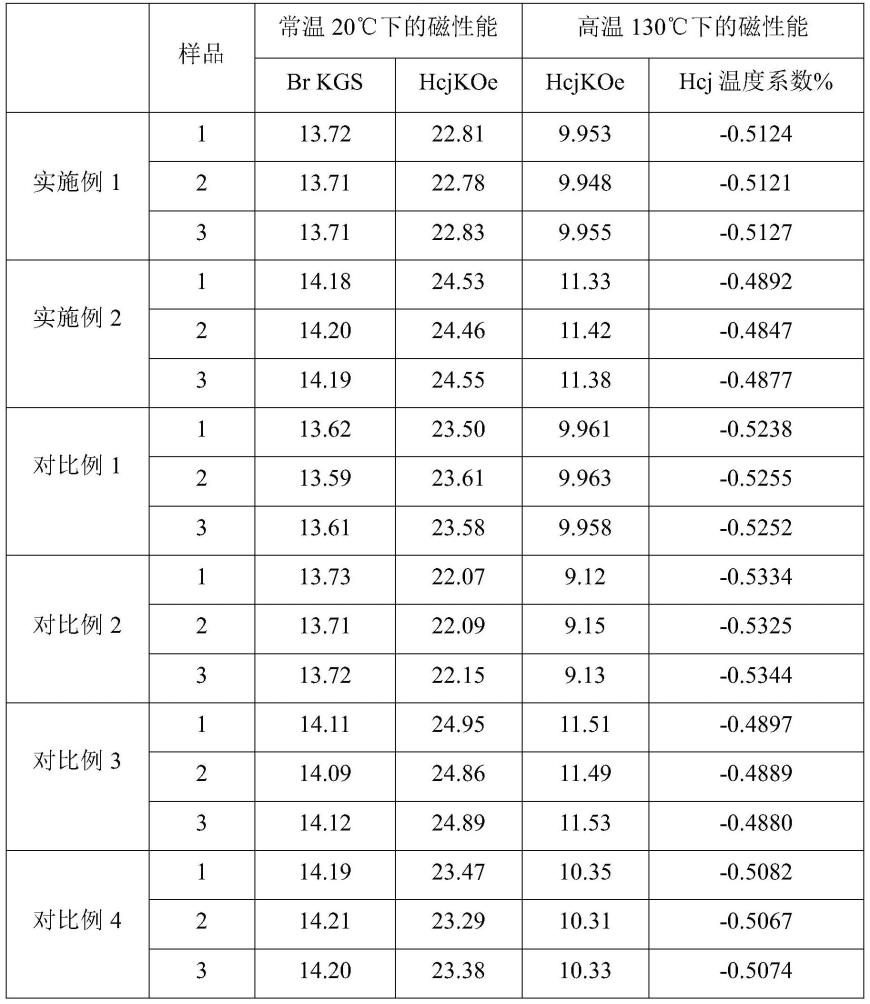
re-fe-b系永磁体的制备方法
技术领域
1.本发明涉及永磁体材料技术领域。更具体地说,本发明涉及一种re-fe-b系永磁体的制备方法。
背景技术:2.稀土nd2fe
14
b永磁体凭借其优良的综合磁性能,被广泛应用于通讯、信息、交通、能源和节能等领域,是目前应用最广的永磁材料。随着新能源技术的迅猛发展,钕铁硼永磁电机的应用范围日益扩大,不同领域对于钕铁硼磁体的性能要求也在不断提高。近年来,烧结re-fe-b磁体研发主要分两个方向:一是高性能;二是低成本。随着烧结re-fe-b磁体在风力发电、新能源汽车和节能家电等低碳经济领域的应用,兼具高磁能积和高矫顽力的双高特性的烧结re-fe-b磁体成为一个重要的研究方向。
3.近期研究表明,利用晶界扩散技术(gbdp)对钕铁硼磁体进行优化处理,能使其矫顽力大幅提高,而剩磁或最大磁能积基本不下降,此技术已成为大幅提升钕铁硼矫顽力并能够节省重稀土使用成本的最有效手段。但是,在实际生产过程中,重稀土dy或tb经过晶界扩散后,经常出现磁性能偏差大的问题,尤其表现在成品片在测试抗退磁性时,磁片的热减磁率波动较大,进而影响在电机使用时的性能。为了弥补性能和热减磁率的不足,通常会采用增大重稀土dy或tb使用量的方法,但是比较高含量的重稀土的使用,成本优势很弱,并且对于稀土资源的平衡及高效利用也处于不利的局势。专利文献jp-a2006-344779公开了蒸镀tb或者dy的氟化物同时扩散进烧结磁体内部的方法,但采用该方法处理磁体,需严格控制蒸发源蒸发速度和蒸汽浓度,对温度、真空度及操作系统的要求很高;同时由于受处理磁体与蒸发源之间有一定间隔,降低了空间利用率,处理成本较高。
技术实现要素:4.本发明的一个目的是提供一种re-fe-b系永磁体的制备方法,其能够在不增加稀土使用量的情况下,有效提升磁体的热稳定性。
5.为了实现根据本发明的这些目的和其它优点,根据本发明的一个方面,本发明提供了re-fe-b系永磁体的制备方法,包括以下步骤:将纳米级的cu粉加入有机溶剂a中,配制成混合悬浮液a,将所述混合悬浮液a包覆于粗磁粉中,压制成生坯块,烧结,加工成磁片;再将稀土金属粉加入有机溶剂b中,配制成混合悬浮液b,将所述混合悬浮液b涂敷于所述磁片的表面,晶界扩散,制得re-fe-b系永磁体。
6.优选的是,所述cu粉的粒径为500nm~1500nm。
7.优选的是,所述混合悬浮液a为cu粉与正庚烷、辛酸甲酯的混合溶液按25%~75%的质量比配制而成,其中,所述正庚烷和辛酸甲酯的质量比为1:3。
8.优选的是,所述粗磁粉为将pr、nd、ce、b、cu、co、ga、zr、ti、fe各金属元素按(3~3.2):(9.5~10):(0.5~1):(5.4~5.6):(0.1~0.15):(0.6~1.5):(0.18~0.25):(0~0.15):(0~0.2):(78.4~80.27)的原子百分比,经配料、熔炼、氢化处理制得的。
9.优选的是,所述磁片的具体制备过程为:
10.步骤一、在所述粗磁粉的气流制粉过程中,将所述混合悬浮液a添加入气流磨磨机内,经气流磨磨机内部的碰撞将混合悬浮液a包覆于粗磁粉中,获得钕铁硼粗磁粉,其中所述混合悬浮液a与粗磁粉的质量比为(2
