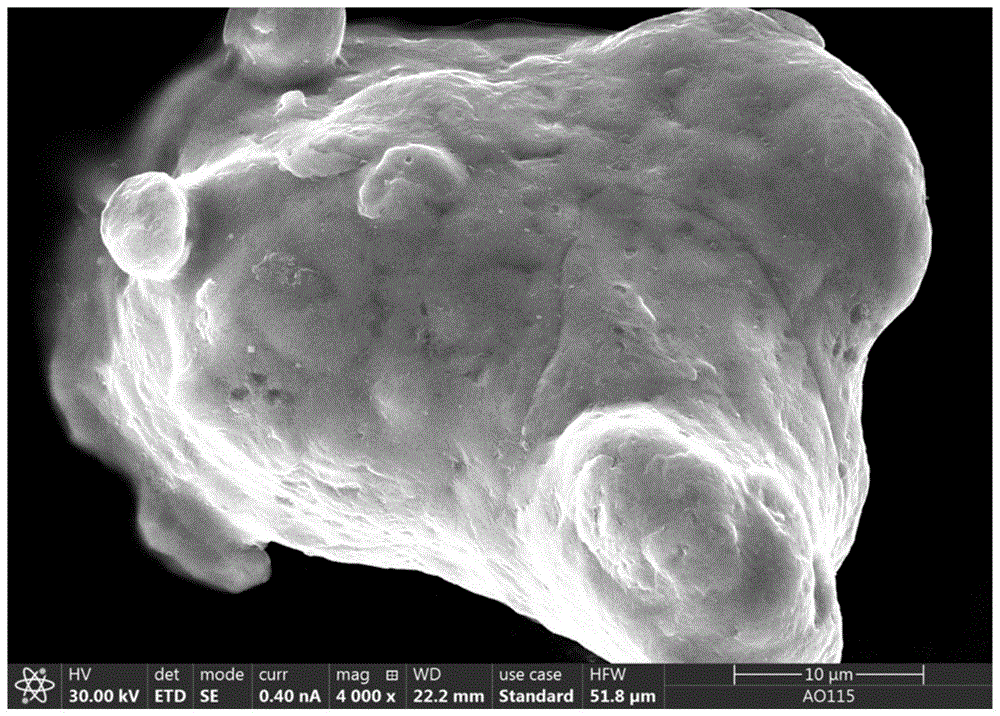
本发明涉及磁性材料
技术领域:
,特别涉及一种金属软磁复合材料及其制备方法。
背景技术:
:随着电子信息技术的不断进步,对磁性器件等行业也提出了更高的要求。磁性器件在通讯领域、数字终端及智能控制系统领域、汽车电子领域等新兴高端领域中发挥着关键性作用,目前整机电子产品核心和关键技术正迅速向元器件转移。轻、薄、短、小,高性能、高可靠、高环境适应性的应用需求推动电子无源元件和有源器件向小型化、微型化、片式化和集成化方向发展,磁性功能器件集成化技术已成为当代发展电子新技术的一个突出亮点。但是为了使设备小型化、轻型化,要求软磁材料向高频稳定化、低损耗化发展,使其在高频条件下具有较高的磁导率和饱和磁化强度,同时具有较低损耗。传统的软磁材料越来越难以满足以上所述现代电子工业的发展,因此需要开发新的软磁材料来满足现代电子器件发展的需求。与传统软磁铁氧体材料相比,金属软磁材料具有饱和磁化强度高,磁导率高,功率密度大等优点,有着独特的优势,但其电阻率低下,在高频应用中容易出现磁导率降低,涡流损耗严重等问题,由此金属软磁复合材料应运而生。软磁复合材料(smcs)通过在基体铁磁性颗粒表面包覆至少一层绝缘层来达到增加电阻率,减少涡流损耗的作用。绝缘材料的选择方面,根据绝缘层种类进行分类又可以分为有机包覆和无机包覆。其中,有机包覆层可以选择环氧树脂,丙烯酸,聚酯和聚氨酯等热固性树脂,无机包覆层可以选择氧化物,磷酸盐和硫酸盐等。软磁复合材料在实际应用中,常常需要进行热处理来消除压制过程中所引入的应力作用,而有机包覆传统工艺中常用的环氧树脂与酚醛树脂耐热性差,加热易分解,这就对后续热处理温度产生了限制。有机物包覆的另一个缺点是包覆层属于非磁性相,引入后会降低材料的饱和磁化强度,不利于获得较高的磁导率。在这方面,在无机包覆中,如磷酸盐包覆,硫酸盐包覆,氧化铝包覆,二氧化硅包覆等有着同样的问题。相关铁氧体的制备技术中,化学共沉淀法需要稳定的溶液ph值,先在基体表面生成氢氧化物前驱体,再经热处理生成目标铁氧体,且对热处理气氛及热处理温度有着一定要求,工艺繁琐。技术实现要素:本发明旨在至少解决现有技术中存在的上述技术问题之一。为此,本发明的目的之一在于提供一种金属软磁复合材料;本发明的目的之二在于提供这种金属软磁复合材料的制备方法;本发明的目的之三在于提供这种金属软磁复合材料的应用。为了实现上述目的,本发明所采取的技术方案是:本发明的第一方面提供了一种金属软磁复合材料,包括铁基体和包覆所述铁基体的包覆层;所述铁基体包括纯铁或者铁合金;所述包覆层包含镍锌铁氧体。铁氧体具有铁磁性,以其作为包覆层对铁磁性基体的饱和磁化强度稀释较小。本发明采用无机磁性相镍锌铁氧体作为铁磁性基体的绝缘包覆层,可以获得更好的磁性能,不仅可以抑制涡流损耗,同样减少了磁稀释,使得金属软磁复合材料的饱和磁化强度高。根据本发明所述金属软磁复合材料的一些实施例,所述铁合金包括铁硅合金、铁硅铝合金、铁硅铬合金、铁镍钼合金、铁镍合金中的至少一种。根据本发明所述金属软磁复合材料的一些实施例,所述包覆层的厚度为0.3微米~1微米。根据本发明所述金属软磁复合材料的一些实施例,所述金属软磁复合材料的饱和磁化强度为195emu/g~210emu/g。