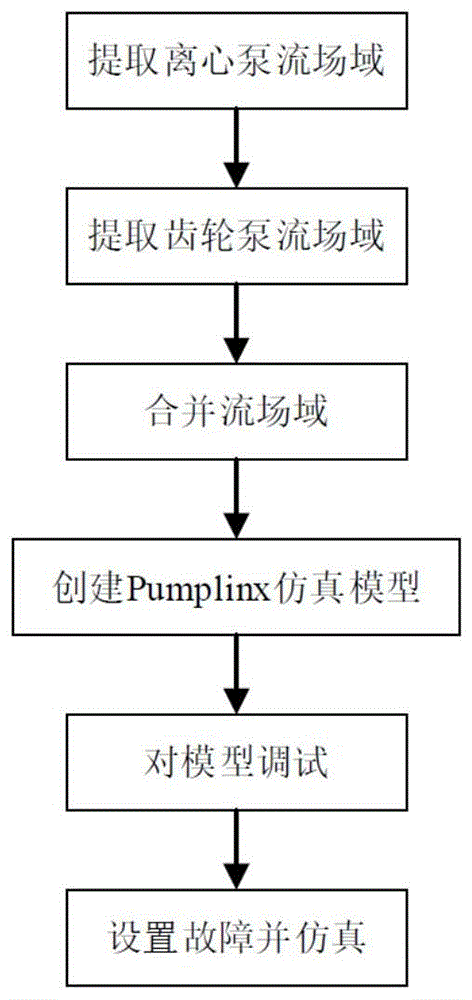
本发明涉及一种组合式航空发动机高压齿轮泵建模仿真及故障注入方法,属于航空发动机建模与仿真
技术领域:
。
背景技术:
:燃油泵是航空发动机燃油系统中的重要部件,随着对航空发动机工作性能要求的不断提高,对燃油泵的性能要求也越来越高。在研究燃油泵工作特性时,单纯地运用传统的物理实验,耗时耗力,且变更参数或条件困难,若采用功能性建模,很难体现齿数、间隙等的影响,结果往往与实际有偏差,而且一些大系统的数学建模往往需要燃油泵的仿真结果做参考数据,所以对燃油泵进行高精度建模仿真是有必要的。目前对泵的仿真都是对离心泵、齿轮泵等的单独仿真,而单独仿真无法反映泵之间的相互影响,为解决该问题并提高建模的精度,本发明提供了一种组合式航空发动机高压齿轮泵建模仿真及故障注入方法。此种方法根据离心泵和齿轮泵的结构提取出流场域,并合并形成组合流场域,根据其工作原理拆分成不同单元,在pumplinx中建立仿真模型仿真得到泵的工作特性,通过调试使仿真误差在5%以内;并建立几种常见故障下的故障模型,观察故障下泵工作特性的变化,为泵的故障分析及优化设计提供参考。技术实现要素:针对现有技术中燃油泵只有单独仿真且精度不高的问题,本发明提供了一种组合式航空发动机高压齿轮泵建模仿真及故障注入方法。本发明的技术方案:一种组合式航空发动机高压齿轮泵建模仿真及故障注入方法,包括以下步骤:s1.根据离心泵的三维模型,采用ug提取出离心泵的流场域s1.1使用ug创建一个包含离心泵流场域的圆柱实体,与离心泵求交,得到初步的流场域;s1.2对初步的流场域进行修剪,将不属于流场域的部分除去;s1.3对流场域进行优化,除去诱导轮与叶轮之间的间隙;s1.4将流场域按工作原理拆分成不同的单元,包括进口单元、诱导轮单元、叶轮单元和出口单元四个部分;首先,创建一个与诱导轮所处腔室入口齐平的平面片体,用该平面片体拆分流场域,上方为进口单元;再创建一个与叶轮所处腔室出口齐平的圆柱片体,用该圆柱片体拆分剩余流场域,将出口单元拆分出来;然后,创建一个顶点在离心泵转轴上、面处于叶轮和诱导轮之间且不与两轮轮齿相交的圆锥形片体,用该圆锥形片体拆分剩余流场域,将叶轮部分与诱导轮部分初步分开;最后,创建一个与离心泵转轴垂直且高度上比诱导轮底部高的平面片体,用该平面片体拆分诱导轮部分,得到该平面片体上方为诱导轮单元,下方与叶轮部分合并形成叶轮单元;s2.根据齿轮泵的三维模型,采用ug提取出齿轮泵的流场域s2.1使用ug创建一个包含齿轮泵流场域的圆柱实体,与齿轮泵求交,得到初步的流场域;s2.2对初步的流场域进行修剪,将不属于齿轮泵流场域的部分除去;s2.3对流场域进行优化,对齿轮泵进口管道进行切除简化,在进口处拉伸生成一个小圆柱体以便仿真设置;s2.4将流场域按工作原理拆分成不同的单元,包括进口单元、齿轮单元、卸荷槽单元、扩大高压区单元及出口单元五种部分;首先,创建一个与齿轮腔壁相重合且穿过齿轮泵流场域的片体,用该片体拆分流场域得到进口单元和出口单元;然后,创建分别与齿轮上、下表面齐平的平面片体,用这两个片体拆分剩余流场域得到齿轮单元;最后,创建与卸荷槽外壁面重合的片体,用该片体拆分剩余流场域得到四个卸荷槽单元和八个扩大高压区单元;s3.将离心泵和齿轮泵的流场域合并形成组合流场域s3.1在模型中提取出离心泵下部连接管道的流场域;s3.2将离心泵流场域、齿轮泵流场域及连接管道的流场域导入一个模型文件中,将齿轮泵流场域旋转、平移至齿轮泵进口与连接管道出口平行,且连接管道出口圆心在齿轮泵进口处小圆柱体中心线上;s3.3在齿轮泵进口与连接管道出口间创建圆台,用于将齿轮泵流场域和连接管道流场域连接起来;s3.4将齿轮泵进口单元、连接管道流场域与离心泵出口单元合并为组合流场域模型;s4.