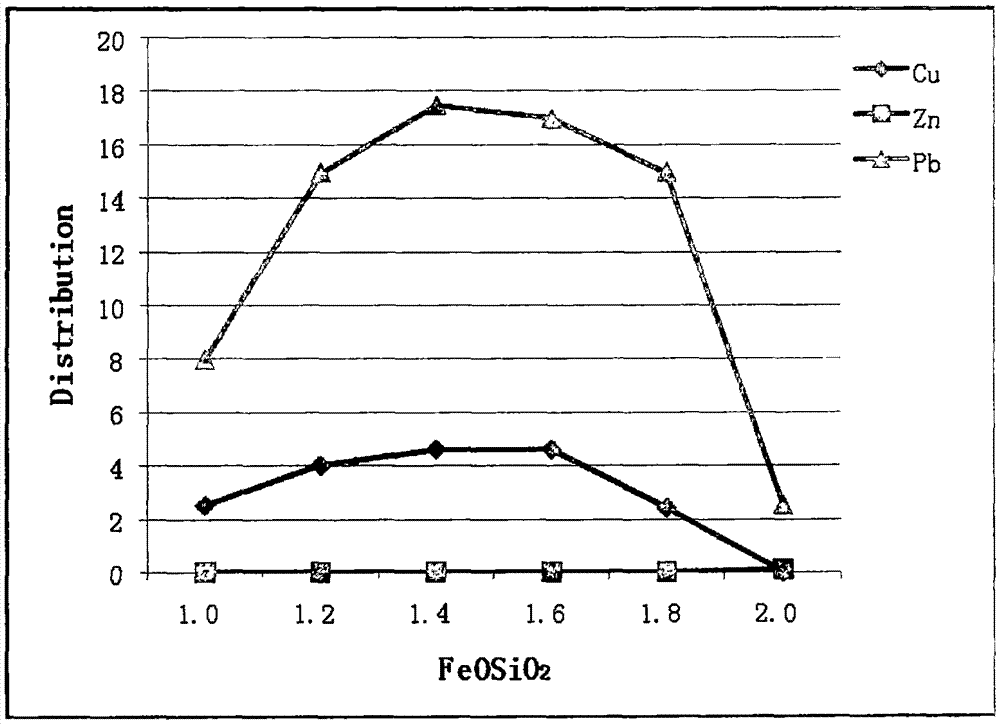
本发明涉及冶金
技术领域:
,具体是熔融液态高铅渣节能还原熔炼方法。
背景技术:
:我国的铅生产量和消费量居世界第一。铅渣一般是火法炼铅的冶炼渣,铅渣中含铁21-31%、含锌2-15%、含铅0.02-3%。目前铅渣大量堆存,占用土地资源并污染环境。铅渣的处理主要集中于回收铅渣中铅锌和稀散金属、将铅渣作井下矿坑的充填材料、生产玻璃及陶瓷、生产砖和砌块水泥等建材等,但铅渣中大量的铅与锌资源未得到回收。锌的用途十分广泛,在国民经济中占有重要的地位,锌的熔点较低,熔体流动性好,有较好的抗腐蚀性能,主要用于镀锌工业,常作为钢铁的保护层,如镀锌的板材管件等,其消耗量占世界锌消耗量的50%。而我国铅渣量大,渣中的铅、锌含量高,因此将铅渣中的铅、锌资源作为原料不失为弥补我国矿石资源长期短缺的一种途径。目前铅渣中铅、锌资源的回收利用缺乏有效的方法,使得铅渣中铅、锌资源得不到高效回收利用。可以说铅渣中的铅、锌资源的回收利用是冶金和环境领域哑待解决的难题,迫切需要一种节能、高效、流程短的工艺方法回收铅渣中伴生的资源。技术实现要素:本发明的目的在于提供流程简单、处理效果好、成本低熔融液态高铅渣节能还原熔炼方法,以解决上述
背景技术:
中提出的问题。为实现上述目的,本发明提供如下技术方案:熔融液态高铅渣节能还原熔炼方法,利用还原剂对熔融液态铅渣进行直接还原,还原剂的加入量是熔融液态铅渣质量的3.25~3.5%;还原温度为1200~1225℃;还原时间为30~60min。作为本发明进一步的方案:还原剂采用co、c、固体煤、h2或ch4。作为本发明进一步的方案:还原剂采用固体煤。作为本发明进一步的方案:还原剂采用固体无烟煤。作为本发明进一步的方案:熔融液态铅渣采用的渣型是cao/sio2在0.4~0.8之间,feo/sio2在1.2~1.8之间。作为本发明进一步的方案:feo/sio2=1.5。与现有技术相比,本发明的有益效果是:本发明克服了高铅体系下铅、锌回收率低的难题,流程简单,处理效果好,能高效回收锌等有价金属,解决大量废弃渣堆存造成的环境污染及资源浪费问题。本发明直接冶炼处理熔融铅渣,充分利用熔融铅氧化渣的热焓,节省能源。本发明的冶炼方法采用直接还原方法,提高碳质还原剂的利用率,节省冶炼成本。附图说明图1是铁硅比对铅锌铜的回收率的影响;图2是铁硅比对铅锌铜分配的影响;图3是钙硅比对铅锌铜回收率的影响;图4是钙硅比对铅锌铜分配的影响;图5是温度对无烟煤的co2还原率的影响;图6是还原剂煤比对试验的影响效果;图7是还原剂煤比对金属回收率的影响;图8是还原温度对金属回收率的影响(时间60min);图9是还原温度对金属回收率的影响(时间30min);图10是还原时间对金属回收率的影响(温度1200℃);图11是还原时间对金属回收率的影响(温度1225℃);图12是还原时间对金属回收率的影响(温度1250℃);图13是钙硅比0.45还原温度对金属回收率的影响;图14是不同钙硅比对金属回收率的影响;图15是不同铁硅比对金属回收率的影响。具体实施方式下面将结合本发明实施例,对本发明实施例中的技术方案进行清楚、完整地描述,显然,所描述的实施例仅仅是本发明一部分实施例,而不是全部的实施例。基于本发明中的实施例,本领域普通技术人员在没有做出创造性劳动前提下所获得的所有其他实施例,都属于本发明保护的范围。实施例11.1高铅渣还原过程的渣型选择的实验研究铅渣是复杂的多元系,是由各种氧化物组成的,它们相互结合而形成化合物、固溶体、液熔体及共晶混合物。具体地说,炉渣是由各种金属的硅酸盐、亚铁酸盐及铝酸盐等所组成;此外,含有少量的金属硫化物、金属及气体。sio2、feo和cao是铅炉渣的主要成分,但相对其他有色金属炉渣而言,高cao、高zno含量又是铅炉渣的特点。