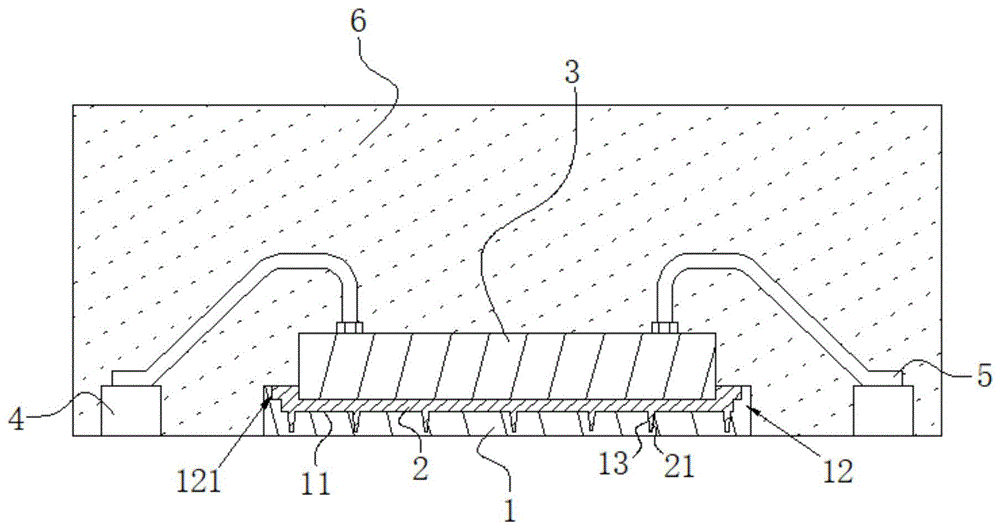
本发明属于无引脚封装
技术领域:
,尤其涉及一种高导热dfn封装器件的制备方法。
背景技术:
:dfn是一种无引脚封装,呈正方形或矩形,封装底部中央位置有一个大面积裸露焊盘用来导热,围绕大焊盘的封装外围四周有实现电气连结的导电焊盘。由于dfn封装不像传统的soic与tsop封装那样具有鸥翼状引线,内部引脚与焊盘之间的导电路径短,自感系数以及封装体内布线电阻很低,所以它能提供卓越的电性能,而得到广泛应用。由于在封装过程中环氧树脂组成物流动性差或固化不均一,易导致内部的气体未被完全赶走而产生气孔,进而导致封装器件吸湿导致可靠性失效,且内部气孔的产生还可能会导致导热性能降低从而引起电性方面的失效或热量损耗。因此,如何提供一种导热性能好,内部气孔的发生率低的dfn封装器件,成为本领域技术人员努力的方向。技术实现要素:本发明目的在于提供一种高导热dfn封装器件的制备方法,该方法制备得到的高导热dfn封装器件内部气孔的发生率低,有效避免了气孔导致的导热性能降低进而引起电性方面的失效的问题。为达到上述目的,本发明采用的技术方案是:一种高导热dfn封装器件的制备方法,所述高导热dfn封装器件包括位于环氧绝缘体中的散热焊盘、芯片和导电焊盘,所述芯片位于散热焊盘上,位于散热焊盘周边设有若干个导电焊盘,所述导电焊盘和芯片通过一引线连接;所述散热焊盘的中央区开有一供芯片嵌入的沉槽,从而在散热焊盘的边缘区形成一围堰部,所述沉槽的底部和围堰部与芯片的下表面和侧壁之间均设置有银浆层,所述沉槽的底部开有若干个延伸至散热焊盘内的换热盲孔,所述换热盲孔中具有银浆填充部;所述环氧绝缘体的原料的制备方法包括以下步骤:s1.先将硅微粉65~90份和阻燃剂10~25份与3-氨基丙基三乙氧基硅烷2~5份混合均匀,进行表面处理;s2.再加入环氧树脂80~100份、线型酚醛树脂50~70份、液体丁腈橡胶12~18份、焦碳酸二乙酯3~8份、聚乙二醇单辛基苯基醚0.1~1.5份、醋酸丁酸纤维素2~6份、5-氟-2-甲氧基苯胺0.3~2份、2,4,6-三(二甲氨基甲基)苯酚0.5~5份和脱模剂1~5份,混合均匀;s3.将混合物于90~110℃混炼3~5分钟,产物冷却后粉碎过筛,以上份数均为重量份。上述技术方案中进一步改进的技术方案如下:1.上述方案中,所述沉槽深度不大于芯片厚度设置。2.上述方案中,所述换热盲孔为锥形盲孔,所述换热盲孔靠近芯片一端端口的孔径大于换热盲孔远离芯片一端端口的孔径。3.上述方案中,所述换热盲孔延伸至散热焊盘中下部。4.上述方案中,所述围堰部内侧上开有阶梯部。5.上述方案中,所述脱模剂选自硬脂酸、硬脂酸盐或者氧化聚乙烯蜡中的至少一种。6.