根据本发明所述金属软磁复合材料的一些实施例,所述金属软磁复合材料的矫顽力为15oe~30oe。根据本发明所述金属软磁复合材料的一些实施例,所述金属软磁复合材料在1mhz频率下的磁导率(实部)为50~75。根据本发明所述金属软磁复合材料的一些实施例,所述金属软磁复合材料在10khz频率下的损耗为20mw/cm3~40mw/cm3。根据本发明所述金属软磁复合材料的另一些实施例,所述金属软磁复合材料在10khz频率下的损耗为25mw/cm3~37mw/cm3。根据本发明所述金属软磁复合材料的一些实施例,所述金属软磁复合材料在50khz频率下的损耗为50mw/cm3~150mw/cm3。根据本发明所述金属软磁复合材料的另一些实施例,所述金属软磁复合材料在50khz频率下的损耗为60mw/cm3~130mw/cm3。根据本发明所述金属软磁复合材料的一些实施例,所述金属软磁复合材料在100khz频率下的损耗为100mw/cm3~400mw/cm3。根据本发明所述金属软磁复合材料的另一些实施例,所述金属软磁复合材料在100khz频率下的损耗为120mw/cm3~360mw/cm3。根据本发明所述金属软磁复合材料的一些实施例,所述金属软磁复合材料在200khz频率下的损耗低于270mw/cm3。根据本发明所述金属软磁复合材料的一些实施例,所述金属软磁复合材料在200khz频率下的损耗约为265mw/cm3。本发明的第二方面提供了一种根据本发明第一方面所述金属软磁复合材料的制备方法,包括以下步骤:1)将氨水、锌源与镍源混合,得到反应液;2)将所述反应液与铁基体混合,进行水热反应,得到金属软磁复合物,即所述的金属软磁复合材料。本发明采用原位水热法制备fe/nizn铁氧体软磁复合物粉末,反应前先添加ni离子与zn离子,使其与氨水生成络合物,接着加入铁基体,在水热过程中,利用络合物解离的方式在铁基体表面生成镍锌铁氧体,包覆层均匀致密,且无需热处理直接就可生成铁氧体,操作简便。根据本发明所述制备方法的一些实施方式,所述铁基体与锌源中的锌、镍源中的镍摩尔比为100:(0.2~0.4):(0.05~0.15)。根据本发明的一些实施例,所述铁基体与锌源中的锌、镍源中的镍摩尔比为100:(0.25~0.36):(0.08~0.12)。根据本发明所述制备方法的一些实施方式,所述锌源为二价锌盐。根据本发明的一些实施例,所述锌源包括氯化锌、硫酸锌、硝酸锌中的至少一种。根据本发明所述制备方法的一些实施方式,所述镍源为二价镍盐。根据本发明的一些实施例,所述镍源包括氯化镍、硫酸镍、硝酸镍中的至少一种。根据本发明所述制备方法的一些实施方式,所述步骤1)中,氨水的质量浓度为1%~2%。根据本发明所述制备方法的一些实施方式,所述步骤1)中,氨水是由质量浓度为25%~28%的浓氨水加水稀释制得。根据本发明的一些实施例,所述步骤1)中,氨水的质量浓度为1.3%~1.6%。根据本发明所述制备方法的一些实施方式,所述步骤1)中,反应液中锌源和镍源的浓度均为0.001g/ml~0.01g/ml。根据本发明的一些实施例,所述步骤1)中,反应液中锌源的浓度为0.002g/ml~0.006g/ml。