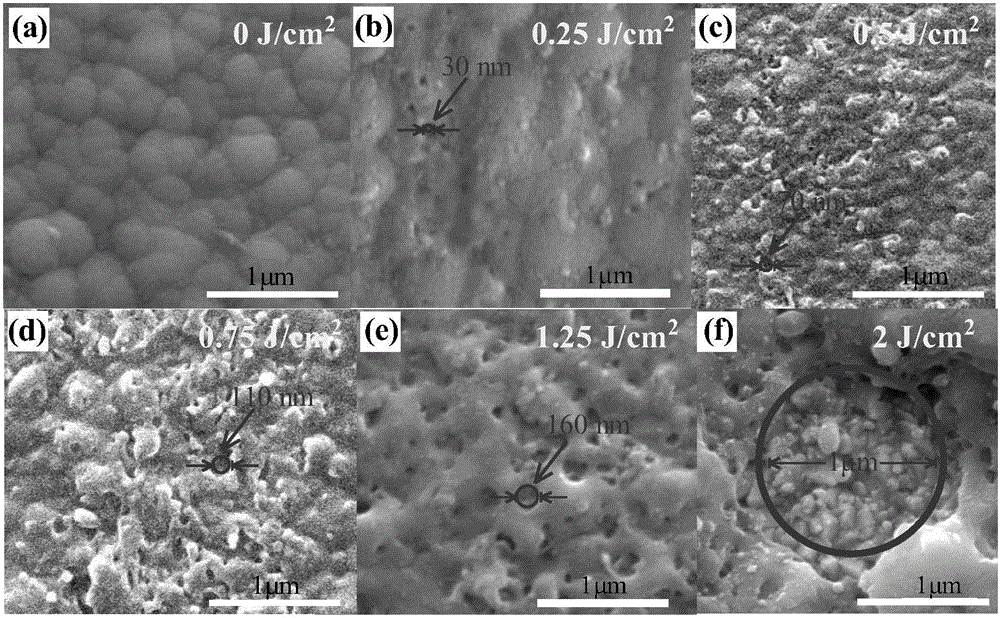
本发明涉及纳米材料制备
技术领域:
,尤其涉及一种通过飞秒激光脉冲刻蚀方法制备太阳能电池表面减反射层以增强非晶硅薄膜太阳能(a-SiTFSCs)电池性能的方法。
背景技术:
:目前环境污染和传统能源(包括石油、煤和天然气)短缺,成为限制世界各国经济发展的两大难题。太阳能电池作为一种可以把太阳辐射光能直接转化为电能的装置,在光电转化过程中,既不需要消耗传统能源,同时,也完全没有环境污染物产生,是一种非常有前景的光电半导体转化器件。目前各国正在研究的太阳能电池类型主要有硅基太阳能电池、薄膜太阳能电池、多元化合物太阳能电池(如CdS/CdTe、Cu(In,Ga)Se2/CdS等),以及有机染料敏化太阳能电池等。综合考虑能量转换效率和使用寿命等性能,非晶硅太阳能电池虽然转换效率略低,但成本更低廉,因而成为更有发展前途的新型硅基太阳能电池。目前情形,p-i-n结构的非晶硅薄膜太阳能电池耗材更少,且光电转化效率相对较高的特点,决定了它仍是薄膜太阳能电池的主流。当前,如何进一步提高非晶硅薄膜太阳能电池的光电转换效率(η)仍是该领域亟待研究的问题之一。到目前为止,通过硅基太阳能电池硅膜表面“光俘获”增强光吸收的方法,主要包括减反射吸收层绒面的制备、贵金属纳米粒子等离激元共振增强光吸收和金属狭缝非局域等离激元增强光吸收等。制备减反射层绒面相对于等离激元增强薄膜电池表面光吸收而言,具有制作工艺简单成熟,性能相对稳定,造价低廉等优势。PythonM等人通过化学气相沉积(LP-CVD)的方法在微晶硅太阳电池硅表面上形成“V型”和“U型”绒面结构使电池的反向饱和电流有显著增加,并且Voc(open-circuitvoltage,开路电压)和FF(fillfactor,填充因子)也有明显提高。Sandeep等人通过高温退火的方式,在半导体硅材料表面成功制备了“倒金字塔型”绒面结构,使得硅表面光吸收性能得到显著提升。然而,上述减反射层绒面制备方法,并不适应于吸收层厚度仅为1-2μm的非晶硅薄膜太阳能电池。Maliheh等人采用纳秒Nd:YAG激光脉冲辐照条件下,诱导抛光硅表面“树突状”光俘获微纳结构的形成,进而达到减反射的目的。激光微纳加工技术以其加工过程简单、制备精度高、以及精确操控性强等优势,日益受到人们关注。技术实现要素:本发明所要解决的技术问题是提供一种制备工艺简单,成本低廉,光电转换性能提高显著,且没有任何污染物的飞秒激光刻蚀增强非晶硅薄膜太阳能电池性能的方法。本发明的技术解决方案是:一种飞秒激光刻蚀增强非晶硅薄膜太阳能电池性能的方法,其具体步骤如下:将p-i-n结构非晶硅薄膜太阳能电池,固定于飞秒激光微纳加工平台,飞秒激光脉冲经10倍物镜(数值孔径为0.25)的显微镜系统垂直入射,聚焦在薄膜太阳能电池n型非晶硅膜表面上;设置飞秒激光脉冲能量密度为0.5J/cm2~1.25J/cm2和激光脉冲刻蚀周期间隔为8μm~30μm,线偏振飞秒激光脉冲将对非晶硅薄膜太阳能电池n型非晶硅膜表面上进行绒化处理,得到高效的p-i-n结构非晶硅薄膜太阳能电池。进一步的,飞秒激光微纳加工平台,移动速率为1mm/s恒速移动,平台电机步进精度为0.1μm。进一步的,飞秒激光脉冲能量密度(W)为0.75J/cm2;激光脉冲刻蚀周期间隔(T)为15μm。进一步的,所述飞秒激光脉冲经10倍物镜的数值孔径为0.25。