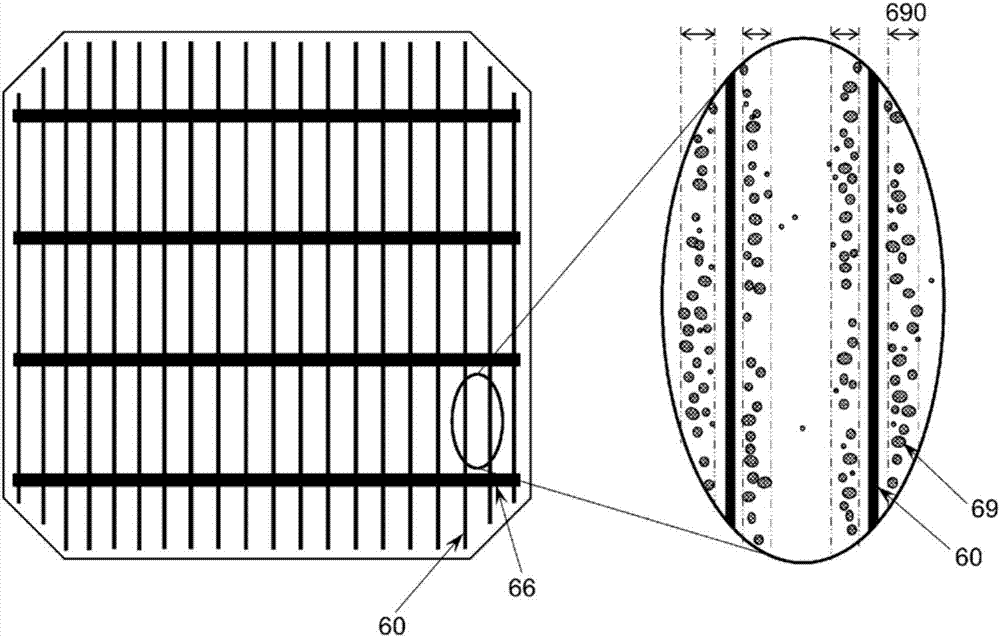
本发明涉及太阳能电池及其制造方法、以及太阳能电池模块。
背景技术:
:在太阳能电池中,通过将对具有半导体接合的光电转换部照射光而产生的载流子(电子及空穴)取出至外部电路,由此,进行发电。为了将光电转换部中产生的载流子有效地回收并取出至外部电路,在太阳能电池的受光面及背面侧的表面上设置金属集电极。例如,通过在导电型单晶硅基板表面上设置硅系薄膜而形成半导体接合的异质结太阳能电池中,通过在受光面侧及背面侧的硅系薄膜上设置由透明导电性氧化物等制成的透明电极,并在透明电极上设置金属集电极,从而回收晶体硅基板上产生的光载流子。到达形成金属集电极的区域的光被金属集电极反射或吸收,因此,产生阴影损失。为了降低阴影损失,使受光面侧的集电极形成为图案状。作为集电极的图案,典型性的是由叉指电极及汇流条电极构成的格栅图案。背面侧的集电极也可以设置于整个面,也可以设置成图案状。像平顶类型、地上设置类型那样,光也从背面侧入射的设置方式的太阳能电池模块中,在太阳能电池的背面侧设置图案状的集电极。另外,构成为用底层片使入射至相邻的电池间的光反射的太阳能电池模块也在背面侧设置图案状的集电极。图案状的集电极通常通过对银膏等导电性糊进行丝网印刷而形成。但是,使用银膏形成的集电极含有树脂材料,因此,电阻率高,材料成本也高。因此,为了降低电极材料成本等,提出了通过镀敷法形成金属集电极的方法。镀敷法可以形成厚度大且低电阻的金属电极,因此,与使用导电性糊的情况相比,可减小金属电极的线宽。因此,由镀敷法形成金属集电极在由阴影损失的降低带来的光摄入效率提高上也具有优点。作为通过镀敷法形成规定图案的集电极的方法,已知以下方法:在光电转换部的表面设置具有开口的绝缘层,使金属在开口形成部位的表面析出。例如,专利文献1中公开了一种方法:在光电转换部的透明电极上形成膜厚为10~15μm左右的绝缘层,绝缘层设置开口后,通过电解镀敷形成集电极。专利文献2及专利文献3中,提出了一种方法:在通过对含有低熔点材料的导电性糊进行印刷而形成的金属籽晶层上形成绝缘层后,通过加热进行退火,由此,使金属籽晶层内的低熔点材料进行热流动,在金属籽晶层上的绝缘层形成龟裂状的开口。该方法可以向金属籽晶层选择性地形成区域形成开口,不需要用抗蚀剂等进行绝缘层的图案化,因此,在材料成本及工艺成本的方面优异。现有技术文献专利文献专利文献1:wo2012/029847号国际公开小册子;专利文献2:wo2013/077038号国际公开小册子;专利文献3:wo2014/185537号国际公开小册子。技术实现要素:发明所要解决的课题如上所述,通过镀敷法形成金属集电极,由此,可减少电极面积并降低阴影损失。但是,为了减小电极面积而扩大相邻的叉指电极间的电极间隔时,存在载流子回收效率降低且太阳能电池的填充因子降低的倾向。因此,考虑阴影损失和载流子回收效率的平衡,决定电极的图案形状。通常,受光面侧的集电极以叉指电极的合计面积成为受光面整体的1~3%左右的方式,设定相邻电极间的间隔。为了进一步提高太阳能电池的转换效率,优选保持电极面积,同时降低阴影损失并提高光摄入效率。用于解决课题的方案本发明人等发现,通过在受光面侧未形成集电极的区域析出小面积的镀金属,尽管由金属导致的遮光面积增加,还是可以增大光摄入量。本发明的太阳能电池具备:包含半导体接合的光电转换部、设置于光电转换部的受光面的多个受光面叉指电极及设置于光电转换部的背面侧的多个背面叉指电极。优选受光面叉指电极的间隔距离比背面叉指电极的间隔距离大。光电转换部的受光面被第一绝缘层覆盖。受光面叉指电极具备第一金属籽晶层及第一镀金属层。第一金属籽晶层设置于光电转换部和第一绝缘层之间,第一金属籽晶层和第一镀金属层通过设置于第一绝缘层的开口导通。本发明的太阳能电池具有与受光面叉指电极及背面叉指电极的任一电极均不接触的独立镀金属层。独立镀金属密集区域以与受光面叉指电极的延伸方向平行的带状形状存在于第一绝缘层的表面。独立镀金属密集区域是独立镀金属层的面积密度为未形成受光面叉指电极区域整体平均值二倍以上的区域。优选独立镀金属密集区域以距受光面叉指电极间隔20μm以上的方式存在。优选光电转换部的背面由第二绝缘层覆盖,背面叉指电极具备第二金属籽晶层及第二镀金属层。第二金属籽晶层设置于光电转换部和第二绝缘层之间,第二金属籽晶层和第二镀金属层通过设置于第二绝缘层的开口导通。该方式中,优选第一绝缘层表面的独立镀金属层的面积密度比第二绝缘层表面的独立镀金属层的面积密度大。优选第一绝缘层及第二绝缘层均为无机层。