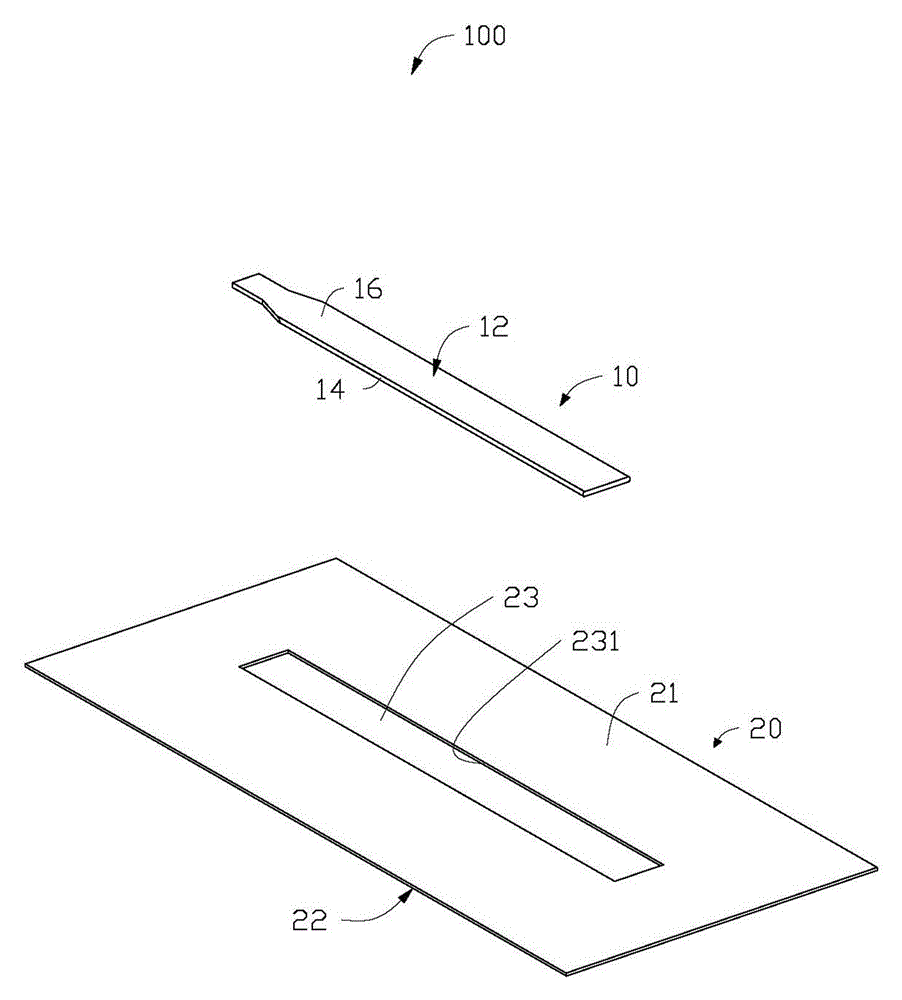
本发明涉及散热领域,尤其涉及一种散热器及其制造方法。
背景技术:
:现有技术中在计算机及许多其他电子产品里,由于电子元件在工作过程中不断产生热量,因此需要进一步装设散热装置来辅助电子元件的散热,以免热量堆积而影响电子元件工作的正常进行。一般简易的散热装置通常包括一个热管和金属板材,该热管通常采用固定连接的方式连接在金属板材上,因此整体散热装置的厚度为热管、金属板材以及两者之间用于固定连接的层三者的厚度之和。然而随着电子产品愈来愈趋向轻薄化,上述这种散热装置的总厚度显然不符合轻薄化的需求。技术实现要素:有鉴于此,有必要提供一种更轻薄化的散热器及其制造方法。一种散热器,包括热管和金属板,所述金属板包括第一表面和第二表面,所述金属板上形成开口,所述开口贯穿所述第一表面和第二表面,所述热管容置在所述开口中并与所述开口紧配合。本发明实施方式提供的散热器中,在金属板中开设开口,以使热管容置在该开口中,而不同于现有技术中两者叠加设置的方式,从而节省了热管叠加的厚度,使该散热器的厚度更加薄,符合产品薄形化的需求。附图说明图1是本发明第一实施方式提供的散热器的示意图。图2是图1中的散热器的分解图。图3是图1中的散热器已经完成焊锡和压扁热管工序的沿III-III的部分放大剖面图。图4是图3中的散热器还未完成焊锡和压扁热管工序的剖面图。图5是本发明第二实施方式提供的散热器的示意图。图6是图5中的散热器的分解图。图7是图5中的散热器已经完成焊锡和压扁热管工序的沿VII-VII的剖面图。图8是图7中的散热器还未完成焊锡和压扁热管工序的部分放大剖面图。图9是本发明第三实施方式提供的散热器的示意图。主要元件符号说明散热器100、100’、100’’热管10、10’壳体12侧部14表面16金属板20、20’、20’’第一表面21、24第二表面22、25开口23、23’、23’’内壁231、231’’凸部232凹部233空隙234散热鳍片组30鳍片32如下具体实施方式将结合上述附图进一步说明本发明。具体实施方式请参见图1至图2,图1为本发明第一实施方式提供的散热器100包括热管10和金属板20。所述散热器100用于为电子设备中的发热电子元件散热。所述电子设备可以为平板电脑、智能手机、一体机、摄影摄像机等薄型化产品。所述发热电子元件可以为上述电子设备中的例如CPU等元件。所述热管10为普通热管,其包括壳体12和密封于壳体12内的工作介质(图未标出)。该壳体12的内壁还可以形成毛细结构以加速工作介质的回流,提高热管10的散热效率。所述热管10包括左右两个侧部14和上下两个表面16。所述热管10的形状并不限定,可以根据需求选择各种形状的热管10。在本实施方式中,为了达到更好的薄形化的效果,所述热管10为扁平状,所述热管10的厚度小于其宽度,上下两个表面16均为平整的平面。