对铅冶炼炉渣的要求主要有:(1)炉渣成分必须符合熔炼时熔剂消耗量最少的要求;(2)炉渣的熔点合适;(3)炉渣的粘度要小;(4)炉渣比重要小;(5)炉渣的表面性质(表面张力、界面张力等)对炉渣与金属或锍的分离起着重要的作用,此外,炉渣对耐火材料的腐蚀也与炉渣的表面性质有较大的关系。为了降低渣含铅,提高原料综合利用程度和处理高锌物料,广泛采用高锌高钙渣型。本发明中,炉渣拟采用铁钙硅酸盐的熔合体,并选择合适的铁硅比和钙硅比。1.1.1铁硅比对高铅渣还原过程有价金属分布的影响图1为feo/sio2比对高铅渣还原过程中铅锌铜回收率的影响。由图可知,铅和铜主要存在于金属相中,锌则主要存在于渣中。铅和铜的回收率均呈先增大后减小的趋势,但两者趋势有明显的不同。在feo/sio2比例为1.0-1.8的范围内,pb回收率呈现平稳增长的趋势,在feo/sio2=1.8时达到最高的回收率84.8%,进一步增加feo/sio2比例将导致pb回收率急剧下降。而cu回收率在feo/sio2=1.25时达到最高值(81.7%),增大或减小feo/sio2比均将导致回收率大幅度的下降,当feo/sio2比增大至2.0时甚至将降低至20%。在金属相中基本没有检出锌,说明在实验所检测的feo/sio2比例下锌主要是进入渣相中,因此锌的回收率主要通过渣中锌含量来考察。如图1所示,其随feo/sio2变化显示出与pb、cu 相反的趋势。锌在feo/sio2为1.5时在渣中含量最少(75%)增大和降低feo/sio2将提高锌的回收率,最高可达到90%。图2为feo/sio2对高铅渣还原过程中铅锌铜分配行为的影响。由图可知,随着feo/sio2的增加,铅、铜的分布呈先增长后减小的趋势,而锌的则由于主要进入渣相而在实验测试的feo/sio2范围内分配比平稳地保持在0附近。值得注意的是,不同的feo/sio2比例下,pb的分配比均高于cu,且feo/sio2比对pb分配比的影响非常明显。当feo/sio2比从1增加到1.5时,分配比从8.2增大到18.6,增长幅度达到1.2倍,进一步增加feo/sio2比则导致分配比急剧下降,feo/sio2=2时分配比下降至最低(1.6)。cu分配比受feo/sio2比的影响相对较小,除feo/sio2=2.0时分配比为0.4外,其他比例下分配比均在2以上,且与最高分配比4.9(feo/sio2=1.5)差值不大。这些结果与图1所示结果具有较好的对应性,说明在feo/sio2=1.5的条件下pb、cu可以获得在金属相中最大的分配,而锌则主要进入渣中,因此feo/sio2=1.5为最佳条件。1.1.2钙硅比对高铅渣还原过程有价金属分布的影响图3为cao/sio2对有价金属回收率以及在金属、渣相中分配比的影响。实验结果如图2所示。由图可知,中可以看到在高铅渣还原中不同钙硅比时铅锌铜回收率的变化。当cao/sio2在0.4~0.8之间变化时,铅、铜的回收率上升而锌的回收率下降。在cao/sio2=0.8时,pb达到最高的回收率84.9%,zn的回收率在此时则降低至最低。继续提高cao/sio2比将使得pb的回收率降低,而铜和锌的回收率则会继续保持上升的趋势,并分别达到最高点(81.3%,100%),在实验所用最高的cao/sio2(1.4)下,铅和铜回收率均大幅降低,分别为51%和10%。锌的回收率则继续保持在最高点。图4显示了采用不同钙硅比时铅锌铜在金属相和渣相中的分配比。可以看出,cao/sio2为0.8时铅、铜的分配比均达到最大值,锌的分配比则在整个测试范围内基本保持在0。在其他的cao/sio2比下,铅、铜的分配分别在3.8和2左右波动,差别并不显著。值得一提的是,当cao/sio2比为1.4时,铅、铜分配比均下降至最低值。综上所述,液态高铅渣直接还原实验室所采用的渣型是cao/sio2在0.4~0.8,feo/sio2在1.2~1.8之间。