优选第一绝缘层及第二绝缘层的膜厚为10~200nm。优选第一镀金属层、第二镀金属层及独立镀金属层均含有铜。本发明的太阳能电池的叉指电极通过以下方法得到:通过设置于金属籽晶上的绝缘层的开口,采用镀敷法在金属籽晶上形成镀金属层。在通过导电性糊的印刷形成金属籽晶层时,如果溶剂从导电性糊形成区域渗出,则在形成镀金属层时,容易在溶剂渗出区域的外缘附近的绝缘层上形成独立镀金属层。因此,独立镀金属密集区域形成为与叉指电极的延伸方向平行的带状。此外,本发明涉及具备所述太阳能电池的太阳能电池模块。本发明的太阳能电池模块具备设置于太阳能电池的受光面侧的受光面保护材料和设置于太阳能电池的背面侧的背面保护材料。在太阳能电池和受光面保护材料之间、及太阳能电池和背面保护材料之间具有密封材料。受光面保护材料透明,优选使用玻璃。背面保护材料可以透明,也可以不透明。背面保护材料优选使用不含有金属箔的材料。设置于太阳能电池和背面保护材料之间的密封材料优选含有聚烯烃树脂。发明的效果本发明的太阳能电池可以使由受光面侧的叉指电极反射的光在独立镀金属层散射,向光电转换部入射。因此,光摄入效率优异。附图说明图1是一实施方式的太阳能电池的示意性的截面图。图2是太阳能电池的受光面的俯视图。图3是太阳能电池的背面的俯视图。图4是一实施方式的太阳能电池模块的示意性的截面图。图5是实施例的太阳能电池的受光面的显微镜观察照片。图6是实施例的太阳能电池的背面的显微镜观察照片。附图标记说明10.硅基板;21、22.本征硅系薄膜;31、32.导电型硅系薄膜;41、42.透明电极层;81、82.绝缘层;50光电转换部;81、82.绝缘层;60、70.叉指电极;61、71.金属籽晶层;62、72.镀金属层;69.独立镀金属层;690.独立镀金属密集区域;100.太阳能电池;105.配线材料;111、112.密封材料;120、130.保护材料。具体实施方式图1是本发明一实施方式的异质结太阳能电池的示意性的截面图。如图1中示意性地表示,本发明的太阳能电池在光电转换部50的受光面侧具备多个受光面叉指电极60,在光电转换部50的背面侧具备多个背面叉指电极70。受光面叉指电极60从光电转换部50侧依次具备金属籽晶层61及镀金属层62。以下,以异质结太阳能电池为例子,更详细地说明本发明。异质结太阳能电池是通过在导电型单晶硅基板表面设置间隙与单晶硅不同的硅系薄膜而形成半导体接合的晶体硅太阳能电池。已知通过在用于形成扩散电位的导电型硅系薄膜31、32和导电型单晶硅基板10之间隔着本征硅系薄膜21、22,导电型单晶硅基板10的表面缺陷被终止,转换效率提高。[光电转换部的构成](硅基板)作为导电型单晶硅基板10,也可以使用n型单晶硅基板和p型单晶硅基板的任一种。从硅基板内的载流子寿命的长度来看,优选使用n型单晶硅基板。(硅系薄膜)在导电型单晶硅基板10的第一主面上(受光面侧)设置第一导电型硅系薄膜31,在第二主面上(背面侧)设置第二导电型硅系薄膜。第一导电型硅系薄膜31和第二导电型硅系薄膜32具有不同的导电型,一方为p型,另一方为n型。作为这些导电型硅系薄膜31、32,可使用p型硅系薄膜及n型硅系薄膜。导电型硅系薄膜的膜厚优选为20nm以下,更优选为15nm以下。从良好地保持制膜的覆盖率方面来看,导电性硅系薄膜的膜厚优选为2nm以上。导电型硅系薄膜31、32中,将具有与导电型单晶硅基板10不同的导电型的硅层称为“发射极层”。将具有与导电型单晶硅基板10和设置于受光面侧的第一导电型硅系薄膜31不同的导电型、且具有与导电型单晶硅基板10和设置于背面侧的第二导电型硅系薄膜32相同的导电型的结构称为“表发射极结构”。例如,使用了n型单晶硅基板作为导电型单晶硅基板10的“表发射极结构”的异质结太阳能电池中,在受光面侧配置成为发射极层的p型硅系薄膜,在背面侧配置n型硅系薄膜。另一方面,将具有与导电型单晶硅基板10和第一导电型硅系薄膜31相同的导电型、且具有与导电型单晶硅基板10和第二导电型硅系薄膜32不同的导电型的结构称为“背面发射极结构”。作为导电型硅系薄膜31、32的材料,优选非晶质硅。作为掺杂杂质,如果是n型硅层,则优选使用p(磷),如果是p型硅层,则优选使用b(硼)。优选在硅基板10和第一导电型硅系薄膜31之间、及硅基板10和第二导电型硅系薄膜32之间设置本征硅系薄膜21、22。通过在导电型单晶硅基板10的表面设置本征硅系薄膜21、22,硅基板10的表面缺陷被终止,载流子寿命提高,因此,太阳能电池的输出提高。对于硅系薄膜的制膜方法,没有特别限定,但从可以进行精密的膜厚控制来看,优选cvd(chemicalvaperdeposition)法。