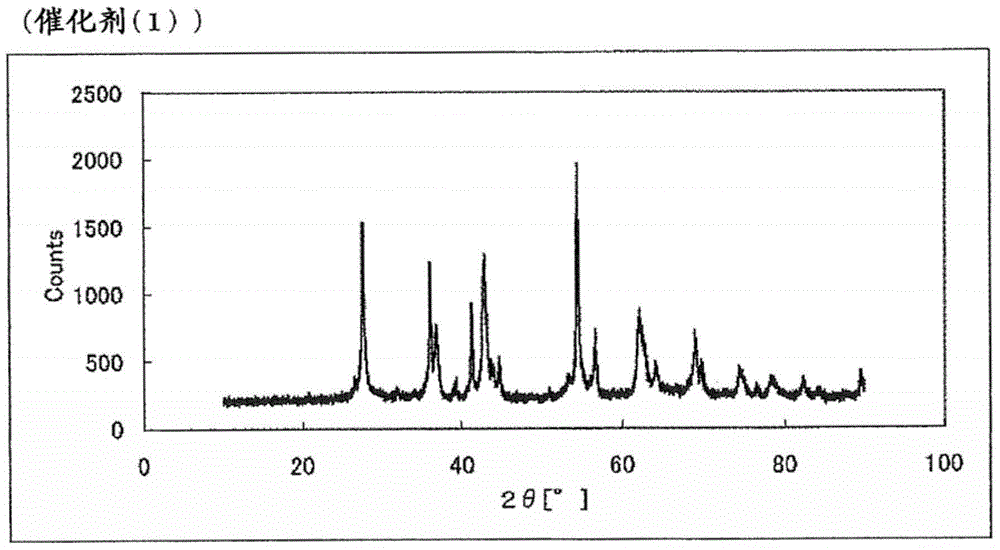
本发明涉及燃料电池用电极催化剂的制造方法、和燃料电池用电极等的制造方法,更具体地是涉及能够作为铂等贵金属的替代催化剂使用的燃料电池用催化剂、和燃料电池用电极等的制造方法。
背景技术:高分子固体型燃料电池是以下形式的燃料电池:使高分子固体电解质被阳极和阴极夹持,向阳极供给燃料,向阴极供给氧气或空气,在阴极将氧还原,取出电。燃料主要使用氢气或甲醇等。以往为了提高燃料电池的反应速度、提高燃料电池的能量转换效率,在燃料电池的阴极(空气极)表面或阳极(燃料极)表面设置含有催化剂的层(下面也记作“燃料电池用催化剂层”。)。作为该催化剂,通常使用贵金属,在贵金属中主要使用在高电位下稳定、活性高的铂、钯等贵金属。但这些贵金属价格昂贵、而且资源量有限,所以需要开发能够代替它们的催化剂。此外,在阴极表面使用的贵金属在酸性气氛下有时会溶解,因此存在以下问题:不适合需要长期耐久性的用途。因此,强烈要求开发在酸性气氛下不腐蚀、耐久性优异、具有高氧还原性能的催化剂。作为代替贵金属的催化剂,已经报告了完全不使用贵金属的贱金属碳化物、贱金属氧化物、贱金属碳氮氧化物、硫属元素化合物和碳催化剂等(参照例如专利文献1~专利文献4)。这些材料,与铂等贵金属材料相比,价格便宜,资源量丰富。但是,专利文献1和专利文献2中记载的含有贱金属材料的这些催化剂,存在实用上得不到充分的氧还原性能的问题。此外,专利文献3和专利文献4中记载的催化剂,尽管显示出高的氧还原催化活性,但具有在燃料电池运转条件下稳定性不充分的问题。作为这种贵金属替代催化剂,专利文献5和专利文献6中的Nb和Ti碳氮氧化物能够有效表现出上述性能,所以特别受到关注。专利文献5和专利文献6中记载的催化剂,与以往的贵金属替代催化剂相比,是极其高的性能,但在其制造工序的一部分中需要在1600℃~1800℃的高温下进行加热处理(例如专利文献5的实施例1、或专利文献6的实施例1)。这种高温加热处理,虽然在工业上不是不可能,但会有困难,随之导致设备费的高涨和运转管理的困难,进而制造成本变高,所以期望开发出能够以更便宜的价格进行制造的方法。专利文献7中报告了涉及含有碳、氮和氧的含碳的钛氧氮化物的制造的技术。但是,专利文献7所记载的制造方法,为了制造含碳的钛氧氮化物,需要通过含氮有机化合物和钛前体的反应来制造钛氧氮化物、以及通过酚树脂和钛氧氮化物前体的反应来制造含碳的钛氧氮化物这两阶段的合成,工序复杂。特别是,钛氧氮化物前体制造时需要80℃下的搅拌、过热、和回流、以及冷却和减压浓缩等复杂工序,所以制造成本高。此外,由于酚树脂是具有3维网状结构的热固化性树脂,所以难以与金属氧化物均匀混合、反应。特别是,由于酚树脂的热分解温度是400℃~900℃,所以存在在1000℃以下的温度下难以通过酚树脂的完全分解引起碳化反应的问题。进而,在专利文献7和非专利文献1中,作为其用途,仅记载了作为太阳光集热器用的薄膜和光催化剂使用,关于具有对电极催化剂很有用的粒状或纤维状等形状的金属碳氮氧化物的制造方法以及其用途却没有公开和研究。专利文献8公开了特征在于将氧化物和碳材料前体的混合材料料进行烧成的、电极催化剂的制造方法,但得不到具有充分的催化剂性能的电极催化剂。此外,专利文献9中公开了使用钴等多核配合物而成的燃料电池用电极催化剂,但存在高成本,不具有充分的催化活性的问题。在非专利文献2中公开了特征在于将钛的醇盐和碳材料前体的混合材料料进行烧成的、电极催化剂的制造方法,但在制造工序中没有使用含氮的有机物,没有得到具有充分的催化剂性能的电极催化剂。专利文献10中公开了,将氢氧化锆等金属化合物和碳材料前体在所述碳材料前体能够转化成碳材料的条件(例如400~1100℃)下进行烧成的电极催化剂的制造方法,但得不到具有充分催化性能的电极催化剂。需说明的是,专利文献11中公开了一种燃料电池用电极催化剂的制造方法,其含有以下工序:至少将含有过渡金属(元素周期表第IVB族和第VB族元素等)的化合物、含氮有机化合物和溶剂混合在一起,得到催化剂前体溶液的工序1,从所述催化剂前体溶液除去溶剂的工序2,以及将工序2中得到的固体成分残渣在较低温度下进行热处理,得到电极催化剂的工序3,但下文中说明那样的、包含通过使过渡金属化合物(1)的水溶液与氨和/或氨水接触来生成含有所述过渡金属的原子的沉淀物的工序的燃料电池用电极催化剂的制造方法尚未公开。现有技术文献专利文献专利文献1:日本特开2004-303664号公报专利文献2:国际公开第07/072665号小册子专利文献3:美国专利申请公开第2004/0096728号说明书专利文献4:日本特开2005-19332号公报专利文献5:国际公开第2009/031383号小册子专利文献6:国际公开第2009/107518号小册子专利文献7:日本特开2009-23887号公报专利文献8:日本特开2009-255053号公报专利文献9:日本特开2008-258150号公报专利文献10:国际公开第2009/116369号小册子专利文献11:国际公开第2011/99493号小册子非专利文献非专利文献1:JournalofInorganicMaterials(汉语)20,4,第785页非专利文献2:ElectrochemistryCommunicationsVolume12,Issue9,2010年9月,第1177-1179页
技术实现要素:发明要解决的课题本发明的目的在于,提供一种经较低温度下的热处理、使用过渡金属(钛等)来制造具有高催化活性的燃料电池用电极催化剂的方法。解决课题的手段本发明涉及例如以下的【1】~【10】。【1】.一种燃料电池用电极催化剂的制造方法,其特征在于,包含以下工序:工序(I):使过渡金属化合物(1)的水溶液与氨和/或氨水接触,而生成含有所述过渡金属的原子的沉淀物(A);工序(II):使至少所述沉淀物(A)、有机化合物(B)和液体介质(C)混合,而得到催化剂前体;工序(IV):将所述催化剂前体在500~1200℃的温度下进行热处理,得到电极催化剂,所述过渡金属化合物(1)的一部分或全部,是作为过渡金属元素含有选自元素周期表第IVB族和第VB族元素中的至少1种过渡金属元素M1的化合物,所述有机化合物(B)是选自糖、氨基糖、糖胺聚糖、聚乙烯醇、聚烷撑二醇、聚酯、含氮高分子化合物、含氰基化合物、氨基酸和有机酸中的至少1种。【2】.如【1】所述的燃料电池用电极催化剂的制造方法,其特征在于,包含以下工序(III):在上述工序(IV)之前、从所述催化剂前体中除去所述液体介质(C)。【3】.如【1】或【2】所述的燃料电池用电极催化剂的制造方法,其特征在于,所述过渡金属元素M1是选自钛、锆、铌和钽中的至少1种。【4】.