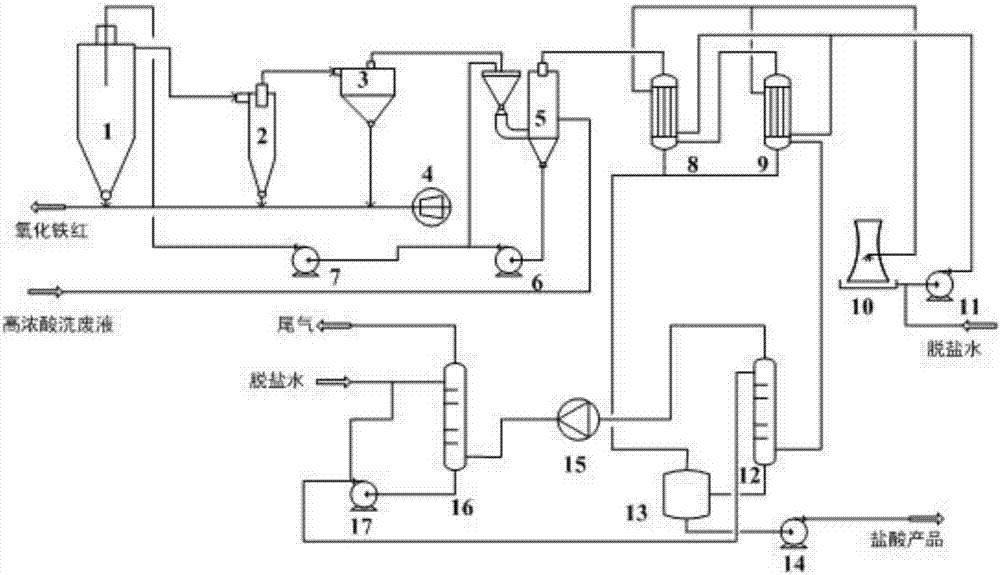
本发明涉及酸洗废液处理
技术领域:
,尤其涉及一种高浓酸洗废液再生工艺及系统。
背景技术:
:在钢材深加工过程中,需对其表面进行酸洗除锈处理。常用的酸洗液为盐酸和硫酸,目前大多数企业均采用盐酸作为酸洗液。钢材经盐酸酸洗后,会产生大量的酸洗废液。盐酸酸洗废液的组成主要是氯化氢、氯化亚铁、水及少量杂质,各成分含量随酸洗工艺、操作温度、钢材品种和规格不同而异,一般含氯化亚铁10~20%,氯化氢3~10%。其中,钢铁热轧所产生的酸洗废液一般含有1~5g/l的h+,60~250g/l的fe2+,由于酸洗废液具有严重的腐蚀性,已被列入《国家危险废物名录》,该类废液直接排放不仅严重污染环境,而且造成极大的浪费。按国家环保要求酸洗废液是不能直接排放的,传统的处理方法有中和法、蒸发结晶法或焙烧回收盐酸法。中和法是目前钢铁企业普遍采用的方法,但其存在的缺点也较突出,一方面要消耗大量的碱性药剂(如烧碱、石灰等),处理成本十分昂贵;另一方面又会生成大量难以处置的含铁污泥,对环境造成变相二次污染;蒸发结晶法是通过对废酸液加热蒸发、冷凝器冷凝后形成稀盐酸,返回车间重新使用;通过蒸发浓缩、冷却浓缩液析出fecl2结晶,得到固体产品。该技术的优点是能处理废酸液,回收98%以上的盐酸,盐酸浓度比废液浓度下降1%~4%;使fe2+全部以fecl2固体形式排出,且设备简单,投资小,处理成本低;但是,此技术存在着极大的环境风险和市场风险,为了节约成本,用于酸洗的盐酸多采用其他化工行业的副产盐酸,其中含有大量的有机物甚至是有毒的物质,虽然对钢铁行业酸洗没有影响,但蒸发浓缩后获得的氯化亚铁等产品均不可避免的含有一些有机物甚至是有毒物质,而fecl2一般是作为净水剂使用,一旦上述有毒的氯化亚铁等产品用于水处理中,必然对所处理的水造成二次污染,后果不堪设想。加之净水剂市场需求量有限,也严重限制了该技术的应用。焙烧回收盐酸法将废液的加热、脱水、亚铁盐的氧化和水解、氯化氢气体的收集及吸收成盐酸有机地结合在一个系统内一并完成,具有处理能力大、设施紧凑、资源回收率高(可达98%~99%),再生酸浓度高、酸中含fe2+少、氧化铁品位高(可达98%以上)及应用广等特点,因此得到了快速推广;目前,国内有两百余套焙烧法回收盐酸法装置在连续运行。现有的焙烧回收盐酸法最为广泛的技术为奥地利的ruthner工艺技术,国内大多采用此技术。但是,随着钢铁行业对酸洗效率的要求愈来愈高,使用高浓度的盐酸作为酸洗介质以大幅度提高酸洗效率成为趋势。但是,盐酸在常压情况下,22%是其恒沸浓度,ruthner工艺技术由于采用水吸收hcl的工艺,其再生盐酸的浓度无法超过22%wt,只能达到18%-~20%wt,无法满足企业对22%以上浓度再生盐酸的需求。技术实现要素:本发明提供了一种高浓酸洗废液再生工艺及系统,预浓缩器后的烟气直接采用二级冷凝装置进行冷凝,将烟气中的高浓度hcl与水冷凝下来,避开盐酸溶液的恒沸点,实现再生盐酸浓度超过22%以上的目标,冷凝后烟气中更高浓度的hcl在盐酸吸收塔中用水吸收,获得所需浓度的盐酸。