作为用于cvd的原料气体,可使用sih4等硅系气体。也可以使用含硅气体和h2的混合气体。为了提高硅系薄膜的光透射性等,也可以微量添加含有氧、碳等的原料气体。作为用于形成导电型硅系薄膜的掺杂气体,可举出b2h6、ph3等。(透明电极层)异质结太阳能电池的光电转换部50在导电型硅系薄膜31、32上具备透明电极层41、42。作为透明电极层41、42透明电极层的材料,通常使用氧化铟、氧化锡、氧化锌、氧化钛、其复合氧化物等透明导电性金属氧化物。其中,从兼具高导电率和透明性的观点来看,优选为以氧化铟为主要成分的铟系复合氧化物。作为铟系复合氧化物的掺杂杂质,可举出sn、ti、w、ce、ga等金属、它们的金属氧化物。透明电极层41、42的膜厚优选为40~80nm,更优选为50~70nm。对于透明电极层的形成方法,没有特别限定,但出于可以进行精密的膜厚控制,优选溅射法、rpd(radicalplasmadeposition)法等。在发射极层侧(配置与硅基板不同的导电型的硅层一侧)的面内的端部区域形成透明电极时,容易发生复合、漏电。因此,发射极层侧的透明电极层优选用掩模包覆基板的端部、周缘部而进行制膜。在此,“周缘部”是指,距基板端部300μm~1000μm左右的区域。另一方面,非发射极侧(配置与硅基板相同的导电型的硅层一侧)的复合、漏电的影响小,因此,即使在整个面形成透明电极层,也不易发生输出降低。[集电极]在受光面侧的第一透明电极层41上形成受光面侧集电极,在背面侧的第二透明电极层42上形成背面侧集电极。本发明的太阳能电池在受光面侧及背面侧具备经图案化的集电极。因此,也可以从背面侧摄入光。受光面侧的集电极及背面侧的集电极均包含多个叉指电极。优选多个叉指电极的延伸方向平行。图2是太阳能电池的受光面侧的俯视图,图3是太阳能电池的背面侧的俯视图。图2及图3的右侧的圆包围部分是叉指电极附近的放大图。图2所示的方式中,在光电转换部的受光面设有多个叉指电极60及与叉指电极正交的汇流条电极66。图3所示的方式中,在光电转换部的背面设有多个叉指电极70及与叉指电极正交的汇流条电极76。如图2及图3所示,通过设置与叉指电极正交的汇流条电极,并将集电极形成为格栅状,提高载流子回收效率。另外,通过设置汇流条电极,在进行模块化时,通过配线材料进行的太阳能电池间的电连接变得容易。从背面侧入射的光量为受光面侧的10%以下,因此,对于背面侧的叉指电极而言,由电极面积增大带来的阴影损失的影响比受光面小。因此,优选设计为背面叉指电极优先提高载流子回收效率。优选背面叉指电极形成得比受光面叉指电极更密集,受光面叉指电极的间隔距离比背面叉指电极的间隔距离大。叉指电极的间隔距离为相邻叉指电极中心线间的距离。受光面叉指电极的间隔距离优选为背面叉指电极间隔距离的1.5~5倍,更优选为2~4倍。如图1所示,受光面叉指电极60在金属籽晶层61上具有镀金属层62。金属籽晶层61设置于光电转换部50和绝缘层81之间。镀金属层62通过设置于绝缘层81的开口86与金属籽晶层61导通。(金属籽晶层)金属籽晶层61是作为镀金属层62的基底层发挥作用的层。作为金属籽晶层所含的金属,可举出au、ag、ni、cu、sn、al等。其中,从保持与光电转换部表面的接触电阻为较低水平,且抑制氧化带来的电阻率增加等观点来看,优选为ag、ni、sn。为了保持可靠性,且降低成本,也可以组合使用多个金属材料。金属籽晶层61可通过非电解镀敷、溅射、蒸镀、印刷等形成。从材料的利用效率的观点来看,优选金属籽晶层通过印刷形成。在通过印刷形成金属籽晶层的情况下,优选使用含有金属微粒、粘合剂树脂材料和溶剂的导电性糊。作为粘合剂树脂,优选使用环氧系树脂、苯酚系树脂、丙烯酸系树脂等热固化性树脂。这些树脂也可以是固体状的树脂,也可以是液态树脂。(镀金属层)在金属籽晶层61上形成镀金属层62。由此,与仅由ag膏形成集电极的情况相比,可以以更低成本形成低电阻的集电极。作为以镀金属层形式析出的金属,可使用sn、cu、ag、ni等。其中,从可以以更低成本进行低电阻化来看,优选cu。镀金属层62的形成也可以通过非电解镀敷及电解镀敷的任一种进行,但优选为电解镀敷。就电解镀敷而言,不仅金属的析出速度较快,而且可基于库仑量控制金属的析出量,因此,从生产性方面考虑是优选的。镀金属层62也可以由多个层构成。例如,在形成cu等导电率高的镀金属层后,形成sn等化学稳定性优异的镀金属层,由此,可抑制由氧化等引起的镀敷层的劣化。