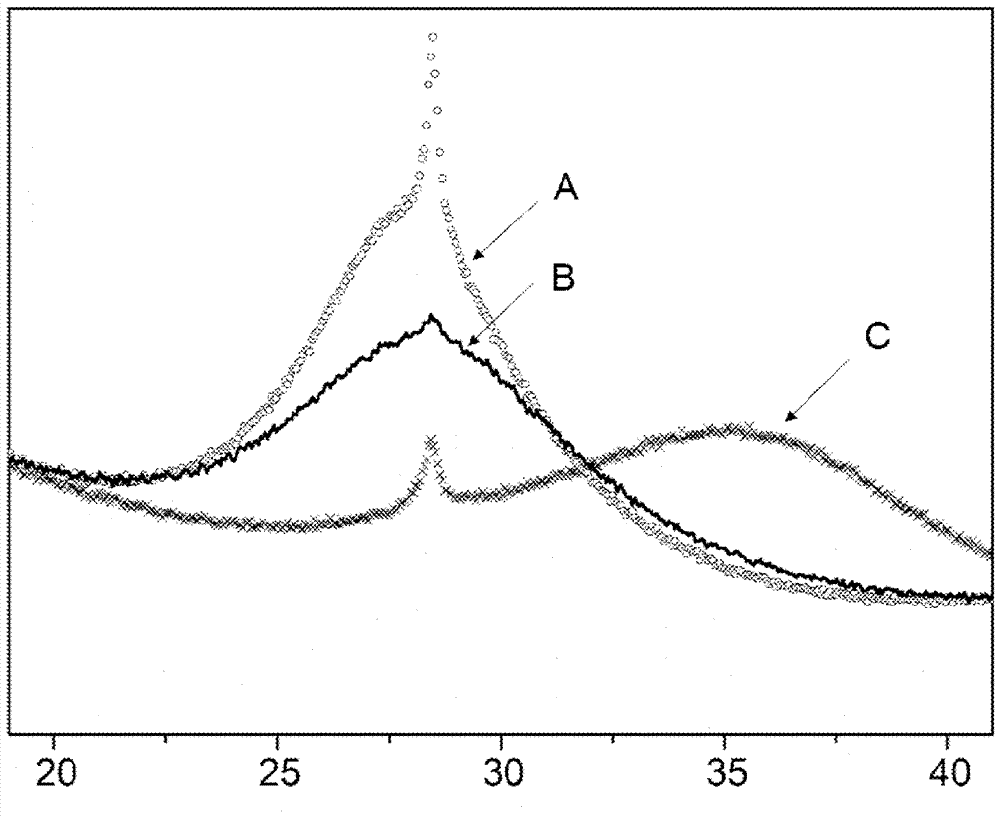
本发明涉及硅-碳复合粉末,其制造方法及其在锂离子电池中的用途。
背景技术:
:已知在锂的合金化/去合金化过程中的剧烈体积膨胀/收缩会导致裂缝的形成和随后的活性物质颗粒粉末化,从而导致锂离子电池中的永久容量损失。为了克服si阳极的剧烈体积变化并因此获得更好的容量保持和循环寿命,已经使用了各种方法。其中,最有希望的方法是产生纳米复合结构,其中纳米尺寸的si颗粒被活性壳,优选碳壳包围。此外,由于在循环期间si基阳极经历的剧烈体积变化而形成的裂缝导致电极表面暴露于电解质。这导致连续形成厚的固体电解质界面(sei)层。sei的过度生长导致低的库仑效率,更高的离子传输阻力和电极的低电子传导性,并最终导致电池干耗(dry-out)。其中纳米尺寸的si颗粒被碳壳包围的复合材料被证明也有利于抑制sei的形成[dimitrijevic等人,j.powersources206(2012)343]。已经采用各种方法制备硅-碳复合材料。方法包括球磨或机械研磨、热解、化学/热气相沉积和凝胶的化学反应。在wo2013078645a1中,要求保护一种硅-碳复合材料,其包含介孔的硅颗粒和在该硅颗粒上提供的碳涂层,其中硅颗粒具有2-4nm和20-40nm的两种孔径分布。碳涂层的厚度为5-10nm,和碳的含量基于所述复合材料的总重量为10-50重量%。还要求保护一种用于制备所述硅-碳复合材料的方法,包括如下步骤:在球磨的作用下通过sicl4和li13si4之间的机械化学反应和随后热处理和洗涤过程制备介孔的硅颗粒;和利用化学气相沉积在介孔的硅颗粒上涂覆碳。ng等人在angew.chem.,int.ed.2006,45,6896中公开了在400℃下在空气中使用喷雾热解法得到的碳涂覆的si纳米复合材料。在该纳米复合材料中的碳最可能具有无定形的性质。硅的主要部分对应于纳米晶体si,但可能存在少量的无定形硅。所述硅由厚度为约10nm的无定形或部分无定形的碳层包围。ng等人在j.phys.chem.c2007,111,11131中进一步公开了进行低温喷雾热解以制造在可充电锂离子电池中作为阳极材料的si纳米复合材料。将纳米尺寸的si颗粒(<100nm)在柠檬酸/乙醇溶液中进一步喷雾热解,从而在球状si纳米颗粒的表面上形成一层均匀的碳涂层。yang等人在electrochemistrycommunications28(2013)40中公开了含有嵌入碳基质中的si的复合材料。通过喷雾热解制备该硅-碳纳米复合粉末。将包含活性有机硅烷(在后来的纳米复合材料中形成si和c两者)的气溶胶在管式炉中在900℃下反应。si的重量分数估计为40%。重要的是,该方法产生尺寸均匀的颗粒,其中碳和无定形si分布均匀。zhang等人在nanoscale,2013,5,5384中报道了在锂离子电池中作为阳极材料的无定形硅-碳纳米球的制备。这些纳米球通过化学气相沉积在900℃下而合成,其中使用甲基三氯硅烷(ch3sicl3)作为si和c两者的前体。已经发现,si-c纳米球由约60重量%的无定形c和约40重量%的si组成,其中直径为400-600nm和表面积为43.8m2/g。