1.2确定的渣型与传统鼓风炉熔炼渣的比较原来的常规铅烧结块为自熔疏松多孔的块状物,孔隙率一般为50%-60%,堆比重1.8-2.2,块度一般为50~150mm。烧结块中以硅酸铅和游离氧化铅形态存在的铅约占总铅量40%-60%,故在鼓风炉还原熔炼时,游离pbo在600℃时已大量被还原,各种硅酸铅在700~900℃时开始熔化并还原,其它金属氧化物熔体中铅化合物在熔化区被上升气流中的co及熔剂中的cao、feo所还原和置换,在焦点区,c直接参与了从熔体中还原硅酸铅中的铅。由于铅烧结块表面积大,co气固反应和碳的直接还原反应比较活跃,还原过程进行得很彻底。氧气底吹炉得到高铅渣为一种含铅高、致密的块状物料,堆比重3.05,比表面积小,气(co)-固(固态高铅渣)还原接触面积小,还原能力弱,和烧结块有很大的差别。铅鼓风炉还原熔炼所产炉渣特点是渣含zno较高,通常sio2、feo、cao和zno之和占渣总量的85%-90%。鼓风炉渣含铅一般为3%-5%,占熔炼过程总损失的60%-70%。鼓风炉熔炼铅在渣中的损失形态主要分为三类:①硅酸铅形态的化学损失;②以硫化铅溶解于渣中的物理损失;③以金属铅微粒夹杂的机械损失。一般来说,降低渣含铅是提高金属回收和企业经济效益的关键。一般炉渣中钙硅比为w(cao)/w(sio2)=0.4-0.8,w(feo)/w(sio2)=0.6-1.3。液态还原炉渣钙低锌高的铁硅渣型,且渣中铅含量小于2%,综合上面的实验,初步确定液态还原渣中w(cao)/w(sio2)<0.8,w(feo)/w(sio2)=0.6-1.4,主要是cao含量较低,同时铁含量较高。1.3还原终渣中氧化铅和金属铅的溶解行为还原渣中的相别有氧化铅相、砷酸铅相、铁酸锌相、尖晶石相、硅酸盐相、硫化物相及玻璃相。铅在该还原渣中主要有三种损失状态,一是氧化铅相、二是砷酸铅相,三是玻璃相,后者是铅的主要损失形式,而氧化铅和砷酸铅在该渣中的含量比较低。表1为对玻璃相进行的扫描电镜能谱分析,玻璃相中铅的平均含量为2.31%。表1玻璃相的基本化学组成(%)测点naalsipsclkcamnfeznbapbo12.885.6618.501.040.410.295.557.470.8211.134.731.861.5838.0823.096.0218.390.880.040.454.935.890.799.576.205.291.3037.1632.756.2319.050.600.310.415.427.190.7310.774.272.521.5638.1943.765.9719.260.720.460.374.814.890.837.737.343.622.2537.9953.705.2419.360.730.290.464.455.590.598.686.774.572.0537.5263.664.4618.480.460.300.394.095.880.619.048.044.503.9936.1073.195.3818.560.570.230.444.856.880.8011.126.532.331.8337.2983.214.6019.710.660.040.314.014.740.889.658.853.312.9137.1293.713.8919.080.660.260.513.466.641.009.955.894.234.2336.49103.635.1519.870.730.330.464.585.350.827.866.024.003.5137.69113.574.8919.230.720.060.324.266.590.508.756.923.263.8737.06123.644.2619.230.560.070.414.405.860.869