对于背面叉指电极70的构成,没有特别限定,但优选与受光面叉指电极60一样,在金属籽晶层71上具有镀金属层72,且金属籽晶层71和镀金属层72通过设置于绝缘层82的开口87进行导通。受光面叉指电极60的第一镀金属层62的材料和背面叉指电极70的第二镀金属层72的材料也可以相同,也可以不同。如果正面和背面的镀金属层的材料相同,则可以使光电转换部正面和背面的应力及热膨胀均匀。另外,可以在一个镀敷浴中同时形成受光面的第一镀金属层62和背面的第二镀金属层72,因此,可简化工艺,提高生产效率,降低工艺成本。对于汇流条电极66、76的形成方法,没有特别限定,但优选与叉指电极60、70一样,在金属籽晶层上形成镀金属层。通过相同方法形成叉指电极和汇流条电极,由此,可以简化工艺,提高生产性。另外,汇流条电极的线宽比叉指电极的线宽大,因此,通过在汇流条电极的金属籽晶层上设置供电点而进行电解镀敷,可形成面内的均匀性高的镀金属层。[绝缘层]光电转换部受光面的未形成集电极的区域大致整个面被绝缘层81覆盖。“大致整个面”是指95%以上的面积区域。其中,从提高绝缘层带来的水蒸气阻隔效果、防氢脱离效果的观点来看,优选未形成集电极的区域的98%以上被绝缘层覆盖,更优选99%以上被绝缘层覆盖。优选光电转换部背面的未形成集电极的区域大致整个面也被绝缘层82覆盖。通过设置受光面的第一绝缘层81及背面的第二绝缘层82,在形成第一镀金属层62及第二镀金属层72时,可以保护光电转换部50免受镀敷液的影响。另外,通过在金属籽晶层61、71上的绝缘层81、82设置开口86、87,可以在金属籽晶层61、71上选择性地形成镀金属层62、72。本发明中,通过在未设置金属籽晶层61的区域的第一绝缘层81形成开口89,在受光面的给定位置可形成独立镀金属层69。对于绝缘层81、82的材料,没有特别限定,但出于容易形成开口及保护性能优异,优选无机材料。作为绝缘层的无机材料,可使用氧化硅、氧化镁、氧化铜、氧化铌等金属氧化物。出于容易通过cvd、印刷形成、且透明性优异,作为绝缘层的无机材料,优选sio、sin、sion等。从提高太阳能电池模块的光摄入效率的观点来看,优选绝缘层81、82的折射率比光电转换部50的最表面层41、42的折射率小,且比密封材料111、112的折射率大。对于绝缘层81、82的膜厚,没有特别限定。从兼具光电转换部50的保护性和开口形成的容易性的观点来看,第一绝缘层81及第二绝缘层82的膜厚优选为10~200nm,更优选为30~150nm。由无机材料制成的绝缘层的水蒸气阻隔性高,因此,也具有保护设置于光电转换部50表面的透明电极层41、42免受环境中水分影响的作用。光电转换部表面被无机绝缘层81、82覆盖,由此,即使在背面保护材料130不含有金属箔的情况下,也可得到可靠性优异的太阳能电池模块。因此,可以使用不含有金属箔的背面保护材料130,如平顶类型、地上设置类型那样,可提高从背面侧也入射光的设置方式的太阳能电池模块的转换效率。对于绝缘层的形成方法,没有特别限定。在通过导电性糊的印刷形成金属籽晶层61、71的情况下,绝缘层81、82优选通过cvd形成。如上述wo2013/077038号(专利文献1)所记载,在通过对导电性糊等进行丝网印刷形成金属籽晶层、且通过cvd在该金属籽晶层上形成氧化硅等无机绝缘层的方法中,由于cvd制膜时或cvd制膜后的加热,使金属籽晶层的表面形状改变,在形成于金属籽晶层上的绝缘层可形成龟裂状的开口。在绝缘层81、82的开口86、87下露出的金属籽晶层61、71成为镀敷的起点,因此,可以在金属籽晶层形成区域上选择性地形成镀金属层62、72。[独立镀金属层]本发明的太阳能电池在受光面的第一绝缘层81的表面具有不与叉指电极接触的独立镀金属层69。独立镀金属层是不与叉指电极导通、且无助于向外部取出太阳能电池的光载流子的金属层。独立镀金属层具有使光散射反射、大幅改变太阳能电池表面附近的光的传播方向的效果。各个独立镀金属层优选形成投影面的直径为0.1μm~10μm左右的大致圆形。如图2的圆包围的放大图中模式性地表示的那样,受光面的独立镀金属层69被设置成以与受光面叉指电极60的延伸方向平行的带状形状集中存在,并形成独立镀金属密集区域690。独立镀金属密集区域是独立镀金属层的面积密度高于未形成受光面叉指电极区域整体的独立镀金属层面积密度的平均值的区域。在独立镀金属密集区域中,以受光面整体平均值二倍以上的面积密度设置独立镀金属层。独立镀金属层的面积密度通过将受光面划分成10μm见方(100μm2)区域,并算出各区域内的独立镀金属层的面积而求得。独立镀金属密集区域690的宽度优选为300μm以下,更优选为200μm以下。