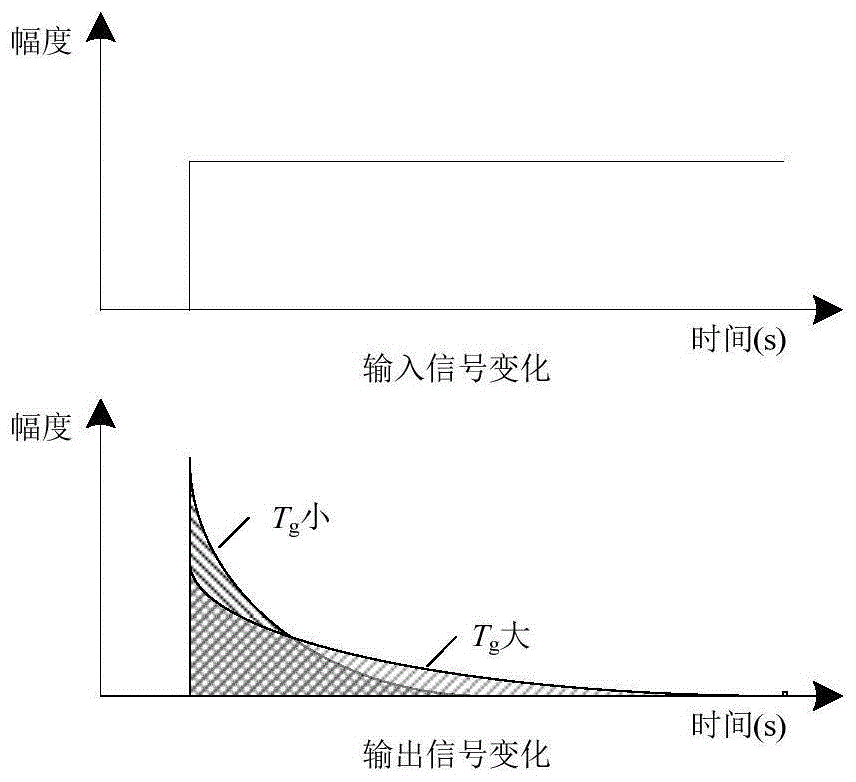
本发明涉及火力发电机组协调控制系统燃料量控制
技术领域:
,尤其涉及一种顾及磨煤机运行状态的协调控制系统燃料量前馈控制方法。
背景技术:
:本部分的陈述仅仅是提供了与本发明相关的
背景技术:
信息,不必然构成在先技术。电网要求火电机组实际发电负荷快速跟随电网agc(自动发电控制)指令变化,因此正常工况下火电机组协调控制系统需投入以炉跟机为基础的协调控制方式,即通过汽轮机调门开度控制发电负荷,通过锅炉燃料量控制汽轮机前蒸汽压力。协调控制系统被控对象的特点是:汽轮机前蒸汽压力和发电负荷响应汽轮机调阀开度变化的过程都非常迅速,而响应锅炉燃料量变化的过程都非常迟缓。因此,采用汽轮机调阀控制其中任何一个参数都相对容易,而采用燃料量控制其中任何一个参数都比较困难。所以,炉跟机控制方式的特点是发电负荷控制品质好、汽轮机前蒸汽压力控制品质差。为了减少变负荷过程中机前压力的波动,尽量提高机前压力的控制品质,机跟炉协调控制方式都设计有agc指令对燃料量的前馈控制逻辑,构成前馈反馈复合控制系统。锅炉制粉系统的大惯性、大迟延是造成汽轮机前蒸汽压力和发电负荷响应燃料量变化非常迟缓的主要原因,典型制粉系统的传递函数gf(s)为:其中:k1为机组燃料量对发电负荷的静态增益,mw/(t/h);tf为锅炉制粉系统惯性时间,s;τ为锅炉制粉系统迟延时间,s;s为拉式变换的复变量,无单位。构造协调控制系统中agc指令对燃料量前馈控制的传递函数,需要设法对消掉制粉系统传递函数中各种产生滞后的环节,尽量加快燃料量动作。由于对消纯迟延环节的方法物理上不可实现,只能对消惯性环节,因此得到agc指令对燃料量前馈控制的传递函数gpr(s)的形式为:其中:tg为保证传递函数物理可实现的实际微分环节的惯性时间,s。中速磨制粉系统的惯性时间tf很大,同时为了保证控制效果,tg应显著小于tf。因此燃料量前馈控制呈现出明显的微分调节的特征,会显著放大agc指令的变化。例如,某机组燃料量对发电负荷的静态增益为2mw/(t/h),意味着静态工况下,agc指令变化20mw,燃料量只需要变化10t/h即可。但由于燃料量前馈控制的放大作用,agc指令变化20mw时,燃料量瞬时变化幅度可以达到30t/h,然后逐渐恢复至10t/h,并且机组响应agc指令变化的速率越快,燃料量的瞬时变化幅度也越大。所以,燃料量前馈控制提升控制品质是以增加燃料量的波动幅度为代价的。agc指令变化频繁造成燃料量大幅波动,会导致剧烈的燃烧扰动,进而引起炉膛压力、烟气氧量、过热/再热汽温、nox生成量等参数不稳定,降低机组运行安全性、经济性、清洁性。特别是随着煤炭价格上涨电厂燃煤煤质变差,燃料量大幅波动会严重降低制粉系统运行安全性。绝大部分火电机组采用中速磨正压直吹式制粉系统。磨煤机是制粉系统中的关键设备,在燃料量控制系统中燃料量指令被转换为各台磨煤机的给煤量指令,进入磨煤机的煤量跟随给煤量指令变化。原煤在磨煤机底部的磨盘与磨辊之间被碾压、研磨,然后被一次风吹起经过粗粉分离器,合格的煤粉被一次风输送到锅炉燃烧器,不合格煤粒返回至磨底部继续磨制。中速磨对原煤中的沙子、石子、木块等杂质非常敏感,在原煤磨制过程中,这些杂质会硌在磨盘和磨辊之间形成较大的空隙,导致其中的原煤不能得到有效碾压、研磨,大量杂质和煤粒在磨内反复循环,造成磨内存煤量增加,磨电流增加,制粉出力下降,形成轻微堵塞,如果控制系统继续大幅增加给煤量将迅速加重这种情形,造成磨煤机严重堵塞。