.237.543.943.5136.49133.334.9919.720.690.100.314.666.200.798.366.893.562.9137.49142.275.0418.960.400.260.234.428.741.4211.515.501.292.3837.58153.105.5019.560.510.230.304.845.860.879.725.763.162.9637.63163.385.5419.50.420.240.425.026.280.8810.34.763.691.8837.69173.846.0620.370.390.210.395.545.930.679.154.722.571.5238.64183.225.0218.980.710.340.474.685.600.718.378.653.642.4537.16193.515.4318.760.670.60.424.666.400.838.296.574.282.0237.56203.656.6219.80.570.350.405.434.790.847.725.263.702.5138.36214.085.4319.150.400.400.485.054.900.327.927.925.241.5037.21223.485.5319.950.810.270.325.674.690.617.497.044.551.5738.02233.397.1119.030.700.290.536.135.040.428.745.443.641.2738.27244.008.1619.250.450.230.136.125.740.618.243.863.880.3039.03253.995.1118.690.590.260.424.75.370.468.388.864.341.9836.85平均3.445.4919.220.620.260.394.875.940.759.116.413.642.3137.552突破了液态高铅渣还原过程气氛优化控制关键技术2.1高铅渣还原过程机制根据pb-s-o系氧位图,熔炼时铅液稳定存在的温度区域应高于900℃,同时为保证氧气底吹炉渣的过热要求,冶炼的温度区域一般控制在1000-1150℃,排出的高铅渣温度在900℃以上。高铅渣中的铅主要以氧化铅和硅酸铅存在,通过热力学计算,co、c、h2、ch4都可作为还原剂,考虑加入固体煤作为还原剂。pbo+c=pb+copbo+co=pb+co2pbo·sio2+c=pb+co+sio2pbo·sio2+co=pb+co2+sio2在还原熔炼中,氧化铅被co还原是其主要途径,而硅酸铅的还原一定是在有碱性氧化物(cao和feo)参与下,并且主要在炉料熔化后发生,其原因在于只有在熔融状态下硅酸铅才能与碱性氧化物、还原剂或co有良好接触,从而完成还原反应。pbo·sio2+cao+co=cao·sio2+pb+co22pbo·sio2+2cao+2co=2cao·sio2+2pb+2co2pbo·sio2+feo+co=feo·sio2+pb+co22pbo·sio2+2feo+2co=2feo·sio2+2pb+2co22pbo·sio2+cao+feo+2co=cao·feo·sio2+2pb+2co2pbo·fe2o3+co=pb+fe2o3+co2fe2o3+co=2feo+co2显然,液态铅渣直接还原与高铅渣铸块鼓风炉还原的不同是因为铅渣入炉状态和方式的不同造成的。在鼓风炉还原高铅渣铸块过程中,在以焦炭作还原剂时,氧化铅和硅酸铅的还原是包含了与还原剂固(铅的氧化物)一固(焦炭)或固(铅的氧化物)-气(co)接触,到液(熔融的铅的氧化物)一固(炽热焦炭)或液(熔融的铅的氧化物)-气(co)接触过程的。