对于独立镀金属密集区域690的宽度的下限,没有特别限定,独立镀金属层也可以在一条直线上排列。独立镀金属密集区域不需要连接整个受光面叉指电极60的延伸方向,也可以在一部分中断。另外,独立镀金属密集区域不需要与受光面叉指电极60完全平行地存在,也可以存在相对于受光面叉指电极延伸方向弯折的部位。独立镀金属层69被设置成在与受光面叉指电极60的延伸方向平行的带状区域集中存在,由此,有太阳能电池的电流密度提高的倾向。通过在受光面存在独立镀金属层,尽管遮光面积变大,电流密度也会增加,认为其原因是入射至受光面叉指电极的太阳光(平行光)被独立镀金属层反射,由此,向光电转换部入射的光量增大。入射至叉指电极的光沿与受光面平行的方向、光入射方向正反射。有时向光入射方向反射的光在表面保护层(例如玻璃板)的界面再反射并向光电转换部进行入射,但通常难以使与受光面平行方向的反射光摄入光电转换部。另一方面,认为在受光面叉指电极60附近设有独立镀金属层69时,利用叉指电极向与受光面平行方向反射的光被独立镀金属层反射,因此,向光电转换部50摄入的光量增大。受光面的独立镀金属密集区域690优选以距受光面叉指电极的边缘间隔20μm以上的方式存在。独立镀金属层69与受光面叉指电极60的距离过小时,有被独立镀金属层散射反射的光再次到达受光面叉指电极的比例变大而可摄入光电转换部50的反射光量降低的倾向。另一方面,独立镀金属层69与受光面叉指电极60的距离过大时,有受光面叉指电极中的反射光到达独立镀金属层的比例变小而在大气中反射的反射光的比例变大的倾向。因此,受光面叉指电极60与独立镀金属密集区域690的间隔(间隔距离)优选为200μm以下。受光面叉指电极60与独立镀金属密集区域690的间隔更优选为30μm~150μm,进一步优选为40μm~100μm。如图3的圆包围的放大图中模式性地表示那样,也可以在背面侧的第二绝缘层82的表面形成独立镀金属层79。向太阳能电池的背面侧入射的光是在光电转换部未吸收而透射至背面侧的近红外线、入射至相邻配置的太阳能电池间间隙的光反射的再入射光的大部分,且为非平行光。因此,即使在背面侧设置独立镀金属层,也难以得到受光面侧那样的由散射反射带来的再入射效果。另一方面,入射至独立镀金属层的光成为阴影损失的原因。因此,当在背面侧的第二绝缘层82上设置的独立镀金属层的面积变大时,来自背面的反射光的摄入效率有降低的倾向。因此,优选受光面侧的第一绝缘层81表面的独立镀金属层69的面积密度比背面侧的第二绝缘层82表面的独立镀金属层79的面积密度大。第一绝缘层表面的独立镀金属层的面积密度优选为第二绝缘层表面的独立镀金属层的面积密度的1.2倍以上,更优选为1.5倍以上,进一步优选为2倍以上。对于距叉指电极的边缘250μm以内的区域中的独立镀金属层的面积密度而言,受光面侧优选为背面侧的2倍以上,更优选为5倍以上,进一步优选为8倍以上。对于独立镀金属层的形成方法,没有特别限定,但优选与叉指电极60的镀金属层62同时通过镀敷法形成。因此,独立镀金属层69的材料优选与镀金属层62相同。优选镀金属层62含有铜时,独立镀金属层69也含有铜。在未形成金属籽晶层61的区域上的绝缘层81设置开口89,以在开口下露出的透明电极层41为起点析出镀金属,由此,可同时形成镀金属层62和独立镀金属层69。通过沿着与金属籽晶层61的延伸方向平行的方向设置多个开口89,可形成以与叉指电极60的延伸方向平行的带状形状集中存在的独立镀金属层69。对于在未形成金属籽晶层区域上的绝缘层81形成开口89的方法,没有特别限定。例如,通过激光划线、机械划线等机械性的方法可形成开口89。另外,使树脂制的刷毛等与形成绝缘层81前的光电转换部50的表面(透明电极层41)接触而产生微细的微粒,并在该表面上制膜成绝缘层,由此,可在绝缘层81形成针孔状的开口89。通过在光电转换部的表面按压多孔状的树脂片、辊的方法、吹送粒子的方法等,也能在光电转换部的表面产生微粒,在绝缘层81形成开口89。优选的方式中,通过利用在形成金属籽晶层61时所使用的导电性糊的溶剂的渗出,不会擦伤光电转换部的表面而能够在金属籽晶层非形成区域上的绝缘层81形成开口89。导电性糊通常以如下方式设计触变性:即使在印刷压力较大的情况下,也不会发生导电性微粒及粘合剂树脂向印刷区域外渗出,但随着印刷压力的增大,溶剂的渗出量有变大的倾向。通过使膏固化时的加热,渗出至导电性糊形成区域(印刷区域)外侧的溶剂挥发,但在该区域上形成绝缘层时,溶剂渗出区域的外缘附近有容易形成针孔的倾向。