停止运转;由于每完成一次试验电机会转向一次,因此方向脉冲的个数等于试验的次数;PLC将方向脉冲列的个数传递给计算机,即完成试验次数的记录。所述的导轨为直线导轨,导轨设置在试验台架的上表面,试件钢丝夹在液压夹具系统之间,在钢丝试件安装后,静止端前后都设置有定位块,定位块被配置为保持钢丝在实验过程中拉直。本实用新型的有益效果如下:本实用新型所述的试验方法其试件与制成弹簧产品的钢丝同尺寸,与基于材料的旋转弯曲疲劳试验方法相比,它可以满足疲劳试验中尺寸因素的要求,减少了修正因素,获得的结果更为可靠;与基于产品的拉压疲劳试验方法相比,它在高应力,大振幅的试验要求场合中优势显著。本实用新型所述的试验装置通过从采用弹簧夹头夹持、零件滚动轴承及圆头平键的设定,满足试验方法过程中高频长周期的需求,使得试验装置在实验运行过程中安全可靠,采用直驱伺服驱动系统作为传动方式,减少中间的机械传动装置,提高了试验装置的灵活性和响应速度,避免了传动环节的机械磨损,提升了试验装置长周期工作的安全性和稳定性,消除了中间环节的机械间隙,满足试验高精度的要求;通过采用位置控制的伺服控制模式,以转角为被控量,确保了电机位置的准确性。附图说明为了更清楚地说明本实用新型实施例或现有技术中的技术方案,下面将对实施例或现有技术描述中所需要使用的附图作简单地介绍,显而易见地,下面描述中的附图仅仅是本实用新型的一些实施例,对于本领域普通技术人员来讲,在不付出创造性劳动的前提下,还可以根据这些附图获得其他的附图。图1为本实用新型一种弹簧钢丝扭转疲劳试验装置中所述弹簧钢丝试件的簧丝截面示意图;图2为本实用新型一种弹簧钢丝扭转疲劳试验装置中簧丝实体的弹簧材料截面应力状态示意图;图3为本实用新型一种弹簧钢丝扭转疲劳试验装置所述的弹簧材料截面受力分析图;图4为本实用新型一种弹簧钢丝扭转疲劳试验装置所述图3中的截面A的切应力分布图;图5为本实用新型一种弹簧钢丝扭转疲劳试验装置所述扭转疲劳试验装置控制原理图;图6为本实用新型一种弹簧钢丝扭转疲劳试验装置所述总体电路接线图;图7为本实用新型一种弹簧钢丝扭转疲劳试验装置中所述试件的区域分布示意图;图8为本实用新型一种弹簧钢丝扭转疲劳试验装置中所述的打滑测试流程图;图9为本实用新型一种弹簧钢丝扭转疲劳试验装置的控制方法步骤流程图;图10为本实用新型一种弹簧钢丝扭转疲劳试验装置的夹具结构示意图。具体实施方式下面将结合本实用新型实施例中的附图,对本实用新型实施例中的技术方案进行清楚、完整地描述,显然,所描述的实施例仅仅是本实用新型一部分实施例,而不是全部的实施例。基于本实用新型中的实施例,本领域普通技术人员在没有付出创造性劳动前提下所获得的所有其他实施例,都属于本实用新型保护的范围。本实用新型公开一种弹簧钢丝扭转疲劳试验装置,其基本思想是将弹簧拉压疲劳试验等效为同参数钢丝的扭转疲劳试验,两者等效转换的具体推导过程如图1~4所示:在通过弹簧轴线的平面V所截的弹簧材料斜截面上,作用有扭矩Tt=FD/2和径向力F。平面V'垂直于弹簧材料中心线,与平面V成夹角ɑ,ɑ为弹簧的螺旋升角,在平面V'上的截面A是弹簧材料截面。在弹簧材料截面A的中心取弹簧材料中心轴线为t轴,法线为n轴,n轴位于V平面与V'平面的交线上,次法线为b轴,b轴位于V'平面内。在弹簧材料的截面A内,Tt和F可分解为绕t轴回转的扭矩:式中:F-轴向力;D-弹簧中径;α-螺旋升角绕b轴回转的弯矩:沿t轴作用的轴向力:Fb1=Fcosα沿b轴作用的径向力:Ft1=Fsinα旋绕比不是很大(C<10),簧丝直径相对于弹簧中径并不可以忽略,这时还需要考虑簧丝曲度的影响。在簧丝截面上(与中性轴垂直截面)面上各点到弹簧轴线的距离不同导致了各点单元应力也不同,同时,因为簧丝内外径的差值不可忽视,簧丝曲度导致了截面应力的修正。截面NN'与截面MM'均是垂直于簧丝中性轴的截面,故在载荷加载前后截面NN'与截面MM'均保持平面状态,即M点与M'点的变形量相同。N'M'明显长于NM,因此N'M'段的单位长度变形量必定小于NM段,即M点的应变大于M'点的应变,弹性范围内应变与应力成正比,故M点的应力大于M'点应力。根据径向力,轴向力,弯矩及扭矩加载在截面产生的应力分布,可以分别得到截面上x=0,AB段路径上各应力的分布,如图2所示,显然等效应力的最大值位于A点,最小值位于B点。A点剪切应力与扭转切应力方向相同,故二者直接相加,弯曲应力是张应力与压应力方向相反,二者相减,应用第四强度理论:如图2所述的弹簧材料截面应力状态示意图所示,A点等效应力:其中同簧丝直径规格的弹簧产品与钢丝试件,建立弹簧压缩试验与钢丝扭转试验等效转换关系的前提是二者加载过程中弹簧内圈与钢丝表面的等效应力相等,利用这一等式建立弹簧产品轴向载荷F与钢丝试件加载扭矩T之间的对应关系式。