请同时参阅图3和4,所述金属板20与所述热管10固定连接。所述金属板20贴设于发热电子元件上,从而将发热电子元件发出的热量全部经由金属板20传递至热管10以使发热电子元件的热量能够全部快速散发。所述金属板20可以为铜板、铝板等具有较高导热性能的金属板体。所述金属板20包括相对的第一表面21和第二表面22。所述热管10的厚度可大于或等于该金属板20的厚度。所述金属板20上开设有一个开口23。所述开口23具有内壁231。在本实施方式中,所述开口23的形状和尺寸与所述热管10的形状以及尺寸相匹配,即,所述内壁231为四个首尾依次连接的平面,从而使热管10容置于该开口23中,并使热管10的两个侧部14分别贴设在开口23的内壁231上。当然,当所述开口23的四角形成倒角时,所述内壁231的数量不止四个,而可以是大于四个的若干个。所述开口23的宽度与所述热管10的宽度大致相等,开口23的长度大于所述热管10的长度。所述热管10的两个表面16分别与金属板20的相对的第一表面21和第二表面22平齐。所述热管10与所述开口23为紧配合。进一步的,所述热管10的侧部14与金属板20的开口23之间的连接处还可通过焊料焊接,以进一步加强热管10与金属板20的固定连接。在本第一实施方式中,所述金属板20为一平板结构。金属板20的相对两个表面均为平面。当然,在不同的实施方式中,所述热管10的两个表面16可视实际需要而与所述金属板20的第一表面21和/或第二表面22平齐或超出所述金属板20的第一表面21和/或第二表面22。本发明第一实施方式提供的散热器100中,在金属板20中开设开口23,以使热管10容置在该开口23中,而不同于现有技术中两者叠加设置的方式,从而节省了热管10叠加的厚度,使该散热器100的厚度更加薄,符合产品薄形化的需求。本发明的上述第一实施方式提供的散热器100可采用以下方法制成:提供一个热管10’和一个金属板20;在金属板20上开设开口23;将热管10’容置在所述开口23中;对热管10’进行打扁工序使其形成厚度减小的热管10,热管10与开口23形成紧配合;以及在热管10与开口23的连接处通过焊料焊接。在上述制造方法中,请同时参阅图4,热管10’的厚度略大于所述金属板20的厚度,而在热管10’经过打扁工序后形成了热管10后,热管10的厚度可大于或等于所述金属板20的厚度。所述金属板20可通过现有技术中的方法制成,例如,可以是铝挤或压铸成型制成。所述开口23可通过模具或机械加工制成。在对热管10’进行打扁工序的过程完成之后,使热管10与开口23之间形成紧配合,从而使热管10与金属板20之间形成初级的紧固连接,为后续两者之间的固定做铺垫,防止热管10与金属板20之间由于间隙过大而造成两者在后续的焊接中无法快速对位而增加制作工序、延长制作时间。