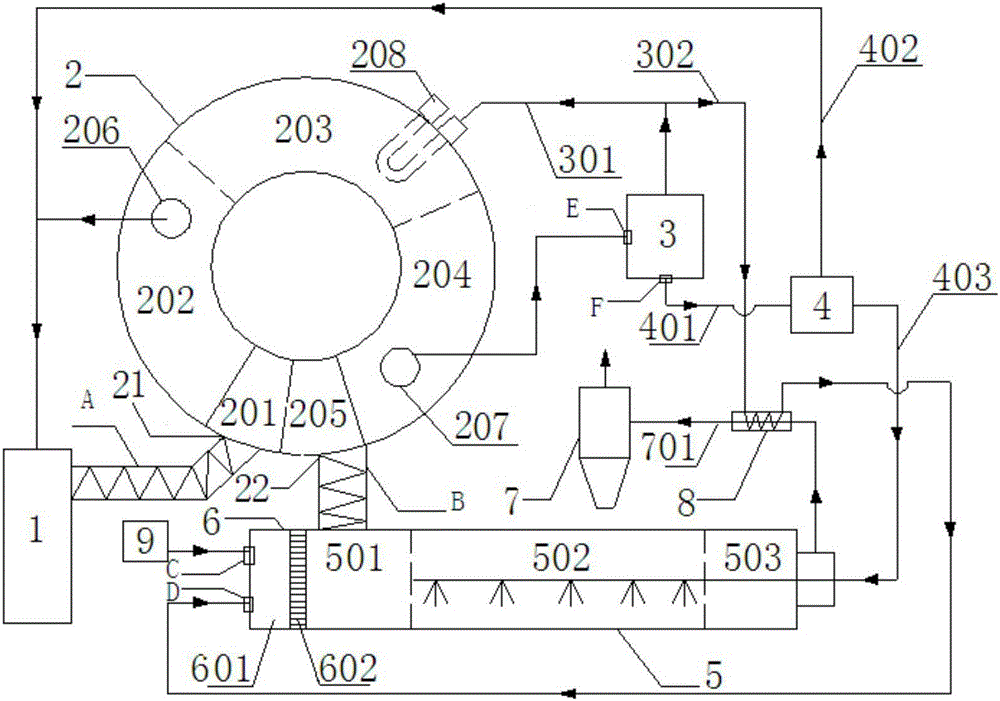
本发明涉及能源化工领域,具体而言,本发明涉及制备活性炭的系统及方法。
背景技术:
:污泥中含有大量的致病菌、寄生虫卵、病毒、重金属等有害物质,同时污泥中的有机质成分可通过多种技术进行利用。目前,国内外污泥利用技术种类繁多、技术复杂多样,其中主要的方法有:地表处理与填埋、污泥焚烧、污泥农用、污泥建材化利用以及污泥热裂解技术等。其中,地表处理与填埋技术相对简单,成本较低,但是需要占用大量的土地资源、污染地下水,同时不断发酵产生大量的甲烷,造成严重的温室效应;污泥焚烧是在有氧氛围下与污泥中的有机物充分反应,生成稳定的无机物,同时实现污泥的减量化和资源化利用。但是污泥焚烧成本高、能耗大,焚烧过程中存在二次污染,并产生二噁英等高致癌性气体;污泥农用是我国目前应用最广泛的污泥处置方式,其有机物中含有大量的植物生长必须的营养物质,可以改良土壤,增加土壤肥力,但是污泥中的重金属、病原体以及有机污染物等很难分解去除,农用时在土壤中积累,造成生态毒性问题;污泥建材化利用是重要的发展方向之一,但是目前面临着市场承载能力不足,限制其大规模发展。然而,目前污泥处理的系统及方法仍有待改进。技术实现要素:本发明旨在至少在一定程度上解决相关技术中的技术问题之一。为此,本发明的一个目的在于提出制备活性炭的方法和系统。该方法可以将污泥热解得到的污泥热解炭深加工为高附加值的活性炭,并且无需外加能源,低碳环保,适合大规模推广。在本发明的第一方面,本发明提出了一种制备活性炭的系统。根据本发明的实施例,所述系统包括:烘干单元,所述烘干单元适于将污泥进行烘干;热解单元,所述热解单元设置有污泥进料口和污泥热解炭出料口,所述污泥进料口与所述烘干单元相连,所述热解单元适于将所述烘干后的污泥进行热解,以便得到热解气和污泥热解炭;气液分离单元,所述气液分离单元与所述热解单元相连,适于将所述热解气进行气液分离,以便得到燃气和焦油;产蒸汽单元,所述产蒸汽单元与所述气液分离单元相连,适于将部分所述燃气供给至所述产蒸汽单元内,得到高温蒸汽;以及活化单元,所述活化单元分别与所述污泥热解炭出料口和产蒸汽单元相连,适于将所述污泥热解炭和部分所述高温蒸汽供给至所述活化单元,使得所述污泥热解炭进行活化处理,以便得到活性炭。由此,根据本发明实施例的制备活性炭的系统通过将经烘干的污泥供给至热解单元进行热解处理,得到热解气和污泥热解炭,热解气经气液分离后,得到燃气和焦油,其中焦油可以作为产蒸汽单元的燃料,使产蒸汽单元燃烧产生高温蒸汽,无需为产蒸汽单元外加能源,进而将高温蒸汽和污泥热解炭供给至活化单元进行活化处理,得到活性炭和高温烟气。该系统实现了污泥的充分利用,将污泥热解炭深加工为高附加值的活性炭,且能耗较低,对环境友好,适合大规模推广。另外,根据本发明上述实施例的制备活性炭的系统还可以具有如下附加的技术特征:根据本发明的实施例,所述热解单元为旋转床,沿物料流动方向,所述热解单元依次包括:进料区,所述进料区设置有所述污泥进料口,污泥进料口通过污泥进料螺旋与所述烘干单元相连;预热区,所述预热区设置有水蒸气排气口,所述水蒸气排气口与所述烘干单元相连,所述水蒸气排气口适于将烘干后的污泥进行预热所得到的水蒸气供给至所述烘干单元内;过渡区;产气区,所述产气区设置有热解气排气口,所述热解气排气口与所述气液分离单元相连,适于将产生的热解气供给至气液分离单元内;以及出料区,所述出料区设置有所述污泥热解炭出料口,其中,所述预热区、过渡区和产气区内设置有蓄热式辐射管。由此,可以进一步提高所述热解处理的效率。根据本发明的优选实施例,所述过渡区内设置蓄热式辐射管的数量大于所述预热区内设置蓄热式辐射管的数量且小于所述产气区内设置蓄热式辐射管的数量。由此,可以进一步提高所述热解处理的效率。