为了达到上述目的,本发明采用以下技术方案实现:一种高浓酸洗废液再生工艺,包括如下步骤:1)fe离子浓度>150g/l的高浓度酸洗废液在预浓缩器中经高温烟气浓缩,浓缩后fe离子浓度>200g/l的酸洗废液进入水解焙烧炉中进行高温分解,分解温度400~700℃;2)将步骤1)制备的含hcl的高温烟气依次送入旋风除尘器与多管除尘器进行除尘处理,其中95%以上的粉尘被收集后作为氧化铁红回收利用;3)将步骤2)得到气体送入预浓缩器,与高浓度酸洗废液进行接触,完成除尘、液体浓缩、气体降温等过程,预浓缩器操作温度85~95℃;4)将经步骤3)处理后的气体进行二级冷凝,冷凝温度分别为65~75℃和45~55℃,获得浓度为23~25%wt的高浓度再生盐酸;5)将经步骤4)处理后的气体送入盐酸吸收塔,用水吸收,获得浓度为23~25%wt的高浓度再生盐酸;吸收hcl气体后的烟气送往洗涤塔进行洗涤,洗涤后的烟气达标排放,洗涤液作为盐酸吸收液使用。所述水解焙烧炉炉顶温度顶350~450℃,炉底温度650~750℃,表压-200~300pa。用于实现所述工艺的一种高浓酸洗废液再生系统,包括水解煅烧炉、二级除尘装置、预浓缩器、二级冷凝装置、空冷塔、盐酸吸收塔和洗涤塔;所述水解煅烧炉的上部烟气出口依次通过由旋风分离器和多管除尘器组成的二级除尘装置连接预浓缩器顶部烟气入口;水解煅烧炉、旋风分离器和多管除尘器的粉末出口分别连接气力输送管道,气力输送管道上设有气力输送风机;预浓缩器的底部液体出口一路通过循环浓缩泵连接预浓缩器的顶部液体入口,另一路通过给料泵连接水解煅烧炉的顶部液体喷枪;预浓缩器上的浓缩酸液入口连接高浓度酸洗废液输送管道;预浓缩器的气体出口依次通过由第一冷凝器和第二冷凝器组成的二级冷凝装置连接盐酸吸收塔底部气体入口;第一冷凝器和第二冷凝器的液体出口连接盐酸混合槽的液体入口;第一冷凝器和第二冷凝器的冷却水入口通过空冷循环泵连接空冷塔的出口,空冷循环泵入口另外连接脱盐水输送管道;第一冷凝器和第二冷凝器的冷却水出口连接空冷塔的入口;盐酸吸收塔底部液体出口连接盐酸混合槽的液体入口,盐酸混合槽的液体出口通过盐酸泵连接盐酸产品外送管道;盐酸吸收塔顶部气体出口通过耐酸风机连接洗涤塔的底部气体入口;洗涤塔的底部液体出口通过洗涤泵连接盐酸吸收塔顶部液体入口和洗涤塔顶部液体入口;洗涤塔顶部液体入口另外连接脱盐水输送管道。与现有技术相比,本发明的有益效果是:1)能够获得浓度超过22%的高浓度再生盐酸产品,满足现有企业采用高效酸洗工艺对高浓度盐酸的需求;2)基于ruthner技术进行技术改进,广泛适用于新建工程项目及现有工程改造,改造方案简单,易于实施。附图说明图1是本发明所述一种高浓酸洗废液再生工艺的原理框图。图2是本发明所述一种高浓酸洗废液再生工艺的流程图。图中:1.水解煅烧炉2.旋风分离器3.多管除尘器4.气力输送风机5.预浓缩器6.循环浓缩泵7.给料泵8.第一冷凝器9.第二冷凝器10.空冷塔11.空冷循环泵12.盐酸吸收塔13.盐酸混合槽14.盐酸泵15.耐酸风机16.洗涤塔17.