进一步的,所述p-i-n结构非晶硅薄膜太阳能电池的制备步骤如下:1.1、制备TCO层首先,通过射频磁控溅射方法在玻璃基底一侧溅射厚度为200nm由SnO2构成的TCO层;1.2、制备p型非晶硅半导体通过等离子体增强化学气相沉积方法,在TCO层上面沉积厚度为600nm的p型非晶硅半导体;1.3、制备i型非晶硅半导体在p型非晶硅半导体层上面,通过等离子体增强化学气相沉积方法,沉积厚度为600nm的i型非晶硅半导体;1.4、制备n型非晶硅半导体在i型非晶硅半导体层上面,还是通过等离子体增强化学气相沉积方法,沉积厚度为600nm的n型非晶硅半导体;1.5、制作铝电极通过真空蒸镀的方式,在制备的p-i-n结构非晶硅薄膜太阳能电池顶部,制作铝电极,得到p-i-n结构非晶硅薄膜太阳能电池。进一步的,制备TCO层时,将In2O3-SnO2陶瓷靶放置于磁控溅射镀膜系统内,将清洗干净的玻璃基底水平放置于衬底座的中心位置,封闭反应室,进行溅射镀膜;其中,溅射腔的真空度为10-2Pa,通入纯度为99.99%的氩气作为反应气体,氩气流速为15.3sccm,衬底温度为300℃,溅射功率为600W,In2O3-SnO2陶瓷靶溅射电压为-110V,溅射时间为20分钟,沉积速率10nm/min。进一步的,制备p型非晶硅半导体时,将表面沉积TCO导电层的玻璃基底水平放置于磁控溅射镀膜系统衬底座的中心位置,封闭反应室,进行增强化学气相沉积;其中,反应室真空度为10-5Pa,衬底温度为250℃,向反应室内通入SiH4、B2H6和H2,SiH4、B2H6和H2的流速分别为6sccm、4sccm和20sccm,沉积时气压控制在80Pa,射频功率为160W,溅射时间为15分钟,沉积速率40nm/min。进一步的,制备i型非晶硅半导体时,将最上表面沉积p型非晶硅半导体玻璃基底水平放置于磁控溅射镀膜系统衬底座的中心位置,封闭反应室;其中,反应室真空度为10-5Pa,衬底温度为350℃,向反应室内通入SiH4和H2,SiH4和H2的流速分别为6sccm和24sccm,沉积时气压控制在80Pa,射频功率为160W,溅射时间为15分钟,沉积速率40nm/min。进一步的,制备n型非晶硅半导体时,将最上表面沉积i型非晶硅半导体玻璃基底水平放置于磁控溅射镀膜系统衬底座的中心位置,封闭反应室;其中,反应室真空度为10-5Pa,衬底温度为300℃;通入SiH4、PH3和H2,SiH4、PH3和H2的流速分别为6sccm、4sccm和20sccm,沉积时气压控制在80Pa,射频功率为160W,溅射时间为15分钟,沉积速率40nm/min。本发明的有益效果:1、极短的脉冲持续时间(10-15s),使得飞秒激光脉冲与非晶硅薄膜太阳能电池相互作用过程中,基本上不需要考虑流体动力学过程的影响。激光能量直接沉积在硅膜固体密度的趋肤层内,使能量的吸收更为集中,大大降低了材料的烧蚀阈值。再加上光与物质相互作用时间的缩短,热传导作用的热效应体积大大减少,当激光能流密度被调整到等于或刚刚超过硅膜半导体材料的烧蚀阈值时,材料中的热影响区实际上比聚焦会更小,这不仅极大的提高了加工的精度,同时也实现了真正意义上的“冷”加工;2、基于飞秒激光微纳加工技术加工精度高、热效应小和损伤阈值低的特点,以及聚焦飞秒激光脉冲附近具有超高电场强度,能够诱导多光子吸收、离子化等非线性效应;飞秒激光脉冲刻蚀非晶硅薄膜太阳能电池时,主要是以蒸发汽化的方式进行,半导体材料熔化、液相流动以及再凝结等过程的影响被大大减小,甚至可以忽略,使得表面绒化非晶硅太阳能电池的表面更为平整和光滑,提高了微纳加工过程的可控性和精密性;3、操作过程简单,全程自动化,通过预先设定激光微纳加工系统的刻蚀参数,激光脉冲能量和刻蚀周期间隔,在半导体材料表面,精确、灵活的诱导形成周期性微结构;4、通过飞秒激光微纳加工,制备的非晶硅薄膜太阳能电池表面减反射层,光吸收增强效果明显,得到的太阳能电池光电转换效率达到14.9%,是未经处理非晶硅薄膜太阳能电池转换效率的2倍。