sorice等人在acsappl.mater.interfaces2015,7,6637中报道了在两阶段激光热解反应器中通过一步连续工艺形成碳覆盖的硅纳米颗粒。在第一阶段中形成的结晶硅核在第二阶段中由主要由碳组成的连续壳覆盖。在si/c界面处,不存在碳化硅。在第一阶段中,激光束与sih4流相互作用,从而合成硅纳米颗粒。ar载气流将它们转移到第二阶段,在该阶段中将乙烯(c2h4)同轴导入。激光束通过两个反射镜传输到第二阶段并发生离焦(defocalize),以最大化c2h4流与硅核之间相互作用的时间。该第二相互作用导致在硅纳米颗粒的小聚集体周围沉积碳壳。将硅纳米颗粒的直径调节为约30nm。调整激光功率和聚焦以有利于硅核的晶体结构。yu等人在ind.eng.chem.res.2014,53,12697中报道了通过动态化学气相沉积(cvd)工艺以甲苯或乙炔作为碳源在晶体si纳米颗粒上形成均匀的碳涂层。chaukulkar等人在acsappl.mater.interfaces2014,6,19026中报道了碳涂覆的硅纳米颗粒的等离子体合成。在管式石英反应器中,sih4以50w的射频功率向上游注入。将c2h2从sih4注入点向下游注入石英管中。尽管与纯si阳极相比,所有这些方法的硅-碳复合材料阳极提供了更好的循环性能,但是容量衰减仍然需要改进。据报道,当电压小于50mv时,在硅的锂化过程中形成晶体lixsi(x≥3.75)。如iaboni和obrovac在j.electrochemicalsoc.2016,163,a255中所报道的,在锂化时向lixsi(x≥3.75)相的转变导致高的内应力,从而导致颗粒破裂和电池性能衰减。抑制lixsi(x≥3.75)的形成的方法之一是将含si电极的循环电压限制在50mv以上。然而,这导致电池能量密度显著降低。除了具有较低的能量密度之外,限制含si电极的电压可能是不实际的,因为高密度合金电极可能与石墨或其他形式的碳共混。在这种电极中,合金相必须循环到低电压,以使石墨或碳有活性。因此,希望在不限制电压的情况下抑制lixsi(x≥3.75)的形成。抑制lixsi(x≥3.75)的形成可以在包含活性si相和非活性基质相的颗粒中实现,例如在含si合金和si/siox(x≤2)复合材料中所发现的。然而,非活性相降低了材料的比容量,因此是不希望的。技术实现要素:本发明的主题是硅-碳复合粉末,其中a)si和c分布在整个颗粒中,和b)颗粒表面上的重量比(c/si)表面大于整个颗粒内的重量比(c/si)总计。在这种硅-碳复合粉末中,如电压与容量测量所证明的,lixsi(x≥3.75)的形成受到抑制。此外,在该硅-碳复合粉末的表面上的较高c含量在抑制过度sei生长方面是有利的。本发明的硅-碳复合粉末具有令人惊讶的性质,即它不具有可通过透射电子显微镜(tem)检测到的核壳结构。通过透射电子显微镜(tem)中的能量色散x射线分析(edx)测定颗粒表面上的重量比(c/si)表面和重量比(c/si)总计两者。在一个优选的实施方案中,比率(c/si)表面/(c/si)总计为3≤(c/si)表面/(c/si)总计≤130。在另一个优选的实施方案中,比率(c/si)表面/(c/si)总计为10≤(c/si)表面/(c/si)总计≤50。重量比(c/si)总计优选为0.01≤(c/si)总计≤3,更优选0.3≤(c/si)总计≤1。