根据本发明的实施例,所述活化单元为回转式活化炉,所述回转式活化炉包括:加热区,所述加热区的进料端与所述污泥热解炭出料口通过污泥热解炭出料螺旋相连,适于对所述污泥热解炭进行加热;活化区,所述活化区与所述加热区相连,适于对经过所述加热后的污泥热解炭进行活化处理,以便得到活性炭;以及降温区,所述降温区与所述活化区相连,适于将所述活性炭进行降温,其中,所述催化燃烧器包括:燃料预混区,所述燃料预混区设置有空气入口和燃气入口,适于将供给至的空气和燃气进行混合,得到混合气;以及覆有催化剂的载体。根据本发明的优选实施例,所述混合气的过剩空气系数为2。由此,可以进一步提高所述活化处理的效率。根据本发明的实施例,所述系统进一步包括:除尘器,所述除尘器与所述活化单元通过烟气管道相连,适于将所述活化单元中产生的烟气进行除尘。根据本发明的实施例,所述系统进一步包括:换热器,所述换热器设置于所述烟气管道上。由此,便于热量的回收利用。根据本发明的实施例,所述系统进一步包括:鼓风机,所述鼓风机与所述加热区相连,适于向所述加热区供给空气。由此,便于燃气燃烧放热,以促进污泥热解炭发生活化反应。根据本发明的实施例,所述气液分离单元包括:热解气进入口,所述热解气进入口与所述热解气排气口相连;第一燃气管道,所述第一燃气管道与所述蓄热式辐射管相连,适于使所述气液分离单元分离的一部分燃气供给至所述蓄热式辐射管作为燃料;第二燃气管道,所述第二燃气管道通过所述换热器与所述活化单元相连;以及焦油出口,所述焦油出口与所述产蒸汽单元相连,适于将所述气液分离单元分离的焦油供给至所述产蒸汽单元。根据本发明的实施例,所述污泥的粒径不大于100nm,优选45~55nm。由此,可以显著提高所述热解处理的效率。根据本发明的实施例,所述产蒸汽单元包括:焦油进入管道,所述焦油进入管道与所述焦油出口相连,适于将所述气液分离单元分离的焦油供给至所述产蒸汽单元内;第一蒸汽管道,所述第一蒸汽管道与所述烘干单元相连,适于将所述气液分离单元分离的部分高温蒸汽供给至所述烘干单元内;以及第二蒸汽管道,所述第二蒸汽管道与所述活化单元相连,适于将所述气液分离单元分离的另一部分高温蒸汽供给至所述活化单元内,根据本发明的具体实施例,供给至所述活化单元的高温蒸汽量与所述污泥热解炭质量之比为1:1.5。在本发明的另一方面,本发明提出了一种利用前面所描述的制备活性炭的系统制备活性炭的方法。根据本发明的实施例,所述方法包括:将污泥投入所述烘干单元中,进行烘干;将所述烘干后的污泥由所述污泥进料口送入所述热解单元中,进行热解处理,得到热解气和污泥热解炭;将所述热解气供给至所述气液分离单元,进行气液分离,以便得到燃气和焦油;将所述焦油供给至所述产蒸汽单元,以便得到高温蒸汽;以及将所述污泥热解炭和部分所述高温蒸汽供给至所述活化单元,以便对所述污泥热解炭进行活化处理,得到活性炭。由此,根据本发明实施例的制备活性炭的方法通过将经烘干的污泥供给至热解单元进行热解处理,得到热解气和污泥热解炭,热解气经气液分离后,得到燃气和焦油,其中焦油可以作为产蒸汽单元的燃料,使产蒸汽单元燃烧产生高温蒸汽,无需为产蒸汽单元外加能源,进而将高温蒸汽和污泥热解炭供给至活化单元进行活化处理,得到活性炭和高温烟气。该方法实现了污泥的充分利用,将污泥热解炭深加工为高附加值的活性炭,且能耗较低,对环境友好,适合大规模推广。根据本发明的实施例,所述方法进一步包括:将所述燃气分别供给至所述热解单元内的蓄热式辐射管和/或所述活化单元内的催化燃烧器;将另一部分所述高温蒸汽供给至所述烘干单元内,以便供所述污泥进行烘干。根据本发明的实施例,所述活化的温度为800~950℃。由此,可以显著提高所述活化处理的效率。根据本发明的实施例,所述热解的温度为500~850℃。由此,可以显著提高所述热解处理的效率。根据本发明的实施例,所述烘干后的污泥依次通过所述进料区、预热区、过渡区、产气区和出料区,其中,所述预热区的温度为150~400℃,所述过渡区的温度为400~500℃,所述产气区的温度为500~850℃。由此,可以显著提高所述热解处理的效率。根据本发明的实施例,所述燃烧产生的烟气中氧含量为8~10质量%、二氧化碳含量为4~6质量%、CO含量低于4mg/m3、NOx含量低于10mg/m3。