上述方案中,所述阻燃剂为硼酸盐和/或钼酸盐。7.上述方案中,步骤s3中,混炼温度为100℃。由于上述技术方案的运用,本发明与现有技术相比具有下列优点:1、本发明高导热dfn封装器件的制备方法,其在散热焊盘的中部开设与芯片匹配的沉槽,从而使得在贴装芯片时,工作人员将银浆置于沉槽中,并将对应的芯片安装进沉槽即可;此时,芯片下部嵌于沉槽中,不仅其底部能够通过形成的银浆层与沉槽底部粘结,芯片下部的侧壁也能与沉槽外部的围堰部的内壁通过银浆层相互粘结,不仅芯片与银浆层的接触面积有所增加,而且银浆层与散热焊盘的接触面积也有所增加,从而使得单位时间内,更多的热量在芯片与银浆层之间、银浆层与散热焊盘之间传导,进而改善dfn封装半导体器件的散热效果。2、本发明高导热dfn封装器件的制备方法,在散热焊盘的中央区设置有沉槽,能方便工作人员校准芯片的安装位置,实现芯片的精确安装,提高芯片封装质量;同时,将芯片嵌装于沉槽中,能够定位芯片位置,配合银浆的设置保护芯片和与芯片连接的引线,提高封装质量;此外,沉槽底部开设换热盲孔,换热盲孔的设置能够容纳部分银浆,避免多余的银浆溢出沉槽,待换热盲孔中具有银浆填充部后,银浆与散热焊盘的接触面积进一步增加,封装散热效果得到进一步的提升。3.本发明高导热dfn封装器件的制备方法,其环氧绝缘体配方在环氧树脂体系中加入了液体丁腈橡胶12~18份,采用2,4,6-三(二甲氨基甲基)苯酚0.5~5份作为固化促进剂,并额外添加了焦碳酸二乙酯3~8份和5-氟-2-甲氧基苯胺0.3~2份,提高了固化物的交联密度,从而增强了环氧绝缘体的整体力学性能,有效保证了制得dfn封装器件结构稳定性。4.本发明高导热dfn封装器件的制备方法,其环氧绝缘体配方采用环氧树脂80~100份和线型酚醛树脂50~70份,并添加聚乙二醇单辛基苯基醚0.1~1.5份和醋酸丁酸纤维素2~6份,降低了树脂体系与无机填料间的相互作用力,显著改善了组合物的流动性,能够有效降低封装后内部气孔的发生率,避免了气孔导致的导热性能降低进而引起电性方面的失效的问题,提高了封装成品率。附图说明附图1为本发明高导热dfn封装器件结构示意图。以上附图中:1、散热焊盘;11、沉槽;12、围堰部;121、阶梯部;13、换热盲孔;2、银浆层;21、银浆填充部;3、芯片;4、导电焊盘;5、引线;6、环氧绝缘体。