如【1】~【3】的任一项所述的燃料电池用电极催化剂的制造方法,其特征在于,过渡金属化合物(1)是选自金属卤化物、金属硫酸盐、金属醇盐、金属乙酸盐、金属磷酸盐、金属硝酸盐、金属有机酸盐、金属卤氧化物、金属高卤酸盐和金属次卤酸盐、金属配合物中的至少1种。【5】.如【1】~【4】的任一项所述的燃料电池用电极催化剂的制造方法,其特征在于,在上述工序(II)中,还混合进作为过渡金属元素含有选自铁、镍、铬、钴和锰中的至少1种过渡金属元素M2的化合物。【6】.一种燃料电池用电极催化剂层的制造方法,其特征在于,包含以下工序:通过【1】~【5】的任一项所述的方法制造燃料电池用电极催化剂的工序,以及,使用含有所述燃料电池用电极催化剂的催化剂层形成用材料、来形成燃料电池用电极催化剂层的工序。【7】.一种燃料电池用电极的制造方法,所述燃料电池用电极具有燃料电池用电极催化剂层和多孔质支持层,所述制造方法的特征在于,包含以下工序:通过【6】所述的方法制造燃料电池用电极催化剂层的工序,以及,在所述多孔质支持层的表面上形成所述燃料电池用电极催化剂层的工序。【8】.一种膜电极接合体的制造方法,所述膜电极接合体具有阴极、阳极和配置在所述阴极和所述阳极之间的电解质膜,所述制造方法的特征在于,包含以下工序:通过【7】所述的方法制造燃料电池用电极的工序,以及,使用燃料电池用电极作为所述阴极和所述阳极中的至少一者,并且配置所述阴极、所述电解质膜和所述阳极而制造膜电极接合体的工序。【9】.一种燃料电池的制造方法,其特征在于,包含以下工序:通过【8】所述的方法制造膜电极接合体的工序,以及,使用所述膜电极接合体来制造燃料电池的工序。【10】.如【9】所述的燃料电池的制造方法,其特征在于,所述燃料电池为固体高分子型燃料电池。发明效果通过本发明的制造方法,能够经较低温度下的热处理,制造出使用了过渡金属(钛等)的具有高催化活性的燃料电池用电极催化剂。附图说明图1是实施例1的燃料电池用电极(1)的氧还原电流密度-电位曲线。图2是实施例1的催化剂(1)的粉末X射线衍射谱图。图3是实施例2的燃料电池用电极(2)的氧还原电流密度-电位曲线。图4是实施例2的催化剂(2)的粉末X射线衍射谱图。图5是实施例3的燃料电池用电极(3)的氧还原电流密度-电位曲线。图6是实施例3的催化剂(3)的粉末X射线衍射谱图。图7是实施例4的燃料电池用电极(4)的氧还原电流密度-电位曲线。图8是实施例4的催化剂(4)的粉末X射线衍射谱图。图9是实施例5的燃料电池用电极(5)的氧还原电流密度-电位曲线。图10是实施例5的催化剂(5)的粉末X射线衍射谱图。图11是比较例1的燃料电池用电极(c1)的氧还原电流密度-电位曲线。图12是比较例1的催化剂(c1)的粉末X射线衍射谱图。图13是比较例2的燃料电池用电极(c2)的氧还原电流密度-电位曲线。图14是比较例2的催化剂(c2)的粉末X射线衍射谱图。图15是比较例3的燃料电池用电极(c3)的氧还原电流密度-电位曲线。图16是比较例4的燃料电池用电极(c4)的氧还原电流密度-电位曲线。具体实施方式[燃料电池用电极催化剂的制造方法]本发明的燃料电池用电极催化剂的制造方法,其特征在于,包含以下工序:工序(I):使过渡金属化合物(1)的水溶液与氨和/或氨水接触,生成含有所述过渡金属的原子的沉淀物(A);工序(II):使至少所述沉淀物(A)、有机化合物(B)和液体介质(C)混合,得到催化剂前体;工序(IV):将所述催化剂前体中的固体成分在500~1200℃的温度下热处理,得到电极催化剂,所述过渡金属化合物(1)的一部分或全部为作为过渡金属元素含有选自元素周期表第IVB族和第VB族的元素中的至少1种过渡金属元素(下文中也记作“过渡金属元素M1”或“M1”。)的化合物,所述有机化合物(B)是选自糖、氨基糖、糖胺聚糖(glycosaminoglycan)、聚乙烯醇、聚烷撑二醇、聚酯、含氮高分子化合物、含氰基化合物、氨基酸和有机酸中的至少1种。需说明的是,本说明书中,如果没有特别情况,将原子和离子不加以严格区别而都记作“原子”。(工序(I))工序(I)中,使过渡金属化合物(1)的水溶液与氨和/或氨水接触,产生含有所述过渡金属的原子的沉淀物(A)。该沉淀物(A)含有过渡金属的氢氧化物。接触操作优选通过向氨水中添加过渡金属化合物(1)的水溶液来实施。通过这样,能够得到分散性更高、涂布性更优异的催化剂。此外,也可以通过向过渡金属化合物(1)的水溶液中吹入氨气或添加氨水来实施。此外,优选向氨水中少量少量地分多次滴加过渡金属化合物(1)的水溶液(即、不是将所有量一次性加入。)。将所述沉淀物(A)回收后供给后述工序(II)。所述沉淀物(A)的回收既可以通过使含有沉淀物(A)的水溶液进行离心分离来进行,也可以通过过滤进行,但优选通过离心分离进行。通过离心分离进行的所述沉淀物(A)的回收,通过含有沉淀物(A)的水溶液的离心分离、和上清液的除去这一系列的操作进行。上清液可以全都被除去,也可以仅除去一部分。在后者时,沉淀物(A)将与上清液一起被供给工序(II)。通过离心分离进行的回收,能够将所述沉淀物(A)的更小粒子都供给后面的工序,这从得到更高比表面积的催化剂、催化剂的单位质量的活性变高来看优选。离心分离优选进行多次(例:2~7次)。即、优选将回收的沉淀物(A)添加到水中的添加、(任意性的搅拌)、离心分离、上清液的除去这些操作反复进行。通过反复进行离心分离,能够使沉淀物(A)被纯化。离心分离在例如转速:500~20000rpm、时间:5分~120分钟的条件下进行。通过过滤回收所述沉淀物(A)的回收,既可以使用滤纸或过滤膜进行,也可以通过将一边使用超滤膜一边将回收的沉淀物(A)添加到水中的添加、(任意性的搅拌)、过滤、滤液的除去这些操作反复进行,从而一边使沉淀物(A)一边纯化,一边进行所述沉淀物(A)的回收。该沉淀物也可以是凝胶状物质。<过渡金属化合物(1)>所述过渡金属化合物(1)的一部分或全部是作为过渡金属元素含有选自元素周期表第IVB族和第VB族元素中的至少1种过渡金属元素M1的化合物。作为所述过渡金属元素M1,具体可以列举出钛、锆、铪、铌、钒和钽。它们既可以1种单独使用,也可以2种以上并用。在过渡金属元素M1中,从成本和得到的催化剂的性能的观点考虑,优选钛、锆、铌和钽,更优选钛和锆。这些金属,特别是由于在地壳中埋藏量多、产品能够稳定供给,所以在产业上优势大。作为所述过渡金属化合物(1)的具体例,可以例举出金属硫酸盐、金属卤化物、金属醇盐、金属乙酸盐、金属磷酸盐、金属硝酸盐、金属有机酸盐、金属卤氧化物(金属卤化物的不完全水解物)、金属高卤酸盐和金属次卤酸盐、金属配合物,优选金属硫酸盐、金属卤化物。作为所述金属卤化物,可以例举出所述过渡金属的氯化物、溴化物和碘化物,由于使用时的安全性高,优选所述过渡金属的氯化物。