当高铅渣以液态方式进入还原过程时,由于不管是固体氧化铅还是液体氧化铅都是易还原的氧化物,而熔融的炉料又有利于硅酸铅的还原,所以液态铅渣的直接还原就显而易见了。2.2高铅渣还原还原气氛的调控在煤比3.5%,还原温度1250℃,时间60min时,在管式炉中进行铅渣的还原反应。在升温过程以及保温阶段,进行了气体的取样和成分测定,明确还原过程中气氛的变化过程。利用奥氏气体分析仪主要进行了co2、co和o2的分析测定,氧气的吸收剂为焦性没食子酸的碱性溶液,二氧化碳为酸性氧化物,一般采用苛性碱(koh)为吸收剂,用氯化亚铜氨性溶液做一氧化碳的吸收剂。具体检测结果如表2所示。由表可知,随着温度的升高,碳氧反应发生,生成一氧化碳和二氧化碳。同时一氧化碳含量增加并趋于稳定,二氧化碳含量降低并趋于稳定,co/co2比值逐渐增加。氧气和氮气的含量在还原过程中基本稳定。 温度1100℃之后,还原气氛的组成基本稳定,co含量基本在体积百分比60%左右。表2铅渣还原过程中气体的组成及变化2.3开展了高铅渣还原实验及锌富集技术研究以高铅渣为原料,于还原过程中考察主要金属铅、锌、铜、铁的走向,并确定合小试针对高铅渣原料,进行不同工艺参数研究,并考察主要金属铅、锌、铜、铁的走向。确定合理的还原参数并验证确定的确定的渣型。2.3.1还原剂煤的物化性能研究表3为试验所用还原剂为固体无烟煤的成分和物理性能分析结果由表可知该还原剂煤碳含量高,灰分低,孔隙度大。表3无烟煤物理化学分析表4为以co2作为气体介质,煤对二氧化碳的化学反应性分析结果。由表可知,各种 煤的反应性随煤化度的加深而减弱。因为碳和co2反应不仅在燃料的外表面进行,而且也在燃料内部微细孔隙的毛细管壁上进行,孔隙率愈高,反应的表面积愈大。不同煤化度煤的气孔率、化学结构不同,因此其反应性不同。褐煤的反应性最强,但当温度较高(900℃以上)时,反应性增高减慢。无烟煤的反应性最弱,但在较高温度时,随温度升高其反应性显著增强。煤的灰分组成与数量对其反应性也有明显的影响。碱金属和碱土金属对碳与co2的反应起着催化作用,使煤的反应性提高。图5为温度对无烟煤的co2还原率的影响,由图可知,煤的co2还原率α随着温度升高而增加,表明生成co量增加,煤的化学反应性随反应温度的升高而增强。表4无烟煤对co2化学反应性2.3.2还原剂煤用量图6和图7分别表示在高铅渣400g,温度1250℃,时间60min条件下,不同还原剂无烟煤用量对高铅渣的还原效果和有价金属回收率的影响,由图可知随着煤比的增加,铅渣的失重率增大,表明高铅渣中的各种氧化物被还原程度增强。渣中的铅含量逐渐降低,同时锌含量也逐渐降低。渣中的铁含量先略有增加然后逐渐降低。由图7可知,金属块中铅和铜的回收率随着煤比的增加而增加。而还原渣中锌和铁的回收率随着煤比增加而降低,尤其是煤比在3.5%以后,锌由于挥发进入烟气、铁由于还原进入金属都使还原渣中锌、铁含量降低。高铅渣原料中钙硅比为0.17,不同煤比还原后的 钙硅比大致还在0.17左右,表明还原剂煤中所含的cao和sio2对还原渣的渣型影响甚微,在后面研究中不考虑还原剂煤中所含化学成分的影响。试验表明,在煤比3.25%时,还原渣中铅含量2.41%,此时铅的回收率为98.11%,而锌的回收率为85.19%。在煤比3.5%时,还原渣中铅含量1.48%,此时铅的回收率为98.86%,而锌的回收率仅为82.91%。综合考虑建议煤比在3.25~3.5%。2.3.3还原剂温度的影响表5和表6分别为在煤比3.25%和3.5%,时间60min时,不同还原温度对高铅渣的还原效果。表7在煤比3.25%和3.5%,时间30min时,不同还原温度对高铅渣的还原效果。由表5、表6及图8可知,还原时间60min时,随着还原温度的升高,铅的回收率稍有增加,且煤比3.5%比煤比3.25%的铅回收率稍高,煤比高,则还原气氛高,利于铅的还原;锌的回收率降低比较明显,温度升高增加了锌的挥发。