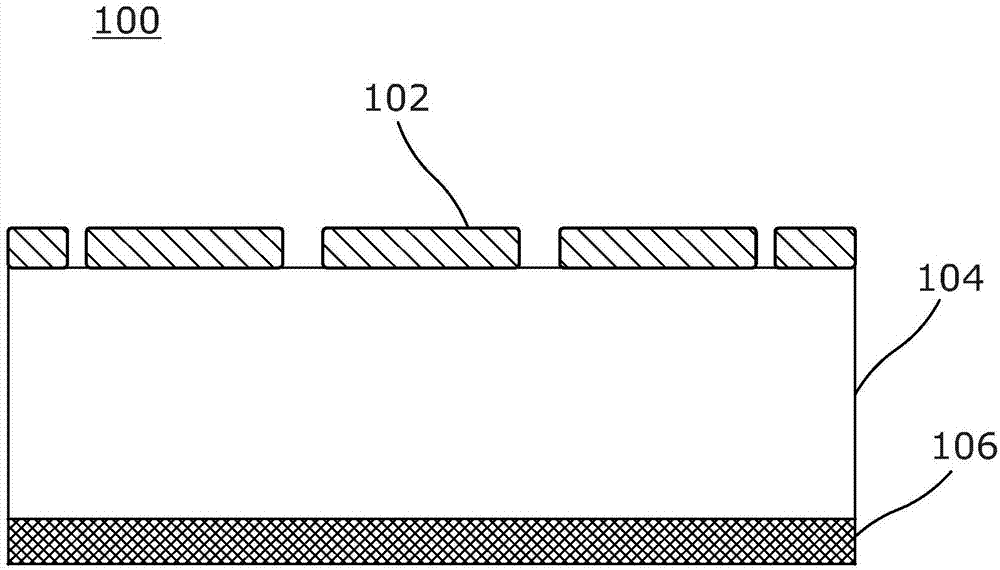
本发明涉及等离子体蚀刻和等离子体切割的方法。
背景技术:
半导体制造通常涉及在单个半导体晶片上并行地处理大量的硅芯片。一旦处理步骤完成,晶片必须被切成独立的芯片。然后,对随后被封装的芯片进行连接。常规地,使用金刚石锯实施切割步骤,该金刚石锯沿着晶片上的划线进行切割。最近,人们对提供用于切割晶片的新方法存在很大的兴趣。这些方法提供了增强性能和降低成本的可能性。这样的方法之一是使用激光来实施晶片的切割。替代的方法是使用等离子体蚀刻来切割晶片。该方法具有如下方面的益处:使裸片边缘损伤最小化,通过使用非常狭窄的划线来使对晶片表面的有效使用最大化,并提供使用非正交划线布局的选择。根据应用要求,等离子体蚀刻可以在晶片的减薄或研磨之前或之后发生。与其他切割方法(诸如激光切割或刀片切割)相比,等离子体切割具有许多益处,诸如,切屑更少、提高裸片强度/产量和提高每张晶片的裸片密度。晶片通常在框架结构中被安装在胶带上,并使用已知的“博世(bosch)”工艺各向异性地进行等离子体蚀刻,该工艺是一种使工艺气体在钝化(沉积)气体和蚀刻气体之间交替的技术。通过控制工艺参数,可以以高蚀刻速率获得优异的各向异性分布。博世工艺的后果是侧壁由于其形状而具有被称为圆齿(scallop)的固有粗糙度。通常,一个背面金属(backsidemetal,bsm)层或多个背面金属层被附接到晶片,以进行电接触。一些切割技术(诸如锯切或激光划切)可以沿着划线去除bsm。然而,这些金属层的存在在晶片的等离子体切割中可能会有问题,因为用于蚀刻体硅的等离子体化学组成不能很好地适合对背面金属进行蚀刻。在不蚀刻背面金属的情况下,在裸片分割步骤中存在金属撕裂的风险,其中金属碎片被留下且粘附于已分离的裸片的底部上。不良bsm断裂可能会在随后的工作流程中引起问题,因此希望来自暴露的通道中的所有金属在bsm分离过程和裸片剥离后保持粘附到切割胶带上。us2010/010227a1(以下称为us‘227)公开了一种半导体裸片分割方法。us‘227文献没有提到bsm撕裂的问题,但是提出了当接近硅/bsm界面时,可以通过使用常规的各向异性博世蚀刻或大部分各向同性蚀刻步骤来成功地分离裸片。具体来讲,us‘227公开了当接近bsm层时通过形成更大和更明显的圆齿来增加切割通道的宽度。本发明的目的是提供一种等离子体蚀刻工艺,该工艺能够快速去除硅并且能够在没有不利地撕裂bsm的情况下进行分割。发明人已经研究了bsm撕裂的问题,并且发现,存在两个影响bsm分离的干净程度的主要参数:1、在裸片/bsm界面处的bsm平面与局部裸片侧壁平面之间的角度。2、沿着裸片底部边缘的规则度。这些参数与硅/bsm界面处的圆齿形状有关。具体来说,发明人已经发现,在硅/bsm界面处bsm平面与局部裸片侧壁平面之间的角度越大(即,在该界面处侧壁越接近垂直于bsm平面),bsm分离的越干净。