由此,可以显著提高所述活化处理的效率,提高活性炭品质。本发明的附加方面和优点将在下面的描述中部分给出,部分将从下面的描述中变得明显,或通过本发明的实践了解到。附图说明本发明的上述和/或附加的方面和优点从结合下面附图对实施例的描述中将变得明显和容易理解,其中:图1显示了根据本发明一个实施例的制备电石系统的结构示意图;以及图2显示了根据本发明一个实施例的制备电石方法的流程示意图。具体实施方式下面详细描述本发明的实施例。下面描述的实施例是示例性的,仅用于解释本发明,而不能理解为对本发明的限制。需要说明的是,术语“第一”、“第二”仅用于描述目的,而不能理解为指示或暗示相对重要性或者隐含指明所指示的技术特征的数量。由此,限定有“第一”、“第二”的特征可以明示或者隐含地包括一个或者更多个该特征。进一步地,在本发明的描述中,除非另有说明,“多个”的含义是两个或两个以上。在本发明的描述中,需要理解的是,除非另有明确的规定和限定,术语“相连”应做广义理解,例如,可以是固定连接,也可以是可拆卸连接,或成一体;可以是机械连接,也可以是电连接;可以是直接相连,也可以通过中间媒介间接相连,可以是两个元件内部的连通或两个元件的相互作用关系,除非另有明确的限定。对于本领域的普通技术人员而言,可以根据具体情况理解上述术语在本发明中的具体含义。本发明提出了一种制备活性炭的系统和方法,下面将分别对其进行详细描述。制备活性炭的系统在本发明的一个方面,本发明提出了一种制备活性炭的系统。根据本发明的实施例,参见图1,该系统包括:烘干单元1、热解单元2、气液分离单元3、产蒸汽单元4以及活化单元5。根据本发明的实施例,烘干单元1适于将污泥进行烘干,以便进行后续热解处理。根据本发明的具体实施例,适用于旋转床的污泥粒径不受特别限制,在本发明的一些优选实施例中,该旋转床采用的污泥粒径在100mm以下,粒径过大资源利用率降低,结合旋转床的特点,在具体实施中,粒径为45~55mm可充分发挥旋转床热解优势,并达到极佳的资源利用率。根据本发明的实施例,热解单元2设置有污泥进料口21和污泥热解炭出料口22,该污泥进料口与烘干单元1相连,热解单元2适于将烘干后的污泥进行热解,以便得到热解气和污泥热解炭。根据本发明的实施例,热解处理的条件并不受特别限制,本领域技术人员可以根据实际需要进行选择,根据本发明的具体实施例,热解处理可以在500~850摄氏度下进行。发明人发现,如果热解处理的温度过低,则无法使污泥中的大分子有机物有效地分解为焦油等小分子化合物;而如果热解处理的温度过高,则会使能耗增大。根据本发明的具体实施例,热解单元为旋转床,沿物料流动方向,所述热解单元依次包括:进料区201、预热区202、过渡区203、产气区204和出料区205。根据本发明的具体实施例,进料区201设置有污泥进料口21,污泥进料口通过污泥进料螺旋A与烘干单元5相连。根据本发明的具体实施例,预热区202设置有水蒸气排气口206,水蒸气排气口206与烘干单元1相连,所述水蒸气排气口适于将烘干后的污泥进行预热所得到的水蒸气供给至烘干单元内。根据本发明的具体实施例,产气区204设置有热解气排气口207,热解气排气口207与气液分离单元3相连,适于将产生的热解气供给至气液分离单元3内。根据本发明的具体实施例,出料区205设置有污泥热解炭出料口22。根据本发明的具体实施例,预热区202、过渡区203和产气区204内设置有蓄热式辐射管208。根据本发明的优选实施例,过渡区内设置蓄热式辐射管的数量大于预热区内设置蓄热式辐射管的数量且小于产气区内设置蓄热式辐射管的数量。根据本发明的具体实施例,预热区的温度为150~400℃,过渡区的温度为400~500℃,产气区的温度为500~850℃。