且煤比3.5%比煤比3.25%的锌回收率低,煤比高,则还原气氛高也增加了锌的挥发;铜的回收率呈现先增加再降低的趋势,在1225℃时铜回收率最大,且煤比3.5%比煤比3.25%的铜回收率稍高;铁的回收率随还原温度升高逐渐增加,铁酸铅温度高时才能被还原,使铁以feo和硅造渣进入渣相,且煤比3.5%比煤比3.25%的铁回收率低,煤比高则还原气氛强,会使铁还原进入金属相。表5不同还原温度的还原试验情况(时间60min,煤比3.25%)表6不同还原温度的还原试验情况(时间60min,煤比3.5%)由表7及图9可知,还原时间30min时,随着还原温度的升高,铅的回收率稍有增加,且煤比3.5%比煤比3.25%的铅回收率稍高;锌的回收率降低比较明显,且煤比3.5%比煤比3.25%的锌回收率低;铜的回收率影响不明显,且煤比3.5%比煤比3.25%的铜回收率稍高;铁的回收率随还原温度升高逐渐增加,且煤比3.5%比煤比3.25%的铁回收率低。还原时间30min时试验现象与还原时间60min时相同,但还原时间较短时,锌的回收率相对较高,铁的回收率相对较低。另外,还原温度低时,试验中渣金分离效果不好,使金属相中夹杂有浮渣,还原温度升高,铅、铁的回收率稍有增加,但锌的回收率降低。综合考虑,建议还原温度为1200~1225℃。表7不同还原温度的还原试验情况(时间30min)2.3.4还原剂时间的影响表8~表10分别为在1200℃、1225℃和1250℃时,不同还原时间对高铅渣还原效果的影响。由表8和图10可知,在温度1200℃时,随着还原时间的延长,铅的回收率稍有增加,且煤比3.5%比煤比3.25%的铅回收率稍高;锌的回收率稍有降低,且煤比3.5%比煤比3.25%的锌回收率低;铜的回收率略有降低,且煤比3.5%比煤比3.25%的铜回收率稍高;铁的回收率随还原时间延长逐渐增加,且煤比3.5%比煤比3.25%的铁回收率低。由表9和图11可知,在温度1225℃时,随着还原时间的延长,铅的回收率稍有增加,且煤比3.5%比煤比3.25%的铅回收率稍高;锌的回收率稍有降低,且煤比3.5%比煤比3.25%的锌回收率低;铜的回收率变化不明显,且煤比3.5%比煤比3.25%的铜回收率稍高;铁的回收率随还原时间延长逐渐增加,且煤比3.5%比煤比3.25%的铁回收率低。表8不同还原时间的还原试验情况(温度1200℃)由表10和图12可知,在温度1250℃时,随着还原时间的延长,对铅、锌、铜和铁的回收率影响不明显,铅和铜回收率煤比3.5%比煤比3.25%的稍高。锌和铁回收率煤比3.5%比煤比3.25%的稍低。由此可见,在温度1200℃和1225℃随着还原时间延长,渣中铅含量逐渐降低,铅、铁的回收率稍有增加,锌的回收率随着时间增加逐渐降低。在温度1250℃时,还原时间对铅、锌、铜和铁的回收率影响不明显。还原时间对铅还原反应影响不显著,对铁和锌回收率略有影响。在煤比3.5%,1200℃温度下还原时间为30min,渣含铅为1.91%,锌回收率为90.85%,铁回收率为91.73%;还原时间为60min,渣含铅为1.83%,锌回收率为89.43%,铁回收率为92.58%。1225℃温度下还原时间为30min,渣含铅为1.84%,锌回收率为89.36%,铁回收率为92.11%;还原时间为60min,渣含铅为1.35%,锌回收率为87.95%,铁回收率为94.21%。综合考虑建议还原时间为30~60min。表9不同还原时间的还原试验情况(温度1225℃)表10不同还原时间的还原试验情况(温度1250℃)2.3.5钙硅比的影响高铅渣中w(cao)/w(sio2)为0.17,w(feo)/w(sio2)为1.66,相对传统渣型,钙硅比较 低。配入碳酸钙,提高还原渣的钙硅比,考察不同渣型的影响。