因此,大而深的明显圆齿会增加bsm撕裂的风险,因为它们会导致不规则的裸片底部边缘和在硅/bsm界面处bsm和裸片侧壁之间的小角度。这与us‘227的公开形成了对比。此外,等离子体蚀刻(和其他蚀刻工艺)的现象是蚀刻速率由于气体传输限制而依赖于蚀刻通道的纵横比。这被称为纵横比决定蚀刻(aspectratiodependentetching,arde)。具体来讲,通道的交叉点和通道的中心被以不同的蚀刻速率蚀刻,这通常导致交叉点“触地(touchingdown)”(到达bsm层)更早。这导致bsm层在每个圆齿内的不同位置处截断裸片侧壁,由此产生不规则的裸片底部边缘。这还导致“蚀刻前方”面积减少,这增加了对最后的圆齿的蚀刻速率,使该圆齿甚至更加明显并增加了bsm撕裂问题。技术实现要素:根据本发明的第一方面,提供了一种在附接有背面金属层的硅衬底中等离子体蚀刻一个或多个切割通道的方法,所述方法包括以下步骤:使用交替重复沉积步骤和蚀刻步骤的周期性等离子体蚀刻工艺执行主蚀刻,以产生具有圆齿形侧壁的切割通道;和切换为使用交替重复沉积步骤和蚀刻步骤的周期性等离子体蚀刻工艺执行第二等离子体蚀刻,直至到达背面金属层;其中,在第二蚀刻期间的一个蚀刻步骤中去除的硅量是在主蚀刻期间的一个蚀刻步骤中去除的硅量的一半或者更少。通过在接近bsm层时去除较少的硅,在第二蚀刻期间形成的圆齿(作为博世工艺的结果)比在主蚀刻期间形成的圆齿更小且更浅。通过在硅/bsm界面处形成小而浅的圆齿,在硅/bsm界面处bsm平面与局部裸片侧壁平面之间的角度更有可能较高。在硅/bsm界面附近蚀刻出小而浅的圆齿也减少了arde效应,从而减少了沿着裸片底部边缘的不规则度。此外,通过执行包括主蚀刻和第二蚀刻的多步骤工艺,主蚀刻可在高速率下实施以实现高的处理能力。设想在主蚀刻期间的蚀刻步骤中去除的硅量将不会在主蚀刻的过程中变化。然而,原则上,在蚀刻步骤中去除的硅量可以在主蚀刻的过程中变化。在那些实施方式中,在第二蚀刻期间的一个蚀刻步骤中去除的硅量被理解为相对于在主蚀刻中的每个蚀刻步骤中去除的平均硅量来表示。在一些实施方式中,在第二蚀刻期间的一个蚀刻步骤中去除的硅量是在主蚀刻期间的一个蚀刻步骤中去除的硅量的三分之一或者更少。在其它实施方式中,在第二蚀刻期间的一个蚀刻步骤中去除的硅量是在主蚀刻期间的一个蚀刻步骤中去除的硅量的四分之一或者更少。在其它实施方式中,在第二蚀刻期间的一个蚀刻步骤中去除的硅量是在主蚀刻期间的一个蚀刻步骤中去除的硅量的五分之一或者更少。在其它实施方式中,在第二蚀刻期间的一个蚀刻步骤中去除的硅量是在主蚀刻期间的一个蚀刻步骤中去除的硅量的六分之一或者更少。鉴于第二蚀刻工艺去除较少的硅并且因此比主蚀刻工艺慢,所以需要在维持高处理能力和降低bsm撕裂的风险之间找到平衡。因此,优选地,在第二蚀刻期间的一个蚀刻步骤中去除的硅量至少是在主蚀刻期间的一个蚀刻步骤中去除的硅量的四十分之一。在一些实施方式中,在第二蚀刻期间的一个蚀刻步骤中去除的硅量至少是在主蚀刻期间的一个蚀刻步骤中去除的硅量的三十分之一。