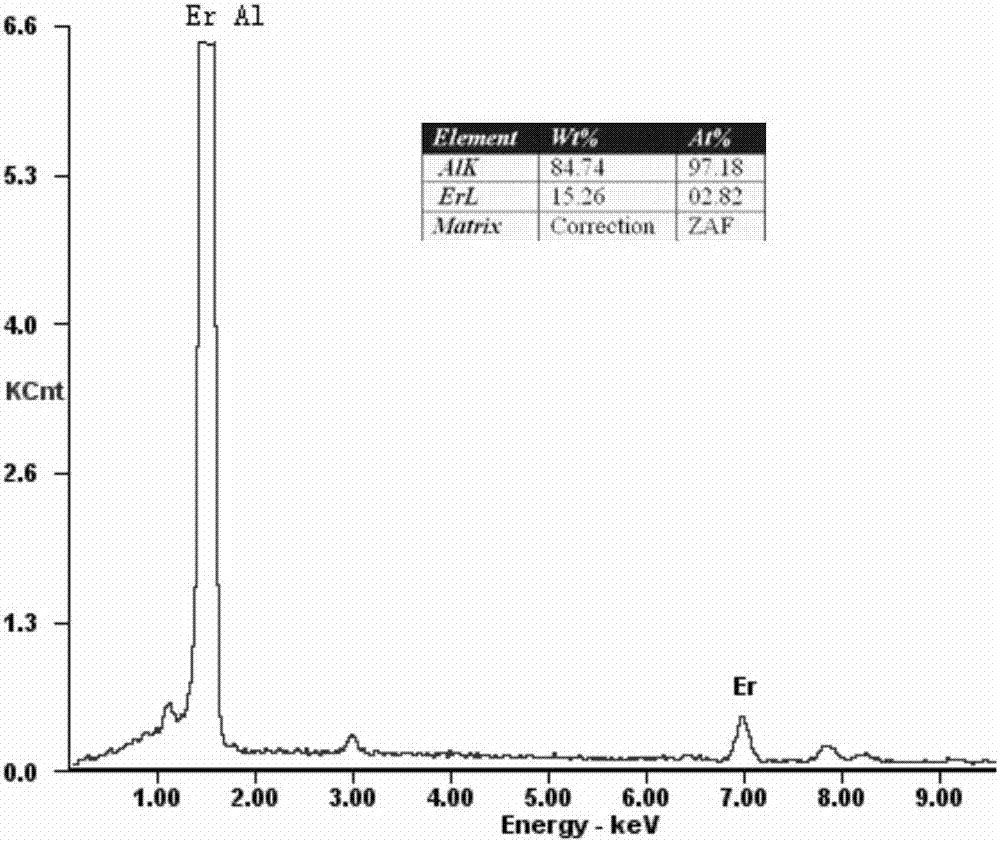
本发明涉及一种轻质高导耐热铝导线及其制备方法,属于电工材料技术领域。技术背景根据能源互联的战略部署,我国电网将实现“西电东送,南北互供、全国联网”,输电线路距离远、输电容量大、自然环境复杂,为了降低输送线损、减少线路建设成本、节约紧张的走廊资源,对输电导线提出了更高的要求,既要有高电导率,又要有良好的耐热性能和抗弧垂特性。因此,研发一种具有高导电率、良好的耐热性能、密度小的铝导线,成为业内亟需解决的技术难题。金属中的自由电子在外加电场作用下发生定向运动形成电流,而晶格场周期性的异常点(或不规则点)会阻碍电子的定向运动并对电子波产生散射作用。金属材料的导电性跟自由电子的平均自由程(相邻异常点间距的平均值)紧密相关,自由电子的平均自由程越小,材料电导率越低。金属中的杂质元素、固溶原子以及晶体缺陷都会导致晶格场局部偏离其周期性位置,缩短自由电子的平均自由程,从而导致金属电导率的降低。杂质对电导率的影响与杂质元素的种类、含量、在金属中存在的状态紧密相关,工业纯铝中不可避免的杂质元素Ti、V、Cr、Mn等对导电性影响较大,特别是较高含量的杂质元素固溶于铝基体时,会大幅降低铝导体的电导率。固溶原子导致晶格畸变而破坏金属库仑势场的周期性,并成为对导电电子的散射中心,固溶原子摩尔浓度越大,相邻散射中心间的距离越小,电子的平均自由程越小,电导率越低,以Zr为例,少量Zr原子固溶于铝基体中便会显著降低合金的电导率。纯度为99.99%的高纯Al在20℃的电导率高达64.94%IACS,密度为2.7g/cm3,但强度仅为80~100MPa,再结晶温度为150℃左右。添加0.6~0.9wt.%Mg、0.5~0.9wt.%Si、0.5wt.%Fe、0.1wt.%Cu、0.1wt.%Zn的6021合金是常用的高强度电工铝合金,抗拉强度可达到295~325MPa,但是,其20℃时的导电率仅为52.5~55%IACS。旨在提高铝导体耐热性和强度的微合金化,特别是当合金组分及配比设计不当时,会对导电性能产生非常不利的影响,研发轻质高导耐热铝导线的技术难点是在导电性、耐热性、比强度之间寻求最佳平衡点。通常,导电率和耐热性呈此消彼长的关系,现有公开的技术方案中往往存在着顾此失彼的情况,导电率高的技术方案,耐热性不理想,耐热性好的技术方案,导电率不够理想。公开号为CN102230113A的专利,公开的成分为0.06~0.15wt.%Zr,0.15~0.30wt.%Er,0.1~0.2wt.%Fe,通过Zr、Er、Fe的微合金化,采用连铸连轧工艺,制备出的铝电线,导电率只有59.5~60.5%IACS,短时耐热温度为210℃,长期耐热温度为180℃,抗拉强度为157MPa,没有公开合金的密度参数。公开号为CN103498083A的专利,公开的成分为0.01~0.2wt.%Er,0~0.3%wt.Zr,0~0.2wt.%B,从其实施例记载的参数来看,含有Er、Zr、B的实施例的导电率仅为60%IACS,而只含Er、Zr元素中的一种或两种的实施例的导电率只有58%IACS,且没有公开合金密度、强度、耐热性能参数及连铸连轧的工艺参数。因此,通过优化合金组分及制备工艺,在不降低电导率的前提下,提高铝导线的耐热性和比强度,制备轻质、高导、耐热铝导线是本领域长期以来的追求。