将组合流场域模型导入pumplinx中,进行仿真模型的创建s4.1在pumplinx中导入组合泵流场域模型,建立四个监视点,分别为齿轮泵主动齿轮旋转中心、从动齿轮旋转中心、组合泵进口、组合泵出口;s4.2将组合流场域模型的x、y、z三个方向缩放至监视点位置与实际位置重合,统一单位;s4.3对组合流场域进行“splitdisconnected”操作,按s1.4和s2.4所述方式分成不同单元,对每个单元依次创建surface;s4.4对各单元进行网格划分,齿轮单元的网格划分采用样板转子网格划分功能,其余单元的网格划分采用普通网格划分功能;s4.5对相连的单元设置交界面,包括进口单元与诱导轮单元、诱导轮单元与叶轮单元、叶轮单元与离心泵-齿轮泵的连接单元、齿轮单元与离心泵-齿轮泵的连接单元、齿轮单元与出口单元、齿轮单元与卸荷槽单元、齿轮单元与扩大高压区单元、出口侧的卸荷槽单元与扩大高压区单元;s4.6添加模块,包括“axialflow”、“centrifugal”、“gear”三种转子模块及“turbulence”、“cavitation”、“heat”、“streamline”和“particle”模块,并设置各模块参数;s4.7设置边界条件;s4.8设定介质常数;s5.对仿真模型进行调试,针对不同的工况分别调整齿轮侧向间隙,直至仿真结果与实验数据误差在5%以内;s6.对额定工况下的仿真模型进行故障注入s6.1选择额定工况下仿真模型进行故障注入,对离心泵出口燃油无增压、离心泵出口燃油增压降低、齿轮泵供油流量降低三种故障模式选择模型故障参数设置方式;s6.2对于离心泵出口燃油无增压故障,在pumplinx中设置叶轮和诱导轮转速为0进行仿真;s6.3对于离心泵出口燃油增压降低故障,在ug中分别对诱导轮和叶轮对应流场域处加厚,实现间隙的增大;s6.4对于齿轮泵供油流量降低故障,在ug中将齿轮的齿削薄来实现径向间隙增大;在pumplinx中划分齿轮单元网格时,增大端面间隙即“sideleakagegap”的数值;s7.对各故障下仿真模型分别仿真,得出各故障下泵特性的变化。本发明的有益效果:通过本发明所提供方法对航空发动机燃油泵进行建模仿真及故障注入,相比于以往的方法,体现出了离心泵与齿轮泵之间的相互影响,并提高了仿真精度。燃油泵仿真数据可用于航空发动机燃油与作动系统的数学建模,因此该方法可直接提高航空发动机燃油与作动系统数学建模的精度和可靠性。同时,本方法经过适当的调整可用于其它型号燃油泵的建模与仿真,具有一定的普适性。附图说明图1为组合式航空发动机高压齿轮泵建模仿真及故障注入方法流程图;图2为提取泵流场域的流程图;图3为合并流场域的流程图;图4为组合流场域模型图;图5为创建pumplinx仿真模型的流程图;图6为叶轮和诱导轮转速为0的故障下的仿真出口流量-时间关系图。图7为径向间隙增大为0.45mm的故障下的仿真出口流量-时间关系图。图8为端面间隙增大为0.1mm的故障下的仿真出口流量-时间关系图。具体实施方式下面结合附图对本发明作进一步说明,本发明依托背景为某型航空发动机燃油泵三维模型及实验数据,组合式航空发动机高压齿轮泵建模仿真及故障注入方法流程如图1所示。图2为提取泵流场域的流程图,提取离心泵的流场域步骤如下:s1.使用ug,首先创建一个包含离心泵流场域的圆柱实体,与离心泵求交,得到初步的流场域;s2.对初步的流场域进行修剪,创建一个与转轴相同直径的圆柱实体,并用其与流场域求差,将中间转轴部分除去。创建一个与叶轮下方壳体相同直径的圆柱实体,与流场域求差使叶轮下面的间隙值为0.15mm;其余不属于流场域的部分都通过“拉伸”、“修剪体”、“求差”等命令一步步去除。s3.对流场域进行优化,除去诱导轮与叶轮之间的间隙,创建一个与诱导轮底部内径相同的圆柱片体,对流场域拆分并删除拆分下来的间隙,将剩余被拆分下来的部分合并到流场域中;s4.将离心泵流场域按其工作原理分成不同的单元,包括进口单元、诱导轮单元、叶轮单元、出口单元四个部分。