在一些实施方式中,在第二蚀刻期间的一个蚀刻步骤中去除的硅量至少是在主蚀刻期间的一个蚀刻步骤中去除的硅量的二十分之一。大致上,如果诸如射频功率和气体流等的工艺条件保持在恒定值,则在蚀刻步骤期间去除的硅量与蚀刻步骤的蚀刻时间成正比。因此,为了实现主蚀刻和第二蚀刻之间去除的硅量的特定比例,可以使用相同的蚀刻时间比例。优选地,在第二蚀刻期间的一个蚀刻步骤的蚀刻时间是主蚀刻期间的一个蚀刻步骤的蚀刻时间的一半或者更少。在一些实施方式中,在第二蚀刻期间的一个蚀刻步骤的蚀刻时间是在主蚀刻期间的一个蚀刻步骤的蚀刻时间的三分之一或者更少。在其它实施方式中,在第二蚀刻期间的一个蚀刻步骤的蚀刻时间是在主蚀刻期间的一个蚀刻步骤的蚀刻时间的四分之一或者更少。在其他实施方式中,在第二蚀刻期间的一个蚀刻步骤的蚀刻时间是在主蚀刻期间的一个蚀刻步骤的蚀刻时间的五分之一或者更少。在其它实施方式中,在第二蚀刻期间的一个蚀刻步骤的蚀刻时间是在主蚀刻期间的一个蚀刻步骤的蚀刻时间的六分之一或者更少。如果在第二蚀刻期间的一个蚀刻步骤的蚀刻时间低于在主蚀刻期间的一个蚀刻步骤的蚀刻时间,则需要在维持高处理能力和降低bsm撕裂的风险之间找到平衡。因此,优选地,在第二蚀刻期间的一个蚀刻步骤的蚀刻时间至少是在主蚀刻期间的一个蚀刻步骤的蚀刻时间的四十分之一。在一些实施方式中,在第二蚀刻期间的一个蚀刻步骤的蚀刻时间至少是在主蚀刻期间的一个蚀刻步骤的蚀刻时间的三十分之一。在一些实施方式中,在第二蚀刻期间的一个蚀刻步骤的蚀刻时间至少是在主蚀刻期间的一个蚀刻步骤的蚀刻时间的二十分之一。设想在主蚀刻期间的蚀刻步骤的蚀刻时间将不会在主蚀刻的过程中变化。然而,原则上,蚀刻步骤的蚀刻时间可以在主蚀刻的过程中变化。在那些实施方式中,第二蚀刻期间的蚀刻步骤的蚀刻时间被理解为相对于主蚀刻中的蚀刻步骤的平均蚀刻时间来表示。在主蚀刻和第二蚀刻之间的切换期间,在每个蚀刻步骤期间去除的硅量可以逐渐减少。切换可以在数个蚀刻周期中发生,一个蚀刻周期被定义为一个沉积步骤和一个蚀刻步骤。例如,在2个蚀刻周期、3个蚀刻周期、4个蚀刻周期、5个蚀刻周期、6个蚀刻周期、7个蚀刻周期或8个蚀刻周期内,随着主蚀刻切换到第二蚀刻,在一个蚀刻步骤中被去除的硅量可以逐渐减少。在切换期间去除的硅量的逐渐减少可以是线性的。在主蚀刻和第二蚀刻之间的切换期间,每个蚀刻步骤的蚀刻时间可以逐渐减少。切换可以在数个蚀刻周期中发生,一个蚀刻周期被定义为一个沉积步骤和一个蚀刻步骤。例如,在2个蚀刻周期、3个蚀刻周期、4个蚀刻周期、5个蚀刻周期、6个蚀刻周期、7个蚀刻周期或8个蚀刻周期中,随着主蚀刻切换到第二蚀刻,每一个步骤的蚀刻时间可以逐渐减少。在切换期间的蚀刻时间的逐渐减少可以是线性的。优选地,在第二蚀刻期间的一个蚀刻步骤的蚀刻时间为1.5秒或更少。在一些实施方式中,在第二蚀刻期间的一个蚀刻步骤的蚀刻时间为1秒或更少。在其它实施方式中,在第二蚀刻期间的一个蚀刻步骤的蚀刻时间为0.5秒或更少。