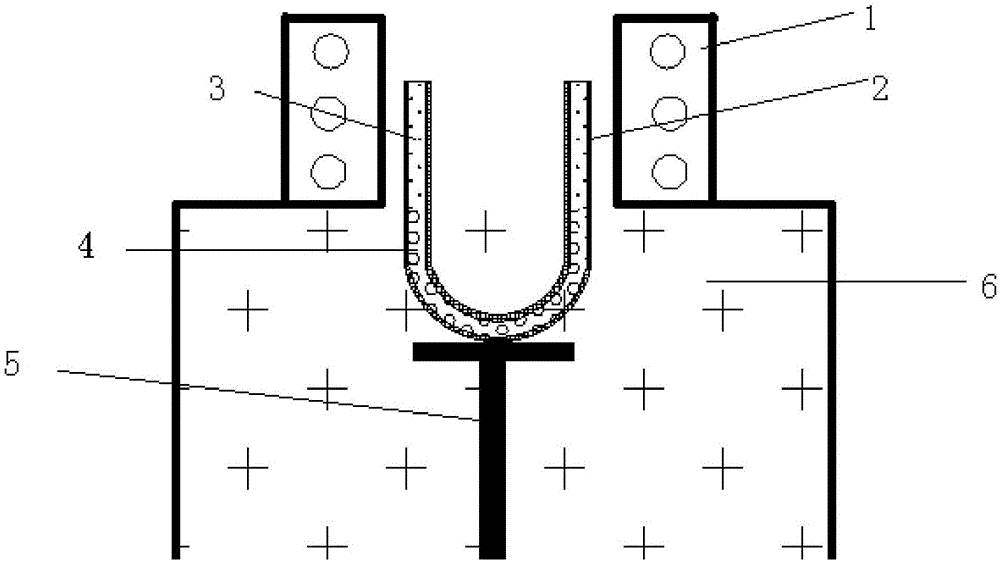
本发明属于内生铝基材料铸件制备
技术领域:
,特别涉及一种具有组织均匀、内生相体积分数可调和变体积分数的铝基复合材料铸件制备方法。
背景技术:
:随着现代科学技术的飞速发展,人们对材料的要求越来越高。在结构材料方面,不但要求强度高,还要求其重量要轻,在航空航天领域尤其如此。金属基复合材料正是为了满足上述要求而诞生的。与传统的金属材料相比,具有较高的比强度与比刚度,而与树脂基复合材料相比,具有优良的导电性与耐热性,与陶瓷材料相比,又具有高韧性和高冲击性能。铝基复合材料具有高比强度、高比模量、高硬度、高耐磨性、耐高温、耐冲击、耐冲蚀、低的热膨胀系数、良好的热稳定性和导电导热性,在航空航天、汽车工业、电子业等领域中具有广阔的应用前景。由于内生复合克服了外加复合的一些不足,因此内生铝基复合材料的研究发展较快,成为金属基复合材料研究中的一个热点。内生复合的基本原理是在一定条件下,通过元素之间或元素与化合物之间的化学反应,在金属基体内原位生成一种或几种高硬度、高弹性模量的增强相,从而达到强化金属基体的目的。内生铝基复合材料具有一下优点:①增强体在铝基体上原位形核长大具有增强界面结合良好的互容性;②省去了增强物质的预处理,简化了工艺流程,成本也相对降低;③增强相颗粒细小,往往处于微米级或微米级以下,能保证铝基复合材料不但有良好的韧性和高温性能,而且有很高的强度和弹性模量;④能与铸造工艺结合,直接制造出形状复杂,尺寸变化大的近终形产品。然而,内生铝基复合材料铸件存在内生相的均化问题,对于那些在长时间熔炼保温的金属液,已形成的内生相在金属液内容易聚结、偏析,而且在浇注模具后慢速凝固过程中,内生相常偏析于树枝晶间或晶粒边界,对材料组织和性能产生不良影响。同时,内生相的体积分数,主要是通过调整材料的配方进行控制,造成工艺繁琐,成本较高。技术实现要素:针对现有技术的不足,本发明是通过提供一种内生铝基复合材料铸件制备方法,实现内生铝基复合材料铸件组织均匀、内生相体积分数可调和变体积分数的目标,开辟制备内生铝基金属复合材料铸件的新途径。本发明的技术方案是通过以下进行实现的,具体为:一种内生铝基复合材料铸件制备方法,其步骤包括:第一步:合金配比;第二步:将熔点组元制备成中间合金;第三步:将中间合金破碎与低熔点组元熔炼制成母合金;第四步:将母合金熔化,注入模具中;第五步:采用加热方式,调节加热功率,控制加热温度,将母合金加热至完全融化状态,保温后浸入到冷却介质中,快速凝固成型。本发明与现有技术相比,其显著优点是:1、首先熔炼母合金锭,然后合金锭融化在模具中成型后,最后调节内生相的体积分数分。避免常规熔炼长时间保温过程中内生相在金属液内聚结、偏析的问题;2、浸入冷却介质为冷却能力极强的液态合金,实现快速冷却,解决了现有的金属液注入模具缓慢冷却过程中,内生相偏析于树枝晶间或晶粒边界的问题;3、通过调节加热功率,控制加热温度,可以调节内生相的体积分数,与常规的通过变化配方调节内生相体积分数的方法相比,成本低、效率高;4、可以控制铸件不同部位的温度,实现同一试样不同部位的内生相的体积分发生变化。附图说明图1是本发明实施例内生铝基复合材料铸件制备流程;图2是本发明实施例内生铝基复合材料铸件制备原理示意图;图3是本发明实施例750℃内生铝基复合材料铸件微观组织;图4是本发明实施例800℃内生铝基复合材料铸件微观组织。具体实施方式为使本发明的上述目的、特征和优点能够更为明显易懂,下面结合附图对本发明的具体实施方式做详细的说明。