一般轻微堵塞时可采取暂时减少给煤并加大一次风量进行吹扫的措施排除故障,严重堵塞时只能停磨由检修人员进入磨煤机内进行清理。与之相反,当磨煤机内存煤量过少时,大幅减少给煤量,会使磨盘上铺煤不均匀,磨盘转动时与磨辊发生局部的直接碰撞,导致磨煤机出现剧烈的振动,严重时可能导致磨辊大轴、磨盘减速齿轮断裂的故障。传统协调控制系统中的燃料量前馈控制,没有顾及磨煤机及制粉系统运行状态的变化,变负荷时总是按照固定的前馈幅度增减燃料量,当制粉系统运行状态不佳时,不但不能获得良好的控制效果,反而会导致制粉系统运行状态进一步恶化。技术实现要素:针对现有协调控制系统中agc指令对燃料量前馈控制没有考虑制粉系统运行状态,变负荷过程中易造成磨煤机堵塞或空载振动的缺点,本发明提出了一种顾及磨煤机运行状态的协调控制系统燃料量前馈控制方法,能够更好地协调变负荷过程中汽轮机前蒸汽压力控制品质与制粉系统运行安全性之间的矛盾,在保持前馈总量不变的前提优化调整前馈信号的变化幅度,最终实现制粉系统运行状态良好时大幅快速增减燃料量优先保证汽轮机前蒸汽压力控制品质、制粉系统运行状态不佳时小幅慢速增减燃料量优先保证磨煤机稳定运行的目的。在一些实施方式中,采用如下技术方案:顾及磨煤机运行状态的协调控制系统燃料量前馈控制方法,包括:对所有给煤量投入自动的磨煤机,分别选取各磨煤机电流与磨煤机给煤量比值的代表值、一次风压与各磨煤机给煤量比值的代表值以及各磨煤机给煤量的代表值;分别计算上述代表值各自对应的agc指令对燃料量前馈环节中实际微分控制作用的惯性时间,选取其中的最大值经过一阶惯性滤波后作为最终的实际微分环节的惯性时间。得到实际微分环节的惯性时间后,还包括如下过程:制粉系统惯性时间除以实际微分环节的惯性时间后减去1得到中间系数;机组实际agc指令信号除以燃料量对发电功率静态增益的数值后得到静态燃料量前馈信号;静态燃料量前馈信号减去静态燃料量前馈信号经过惯性时间设置为实际微分环节惯性时间的一阶惯性模块输出后的信号,再乘以所述中间系数,得到值加上静态燃料量前馈信号,得到agc指令对燃料量的前馈信号。与现有技术相比,本发明的有益效果是:(1)本发明所述的顾及磨煤机运行状态的协调控制系统燃料量前馈控制方法,特别适用于煤质复杂、agc指令频繁波动的火电机组,控制系统能够协调变负荷过程中汽轮机前蒸汽压力控制品质与制粉系统运行安全性之间的矛盾,最大限度地发挥设备的极限性能,保证制粉系统不发生故障的前提下获得最好的控制效果。(2)本发明所述控制逻辑只需要依据实施方案完成组态、设置好参数后即可投入使用,不需要进行现场调试,实施方便。附图说明图1为本发明实施例一中实际微分环节对阶跃输入的响应曲线;图2为本发明实施例一中磨煤机电流同磨煤机给煤量比值的代表值计算逻辑;图3为本发明实施例一中一次风压同磨煤机给煤量比值的代表值计算逻辑;图4为本发明实施例一中磨煤机给煤量的代表值计算逻辑;图5为本发明实施例一中agc指令对燃料量的前馈控制逻辑。具体实施方式应该指出,以下详细说明都是例示性的,旨在对本申请提供进一步的说明。除非另有指明,本发明使用的所有技术和科学术语具有与本申请所属
技术领域:
的普通技术人员通常理解的相同含义。需要注意的是,这里所使用的术语仅是为了描述具体实施方式,而非意图限制根据本申请的示例性实施方式。如在这里所使用的,除非上下文另外明确指出,否则单数形式也意图包括复数形式,此外,还应当理解的是,当在本说明书中使用术语“包含”和/或“包括”时,其指明存在特征、步骤、操作、组件和/或它们的组合。实施例一在一个或多个实施例中,公开了一种顾及磨煤机运行状态的协调控制系统燃料量前馈控制方法,在dcs(分散控制系统)中以逻辑组态的形式实现,包括以下过程:对所有给煤量投入自动的磨煤机,分别选取各磨煤机电流与磨煤机给煤量比值的代表值、一次风压与各磨煤机给煤量比值的代表值以及各磨煤机给煤量的代表值;分别计算上述代表值各自对应的agc指令对燃料量前馈环节中实际微分控制作用的惯性时间,选取其中的最大值经过一阶惯性滤波后作为最终的实际微分环节的惯性时间。该方法依据机组运行过程中各磨煤机电流与磨煤机给煤量的比值、一次风压与各磨煤机给煤量的比值、各磨煤机的给煤量三个信号的变化情况,在线调整agc指令对燃料量前馈环节中实际微分控制作用惯性时间,在保持前馈总量不变的前提优化调整前馈信号的变化幅度,最终实现制粉系统运行状态良好时大幅快速增减燃料量优先保证汽轮机前蒸汽压力控制品质、制粉系统运行状态不佳时小幅慢速增减燃料量优先保证磨煤机稳定运行的目的。控制方法具有物理意义明确、现场实施简便的优点。下面对本实施例方法进行详细的说明:(1)实际微分环节特性分析理想微分环节物理上不可实现,实际微分环节传递函数gd(s)结构为:其中:td为微分时间,s。微分时间td决定了微分总量的大小,而实际微分环节的惯性时间tg则影响着微分响应的幅度和变化时间。图1显示了实际微分环节的惯性时间tg不同时实际微分环节对阶跃输入的响应曲线。tg越大,响应曲线幅值变化的幅度越小,响应曲线持续的时间越长,但响应曲线的总面积保持不变。理论上,可以通过调整实际微分环节的惯性时间,在微分总量保持不变的条件下,改变微分环节输出的最大变化幅度。对式(2)进行变形后如式(4)所示。可以发现,agc指令对燃料量前馈控制的传递函数gpr(s)实际上是由一个静态增益项和一个实际微分环节相加后构成的,因此也可通过调整实际微分环节的惯性时间来调整前馈控制的动作幅度。对式(4)进一步变形,可以得到式(5)所示的便于工程组态实现的结构。主要是将实际微分环节等效变换为惯性环节实现。(2)反映制粉系统运行状态的信号磨煤机电流与磨煤机给煤量的比值能够代表煤的可磨性。给煤量相同的情况下,磨煤机电流越大,意味着煤可磨性越差,相应磨煤机内存煤也越多,磨煤机发生堵塞的风险越高。相反,给煤量相同的情况下,磨煤机电流越小,意味着煤可磨性越好,相应磨煤机内存煤也越少,磨煤机发生空载振动的风险越高。另外,磨煤机在设计时有最高一次风压和最低一次风压的要求,一次风压与给煤量的比值越高,一次风的携带能力越强,磨煤机越容易发生空载振动;一次风压与给煤量的比值越低,一次风的携带能力越弱,磨煤机越容易发生堵塞。再者,磨煤机在设计时有最大给煤量和最小给煤量的限制。给煤量接近或超过最大设计给煤量时,磨煤机容易堵塞;给煤量接近或低于最小设计给煤量时,磨煤机容易发生空载振动。这样,当磨煤机电流与磨煤机给煤量的比值、一次风压同磨煤机给煤量的比值、磨煤机给煤量三个信号中任何一个明显超出正常范围时,都需要适当降低燃料量指令的变化幅度,防止磨煤机出现异常。