根据本发明的另一些实施例,所述步骤1)中,反应液中锌源的浓度为0.002g/ml~0.004g/ml。根据本发明的一些实施例,所述步骤1)中,反应液中镍源的浓度为0.0012g/ml~0.002g/ml。根据本发明所述制备方法的一些实施方式,所述步骤1)中,混合的方式为搅拌。根据本发明的一些实施例,所述步骤1)中,混合具体是搅拌至溶液无沉淀。根据本发明的一些实施例,搅拌的时间为5分钟~20分钟。根据本发明所述制备方法的一些实施方式,所述步骤2)中,铁基体的粒径为20微米~40微米。根据本发明所述制备方法的一些实施方式,所述步骤2)中,铁基体为铁粉。根据本发明所述制备方法的一些实施方式,所述步骤2)中,水热反应的温度为150℃~200℃。根据本发明的一些实施例,所述步骤2)中,水热反应的温度为170℃~190℃。根据本发明的另一些实施例,所述步骤2)中,水热反应的温度为175℃~185℃。根据本发明所述制备方法的一些实施方式,所述步骤2)中,水热反应的时间为1小时~5小时。根据本发明所述制备方法的一些实施方式,所述步骤2)中,进行水热反应后,还包括将水热反应得到的固体产物进行洗涤,干燥的步骤。根据本发明所述制备方法的一些实施例,洗涤具体是用水、乙醇分别洗涤。根据本发明所述制备方法的一些实施例,干燥的温度为70℃~90℃。根据本发明所述制备方法的一些实施方式,所述制备方法还包括步骤3),将步骤2)得到的金属软磁复合物与粘结剂混合,再压制,热处理。通过压制制得磁芯后,再进行热处理制成金属软磁复合材料。根据本发明所述制备方法的一些实施方式,所述步骤3)中,粘结剂包括二氧化硅、硅树脂(聚硅氧烷树脂)、铋基玻璃中的至少一种。根据本发明的一些实施例,所述步骤3)中,粘结剂选自硅树脂、二氧化硅和硅树脂、铋基玻璃和硅树脂的任意一种。根据本发明的一些实施例,所述粘结剂中,二氧化硅为纳米二氧化硅。根据本发明所述制备方法的一些实施方式,所述步骤3)中,粘结剂的质量为金属软磁复合物质量的0.5%~5%。根据本发明所述制备方法的一些实施例,所述步骤3)中,粘结剂的质量为金属软磁复合物质量的1.5%~3.5%。根据本发明所述制备方法的一些实施方式,所述步骤3)中,当粘结剂为硅树脂时,硅树脂的质量为金属软磁复合物质量的1.5%~2.5%。根据本发明所述制备方法的一些实施方式,所述步骤3)中,当粘结剂为二氧化硅和硅树脂时,二氧化硅的质量为金属软磁复合物质量的0.2%~1.2%,硅树脂的质量为金属软磁复合物质量的1.5%~2.5%。根据本发明所述制备方法的一些实施方式,所述步骤3)中,当粘结剂为铋基玻璃和硅树脂时,铋基玻璃的质量为金属软磁复合物质量的0.4%~0.6%,硅树脂的质量为金属软磁复合物质量的1.5%~2.5%。根据本发明所述制备方法的一些实施方式,所述步骤3)中,将金属软磁复合物与粘结剂混合具体是将金属软磁复合物与粘结剂混合,加热,干燥。根据本发明所述制备方法的一些实施方式,所述步骤3)中,压制的压力为600mpa~800mpa。根据本发明所述制备方法的一些实施方式,所述步骤3)中,压制时保压的时间为3分钟~10分钟。根据本发明所述制备方法的一些实施方式,所述步骤3)中,热处理是在惰性气氛中进行。