钢丝试件其表面等效应力最大为σ1,根据第四强度理论它与钢丝表面切应力τ1的关系表达式为:在钢丝扭转试验中,对钢丝试件施加的当量扭矩T与钢丝表面切应力τ1的关系式:故可建立等效应力与扭矩的关系式:根据两种试验方法等效应力相等的前提建立扭矩与轴向力的关系式:最终获得轴向力与扭矩的表达式:根据上式可以将簧丝直径为d,旋绕比为C螺旋升角为α的弹簧产品进行最大轴向载荷F1最小轴向载荷F2的压缩疲劳试验等效转换为直径为d进行最大扭矩T1最小扭矩T2的往复扭转疲劳试验,其中T1与F1,T2与F2满足轴向力与扭矩的表达式。等效转换的含义是弹簧最大应力点内圈边缘与钢丝最大应力点钢丝表面两者等效应力相等。上述推导过程可以从理论上证明受交变载荷的弹簧产品其疲劳强度可以利用同截面钢丝的扭转疲劳试验获得。目前,根据试验目的弹簧疲劳试验大致分为两类:一类是对弹簧产品或设计的弹簧样品进行试验,这类试验主要是对产品或设计的零件进行疲劳寿命验证和可靠性评定,它是基于实际弹簧产品尺寸的试验,一般利用典型的弹簧疲劳试验设备对弹簧试件进行试验,即基于弹簧产品的拉压疲劳试验方法;另一类是为确定弹簧材料的疲劳极限或S-N曲线所进行的试验,其主要目的是为设计提供数据,一般要求试验频率高,试验应力大,循环特性系数小。基于弹簧产品的拉压疲劳测试方法试验载荷与波形参数接近弹簧实际工作参数,但弹簧疲劳是高周疲劳,疲劳试验需消耗大量的时间,弹簧本身高寿命高可靠性的特点甚至会出现无限寿命的情况。而基于弹簧材料的旋转弯曲疲劳测试方法,其试验结果可能不准确。因为这种方法先忽略了弹簧的几何形状、表面状态及加工质量等因素对试验结果的影响,而这些因素恰恰是决定弹簧疲劳性能好坏的关键因素。试验完成后再将材料的疲劳测试数据根据上述因素的影响进行修正,可能会导致最终的试验结果失真。根据两种试验目的,为设计提供可靠数据和验证产品的疲劳强度,设定试验装置具备两种疲劳测试模式:基于弹簧产品的疲劳寿命试验,基于弹簧材料的疲劳寿命试验。1)基于弹簧产品的疲劳寿命测试:已知弹簧参数如下:钢丝直径d,中径D,螺旋升角ɑ,试验最大载荷为F1,最小载荷F2,工况下的循环特性系数r,钢丝的标定长度l,标定长度与钢丝直径的比值n。根据扭转角与扭矩的关系式:式中:T-负载扭矩;G-钢丝材料的切变模量;IP-极惯性矩,计算公式为:于是,连立以上三式可以得到弹簧的轴向力与钢丝扭转角度之间的关系式:因此,将F1,F2的值代入上式可以得到它们分别对应的扭转角值其中为输出参数中的预扭角;为输出参数中的最小扭转角。同时可以求出转角幅:式中:r-循环特性系数;-最大扭转角;2)基于弹簧材料的疲劳寿命测试:钢丝的直径d,试验要求的最大切应力τmax,循环特性系数r,钢丝试件标定长度l,需求出对应的最大转角,转角幅。切应力与扭矩的关系式:扭转角与扭矩的关系式:于是有切应力与扭转角之间的转换关系:式中:τ-切应力;l-标定长度;将试验要求的最大应力值代入上式即可得出满足试验要求的最大扭转角,再利用公式求出转角幅,将弹簧材料疲劳试验的应力幅等效转换为钢丝扭转疲劳试验的转角幅。作为本实用新型的实施例,钢丝材料为55CrSi,考虑到电机的功率范围及课题研究的高效和经济性,试件直径范围选定为3~5mm。根据GB/T239-1999《金属线材扭转试验方法》规定,金属线材公称直径d在1~5mm之间,标定长度l一般为100d,特殊协议时可以采用20~50d。当扭矩值确定时,标定长度与转角值成正比。转角值越小试验频率越高,因此从提高效率的角度出发,标定长度应该小一些合适。另一方面,标定长度过小会影响试验结果,使得靠近夹持端的试件部位应力集中易断裂。因此,综合两方面的考虑,两夹头间标定距离l取为30~60d,即在150-300mm之间。3)试验装置的最大扭矩及最大旋转角:试件采用55CrSi钢制造的油淬火回火弹簧钢丝,其抗拉强度最大能达到2011Mpa。通常,金属的抗扭强度τ约为抗拉强度的0.55~0.62倍。因此设定本试验装置中可以达到的最大切应力τmax为1200MPa,试件长径比n最大值为60。于是有试验装置疲劳试验的最大扭矩(负载转矩):对应最大旋转角度:因此,设定试验装置工作扭矩-40NM~40NM,工作扭转角-120°~120°。本实用新型通过阐述扭转疲劳试验方法的基本理论,受轴向力作用的弹簧其材料截面起主要作用的是扭矩和径向力,最大切应力位于弹簧内侧外表面,疲劳裂纹源一般产生于此。设定扭转疲劳试验中钢丝外表面应力状态与弹簧内侧外表面的应力状态等效,建立拉压疲劳试验的轴向力和扭转疲劳试验当量扭矩之间的数值关系。根据不同的试验目的,提出试验装置的两种工作模式,基于弹簧产品拉压疲劳试验和基于弹簧材料的疲劳试验。详细阐述两种试验方法等效为钢丝扭转疲劳试验的推导及数量关系。根据弹簧材料特性求出试验装置需满足的最大扭矩及最大旋转角度。本实用新型提出的基于钢丝的扭转疲劳试验方法具备以下几个显著特点:1)弹簧拉压试验方法受弹簧结构限制,一般切应力仅能到1050MPa左右,弹簧就已经压并了,无法再增大试验载荷。而本实用新型提出的扭转疲劳试验法施加的扭矩不受试件结构限制,最大切应力可以接近抗扭强度。2)由于拉压疲劳试验装置传动结构的限制,试验行程范围小,位移幅小,在满足试验要求的最大切应力时可实现的循环特性系数最小值仅为0.3,而本实用新型试制的试验装置采用直驱传动方式,扭转角不受限制,转角幅值范围广,循环特性系数的最小值完全可以达到-1,可以实现对称循环应力下的钢丝扭转疲劳试验。