洗涤泵具体实施方式下面结合附图对本发明的具体实施方式作进一步说明:如图1、图2所示,本发明所述一种高浓酸洗废液再生工艺,包括如下步骤:1)fe离子浓度>150g/l的高浓度酸洗废液在预浓缩器5中经高温烟气浓缩,浓缩后fe离子浓度>200g/l的酸洗废液进入水解焙烧炉1中进行高温分解,分解温度400~700℃;2)将步骤1)制备的含hcl的高温烟气依次送入旋风除尘器2与多管除尘器3进行除尘处理,其中95%以上的粉尘被收集后作为氧化铁红回收利用;3)将步骤2)得到气体送入预浓缩器5,与高浓度酸洗废液进行接触,完成除尘、液体浓缩、气体降温等过程,预浓缩器5操作温度85~95℃;4)将经步骤3)处理后的气体进行二级冷凝,冷凝温度分别为65~75℃和45~55℃,获得浓度为23~25%wt的高浓度再生盐酸;5)将经步骤4)处理后的气体送入盐酸吸收塔12,用水吸收,获得浓度为23~25%wt的高浓度再生盐酸;吸收hcl气体后的烟气送往洗涤塔16进行洗涤,洗涤后的烟气达标排放,洗涤液作为盐酸吸收液使用。所述水解焙烧炉1炉顶温度顶350~450℃,炉底温度650~750℃,表压-200~300pa。用于实现所述工艺的一种高浓酸洗废液再生系统,包括水解煅烧炉1、二级除尘装置、预浓缩器5、二级冷凝装置、空冷塔10、盐酸吸收塔12和洗涤塔16;所述水解煅烧炉1的上部烟气出口依次通过由旋风分离器2和多管除尘器3组成的二级除尘装置连接预浓缩器5顶部烟气入口;水解煅烧炉1、旋风分离器2和多管除尘器3的粉末出口分别连接气力输送管道,气力输送管道上设有气力输送风机4;预浓缩器5的底部液体出口一路通过循环浓缩泵6连接预浓缩器5的顶部液体入口,另一路通过给料泵7连接水解煅烧炉1的顶部液体喷枪;预浓缩器5上的浓缩酸液入口连接高浓度酸洗废液输送管道;预浓缩器5的气体出口依次通过由第一冷凝器8和第二冷凝器9组成的二级冷凝装置连接盐酸吸收塔12底部气体入口;第一冷凝器8和第二冷凝器9的液体出口连接盐酸混合槽13的液体入口;第一冷凝器8和第二冷凝器9的冷却水入口通过空冷循环泵11连接空冷塔10的出口,空冷循环泵11入口另外连接脱盐水输送管道;第一冷凝器8和第二冷凝器9的冷却水出口连接空冷塔10的入口;盐酸吸收塔12底部液体出口连接盐酸混合槽13的液体入口,盐酸混合槽13的液体出口通过盐酸泵14连接盐酸产品外送管道;盐酸吸收塔12顶部气体出口通过耐酸风机15连接洗涤塔16的底部气体入口;洗涤塔16的底部液体出口通过洗涤泵27连接盐酸吸收塔12顶部液体入口和洗涤塔16顶部液体入口;洗涤塔16顶部液体入口另外连接脱盐水输送管道。本发明所述一种高浓酸洗废液再生工艺在现有ruthner技术进行了改进,工艺过程中高浓度的酸洗废液在预浓缩器5中被高温烟气浓缩后进入水解煅烧炉1中进行高温分解,获得的高温烟气经过旋风除尘器2与多管除尘器3除尘后进入预浓缩器5,与要处理的酸洗废液进行接触,温度降低至85-95℃的气体不是直接用水进行吸收,而是进入二级冷凝装置8、9进行冷凝,将烟气中的hcl与水冷凝下来;由于避免了水的加入,使高浓度的hcl与水可以同时冷凝下来,避开了盐酸溶液的恒沸点,实现再生盐酸浓度超过22%以上。冷凝处理后的烟气中含有浓度更高的hcl,在盐酸吸收塔12中利用一定配比的水进行吸收,获得所需浓度的盐酸。吸收盐酸的尾气经过洗涤塔16进一步吸收,尾气达标排放。以下实施例在以本发明技术方案为前提下进行实施,给出了详细的实施方式和具体的操作过程,但本发明的保护范围不限于下述的实施例。下述实施例中所用方法如无特别说明均为常规方法。