附图说明图1(a)是本发明制备的p-i-n非晶硅薄膜太阳能电池结构以及(b)飞秒激光刻蚀电池表面“凹槽”结构SEM照片;图2(a)-(f)是本发明(实施例1-实施例3、对比例1-对比例3)未经飞秒激光刻蚀(0J/cm2)和不同激光脉冲能量刻蚀(0.25J/cm2、0.5J/cm2、0.75J/cm2、1.25J/cm2、2J/cm2)a-SiTFSCs表面凹槽内诱导多孔微结构SEM照片;图3是本发明(对比例2)飞秒激光脉冲能量为2J/cm2时,a-SiTFSCs硅膜表面XRD图谱;图4是本发明(实施例1-实施例3、对比例1-对比例3)相同刻蚀周期间隔,不同飞秒激光脉冲刻蚀能量(0J/cm2、0.25J/cm2、0.5J/cm2、0.75J/cm2、1.25J/cm2、2J/cm2)a-SiTFSCs的I-V特性测试;图5是本发明(实施例1-实施例3、对比例1-对比例3)a-SiTFSCs的η与飞秒激光脉冲刻蚀能量的变化关系;图6是本发明(实施例1-实施例3、对比例1-对比例3)相同刻蚀周期间隔,不同飞秒激光脉冲刻蚀能量(0J/cm2、0.25J/cm2、0.5J/cm2、0.75J/cm2、1.25J/cm2)a-SiTFSCs的紫外-可见反射吸收谱;图7是本发明(实施例4-实施例6、对比例4、对比例5)相同飞秒激光脉冲W,不同刻蚀周期T(5μm、8μm、15μm、30μm、50μm)a-SiTFSCs的表面绒化SEM图片;图8是本发明(实施例4-实施例6、对比例4、对比例5)相同飞秒激光脉冲能量W,不同激光脉冲刻蚀周期T(0μm、5μm、8μm、15μm、30μm、50μm)a-SiTFSCs的I-V特性测试;图9是本发明(实施例4-实施例6、对比例4、对比例5)表面绒化a-SiTFSCs的η与飞秒激光脉冲刻蚀周期间隔的变化关系。具体实施方式本发明的飞秒激光微纳加工平台采用的激光器为商业化集成再生放大Ti:sapphire飞秒激光系统(CoherentInc.),包括显微镜聚焦系统(Nikon,SonyInc.)和精密微加工平台(PriorInc.)。飞秒激光经OPA(光参量放大器)系统后,最终可以输出脉冲FWHM(半值宽度)为120fs,中心波长为800nm的脉冲序列,可调谐重复频率1Hz~1kHz,峰值能量30J/cm2,光斑直径约为6mm;飞秒激光脉冲刻蚀能量可通过调谐衰减片进行调节,从而实现0~30J/cm2连续输出,所有飞秒激光微纳加工试验均在千级净化超净环境中完成。实施例如图2所示,飞秒激光脉冲绒面刻蚀周期T为一定值,改变飞秒激光脉冲能量W,制备非晶硅薄膜太阳能电池表面多孔微结构减反射层方法如下:1.1、将非晶硅薄膜太阳能电池黏附到载玻片上,然后将其固定到飞秒激光微纳加工平台上平台电机步进精度为0.1μm,太阳能电池尺寸大小1.5×1.5cm2;1.2、飞秒激光脉冲经10×物镜(数值孔径为0.25)的显微镜系统垂直入射聚焦在薄膜太阳能电池n型非晶硅膜表面上,形成束腰半径约为0.5μm的光斑;1.3、通过计算机终端控制,聚焦的飞秒激光脉冲将以1mm/s的速率沿平台竖直方向恒速移动,设置飞秒激光脉冲重复频率为1kHz,同时设置非晶硅薄膜太阳能电池相同飞秒激光脉冲刻蚀周期T为15μm,不同激光脉冲能量W(0.25J/cm2、0.5J/cm2、0.75J/cm2、1.25J/cm2、2J/cm2)的微加工参数,线偏振飞秒激光脉冲将对非晶硅薄膜太阳能电池n型非晶硅膜表面上进行绒化处理,得到高效的p-i-n结构非晶硅薄膜太阳能电池。