3)拉压疲劳试验设备仅能进行疲劳寿命测试,而本实用新型研发的扭转疲劳试验装置既适于弹簧疲劳试验,还可以满足钢丝的静态机械性能与动态疲劳试验。4)以弹簧钢丝代替弹簧产品,大大降低了试件的制作成本,可以在控制成本的前提下,进行多次重复试验,即低成本获得更准确的数据。本试验方法其试件与制成弹簧产品的钢丝同尺寸,与基于材料的旋转弯曲疲劳试验方法相比,它可以满足疲劳试验中尺寸因素的要求,减少了修正因素,获得的结果更为可靠。与基于产品的拉压疲劳试验方法相比,它在高应力,大振幅的试验要求场合中优势显著。实施例2,根据上述弹簧钢丝扭转疲劳试验方法,本实用新型还公开一种弹簧钢丝扭转疲劳试验装置,所述的试验装置包括驱动系统,夹具系统,优选液压夹具系统,静止端和试验台架四个部分,驱动机构包括直驱电机和输出主轴;液压夹具系统包括液压夹头及液压泵站;静止端包括扭矩传感器和支撑架;试验台架被配置为支撑整个扭转装置,它包括导轨,优选为直线导轨,导轨滑块,定位块及试验台面。根据JB/T9370-1999《扭转试验机技术条件》试验机扭转角示值各项允许误差应符合下列规定:a.示值相对误差的最大允许值为士1%;b.示值重复性相对误差的最大允许值为士1%;用电机尾部旋转编码器对转角示值以不少于五点进行检验。各点均匀分布,选择试验装置最大转角的10%,20%,50%,80%,100%为五个不同的测试点,不夹持试件测试,每点至少测量三次(三次理论转角相同,但转速及时间不同);示值相对误差q按上述公式计算:-同一测量点,三次测试转角示值的算术平方根,单位度-理论标准转角值,单位度示值重复性相对误差b:-同一测量点,样机转角示值的最大值-同一测量点,样机转角示值的最小值控制系统误差测试记录及计算结果根据试验计算结果,试验装置符合JB/T9370-1999《扭转试验机技术条件》规定的精度要求。由前面对试验装置的功能实现分析及极限值计算,可以得出试验装置的性能指标要求如下:1)工作扭矩:-40NM~40NM;2)工作行程:-120°~120°;3)钢丝直径:3~5mm;4)加载频率:0~30Hz;5)工作温度:5°~45°;6)工作方式:连续工作;7)测量精度:控制系统转角测试精度0.008%;8)加载方式:动载频率可调,转角幅值可调。所述的夹具系统按照试验要求,迅速实现试件的定位与夹紧,并在试验过程中保持试件和机器之间的相对位置,在试验过程中,夹具要保证试件不打滑,即保持试验过程中试件对夹具的摩擦力矩M和主轴施加给夹具的负载转矩Tl大小相等,方向相反。因为负载转矩:于是可知径向夹紧力:式中:T-负载扭矩;d-钢丝直径;μ-摩擦系数当取到最大径向夹紧力时,切应力τmax应为1200MPa,试件直径应为5mm,将摩擦系数μ=0.16代入有,夹紧力W=73.6KN。在试验过程中还必须保证接触应力在许用接触应力范围内。夹紧力过大,接触应力超过许用接触应力,试件可能直接在夹持部位断裂。因此,如何在保证试件夹紧的前提下减小接触应力是本实用新型的研究重点。本实用新型主要考虑了两种夹持方式,利用赫兹公式计算两种方式下最大接触应力,考察其是否满足试验要求。1)赫兹公式的假设:赫兹公式的主要目的是研究两物体因受压相触后产生的局部应力和应变分布规律。1881年H.R.赫兹最早研究了玻璃透镜在使它们相互接触的力作用下发生的弹性变形。他假设:①接触区发生小变形。②接触面呈椭圆形。③相接触的物体可被看作是弹性半空间,接触面上只作用有分布的垂直压力。凡满足以上假设的接触称为赫兹接触。当接触面附近的物体表面轮廓近似为二次抛物面,且接触面尺寸远比物体尺寸和表面的相对曲率半径小时,由赫兹理论可得到与实际相符的结果。在赫兹接触问题中,由于接触区附近的变形受周围介质的强烈约束,因而各点处于三向应力状态,且接触应力的分布呈高度局部性,随离接触面距离的增加而迅速衰减。此外,接触应力与外加压力呈非线性关系,并与材料的弹性模量和泊松比有关。在压紧力F作用下,两圆柱体接触,其接触面为矩形,其最大接触应力σHmax位于接触面宽中线处:接触面半宽式中:μ1-试件材料泊松比;μ2-夹具材料的泊松比;E1-圆柱体1的弹性模量;E2-圆柱体2的弹性模量;ρ-综合曲率半径,满足正号用于外接触,负号用于内接触,平面和圆柱或球接触,取平面曲率半径ρ2=∞;ρ1-圆柱体1初始接触线处的曲率半径;ρ2-圆柱体2初始接触线处的曲率半径;b-两接触体的接触线长;最大接触应力2)卡盘夹持:卡盘是指利用均布在卡盘体上的活动卡爪的径向移动,把试件夹紧和定位的通用夹具。一般由卡盘体,活动卡爪和卡爪驱动机构三部分组成,其中央有通孔,以便通过试件,背部有圆柱形结构,可通过法兰盘与装置主轴端部相连接。本实用新型所述的试验以试件的外圆柱面定位,因此,可采用三爪卡盘夹紧。三爪卡盘是一种典型的定心夹紧机构。三只卡爪能同步移动,因此在夹紧试件的同时实现了定心定位。