具体地,以天然气启动蓄热式辐射管,此辐射管不均匀的分布于预热区、过渡区和产气区,且其数量关系为预热区<过渡区<产气区,待正常产气后,可将气液分离单元分离的燃气通入蓄热式辐射管作为燃料;将污泥送入烘干设备进行烘干,污泥可从含水率80%左右烘干至50%,经污泥进料口将污泥由进料区送入旋转床1,在预热区进一步烘干,将水蒸气由水蒸气排气口排出,与产蒸汽单元送出的部分高温蒸汽混合后送入污泥烘干单元,经预热的污泥在产气区高温析出挥发分,产气区温度在500~850℃之间,所得热解气通过热解气排气口送至气液分离单元,所得污泥热解炭在出料区经污泥热解炭出料口送入活化单元。根据本发明的实施例,气液分离单元3与热解单元相连,适于将热解气分离,以便得到燃气和焦油。具体地,得到的燃气具有一定的热值,可以进一步作为后续步骤中所需的燃料气加以利用,而得到的焦油可以储存并对外销售,也可以通入产蒸汽单元,作为燃料用于产出高温蒸汽。根据本发明的实施例,气液分离单元包括:热解气进入口E、第一燃气管道301、第二燃气管302以及焦油出口F。根据本发明的实施例,燃气具有一定的热值,可以作为蓄热式辐射管和催化燃烧器的燃料气加以利用,无需另外通入额外的燃料气,从而可以降低热解处理和活化处理的能耗。根据本发明的具体实施例,所述热解气进入口E与热解气排气口22相连。根据本发明的具体实施例,第一燃气管道301与蓄热式辐射管208相连,适于使气液分离单元3分离的一部分燃气供给至蓄热式辐射管208作为燃料。根据本发明的实施例,燃气具有一定的热值,可以作为蓄热式辐射管的燃料气加以利用,无需另外通入额外的燃料气,从而可以降低热解处理能耗。根据本发明的具体实施例,第二燃气管道302通过换热器8与活化单元5相连。根据本发明的实施例,燃气具有一定的热值,可以作为催化燃烧器的燃料气加以利用,无需另外通入额外的燃料气,从而可以降低活化处理的能耗。此外,由活化单元产生的高温烟气会与燃气在换热器中进行热交换,从而提高低热值燃气的热量,使得燃气在催化燃烧器中可达到与天然气同等的放热效果。根据本发明的具体实施例,焦油出口F与产蒸汽单元4相连,适于将气液分离单元3分离的焦油供给至产蒸汽单元4。具体地,热解气经气液分离单元分离得到燃气和焦油。其中燃气分为两路,第一路燃气经第一燃气管道输送至旋转床的蓄热式辐射管,可通过调节蓄热式辐射管的烧嘴开度来控制辐射管的放热量,同时调节旋转床各区的温度;第二路燃气通过第二燃气管道在换热器中换热后通入活化单元加热区内设置的催化燃烧器,在换热器中换热的目的是提高低热值燃气的热量,使得燃气在催化燃烧器中可达到与天然气同等的放热效果。根据本发明的实施例,产蒸汽单元4与气液分离单元3相连,适于将部分燃气供给至产蒸汽单元4内,得到高温蒸汽。根据本发明的实施例,得到的高温蒸汽可以满足后续活化处理中所需的蒸汽量,从而可以降低活化处理的能耗。需要说明的是,对于产蒸汽单元的设备不作严格限定,只要能够实现产出高温蒸汽即可。根据本发明的具体实施例,产蒸汽单元可以为燃气锅炉。由此,气液分离单元产出的焦油可以作为燃气锅炉的燃料,以减少额外投入的燃料,节约成本。根据本发明的具体实施例,产蒸汽单元包括:焦油进入管道401、第一蒸汽管道402和第二蒸汽管道403。根据本发明的具体实施例,焦油进入管道401与焦油出口F相连,适于将气液分离单元3分离的焦油供给至产蒸汽单元内。根据本发明的具体实施例,第一蒸汽管道402与烘干单元1相连,适于将气液分离单元3分离的部分高温蒸汽供给至烘干单元1内。根据本发明的具体实施例,第二蒸汽管道403与活化单元5相连,适于将气液分离单元3分离的另一部分高温蒸汽供给至活化单元5内。根据本发明的具体实施例,供给至活化单元的高温蒸汽量与污泥热解炭质量之比为1:1.5。由此,以进一步加热污泥热解炭,使其达到活化温度,发生活化以得到活性炭。具体地,由气液分离单元分离出的焦油直接通入产蒸汽单元燃烧放热,所产蒸汽分为两路,第一路蒸汽通过第一蒸汽管道与来自于旋转床预热区产生的水蒸气混合后通入污泥烘干单元,将污泥由含水率80%烘干至50%。第二路蒸汽经第二蒸汽管道送入回转式活化炉,用于活化污泥热解炭。根据本发明的实施例,活化单元5分别与污泥热解炭出料口22和产蒸汽单元4相连,适于将污泥热解炭和部分高温蒸汽供给至活化单元5,使得污泥热解炭进行活化处理,以便得到活性炭。