(3)信号综合处理下面说明如何依据磨煤机电流与磨煤机给煤量的比值、一次风压同磨煤机给煤量的比值、磨煤机给煤量三个信号确定实际微分环节惯性时间的方法。火电机组都配置多台磨煤机并列运行。现场根据机组总燃料量指令的大小,启动不同台数的磨煤机,使每台磨煤机给煤量都在合理范围内。磨煤机工作正常时,运行人员会将与此磨煤机对应给煤机的给煤量控制投入自动控制,参与总燃料量自动调节。这样,每一个给煤量投入自动的磨煤机都可以产生磨煤机电流与磨煤机给煤量的比值、一次风压同磨煤机给煤量的比值、磨煤机给煤量三个信号。理论上,所有磨煤机中,应该是上述三个信号最极端的一个磨煤机最容易发生堵塞或空载振动,但是由于现场存在各种干扰和不确定因素,上述三个信号反映磨煤机堵塞或空载振动的准确度并不是很高,存在漏判或误判的可能。因此采用类似表决的原则进行信号综合处理,方法是:对所有给煤量投入自动的磨煤机,选择磨煤机电流与磨煤机给煤量比值中的次大值作为所有磨煤机电流与磨煤机给煤量比值的代表值,同理分别选择一次风压同磨煤机给煤量比值的次大值、磨煤机给煤量次大值作为所有一次风压同磨煤机给煤量比值和磨煤机给煤量的代表值,由三个代表值分别计算出各自对应的实际微分环节的惯性时间,再选择其中最大值作为最终的实际微分环节的惯性时间。下面以一台配置5台磨煤机的火电机组为例说明本发明技术方案。实现本发明控制方法的控制系统结构示意图如图2~5所示。其中图2为磨煤机电流同磨煤机给煤量比值的代表值计算逻辑,图3为一次风压同磨煤机给煤量比值的代表值计算逻辑,图4为磨煤机给煤量的代表值计算逻辑,图5为agc指令对燃料量的前馈控制逻辑。图2~5中:div1~div12为除法计算模块1~12,带标志“b”的输入端为被除数;t1~t15为信号选择模块,右侧开关量输入端信号为“1”时选择“y”输入端的信号作为输出,开关量输入端信号为“0”时选择“n”输入端的信号作为输出;ls1~ls30为小选模块1~30,功能是比较两个输入信号数值大小,选择数值小的信号作为输出;hs1~hs29为大选模块1~29,功能是比较两个输入信号数值大小,选择数值大的信号作为输出;f(x)1~f(x)3为多点折线函数模块1~3;lag1~lag2为一阶惯性模块1~2,其中lag2中右向箭头输入端为惯性时间数值输入端;sum1~sum3为求和计算模块1~3;mul为乘法计算模块;k1、tf、1为常数模块,分别输出常数k1、tf、1。图2中,首先分别计算a、b、c、d、e共5台磨煤机的磨煤机电流同给煤量的比值;然后判断磨煤机给煤量是否投入自动控制,投入自动则输出计算比值,没投入自动则输出0;最后从5个信号中选择次大值作为磨煤机电流同磨煤机给煤量比值的代表值。其中选择次大值的逻辑是:分别对5个输入信号两个一组进行选小,然后从所有选小的输出值中选出最大值。图3中,分别计算a、b、c、d、e共5台磨煤机的一次风压同给煤量的比值;然后判断磨煤机给煤量是否投入自动,投入自动则输出计算比值,没投入自动则输出0;最后从5个信号中选择次大值作为一次风压同磨煤机给煤量比值的代表值。其中选择次大值的逻辑是:分别对5个输入信号两个一组进行选小,然后从所有选小的输出值中选出最大值。图4中,分别判断a、b、c、d、e共5台磨煤机给煤量是否投入自动,投入自动则输出计算磨煤机给煤量,没投入自动则输出0;最后从5个信号中选择次大值作为磨煤机给煤量的代表值。