首先创建一个与诱导轮所处腔室入口齐平的平面片体,用该片体拆分流场域,上方为进口单元;创建一个与叶轮所处腔室出口齐平的圆柱片体,用该片体拆分剩余流场域,将出口单元拆分出来;创建一个顶点在离心泵转轴上,面处于叶轮和诱导轮之间且不与两轮轮齿相交的圆锥形片体,用该片体拆分剩余流场域,将叶轮部分与诱导轮部分初步分开,再创建一个与离心泵转轴垂直且高度上比诱导轮底部略高的平面片体,用该片体拆分诱导轮部分,得到该片体上方为诱导轮单元,下方与叶轮部分合并形成叶轮单元。提取齿轮泵的流场域步骤如下:s1.使用ug,首先创建一个包含齿轮泵流场域的圆柱实体,与齿轮泵求交,得到初步的流场域;s2.对初步的流场域进行修剪,将不属于齿轮泵流场域的部分除去;s3.对流场域进行优化,对齿轮泵进口管道进行切除简化,在进口处拉伸生成一个小圆柱体以便仿真设置;s4.将流场域按工作原理分成不同的单元,包括进口、齿轮、卸荷槽、扩大高压区及出口五种单元。首先创建一个与齿轮腔壁相重合穿过齿轮泵流场域的片体,用该片体拆分流场域得到进口单元和出口单元;创建分别与齿轮上、下表面齐平的平面片体,用这两个片体拆分剩余流场域得到齿轮单元;创建与卸荷槽外壁面重合的片体,用该片体拆分剩余流场域得到四个卸荷槽单元和八个扩大高压区单元。图3为合并流场域的流程图,合并流场域的步骤如下:s1.在模型中提取出离心泵下部连接管道的流场域;s2.将离心泵流场域、齿轮泵流场域及连接管道的流场域导入一个模型文件中,将齿轮泵流场域旋转、平移至齿轮泵进口与连接管道出口平行,且连接管道出口圆心在齿轮泵进口处小圆柱体中心线上;s3.在齿轮泵进口与连接管道出口间创建圆台,将齿轮泵流场域和连接管道流场域连接起来;s4.将齿轮泵进口单元、连接管道流场域与离心泵出口单元合并。图4为最终形成的组合流场域模型图。图5为创建pumplinx仿真模型的流程图,pumplinx仿真模型的创建步骤如下:s1.在pumplinx中导入组合泵流场域模型,建立四个监视点,分别为齿轮泵主动齿轮旋转中心、从动齿轮旋转中心、进口、出口;s2.将模型x、y、z三个方向都按0.001的比例因子缩放,监视点位置与实际位置重合,则单位统一完毕;s3.对流场域进行“splitdisconnected”操作,按不同单元分开,将每个单元依次创建surface。对进口单元创建“inlet_inlet”、“inlet_mgi_youdao”、“inlet_walls”三个surface;对诱导轮单元创建“youdao_mgi_inlet”、“youdao_mgi_yelun”、“youdao”、“youdao_walls”四个surface;对叶轮单元创建“yelun_mgi_youdao”、“yelun_mgi_connect”、“yelun”、“yelun_bot”、“yelunwalls”五个surface;对离心泵-齿轮泵的连接单元创建“connect_mgi_yelun”、“connect_mgi_drive”、“connect_mgi_slave”、“connect_walls”四个surface;对齿轮单元创建“gear_drive_shroud”、“gear_slave_shroud”、“gears_outertop”、“gears_outer_bottom”、“gears_drive”、“gears_slave”六个surface;对齿轮泵进口处上部的卸荷槽单元创建“relieftopinlet_mgigears”、“relieftopinlet_walls”两个surface,齿轮泵进口处下部的卸荷槽单元与之相同;对齿轮泵出口处上部的卸荷槽单元创建“relieftopoutlet_mgigears”、“relieftopoutlet_mgi_expand1”、“relieftopoutlet_mgi_expand2”、“relieftopoutlet_walls”四个surface,齿轮泵出口处下部的卸荷槽单元与之相同;对四个扩大高压区单元,分别创建“expand_bottom_drive_mgi_gears”、“expand_bottom_drive_mgi_relief”、“expand_bottom_drive_walls”三个surface;对出口单元创建“outlet_mgidrive”、“outlet_mgislave”、“outlet_outlet”、“outlet_walls”四个surface。