‰
~6
‰
):1;
11.步骤二、在氧含量低于50ppm的密闭全自动压机中,将所述钕铁硼粗磁粉压制成生坯块,生坯块的密度为4.3~4.55g/cm3,将所述生坯块置于真空恒温箱内,设置真空度为1pa,温度为200℃,处理时间2h;
12.步骤三、将生坯块运转至真空烧结炉,设置真空度低于1.0
×
10-2
pa,升温至150℃,保温0.5~1.5h,中间充入一次氩气进行洗炉,压力为50~100pa,继续升温至380℃,保温0.5~2h,继续升温至500~600℃,保温0.5~2h,继续升温至800~900℃,保温5~8h,继续升温至1040~1080℃,进行高温最终烧结致密,保温4~8h,充入氩气或氦气至85~100kpa进行冷却,待冷却至温度低于70℃时出炉,获得烧结钕铁硼磁体块;
13.步骤四、将所述烧结钕铁硼磁体块经磨床、多线切割机加工成磁片。
14.优选的是,所述稀土金属粉为重稀土金属粉。
15.优选的是,所述重稀土金属粉为dy金属粉或tb金属粉中的任意一种。
16.优选的是,所述混合悬浮液b为稀土金属粉与无水乙醇、聚乙烯醇缩丁醛按照18:10:1的质量比混合形成的悬浮液。
17.优选的是,所述晶界扩散的具体步骤为:
18.步骤a、将混合悬浮液b均匀涂敷于所述磁片的表面,然后经真空低温加热烘干;
19.步骤b、将烘干后的磁片置于氧含量低于50ppm的真空渗透炉内,设置真空度低于1.0
×
10-2
pa,升温至150℃,保温1~2h,继续升温至350~550℃保温2~5h,继续升温至700~800℃,并充入氩气或氦气,使真空度保持在5.0
×
10-2
~1.0
×
10-1
pa之间,保温3~10h,抽真空使真空度低于1.0
×
10-2
pa,继续升温至850~950℃,保温10~25h,充入氩气或氦气至85~100kpa进行冷却,待冷却至温度低于70℃时转入热处理炉,抽真空至真空度低于1pa进行热处理,热处理温度为450~650℃。
20.本发明至少包括以下有益效果:本发明在烧结钕铁硼生产过程中,利用有机添加剂作为介质,加入一定比例的纳米cu粉,在真空高温的条件下,优化组织结构,提升高温磁性能,降低热减磁率,改善烧结钕铁硼永磁体的热稳定性,取代传统增加重稀土使用量的工艺,从而大幅度的降低成本。
21.本发明的其它优点、目标和特征将部分通过下面的说明体现,部分还将通过对本发明的研究和实践而为本领域的技术人员所理解。
具体实施方式
22.下面结合具体实施方式对本发明做进一步的详细说明,以令本领域技术人员参照说明书文字能够据以实施。
23.应当理解,本文所使用的诸如“具有”、“包含”以及“包括”术语并不排除一个或多个其它元件或其组合的存在或添加。
24.需要说明的是,下述实施方案中所述实验方法,如无特殊说明,均为常规方法,所述试剂和材料,如无特殊说明,均可从商业途径获得;在本发明的描述中,需要说明的是,除
非另有明确的规定和限定,术语“安装”、“相连”、“设置”应做广义理解,例如,可以是固定相连、设置,也可以是可拆卸连接、设置,或一体地连接、设置。对于本领域的普通技术人员而言,可以具体情况理解上述术语在本发明中的具体含义。术语“横向”、“纵向”、“上”、“下”、“前”、“后”、“左”、“右”、“竖直”、“水平”、“顶”、“底”、“内”、“外”等指示的方位或位置关系,仅是为了便于描述本发明和简化描述,并不是指示或暗示所指的装置或元件必须具有特定的方位、以特定的方位构造和操作,因此不能理解为对本发明的限制。