在其它实施方式中,在第二蚀刻期间的一个蚀刻步骤的蚀刻时间为约0.5秒。切换到第二蚀刻可以在主蚀刻到达背面金属层之前开始。在一些实施方式中,当主蚀刻与背面金属层相距的距离达到约60μm或更小(即,距离硅和背面金属层之间的界面约60μm或更小)时,开始第二蚀刻。在其它实施方式中,当主蚀刻与背面金属层相距的距离达到约50μm或更小时,开始第二蚀刻。在其它实施方式中,当主蚀刻与背面金属层相距的距离达到约40μm或更小时,开始第二蚀刻。在其它实施方式中,当主蚀刻与背面金属层相距的距离达到约30μm或更小时,开始第二蚀刻。在其它实施方式中,当主蚀刻与背面金属层相距的距离达到约20μm或更小时,开始第二蚀刻。替代地,在要蚀刻多个相交的切割通道的情况下,当切割通道交叉点(即,切割通道相交的点)到达背面金属层时,可以开始切换到第二蚀刻。与在主蚀刻到达背面金属层之前切换到第二蚀刻相比,该实施方式可以允许更高的处理能力,因为在切换到(较慢的)第二蚀刻工艺之前主蚀刻工艺可以被执行更长时间。此外,切割通道交叉点到达bsm层的点可以使用已知的方法检测,由此提供可开始第二蚀刻的可便利检测的点。在执行第二蚀刻之后,可以执行平滑化步骤以降低圆齿化(scalloping),其中,平滑化步骤包括将每个切割通道的侧壁暴露于各向异性等离子体蚀刻,所述各向异性等离子体蚀刻至少部分地蚀刻圆齿以提供平滑的侧壁。该平滑化步骤是一种高度方向性的蚀刻,其被设计成去除硅/bsm界面处的促使bsm撕裂的尖锐边缘和不规则部分。主蚀刻和/或第二蚀刻可以是通常称为“博世蚀刻(boschetch)”的类型。示例性的参考文献是us5,501,893、us7,648,611和us8,133,349,这些文献的全部内容通过引用并入本文。典型地,在执行主蚀刻之前在硅衬底上形成掩模,以便限定出一个或多个切割通道。在本发明的另一方面中,提供了一种在附接有背面金属层的硅衬底中等离子体蚀刻出一个或多个切割通道的方法,所述方法包括以下步骤:使用交替地重复沉积步骤和蚀刻步骤的周期性等离子体蚀刻工艺执行主蚀刻,直至达到背面金属层;执行平滑化步骤以降低圆齿化,其中,平滑化步骤包括将每个切割通道的侧壁暴露于各向异性等离子体蚀刻,该各向异性等离子体蚀刻至少部分地蚀刻圆齿以提供平滑的侧壁。优选地,各向异性等离子体蚀刻使用由含氟气体产生的等离子体,该含氟气体例如为sf6。等离子体可以在包括含氟气体和惰性气体的气体混合物中产生,该惰性气体优选为氩气。优选地,各向异性等离子体蚀刻使用具有500w或更高的射频功率的射频偏压。优选地,各向异性等离子体蚀刻使用由具有3000w或更高的射频功率的射频信号产生的等离子体。在本发明的另一方面中,提供了一种对附接有背面金属的硅衬底进行等离子体切割的方法,所述方法包括:执行本发明的之前方面中任一方面所述的等离子体蚀刻方法;和沿着切割通道将衬底分割成一个或多个裸片。技术人员熟知用于分割具有蚀刻的切割通道和一个或多个bsm层的硅衬底的合适方法。