然后再在两者的连接处采用焊接的方式使两者完全连接固定。进一步由于热管10和金属板20之间已形成了紧配合连接,因此可减少用来弥补两者之间过大的间隙而使用焊接材料的用量。请参图5至图8,本发明第二实施方式提供的散热器100’,其包括热管10、金属板20’和散热鳍片组30。与第一实施方式不同的是,所述热管10的长度大于所述金属板20’的长度,所述金属板20’为折板结构。所述金属板20’的同一侧包括位于第一平面内的第一表面24和位于第二平面内的第二表面25,第一表面24和第二表面25之间倾斜连接,两者之间具有一个高度差。进一步的,第一表面24与第二表面25之间的高度差可等于所述热管打扁后的厚度。在其他实施方式中,所述高度差也可以小于所述热管打扁后的厚度,以使热管的至少一个表面超出该第一表面24或第二表面25。所述开口23’同时贯穿第一表面24与第二表面25。所述热管10的一端容置在所述金属板20’的开口23’中,另一端伸出所述金属板20’并与散热鳍片组30热连接。所述热管10与所述金属板20’连接的一端为蒸发段,另一端与散热鳍片组30连接的为冷凝段。所述热管10的蒸发段容置于所述开口23’中,超出所述开口23’的部分则叠置在所述金属板20’的第二表面25上,而热管10的另一表面与所述金属板20’的第一表面24平齐。因此热管10与金属板20’两者装配在一起的厚度等于金属板20’的厚度。当然,在其他实施方式中,热管10的另一表面也可超出所述金属板20’的第一表面24,使热管10与金属板20’两者装配在一起的厚度大于金属板20’的厚度。该第二实施方式中的散热器100’也可采用上述第一实施方式中的散热器100的制造方法制成。同样的,在热管10进行打扁工序之前,其厚度大于所述金属板20’的第一表面24和第二表面25之间的高度差。所述散热鳍片组30连接于所述热管10的冷凝段,用于加速热管10传递至冷凝段的热量的散发,从而增强散热器100’的散热器效率。所述散热鳍片组30包括若干并排且间隔设置的鳍片32。这些鳍片32沿热管10的长度方向依次间隔排列。请参阅图9,为本发明第三实施方式提供的散热器100’’,其包括热管10和金属板20’’。与第一实施方式不同的是,所述金属板20’’上开设的开口23’’的内壁231’’为非平面结构。具体的,每一个内壁231’’具有凸部232和凹部233。所述凸部232和凹部233交替连接形成波浪形结构。所述热管10容置在所述金属板20’’的开口23’’中,热管10的侧部14与所述开口23’’的内壁231’’的凸部232紧配合,并与所述凹部233之间形成空隙234。可以理解的是,对于本领域的普通技术人员来说,可以根据本发明的技术构思做出其它各种相应的改变与变形,而所有这些改变与变形都应属于本发明权利要求的保护范围。当前第1页1 2 3