技术实现要素:本发明的目的在于克服现有技术之不足而提供一种组分配比合理、合金化元素少、工艺简单且灵活、生产成本低的轻质高导耐热铝导线及制备方法。本发明通过微量添加对导电率损害较小的合金元素,产生净化、变质、细化和弥散强化作用,相对99.99%的高纯铝,在电导率下降很少的前提下,大幅提高导线的耐热性和比强度,从而满足大容量远距离输电线路的轻质、高导、耐热的服役要求。本发明一种轻质高导耐热铝导线,包括下述组分按质量百分比组成:B:0.035~0.06wt.%;Zr:0.1~0.2wt.%;Er:0.2~0.4wt.%(但不包含0.2wt%);Ti、V、Cr、Mn杂质元素总含量小于等于0.01wt.%,其余为Al;其中,Zr、Er按质量比Zr:Er=1:1.5~2.5添加,优选Zr、Er按质量比Zr:Er=1:1.5~2添加。本发明一种轻质高导耐热铝导线的制备方法,包括下述步骤:第一步:将工业纯铝锭加热至740℃~780℃熔化,按设计的铝导线组分中Zr、Er的质量百分比配取Al-Zr和Al-Er中间合金加入铝熔体中,待中间合金完全熔化并搅拌均匀后,对Zr、Er、Al合金熔体进行炉前快速成分分析,并将合金熔体降至720℃~730℃保温,同时添加Al-B中间合金进行精炼,然后静置、扒渣、铸造,得到坯料;第二步:将坯料退火后,进行挤压、拉拨成单丝。本发明一种轻质高导耐热铝导线的制备方法,所述Al-B中间合金的添加量由以下两部分确定:第一,按设计组分中B的质量百分比配取的Al-B中间合金;第二,按B的质量为Zr、Er、Al合金熔体中Ti、V、Cr、Mn杂质元素总含量的2-5倍配取的Al-B中间合金。本发明一种轻质高导耐热铝导线的制备方法,所述铸造方式可根据生产线设备配置情况变换,既可通过普通铸造或半连续铸造获得锭坯,也可通过连续铸造获得杆坯。本发明一种轻质高导耐热铝导线的制备方法,铸造时,铸锭以20-300℃/s的速度冷却至室温。本发明一种轻质高导耐热铝导线的制备方法,铸造时采用水冷铸造。本发明一种轻质高导耐热铝导线的制备方法,所述坯料的退火工艺为:退火温度为480℃~500℃,保温1-10h后随炉冷却。本发明一种轻质高导耐热铝导线的制备方法,所述挤压方式可根据生产线设备配置情况进行变换,既可采用加热的锭坯进行常规热挤压,也可采用室温杆坯进行连续挤压,所述热挤压温度为300~450℃。本发明一种轻质高导耐热铝导线的制备方法,热挤压或室温连续挤压的挤压比大于等于80,挤压总变形量大于等于80%。本发明一种轻质高导耐热铝导线的制备方法,所述拉拔采用挤压杆料进行多道次冷拉拔,可根据实际需要确定拉拔坯料直径,特别是可根据服役强度要求确定所用坯料直径,并通过不同的拉拨变形量来调控单丝的强度。本发明一种轻质高导耐热铝导线的制备方法,挤压后进行多道次拉拨,道次延伸系数为1.2~1.5,累计总延伸系数为5.5~10.5,可采用普通润滑油或乳浊液进行润滑,乳浊液还可起冷却作用,以使铝丝的温度不超过180℃。本发明一种轻质高导耐热铝导线的制备方法,所制备的导线,密度小于等于2.71g/cm3,在20℃的电导率大于等于62%IACS,短时耐热温度高达230℃,长期耐热温度高达210℃,抗拉强度大于等于165MPa。