根据本发明的具体实施例,活化单元为回转式活化炉,回转式活化炉包括:加热区501、活化区502以及降温区503。根据本发明的具体实施例,加热区501的进料端与污泥热解炭出料口22通过污泥热解炭出料螺旋B相连,适于对污泥热解炭进行加热。根据本发明的具体实施例,活化区502与加热区501相连,适于对经过加热后的污泥热解炭进行活化处理,以便得到活性炭。根据本发明的具体实施例,降温区503与活化区502相连,适于将活性炭进行降温。根据本发明的具体实施例,加热区内设置有催化燃烧器6。具体地,该催化燃烧器包括:燃料预混区601,燃料预混区设置有空气入口C和燃气入口D,燃料预混区适于将通入的空气和燃气进行混合,得到混合气;以及覆有催化剂的载体602。根据本发明的具体实施例,覆有催化剂的载体为蘸有催化剂的蜂窝状堇青石载体。具体地,活化单元首先需要加热至800℃,并保证炉内的含氧量,其热量来源于催化燃烧器,由于催化燃烧是贫燃料、富氧燃烧,满足活化炉内的含氧量;根据本发明的实施例,催化燃烧后的烟气中,氧含量9%左右,二氧化碳含量5%左右,保证活化炉内含氧量的同时,二氧化碳也可与污泥热解炭中的炭黑反应,提高活性炭的品质;同时,催化燃烧烟气中污染物含量极低,CO低于4mg/m3,NOX含量低于10mg/m3,污染物近零排放。根据本发明的实施例,活化处理的条件并不受特别限制,本领域技术人员可以根据实际需要进行选择,根据本发明的具体实施例,活化处理是在800~950摄氏度下完成的。发明人发现,采用该温度进行活化处理,可以显著提高活化处理的效率并提高制备得到的活性炭的品质。具体地,根据本发明的实施例,首先启动回转式活化炉内的催化燃烧器,并使其中的过剩空气系数为2,使燃气与空气在蘸有催化剂的蜂窝状堇青石载体表面稳定无焰燃烧,从而向回转式活化炉中以辐射的方式传递热量,进一步地,向污泥热解炭喷洒高温蒸汽,使污泥热解炭的温度进一步升高,同时通过与高温蒸汽的不断接触不断活化,生成活性炭。此外,回转式活化炉中的二氧化碳还可以与污泥热解炭中的炭黑反应,从而提高制备得到的活性炭的品质,进一步增加活性炭的比表面积。根据本发明的实施例,该系统进一步包括:除尘器7、换热器8和鼓风机9。根据本发明的具体实施例,除尘器7与活化单元5通过烟气管道701相连,适于将活化单元5中产生的烟气进行除尘。根据本发明的实施例,由回转式活化炉排除的高温烟气与准备供给至催化燃烧器的燃气在换热器内进行热交换后,经除尘器除尘后达标排放。由于采用催化燃烧器对回转式活化炉进行加热,高温烟气经除尘后的尾气中污染物含量极低,其中CO含量不高于4毫克/立方米,NOx含量不高于10毫克/立方米。根据本发明的具体实施例,换热器8设置于烟气管道701上,此外,由气液分离单元分离得到的部分高温蒸汽流经换热器,再通入活化单元。由此,活化处理产生的高温烟气与气液分离单元分离的部分燃气能够实现热交换,从而可以有效地提高燃气的热值,使燃气在催化燃烧器中燃烧时可以达到与天然气同等的放热效果。根据本发明的具体实施例,鼓风机9与空气入口C相连,适于向燃料预混区供给空气。由此,通入的空气与气液分离单元分离的燃气在蘸有催化剂的蜂窝状堇青石载体表面稳定无焰燃烧,从而向回转式活化炉中以辐射的方式传递热量。由此,根据本发明实施例的制备活性炭的系统通过将经烘干的污泥供给至热解单元进行热解处理,得到污泥热解炭和热解气。热解气经气液分离后,得到燃气和焦油,其中焦油可以作为产蒸汽单元的燃料,使产蒸汽单元燃烧产生高温蒸汽,燃气可以分别作为燃料气供给至热解单元内的蓄热式辐射管和/或活化单元内的催化燃烧器,从而无需为产蒸汽单元、蓄热式辐射管和催化燃烧器外加能源。将高温蒸汽和污泥热解炭供给至活化单元进行活化处理,得到活性炭和高温烟气。经计算,生产1t活性炭需要2t蒸汽,2.5~3t污泥热解炭可产1t活性炭。该系统实现了污泥的充分利用,将污泥热解炭深加工为高附加值的活性炭,且能耗较低,对环境友好,适合大规模推广。