对比例11.1、制备TCO层首先,通过射频磁控溅射方法,在玻璃基底上溅射厚度为200nm由SnO2构成的TCO导电层,玻璃基底面积为1.5×1.5cm2;a.将In2O3-SnO2陶瓷靶放置于磁控溅射镀膜系统内,清洗干净的玻璃基底水平放置于衬底座中心位置,封闭反应室;b.通过真空抽气系统,将反应室真空度抽至10-2Pa,同时设置衬底温度为300℃;c.向反应室内通入氩气,氩气流速为15.3sccm,压力稳定后打开射频系统,进行辉光放电溅射,射频功率为600W,In2O3-SnO2陶瓷靶溅射电压为-110V,溅射时间为20分钟,沉积速率10nm/min;d.TCO薄膜沉积结束后,关闭氩气气路、射频电源和加热装置,冷却至室温后,打开反应室取出;1.2、制备p型非晶硅半导体通过等离子体增强化学气相沉积方法,在TCO导电层上面沉积厚度约为600nm的p型非晶硅半导体;a.将表面沉积TCO导电层的玻璃基底水平放置于磁控溅射镀膜系统衬底座的中心位置,封闭反应室;b.通过真空抽气系统,将反应室真空度抽至10-5Pa,同时设置衬底温度为250℃;c.打开电磁截止阀向反应室内通入SiH4、B2H6和H2,其流速分别为6sccm、4sccm和20sccm,气压稳定为80Pa,打开射频系统进行辉光放电溅射,射频功率为160W,溅射时间为15分钟,沉积速率40nm/min;d.薄膜沉积结束后,关闭SiH4和B2H6气路、射频电源和加热装置,保持通H2直至冷却至室温后,然后关闭H2气路,打开反应室取出;1.3、制备i型非晶硅半导体在p型非晶硅半导体层上面,通过等离子体增强化学气相沉积的方法,制备厚度约为600nm的i型非晶硅半导体;a.将最上表面沉积p型非晶硅半导体玻璃基底水平放置于磁控溅射镀膜系统衬底座的中心位置,封闭反应室;b.通过真空抽气系统,将反应室真空度抽至10-5Pa,同时设置衬底温度为350℃;c.打开电磁截止阀向反应室内通入SiH4和H2,其流速分别为6sccm和24sccm,气压稳定为80Pa,打开射频系统进行辉光放电溅射,射频功率为160W,溅射时间为15分钟,沉积速率40nm/min;d.薄膜沉积结束后,关闭SiH4气路、射频电源和加热装置,保持通H2直至冷却至室温后,然后关闭H2气路,打开反应室取出;1.4、制备n型非晶硅半导体在i型非晶硅半导体层上面,还是通过等离子体增强化学气相沉积的方法,沉积厚度约为600nm的n型非晶硅半导体;a.将最上表面沉积i型非晶硅半导体玻璃基底水平放置于磁控溅射镀膜系统衬底座的中心位置,封闭反应室;b.通过真空抽气系统,将反应室真空度抽至10-5Pa,同时设置衬底温度为300℃;c.打开电磁截止阀向反应室内通入SiH4、PH3和H2,其流速分别为6sccm、4sccm和20sccm,气压稳定为80Pa,打开射频系统进行辉光放电溅射,射频功率为160W,溅射时间为15分钟,沉积速率40nm/min;d.薄膜沉积结束后,关闭SiH4和PH3气路、射频电源和加热装置,保持通H2直至冷却至室温后,然后关闭H2气路,打开反应室取出;1.5、制作铝电极通过真空蒸镀的方式,在制备的p-i-n结构非晶硅薄膜太阳能电池顶部,制作铝电极,得到p-i-n结构非晶硅薄膜太阳能电池。该非晶硅薄膜太阳能电池a-SiTFSCs表面SEM图如图2(a)所示。