本发明原理和优势根据金属导电理论,杂质和晶体缺陷对铝的导电性影响很大,杂质含量越少、晶格畸变和晶界等晶体缺陷越少,金属晶体的导电性越好,在工业纯铝的不可避免的杂质中,Ti、V、Cr、Mn对导电性的有害影响较大,特别是当其以固溶形式存在于铝基体时。本发明B的添加量为按设计的铝导线组分中B的质量百分比(0.035-0.06wt.%)和工业纯铝中Ti、V、Cr、Mn杂质元素总含量的2-5倍确定的B的质量之和,在满足B元素作为精炼剂和变质剂的前提下,B、Zr、Er的协同作用带来了预料不到的技术效果。本发明的合金熔炼过程中,Al-B中间合金的添加量按两部分确定,合金熔体中B含量远远超过0.06wt.%,其作为精炼剂和变质剂。首先,B作为精炼剂时,与工业纯铝中不可避免的Ti、V等杂质反应,生成比重较大的硼化物,以炉渣的形式被除去(见附图2、附图3),从而大幅提高铝导体的电导率。其次,富余的B作为变质剂,产生变质作用,可以使沿晶界连续分布的富Fe相变为不连续的颗粒状,既可以改善铝导线的导电性能的同时,也可提高其强度和热稳定性,同时,可以降低对原材料工业纯铝锭的纯度要求,从而大幅度降低合金制备成本。发明人发现:如果加入的精炼剂和变质剂的B含量太少,使合金基体中B含量小于0.035%,则会降低材料的电导率,但是,如果加入过量的B作为精炼剂和变质剂(B含量为Ti、V总含量的8倍),则铝中会出现较多粗大的Al、B的化合物,也会明显降低材料的电导率。Er元素倾向于吸附在α-Al晶核上,生成Al3Er阻碍α-Al枝晶成长,达到细化二次枝晶组织的效果,初生的Al3Er被推挤到晶界,在熔体最后完全凝固时形成含α-Al相和Al3Er相的共晶化合物。作为稀土元素,Er也可与Fe等杂质元素形成化合物,产生净化和变质作用。附图6为对比例2中的第二相粒子及能谱分析结果,对比例2未添加B,图6(b)显示晶内可能形成了Al3Er和(Al,Fe)的混合相,或(Al,Fe,Er)三元化合物,没有B的作用,Er元素更倾向于与杂质元素形成化合物或者形成Al3X相。本发明的优势是利用B和Zr、Er的协同作用,由B来产生除杂和变质作用,抑制含Er杂质相的形成,并通过铸造过程的快速冷却抑制粗大的初生相形成,使Zr和Er主要以亚稳定的过饱和固溶态存在,从而促使后续退火过程析出大量与基体共格的Al3(Er,Zr)复合粒子,如附图5所示。本发明Al3(Er,Zr)三元相析出的原理是:退火过程中,扩散速率较快的Er在基体中率先形成粒子,为Zr的脱溶析出提供形核质点,促进Al-Zr固溶体的分解,扩散速率较慢的Zr聚集在Al3Er粒子的外层,形成与基体共格的、L12结构的、纳米级的球状Al3(Er,Zr)复合粒子。本发明析出纳米尺度的Al3(Er,Zr)复合粒子有如下优势:一方面,降低Zr和Er在铝基体中的固溶程度,提高铝导线的电导率,另一方面,弥散分布的与晶体共格的纳米尺度的Al3(Er,Zr)复合粒子,对位错、亚晶、晶界产生钉扎作用,具有明显的强化作用及抑制再结晶作用,能有效提高铝导体的强度和耐热性。本发明采用铸造、退火、挤压、拉拨的制备工艺,能够区别其他铝导线的连铸连轧工艺,具有生产流程短、工艺控制简单灵活的优势,制备的导线在保证较高导电率的前提下,具有较好的耐热性和比强度。本发明的快速冷却铸造有一定抑制粗大初生相形成的作用,使铸坯具有较高过饱和固溶度,为后续退火工序析出细小弥散分布的第二相粒子提供驱动力。