卡盘每爪所需夹紧力:式中:K-夹持系数,卡盘夹紧方式K取1.2;由于卡爪夹持部分为平面:式中:ρ1-钢丝试件初始接触线处的曲率半径;ρ2-卡盘初始接触线处的曲率半径;ρ-综合曲率半径代入赫兹公式可以得到卡盘夹持方式下接触处的最大接触应力:式中:μ-摩擦系数,弹簧夹头夹持时,接触线长b=10mm,弹性模量E=209GPa,摩擦系数μ=0.16。当d1=5.00mm,τ=1200MPa时,最大接触应力达最大值,σHmax=2318MPa。根据GB/T239-1999《金属线材扭转试验方法》规定,试验装置夹头应具有足够的硬度,夹持钳口的硬度为55HRC~65HRC,试件材料55CrSi的硬度一般为HRC50~53。当两种接触材料为钢-钢,硬度(HB)为500-500时,许用接触应力[σHmax]=1336MPa。3)弹簧夹头夹持:弹簧夹头是一种定心夹紧装置,如图10,能精确定位与夹紧试件,具有抵抗扭矩和承受来自多方向附加作用力的功能,具有增大驱动力和转换驱动力为夹紧力的功能,能在较宽的主轴转速范围内工作且只有极小的夹紧力损失。本装置若采用哈挺生产的16C弹簧夹头夹持,在夹紧力作用下,弹簧夹头与试件表面理论上为线接触,考虑到弹性变形,实际上是很小的面接触。接触时的接触应力和接触尺寸按赫兹公式计算。接触面为矩形,最大接触应力σHmax位于接触面宽中心线处;接触表面的失效形式是塑性变形。弹簧夹头工作部分材料为65Mn,泊松比μ2=0.3;试件材料为55CrSi,泊松比μ1=0.3。同类金属的弹性模量相差不大,夹头弹性模量E1=209GPa,试件弹性模量E2=209GPa。当μ1=μ2=0.3,E1=E2=E时,计算公式简化为:将试件直径范围(3~5mm)分为二十个系列:每个系列相差0.1mm(0.008英寸),对应的弹簧夹头夹持半径也分20个系列,从3.10-5.10mm。试件直径比夹具夹持直径最多相差0.1mm,按夹持部分直径与试件直径相差0.1mm计算。最终可以得到采用弹簧夹头夹持时,试件夹持部位接触应力的公式:式中:d1-试件直径;τ-最大切应力;由此可以看出,对接触应力影响最大的是试验要求的最大切应力。根据GB/T1358-2009《圆柱螺旋弹簧尺寸系列》规定,对于一般用途的圆柱螺旋弹簧其弹簧材料直径在3~5mm范围内优先系列如下表所示:以弹簧材料直径优先系列作为常用试件,本实用新型给出最大切应力在一定范围内(0~1200MPa)对应的理论夹紧力及对应接触应力。第一系列3.003.504.004.505.00第二系列3.20常用试件系列夹持参数由夹持参数表可知:试件直径在3~5mm范围内,当试件直径为5.00mm,最大切应力为1200MPa时,最大接触应力σHmax取得最大值,为1027MPa,满足σHmax<[σHmax]=1336MPa,因此,采用16C弹簧夹头夹紧能够取得很好的夹持效果。4)夹具的动力源:气压和液压是夹具中使用最多最广泛的动力源。气压夹紧工作压强较低,动力装置体积及尺寸较大,不符合试验装置高效节能,结构紧凑的要求。而液压夹紧夹紧后保持油压能力强,可由多种动力源提供动力,使用方便,液压系统工作油压较高,液压缸尺寸较小,可以满足试验装置体积小,结构紧凑,节能经济的要求。因此,试验装置中采用哈挺公司出产的16C液压弹簧夹头夹紧试件。夹头轴向拉力的计算:轴向拉力式中:K-安全系数;ɑ-夹头锥角;-摩擦角;Q′-夹爪变形阻力;夹爪变形阻力:F-弹簧夹头的弹性变形系数。当夹头瓣数为3,4,5时,其值分为600,200,40。这里取40;d-弹簧夹头弯曲部分外径(m);l-弹簧夹头锥面中部到根部的距离(m);t-弹簧夹头弯曲部分的厚度(m);Δ-夹头与工件径向间隙(直径上)(m);根据弹簧夹头推荐尺寸:D=3-5mm时,d1=17.于是:代入计算有Q'=11.55×10-6N哈挺16C系列夹头锥角α=10°,摩擦系数摩擦角K是安全系数,本例采用液压动力源,因此取为1.5。再将最大夹紧力为W=73.6KN代入公式,最终计算得轴向拉力Q=38.24KN。与16C夹头配套的夹头座其动作缸支持半径为32.88mm,作用面积为3392mm2,所需的工作压强P=11.27MPa。因此,选择哈挺公司16C液压弹簧夹头及其配套的夹头座作为试验装置的夹具,液压源选择工作压强为0~12MPa的液压泵站。试验装置对夹具的要求有两点,一是夹紧力足够大,必须保证试件在试验过程中不打滑,夹持部位不松弛;二是夹持端对试验结果的影响小,即要求夹持面积大,受力均匀,接触应力小于许用接触应力。通过利用赫兹公式法和ANSYS软件分析,发现液压夹头夹紧的夹持方案符合夹持要求。作为本实用新型的一些实施例,试验装置利用滚动轴承将输出主轴安装在机架上,与滑动轴承相比,滚动轴承的优势在于:在一般工作条件下,摩擦阻力矩大体和液体动力润滑轴承相当,比混合润滑轴承要小很多倍。滚动轴承效率较混合润滑轴承要高一些,启动力矩小有利于在负载下启动;径向游隙比较小,可用预紧方法消除游隙,运转精度高;对于同尺寸的轴颈,滚动轴承的宽度比滑动轴承小很多,可以使试验装置轴向结构紧凑;大多数滚动轴承能同时承受径向和轴向载荷,轴承组合结构简单;消耗润滑剂少,便于密封,易于维护;标准化程度高,成批生产,成本较低,能保证质量,在使用,安装和更换等方面很方便。