其中,惰性气氛的气体可选自氮气和/或氩气。根据本发明所述制备方法的一些实施方式,所述步骤3)中,热处理具体是:以4℃/min~6℃/min的升温速率升温至400℃~600℃,保温30分钟~2小时。根据本发明的一些实施例,所述步骤3)中,热处理具体是:以4.5℃/min~5.5℃/min的升温速率升温至400℃~600℃,保温30分钟~1小时。根据本发明的另一些实施例,所述步骤3)中,热处理具体是:以5℃/min的升温速率升温至400℃~600℃,保温30分钟~1小时。本发明的第三方面提供了金属软磁复合材料在电子领域、通讯领域或控制系统领域中的应用,所述金属软磁复合材料是本发明第一方面所述的金属软磁复合材料,或者是由本发明第二方面所述的制备方法制得。本发明的有益效果是:本发明提供了一种原位水热法制备fe/nizn铁氧体软磁复合材料的方法,制备工艺简便,易操作。通过该方法制备得到的金属软磁复合材料具有高频下高磁导率、低涡流损耗的特点,应用前景广阔。具体来说,与现有技术相比,本发明具有以下优点:传统的包覆工艺中,对基体颗粒形状有一定要求,如球形等具有规则形状的基体颗粒更容易实现均匀包覆。本发明采用原位水热法包覆,对基体形状无限制,且包覆层薄,制得的金属软磁复合材料饱和磁化强度高,高频损耗低,磁导率频率稳定性良好。附图说明图1为实施例1包覆前的样品扫描电镜图;图2为实施例1包覆后的样品扫描电镜图;图3为图2的局部放大图;图4为实施例1金属软磁复合物的磁滞回线图;图5为实施例1金属软磁复合物的xrd图;图6为实施例1金属软磁复合物的raman光谱图;图7为实施例1金属软磁复合材料环形样品的扫描电镜图;图8为实施例1金属软磁复合材料环形样品的能谱图;图9为实施例1金属软磁复合材料的动态磁导率谱图;图10为实施例2包覆前的样品扫描电镜图;图11为实施例2包覆后的样品扫描电镜图;图12为图11的局部放大图;图13为实施例2金属软磁复合材料的动态磁导率谱图;图14为实施例3金属软磁复合材料的动态磁导率谱图;图15为实施例4金属软磁复合材料的动态磁导率谱图;图16为实施例5金属软磁复合材料的动态磁导率谱图。具体实施方式以下通过具体的实施例对本发明的内容作进一步详细的说明。实施例中所用的原料、试剂或装置如无特殊说明,均可从常规商业途径得到,或者可以通过现有技术方法得到。除非特别说明,试验或测试方法均为本领域的常规方法。实施例1取适量25%-28%(质量浓度)瓶装氨水溶液加水稀释(体积比为1:18),加入0.0023g/mlzncl2,0.0013g/mlnicl2·6h2o配置成34ml反应液,搅拌至溶液无沉淀;然后加入10.8gfe粉(30μm),搅拌均匀,装入50ml聚四氟乙烯内胆的水热反应釜中,升温至180℃,保温1h,冷至室温,将粉末取出抽滤,用水、酒精分别洗涤3次,烘箱80℃烘干,得到金属软磁复合物粉末。附图1和附图2分别为实施例1包覆前、包覆后的样品扫描电镜图,附图3为图2的局部放大图。从图1~3可见,包覆后fe基体光滑的表面变得粗糙,出现了细小的颗粒状物质,表明成功对fe基体进行了包覆。包覆层的厚度为0.3微米~0.8微米。附图4为实施例1金属软磁复合物的磁滞回线图。