在以下描述中阐述了具体细节以便于充分理解本发明。但是本发明能够以多种不同于在此描述的其它方式来实施,本领域技术人员可以在不违背本发明内涵的情况下做类似推广。因此本发明不受下面公开的具体实施方式的限制。结合图1、图2所示,图2中,1为感应加热装置,2为模具,3为铸件熔化部分,4为铸件凝固部分,5为抽拉机构,6为冷却液;一种内生铝基复合材料铸件制备方法,包括以下步骤:第一步:合金配比;根据铝基复合材料成分配方,计算各组元质量,采用高纯组元进行配比。第二步:将熔点组元制备成中间合金;首先将高熔点组元熔制成中间合金锭,以确保获得成分均匀的中间合金;第三步:将中间合金破碎与低熔点组元熔炼制成母合金;将中间合金破碎,与低熔点组元按设计成分配比混合后放入预处理过的坩埚内,熔炼成母合金。第四步:将母合金熔化,注入模具中;将适量母合金锭表面机械打磨放入坩埚中,加热重熔后,注入模具中。模具的几何尺寸和形状可根据产品的要求进行调整。第五步:采用感应线圈加热方式加热模具,调节加热功率,控制加热温度,加热温度为750-950℃,保温时间10分钟,将母合金加热至完全融化状态,保温后浸入到冷却Ga-In-Sn液态合金中,浸入冷却介质的速率控制在10-20mm/s,快速凝固成型。采用感应线圈加热方式加热模具,将模具内的合金加热到完全融化(模具未融化)。由于内生相的固溶度与温度相关,因此不同温度条件下内生相的体积分数是不同的。通过调节加热功率控制温度,调整内生相的体积分数,浸入冷却介质为冷却能力极强的Ga-In-Sn液态合金,快速冷却。实施例1(1)合金配比本发明制备内生相TiB2增强ZAlCu5MnA铝基复合材料,高熔点组元重量百分比见表1,低熔点组元重量百分比见表2,高熔点组元与低熔点组员重量之比为4:1。表1高熔点组元重量百分比(%)组元AlCuMnTi重量/%其余4.8-5.30.6-1.00.15-0.35表2低熔点组元重量百分比(%)组元K2TiF6KBF4重量/%3466(2)母合金的制备将高熔点组元Al、Cu、Mn、Ti的表面机械打磨去掉表面的氧化皮后,按照选定/设计好的成分配比料备料,熔化获得中间合金;第二步将去除氧化皮后的中间合金破碎,与低熔点组元K2TiF6、KBF4按设计成分配比混合后放入预处理过的坩埚内,在感应炉中熔炼成母合金。(3)试样成型将母合金锭表面机械打磨,熔化后注入模具中。(4)快速凝固将装有母合金的模具放入感应熔炼装置中,调节加热功率加热到750℃,内生相的体积分数为10%,保温10min,然后以15mm/s的抽拉速率浸入冷却介质为冷却能力极强的Ga-In-Sn液态合金。图3为750℃快速凝固条件下,内生铝基复合材料铸件微观组织扫描照片。通过图片可以看出内生相分布均匀,不存在聚结和偏析于晶界的问题。实施例2合金配比、母合金制备和试样成型采用与实施例1相同的制备方法,快速凝固工序中加热温度为800℃,内生相的体积分数为8%,见图4。事实证明,通过调调节加热功率,控制重熔温度,可以调节内生相的体积分数。实施例3合金配比、母合金制备和试样成型采用与实施例1相同的制备方法,快速凝固工序中试样的下半部加热到750℃,浸入冷却介质为冷却能力极强的Ga-In-Sn液态合金,得到内生相体积分数为10%的组织。试样的上半部在感应加热的区域加热到800℃,浸入冷却介质为冷却能力极强的Ga-In-Sn液态合金,得到内生相体积分数为8%的组织。实现变体积分数试样的制备。当前第1页1 2 3