本发明的铸坯高温短时退火,其主要作用是析出大量弥散分布的第二相粒子,尤其是析出很多与晶体共格的纳米尺度的Al3(Er,Zr)复合粒子,其次要作用是适当消除坯料的成分偏析、组织偏析及铸造应力,从而改善铸造组织和加工性能,此外,相对铝合金的均匀化退火时间及已公开专利的退火时间,本发明的退火时间较短,具有节能降耗优势。本发明采用挤压进行塑性变形,具有生产灵活、工艺控制简单的优势,既可采用锭坯一次挤压成线杆,也可采用连续铸造的杆坯连续挤压成较小直径的线坯,相比轧制变形,具有更大的变形程度和更强烈的三向压应力状态,可大大改善铸造组织和提高后续加工性能。本发明采用挤压杆料进行多道次冷拉拔获得铝合金单丝,可根据实际需要确定杆料直径,特别是可根据服役强度要求确定所用杆料直径,并通过不同拉拨变形量来调控单丝的强度。综上所述,本发明基于Al、B、Zr、Er元素的合理配比和含B精炼剂的适量加入,通过快速冷却铸造、铸坯的高温短时退火、大变形量的挤压,使B产生净化、变质及协同Zr、Er的复合微合金化作用,制备出的导线在20℃的电导率大于等于62%IACS,长期耐热温度高达210℃,短时耐热温度高达230℃,抗拉强度大于等于165MPa,密度(≤2.71g/cm3)与纯铝的密度2.7g/cm3比较接近,可提高输电线路容量和降低输送线损,具有良好的抗弧垂特性和耐热性能,可增加输电线路塔杆的间距和提高远距离、大容量输电线路的安全稳定性和服役寿命。本发明生产流程短、工艺控制简单灵活且要求较低,加入的合金化元素数目少、含量低,节省了昂贵稀土元素的用量,对原材料杂质含量和铸坯质量没有严格要求,能源消耗也不高,因此,还具有生产成本较低的优势。附图说明附图1(a)为实施例1的铸态金相组织,附图1(b)为实施例2的铸态金相组织,附图1(c)为实施例3的铸态金相组织;附图2为本发明实施例2熔炼炉渣的微观组织照片,附图3为附图2中质点的能谱分析结果;附图4(a)为对比例2合金的金相组织照片,附图4(b)为实施例2合金的金相组织照片,附图4(c)为对比例1合金的金相组织照片;附图5(a)为实施例2合金的低倍率TEM照片,附图5(b)为实施例2合金的高倍率TEM照片,附图5(c)为实施例2合金中Al3(Er,Zr)复合粒子的高分辨TEM形貌;附图6(a)为对比例2合金退火态合金的微观组织形貌,附图6(b)为附图6(a)中标识处A点析出相能谱分析结果,附图6(c)为附图6(a)中标识处B点析出相能谱分析结果,附图6(d)为附图6(a)中标识处C点析出相能谱分析结果;附图7~附图10为实施例2所制备的Φ4铝导线的性能检测报告。由图1(a)、图1(b)、图1(c)可以看出,Zr、Er元素的联合添加具有明显的晶粒细化效果,并且Zr、Er元素的含量越大,晶粒细化效果越明显。由图2、图3所示实施例2炉渣的微观组织形貌及能谱分析结果可以看出:存在不同于白色AlFe相的另一种相,该相呈现出四周较暗中间亮白的特点,能谱分析结果显示,该相为含Al、B、Ti、V的相,说明杂质Ti、V确实与B形成了化合物而进入炉渣,这是使得合金电导率提高的重要原因之一。由图4(a)可以看出,不用B作精炼剂时,晶界分布着较多连续的杂质相;由图4(b)可以看出,采用合适质量比例的硼精炼剂后,基体中出现了较多的点状相,晶界的连续相也转变为不连续的条状及点状;由图4(c)可以看出,采用过量的B作为精炼剂后,基体中出现了较多粗大的第二相,能谱分析结果表明为Al、B的化合物。