通过以该针孔89为起点析出镀金属,能够形成与受光面叉指电极60的延伸方向平行的带状的独立镀金属密集区域690。为了在受光面侧形成与叉指电极60的延伸方向平行的带状的独立镀金属层69、且抑制在背面侧形成独立镀金属层,只要使形成受光面的第一金属籽晶层61时的导电性糊的印刷压力比形成背面的第二金属籽晶层71时的导电性糊的印刷压力大即可。通过增大受光面侧的导电性糊的印刷压力,使膏中的溶剂渗出,在第一绝缘层81形成针孔,并减小背面侧的导电性糊的印刷压力,由此,可抑制溶剂的渗出,抑制在第二绝缘层82形成针孔。因此,即使在以相同的镀敷条件形成受光面的第一镀金属层62和背面的第二镀金属层72的情况下,也可以在受光面侧选择性地形成独立镀金属层69。如上所述,在受光面叉指电极60的间隔比背面叉指电极70的间隔大,且密集地形成背面的叉指电极的情况下,在印刷导电性糊时,背面侧可使用开口面积率大的丝网印版。因此,如果以相同的印刷条件形成受光面侧的第一金属籽晶层和背面侧的第二金属籽晶层,则受光面侧的印刷压力相对性地变大。[应用于异质结太阳能电池以外的实例]以上,以光电转换部50在导电型单晶硅基板10的两面具备导电型硅系薄膜31、32及透明电极层41、42的异质结太阳能电池的例子为中心,说明了本发明的太阳能电池的结构,但本发明也可以应用于异质结太阳能电池以外的太阳能电池。具体而言,可举出:异质结型以外的晶体硅太阳能电池、使用了gaas等除硅以外的半导体基板的太阳能电池、在非晶质硅系薄膜、晶体硅系薄膜的pin接合或pn接合上形成透明电极层的硅系薄膜太阳能电池、cis、cigs等化合物半导体太阳能电池、色素敏化太阳能电池、有机薄膜(导电性聚合物)等有机薄膜太阳能电池等。[太阳能电池模块]本发明的太阳能电池在用于实际使用时,优选进行模块化。太阳能电池的模块化通过适当方法进行。例如,如图4所示,使太阳能电池100的汇流条电极66、76与极耳等配线材料105连接,由此,形成将多个太阳能电池串联或并联地连接的太阳能电池串,将太阳能电池串利用密封材料111、112及保护材料120、130进行密封,由此,进行模块化。太阳能电池和配线材料可以通过使用低熔点焊锡的焊锡连接、使用cf(conductivefilm)进行压接的连接等,进行电连接。作为密封材料,可使用:乙烯/醋酸乙烯酯共聚物(eva)、乙烯/醋酸乙烯酯/异氰脲酸三烯丙酯(evat)、聚乙烯醇缩丁醛(pvb)、硅、聚氨酯、丙烯酸、环氧、烯烃等透光性的树脂。从成本降低的观点来看,作为受光面侧密封材料111,优选使用eva。在使用不含有金属箔的背面保护材料130的情况下,为了提高模块的可靠性,优选使用含有聚烯烃树脂的背面侧密封材料112。聚烯烃树脂的水分透射率小,因此,即使在使用不含有金属箔的背面保护材料的情况下,也可抑制水分侵入光电转换部。优选背面侧密封材料的折射率n1、第二绝缘层的折射率n2、及光电转换部50的背面侧的最表面层的折射率n3满足n1<n2<n3。折射率从背面侧向光电转换部阶段性地变大,由此,背面侧的反射光通过光电转换部大量摄入,因此,可提高模块转换效率。异质结太阳能电池中,光电转换部50的背面侧的最表面层为第二透明电极层42,因此,只要使用折射率比氧化硅等透明电极层低的材料作为第二绝缘层,且使用更低折射率的材料作为背面侧密封材料即可。密封材料的折射率通常为1.5左右,透明电极的折射率为1.9~2.3左右,因此,优选绝缘层的折射率为1.5~2.3的范围内。需要说明的是,折射率是波长为600nm的条件下的值,通过椭偏仪法测定。作为受光面保护材料120,可使用玻璃板(蓝板玻璃、白板玻璃)、聚氟乙烯膜(例如,tedlar膜(注册商标))等氟树脂膜、聚对苯二甲酸乙二醇酯(pet)膜等。从机械强度、光透射率、水分隔绝性、成本等方面来看,优选为玻璃板,其中,特别优选为白板玻璃。作为背面保护材料130,可使用玻璃板、树脂膜、由铝等构成的金属箔或它们的叠层体。本发明的太阳能电池中,背面侧的集电极为图案状,因此,如果使用光透射性的背面保护材料130,则也可以从背面侧摄入光。因此,如平顶类型、地上设置类型那样,光也从背面侧入射的设置方式的太阳能电池模块中,优选使用不含有金属箔的光透射性的背面保护材料130。在背面保护材料不含有金属箔的情况下,存在水分从太阳能电池模块的背面侧的侵入量增大的倾向。本发明的太阳能电池中,光电转换部的正面和背面两面被绝缘层覆盖,因此,即使在使用了不含有金属箔的背面保护材料的情况下,也可以防止水分侵入光电转换部。一实施方式中,作为背面保护材料130,可使用从太阳能电池侧依次叠层有黑色树脂层和红外线反射层的叠层膜。