25.需要说明的是,下述实施方案中所述实验方法,如无特殊说明,均为常规方法,所述试剂和材料,如无特殊说明,均可从商业途径获得。
26.《实施例1》
27.一种re-fe-b系永磁体的制备方法,包括以下步骤:
28.步骤一、将粒径为500nm的cu细粉,按35%质量比与正庚烷、辛酸甲酯的混合溶液配制成混合悬浮液a,其中正庚烷与辛酸甲酯的质量比为1:3;
29.步骤二、选取成分为pr、nd、ce、b、cu、co、ga、zr、fe各金属元素按3:10:1:5.6:0.1:1.5:0.25:0.15:78.4的原子百分比的配方,经过配料、熔炼、氢化处理后得到粗磁粉,然后在气流磨制粉过程中将配好的混合悬浮液a,按质量比为5
‰
的比例,以一定的速率添加至粗磁粉中,经过气流磨磨机内部的碰撞将混合悬浮液a包覆于粗磁粉中,随机内的惰性气体旋流带入出料粉罐内,获得钕铁硼粗磁粉;
30.步骤三、向密闭全自动压机的模具上涂抹异丙醇作为脱模剂,在氧含量低于50ppm的条件下,采用一次成型工艺将所述钕铁硼粗磁粉压制成生坯块,生坯块的密度为4.4g/cm3,机械手将生坯块码于料舟内,传送至真空恒温箱内,设置真空度为1pa,温度为200℃,将生坯块表面的悬浮液、脱模剂(异丙醇)、水分烘干除掉,处理时间为2h;
31.步骤四、烘干处理完成后,密封对接周转入炉车,通过入炉车将生坯块运转至真空烧结炉,经过高真空低温加热再次将生坯表面的悬浮液、脱模剂(异丙醇)、水分及其他引入的水气进一步除掉,具体操作为在真空度为1.0
×
10-2
pa以下,升温至150℃,保温0.5h,中间充入一次氩气进行洗炉,压力为50pa,继续升温至380℃保温0.5h,继续升温至500℃,保温2h,继续升温至800℃,保温5h,继续升温至1040℃,进行高温最终烧结致密,保温5h,充入氩气或氦气至85~100kpa进行冷却,待冷却至70℃以下后出炉,获得烧结钕铁硼磁体块;
32.步骤五、将所述烧结钕铁硼磁体块经过磨床、多线切割机加工成29.5*11.5*1.89的磁片,然后通过旋转辊轮,将dy金属粉、无水乙醇和聚乙烯醇缩丁醛按照18:10:1的质量比配制成的混合悬浮液b涂覆于磁片的表面上,涂覆量比例为0.7%,然后经过真空低温加热将悬浮溶液b中的无水乙醇及表面吸附的水分烘干除掉,处理后的磁片在氧含量低于50ppm的封闭码片箱中码于高密度的石墨料舟内,码片箱对接真空渗透炉,在渗透炉的氧含量达到50ppm以下后,升起渗透炉门,将码好的磁片送入渗透炉内,对渗透炉抽真空,在真空度为1.0
×
10-2
pa以下,升温至150℃,保温2h,继续升温至350℃保温5h,继续升温至700℃,并充入氩气或氦气,使真空度保持在5.0
×
10-2
~1.0
×
10-1
pa之间,保温10h,抽真空使真空度为1.0
×
10-2
pa以下,继续升温至890℃,保温25h,充入氩气或氦气至85~100kpa进行冷却,待冷却至70℃以下后,转入热处理炉,抽真空至1pa以下,开始升温,热处理温度为500℃,获得所述re-fe-b系永磁体。
