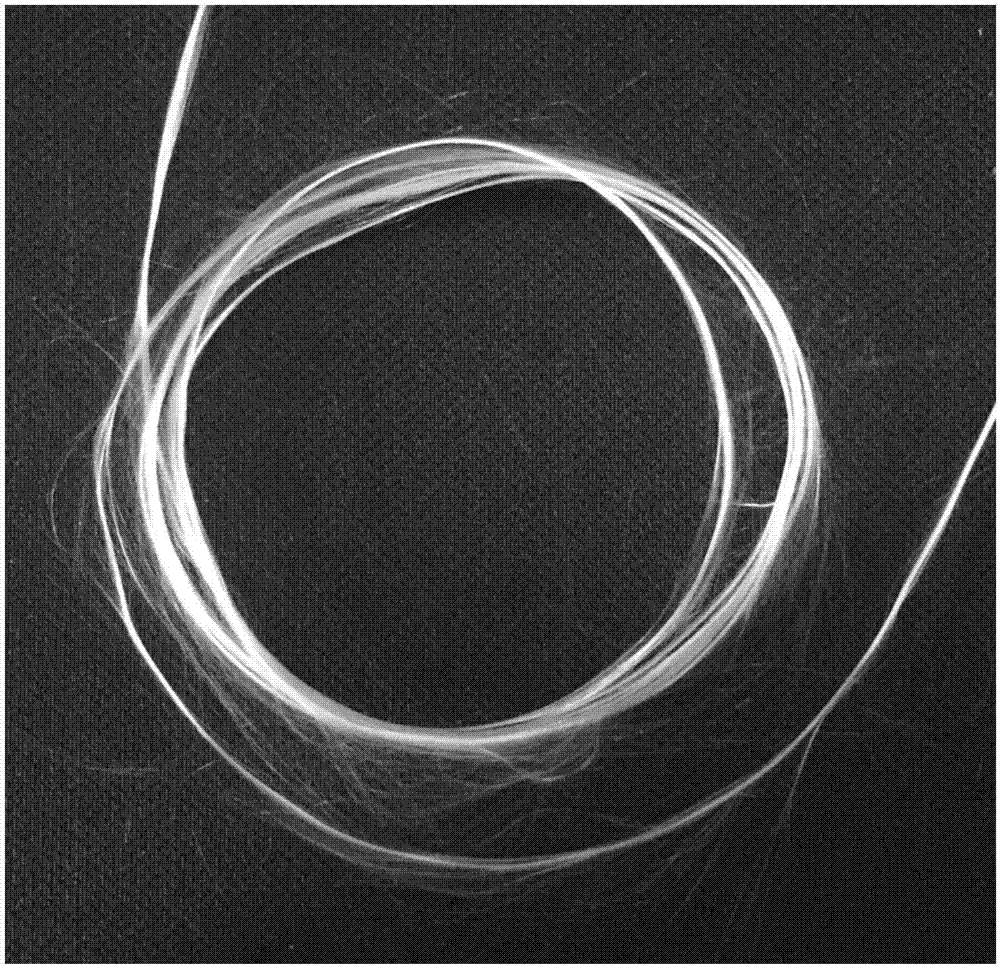
本发明涉及一种连续纤维表面改性技术,具体涉及一种氧化铝连续纤维加捻纱专用浸润剂及其制备方法,属于无机陶瓷纤维浸润剂领域。
背景技术:
:氧化铝连续纤维是重要的高性能无机非金属材料,属于陶瓷纤维的一种,以al2o3为主要成分,同时还添加fe2o3、sio2等。通过溶胶凝胶法结合干法纺丝制备的氧化铝连续纤维具有直径小、高强度、耐高温、耐腐蚀、可编织、重量轻、表面光洁等一系列优点,可以做高温高效隔热材料、高性能复合材料和催化剂载体等,应用在高温工业炉、新材料、化工以及军工、核工业、航天航空等领域。目前通过溶胶凝胶法制备氧化铝连续纤维是将制备好的可纺性溶胶加入到料筒中,通过一定压力的挤压使可纺性溶胶从喷丝孔中挤出进入纺丝甬道形成细流,在甬道热空气作用下,细流中水快速挥发,纤维发生固化,在收丝辊缠绕力的作用下伸长变细形成凝胶纤维,再将凝胶纤维放入高温炉中煅烧形成氧化铝连续纤维,通过加捻收丝得到氧化铝连续纤维成品。而氧化铝凝胶纤维在高温煅烧过程中,由于纤维受热分解发生收缩,纤维单丝之间产生摩擦形成较强的静电作用,在后续的合股加捻工艺中由于强静电作用影响纤维的成束性,再加上纤维表面不润滑,氧化铝纤维本身柔韧性较差在加捻过程中受到扭曲力导致纤维发生断丝现象,影响纤维束的性能,从而影响氧化铝连续纤维的成品生产。要解决以上存在的问题就需要对氧化铝连续纤维进行表面改性,消除静电,赋予纤维一定的柔韧性、表面润滑性,同时将数百根乃至数千根纤维单丝集成一束,使纤维顺利完成合股加捻工艺。纤维表面改性技术大体可以分成三类:等离子体改性、氧化改性技术及涂层改性技术。其中利用等离子体改性技术可以改善纤维浸润性、粘结性、亲水性等性能以及对纤维的消毒清洗等(参见:毕松梅等,产业用纺织品2013,6,32-35);氧化改性技术又分为电化学氧化、气相氧化法和液相氧化法,利用氧化改性技术处理纤维,可以改善纤维表面状态(参见:张美云,中国造纸学会第十