作为所述金属醇盐,优选所述过渡金属的甲醇盐、丙醇盐、异丙醇盐、乙醇盐、丁醇盐、和异丁醇盐,更优选所述过渡金属的异丙醇盐、乙醇盐和丁醇盐。所述金属醇盐可以具有1种烷氧基,也可以具有2种以上的烷氧基。作为所述金属卤化物,可以例举出所述过渡金属的氯化物、溴化物和碘化物,作为所述金属卤氧化物,可以列举出所述过渡金属的氯氧化物、溴氧化物、碘氧化物。作为所述金属卤氧化物,可以例举出金属氯氧化物,作为金属高卤酸盐可以例举出金属高氯酸盐,作为金属次卤酸盐可以列举出金属次氯酸盐。作为所述过渡金属化合物(1)的具体例,可以列举出:硫酸钛、四氯化钛、三氯化钛、四溴化钛、三溴化钛、四碘化钛、三碘化钛、四甲醇钛、四乙醇钛、四丙醇钛、四异丙醇钛、四丁醇钛、四异丁醇钛、四戊醇钛、四乙酸钛等乙酸钛、二氧化钛、相对于1个钛原子具有1个以上2个以下氧原子的氧化钛、四乙酰丙酮钛、二乙酰丙酮氧钛、三(乙酰丙酮)钛氯化钛([Ti(acac)3]2[TiCl6])、氯氧化钛、溴氧化钛、碘氧化钛、硝酸钛、硝酸氧钛等的钛化合物;硫酸铌、五氯化铌、五溴化铌、五碘化铌、五甲醇铌、五乙醇铌、五异丙醇铌、五丁醇铌、五戊醇铌、五氧化铌、相对于1个铌原子具有2.5个以下氧原子的氧化铌、氯氧化铌、溴氧化铌、碘氧化铌、硝酸铌、硝酸氧铌等铌化合物;硫酸锆、四氯化锆、四溴化锆、四碘化锆、四甲醇锆、四乙醇锆、四丙醇锆、四异丙醇锆、四丁醇锆、四异丁醇锆、四戊醇锆、四乙酸锆、二氧化锆、相对于1个锆原子具有1个以上2个以下氧原子的氧化锆、四乙酰丙酮锆、氯氧化锆、溴氧化锆、碘氧化锆、硝酸锆、硝酸氧锆等锆化合物;硫酸钽、五氯化钽、五溴化钽、五碘化钽、五甲醇钽、五乙醇钽、五异丙醇钽、五丁醇钽、五戊醇钽、五乙酸钽、五氧化钽、相对于1个钽原子具有2.5个以下氧原子的氧化钽、四乙氧基乙酰丙酮钽、氯氧化钽、溴氧化钽、碘氧化钽、硝酸钽等钽化合物;硫酸氧钒、五氯化钒、五溴化钒、五碘化钒、三甲氧基氧化钒、三乙氧基氧化钒、三异丙氧基氧化钒、三丁氧基氧化钒、氧化钒、相对于1个钒原子具有2.5个以下氧原子的氧化钒、乙酰丙酮钒(III)、乙酰丙酮钒(V)、氯氧化钒、溴氧化钒、碘氧化钒、硝酸钒、硝酸氧钒等钒化合物;硫酸铪、四氯化铪、溴化铪、碘化铪、四甲醇铪、四乙醇铪、四丙醇铪、四异丙醇铪、四丁醇铪、四异丁醇铪、四戊醇铪、乙酸铪、二氧化铪、相对于1个铪原子具有1个以上2个以下氧原子的氧化铪、四乙酰丙酮铪、氯氧化铪、溴氧化铪、碘氧化铪、硝酸铪、硝酸氧铪等的铪化合物。它们可以1种单独使用,也可以2种以上并用。在这些化合物中,优选硫酸钛、四氯化钛、硫酸铌、五氯化铌、硫酸锆、四氯化锆、氯氧化锆、硫酸钽、五氯化钽,更优选硫酸钛、四氯化钛。<过渡金属化合物(2)>过渡金属化合物(1)的水溶液与氨和/或氨水的接触也可以在过渡金属化合物(2)的存在下进行。作为该过渡金属化合物(2),可以使用与所述过渡金属化合物(1)不同的、作为过渡金属元素含有选自铁、镍、铬、钴和锰中的至少1种过渡金属元素(下文中也记作“过渡金属元素M2”或“M2”。)M2的过渡金属化合物。若使用过渡金属化合物(2),则得到的催化剂的性能提高。作为过渡金属元素M2,由于每单位成本的催化剂性能高,所以优选铁和铬,更优选铁。作为过渡金属化合物(2)的具体例,可以列举出:氯化铁(II)、氯化铁(III)、硫酸铁(III)、硫化铁(II)、硫化铁(III)、亚铁氰化钾、铁氰化钾、亚铁氰化铵、铁氰化铵、亚铁氰化铁、硝酸铁(II)、硝酸铁(III)、草酸铁(II)、草酸铁(III)、磷酸铁(II)、磷酸铁(III)、二茂铁、氢氧化铁(II)、氢氧化铁(III)、氧化铁(II)、氧化铁(III)、四氧化三铁、乙酸铁(II)、乳酸铁(II)、柠檬酸铁(III)等铁化合物;氯化镍(II)、硫酸镍(II)、硫化镍(II)、硝酸镍(II)、草酸镍(II)、磷酸镍(II)、二茂镍、氢氧化镍(II)、氧化镍(II)、乙酸镍(II)、乳酸镍(II)等镍化合物;氯化铬(II)、氯化铬(III)、硫酸铬(III)、硫化铬(III)、硝酸铬(III)、草酸铬(III)、磷酸铬(III)、氢氧化铬(III)、氧化铬(II)、氧化铬(III)、氧化铬(IV)、氧化铬(VI)、乙酸铬(II)、乙酸铬(III)、乳酸铬(III)等铬化合物;氯化钴(II)、氯化钴(III)、硫酸钴(II)、硫化钴(II)、硝酸钴(II)、硝酸钴(III)、草酸钴(II)、磷酸钴(II)、二茂钴、氢氧化钴(II)、氧化钴(II)、氧化钴(III)、四氧化三钴、乙酸钴(II)、乳酸钴(II)等钴化合物;氯化锰(II)、硫酸锰(II)、硫化锰(II)、硝酸锰(II)、草酸锰(II)、氢氧化锰(II)、氧化锰(II)、氧化锰(III)、乙酸锰(II)、乳酸锰(II)、柠檬酸锰等锰化合物。这些化合物可以1种单独使用,也可以2种以上并用。在这些化合物中,氯化铁(II)、氯化铁(III)、亚铁氰化钾、铁氰化钾、亚铁氰化铵、铁氰化铵、乙酸铁(II)、乳酸铁(II)、氯化镍(II)、乙酸镍(II)、乳酸镍(II)、氯化铬(II)、氯化铬(III)、乙酸铬(II)、乙酸铬(III)、乳酸铬(III)、氯化钴(II)、氯化钴(III)、乙酸钴(II)、乳酸钴(II)、氯化锰(II)、乙酸锰(II)、乳酸锰(II),由于以它们作为原料得到的催化剂的活性高,所以更优选,氯化铁(II)、氯化铁(III)、亚铁氰化钾、铁氰化钾、亚铁氰化铵、铁氰化铵、乙酸铁(II)、乳酸铁(II)、氯化铬(II)、氯化铬(III)、乙酸铬(II)、乙酸铬(III)、乳酸铬(III),由于以它们作为原料得到的催化剂的活性极高,所以进而优选,(工序(II))工序(II)中,至少将所述沉淀物(A)、有机化合物(B)(具体如后文所记载)和液体介质(C)混合在一起,而配制催化剂前体液。混合操作,也可以通过先将所述有机化合物(B)和所述液体介质(C)混合而配制所述有机化合物(B)的溶液(或分散液),然后使该溶液(或分散液)和所述沉淀物(A)混合来实施。若在液体介质(C)的存在下将所述沉淀物(A)和所述有机化合物(B)混合,则能够使它们没有分布不均地进行混合。此外,还可以向所述有机化合物(B)的溶液或分散液中将所述沉淀物(A)少量少量地分多次添加(即、不是将所有量一次性加入。)。工序(II)中,还可以向高压釜等能够加压的容器中加入所述沉淀物(A)、所述有机化合物(B)、所述液体介质(C),一边施加常压以上的压力一边进行混合。