实施例11.1、将对比例1制备的非晶硅薄膜太阳能电池黏附到载玻片上,然后将其固定到飞秒激光微纳加工平台上平台电机步进精度为0.1μm,太阳能电池尺寸大小1.5×1.5cm2;1.2、飞秒激光脉冲经10×物镜(数值孔径为0.25)的显微镜系统垂直入射聚焦在薄膜太阳能电池n型非晶硅膜表面上,形成束腰半径约为0.5μm的光斑;1.3、通过计算机终端控制,聚焦的飞秒激光脉冲将以1mm/s的速率沿平台竖直方向恒速移动,设置飞秒激光脉冲重复频率为1kHz,同时设置非晶硅薄膜太阳能电池飞秒激光脉冲刻蚀周期T为15μm,激光脉冲能量(W)0.5J/cm2的微加工参数,线偏振飞秒激光脉冲将对非晶硅薄膜太阳能电池n型非晶硅膜表面上进行绒化处理,得到高效的p-i-n结构非晶硅薄膜太阳能电池。该非晶硅薄膜太阳能电池a-SiTFSCs表面凹槽内诱导多孔微结构SEM图如图2(c)所示。实施例21.1、将对比例1制备的非晶硅薄膜太阳能电池黏附到载玻片上,然后将其固定到飞秒激光微纳加工平台上平台电机步进精度为0.1μm,太阳能电池尺寸大小1.5×1.5cm2;1.2、飞秒激光脉冲经10×物镜(数值孔径为0.25)的显微镜系统垂直入射聚焦在薄膜太阳能电池n型非晶硅膜表面上,形成束腰半径约为0.5μm的光斑;1.3、通过计算机终端控制,聚焦的飞秒激光脉冲将以1mm/s的速率沿平台竖直方向恒速移动,设置飞秒激光脉冲重复频率为1kHz,同时设置非晶硅薄膜太阳能电池飞秒激光脉冲刻蚀周期T为15μm,激光脉冲能量(W)0.75J/cm2的微加工参数,线偏振飞秒激光脉冲将对非晶硅薄膜太阳能电池n型非晶硅膜表面上进行绒化处理,得到高效的p-i-n结构非晶硅薄膜太阳能电池。该非晶硅薄膜太阳能电池a-SiTFSCs表面凹槽内诱导多孔微结构SEM图如图2(d)所示,a-SiTFSCs表面绒化SEM图如图7(c)所示。实施例31.1、将对比例1制备的非晶硅薄膜太阳能电池黏附到载玻片上,然后将其固定到飞秒激光微纳加工平台上平台电机步进精度为0.1μm,太阳能电池尺寸大小1.5×1.5cm2;1.2、飞秒激光脉冲经10×物镜(数值孔径为0.25)的显微镜系统垂直入射聚焦在薄膜太阳能电池n型非晶硅膜表面上,形成束腰半径约为0.5μm的光斑;1.3、通过计算机终端控制,聚焦的飞秒激光脉冲将以1mm/s的速率沿平台竖直方向恒速移动,设置飞秒激光脉冲重复频率为1kHz,同时设置非晶硅薄膜太阳能电池飞秒激光脉冲刻蚀周期T为15μm,激光脉冲能量(W)1.25J/cm2的微加工参数,线偏振飞秒激光脉冲将对非晶硅薄膜太阳能电池n型非晶硅膜表面上进行绒化处理,得到高效的p-i-n结构非晶硅薄膜太阳能电池。该非晶硅薄膜太阳能电池a-SiTFSCs表面凹槽内诱导多孔微结构SEM图如图2(e)所示。对比例21.1、将对比例1制备的非晶硅薄膜太阳能电池黏附到载玻片上,然后将其固定到飞秒激光微纳加工平台上平台电机步进精度为0.1μm,太阳能电池尺寸大小1.5×1.5cm2;1.2、飞秒激光脉冲经10×物镜(数值孔径为0.25)的显微镜系统垂直入射聚焦在薄膜太阳能电池n型非晶硅膜表面上,形成束腰半径约为0.5μm的光斑;1.3、通过计算机终端控制,聚焦的飞秒激光脉冲将以1mm/s的速率沿平台竖直方向恒速移动,设置飞秒激光脉冲重复频率为1kHz,同时设置非晶硅薄膜太阳能电池飞秒激光脉冲刻蚀周期T为15μm,激光脉冲能量(W)0.25J/cm2的微加工参数,线偏振飞秒激光脉冲将对非晶硅薄膜太阳能电池n型非晶硅膜表面上进行绒化处理,得到高效的p-i-n结构非晶硅薄膜太阳能电池。该非晶硅薄膜太阳能电池a-SiTFSCs表面凹槽内诱导多孔微结构SEM图如图2(b)所示。