虽然上文描述了本发明,但是本发明可延伸到上文所列出的或下文的描述、附图或权利要求中所列出的特征的任何创造性组合。附图说明现在将参考附图仅通过示例的方式描述本发明,在附图中:图1(a)和图1(b)是典型的切割工艺的示意图。图2是示出了已使用博世工艺进行蚀刻的两个相邻的裸片110的侧视图的图像。图3是示出了两个分割开的裸片之间的不良bsm分离的图像。图4示出了根据第一实施方式的方法的流程图。图5是示出了在硅/bsm界面的不同的可能位置处的明显深的圆齿和浅而小的圆齿之间的角度(α)的差异。图6示出了在第二蚀刻期间针对不同蚀刻时间的裸片的侧壁的图像。图7示出了在执行第一实施方式的方法之后已经分离的裸片的图像。图8示出了根据第二实施方式的方法的流程图。图9示出了根据第三实施方式的方法的流程图。图10示出了平滑化步骤之前的典型的圆齿形特征的图像以及平滑化步骤之后的特征图像。具体实施方式图1(a)示出了用于执行已知等离子体蚀刻工艺的典型的起始结构100的示意图。结构100包括覆盖硅衬底104的一侧的图案化的光刻胶层102。背面金属(bsm)层106被粘附到硅衬底104的相反侧。图1(b)示出了在执行等离子体蚀刻工艺以产生切割通道108之后的结构100的示意图。硅衬底104被蚀刻到到底,但由于等离子体化学组成不适于穿过bsm层106进行蚀刻,所以等离子体蚀刻工艺在bsm层106处停止。图2是扫描电子显微镜(scanningelectronmicroscope,sem)图像,其示出了已使用博世工艺进行蚀刻并且随后被分割的两个相邻的裸片110的侧视图。可以看到,作为使用博世工艺来产生切割通道108的结果,每个裸片110的侧壁是圆齿形的。硅/bsm界面表示在图像的底部。图3示出了两个分割开的裸片之间的不良bsm分离的示例。在图3的两个图像中,裸片被定向成使得bsm层面向上。可以看到,bsm层没有干净地分离,其中,金属残留物粘附在不规则的硅/bsm界面上。图4示出了根据第一实施方式的方法的流程图。如上文所述且在图1(b)中所示出的,首先使附接有背面金属(bsm)层106的硅衬底104经历主蚀刻工艺。主蚀刻是博世等离子蚀刻,即,包括沉积步骤和等离子蚀刻步骤,该沉积步骤和该等离子蚀刻步骤被交替重复以部分地形成穿过硅衬底104的切割通道108。在该实施方式和其他实施方式中的沉积步骤和随后的沉积步骤可以使用由合适的源气体(诸如碳氟化合物,例如c4f8)形成的等离子体来执行。在该实施方式和其他实施方式中的蚀刻步骤和随后的蚀刻步骤可以使用由合适的蚀刻气体或气体混合物(诸如含氟气体,例如sf6)形成的等离子体来执行。用于主蚀刻工艺的示例工艺条件在表1中示出。表1工艺参数沉积去除蚀刻时间[s]1-50.5-53-10压力[毫托]60-12015-50100-180射频功率[w]450045005200偏压功率[w]0500-12000-100c4f8[sccm]200-600--sf6[sccm]-200-400750在通过主蚀刻形成的切割通道到达bsm层之前,第一实施方式的方法从执行主蚀刻工艺切换到执行第二蚀刻工艺。