从图4可见,包覆后饱和磁化强度为205.51emu/g,矫顽力为27.25oe,饱和磁化强度高。附图5为实施例1金属软磁复合物的xrd图。从图5可见,仅观测到代表fe的三个特征峰,35°左右处尖晶石铁氧体峰不明显,表明铁氧体含量很少。附图6为实施例1金属软磁复合物的raman光谱图。从图6可见,未经热处理时在270cm-1、650cm-1、540cm-1处存在峰,这与尖晶石铁氧体相对应特征峰吻合,表明表面产物为铁氧体。为进一步证明包覆层成分及包覆均匀性,将粉末压制成环,抛光后采用扫描电子显微镜及能谱仪进行测试。附图7为实施例1金属软磁复合材料环形样品的扫描电镜图,附图8为实施例1金属软磁复合材料环形样品的能谱图。从图7-8可见,包覆层成分主要为ni、zn、fe、o,越接近边界处,相关元素含量越高,表明包覆层成分主要为nizn铁氧体,包覆均匀。向实施例1得到的金属软磁复合物粉末中加入2wt%硅树脂,在750mpa压力下压制成外径13mm、内径7mm,厚度为1.5mm的圆环,在ar气氛中以5℃/min升温至555℃热处理1h后,制成金属软磁复合材料。采用lcr测试仪进行了磁谱测试,采用宽频功率分析仪在b=20mt条件下进行了损耗测试。附图9为实施例1金属软磁复合材料的动态磁导率谱图。表1所示为实施例1金属软磁复合材料的损耗结果。表1实施例1金属软磁复合材料损耗结果频率(khz)1050100200损耗(mw/cm3)24.8116.2359.93320.1从测试结果可见,实施例1的金属软磁复合材料磁导率频率稳定性良好,1mhz时仍可保持70的磁导率。实施例2取适量25%-28%瓶装氨水溶液加水稀释(体积比为1:18),加入0.0031g/mlzncl2,0.0017g/mlnicl2·6h2o配置成30ml反应液,搅拌至溶液无沉淀;然后加入10.8gfe粉(30μm),搅拌均匀,装入50ml聚四氟乙烯内胆的水热反应釜中,升温至180℃,保温1h,冷至室温,将粉末取出抽滤,用水、酒精分别洗涤3次,烘箱80℃烘干,得到金属软磁复合物粉末。附图10和附图11分别为实施例2包覆前、包覆后的样品扫描电镜图,附图12为图11的局部放大图。从图10~12可见,经过包覆后粉末样品的包覆层致密。向实施例2得到的金属软磁复合物粉末中加入2wt%硅树脂,在750mpa压力下压制成外径13mm、内径7mm,厚度为1.5mm的圆环,在ar气氛中以5℃/min升温至555℃热处理1h后,制成软磁复合材料。采用lcr测试仪进行了磁谱测试,采用宽频功率分析仪在b=20mt条件下进行了损耗测试。附图13为实施例2金属软磁复合材料的动态磁导率谱图。表2所示为实施例2金属软磁复合材料的损耗结果。表2实施例2金属软磁复合材料损耗结果频率(khz)1050100200损耗(mw/cm3)26.164.0124.2296.0从测试结果可见,实施例2的金属软磁复合材料磁导率频率稳定性良好,1mhz时仍可保持64的磁导率。与实施例1相比,实施例2制备金属软磁复合材料时采用的镍锌盐浓度不同,实施例2制得的金属软磁复合材料表面生长的颗粒较多,包覆层更厚,因此其绝缘性能比实施例1更好,磁导率随频率增大更加稳定,因此损耗更少。