33.《实施例2》
34.一种re-fe-b系永磁体的制备方法,包括以下步骤:
35.步骤一、将粒径为1500nm的cu细粉,按50%质量比与正庚烷、辛酸甲酯的混合溶液配制成混合悬浮液a,其中正庚烷与辛酸甲酯的质量比为1:3;
36.步骤二、选取成分为pr、nd、ce、b、cu、co、ga、ti、fe各金属元素按3.2:9.5:0.5:5.4:0.15:0.6:0.18:0.2:80.27的原子百分比的配方,经过配料、熔炼、氢化处理后得到粗磁粉,然后在气流磨制粉过程中将配好的混合悬浮液a,按质量比为2
‰
的比例,以一定的速率添加至粗磁粉中,经过气流磨磨机内部的碰撞将混合悬浮液a包覆于粗磁粉中,随机内的惰性气体旋流带入出料粉罐内,获得钕铁硼粗磁粉;
37.步骤三、向密闭全自动压机的模具上涂抹异丙醇作为脱模剂,在氧含量低于50ppm的条件下,采用一次成型工艺将所述钕铁硼粗磁粉压制成生坯块,生坯块的密度为4.45g/cm3,机械手将生坯块码于料舟内,传送至真空恒温箱内,设置真空度为1pa,温度为200℃,将生坯块表面的悬浮液、脱模剂(异丙醇)、水分烘干除掉,处理时间为2h;
38.步骤四、烘干处理完成后,密封对接周转入炉车,通过入炉车将生坯块运转至真空烧结炉,经过高真空低温加热再次将生坯表面的悬浮液、脱模剂(异丙醇)、水分及其他引入的水气进一步除掉,具体操作为在真空度为1.0
×
10-2
pa以下,升温至150℃,保温1.5h,中间充入一次氩气进行洗炉,压力为70pa,继续升温至380℃保温1.5h,继续升温至550℃,保温1h,继续升温至850℃,保温8h,继续升温至1060℃,进行高温最终烧结致密,保温7h,充入氩气或氦气至85~100kpa进行冷却,待冷却至70℃以下后出炉,获得烧结钕铁硼磁体块;
39.步骤五、将所述烧结钕铁硼磁体块经过磨床、多线切割机加工成29.5*11.5*1.89的磁片,然后通过旋转辊轮,将tb金属粉、无水乙醇和聚乙烯醇缩丁醛按照18:10:1的质量比的混合悬浮液b涂覆于磁片的表面上,涂覆量比例为0.4%,然后经过真空低温加热将悬浮溶液b中的无水乙醇及表面吸附的水分烘干除掉,处理后的磁片在氧含量低于50ppm的封闭码片箱中码于高密度的石墨料舟内,码片箱对接真空渗透炉,在渗透炉的氧含量达到50ppm以下后,升起渗透炉门,将码好的磁片送入渗透炉内,对渗透炉抽真空,在真空度为1.0
×
10-2
pa以下,升温至150℃,保温1h,继续升温至450℃保温3h,继续升温至800℃,并充入氩气或氦气,使真空度保持在5.0
×
10-2
~1.0
×
10-1
pa之间,保温5h,抽真空使真空度为1.0
×
10-2
pa以下,继续升温至910℃,保温15h,充入氩气或氦气至85~100kpa进行冷却,待冷却至70℃以下后,转入热处理炉,抽真空至1pa以下,开始升温,热处理温度为450℃,获得所述re-fe-b系永磁体。
40.《对比例1》
41.与实施例1对比,利用传统增加稀土使用量的工艺制备re-fe-b系永磁体,包括以下步骤:
42.步骤一、选取成分为pr、nd、ce、b、cu、co、ga、zr、fe各金属元素按3:10:1:5.6:0.1:1.5:0.25:0.15:78.4的原子百分比的配方,经过配料、熔炼、氢化处理、气流磨制粉及细粉混合后,获得钕铁硼粗磁粉;
43.步骤二、向密闭全自动压机的模具上涂抹异丙醇作为脱模剂,在氧含量低于50ppm的条件下,采用一次成型工艺将所述钕铁硼粗磁粉压制成生坯块,生坯块的密度为4.4g/cm3,机械手将生坯块码于料舟内,传送至真空恒温箱内,设置真空度为1pa,温度为200℃,将生坯块表面的脱模剂(异丙醇)、水分烘干除掉,处理时间为2h;
44.步骤三、烘干处理完成后,密封对接周转入炉车,通过入炉车将生坯块运转至真空烧结炉,经过高真空低温加热再次将生坯表面的脱模剂(异丙醇)、水分及其他引入的水气进一步除掉,具体操作为在真空度为1.0
×
10-2
pa以下,升温至150℃,保温0.5h,中间充入一次氩气进行洗炉,压力为50pa,继续升温至380℃保温0.5h,继续升温至500℃,保温2h,继续升温至800℃,保温5h,继续升温至1040℃,进行高温最终烧结致密,保温5h,充入氩气或氦气至85~100kpa进行冷却,待冷却至70℃以下后出炉,获得烧结钕铁硼磁体块;
45.步骤四、将所述烧结钕铁硼磁体块经过磨床、多线切割机加工成29.5*11.5*1.89的磁片,然后通过旋转辊轮,将dy金属粉、tb金属粉、无水乙醇和聚乙烯醇缩丁醛按照15:3:10:1的质量比配制成混合悬浮液b涂覆于磁片的表面上,涂覆量比例为0.7%,然后经过真空低温加热将悬浮溶液b中的无水乙醇及表面吸附的水分烘干除掉,处理后的磁片在氧含量低于50ppm的封闭码片箱中码于高密度的石墨料舟内,码片箱对接真空渗透炉,在渗透炉的氧含量达到50ppm以下后,升起渗透炉门,将码好的磁片送入渗透炉内,对渗透炉抽真空,在真空度为1.0
×
10-2
pa以下,升温至150℃,保温2h,继续升温至350℃保温5h,继续升温至700℃,并充入氩气或氦气,使真空度保持在5.0
×
10-2
~1.0
×
10-1
pa之间,保温10h,抽真空使真空度为1.0
×
10-2
pa以下,继续升温至890℃,保温25h,充入氩气或氦气至85~100kpa进行冷却,待冷却至70℃以下后,转入热处理炉,抽真空至1pa以下,开始升温,热处理温度为500℃,获得所述re-fe-b系永磁体。
46.《对比例2》
47.一种re-fe-b系永磁体的制备方法,与对比例1的步骤基本一致,唯一不同的是步骤四里将dy金属粉、无水乙醇和聚乙烯醇缩丁醛按照18:10:1的比例配制成混合悬浮液b涂覆于磁片的表面上,涂覆量比例为0.7%。
48.《对比例3》
49.与实施例2对比,利用传统增加稀土使用量的工艺制备re-fe-b系永磁体,包括以下步骤:
50.步骤一、选取成分为pr、nd、ce、b、cu、co、ga、ti、fe各金属元素按3.2:9.5:0.5:5.4:0.15:0.6:0.18:0.2:80.27的原子百分比的配方,经过配料、熔炼、氢化处理、气流磨制粉及细粉混合后,获得钕铁硼粗磁粉;
51.步骤二、向密闭全自动压机的模具上涂抹异丙醇作为脱模剂,在氧含量低于50ppm的条件下,采用一次成型工艺将所述钕铁硼粗磁粉压制成生坯块,生坯块的密度为4.45g/cm3,机械手将生坯块码于料舟内,传送至真空恒温箱内,设置真空度为1pa,温度为200℃,将生坯块表面的脱模剂(异丙醇)、水分烘干除掉,处理时间为2h;