对比例31.1、将对比例1制备的非晶硅薄膜太阳能电池黏附到载玻片上,然后将其固定到飞秒激光微纳加工平台上平台电机步进精度为0.1μm,太阳能电池尺寸大小1.5×1.5cm2;1.2、飞秒激光脉冲经10×物镜(数值孔径为0.25)的显微镜系统垂直入射聚焦在薄膜太阳能电池n型非晶硅膜表面上,形成束腰半径约为0.5μm的光斑;1.3、通过计算机终端控制,聚焦的飞秒激光脉冲将以1mm/s的速率沿平台竖直方向恒速移动,设置飞秒激光脉冲重复频率为1kHz,同时设置非晶硅薄膜太阳能电池飞秒激光脉冲刻蚀周期T为15μm,激光脉冲能量(W)2J/cm2的微加工参数,线偏振飞秒激光脉冲将对非晶硅薄膜太阳能电池n型非晶硅膜表面上进行绒化处理,得到高效的p-i-n结构非晶硅薄膜太阳能电池。该非晶硅薄膜太阳能电池a-SiTFSCs表面凹槽内诱导多孔微结构SEM图如图2(f)所示,a-SiTFSCs表面绒化SEM图如图12所示,a-SiTFSCs硅膜表面XRD图谱如图3所示。图4为本发明实施例1-实施例3、对比例1-对比例3的表面绒化非晶硅薄膜太阳能电池I-V特性测试曲线,图5是本发明实施例1-实施例3、对比例1-对比例3使用相同飞秒激光刻蚀周期T,不同飞秒激光脉冲刻蚀能量W(0J/cm2、0.25J/cm2、0.5J/cm2、0.75J/cm2、1.25J/cm2)a-SiTFSCs的η与飞秒激光脉冲刻蚀能量的变化关系;图6是本发明实施例1-实施例3、对比例1-对比例3使用相同飞秒激光刻蚀周期T,不同飞秒激光脉冲刻蚀能量W(0J/cm2、0.25J/cm2、0.5J/cm2、0.75J/cm2、1.25J/cm2)非晶硅薄膜太阳能电池紫外-可见反射吸收谱。由图2可以看出,随着飞秒激光脉冲能量(W)的增加,由于a-SiTFSCs表面诱导形成多孔微结构的孔径逐渐增大,使得太阳能电池n型非晶硅薄膜表面的反射光谱强度逐渐降低,从而非晶硅薄膜太阳能电池的“光诱捕”能力逐渐增强。这充分验证了通过飞秒激光微纳加工平台,可以制备高效太阳能电池表面减反射层。表1为本发明实施例1-实施例3、对比例1-3的相同飞秒激光脉冲刻蚀周期T,不同飞秒激光脉冲能量W(0J/cm2、0.25J/cm2、0.5J/cm2、0.75J/cm2、1.25J/cm2、2J/cm2)对非晶硅薄膜太阳能电池刻蚀处理前后的光电转换效率;表1W(J/cm2)Jsc(mA/cm2)Voc(V)FFη(%)对比例100.510.870.188.0实施例10.50.650.930.2012.1实施例20.750.810.970.1914.9实施例31.250.710.950.1912.8对比例20.250.610.910.1810.0对比例3200--通过图4和表1,可以清楚的观察到,未经飞秒激光脉冲表面绒化处理非晶硅薄膜太阳能电池的光电转换效率为8.0%;当激光脉冲能量W增加为0.75J/cm2时,非晶硅薄膜太阳能电池的光电转换效率达到最大值14.9%,近乎是未经飞秒激光脉冲表面绒化处理太阳能电池转换效率的两倍。这充分说明,通过飞秒激光微纳加工技术,能够使非晶硅薄膜太阳能电池的表面绒化,增强非晶硅薄膜太阳能电池表面“光诱捕”能力,进而提高太阳能电池的光电转换效率。实施例制备非晶硅薄膜太阳能电池表面多孔微结构减反射层方法如下:1.1、将非晶硅薄膜太阳能电池黏附到载玻片上,然后将其固定到飞秒激光微纳加工平台上平台电机步进精度为0.1μm,太阳能电池尺寸大小1.5×1.5cm2;1.2、飞秒激光脉冲经10×物镜(数值孔径为0.25)的显微镜系统垂直入射聚焦在薄膜太阳能电池n型非晶硅膜表面上,形成束腰半径约为0.5μm的光斑;1.3、通过计算机终端控制,聚焦的飞秒激光脉冲将以1mm/s的速率沿平台竖直方向恒速移动,设置飞秒激光脉冲重复频率为1kHz,同时设置非晶硅薄膜太阳能电池相同飞秒激光脉冲能量W为0.75J/cm2,不同飞秒激光脉冲刻蚀周期T(5μm、8μm、15μm、30μm、50μm)的微加工参数,线偏振飞秒激光脉冲将对非晶硅薄膜太阳能电池n型非晶硅膜表面上进行绒化处理,得到高效的p-i-n结构非晶硅薄膜太阳能电池。