实施例3本例与实施例1的不同之处仅在于,将水热反应的时间由1h延长至5h,其余条件均与实施例1的相同。附图14为实施例3金属软磁复合材料的动态磁导率谱图。表3所示为实施例3金属软磁复合材料的损耗结果。表3实施例3金属软磁复合材料损耗结果频率(khz)1050100200损耗(mw/cm3)32.1123.1346.31362.8从测试结果可见,反应时间对样品性能十分重要,延长水热反应时间后,磁导率会有一定降低,但能够显著减少试样损耗。实施例4本例制备金属软磁复合物粉末的条件与实施例1相同,所不同之处在于制备磁性材料的方法是:得到复合粉末后向其中加入0.2~1.2wt%纳米sio2,2wt%硅树脂,在750mpa压力下压制成外径13mm、内径7mm,厚度为1.5mm的圆环,在ar气氛中以5℃/min升温至555℃热处理1h后,制成金属软磁复合材料。采用lcr测试仪进行了磁谱测试,采用宽频功率分析仪在b=20mt条件下进行了损耗测试。附图15为实施例4金属软磁复合材料的动态磁导率谱图。表4所示为实施例4金属软磁复合材料的损耗结果。表4实施例4金属软磁复合材料损耗结果从测试结果可见,在水热时间不变的情况下,添加sio2同样可以起到降低损耗的作用,随着sio2添加量的增加,试样磁导率轻微降低,损耗显著降低。实施例5本例制备金属软磁复合物粉末的条件与实施例2相同,所不同之处在于制备磁性材料的方法是:得到复合粉末后向其中加入0.53wt%bi基玻璃,2wt%硅树脂,在750mpa压力下压制成外径13mm、内径7mm,厚度为1.5mm的圆环,在ar气氛中以5℃/min升温至555℃热处理1h后,制成金属软磁复合材料。采用lcr测试仪进行了磁谱测试,采用宽频功率分析仪在b=20mt条件下进行了损耗测试。附图16为实施例5金属软磁复合材料的动态磁导率谱图。表5所示为实施例5金属软磁复合材料的损耗结果。表5实施例5金属软磁复合材料损耗结果频率(khz)1050100200损耗(mw/cm3)28.466.6125.8265.6从测试结果可见,在其余条件不变的情况下,添加bi基玻璃同样可以起到降低损耗的作用。本发明将铁基体纳入反应体系,利用原位水热法进行镍锌铁氧体包覆。反应前先向水中添加ni2+与zn2+,使其与过量氨水生成络合物溶液,接着加入铁基体,搅拌均匀,接着放入水热反应釜中进行反应。在水热过程中,一方面,络合物解离,重新缓慢释放出ni2+与zn2+,生成相关可溶性组分及氢氧化物;另一方面,铁基体与水、溶解在水中的氧发生反应生成[fe(oh)n]-(n-3)(n=2,3)。随着水热反应的进行,可溶性镍组分、锌组分和新形成的zn(oh)2、ni(oh)2将与羟基络合物[fe(oh)n]-(n-3)反应形成目标铁氧体产物。由于基体参与反应,包覆层与基体结合性良好,且无需热处理直接就可生成铁氧体,操作简便。本发明提供的金属软磁复合材料磁性能良好,具有高频下高磁导率、低涡流损耗的特点,在电子领域、通讯领域或控制系统领域中有广阔的应用前景。上述实施例为本发明较佳的实施方式,但本发明的实施方式并不受上述实施例的限制,其他的任何未背离本发明的精神实质与原理下所作的改变、修饰、替代、组合、简化,均应为等效的置换方式,都包含在本发明的保护范围之内。当前第1页12