在试验装置使用中,轴承的工况是转速高,载荷较小且以径向载荷为主,要求旋转精度高,因此选择了结构简单,主要受径向载荷也可承受双向轴向载荷,摩擦系数小,极限转速高的深沟球轴承。滚动轴承工作时内外套圈间有相对运动,滚动体既自转又围绕轴承中心公转,滚动体和套圈分别受到不同的脉动接触应力。试验装置中滚动轴承的内套圈随主轴一起往复旋转,滚动轴承的外套圈静止不动。滚动轴承受载后各滚动体的受力大小不同,滚动体与套圈间产生变化的接触应力,试验周期长,各元件接触表面都可能发生接触疲劳失效,出现点蚀现象,因此必须进行接触疲劳寿命计算。此外,在一定的静载荷或冲击载荷作用下,滚动体或套圈管道上将出现不均匀的塑性变形凹坑,这时轴承的摩擦力矩,振动和噪声都将增加,运转精度也会降低,因此一般工作条件下的回转滚动轴承还需进行静强度计算。输出主轴上采用一对深沟球轴承,初步选定型号为6215,输出主轴最大转速n=300r/min,轴承最大径向载荷Fr=388.31N,没有轴向载荷作用。轴承型号Cr/NC0r/ND/mmB/mmN0/(r/min)619152430022500130255600经计算得,试验装置对于轴承的更换周期至少是5年,我们发现基本额定寿命远大于预计使用寿命,因此在寿命计算上该规格轴承符合要求。基本额定静载荷C0r是指引起轴承滚动体与滚道接触中心处最大接触应力时所相当的假想径向静载荷。为了限制滚动轴承在静载荷作用下产生过大的接触应力和永久变形,需进行静载荷计算。当量静载荷P0r=Fr=388.31N,计算额定静载荷C0r'=S0P0r,装置中对旋转精度及平稳性要求高,因此根据机械设计手册要求安全系数S0取值为2,则C0r>C0r'=776.62N。采用61915深沟球轴承,寿命和静载荷计算均可满足工作要求。作为本实用新型的一些实施例,试验装置采用普通圆头平键实现主轴与法兰盘的联接以传递转矩,键的侧面是工作面,工作时靠键与键槽的互压传递转矩。一般压溃或磨损常是主要失效形式。因此,需按联接的挤压强度或耐磨性计算。一般来说,将法兰盘作为较弱零件按其计算。试验装置暂定的圆头平键参数规格是16×10×90,即宽b=16,高h=10,键长L=100。假设压力在键的接触长度内均匀分布,则根据挤压强度或耐磨性的条件性计算,求得联接所能传递的转矩:式中:h-键的高度;L′-键的接触长度;d-轴径;[P]-许用强度本例键的高度h=10,键的接触长度L'=100-16=84,轴的直径d=50,键的工作条件是轻微冲击载荷,因此许用强度[P]=40MPa。根据计算出所能传递的扭矩T=420NM,而电机输出的最大峰值转矩仅为180NM。经计算得,所述主轴与法兰盘联接的挤压强度完全可以满足工作要求,这种规格的圆头平键可以安全使用。作为本实用新型的一些实施例,本实用新型还公开一种新型的驱动机构-直驱伺服驱动系统,直驱传动是一种新型的电机直接和运动执行部分的结合,即电机直接驱动机器运转,没有中间的机械传动环节。在扭转疲劳试验过程中,系统一直处于从零加速到最大速度再减速到零,往复长周期运转的状态,根据这一试验特点,传动系统必须满足可重复性能好,起停时间短,传动部件数量少且简单,可靠性高的要求,而这些要求恰恰是直驱传动方式的优势所在。因此,本试验装置采用直驱伺服驱动系统。作为本实用新型的一些实施例,利用科尔摩根公司研发的MOTIONEERING选型软件对暂选电机与试验要求进行了匹配,分别考察了加速转矩,制动转矩及转矩均方根这三个数值量,电机选型的五个条件中,峰值转矩,最大转速,功率,惯量这四个条件余量都满足要求。由于电机一直处于加速减速状态,换向频率大,温升高,因此转矩均方根比较大,连续转矩这个条件,余量很小,已经达到极限,认为可以满足正常工作条件下电机散热条件良好的要求。因此,最终选择科尔摩根公司CDDR系列C063C电机及配套的AKD-P01206驱动单元。DDR电机包括转子、定子以及工厂内校准的绝对正弦编码器,它采用机器轴承来支撑转子。通过一个新式压紧联轴器将其转子连接到机器轴,其外壳通过螺栓连接到机框,并带有螺栓安装圆周和法兰连接面,其安装过程简单,将模块化DDR电机滑入机器轴上,用螺栓将模块化DDR电机外壳固定到机器框架上,拧紧压紧联轴器卸下储存装运用固定件,连接电缆即安装完成。本试验属于高频疲劳寿命试验,运行周期可能会长达十几天,且电机一直处于加速减速换向频繁的状态,对于电机内部温升控制要求严格。为防止线圈发热量过大电机损坏的情况,必须严格满足转矩均方根小于电机额定转矩的要求,由计算式可知频率f与转角幅,最大切应力,试件直径及系统转动惯量成反比。使用本装置时,确定了钢丝试件的直径,试验要求的转角幅和最大切应力,系统可以自动给出能够达到的最大频率。作为本实用新型的实施例,本试验中最大试件直径为5mm,最大切应力1200MPa,转角幅为45度时经过计算,频率为11Hz。