【实施例1】1)以天然气作为热源对水解煅烧炉1进行预热,然后加热到所需的温度,其中炉顶温度400℃,炉底温度700℃;将高浓度酸洗废液加入预浓缩器5中,对高温烟气降温的同时,实现高浓度酸洗废液的预浓缩。所需处理的高浓度酸洗废液成分组成如下表所示:成分含量g/l流量kg/h备注fecl347.91105.402fe3+=16.51g/lfecl2340.45748.99fe2+=150.0g/lhcl75.73166.606—h2o911.12004.42—总计1375.193025.418—每小时处需理酸洗废液3.025吨。2)经预浓缩器5预浓缩后的酸洗废液成分组成如下表所示:成分含量g/l流量kg/h备注fecl363.87105.3855fe3+=22.01g/lfecl2453.96749.034fe2+=200g/lhcl135.29223.2285—h2o683.321127.478—总计1336.442205.126—经高温水解后的气体成分组成如下表所示:成分体积%hcl10.5h2o39.8o23.77n242.16co23.77气体总体积为9800m3,温度400℃。气体中含有fe2o360kg,经过二级除尘后,粉尘回收量为57kg,回收率达到95%。水解煅烧炉1炉底收集氧化铁红粉末450kg,其中fe2o3含量为98.8%wt,cl含量1.01%wt,堆密度400kg/m3。经预浓缩器5浓缩后的气体成分组成:成分体积%hcl7.88h2o49.9o23.18n235.5co23.18气体总体积为6413m3/h,密度0.818kg/m3,温度93.5℃。3)进行二级冷凝、吸收、洗涤:其中第一冷凝器8的冷凝温度为70℃,第二冷凝器9的冷凝温度为50℃。盐酸吸收塔12的进液量为224.4kg/h,其中hcl含量为2%wt。经过二级冷凝及盐酸吸收后获得的盐酸量为2629kg/h,浓度为23%wt。经过洗涤塔16后的气体成分组成为:成分体积%hcl1.0×10-3h2o8.87o26.95n277.0co27.18气体总体积2700m3/h,温度41℃。【实施例2】1)以天然气作为热源对水解煅烧炉1进行预热,然后加热到所需的温度,其中炉顶温度350℃,炉底温度650℃;将高浓度酸洗废液加入预浓缩器5中,对高温烟气降温的同时,实现高浓度酸洗废液的预浓缩;所处理的高浓度酸洗废液成分组成如下表所示:成分含量g/l流量kg/h备注fecl347.91105.402fe3+=16.51g/lfecl2340.45748.99fe2+=150.0g/lhcl75.73166.606h2o911.12004.42总计1375.193025.418每小时面需处理酸洗废液量3.025吨2)高浓度酸洗废液经预浓缩器5预浓缩后的成分组成如下表所示:成分含量g/l流量kg/h备注fecl361.10105.7fe3+=21.21g/lfecl2435.28753.0fe2+=191.9g/lhcl130.1224.9h2o703.521172.5总计13302300浓缩后的液体进行高温水解,水解后的气体成分组成如下表所示:成分体积%hcl10.5h2o39.5o23.95n242.1co23.95气体总体积合计8526m3/h,温度350℃。