s4.进行网格划分,对于齿轮单元,采用样板转子网格划分功能,转子类型选择“externalgear”,设置方式选为“advancedmode”,油膜内径与外径分别为为27.05mm和41.7mm;对于涡室部分,划分网格时最大单元格尺寸设为0.01,表面上的单元格尺寸设为0.005;对于其他单元,划分网格时最大单元格尺寸设为0.02,表面上的单元格尺寸设为0.01,对划分网格过程中出现的一些碎小的烂面,用split/combinegeometryorgrid中的“combine”功能整合到相邻的面网格上;s5.对相连的单元设置交界面,包括进口单元与诱导轮单元、诱导轮单元与叶轮单元、叶轮单元与离心泵-齿轮泵的连接单元、齿轮单元与离心泵-齿轮泵的连接单元及出口单元、齿轮单元与卸荷槽及扩大高压区、出口侧的卸荷槽与扩大高压区共11处;s6.添加模块,包括“axialflow”、“centrifugal”、“gear”三种转子模块及“turbulence”、“cavitation”、“heat”、“streamline”和“particle”模块。设置轴流式对应诱导轮,叶片数为5,旋转中心坐标为[000],逆时针旋转,旋转轴矢量为[001]。离心式对应叶轮,叶片数为18,旋转中心坐标为[000],逆时针旋转,旋转轴矢量为[001]。主动、从动齿轮齿数为16,逆时针旋转,旋转轴矢量为[001]。选择齿轮泵做参考泵,旋转圈数设为10,每个驱动齿轮轮齿的时间步长设为30;s7.设置边界条件,将边界面“youdao”设置为轴流转子,axialflow对应选项改为“rotor”;将边界面“yelun”设置为离心转子,centrifugal对应选项改为“rotor”;对边界面“inlet_inlet”设置进口压力,axialflow对应选项改为“inlet”,并输入进口压力数值;对边界面“outlet_outlet”设置出口压力,gear对应选项改为“outlet”,并输入出口压力数值;s8.设定介质常数,介质常数如表1所示。表1介质常数数值表对如表2所示的八种工况进行仿真,通过调节齿轮侧向间隙对仿真模型进行调试,得到仿真结果与实验数据对比如表3,误差均在5%以内。表2八种工况的边界条件表3出口流量仿真结果与实验数据对比工况实验数据(kg/s)仿真结果(kg/s)误差13.17783.252.27%23.09223.234.46%31.50831.481.88%41.44171.384.27%52.032.071.97%61.91611.8254.75%72.54172.5250.66%82.37142.3750.15%图6-8为各故障下模型仿真结果,故障注入的步骤如下:s1.选择额定工况下仿真模型进行故障注入,对离心泵出口燃油无增压、离心泵出口燃油增压降低、齿轮泵供油流量降低三种故障模式选择模型故障参数设置方式,如表4所示;表4故障模式及对应模型故障参数设置方式s2.对于离心泵出口燃油无增压故障,在pumplinx中设置叶轮和诱导轮转速为0,仿真得到燃油泵出口流量为1.8kg/s,如图6所示;s3.对于离心泵出口燃油增压降低故障,在ug中分别对诱导轮和叶轮对应流场域处加厚,实现间隙的增大。仿真得到诱导轮与壳体的间隙增加1.5mm时,离心泵出口压力为0.75mpa,当叶轮与壳体的间隙增加1mm时,离心泵出口压力为1.0mpa;s4.对于齿轮泵供油流量降低故障,在ug中将齿轮的齿削薄来实现径向间隙增大,当间隙为0.45mm时,仿真得燃油泵出口流量为2.7925kg/s,如图7所示。在pumplinx中划分齿轮单元网格时,增大“sideleakagegap”的数值,当间隙为0.1mm时,燃油泵出口流量为2.774kg/s,如图8所示。当前第1页12