制备活性炭的方法在本发明的另一方面,本发明提出了一种制备活性炭的方法。根据本发明的实施例,参见图2,该方法包括:S100烘干在该步骤中,将污泥投入烘干单元中,进行烘干。由此,以便进行后续热解处理。根据本发明的具体实施例,适用于旋转床的污泥粒径不受特别限制,在本发明的一些优选实施例中,该旋转床采用的污泥粒径在100mm以下,粒径过大资源利用率降低,结合旋转床的特点,在具体实施中,粒径为45~55mm可充分发挥旋转床热解优势,并达到极佳的资源利用率。S200热解在该步骤中,将烘干后的污泥由污泥进料口送入热解单元中,进行热解处理,得到热解气和污泥热解炭。根据本发明的实施例,热解处理的条件并不受特别限制,本领域技术人员可以根据实际需要进行选择,根据本发明的具体实施例,热解处理可以在500~850摄氏度下进行。发明人发现,如果热解处理的温度过低,则无法使污泥中的大分子有机物有效地分解为焦油等小分子化合物;而如果热解处理的温度过高,则会使能耗增大。根据本发明的具体实施例,热解单元为旋转床,沿物料流动方向,所述热解单元依次包括:进料区201、预热区202、过渡区203、产气区204和出料区205。根据本发明的具体实施例,进料区201设置有污泥进料口21,污泥进料口通过污泥进料螺旋A与烘干单元5相连。根据本发明的具体实施例,预热区202设置有水蒸气排气口206,水蒸气排气口206与烘干单元1相连,所述水蒸气排气口适于将烘干后的污泥进行预热所得到的水蒸气供给至烘干单元内。根据本发明的具体实施例,产气区204设置有热解气排气口207,热解气排气口207与气液分离单元3相连,适于将产生的热解气供给至气液分离单元3内。根据本发明的具体实施例,出料区205设置有污泥热解炭出料口22。根据本发明的具体实施例,预热区202、过渡区203和产气区204内设置有蓄热式辐射管208。根据本发明的优选实施例,过渡区内设置蓄热式辐射管的数量大于预热区内设置蓄热式辐射管的数量且小于产气区内设置蓄热式辐射管的数量。根据本发明的具体实施例,烘干后的污泥依次通过进料区、预热区、过渡区、产气区和出料区,其中,预热区的温度为150~400℃,过渡区的温度为400~500℃,产气区的温度为500~850℃。具体地,以天然气启动蓄热式辐射管,此辐射管不均匀的分布于预热区、过渡区和产气区,且其数量关系为预热区<过渡区<产气区,待正常产气后,可将气液分离单元分离的燃气通入蓄热式辐射管作为燃料;将污泥送入烘干设备进行烘干,污泥可从含水率80%左右烘干至50%,经污泥进料口将污泥由进料区送入旋转床1,在预热区进一步烘干,将水蒸气由水蒸气排气口排出,与产蒸汽单元送出的部分高温蒸汽混合后送入污泥烘干单元,经预热的污泥在产气区高温析出挥发分,产气区温度在500~850℃之间,所得热解气通过热解气排气口送至气液分离单元,所得污泥热解炭在出料区经污泥热解炭出料口送入活化单元。S300气液分离在该步骤中,将热解气供给至气液分离单元,进行气液分离,以便得到燃气和焦油。具体地,得到的燃气具有一定的热值,可以进一步作为后续步骤中所需的燃料气加以利用,而得到的焦油可以储存并对外销售,也可以通入产蒸汽单元,作为燃料用于产出高温蒸汽。根据本发明的实施例,该方法进一步包括:将燃气分别供给至热解单元内的蓄热式辐射管和/或活化单元内的催化燃烧器。根据本发明的实施例,气液分离单元包括:热解气进入口E、第一燃气管道301、第二燃气管302以及焦油出口F。根据本发明的实施例,燃气具有一定的热值,可以作为蓄热式辐射管和催化燃烧器的燃料气加以利用,无需另外通入额外的燃料气,从而可以降低热解处理和活化处理的能耗。根据本发明的具体实施例,所述热解气进入口E与热解气排气口22相连。根据本发明的具体实施例,第一燃气管道301与蓄热式辐射管208相连,适于使气液分离单元3分离的一部分燃气供给至蓄热式辐射管208作为燃料。根据本发明的实施例,燃气具有一定的热值,可以作为蓄热式辐射管的燃料气加以利用,无需另外通入额外的燃料气,从而可以降低热解处理能耗。