<有机化合物(B)>作为所述有机化合物(B),可以列举出葡萄糖、果糖、蔗糖、纤维素、羟丙基纤维素等的糖;葡萄糖胺、乙酰基葡萄糖胺、半乳糖胺、乙酰基神经氨酸、果糖胺、胞壁二肽、酮胺(ketosamine)等的氨基糖;透明质酸、4-硫酸软骨素、6-硫酸软骨素、肝素、硫酸角质素、硫酸软骨素等糖胺聚糖;聚乙烯醇;聚乙烯基吡咯烷酮、聚苯胺、聚吡咯、聚吡啶等含氮高分子化合物;聚乙二醇、聚丙二醇等聚烷撑二醇类;聚对苯二甲酸乙二醇酯等聚酯;丙烯腈、聚丙烯腈等的含氰基化合物;甘氨酸、丙氨酸、蛋氨酸等氨基酸;抗坏血酸、柠檬酸、硬脂酸等有机酸等等。在这些中,优选分子中含有氮原子的高分子化合物(下文中也记作“含氮高分子化合物”。)和氨基酸,更优选聚乙烯基吡咯烷酮、葡萄糖胺、甘氨酸。作为所述有机化合物(B),可以使用分子中含有氮的有机化合物(含氮有机化合物)和分子中不含氮的有机化合物中的任一者。工序(II)中使用的所述有机化合物(B)的碳的总原子数B相对于本发明的制造方法中使用的过渡金属化合物(即、工序(II)中使用的所述过渡金属化合物(1)和后述工序(III)中任意性使用的过渡金属化合物(2))的过渡金属元素的总原子数A之比(B/A),由于能够减少工序(IV)的热处理时作为二氧化碳、一氧化碳等碳化合物而脱离的成分,即减少制造催化剂时的排气的量,且得到的催化剂的活性高,而优选是1以上200以下,进而优选是1.5以上150以下,进而优选是2以上130以下,更优选是3以上80以下,更进而优选是4以上60以下,特别优选是5以上30以下。在所述有机化合物(B)为含氮有机化合物的情形,工序(II)中使用的所述含氮有机化合物的氮原子的总数C、相对于本发明的制造方法中使用的过渡金属化合物(即、工序(II)中使用的所述过渡金属化合物(1)和后述工序(III)中任意性使用的过渡金属化合物(2))的过渡金属元素原子的总数A的比(C/A),从得到具有良好的氧还原活性的催化剂的观点考虑,优选是1以上28以下、进而优选是1.5以上17以下、更优选是2以上12以下、进而更优选是2.5以上10以下、特别是优选是3.5以上8.5以下。<液体介质(C)>作为所述液体介质(C),可以列举出例如水、醇类、和酸类的水或醇类的溶液。作为醇类,优选乙醇、甲醇、丁醇、丙醇和乙氧基乙醇,更优选乙醇和甲醇。作为酸类,优选乙酸、硝酸、盐酸、磷酸和柠檬酸,在这些酸类为液体状时,既可以将它们以原状直接使用,也可以以水溶液或醇类的溶液的形式使用。由于得到的催化剂的氧还原活性高,所以作为酸类更优选乙酸和硝酸。水、醇类、和酸类(也包括水或醇类的溶液。)既可以单独使用1种,也可以2种以上并用。<过渡金属化合物(2)>工序(II)中,还可以与所述沉淀物(A)、所述有机化合物(B)和液体介质(C)一起混合所述过渡金属化合物(2)。使用所述过渡金属化合物(M2),会使得到的催化剂的性能提高。混合过渡金属化合物(2)时的混合操作,也可以通过先将所述有机化合物(B)和所述过渡金属化合物(2)、和所述液体介质(C)混合,配制溶液(或分散液),然后将该溶液(或分散液)和所述沉淀物(A)混合,从而实施。(工序(III))在工序(IV)之前任意性实施的工序(III)中,从工序(II)得到的所述催化剂前体液中(在将沉淀物(A)随着上清液一起供给工序(II)的情形,连通该上清液一起)除去液体介质(C)。液体介质(C)的除去既可以在大气下进行,也可以在惰性气体(例如,氮气、氩气、氦气)的气氛下进行。使用惰性气体,会使得到的催化剂的活性变高,所以优选,惰性气体中,从成本的观点考虑,优选氮气和氩气,进而优选氮气。除去液体介质(C)时的温度,在液体介质(C)的蒸气压大的情形也可以是常温,但从催化剂的大量生产性的观点考虑,优选是30℃以上、进而优选是40℃以上、更优选是50℃以上,从使工序(II)得到的液中含有的催化剂前体不分解的观点考虑,优选是250℃以下、进而优选是150℃以下、更优选是110℃以下。液体介质(C)的除去,在液体介质(C)的蒸气压大的情形,可以在大气压下进行,但为了在更短时间除去液体介质(C),优选在减压(例如,0.1Pa~0.1MPa)下进行。减压下的液体介质(C)的除去,可以使用例如蒸发仪。液体介质(C)的除去,可以以工序(II)中得到的混合物静置的状态进行,但为了得到更均匀的固体成分残渣,优选一边使混合物转动,一边除去液体介质(C)。在装纳所述混合物的容器的重量大的情形,优选使用搅拌棒、搅拌翼、搅拌子等,使溶液转动。此外,在一边调节装纳所述混合物的容器的真空度,一边进行液体介质(C)的除去的情形,为了在能够密闭的容器中进行干燥,优选一边连同容器一起旋转一边进行液体介质(C)的除去,例如使用旋转蒸发仪进行液体介质(C)的除去。根据液体介质(C)的除去的方法、或所述有机化合物(B)的性状等的不同,有时工序(III)得到的固体成分残渣的组成或凝聚状态不均匀。在这种情形中,如果在工序(IV)中使用将固体成分残渣混合、粉碎而变得更均匀、微细的粉末,则可以得到粒径更均匀的催化剂。将固体成分残渣混合、粉碎,可以使用例如辊转动磨、球磨机、小径球磨机(珠磨机)、介质搅拌磨、气流粉碎机、研钵、自动混炼研钵、槽式分解机、喷射式磨碎机(jetmill),如果固体成分残渣量少,则优选使用研钵、自动混炼研钵、或间歇式的球磨机,在固体成分残渣量多,要进行连续性混合、粉碎处理时,优选使用喷射式磨碎机。(工序(IV))工序(IV)中,对所述催化剂前体液中的固体成分进行热处理。该热处理中,既可以将工序(II)中得到的含有固体成分的所述催化剂前体液以原状直接进行热处理,也可以将工序(III)中得到的所述固体成分残渣进行热处理。该热处理之际的温度是500~1200℃,优选是600~1100℃,进而优选是700~1050℃。如果热处理的温度过于高出上述范围,则得到的热处理物的粒子相互间会出现烧结、粒生长,结果、电极催化剂的比表面积变小,因此,在通过涂布法将该粒子加工成催化剂层时加工性变差。另一方面,如果热处理的温度过于低于上述范围,则得不到具有高活性的电极催化剂。作为所述热处理的方法,可以列举出例如,静置法、搅拌法、下落法、粉末捕捉法。静置法是指,在静置式的电炉等中放置工序(III)中得到的固体成分残渣,将其加热的方法。加热之际,也可以将量取的所述固体成分残渣放入氧化铝槽、石英槽等陶瓷容器中。静置法可以对大量的所述固体成分残渣进行加热,从这点来看优选。搅拌法是指,将上述固体成分残渣放入到旋转炉等电炉中,将其一边搅拌一边加热的方法。搅拌法的情形,可以对大量的上述固体成分残渣进行加热,且可以抑制所得的电极催化剂的粒子凝聚和成长,从这点来看优选。进而,搅拌法,通过使加热炉倾斜,可以连续制造电极催化剂,从这点来看优选。下落法是指,一边向感应炉中流通例如含有微量氧气的惰性气体作为气氛气体,一边将炉加热到规定的加热温度,在该温度保持热平衡后,使上述固体成分残渣下落到作为炉的加热区域的坩埚中,将其加热的方法。下落法,可以将所得的电极催化剂的粒子的凝聚和生长抑制在最小限度,从这点来看优选。