与现有技术相反,在本发明的粉末中,si和c分布在整个颗粒中。通过透射电子显微镜(tem)没有检测到核壳结构。此外,在本发明的粉末中没有检测到碳化硅。本发明粉末的si和c可以是结晶的或无定形的。对于其以后作为锂离子电池的一部分的用途,si和c优选是无定形的。本发明粉末的颗粒可以是分离的或聚集的形式。平均颗粒直径优选为300nm或更低,更优选为20-100nm。本发明还提供一种用于制备所述硅-碳复合粉末的方法,其中将sih4、si2h6、si3h8和/或有机硅烷的气体料流和至少一种选自乙烯、乙烷、丙烷和乙炔的烃的气体料流同时导入反应器中,其中使用等离子体增强的化学气相沉积使所述料流反应。烃与sih4和/或有机硅烷的比例可在很宽的范围内选择。优选地,该比例为0.01-3。所述有机硅烷可以选自如下:ch3sih3、(ch3)2sih2、(ch3)3sih、c2h5sih3、(c2h5)2sih2、(c2h5)3sih、(ch3)4si、(c2h5)4si、c3h7sih3、(c3h7)4si、c4h9sih3、(c4h9)2sih2、(c4h9)3sih、(c4h9)4si、c5h11sih3、(c5h11)2sih2、(c5h11)3sih、(c5h11)4si、c6h13sih3、(c6h13)4si、(c7h15)sih3、(c7h15)2sih2、(c7h15)3sih、(c7h15)4si。最优选ch3sih3、(ch3)2sih2和(ch3)3sih。乙烯、乙烷和丙烷是优选的烃。乙炔是更具反应性的起始材料,必须注意避免形成sic。也就是说,要么使用低浓度的乙炔,要么改变等离子体增强的化学气相沉积的设置。包含硅烷和烃的反应混合物的平均停留时间可以用于影响平均颗粒平均直径。减少等离子体中的停留时间通常会减小颗粒直径。因此,4秒的停留时间产生300nm的平均颗粒大小,1秒的较短停留时间导致平均颗粒大小低于100nm。使用0.5秒的停留时间导致获得颗粒平均直径低于50nm的粉末。本发明的另一主题是硅-碳复合粉末在制造锂离子电池中的用途。附图说明图1显示了实施例中的粉末的x射线衍射(xrd)图案;图2显示了根据对比实施例5的硅-碳复合粉末的电化学电池研究结果;图3显示了根据实施例1-4制备的硅-碳复合粉末的电化学电池研究结果。具体实施方式实施例1(本发明)将射频(rf)非热等离子体应用于化学气相沉积(cvd)方法以产生粉末材料。该装置包括rf等离子体源,管状石英反应器,泵,工艺气体入口,排气口和粉末收集室。将石英管反应器抽空至10-100mbar的基础压力。等离子体源频率为13.56mhz,rf功率设定为50-200w。将稀释在ar中的sih4和乙烯通过质量流量控制器同时注入。气体混合物中硅烷的浓度为20体积%。chx/sih4的比例为0.16。气体流速和压力用于调节等离子体中的停留时间。4秒的较长停留时间导致获得颗粒平均直径低于300nm的粉末。1秒的较短停留时间导致获得颗粒平均直径低于100nm的粉末。使用0.5秒的停留时间导致获得低于50nm的粉末初级颗粒平均直径。在所获得的硅-碳复合粉末中,si和c分布在整个颗粒中。颗粒表面上的重量比(c/si)表面为3.5,并且在整个颗粒内的重量比(c/si)总计为1.0,如通过在透射电子显微镜(tem)中的能量色散x射线分析(edx)所测定的。