52.步骤三、烘干处理完成后,密封对接周转入炉车,通过入炉车将生坯块运转至真空烧结炉,经过高真空低温加热再次将生坯表面的脱模剂(异丙醇)、水分及其他引入的水气进一步除掉,具体操作为在真空度为1.0
×
10-2
pa以下,升温至150℃,保温1.5h,中间充入一次氩气进行洗炉,压力为70pa,继续升温至380℃保温1.5h,继续升温至550℃,保温1h,继续升温至850℃,保温8h,继续升温至1060℃,进行高温最终烧结致密,保温7h,充入氩气或氦气至85~100kpa进行冷却,待冷却至70℃以下后出炉,获得烧结钕铁硼磁体块;
53.步骤四、将所述烧结钕铁硼磁体块经过磨床、多线切割机加工成29.5*11.5*1.89的磁片,然后通过旋转辊轮,将tb金属粉、无水乙醇和聚乙烯醇缩丁醛按照18:10:1的比例
的混合悬浮液b涂覆于磁片的表面上,涂覆量比例为0.5%,然后经过真空低温加热将悬浮溶液b中的无水乙醇及表面吸附的水分烘干除掉,处理后的磁片在氧含量低于50ppm的封闭码片箱中码于高密度的石墨料舟内,码片箱对接真空渗透炉,在渗透炉的氧含量达到50ppm以下后,升起渗透炉门,将码好的磁片送入渗透炉内,对渗透炉抽真空,在真空度为1.0
×
10-2
pa以下,升温至150℃,保温1h,继续升温至450℃保温3h,继续升温至800℃,并充入氩气或氦气,使真空度保持在5.0
×
10-2
~1.0
×
10-1
pa之间,保温5h,抽真空使真空度为1.0
×
10-2
pa以下,继续升温至910℃,保温15h,充入氩气或氦气至85~100kpa进行冷却,待冷却至70℃以下后,转入热处理炉,抽真空至1pa以下,开始升温,热处理温度为450℃,获得所述re-fe-b系永磁体。
54.《对比例4》
55.一种re-fe-b系永磁体的制备方法,与对比例3的步骤基本一致,唯一不同的是步骤四里将tb金属粉、无水乙醇和聚乙烯醇缩丁醛按照18:10:1的比例配制成混合悬浮液b涂覆于磁片的表面上,涂覆量比例为0.4%。
56.《re-fe-b系永磁体的磁性能试验》
57.上述实施例1~2和对比例1~4的制备得到的re-fe-b系永磁体,每组取三个样品,测定其在常温和高温下的剩磁、内禀矫顽力,测定结果如表1所示:
58.实施例1为利用本发明所述方法制备的dy-fe-b系永磁体,其利用纳米级铜细粉,按35%的质量比与正庚烷、辛酸甲酯的混合溶液配制成混合悬浮液a,其中正庚烷与辛酸甲酯的质量比为1:3,并将混合悬浮液a均匀的包覆于粗磁粉中,烧结,再将dy金属粉、无水乙醇和聚乙烯醇缩丁醛按照18:10:1的质量比配制成的混合悬浮液b涂覆于磁片的表面上,涂覆量比例为0.7%。对比例1中采用传统增加稀土使用量的工艺制备re-fe-b系永磁体,其将与实施例1配方一样的粗磁粉直接进行烧结,再将dy金属粉、tb金属粉、无水乙醇和聚乙烯醇缩丁醛按照15:3:10:1的质量比配制成混合悬浮液b涂覆于磁片的表面上,涂覆量比例为0.7%,虽然涂覆量比例与实施例1一致,但重稀土金属的摩尔量增加了,即增加了重稀土金属的使用量。