粉末捕捉法是指在含有微量氧气的惰性气体气氛中,使上述固体成分残渣变为飞沫、浮游,将其捕捉到保持在规定加热温度的垂直管状炉中,进行加热的方法。在利用上述静置法进行热处理时,对升温速度没有特别限定,但优选为1℃/分钟~100℃/分钟左右、进而优选为5℃/分钟~50℃/分钟。此外,加热时间优选为0.1~10小时、更优选为0.5小时~5小时、进而优选为0.5~3小时。当在静置法中在管状炉中进行加热时,电极催化剂粒子的加热时间为0.1~10小时、优选为0.5小时~5小时。上述加热时间为上述范围内,这从形成均匀的电极催化剂粒子,得到高活性催化剂是优选的。在上述搅拌法的情形,上述固体成分残渣的加热时间通常为10分钟~5小时、优选为30分钟~2小时。本法中,在采用使炉倾斜等方式进行连续加热时,将根据恒定的炉内的样品流量计算出的平均滞留时间作为上述加热时间。在上述下落法的情形,上述固体成分残渣的加热时间通常为0.5~10分钟,优选为0.5~3分钟。当上述加热时间为上述范围内时,倾向于形成均匀的电极催化剂粒子。在上述粉末捕捉法的情形,上述固体成分残渣的加热时间为0.2秒钟~1分钟、优选为0.2~10秒钟。当上述加热时间为上述范围内时,倾向于形成均匀的电极催化剂粒子。在采用上述静置法进行热处理时,还可以使用作为热源采用LNG(液态天然气)、LPG(液化石油气)、轻油、重油、电等的加热炉作为热处理装置。该情形,由于在本发明中对上述固体成分残渣进行热处理时的气氛很重要,所以优选从炉的外部进行加热的装置,而不是在炉内存在燃料的火焰、从炉的内部进行加热的装置。在使用上述固体成分残渣的量为每批50kg以上的加热炉时,从成本的观点来考虑,优选以LNG、LPG作为热源的加热炉。在要得到催化活性特别高的电极催化剂时,优选使用能够严密地控制温度的、将电通电阻丝而将其作为热源的电炉。作为炉的形状,可以列举出管状炉、上盖型炉、隧道炉、箱型炉、试样台升降式炉(电梯型)、平板车炉等,在这些之中,优选能够特别严密控制气氛的、管状炉、上盖型炉、箱型炉和试样台升降式炉,优选管状炉和箱型炉。在采用上述搅拌法时,可以使用上述热源,但在搅拌法中、特别是使旋转炉倾斜、对上述固体成分残渣进行连续热处理时,由于设备的规模变大、能量使用量容易变大,因而优选使用来自LPG等燃料的热源。作为进行上述热处理时的气氛,从提高所得的电极催化剂的活性的观点来考虑,优选氮气、氩气、氦气,进而优选氮气和氩气。它们既可以单独使用1种,也可以将两种以上混合使用。在所述有机化合物(B)是分子中不含氮的有机化合物的情形,从提高得到的电极催化剂的活性的观点考虑,优选在氮气环境中800℃以上的温度进行所述热处理。此外,如果在所述热处理的气氛中存在反应性气体,则有时得到的电极催化剂会表现出更高的催化剂性能。作为所述反应性气,可以列举出例如氧气、氢气、甲烷等含碳气体、氨气等含氮气体。在所述热处理的气氛中含有氢气的情形,氢气的浓度是例如100体积%以下、优选是0.01~10体积%、进而优选是1~5体积%。在所述热处理的气氛中含有氧气的情形,氧气的浓度是例如0.01~10体积%、优选是0.01~5体积%。在上述热处理后还可以将热处理物进行粉碎。在进行粉碎时,有时可以改善使用得到的电极催化剂制造电极时的加工性、和所得电极的特性。该粉碎可以使用例如、辊转动磨机、球磨机、小径球磨机(珠磨机)、介质搅拌磨机、气流粉碎机、研钵、自动混炼研钵、槽式分解机或喷射式磨碎机。在电极催化剂量少时,优选研钵、自动混炼研钵、间歇式的球磨机,在连续处理大量热处理物时,优选喷射式磨碎机、连续式的球磨机,在连续式的球磨机中更优选珠磨机。[燃料电池用电极催化剂]本发明的燃料电池用电极催化剂,特征在于,是通过上述本发明的燃料电池用电极催化剂的制造方法制造的(下文中,也将通过上述本发明的燃料电池用电极催化剂的制造方法制造出的燃料电池用电极催化剂简称作“催化剂”。)。若将构成所述催化剂的过渡金属元素(其中,不区分过渡金属元素M1和过渡金属元素M2。)、碳、氮和氧的原子数之比表示成过渡金属元素:碳:氮:氧=1:x:y:z,则优选:0<x≤7、0<y≤2、0<z≤3。由于电极催化剂的活性高,所以x的范围进而优选是0.15≤x≤5.0、更优选是0.2≤x≤4.0,特别优选是1.0≤x≤3.0,y的范围进而优选是0.01≤y≤1.5、更优选是0.02≤y≤0.5,特别优选是0.03≤y≤0.4,z的范围进而优选是0.6≤z≤2.6,更优选是0.9≤z≤2.0,特别优选是0.95≤z≤1.5。此外、所述催化剂,在作为所述过渡金属元素含有选自元素周期表第IVB族和第VB族元素中的1种过渡金属元素M1、和选自铁、镍、铬、钴和锰中的至少1种过渡金属元素M2的情形,若将构成所述催化剂的过渡金属元素M1、过渡金属元素M2、碳、氮和氧的原子数之比表示成过渡金属元素M1:过渡金属元素M2:碳:氮:氧=(1-a):a:x:y:z,则优选:0<a≤0.5、0<x≤7、0<y≤2、0<z≤3。在所述催化剂如此含有M2时,性能进一步变高。由于电极催化剂的活性高,所以x、y和z的优选范围如上所述,a的范围进而优选是0.01≤a≤0.5,更优选是0.015≤a≤0.4,特别优选是0.02≤a≤0.2。所述a、x、y和z的值是通过后述实施例所采用的方法测定得到的值。通过过渡金属元素M2(选自铁、镍、铬、钴和锰中的至少1种金属元素)的存在,能够推测出以下的(1)~(4)。推测(1):所述过渡金属元素M2或所述过渡金属化合物(M2),在合成电极催化剂之际,发挥用于形成所述过渡金属元素M1原子和所述含氮有机化合物中的氮原子之间的键合的催化剂的作用。推测(2):即使在过渡金属元素M1溶出那样的高电位、高氧化性气氛下使用电极催化剂,通过过渡金属元素M2钝态化,也能够防止过渡金属元素M1的进一步溶出。推测(3):在工序(IV)的热处理之际,能够防止热处理物的烧结、即比表面积的降低。推测(4):通过在电极催化剂中存在过渡金属元素M1、过渡金属元素M2,在双方的金属元素相邻的部位出现电荷的分布不均,发生对于作为金属元素仅具有过渡金属元素M1的电极催化剂所得不到的、基质的吸附或反应、或生成物的脱离。本发明的催化剂,优选具有过渡金属元素、碳、氮和氧各原子,具有所述过渡金属元素的氧化物、碳化物或氮化物单独的结晶结构或它们中的多种结晶结构。根据对所述催化剂进行X射线衍射分析得到的结晶结构解析结果和元素分析的结果判断,推测所述催化剂在原样具有所述过渡金属元素的氧化物结构的情况下具有氧化物结构的氧原子的位点被碳原子或氮原子置换的结构、或在原样具有所述过渡金属元素的碳化物、氮化物或碳氮化物的结构的情况下具有碳原子或氮原子的位点被氧原子置换的结构,或是含有这些结构的混合物。