在硅-碳复合粉末中的比率(c/si)表面/(c/si)总计为3.5。实施例2-4:使用实施例1中描述的条件进行进一步的实施方案。与实施例1相比,在实施例2-4中的碳前体气体chx的类型如表格中所列举的而变化。硅-碳复合粉末参数的变化在表格中给出。实施例5(对比):使用实施例1中描述的条件进行进一步的实施方案。与实施例1相比,仅将sih4引入石英管反应器中。不使用碳前体气体。所得粉末仅含硅。因此,在颗粒表面上的的重量比(c/si)表面和在整个颗粒内的重量比(c/si)总计为零。实施例5中的硅粉末与实施例1-4中的硅-碳复合粉末之间的差异在图1所示的x射线衍射(xrd)图案中也是明显的(x-轴=2θ(度);y-轴=强度(a.u.))。实施例5中制备的硅粉末(a)的xrd图案的特征在于,纳米晶体si在28.4°附近的尖峰和无定形si的宽峰(无定形晕(amorphoushalo))。根据定量相分析,晶体硅的量为20体积%。与硅粉末(a)相比,硅-碳复合粉末(b)的xrd图案中的无定形晕的强度降低并且稍微转移到更高的衍射角。在28.4°附近的尖峰是由于纳米晶体si,其在硅-碳复合粉末(b)中的存在量为4体积%。无定形晕强度降低和晕位移表明硅-碳复合粉末的形成,其中si和c分布在整个颗粒中,即无定形晕由si和c混合物产生。在球磨机中制备含有根据对比实施例5制备的硅粉末、苯乙烯-丁二烯橡胶的水溶液和碳纳米管的电极浆料,随后将其涂覆在铜箔上并干燥。由粉末涂料冲压出圆盘,并将其掺入具有li金属对电极和1mlipf6的碳酸亚乙酯/碳酸二甲酯电解质的纽扣电池中。图2(x-轴=容量(mah/g);y-轴=电压(v))显示了根据对比实施例5的硅-碳复合粉末的电化学电池研究结果。存在由于lixsi(x≥3.75)相的脱锂而形成的特征电压坪(voltageplateau)。相反地,在含有根据实施例1-4制备的硅-碳复合粉末的电极中,有效地抑制了对电极稳定性相有害的lixsi(x≥3.75)的形成,这可以从图3中不存在所述特征电压坪而确认。在图2和图3中,数字1、2、3、20、50表示第1、第2......充电循环。图2中的“*”表示与lixsi(x≥3.75)化合物的脱锂相关的坪。实施例6(对比):使用实施例1中描述的条件进行进一步的实施方案。与实施例1相比,将乙炔作为碳前体气体chx引入石英管反应器中,并且chx/sih4的比例为1。对比实施例6的主要反应产物是无定形的sic,只有一小部分主要是晶体si,这是不希望的。根据tem中的edx分析,c/si比例没有显著差异(参见表格):颗粒表面上的重量比(c/si)表面和整个颗粒内的重量比(c/si)总计为1.3。对比实施例6的材料(c)的xrd图案中的无定形晕转移到更高的衍射角,这表明形成了无定形sic。这种类型的材料不太适合电池应用。表格:实施例1-6的工艺气体参数和粉末性质实施例chx*sih4(体积%)chx/sih4(c/si)总计(c/si)表面(c/si)表面/(c/si)总计1乙烯200.161.03.53.52乙烷200.160.716.8253丙烷200.150.449.01254乙炔200.140.39.0325-2000006乙炔1011.31.31*碳前体气体。当前第1页12