作为本实用新型的一些实施例,试验中使用直驱电机作为动力执行机构,通过电机控制模式实现对直驱电机的控制,经电机选型计算后选择与装置匹配的电机型号及伺服驱动器。试验开始前,用户输入试验参数,计算机换算出对应的对应的工作参数,所述的工作参数包括工作频率,旋转角度等参数。本装置提供两种电机控制模式。模式一是PLC脉冲发生模式,具体过程是计算机将换算的工作参数传递给PLC,PLC根据这些参数,发出脉冲信号给伺服驱动器。伺服驱动器根据脉冲信号的频率和脉冲个数控制电机的转速和转角,同时,电机尾部设置的旋转编码器将电机的转角及转速反馈给伺服驱动器,伺服驱动器对比发出脉冲与反馈脉冲调整电机转角,完成伺服控制。PLC记录发出脉冲列的个数,当试件扭转断裂时,安装在固定端的扭矩传感器采集不到扭矩信号,PLC停止给伺服驱动器发送脉冲信号,电机停止运转。由于每完成一次试验电机会转向一次,因此方向脉冲的个数等于试验的次数。PLC将方向脉冲列的个数传递给计算机,即完成试验次数的记录。模式二是由伺服驱动器控制电机的模式。利用科尔摩根公司研制的KMWorkBench软件,输入计算机换算的工作参数,设定电机旋转的运动时间图。此模式的特点是可以预设三种运动时间图,可以在试验过程中的改变频率及试件的速度时间图。伺服驱动器具备输出数字信号引脚,设定电机每旋转到正向最大转角位置输出信号发出一个脉冲,将该输出引脚与PLC的输入端子连接,由PLC高速计数器记录脉冲个数,此脉冲个数即为试验次数。试验装置的控制原理图如图5所示。整个控制系统主要由三部分构成:电源部分、控制核心部分,执行部分。1)电源部分:AC220V及变压器提供动力控制能源。DC24V开关电源,为PLC供电,提供伺服控制信号电源。2)制核心部分:该部分是由PLC负责发出控制信号,伺服驱动器对伺服电机实现闭环控制,对其各种信息做出快速、准确的反应,处理随时变化的信号。3)执行部分:该部分由执行电机拖动所需机械设备进行工作,电机工作情况由自身编码器反馈给驱动器,进行闭环控制。本实用新型所述一种弹簧钢丝扭转疲劳试验方法的总体电路接线图,如图6所示,主体分为五个部分:主电路,控制电路,报警电路,电磁制动电路以及与PLC连接电路。电磁制动电路:单独采用外接24V电源供电,正常工作下,EMG触点闭合,RA常开触点闭合。紧急停止按钮按下,EMG常闭触点断开或是发出警报故障信号,RA常开触点断开,制动器电路失电,压敏电阻消耗放电,电磁抱闸启动,转子立即抱死。EMG紧急停止的常闭触点,急停时断开,任何控制模式下,只有EMG是闭合状态,伺服系统才可以正常工作;总体控制过程:启动过程:空开NFB按下,控制电源接通,ALM有输出,线圈RA得电,RA常开触点接通,按下ON按钮,线圈MC得电,MC常开触点接通,于是主电路接通,整个伺服系统开始正常工作。停止:按下OFF按钮,MC线圈失电,主电路断开出现警报:ALM触点失电,线圈RA失电,电流逆向,二极管发光,主电路中的RA常开触点失电,主电路断开,且电磁制动电路中的RA常开触点失电,电磁抱闸启动,转子立即抱死。紧急停止:按下急停按钮,EMG常闭触点断开,伺服电机电磁抱闸启动,转子立即抱死。伺服驱动器与PLC的连接:主要是X7和X8接线端子的引脚与PLC连接,具体的引脚连线及实现功能如下表所示。伺服驱动器与PLC连线的各引脚作用根据扭转疲劳试验特点,通过转角位置调整试件扭矩,因此选择位置控制模式。位置控制的根本任务就是实现执行部分对位置指令的精确跟踪,被控量一般是负载的空间位移;在位置控制方式下,伺服驱动器接收PLC发出的位置指令脉冲及方向脉冲,送入脉冲列形态,经电子齿轮比分倍频后,在偏差可逆计数器中与反馈脉冲信号比较后形成偏差信号;反馈脉冲是由光电编码器检测到电机实际所产生的脉冲数,经四倍频后产生的;位置控制精度由旋转编码器每转产生的脉冲数控制;X7端口的第二针脚为指令脉冲输入端口,X7端口的第三针脚为方向信号输入端口,分别接收由PLC发出控制信号,控制伺服驱动器的运行角度及运行方向。由于选用PLC作为上位机,因此脉冲的输入方式采用集电极开路输入方式;脉冲信号的传递过程:VDD与内部24V直流电源正极相接,并与OPC短接,为整个输入电路提供电源;集电极导通时,电路导通,二极发光管发光,伺服驱动器内部光感电敏接收到高电平;集电极截止时,电路断开,二级发光管不发光,内部光感电敏接收到低电平;这样晶体管不断的接通关断,伺服驱动器不断得到高电平,低电平,即脉冲送入了伺服驱动器。伺服驱动器提供了电子齿轮功能,方便操作伺服驱动器。它是对来自上位装置输入命令的1个脉冲对应于试件所旋转的移动量进行任意设定的功能;当指令脉冲当量与位置反馈脉冲当量二者不一致时,就需要使用电子齿轮使二者匹配;电子齿轮的作用相当于增加上位机发出脉冲的频率;指令单位是指使负载移动位置数据的最小单位。电机采用的是20位编码器,每转计数1,048,576个脉冲,即反馈脉冲当量为0.00034;PLC脉冲频率最大为100KHz,试验中电机最大转速300r/min,于是最小的脉冲当量为0.018度,即PLC发出一个脉冲,电机转过0.018度。