在高铅渣400g,煤比3%,时间60min条件下,考察钙硅比0.45时不同温度对高铅渣的还原效果。具体试验情况见表11。由表11和图13可知,在钙硅比0.45时,随着还原温度升高,渣中铅的含量降低,铅和铜的回收率在1100℃前增加明显,1100℃后随着还原温度升高缓慢增加,锌的回收率逐渐降低,铁的回收率略有波动。表11钙硅比0.45时不同还原温度的试验情况表12为当高铅渣400g,煤比3.5%,温度1250℃,时间60min,铅渣中w(cao)/w(sio2)为0.17,w(feo)/w(sio2)为1.66时,不同钙硅比对高铅渣的还原效果。由表12和图14可知,在1250℃时,随着钙硅比的增加,渣中铅的含量逐渐升高,铅和铜回收率稍有降低,同时锌的回收率基本没影响,铁的回收率有所降低。通过上述试验结果,添加碳酸钙调整渣型的钙硅比,由于钙硅比增加使渣的熔点增高,使铅金属回收率降低,同时也增加了还 原渣量。因此试验中建议不添加碳酸钙,保持还原渣低的钙硅比。表12不同钙硅比的还原试验情况2.3.6铁硅比的影响表13和图15为不同铁硅比对高铅渣的还原效果的影响。由表13和图15可知,在1250℃时,随着铁硅比的增加,铅、铜和铁回收率基本不变,而锌的回收率略有降低。表13不同铁硅比的试验情况2.4锌在还原渣中产出形式除了氧化铅和砷酸铅相外,锌在该还原渣的各相中都有所分布。锌主要是赋存在尖晶石、铁酸锌中,其次是赋存在硅酸盐相中,当硅酸盐相中含铁较高时,含钙亦较高时,而锌的含量一般较低,少量的锌赋存在玻璃相中,而以硫化物相产出的锌极少。锌在该渣中典型的产出状态如下所述。该还原渣中尖晶石以zn-fe尖晶石为主,其成分中平均含zn16.77%、al9.52%、fe40.26%、o31.44%;铁酸锌平均含zn9.57%、fe51.95%、o30.89%。硅酸盐相按其成分可以分为以zn为主的硅酸盐和fe为主硅酸盐,以含锌为主的硅酸盐的平均成分中含zn34.87%、fe16.42%、si13.72%、o30.76%;以含铁为主的硅酸盐的平均成分中含fe35.53%、zn7.81%、ca4.40%、mn5.72%、si14.25%、o31.96%。该还原渣中主要相别典型产出特征。尖晶石和铁酸锌形成的温度一般较高,在还原体系温度下降时往往结晶较早,尤其是尖晶石多呈自形晶产出,且具有一定的反应边结构; 随着体系温度的降低,硅酸盐相随后形成,最后形成的是玻璃相,玻璃相成分较为复杂,不同程度地含zn、fe、pb、k、na、s、cl等元素。2.5液态高铅渣还原综合条件综合上述还原试验,确定高铅渣还原的基本工艺参数为:还原剂煤比在3.25~3.5%;还原温度为1200~1225℃;还原时间为30~60min。此时,试验结果能满足考核指标,渣中铅含量小于2%,85%锌在渣中。在试验y-111工艺下,即煤比3.5%,温度1225℃,时间30min时,渣中铅含量1.84%,铅的回收率98.57%,锌的回收率89.36%。在试验y-97工艺下,即煤比3.5%,温度1225℃,时间60min时,渣中铅含量1.35%,铅的回收率98.97%,锌的回收率87.95%。对于本领域技术人员而言,显然本发明不限于上述示范性实施例的细节,而且在不背离本发明的精神或基本特征的情况下,能够以其他的具体形式实现本发明。因此,无论从哪一点来看,均应将实施例看作是示范性的,而且是非限制性的,本发明的范围由所附权利要求而不是上述说明限定,因此旨在将落在权利要求的等同要件的含义和范围内的所有变化囊括在本发明内。此外,应当理解,虽然本说明书按照实施方式加以描述,但并非每个实施方式仅包含一个独立的技术方案,说明书的这种叙述方式仅仅是为清楚起见,本领域技术人员应当将说明书作为一个整体,各实施例中的技术方案也可以经适当组合,形成本领域技术人员可以理解的其他实施方式。当前第1页12