具体实施方式下面结合实施例对本发明作进一步描述:实施例1~4:一种高导热dfn封装器件的制备方法,所述高导热dfn封装器件包括位于环氧绝缘体6中的散热焊盘1、芯片3和导电焊盘4,所述芯片3位于散热焊盘1上,位于散热焊盘1周边设有若干个导电焊盘4,所述导电焊盘4和芯片3通过一引线5连接;所述散热焊盘1的中央区开有一供芯片3嵌入的沉槽11,从而在散热焊盘1的边缘区形成一围堰部12,所述沉槽11的底部和围堰部12与芯片3的下表面和侧壁之间均设置有银浆层2,所述沉槽11的底部开有若干个延伸至散热焊盘1内的换热盲孔13,所述换热盲孔13中具有银浆填充部21;上述沉槽11深度不大于芯片3厚度设置;上述换热盲孔13为锥形盲孔,上述换热盲孔13靠近芯片3一端端口的孔径大于换热盲孔13远离芯片3一端端口的孔径;上述换热盲孔13延伸至散热焊盘1中下部;上述围堰部12内侧上开有阶梯部121;上述环氧绝缘体6的原料的制备方法包括以下步骤:s1.先将硅微粉65~90份和阻燃剂10~25份与3-氨基丙基三乙氧基硅烷2~5份混合均匀,进行表面处理;s2.再加入环氧树脂80~100份、线型酚醛树脂50~70份、液体丁腈橡胶12~18份、焦碳酸二乙酯3~8份、聚乙二醇单辛基苯基醚0.1~1.5份、醋酸丁酸纤维素2~6份、5-氟-2-甲氧基苯胺0.3~2份、2,4,6-三(二甲氨基甲基)苯酚0.5~5份和脱模剂1~5份,混合均匀;s3.将混合物于90~110℃混炼3~5分钟,产物冷却后粉碎过筛,以上份数均为重量份。各实施例环氧绝缘体6的原料具体组分如表1所示:表1实施例1中的脱模剂为硬脂酸,阻燃剂为硼酸盐;实施例2中的脱模剂为硬脂酸盐,阻燃剂为硼酸盐;实施例3中的脱模剂为氧化聚乙烯蜡,阻燃剂为钼酸盐;实施例4中的脱模剂为硬脂酸和氧化聚乙烯蜡的混合物,阻燃剂为钼酸盐。对比例1~3:一种环氧绝缘体,原料包括以下重量份组分:表2组分对比例1对比例2对比例3环氧树脂8090100线型酚醛树脂503070液体丁腈橡胶51812焦碳酸二乙酯8-5硅微粉659075聚乙二醇单辛基苯基醚0.11.5-3-氨基丙基三乙氧基硅烷254醋酸丁酸纤维素-365-氟-2-甲氧基苯胺20.3-2,4,6-三(二甲氨基甲基)苯酚0.525脱模剂215阻燃剂102515对比例1中的脱模剂为硬脂酸,阻燃剂为硼酸盐;对比例2中的脱模剂为硬脂酸盐,阻燃剂为硼酸盐;对比例3中的脱模剂为氧化聚乙烯蜡,阻燃剂为钼酸盐。制备工艺方法同实施例。上述实施例1~4和对比例1~3制得的环氧绝缘体的性能如表3所示:表3各实施例和对比例中,环氧绝缘体的成型条件均为:模具温度180℃,注射压力700kg/cm2,固化时间2min。如表3的评价结果所示,各实施例中的环氧绝缘体无论是整体力学性能还是流动性均优于各对比例,用于dfn封装器件中能够保证封装结构稳定性,降低封装后内部气孔的发生率,提高封装成品率。上述实施例只为说明本发明的技术构思及特点,其目的在于让熟悉此项技术的人士能够了解本发明的内容并据以实施,并不能以此限制本发明的保护范围。凡根据本发明精神实质所作的等效变化或修饰,都应涵盖在本发明的保护范围之内。当前第1页12