类似于主蚀刻工艺,第二蚀刻工艺也是包括沉积步骤和等离子体蚀刻步骤的博世等离子体蚀刻,该沉积步骤和该等离子体蚀刻步骤被交替重复以继续形成穿过硅衬底104的切割通道108,直到达到bsm层106。第二蚀刻的结束点可以使用已知技术来估计,该已知技术例如为光学发射光谱法(opticalemissionspectroscopy,oes)或干涉测量法。主蚀刻和第二蚀刻之间的一个区别在于:在第二蚀刻期间的一个蚀刻步骤中去除的硅量是在主蚀刻期间的一个蚀刻步骤中去除的硅量的一半或者更少。通过这种方式,与由主蚀刻形成的圆齿相比,在第二蚀刻期间形成的侧壁圆齿更小且更浅。通过在硅/bsm界面处和附近形成小而浅的圆齿,与明显深的圆齿相比,在该界面处bsm平面与局部侧壁之间的角度更可能较高(接近90°)。图5是示意图,示出了在硅/bsm界面的不同可能位置处的明显深的圆齿(在左侧示出)和浅而小的圆齿(在右侧示出)之间的该角度(α)的差异。图5表明,对于明显深的圆齿,在某些硅/bsm界面位置处,bsm平面与局部侧壁之间的角度可以非常低(例如,图中顶部所示的角度)。大致上,如果射频功率和气体流量保持在恒定值,则在蚀刻步骤期间去除的硅量与蚀刻步骤的蚀刻时间成正比。因此,在蚀刻步骤期间去除较少硅的一种方式是减少蚀刻步骤的蚀刻时间。例如,为了将在一个蚀刻步骤中去除的硅的量减少一半,可以对蚀刻步骤的蚀刻时间减半。图6示出了在第二蚀刻期间对于每个蚀刻步骤经历1秒和1.5秒的蚀刻时间后的裸片的侧壁的扫描电子显微镜(sem)图像。可以看到,与更远离bsm层(位于每个图像的底部)的圆齿(在主蚀刻期间形成的)相比,接近bsm层的圆齿更小且更浅。优选地,在第二蚀刻期间的一个蚀刻步骤的蚀刻时间为约0.5秒。除了蚀刻时间之外,还可以单独或组合地改变其他参数,以减少在蚀刻步骤期间去除的硅量。例如,可以减小射频功率或可以使用更少的蚀刻气体(例如sf6)。该方法从执行主蚀刻切换到执行第二蚀刻的点需要考虑保持高处理能力并允许可靠的bsm分离的需要。为了保持高的处理能力,理想地是,将执行第二蚀刻所花费的总时间保持在最小值。切换点将取决于估计的主蚀刻的蚀刻速率以及取决于估计的硅衬底厚度或已知的硅衬底厚度。实际上,切换点可以通过利用代表性衬底的试错过程来确定。从主蚀刻工艺到第二蚀刻工艺的切换可以是逐渐的,即,随着该方法从主蚀刻工艺切换到第二蚀刻工艺,被去除的硅量可以逐渐减少。切换可以在数个蚀刻周期发生(一个周期被定义为一个沉积步骤和一个蚀刻步骤)。在切换期间,在一个蚀刻步骤期间去除的硅量可以线性地减小。图7示出了在执行第一实施方式的方法之后已经分离的裸片的sem图像和光学显微镜图像。在图7中,裸片被定向为使得bsm层位于顶部。硅衬底的厚度为约100μm。bsm的厚度为0.370μm,并且bsm由20nm的ti、50nm的ni和300nm的au组成。