其中选择次大值的逻辑是:分别对5个输入信号两个一组进行选小,然后从所有选小的输出值中选出最大值。图5中,磨煤机电流同磨煤机给煤量比值的代表值、一次风压同磨煤机给煤量比值的代表值、磨煤机给煤量的代表值分别经过多点折线函数f(x)1~f(x)3计算各自对应的实际微分环节惯性时间,然后经过hs28、hs29选择其中的最大值再经过lag1进行一阶惯性滤波后得到最终的实际微分环节惯性时间tg的数值。制粉系统惯性时间tf的数值通过div12除以实际微分环节惯性时间tg的数值,再通过sum1减去1得到一个中间系数;机组实际agc指令信号通过div11除以燃料量对发电功率静态增益的数值k1后得到静态燃料量前馈信号,静态燃料量前馈信号通过sum2减去静态燃料量前馈信号经过惯性时间设置为微分环节惯性时间tg的一阶惯性模块lag2的输出后的信号,再通过mul乘以中间系数,最后通过sum3加上静态燃料量前馈信号,得到agc指令对燃料量的前馈信号。实现本发明控制方法的控制系统结构的图2~5的逻辑中。lag1模块的惯性时间设置为10s,k1、tf常数模块的输出值分别设置为原协调控制系统中的机组燃料量对发电功率的静态增益和锅炉制粉系统惯性时间。多点折线函数模块f(x)1~f(x)3的设置方法分别见表1~3。表1多点折线函数模块f(x)1的设置序号12345输入0.0×ibe0.5×ibe0.8×ibe1.2×ibe2.0×ibe输出5040204080其中:ibe为磨煤机额定工作电流与额定给煤量的比值,a/(t/h)。表2多点折线函数模块f(x)2的设置序号12345输入0.0×pbe0.7×pbe0.9×pbe1.1×pbe1.5×pbe输出8060202050其中:pbe为额定一次风压与磨煤机额定给煤量的比值,kpa/(t/h)。表3多点折线函数模块f(x)3的设置序号12345输入0.0×rme0.5×rme0.7×rme1.0×rme1.2×rme输出5030203080其中:rme为磨煤机额定给煤量,t/h。实施例二在一个或多个实施方式中,公开了一种顾及磨煤机运行状态的协调控制系统燃料量前馈控制方法,该方法在plc(可编程控制器)中以编写代码的方式予以实现,代码实现的功能具体包括:对所有给煤量投入自动的磨煤机,分别选取各磨煤机电流与磨煤机给煤量比值的代表值、一次风压与各磨煤机给煤量比值的代表值以及各磨煤机给煤量的代表值;分别计算上述代表值各自对应的agc指令对燃料量前馈环节中实际微分控制作用的惯性时间,选取其中的最大值作为最终的实际微分环节的惯性时间;得到实际微分环节的惯性时间后,还包括如下过程:制粉系统惯性时间除以实际微分环节的惯性时间后减去1得到中间系数;机组实际agc指令信号除以燃料量对发电功率静态增益的数值后得到静态燃料量前馈信号;静态燃料量前馈信号减去静态燃料量前馈信号经过惯性时间设置为微分环节惯性时间的一阶惯性模块输出后的信号,再乘以所述中间系数,得到值加上静态燃料量前馈信号,得到agc指令对燃料量的前馈信号。上述过程的具体实现过程与实施例一中的过程相同,此处不再赘述。上述虽然结合附图对本发明的具体实施方式进行了描述,但并非对本发明保护范围的限制,所属领域技术人员应该明白,在本发明的技术方案的基础上,本领域技术人员不需要付出创造性劳动即可做出的各种修改或变形仍在本发明的保护范围以内。当前第1页12