如图7所示,飞秒激光脉冲能量(W)为一定值,改变飞秒激光脉冲刻蚀周期T的的表面绒化SEM图。实施例41.1、将对比例1制备的非晶硅薄膜太阳能电池黏附到载玻片上,然后将其固定到飞秒激光微纳加工平台上平台电机步进精度为0.1μm,太阳能电池尺寸大小1.5×1.5cm2;1.2、飞秒激光脉冲经10×物镜(数值孔径为0.25)的显微镜系统垂直入射聚焦在薄膜太阳能电池n型非晶硅膜表面上,形成束腰半径约为0.5μm的光斑;1.3、通过计算机终端控制,聚焦的飞秒激光脉冲将以1mm/s的速率沿平台竖直方向恒速移动,设置飞秒激光脉冲重复频率为1kHz,同时设置非晶硅薄膜太阳能电池飞秒激光脉冲能量(W)为0.75J/cm2,飞秒激光脉冲刻蚀周期(T)为8μm的微加工参数,线偏振飞秒激光脉冲将对非晶硅薄膜太阳能电池n型非晶硅膜表面上进行绒化处理,得到高效的p-i-n结构非晶硅薄膜太阳能电池。实施例51.1、将对比例1制备的非晶硅薄膜太阳能电池黏附到载玻片上,然后将其固定到飞秒激光微纳加工平台上平台电机步进精度为0.1μm,太阳能电池尺寸大小1.5×1.5cm2;1.2、飞秒激光脉冲经10×物镜(数值孔径为0.25)的显微镜系统垂直入射聚焦在薄膜太阳能电池n型非晶硅膜表面上,形成束腰半径约为0.5μm的光斑;1.3、通过计算机终端控制,聚焦的飞秒激光脉冲将以1mm/s的速率沿平台竖直方向恒速移动,设置飞秒激光脉冲重复频率为1kHz,同时设置非晶硅薄膜太阳能电池飞秒激光脉冲能量(W)为0.75J/cm2,飞秒激光脉冲刻蚀周期(T)为15μm的微加工参数,线偏振飞秒激光脉冲将对非晶硅薄膜太阳能电池n型非晶硅膜表面上进行绒化处理,得到高效的p-i-n结构非晶硅薄膜太阳能电池。实施例61.1、将对比例1制备的非晶硅薄膜太阳能电池黏附到载玻片上,然后将其固定到飞秒激光微纳加工平台上平台电机步进精度为0.1μm,太阳能电池尺寸大小1.5×1.5cm2;1.2、飞秒激光脉冲经10×物镜(数值孔径为0.25)的显微镜系统垂直入射聚焦在薄膜太阳能电池n型非晶硅膜表面上,形成束腰半径约为0.5μm的光斑;1.3、通过计算机终端控制,聚焦的飞秒激光脉冲将以1mm/s的速率沿平台竖直方向恒速移动,设置飞秒激光脉冲重复频率为1kHz,同时设置非晶硅薄膜太阳能电池飞秒激光脉冲能量(W)为0.75J/cm2,飞秒激光脉冲刻蚀周期(T)为30μm的微加工参数,线偏振飞秒激光脉冲将对非晶硅薄膜太阳能电池n型非晶硅膜表面上进行绒化处理,得到高效的p-i-n结构非晶硅薄膜太阳能电池。对比例41.1、将对比例1制备的非晶硅薄膜太阳能电池黏附到载玻片上,然后将其固定到飞秒激光微纳加工平台上平台电机步进精度为0.1μm,太阳能电池尺寸大小1.5×1.5cm2;1.2、飞秒激光脉冲经10×物镜(数值孔径为0.25)的显微镜系统垂直入射聚焦在薄膜太阳能电池n型非晶硅膜表面上,形成束腰半径约为0.5μm的光斑;1.3、通过计算机终端控制,聚焦的飞秒激光脉冲将以1mm/s的速率沿平台竖直方向恒速移动,设置飞秒激光脉冲重复频率为1kHz,同时设置非晶硅薄膜太阳能电池飞秒激光脉冲能量(W)为0.75J/cm2,飞秒激光脉冲刻蚀周期(T)为5μm的微加工参数,线偏振飞秒激光脉冲将对非晶硅薄膜太阳能电池n型非晶硅膜表面上进行绒化处理,得到高效的p-i-n结构非晶硅薄膜太阳能电池。