对比例2中采用与对比例1相同的工艺方法,但重稀土金属的使用量与实施例1一致,即将dy金属粉、无水乙醇和聚乙烯醇缩丁醛按照18:10:1的质量比配制成的混合悬浮液b涂覆于磁片的表面上,涂覆量比例为0.7%。实施例1与对比例1~2的试验结果对比显示,实施例1中采用本发明所述制备方法,即使不增加重稀土金属的使用量,也能达到与对比例2相近的磁性能,且磁性能优于对比例3。另外与对比例2相比,实施例1因未增加重稀土金属的使用量,使成本节约了5%左右。
59.表1
[0060][0061]
同样的,实施例2为利用本发明所述方法制备的dy-fe-b系永磁体,其利用粒度为1500nm的cu细粉,按50%的质量比与正庚烷、辛酸甲酯的混合溶液配制成混合悬浮液a,均匀的包覆于粗磁粉中,烧结,再将tb金属粉、无水乙醇和聚乙烯醇缩丁醛按照18:10:1的质量比配制成的混合悬浮液b涂覆于磁片的表面上,涂覆量比例为0.4%。对比例3中采用传统增加稀土使用量的工艺制备re-fe-b系永磁体,其将与实施例2配方一样的粗磁粉直接进行烧结,再将tb金属粉、无水乙醇和聚乙烯醇缩丁醛按照15:3:10:1的质量比配制成混合悬浮液b涂覆于磁片的表面上,涂覆量比例为0.5%。对比例4中采用与对比例3相同的工艺方法,但重稀土金属的使用量与实施例1一致。实施例2与对比例3~4的试验结果对比显示,实施例2中采用本发明所述制备方法,即使不增加重稀土金属的使用量,也能达到与对比例3相近的磁性能,且磁性能优于对比例4。另外与对比例3相比,实施例2因未增加重稀土金属的使用量,使成本节约了6.3%。
[0062]
《re-fe-b系永磁体的热稳定性能试验》
[0063]
上述实施例1~2和对比例1~4的制备得到的re-fe-b系永磁体,每组取三个样品,置于高温干燥箱中,测定其在130℃
×
2h条件下的热减磁,测定结果如表2所示:
[0064]
表2
[0065][0066]
试验结果显示,实施例1中制得的永磁体的热稳定性明显优于对比例2,说明利用本技术所述制备方法可有效提高re-fe-b系永磁体的热稳定性能;实施例1的减率与对比例1相差不大,说明利用本技术所述制备方法,即使再不增加重稀土金属使用量的情况下,也能达到与之相同的技术效果。
[0067]
同样,实施例2中制得的永磁体的热稳定性明显优于对比例4,说明利用本技术所述制备方法可有效提高re-fe-b系永磁体的热稳定性能;实施例2的减率与对比例3相差不大,说明利用本技术所述制备方法,即使再不增加重稀土金属使用量的情况下,也能达到与之相同的技术效果,从而可以大幅度降低生产成本,同时也提高了稀土资源高效利用。
[0068]
综上所述,本发明在烧结钕铁硼生产过程中,利用有机添加剂作为介质,加入一定
比例的纳米cu粉,在真空高温的条件下,优化组织结构,提升高温磁性能,降低热减磁率,改善烧结钕铁硼永磁体的热稳定性,取代传统增加重稀土使用量的工艺,从而大幅度的降低成本。
[0069]
尽管本发明的实施方案已公开如上,但其并不仅仅限于说明书和实施方式中所列运用,它完全可以被适用于各种适合本发明的领域,对于熟悉本领域的人员而言,可容易地实现另外的修改,因此在不背离权利要求及等同范围所限定的一般概念下,本发明并不限于特定的细节。