<BET比表面积>通过本发明的燃料电池用电极催化剂的制造方法,能够制造比表面积大的燃料电池用电极催化剂,用本发明的催化剂的BET法计算出的比表面积优选是30~350m2/g、进而优选是50~300m2/g、更优选是100~300m2/g。比表面积在上述范围内时,能够更好地保持催化剂的结构,进而单位重量的表面积大,所以催化剂的活性高,所以优选。通过本发明的制造方法制造出的燃料电池用电极催化剂的氧还原电流密度可以以下述方式求出。即、根据下述测定法(A)的结果计算出特定的电位(例如0.7V)时氧气气氛中的还原电流与氮气氛围中的还原电流之差,将算出的值进而除以电极面积,将所得的值作为氧还原电流密度(mA/cm2)。〔测定法(A):以在作为电子传导性物质的碳中分散的催化剂为1质量%的方式,将该催化剂和碳放入到溶剂中,利用超声波进行搅拌,得到悬浊液。另外、作为碳,使用炭黑(比表面积:100~300m2/g)(例如キャボット公司制XC-72),以催化剂和碳的质量比为95:5的方式分散。此外,作为溶剂,使用异丙醇:水(质量比)=2:1。在超声波作用下采集上述悬浊液10μL,然后马上滴加到玻碳电极(直径:5.2mm)上,在120℃下干燥5分钟。经干燥在玻碳电极上形成含有催化剂的燃料电池用催化剂层。进行该滴加和干燥操作,直至在碳电极表面形成1.0mg的燃料电池催化剂层。接下来进而将由5%纳菲昂(NAFION(注册商标))溶液(杜邦公司、DE521)用异丙醇稀释至10倍而成的溶液10μL滴加到上述燃料电池用催化剂层上。将其在120℃下干燥1小时。使用这样得到的电极,在氧气氛围和氮气氛围中、0.5mol/L的硫酸水溶液中、30℃的温度下,以相同浓度的硫酸水溶液中的可逆氢电极作为参比电极,以5mV/秒的电位扫描速度极化,而得到电流-电位曲线。通过本发明的制造方法制造出的燃料电池用电极催化剂的0.7V(vsRHE)时的氧还原电流密度,为了作为固体高分子形燃料电池用空气极催化剂使用,优选是0.08mA/cm2以上10mA/cm2以下,进而优选是0.1mA/cm2以上9mA/cm2以下,更优选是0.2mA/cm2以上8mA/cm2以下,特别是优选是0.3mA/cm2以上7mA/cm2以下。[用途]通过本发明的制造方法制造出的燃料电池用电极催化剂,能够作为铂催化剂的替代催化剂使用。通过本发明的燃料电池用电极催化剂层的制造方法制造出的燃料电池用催化剂层,含有所述催化剂。燃料电池用催化剂电极层有阳极催化剂层、阴极催化剂层,但上述催化剂可以用于任一者。由于所述催化剂,耐久性优异、氧还原性能大,所以优选在阴极催化剂层中使用。本发明的燃料电池用电极催化剂层优选还含有电子传导性粉末。在含有上述催化剂的燃料电池用催化剂层还含有电子传导性粉末的场合,能够进一步提高还原电流。可以想到,电子传导性粉末,能够使上述催化剂产生诱发电化学反应的电接触点,所以能够提高还原电流。所述电子传导性粒子通常作为催化剂的载体使用。虽然所述催化剂具有一定程度的导电性,但为了通过催化剂给予更多的电子,或为了反基质从催化剂接收更多的电子,也可以使催化剂中混合用于赋予导电性的载体粒子。这些载体粒子,既可以混合在经工序(I)~工序(IV)制造出的催化剂中,也可以在工序(II)~工序(IV)的任一阶段中混合。作为电子传导性粒子的材质,可以例举出碳、导电性高分子、导电性陶瓷、金属或氧化钨或氧化铱等的导电性无机氧化物,可以将它们1种单独或组合使用。特别是,由于由碳形成的电子传导性粒子比表面积大,此外,容易廉价地获得小粒径的,耐药品性、耐高电位性优异,所以优选单独的碳,或碳和其他的电子传导性粒子的混合物。即、燃料电池用催化剂层,优选含有上述催化剂和碳粒子。作为碳,可以列举出炭黑、石墨、活性碳、碳纳米管、碳纳米纤维、碳纳米突、富勒烯、多孔体碳、石墨烯等。由碳形成的电子传导性粒子的粒径,如果过小,则电子传导通道难以形成,此外,在下述范围内时,燃料电池用催化剂层的气体扩散性进一步提高,催化剂的利用率进而提高,所以优选是10~1000nm,进而优选是10~100nm。在电子传导性粒子由碳形成时,所述催化剂和电子传导性粒子的重量比(催化剂:电子传导性粒子)优选是4:1~1000:1。对所述导电性高分子没有特殊限定,可以列举出例如聚乙炔、对聚苯、聚苯胺、聚烷基苯胺、聚吡咯、聚噻吩、聚吲哚、聚-1,5-二氨基蒽醌、聚氨基联苯、聚(邻苯二胺)、聚喹啉盐、聚吡啶、聚喹喔啉、聚苯基喹喔啉等。在这些之中,优选聚吡咯、聚苯胺、聚噻吩,更优选聚吡咯。所述燃料电池用电极催化剂层优选还含有高分子电解质。作为上述高分子电解质,只要是在燃料电池用催化剂层中通常使用的,就没有特别限定。具体地说、可以列举出具有磺酸基的全氟碳聚合物(例如、纳菲昂(NAFION(注册商标))、具有磺酸基的烃系高分子化合物、掺杂磷酸等无机酸的高分子化合物、一部分被质子传导性官能团取代的有机/无机混杂聚合物、在高分子基质中浸渍进磷酸溶液、硫酸溶液的质子传导体等。在这些之中,优选纳菲昂(NAFION(注册商标)。作为形成上述燃料电池用催化剂层之际的纳菲昂(NAFION(注册商标))的供给源,可以列举出5%纳菲昂(NAFION(注册商标))溶液(DE521、杜邦公司)等。所述燃料电池用电极催化剂层可以用作阳极催化剂层或阴极催化剂层中的任一者。本发明的燃料电池用催化剂层由于含有具有高氧还原性能、即使在酸性电解质中高电位下也难以被腐蚀的催化剂,所以可以用作设置在燃料电池的阴极中的催化剂层(阴极用催化剂层)。特别适合用作在固体高分子型燃料电池所具有的膜电极接合体的阴极中设置的催化剂层。作为将上述催化剂分散在作为载体的上述电子传导性粒子上的方法,可以列举出气流分散、液中分散等方法。液中分散,可以将溶剂中分散有催化剂和电子传导性粒子的液体用于燃料电池用催化剂层形成工序,所以优选。作为液中分散,可以列举出锐孔收缩流的方法、旋转剪切流的方法或超声波的方法等。液中分散时使用的溶剂,只要可以使催化剂、电子传导性粒子在不被侵蚀的情况下分散,就没有特殊限定,通常使用挥发性的液体有机溶剂或水等。此外,在将所述催化剂分散在所述电子传导性粒子上之际,也可以使上述电解质和分散剂同时分散。作为燃料电池用催化剂层的形成方法,没有特殊限定,但可以列举出例如,将含有上述催化剂和电子传导性粒子、电解质的悬浊液涂布到后述电解质膜或气体扩散层的方法。作为上述涂布的方法,可以列举出浸渍法、丝网印刷法、辊涂法、喷雾法等。此外可以列举出以下方法:将含有上述催化剂和电子传导性粒子、电解质的悬浊液通过涂布法或过滤法在基材上形成燃料电池用催化剂层,然后用转印法在电解质膜上形成燃料电池用催化剂层。通过本发明的电极的制造方法制造的电极具有所述燃料电池用催化剂层和多孔质支持层。所述电极可以作为阴极或阳极任一种电极使用。