结合对比例2中的材料导电率较低的事实,说明添加过量的B对材料的电导率有负面影响。在图5(a)所示析出相周围可以观察到清晰的Ashby-Brown应力衬度,析出相仍与基体保持良好的共格性,图5(b)所示析出相的外壳和内核表现出了明显的衬度差异,图5(c)所示区域可分为基体、析出相的壳、析出相的核3个部分,析出相的壳的选区电子衍射斑点对应L12结构,析出相外壳对应的衍射强度比内核要强,确定为一种内部富含Er、外部壳富含Zr的Al3(Er1-xZrx)复合相。图5(a)、图5(b)、图5(c)证明本发明合金退火过程中析出了大量与基体共格的纳米尺度的Al3(Er,Zr)复合相粒子,从而保障了电导率和耐热性及强度的协调发展。图6(a)-(d)为对比例2中的第二相粒子及能谱分析结果,图6(b)显示晶内A点可能是Al3Er和(Al,Fe)的混合相,也可能是(Al,Fe,Er)三元化合物,图6(c)显示晶界B点颗粒相为Al3Er相,图6(d)显示晶界C点针状相为Al3Fe相。对比例2未添加B,Er元素更倾向于与杂质元素形成化合物或者形成Al3X相,证明B元素有促进Al3(Er1-xZrx)三元复合相析出的作用。附图7~附图10可知,本发明实施例2所制备的铝导线在20℃的电导率达到了62%IACS,短期耐热温度达到230℃(230℃保温1h抗拉强度残留率高达92%,抗拉强度为165MPa,可作为本发明导线性能优越性的有力支撑材料。具体实施方式实施例1以纯度大于99.7%的工业纯铝锭、Al-11.34%Zr中间合金和Al-4.7%Er中间合金为原料,先将工业纯铝在760℃熔化后,加入Al-Zr、Al-Er中间合金,待中间合金完全熔化并搅拌均匀后,对Zr、Er、Al合金熔体进行炉前快速成分分析,并将合金熔体降至730℃保温,再按合金熔体中杂质元素Ti、V总含量的2倍及合金中B的质量百分比,加入Al-2.5%B中间合金进行精炼,使各元素的质量百分比为:B为0.035wt.%,Zr为0.1wt.%,Er为0.21wt.%,Ti、V、Cr、Mn等杂质元素总和为0.001wt.%,Al为余量。然后依次进行搅拌、静置、扒渣,水冷铸造。坏料在480℃保温10h随炉冷却,随后在420℃进行热挤压,挤压比为89.7,挤压变形量为98.7%,得到Φ9.5的圆铝杆,经5道次拉拔成Φ4.0mm的铝导线。对铝导线进行导电率、抗拉强度、耐热性能、密度测试,结果如表1所示。实施例2以纯度大于99.7%的工业纯铝锭、Al-11.34%Zr和Al-4.7%Er中间合金为原料,将工业纯铝在760℃熔化后,加入Al-Zr、Al-Er中间合金,待中间合金完全熔化并搅拌后,对Zr、Er、Al合金熔体进行炉前快速成分分析,并将合金熔体降至730℃保温,再按合金熔体中杂质元素Ti、V总含量的3.5倍及合金中B的质量百分比,加入Al-2.5%B中间合金进行精炼,使各元素的质量百分比为:B为0.05wt.%,Zr为0.1wt.%,Er为0.21wt.%,Ti、V、Cr、Mn等杂质元素总和为0.001wt.%,Al为余量。然后依次进行搅拌、静置、扒渣,水冷铸造。坏料在490℃保温8h随炉冷却,随后在420℃进行热挤压,挤压比为89.7,挤压变形量为98.7%,得到Φ9.5的圆铝杆,经5道次拉拔成Φ4.0mm的铝导线。对铝导线进行导电率、抗拉强度、耐热性能、密度测试,结果如表2所示。