根据本发明的具体实施例,第二燃气管道302通过换热器8与活化单元5相连。根据本发明的实施例,燃气具有一定的热值,可以作为催化燃烧器的燃料气加以利用,无需另外通入额外的燃料气,从而可以降低活化处理的能耗。此外,由活化单元产生的高温烟气会与燃气在换热器中进行热交换,从而提高低热值燃气的热量,使得燃气在催化燃烧器中可达到与天然气同等的放热效果。根据本发明的具体实施例,焦油出口F与产蒸汽单元4相连,适于将气液分离单元3分离的焦油供给至产蒸汽单元4。具体地,热解气经气液分离单元分离得到燃气和焦油。其中燃气分为两路,第一路燃气经第一燃气管道输送至旋转床的蓄热式辐射管,可通过调节蓄热式辐射管的烧嘴开度来控制辐射管的放热量,同时调节旋转床各区的温度;第二路燃气通过第二燃气管道在换热器中换热后通入活化单元加热区内设置的催化燃烧器,在换热器中换热的目的是提高低热值燃气的热量,使得燃气在催化燃烧器中可达到与天然气同等的放热效果。S400产蒸汽在该步骤中,将焦油供给至产蒸汽单元,以便得到高温蒸汽。根据本发明的实施例,得到的高温蒸汽可以满足后续活化处理中所需的蒸汽量,从而可以降低活化处理的能耗。需要说明的是,对于产蒸汽单元的设备不作严格限定,只要能够实现产出高温蒸汽即可。根据本发明的具体实施例,产蒸汽单元可以为燃气锅炉。由此,气液分离单元产出的焦油可以作为燃气锅炉的燃料,以减少额外投入的燃料,节约成本。根据本发明的具体实施例,产蒸汽单元包括:焦油进入管道401、第一蒸汽管道402和第二蒸汽管道403。根据本发明的具体实施例,焦油进入管道401与焦油出口F相连,适于将气液分离单元3分离的焦油供给至产蒸汽单元内。根据本发明的实施例,该方法进一步包括:将另一部分高温蒸汽供给至烘干单元内,以便供污泥进行烘干。根据本发明的具体实施例,第一蒸汽管道402与烘干单元1相连,适于将气液分离单元3分离的部分高温蒸汽供给至烘干单元1内。根据本发明的具体实施例,第二蒸汽管道403与活化单元5相连,适于将气液分离单元3分离的另一部分高温蒸汽供给至活化单元5内。根据本发明的具体实施例,供给至活化单元的高温蒸汽量与污泥热解炭质量之比为1:1.5。由此,以进一步加热污泥热解炭,使其达到活化温度,发生活化以得到活性炭。具体地,由气液分离单元分离出的焦油直接通入产蒸汽单元燃烧放热,所产蒸汽分为两路,第一路蒸汽通过第一蒸汽管道与来自于旋转床预热区产生的水蒸气混合后通入污泥烘干单元,将污泥由含水率80%烘干至50%。第二路蒸汽经第二蒸汽管道送入回转式活化炉,用于活化污泥热解炭。S500活化在该步骤中,将污泥热解炭和高温蒸汽的供给至活化单元,以便对污泥热解炭进行活化处理,以便得到活性炭。根据本发明的实施例,活化单元5分别与污泥热解炭出料口22和产蒸汽单元4相连,适于将污泥热解炭和部分高温蒸汽供给至活化单元5,使得污泥热解炭进行活化处理,以便得到活性炭。根据本发明的具体实施例,活化单元为回转式活化炉,回转式活化炉包括:加热区501、活化区502以及降温区503。根据本发明的具体实施例,加热区501的进料端与污泥热解炭出料口22通过污泥热解炭出料螺旋B相连,适于对污泥热解炭进行加热。根据本发明的具体实施例,活化区502与加热区501相连,适于对经过加热后的污泥热解炭进行活化处理,以便得到活性炭。根据本发明的具体实施例,降温区503与活化区502相连,适于将活性炭进行降温。根据本发明的具体实施例,加热区内设置有催化燃烧器6。具体地,该催化燃烧器包括:燃料预混区601,燃料预混区设置有空气入口C和燃气入口D,燃料预混区适于将通入的空气和燃气进行混合,得到混合气;以及覆有催化剂的载体602。根据本发明的具体实施例,覆有催化剂的载体为蘸有催化剂的蜂窝状堇青石载体。具体地,活化单元首先需要加热至800℃,并保证炉内的含氧量,其热量来源于催化燃烧器,由于催化燃烧是贫燃料、富氧燃烧,满足活化炉内的含氧量;根据本发明的实施例,催化燃烧后的烟气中,氧含量9%左右,二氧化碳含量5%左右,保证活化炉内含氧量的同时,二氧化碳也可与污泥热解炭中的炭黑反应,提高活性炭的品质;同时,催化燃烧烟气中污染物含量极低,CO低于4mg/m3,NOX含量低于10mg/m3,污染物近零排放。