本发明的电极耐久性优异、催化能力大,所以在阴极中使用时,产业上优越性更大。多孔质支持层是使气体可扩散的层(下文中也记作“气体扩散层”。)。作为气体扩散层,只要具有电子传导性、气体的扩散性高、耐蚀性高,就可以是任意的,通常使用碳纸、碳布等碳系多孔质材料、或为了轻量化而使用不锈钢、被覆有耐蚀材料的铝箔。通过本发明的膜电极接合体的制造方法制造的膜电极接合体,是具有阴极和阳极、和配置在所述阴极和所述阳极之间的电解质膜的膜电极接合体,所述阴极和所述阳极的至少一者是通过本发明的电极制造方法制造的电极。作为电解质膜,通常使用例如、使用了全氟磺酸系物质而成的电解质膜或烃系电解质膜等,但也可以使用在高分子微多孔膜中浸渗进液体电解质的膜或在多孔质体中填充有高分子电解质的膜等。此外,通过本发明的制造方法制造的燃料电池具有所述膜电极接合体。燃料电池的电极反应是在所谓的3相界面(电解质-电极催化剂-反应气体)上发生。燃料电池根据所使用的电解质等不同而分为多种,有熔融碳酸盐型(MCFC)、磷酸型(PAFC)、固体氧化物型(SOFC)、固体高分子型(PEFC)等。其中,本发明的膜电极接合体优选用于固体高分子型燃料电池。使用通过本发明的制造方法制造出的燃料电池用电极催化剂的燃料电池,性能高,此外,与使用铂作为催化剂的情形相比较,具有价格非常便宜的特征。所述燃料电池可以使具有选自发电功能、发光功能、发热功能、发音功能、运动功能、显示功能和充电功能中的至少一种功能的、具有燃料电池的物品的性能、特别是可随身携带物品的性能提高。所述燃料电池优选在物品的表面或内部存在。使用通过本发明的制造方法制造出的燃料电池用电极催化剂的燃料电池,单位质量的活性高、且价格便宜,能够在以往难以搭载燃料电池的上述物品上搭载燃料电池,该物品能够以更小体积使用大功率的电力,惠及功能的完善,所以优选。<具有燃料电池的物品的具体例>作为能够具有所述燃料电池的所述物品的具体例,可以列举出高楼、宅院、帐篷等建筑物、荧光灯、LED等、有机EL、路灯、室内照明、信号机等照明器具、机械、包含车辆本身在内的汽车用机器、家电制品、农业机器、电子装置、包含手机等便携信息终端、美容器材、可移动式工具、洗浴用品卫生间用品等卫生器材、家具、玩具、装饰品、告示板、冷藏箱、室外发电机等户外用品、教材、假花、雕刻品、心脏起搏器用电源、具有帕尔贴元件的加热和冷却器用的电源。使用通过本发明的制造方法制造出的燃料电池用电极催化剂的燃料电池,单位质量的发电性能高、且价格便宜,能够在以往难以搭载燃料电池的物品上搭载燃料电池,能够省略用于给电的配线,所以有用。实施例下面通过实施例来更具体地说明本发明,但本发明并不受这些实施例限定。实施例和比较例中的各种测定通过下述方法进行。[分析方法]1.粉末X射线衍射使用理学电机株式会社制ロータフレックス,进行试样的粉末X射线衍射。各试样的粉末X射线衍射中衍射线峰的根数,是将能够检测到信号(S)和噪音(N)之比(S/N)为2以上的信号作为1个峰来计数的。需说明的是,噪音(N)取基线的宽度。2.元素分析碳:量取试样约0.1g,用碳硫分析装置(堀场制作所制、EMIA-110)进行测定。氮·氧:量取试样约0.1g,将试样封入Ni-Cup胶囊中,然后用氧氮分析装置(LECO制、TC600)进行测定。过渡金属元素(钛、锆、铁):在铂盘中量取试样约0.1g,加入酸进行加热分解。将该加热分解物定容,然后稀释,用ICP-MS(Agilent公司制HP7500)进行定量。[实施例1]<硫酸钛-PVP>1.催化剂的制造将30%硫酸钛(IV)水溶液(和光纯药工业(株)制)9.12g加入到蒸馏水中,配制出100ml的钛溶液。准备28%氨水100ml和蒸馏水200ml的混合液,向该混合液中滴加上述钛溶液,生成沉淀物(钛化合物)。放置1小时后、用玻璃吸管除去上清液使反应液(含有沉淀物)剩下100ml。将含有该沉淀物的反应液以10000rpm进行30分钟离心分离,然后用玻璃吸管除去上清液使容器内沉淀物和上清液合计剩下20ml。接下来,向容器内中添加纯水80ml,搅拌容器的内容物,与上述同样进行离心分离,与上述同样地除去上清液,将这一系列的操作反复进行3次,得到含有凝胶状物质的液20ml。可以想到,该凝胶状物质中含有氢氧化钛。接下来,在作为液体介质的蒸馏水100ml中溶解聚乙烯基吡咯烷酮0.85g,进而加入所述含有凝胶状物质的液20ml,搅拌10分钟,得到催化剂前体液。使用旋转蒸发仪,在氮气氛围的减压下将加热搅拌器的温度设定在约100℃,一边将所述催化剂前体液加热且搅拌,一边使水慢慢蒸发。完全使水蒸发后,将得到的固体成分残渣用研钵细细均匀地研磨,得到热处理用粉末。将该热处理用粉末装入管状炉中,在氮气氛围下以升温速度10℃/min加热到1000℃,在1000℃保持3小时,经自然冷却得到催化剂(1)。催化剂(1)的BET比表面积和元素分析结果如表1所示。2.燃料电池用电极的制造接下来,将该催化剂(1)0.095g和碳(キャボット公司制XC-72)0.005g加入到异丙醇:纯水=2:1的质量比混合而成的溶液10g中,用超声波进行搅拌、悬浊混合。将该混合物30μl涂布到玻碳电极(東海カーボン社制、直径:5.2mm)上,120℃下干燥5分钟,就在碳电极表面形成1.0mg的燃料电池催化剂层。进而,在燃料电池用催化剂层上涂布通过将5%纳菲昂(NAFION(注册商标))溶液(デュポン公司、DE521)用异丙醇稀释10倍而成的液体10μl,在120℃干燥1小时,得到燃料电池用电极(1)。3.氧还原性能的评价将制作出的燃料电池用电极在氧气氛围和氮气氛围中、0.5mol/L的硫酸水溶液中、30℃从1.1V开始向低电位侧以5mV/秒的电位扫描速度极化,分别测定出电流-电位曲线。将电流值除以各电极面积,从氧气氛围中观察到的电流密度减去氮气氛围中观察到的电流密度,将所得的值作为氧还原电流密度。此时,以相同浓度的硫酸水溶液中的可逆氢电极作为参比电极。表1示出了0.7V时的氧还原电流密度。显示出氧还原电流密度越高,则燃料电池用电极中催化剂的催化性能越高。[实施例2]<硫酸钛-葡萄糖胺>除将聚乙烯基吡咯烷酮0.85g变为N-乙酰基-D-葡萄糖胺(和光纯药工业(株)、纯度:90%)2.80g以外,进行与实施例1同样的操作,得到催化剂(2)。催化剂(2)的BET比表面积和元素分析结果如表1所示。此外,除将催化剂(2)变为催化剂(1)以外,进行与实施例1同样的操作,得到燃料电池用电极(2),评价其氧还原性能。结果如表1所示。[实施例3]<四氯化钛-葡萄糖胺>除将30%硫酸钛水溶液9.12g变为四氯化钛水溶液(钛含量:16.5质量%、(株)大阪チタニウムテクノロジーズ制)3.3g以外,进行与实施例2同样的操作,得到催化剂(3)。催化剂(3)的BET比表面积和元素分析结果如表1所示。