PLC是计算机技术与传统继电接触器控制技术相结合的产物,它的硬件结构主要有中央处理单元﹑存储器﹑输入输出部件﹑通信接口电源和编码器组成。PLC内部各组成单元之间通过电源总线、控制总线、地址总线及数据总线连接,外部则可根据工程需求扩展相应外部设备与执行装置,构成PLC控制系统。装置采用S7-200小型PLC来执行硬件电路和执行机构的动作。试验设备正常通电后,PLC进行首次扫描初始化,等待来自计算机的操作信号,在接收到计算机的参数信息后,控制伺服驱动器,从而控制整个动力系统。本实用新型根据扭转疲劳试验法的具体要求,公开了一种试验装置的机械结构设计方案,论述了试验装置工作原理,对于装置设计难点夹持方式的分析上,分别运用赫兹公式和ANSYS应力分析软件验证了运用弹簧夹头夹持,试件夹持部分的接触应力符合试验要求。由于本试验高频长周期的特点最后对重要的零件滚动轴承及平键进行了校核运算;通过分析验证发现本实用新型提出的结构设计方案安全可靠,为试验装置试制奠定了基础。本实用新型结合扭转疲劳试验高频长周期的特点,采用新型的直驱传动方式,减少中间的机械传动装置,提高了试验系统的灵活性和响应速度,避免了传动环节的机械磨损,提升了试验装置长周期工作的安全性和稳定性,消除了中间环节的机械间隙,满足试验高精度的要求。采用位置控制的伺服控制模式,以转角为被控量,确保了电机位置的准确性。实施例3作为本实用新型的具体实施例,本文提出用钢丝的扭转疲劳试验代替弹簧的拉压疲劳试验,具体试验要求如下,参照GB/T16947-2009《螺旋弹簧疲劳试验规范》。如图9所示,其操作流程为:第一步:开启电源;第二步:启动PLC控制系统;第三步:选择弹簧钢丝试件;第四步:在试验装置上固定试件;第五步:进行测试,通过打滑测试的转入第六步,没有通过打滑测试的转入第四步重新固定试件;第六步:对选定后的试验模式输入参数;第七步:开始试验,启动试验程序,对试件加载作用力,使得试件在加载作用力下做往复的扭转运动;第八步:判断对试件加载作用力下的扭转次数是否持续达到T次,若是,则进入第十一步;若否,则进入第九步;第九步:判断试件是否断裂,若否,则进入第十一步;若是,则进入第十步;第十步:判断试件断裂位置是否在有效位置,若是,则进入第十一步;若否,则判定试验无效,相同试件条件下转入第四步重新测试;第十一步:记录实验数据并存储。其中:1)试件a.试件尺寸:为了正确反映试样的疲劳强度,应在尽量减小尺寸误差的基础上,提高尺寸的测量精度。ⅰ)试件尺寸的测定应具有0.5%以上的精度。ⅱ)测定钢丝截面直径时,应测定同一截面内互相垂直的两个直径,取其平均值作为试件直径。b.试件的形状:为了保证钢丝在加载后不产生附加载荷,必须严格检查钢丝的平行度。c.加工和热处理:加工和热处理状态是影响试件疲劳强度的重要因素,因此同一批试件必须同时加工和热处理,表面状态应一致,不得有锈蚀﹑刻痕﹑划伤等缺陷,以免引起试件表面应力集中。2)试件安装为了防止钢丝在试验过程收缩,静止端前后必须都夹上定位块,保持钢丝拉直。3)加载在试验开始时,必须首先进行打滑测试,确保在设定夹持力下试件不打滑。在试验过程中,必须保证施加载荷的稳定,不能出现过载,应力以MPa为单位。4)疲劳寿命一般把钢丝疲劳断裂时的作用次数取为疲劳寿命。当作用次数达到T次时钢丝仍不破坏,停止试验;所述的T次为任意预设值,一般根据经验进行判断,在本实用新型中,所述的T为3×108次。5)试验装置的运转试验装置启动平稳,不能有冲击。试验开始到停止应该连续工作,若因为故障或其他原因停止工作时,必须在试验报告中有记载。作为本实用新型的一些实施例,在试验开始前需要对试验模式进行选择,试验装置控制器具备基于弹簧产品的疲劳试验与基于弹簧材料的疲劳试验两种模式,用户可以根据试验目的,是为了验证弹簧产品疲劳强度还是确定弹簧材料疲劳寿命参数来选择相应的模式;此外,主界面上还有电机参数设置选项,可以根据用户的要求调整电机的转速,加速度等参数;所有的试验数据都存储在数据库中,用户可以点击数据库操作查看﹑更改以往的试验数据。选择基于弹簧产品的疲劳试验后进入设定试验参数界面,设定试验编号及日期,便于以后查找试验数据。用户输入弹簧产品的基本参数及工作参数,点击参数计算后,计算机可以给出将弹簧实际工况等效转换为钢丝扭转疲劳试验的相应参数。点击数据保存选项,可以存储此次计算结果,下次试验时可以提取此次结果。也可直接点击进入试验选项。点击进入实验选项后,进入试验界面,点击试验开始后,进入试验,扭矩值窗口时时显示扭矩传感器采集的扭矩值,扭转次数窗口显示当前完成的试验次数。试验完成后,点击数据存储,计算机保存了此次试验的扭转次数及相关试验参数,便于数据处理时查询。在试验装置主界面中,若点击数据库操作选项,进入数据查看窗口,数据以试验模式进行分类,可以根据试验编号或试验日期进行查询,同时提供数据修改及删除功能。在试验装置主界面中,若点击基于弹簧材料的疲劳试验选项,进入材料疲劳试验参数转换窗口,用户可以输入钢丝的直径,最大切应力,循环特性及标定长度等参数,得到在扭转疲劳试验中对应的转角值及转角幅。