黑色树脂层为可见光吸收性,吸收波长800nm以下的可见光。黑色树脂层的可见光透射率优选为10%以下。如果使用包含黑色树脂层的背面保护材料,则背面保护材料和太阳能电池的外观色接近,因此,相邻配置的太阳能电池间的间隙不显著,可得到外观设计性高的太阳能电池模块。通过在黑色树脂层的背面侧配置红外线反射层,可以将在太阳能电池的光电转换部未吸收而透射至背面侧的近红外线、入射至相邻配置的太阳能电池间的间隙的光进行反射,并再入射至太阳能电池,可以提高模块转换效率。红外线反射层中,波长800nm~1200nm的近红外线的反射率优选为80%以上,更优选为85%以上,进一步优选为90%以上。为了使在红外线反射层反射的近红外线再入射至太阳能电池,黑色树脂层中,波长800nm~1200nm的近红外线的透射率优选为80%以上。作为黑色树脂层,优选使用含有聚烯烃系树脂、聚酯系树脂、丙烯酸系树脂、氟树脂、乙烯/醋酸乙烯酯树脂等热塑性树脂及颜料、染料等色料的树脂组合物。着色剂优选为吸收可见光,且透射近红外线的材料,可使用亮度l*为45以上且色调相互不同的三种以上色料的组合、深色系的有机颜料等。黑色树脂层中也可以含有具有红外线反射特性的无机颜料。作为红外线反射层,可使用由含有氧化钛等具有红外线反射性的白色颜料的树脂组合物制成的树脂层、红外线反射性的金属箔(例如铝、银)等。金属箔有时会发生与空气接触导致的腐蚀、短路等。因此,从提高模块的可靠性、安全性的观点来看,作为红外线反射层,优选使用不含有金属箔的树脂层。也可以在黑色树脂层和红外线反射层之间含有用于贴合两者的粘接层等。实施例以下,通过实施例具体地说明本发明,但本发明不限定于以下的实施例。[实施例1](在硅基板表面形成纹理)将受光面的面方位为(100)且厚度为200μm的n型单晶硅基板在丙酮中进行清洗后,在2重量%的hf水溶液中浸渍5分钟,除去表面的氧化硅层,并利用超纯水进行两次冲洗。将清洗后的硅基板在保持为75℃的5/15重量%的koh/异丙醇水溶液中浸渍15分钟,进行各向异性蚀刻。然后,在2重量%的hf水溶液中浸渍5分钟,并利用超纯水进行两次冲洗,在常温条件下进行干燥。通过afm进行硅基板的表面观察,结果,在正面和背面两面形成(111)面露出的四棱锥状的纹理结构,其算术平均粗糙度为2100nm。(硅系薄膜的制膜)向cvd装置导入形成纹理后的单晶硅基板,在受光面上以4nm的膜厚制膜成本征非晶质硅层,在该本征非晶质硅层上以5nm的膜厚制膜成p型非晶质硅层。需要说明的是,本实施例的薄膜的膜厚是根据通过将在硅基板上以同条件制膜的薄膜的膜厚,通过分光椭偏仪(商品名m2000,j.a.woollam股份有限公司制造)测定而求得的制膜速度算出的值。本征非晶质硅层的制膜条件中,基板温度为180℃,压力为130pa,sih4/h2流量比为2/10,投入功率密度为0.03w/cm-2。p型非晶质硅层的制膜条件中,基板温度为190℃,压力为130pa,sih4/h2/b2h6流量比为1/10/3,投入功率密度为0.04w/cm-2。需要说明的是,上述中所说的b2h6气体使用利用h2将b2h6浓度稀释至5000ppm的气体。接着,在硅基板的背面侧,以5nm的膜厚制膜成本征非晶质硅层。在本征非晶质硅层上以10nm的膜厚制膜成n型非晶质硅层。n型非晶质硅层的制膜条件中,基板温度为180℃,压力为60pa,sih4/ph3流量比为1/2,投入功率密度为0.02w/cm-2。需要说明的是,上文所述的ph3气体使用利用h2将ph3浓度稀释至5000ppm的气体。(透明电极层的制膜)将形成硅系薄膜后的基板移送至rpd设备,在p型非晶质硅层上及n型非晶质硅层上分别制膜成膜厚为80nm的氧化铟层作为透明电极层。蒸镀源使用了在in2o3中添加1%的钨的材料。在制膜成受光面侧(p型非晶质硅层上)的透明电极层时,利用掩模包覆基板的周缘部0.5~0.75mm的区域,在周缘部不制膜成氧化铟层。在制膜成背面侧(n型非晶质硅层上)的透明电极层时,不使用掩模,而在整个面上制膜成氧化铟层。(金属籽晶层的形成)在受光面侧的氧化铟层上对导电性糊进行丝网印刷,形成金属籽晶。形成受光面侧的金属籽晶时,使用了以20:80的重量比含有作为导电性微粒的snbi金属粉末(粒径dl=25~35μm,熔点t1=141℃)和银粉末(粒径dh=2~3μm,熔点t2=971℃)、还含有作为粘合剂树脂的环氧系树脂(5wt%)及溶剂的膏。使用具有与汇流条电极和叉指电极的图案对应的开口的丝网印版(叉指电极的宽度:70μm,叉指电极的间距:2mm)对该导电性糊进行丝网印刷,以140℃进行约20分钟的预烧成。