实施例3以纯度大于99.7%的工业纯铝锭、Al-11.34%Zr中间合金和Al-4.7%Er中间合金为原料,将工业纯铝在760℃熔化后,加入Al-Zr、Al-Er中间合金,待中间合金完全熔化并搅拌后,对Zr、Er、Al合金熔体进行炉前快速成分分析,并将合金熔体降至730℃保温,再按合金熔体中杂质元素Ti、V总含量的5倍及合金中B的质量百分比,加入Al-2.5%B中间合金精炼后,各元素的质量百分比为:B为0.06wt.%,Zr为0.2wt.%,Er为0.4wt.%,Ti、V、Cr、Mn等杂质元素总和为0.001wt.%,Al为余量。然后依次进行搅拌、静置、扒渣,水冷铸造。坯料在500℃保温1h随炉冷却,随后在420℃进行热挤压,挤压比为89.7,挤压变形量为98.7%,得到Φ9.5的圆铝杆,经5道次拉拔成Φ4.0mm的铝导线。对铝导线进行导电率、抗拉强度、耐热性能、密度测试,结果如表3所示。对比例1以纯度大于99.7%的工业纯铝锭、Al-11.34%Zr中间合金和Al-4.7%Er中间合金为原料,将工业纯铝在760℃熔化后,加入Al-Zr、Al-Er中间合金,待中间合金完全熔化并搅拌后,对Zr、Er、Al合金熔体进行炉前快速成分分析,并将合金熔体降至730℃保温,再按合金熔体中杂质元素Ti、V总含量的8倍及合金中B的质量百分比,加入Al-2.5%B中间合金精炼后,各元素的质量百分比为:B为0.10wt.%,Zr为0.1wt.%,Er为0.21wt.%,Ti、V、Cr、Mn等杂质元素总和为0.001wt.%,Al为余量。然后依次进行搅拌、静置、扒渣,水冷铸造。坯料在490℃保温8h后随炉冷却,随后在420℃进行热挤压,挤压比为89.7,挤压变形量为98.7%,得到Φ9.5的圆铝杆,经多道次拉拔成Φ4.0mm的铝导线。对铝导线进行导电率、抗拉强度、耐热性能、密度测试,结果如表5所示。对比例2按照工业纯铝、Zr0.2%,Er0.4%进行配料,其原料为纯度大于99.7%的工业纯铝锭、Al-11.34%Zr中间合金、Al-4.7%Er中间合金。将工业纯铝在760℃熔化后,加入Al-Zr、Al-Er中间合金,待中间合金完全熔化并搅拌后,对Zr、Er、Al合金熔体进行炉前快速成分分析,并将合金熔体降至730℃保温,依次进行搅拌、静置、扒渣,水冷铸造。铸锭在500℃保温1h随炉冷却,随后在420℃进行热挤压,挤压比为89.7,挤压变形量为98.7%,得到Φ9.5的圆铝杆,经5道次拉拔成Φ4.0mm的铝导线。对铝导线进行导电率、抗拉强度、耐热性能、密度测试,结果如表4所示。本发明3个实施例得到的铝合金导线,密度均小于等于2.71g/cm3,在20℃常温下导电率大于等于62%IACS,短时耐热温度达到230℃,长期耐热温度达到210℃。对比例1加入了过量的B,其他组分和实施例1和实施例2相同,退火工艺与实施例2相同,对比例2除了未加入B元素外,其他组分与实施例3相同,2个对比例的电导率均低于61%IACS,在230℃退火1小时的强度残存率均低于90%,在230℃退火400小时的强度残存率也低于90%。从以上实施例与对比例所得到的性能参数可知:作为精炼剂和变质剂的B,如果加入含量太少,导致合金基体中B含量小于0.035wt.%,或者加入量过多,如加入Ti、V总含量8倍的B,均会降低导线的导电性能和耐热性能。