此外,除将催化剂(1)变为催化剂(3)以外,进行与实施例1同样的操作,得到燃料电池用电极(3),评价其氧还原性能。结果如表1所示。[实施例4]<硫酸钛-甘氨酸>除将聚乙烯基吡咯烷酮0.85g变为甘氨酸(和光纯药工业(株)制、纯度:99%)11.1g以外,进行与实施例1同样的操作,得到热处理用粉末。将该热处理用粉末装入管状炉中,在氢气4体积%和氮气96体积%的混合气环境下以升温速度10℃/min加热到900℃,在900℃保持3小时,经自然冷却,得到催化剂(4)。催化剂(4)的BET比表面积和元素分析结果如表1所示。此外,除将催化剂(1)变为催化剂(4)变为以外,进行与实施例1同样的操作,得到燃料电池用电极(4),评价其氧还原性能。结果如表1所示。[实施例5]<硫酸钛-甘氨酸-铁>除将甘氨酸11.1g变为甘氨酸(和光纯药工业(株)、纯度:99%)11.1g和乙酸铁(II)(Aldrich公司制、纯度:95%)0.202g以外,进行与实施例4同样的操作,得到催化剂(5)。催化剂(5)的BET比表面积和元素分析结果如表1所示。此外,除将催化剂(1)变为催化剂(5)以外,进行与实施例1同样的操作,得到燃料电池用电极(5),评价其氧还原性能。结果如表1所示。[实施例6]<硫酸钛-甘氨酸-铁>除将热处理温度变为500℃以外,进行与实施例5同样的操作,得到催化剂(6)。催化剂(6)的BET比表面积和元素分析结果如表1所示。此外,除将催化剂(1)变为催化剂(6)以外,进行与实施例1同样的操作,得到燃料电池用电极(6),评价其氧还原性能。结果如表1所示。[实施例7]<硫酸钛-甘氨酸-铁>除将热处理温度变为1200℃以外,进行与实施例5同样的操作,得到催化剂(7)。催化剂(7)的BET比表面积和元素分析结果如表1所示。此外,除将催化剂(1)变为催化剂(7)以外,进行与实施例1同样的操作,得到燃料电池用电极(7),评价其氧还原性能。结果如表1所示。[实施例8]<硫酸钛-葡萄糖>除将聚乙烯基吡咯烷酮0.85g变为D(+)-葡萄糖(和光纯药工业(株)、纯度:98%)1.40g以外,进行与实施例1同样的操作,得到催化剂(8)。催化剂(8)的BET比表面积和元素分析结果如表1所示。此外,除将催化剂(1)变为催化剂(8)以外,进行与实施例1同样的操作,得到燃料电池用电极(8),评价其氧还原性能。结果如表1所示。[实施例9]<硫酸钛-聚乙烯醇>除将聚乙烯基吡咯烷酮0.85g变为聚乙烯醇(关东化学(株)、纯度:78%、聚合度n=2000)1.01g以外,进行与实施例1同样的操作,得到催化剂(9)。催化剂(9)的BET比表面积和元素分析结果如表1所示。此外,除将催化剂(1)变为催化剂(9)以外,进行与实施例1同样的操作,得到燃料电池用电极(9),评价其氧还原性能。结果如表1所示。[实施例10]<硝酸氧锆-甘氨酸-铁>除将30%硫酸钛(IV)水溶液9.12g变为硝酸氧锆·二水和物(和光纯药工业(株)、纯度:97%)1.51g以外,进行与实施例5同样的操作,得到催化剂(10)。催化剂(10)的BET比表面积和元素分析结果如表1所示。此外,除将催化剂(1)变为催化剂(10)以外,进行与实施例1同样的操作,得到燃料电池用电极(10),评价其氧还原性能。结果如表1所示。[实施例11]<乙醇铌-甘氨酸-铁>除将30%硫酸钛(IV)水溶液9.12g变为五乙醇铌(V)(和光纯药工业(株)、纯度:99.9%)1.72g、且将溶剂从水变为乙醇以外,进行与实施例5同样的操作,得到催化剂(11)。催化剂(11)的BET比表面积和元素分析结果如表1所示。此外,除将催化剂(1)变为催化剂(11)以外,进行与实施例1同样的操作,得到燃料电池用电极(11),评价其氧还原性能。结果如表1所示。[比较例1]将氧化钛(产品名スーパータイタニアF-6、昭和电工(株)、锐钛型、BET比表面积100m2/g)2g和碳黑(VulcanXC72Cabot社)0.75g在研钵中充分混合,装入管状炉,在氢气4体积%和氮气96体积%的混合气环境下以升温速度10℃/min加热到1700℃,在1700℃保持3小时,经自然冷却而得到粉末状的催化剂(c1)。催化剂(c1)的BET比表面积和元素分析结果如表1所示。此外,除将催化剂(1)变为催化剂(c1)以外,进行与实施例1同样的操作,得到燃料电池用电极(c1),评价其氧还原性能。结果如表1所示。[比较例2]除将含凝胶状物质的液20ml变为无定形氧化钛(和光纯药工业(株)、无定形、气相合成(bythevaporphasemethod))1.18g以外,进行与实施例4同样的操作,得到催化剂(c2)。催化剂(c2)的BET比表面积和元素分析结果如表1所示。此外,除将催化剂(1)变为催化剂(c2)以外,进行与实施例1同样的操作,得到燃料电池用电极(c2),评价其氧还原性能。结果如表1所示。[比较例3]将比较例1中得到的所述催化剂(c1)0.30g在氧气1体积%、氢气4体积%、氮气95体积%的混合气中加热10小时,从而得到粉末状的催化剂(c3)。催化剂(c3)的BET比表面积和元素分析结果如表1所示。此外,除将催化剂(1)变为催化剂(c3)以外,进行与实施例1同样的操作,得到燃料电池用电极(c3),评价其氧还原性能。结果如表1所示。[比较例4]在容器内将氢氧化锆(東ソー、TZ-0、BET值:13m2/g)3g、市售的聚乙烯醇(クラレ(株)公司制、ポバール117)1.5g溶解在4g水中,然后将它们连同容器一起导入到设定在60℃的热风循环型干燥机中,进行水分的除去。将得到的材料中的1.2g放入氧化铝槽中,在氮气流通下以200ml/分的流量流通,以升温速度150℃/小时从室温(约25℃)升温到800℃,在相同温度下保持3小时,从而得到催化剂(c4)。催化剂(c4)的BET比表面积和元素分析结果如表1所示。此外,除将催化剂(1)变为催化剂(c4)以外,进行与实施例1同样的操作,得到燃料电池用电极(c4),评价其氧还原性能。结果如表1所示。[比较例5]<硫酸钛-甘氨酸-铁>除将热处理温度变为400℃以外,进行与实施例5同样的操作,得到催化剂(c5)。催化剂(c5)的BET比表面积和元素分析结果如表1所示。此外,除将催化剂(1)变为催化剂(c5)以外,进行与实施例1同样的操作,得到燃料电池用电极(c5),评价其氧还原性能。结果如表1所示。[比较例6]<硫酸钛-甘氨酸-铁>除将热处理温度变为1300℃以外,进行与实施例6同样的操作,得到催化剂(c6)。催化剂(c6)的BET比表面积和元素分析结果如表1所示。此外,除将催化剂(1)变为催化剂(c6)以外,进行与实施例1同样的操作,得到燃料电池用电极(c6),评价其氧还原性能。结果如表1所示。[表1]