此外,试验装置在开始试验时必须进行打滑测试。进行疲劳强度试验的前提是保证试件不打滑。若试件打滑,试件的受力状态不能满足试验要求,最终获得的试验结果是不准确的。而试验过程中夹紧力可能有所衰减或其他未定因素对夹持有影响,因此不能够仅依靠理论计算评定试验过程中不存在打滑现象。所以,在每次试验开始时必须进行打滑测试。打滑测试具体过程如下:根据计算的理论夹紧力设定液压泵站工作压强,夹持住试件后泵站保压。根据试验参数计算每次试验理论最大扭矩值。在测试界面,输入采样时间,一般选择20~40s为宜,点击开始进入打滑测试。当达到设定的采样时间后,测试结束。点击结果显示,计算机根据每次采集到的最大扭矩值计算出实际最大扭矩的平均值若其满足即JB/T9370-1999《扭转试验机技术条件》规定的相对误差要求,认为钢丝没有打滑,可以在该夹紧力的作用下进行试验,打滑测试过程流程如图8所示。在本实用新型的实施例中,所述的扭转疲劳试验中,试件标定长度,保证试件不打滑的夹持力,利用正交试验法进行分析。基本试验条件:钢丝直径d=3.8,循环特性r=0.3,最大切应力1200MPa;理论径向夹紧力:试验结果有效性判定标准:将试件分为三个部分:夹持部位,过渡区,中间区,具体分布如图7所示(单位:mm),断裂部位在中间区认为试验结果有效,否则视为无效,相同试验条件下重新测试。1)试验指标:钢丝的扭转疲劳寿命次数y2)选择合理的正交表:影响试验的主要因素和水平如下表所示:影响试验的因素及相应因素的水平3)制定试验方案:根据选定的正交表,至少需完成9次实验。实验具体方案见下表:具体试验方案及试验编号由基本条件:r=0.3,τ=1200MPa再根据最大转角公式,计算出各试验的不同试验条件,如下表所示:试验条件及试验记录备注:断裂在夹持部位和过渡区视为无效试验,必须在相同试验条件下重新测试。上述试验次数是有效试验下的结果。4)结果分析:在d=3.8,循环特性r=0.3,最大切应力1200MPa条件下,分别利用极差分析法和方差分析法分析标定长度,夹持力,频率三个因素在三种不同水平下对指标疲劳寿命次数y的影响。(极差分析法:极差指的是各列中各水平对应的试验指标平均值的最大值与最小值之差。分析结论:在试验范围内,2列的极差最大,表示该列的数值在试验范围内变化时,使试验指标数值的变化最大。三个因素对试验指标的影响从大到小的排列是夹持力,标定长度,试验频率。试验指标最好的适宜的操作条件是l3F1f1,即夹持力为42.5KN,标定长度为114mm,试验频率为20Hz。(方差分析法方差分析是把实验数据总的波动(即数据的总的偏差平方和S总)分解成两部分:一部分反映因素水平变化引起的波动(即因素的偏差平方和),另一部分反映实验误差引起的波动(即误差的偏差平方和Se)。构造F统计量,进行F检验,以判断各个试验因素的作用是否显著。由方差分析结果引出的结论:最佳试验条件是选择标定长度为114mm(30d),夹紧力为43.5KN(理论值),频率可根据实际试验要求选择在20~25Hz之间。在钢丝扭转疲劳试验中,标定长度为30d,夹紧力在保证试件不打滑的条件下选择接近理论计算值为最佳试验条件。③在试验过程中,出现了试件在过渡区和夹持区断裂的情况,具体统计情况如下表所示:试件断裂部位记录表根据断裂部位的记录表发现,在夹紧力大且标定长度短的情况下,试件容易在过渡区断裂,以编号3试验为例,试件甚至出现了直接在夹持区直接断裂的情况。这说明在夹持区与过渡区之间存在附加应力,在满足试件不打滑的要求下减小夹紧力,增加标定长度,可以减小附加应力对最终试验结果的影响。本实用新型针对传统弹簧产品疲劳寿命试验方法的弊端,提出了基于钢丝的扭转疲劳寿命测试方法,该试验方法的钢丝试件与制成弹簧的钢丝同尺寸,可以满足基于疲劳试验中尺寸效应的要求;其快速高效的特点又完全满足基于弹簧材料的疲劳试验要求。它具备以下几个特点:①施加的扭矩不受弹簧结构限制,最大切应力可以接近材料的抗扭强度;②试验装置采用直驱传动方式,扭转角的大小不受限制,转角幅值范围广,循环特性系数可以在-1到1之间,可以实现脉动疲劳试验和对称循环应力下的疲劳试验;③试验装置利用直驱电机直接驱动主轴旋转,提高了试验装置系统的灵活性和响应速度,避免了传动环节的机械磨损,保证试验装置长周期工作下的安全性和可靠性,消除中间环节的机械间隙,可以满足试验高精度的要求;④试验装置还可以测试材料的抗扭强度;⑤钢丝试件制作费用低廉,可在控制试验成本的条件下进行多次重复试验。同时,本实用新型提出对于不同规格试件选用匹配的弹簧夹头进行夹持,夹持直径与试件直径之差不大于0.1mm,有效地增大了试件与夹具之间的接触面积,将接触应力控制在许用接触应力范围内。同时,考虑到试验过程中夹持力的损耗及其他因素的影响,增加了打滑测试过程,确保了试验过程中试件处于夹紧状态。以上所述仅为本实用新型的较佳实施例而已,并不用以限制本实用新型,凡在本实用新型的精神和原则之内,所作的任何修改、等同替换、改进等,均应包含在本实用新型的保护范围之内。当前第1页1 2 3