对比例51.1、将对比例1制备的非晶硅薄膜太阳能电池黏附到载玻片上,然后将其固定到飞秒激光微纳加工平台上平台电机步进精度为0.1μm,太阳能电池尺寸大小1.5×1.5cm2;1.2、飞秒激光脉冲经10×物镜(数值孔径为0.25)的显微镜系统垂直入射聚焦在薄膜太阳能电池n型非晶硅膜表面上,形成束腰半径约为0.5μm的光斑;1.3、通过计算机终端控制,聚焦的飞秒激光脉冲将以1mm/s的速率沿平台竖直方向恒速移动,设置飞秒激光脉冲重复频率为1kHz,同时设置非晶硅薄膜太阳能电池飞秒激光脉冲能量(W)为0.75J/cm2,飞秒激光脉冲刻蚀周期(T)为50μm的微加工参数,线偏振飞秒激光脉冲将对非晶硅薄膜太阳能电池n型非晶硅膜表面上进行绒化处理,得到高效的p-i-n结构非晶硅薄膜太阳能电池。图8为本发明实施例4-实施例6、对比例4、对比例5的表面绒化非晶硅薄膜太阳能电池I-V特性测试曲线,图9是实施例4-实施例6、对比例4、对比例5的表面绒化a-SiTFSCs的η与飞秒激光脉冲刻蚀周期间隔的变化关系。表2为实施例4-实施例6、对比例4、对比例5的相同飞秒激光脉冲能量W,不同飞秒激光脉冲刻蚀周期T(5μm、8μm、15μm、30μm、50μm)对非晶硅薄膜太阳能电池刻蚀处理前后的光电转换效率;表2T(μm)Jsc(mA/cm2)Voc(V)FFη(%)对比例100.510.870.188.0实施例180.690.910.1811.3实施例2150.810.970.1914.9实施例3300.630.890.1810.1对比例450.460.850.187.0对比例5500.560.870.188.8通过图8和表2可以清楚的观察到,未经飞秒激光脉冲表面绒化处理非晶硅薄膜太阳能电池的光电转换效率为8.0%;经飞秒激光脉冲表面绒化的非晶硅薄膜太阳能电池转换效率,与飞秒激光脉冲刻蚀周期T的变化仍是呈非线性关系;当飞秒激光脉冲刻蚀周期T为5μm时,太阳能电池具有最小的转换效率为7.0%,甚至小于未经飞秒激光脉冲表面绒化处理太阳能电池的光电转换效率。当激光脉冲刻蚀周期T继续增大时,表面绒化处理非晶硅薄膜太阳能电池转换效率逐渐增大;当激光脉冲刻蚀周期T增大至15μm时,表面绒化处理非晶硅太阳能电池转化效率达到最大值14.9%;随着飞秒激光脉冲刻蚀周期T的继续增大,太阳能电池转换效率反而降低,最终,当飞秒激光脉冲刻蚀周期T增大至50μm时,表面绒化处理非晶硅薄膜太阳能电池的光电转换效率降低至8.8%。本发明利用飞秒激光微纳加工技术,在非晶硅薄膜太阳能电池n型硅膜表面进行“绒化”刻蚀处理,在扫描区域形成的“凹槽”结构内,诱导纳米级的晶态多孔微结构形成,这样纳米小孔的出现,能够依赖入射光的衍射效应,加强光量子在孔内的振荡,进而增加入射光在电池内部的光程,增大光与半导体的接触机率,提高非晶硅太阳能电池的“光俘获”能力,因此,飞秒激光脉冲非晶硅薄膜太阳能电池表面绒化,对提高太阳能电池光电转换效率是有益的。研究表明,飞秒激光脉冲刻蚀周期(T)和激光脉冲能量(W)的选取,对太阳能电池的开路电压、短路电流密度和光电转换效率特性有直接影响;当飞秒激光脉冲刻蚀周期间距为15μm,脉冲能量为0.75J/cm2时,太阳能电池光电转换效率达到14.9%,是未经激光刻蚀处理非晶硅薄膜太阳能电池转换效率的2倍。以上仅为本发明的具体实施例而已,并不用于限制本发明,对于本领域的技术人员来说,本发明可以有各种更改和变化。凡在本发明的精神和原则之内,所作的任何修改、等同替换、改进等,均应包含在本发明的保护范围之内。当前第1页1 2 3