根据本发明的实施例,活化处理的条件并不受特别限制,本领域技术人员可以根据实际需要进行选择,根据本发明的具体实施例,活化处理是在800~950摄氏度下完成的。发明人发现,采用该温度进行活化处理,可以显著提高活化处理的效率并提高制备得到的活性炭的品质。具体地,根据本发明的实施例,首先启动回转式活化炉内的催化燃烧器,并使其中的过剩空气系数为2,使燃气与空气在蘸有催化剂的蜂窝状堇青石载体表面稳定无焰燃烧,从而向回转式活化炉中以辐射的方式传递热量,进一步地,向污泥热解炭喷洒高温蒸汽,使污泥热解炭的温度进一步升高,同时通过与高温蒸汽的不断接触不断活化,生成活性炭。此外,回转式活化炉中的二氧化碳还可以与污泥热解炭中的炭黑反应,从而提高制备得到的活性炭的品质,进一步增加活性炭的比表面积。由此,根据本发明实施例的制备活性炭的方法通过将经烘干的污泥供给至热解单元进行热解处理,得到污泥热解炭和热解气。热解气经气液分离后,得到燃气和焦油,其中焦油可以作为产蒸汽单元的燃料,使产蒸汽单元燃烧产生高温蒸汽,燃气可以分别作为燃料气供给至热解单元内的蓄热式辐射管和/或活化单元内的催化燃烧器,从而无需为产蒸汽单元、蓄热式辐射管和催化燃烧器外加能源。将高温蒸汽和污泥热解炭供给至活化单元进行活化处理,得到活性炭和高温烟气。经计算,生产1t活性炭需要2t蒸汽,2.5~3t污泥热解炭可产1t活性炭。该方法实现了污泥的充分利用,将污泥热解炭深加工为高附加值的活性炭,且能耗较低,对环境友好,适合大规模推广。下面将结合实施例对本发明的方案进行解释。本领域技术人员将会理解,下面的实施例仅用于说明本发明,而不应视为限定本发明的范围。实施例中未注明具体技术或条件的,按照本领域内的文献所描述的技术或条件或者按照产品说明书进行。所用试剂或仪器未注明生产厂商者,均为可以通过市购获得的常规产品。实施例1将堆密度为939m3/kg,含水率80%的昌平污水厂污泥通入烘干单元,烘干后的污泥含水率位50%,通过旋转床的进料区送入炉内热解。旋转床旋转一周用时90min,炉膛内的温度分布为:预热区150~400℃;过渡区400~500℃;产气区500~850℃。热解后的热解气供给至气液分离单元进行气液分离,得到燃气和焦油。热解后的热解气、污泥热解炭及焦油的产率见表1,污泥热解炭的工业分析和元素分析见表2,热解气的气体成分及热值见表3。将污泥热解炭通入回转式活化炉,活化炉内的温度在800℃以上,通过催化燃烧器,使得活化炉内含氧量为9%,打开蒸汽,使得污泥热解炭与蒸汽比例为1.5:1,污泥热解炭在加热区由600℃升至800℃,并随炉体转动进入活化区,此时污泥热解炭与水蒸气接触反应后,温度迅速升高至950℃,并经过30min的活化进入降温区,生成高品质的活性炭,其碘值大于1000mg/g。表1.市政污泥热解后产物产率工况固体产率/%气体产率/%油产率/%水产率/%143.5016.7517.2522.50240.1517.5019.8522.50表2.污泥热解炭工业分析和元素分析及热值表3.市政污泥热解气组分及热值在本说明书的描述中,参考术语“一个实施例”、“一些实施例”、“示例”、“具体示例”、或“一些示例”等的描述意指结合该实施例或示例描述的具体特征、结构、材料或者特点包含于本发明的至少一个实施例或示例中。在本说明书中,对上述术语的示意性表述不必须针对的是相同的实施例或示例。而且,描述的具体特征、结构、材料或者特点可以在任一个或多个实施例或示例中以合适的方式结合。此外,在不相互矛盾的情况下,本领域的技术人员可以将本说明书中描述的不同实施例或示例以及不同实施例或示例的特征进行结合和组合。尽管上面已经示出和描述了本发明的实施例,可以理解的是,上述实施例是示例性的,不能理解为对本发明的限制,本领域的普通技术人员在本发明的范围内可以对上述实施例进行变化、修改、替换和变型。当前第1页1 2 3