在第二蚀刻期间的一个蚀刻步骤中去除的硅量是在主蚀刻期间的一个蚀刻步骤中去除的硅量的约三分之一。在第二蚀刻期间的一个蚀刻的蚀刻时间是在主蚀刻期间的一个蚀刻的蚀刻时间的约三分之一。从主蚀刻到第二蚀刻的切换发生在剩余的硅为约30μm(即,距硅和背面金属层之间的界面约30μm)处。主蚀刻工艺和第二蚀刻工艺之间的转换步骤消耗了大约10μm的si。该图显示,没有金属残留物粘附到裸片的底部边缘,这表明bsm层沿着切割通道已非常干净地分离。图8示出了根据第二实施方式的方法的流程图。除了第二实施方式的方法在切割通道的交叉点到达bsm层时切换到第二蚀刻工艺之外,第二实施方式与第一实施方式相同。如
背景技术:
部分所提到的,由于arde,通道交叉点通常以不同于通道的剩余部分的蚀刻速率被蚀刻。因此,在通道交叉点到达bsm层的点时,切割通道的剩余部分尚未到达bsm层。使用第二蚀刻完成切割通道,直到切割通道的剩余部分到达bsm层。可以使用已知的方法(诸如光学发射光谱法(opticalemissionspectroscopy,oes)或干涉测量法)来检测通道交叉点到达bsm层的点。第二实施方式的方法与第一实施方式的方法相比允许更高的处理能力,因为在切换到(较慢的)第二蚀刻工艺之前可以执行主蚀刻工艺更长时间。此外,如上文所提到的,切割通道交叉点到达bsm层的点可以使用已知方法来检测,由此提供可以开始第二蚀刻的可便利检测的点。图9示出了根据第三实施方式的方法的流程图。在第三实施方式的方法中,首先使附接有背面金属(bsm)层106的硅衬底104经历主蚀刻工艺。除了执行主蚀刻工艺直到切割通道到达bsm层之外,主蚀刻工艺与第一实施方式和第二实施方式所述的主蚀刻工艺相同。结束点可以使用诸如光学发射光谱法(oes)或干涉测量法的已知方法来确定。接下来,执行平滑化步骤以降低侧壁的圆齿化,例如,通过去除圆齿的尖端。可以使用利用由合适的蚀刻气体或气体混合物(诸如含氟气体,例如sf6)形成的等离子体进行的各向异性等离子体蚀刻来执行平滑化步骤。气体混合物可以包括例如sf6的含氟气体和例如氩气的惰性气体。表2中示出了用于使用sf6和氩气的气体混合物进行的平滑化步骤的示例性工艺条件。表2工艺参数平滑化蚀刻时间[秒]5-150压力[毫托]1-300射频功率[w]4000偏压功率[w]500-1000氩气[sccm]200-400sf6[sccm]100-200第三实施方式的平滑化步骤具有高度方向性并且旨在去除尖锐的边缘以有助于bsm干净分离。图10示出了在平滑化步骤之前典型的圆齿形特征的sem图像和平滑化步骤之后的特征的sem图像。通过执行平滑化步骤,硅/bsm层界面处的不规则的边缘被平滑化,从而在界面处提供更直且更规则的边缘,以有助于bsm分离。平滑化步骤也可以通过在第二蚀刻之后执行平滑化步骤而与第一实施方式和第二实施方式结合。这将界面处更小且更浅的圆齿的有利效果与硅/bsm层界面处更直且更规则的边缘结合到了一起。当前第1页12