气体中含有fe2o345kg,粉尘回收量为43.2kg,回收率达到96%。水解煅烧炉1炉底收集氧化铁红粉末452kg,其中fe2o3含量98.2%wt,cl含量1.51%wt,堆密度400kg/m3。经预浓缩器5浓缩后的气体成分组成如下表所示:成分体积%hcl7.83h2o48.3o23.58n236.8co23.49气体总体积为5761m3/h,密度0.819kg/m3,温度92.3℃。3)进行二级冷凝、吸收、洗涤;其中第一冷凝器8的冷凝温度70℃,第二冷凝器9的冷凝温度50℃。盐酸吸收塔12的进液量为224.4kg/h,其中hcl含量为2%wt。经过二级冷凝及盐酸吸收后获得的盐酸量为2314kg/h,浓度为23%wt。经过洗涤塔16后的气体成分组成如下表所示:成分体积%hcl1.0×10-3h2o5.52o28.85n274.8co210.83气体体积2537m3/h,温度42℃。【实施例3】1)以天然气作为热源对水解煅烧炉1进行预热,然后加热到所需的温度,其中炉顶温度450℃,炉底温度750℃;将高浓度酸洗废液加入预浓缩器5中,对高温烟气降温的同时实现酸洗废液的预浓缩;所处理的高浓度酸洗废液成分组成如下表所示:成分含量g/l流量kg/h备注fecl347.91105.402fe3+=16.51g/lfecl2340.45748.99fe2+=150.0g/lhcl75.73166.606h2o911.12004.42总计1375.193025.418每小时需处理高浓度酸洗废液3.025吨。2)高浓度酸洗废液经预浓缩器5预浓缩后的成分组成如下表所示:成分含量g/l流量kg/h备注fecl366.90105.7fe3+=22.01g/lfecl2461.7729.5fe2+=200g/lhcl132.1208.7h2o719.31136.1总计13802180.0预浓缩后液体进行高温水解,水解后的气体成分组成如下表所示:成分体积%hcl10.4h2o38.71o24.33n242.68co23.88气体总体积合计10593m3,温度450℃。气体中含有fe2o370kg,粉尘回收量为66.5kg,回收率达到95%。水解煅烧炉1炉底收集氧化铁红粉末435kg,其中fe2o3含量99.1%wt,cl含量0.78%wt,堆密度400kg/m3。经过预浓缩器后的气体成分组成如下表所示:成分体积%hcl7.94h2o50.41o23.52n234.95co23.18气体总体积为6610m3/h,密度0.818kg/m3,温度93.9℃3)进行二级冷凝、吸收、洗涤;其中第一冷凝器8的冷凝温度70℃,第二冷凝器9的冷凝温度50℃。盐酸吸收塔12的进液体为255kg/h,其中hcl含量为2%wt。经过二级冷凝,然后经过盐酸吸收后获得的盐酸量为2743kg/h,浓度为23%wt。经过洗涤塔16后的气体组成为:成分体积%hcl1.0×10-3h2o8.91o27.69n276.6co26.80气体体积2767m3/h,温度42℃。以上所述,仅为本发明较佳的具体实施方式,但本发明的保护范围并不局限于此,任何熟悉本
技术领域:
的技术人员在本发明揭露的技术范围内,根据本发明的技术方案及其发明构思加以等同替换或改变,都应涵盖在本发明的保护范围之内。当前第1页12