接着,在背面侧的氧化铟层上,与受光面侧同样地进行导电性糊的印刷及预烧成,形成金属籽晶。形成背面侧的金属籽晶时,使用了叉指电极宽度60μm、叉指电极间距0.75mm的丝网印版。利用光学显微镜观察形成金属籽晶后的基板表面,结果,在受光面侧,在距金属籽晶的端部50~200μm的区域内确认到,导电性糊中的溶剂在印刷时的挥发痕迹。在背面侧未确认到挥发痕迹。(绝缘层的形成)将基板运送至cvd设备,在受光面上制膜成膜厚40nm的氧化硅层后,使基板反转,在背面上制膜成膜厚60nm的氧化硅层。氧化硅的制膜条件中,基板温度为180℃,压力为60pa,sih4/co2流量比为1/10,投入功率密度为0.04w/cm-2。对于制膜成背面侧的氧化硅层后的受光面侧绝缘层的厚度而言,中央部为40nm,周缘部为60nm,周缘部的厚膜变大。由于制膜氧化硅层时的加热,发生金属籽晶中的金属材料的热流动等引起的表面形状的变化及来自金属籽晶的脱气,随之,在制膜于金属籽晶上的氧化硅层产生多个针孔。另外,在受光面侧,在膏中溶剂挥发痕迹的端部附近也产生针孔。(镀金属层的形成)在受光面侧及背面侧各自的汇流条区域的金属籽晶上连接探针,将基板浸渍于镀铜液中进行电解镀敷,在金属籽晶上以约10μm的厚度析出镀铜层。用纯水实施冲洗后,在镀锡液中浸渍基板而进行电解镀敷,在铜表面上以约3μm的厚度析出镀锡层。然后,用纯水进行冲洗。这样,在受光面侧及背面侧分别形成在金属籽晶层上叠层有镀铜层和镀锡层的镀金属层。利用光学显微镜观察电解镀敷后的表面。将受光面的显微镜观察像示于图5,将背面侧的显微镜观察像示于图6。在受光面侧,在距金属籽晶的端部间隔50~200μm左右的区域内,析出大量直径为1~10μm左右的独立镀金属层,形成独立镀金属密集区域。在背面侧随机地形成独立镀金属层,但未形成独立镀金属密集区域。(模块化)使用4块上述得到的太阳能电池,制作微型模块。首先,对相邻的太阳能电池的受光面侧汇流条和背面汇流条焊接极耳线,得到串联连接了4块太阳能电池的太阳能电池串。在太阳能电池串的受光面及背面侧配置作为密封材料的eva树脂片。配置强化白色玻璃作为受光面保护材料,配置含有四氟乙烯和乙烯的共聚物(etfe)树脂的透光性树脂片作为背面保护材料,进行抽真空后,以150℃进行约30分钟加热,使eva进行交联反应,进行密封。[比较例1]减小在受光面侧形成金属籽晶层时的丝网印刷的印刷压力,抑制导电性糊的溶剂的渗出。除此以外,与实施例1同样地进行太阳能电池的制作及微型模块的制作。利用光学显微镜观察形成金属籽晶后的基板表面,结果,在受光面侧及背面侧的任一侧均未确认到挥发痕迹。利用光学显微镜观察电解镀敷后的表面,结果,在受光面侧及背面侧的任一侧均随机形成独立镀金属层,但未形成独立镀金属密集区域。[比较例2]减小在受光面侧形成金属籽晶层时的丝网印刷的印刷压力,抑制导电性糊的溶剂的渗出,增大在背面侧形成金属籽晶层时的丝网印刷的印刷压力,使导电性糊的溶剂渗出。除此以外,与实施例1同样地进行太阳能电池的制作及微型模块的制作。利用光学显微镜观察形成金属籽晶后的基板表面,结果,在受光面侧未确认到挥发痕迹,在背面侧,在距金属籽晶的端部50~300μm的区域内确认到溶剂的挥发痕迹。利用光学显微镜观察电解镀敷后的表面,结果,在受光面侧随机形成了独立镀金属层,但未形成独立镀金属密集区域。在背面侧,在距金属籽晶的端部间隔50~300μm左右的区域内析出大量直径1~10μm左右的独立镀金属层,形成独立镀金属密集区域。[评价]使用背面侧具有光反射性金属的太阳模拟器,实施在实施例及比较例中得到的微型模块的i-v测定。将短路电流密度(jsc)、开路电压(voc)、填充因子(ff)、转换效率(eff)表示于表1。表1中,表示将比较例1的微型模块的转换特性设为1的相对值。[表1]jscvocffeff实施例11.0051.0001.0001.005比较例11111比较例20.9981.0001.0000.998在背面侧的叉指电极附近设有独立镀金属层的比较例2中,与不具有独立镀金属密集区域的比较例1相比,jsc降低。认为这是由于,由背面侧的独立镀金属层引起的遮光面积增大,来自背面侧的光摄入量降低。另一方面,在受光面侧的叉指电极附近带状地设有密集的独立镀金属层的实施例1中,尽管受光面的金属层形成面积增大,与比较例1相比,jsc也增加。认为这是由于,太阳光(平行光)被受光面侧的叉指电极反射后,被独立镀金属层反射,由此,向光电转换部入射的光量增大。当前第1页12