三届学术年会论文集(下),2008);涂层改性技术一般是通过制备纤维专用浸润剂,利用偶联剂在纤维表面接枝高分子成膜剂,对纤维进行表面改性,提高纤维的集束性,润滑性,耐磨擦性等性能(参见:姜雪,玄武岩连续纤维专用浸润剂的研究,哈尔滨工业大学硕士论文,2009)。对以上三种方法进行比较,涂层改性技术使用方便,操作简单,适合于连续纤维生产,对纤维表面改性效果好,可控性强。氧化铝连续纤维与玻璃连续纤维、玄武岩连续纤维等无机纤维相比,由于化学成分组成不同,采用的工艺不同导致纤维直径、强度和表面状态与性质不同。如玻璃纤维是以玻璃球或废旧玻璃为原料经高温熔制、拉丝、络纱、织布等工艺制造成的,玻纤直径一般小于23μm,拉伸强度为2300~4300mpa。玄武岩纤维是由二氧化硅、氧化铝、氧化钙、氧化镁、氧化铁和二氧化钛等氧化物组成的玄武岩石料在高温熔融后,通过漏板快速拉制而成的,单丝直径一般小于9μm,强度与高强度s玻璃纤维相当,而氧化铝连续纤维以al2o3为主要成分,同时还添加fe2o3、sio2通过溶胶凝胶结合干法纺丝技术制备而成,直径小于10μm,拉伸强度为1500~2500mpa。氧化铝连续纤维与玻璃连续纤维及玄武岩连续纤维相比纤维直径不同导致不同纤维表面的比表面积不同;化学成分不同导致不同纤维对不同的浸润剂成分的接触角,表面张力,表面能不同从而导致不同纤维对不同成分浸润剂的浸润性能不同;玻璃连续纤维和玄武岩连续纤维都是采用熔融纺制造工艺拉制而成,不同的是氧化铝连续纤维还要经过高温煅烧过程,这就导致氧化铝连续纤维生产过程更为复杂,对于纤维丝束的保护要求更高,对浸润剂要求也更高。专利文件cn106587659a所述浸润剂适用于格子梁制造的玻璃纤维浸润剂;专利文件cn106242320a所述浸润剂适用于玻璃纤维织造用浸润剂;专利文件cn106277847a所述浸润剂适用于玻璃纤维高速喷射及揉捻用浸润剂;专利文件cn103936302a所述浸润剂适用于玄武岩纤维合股无捻粗砂;专利文件cn102898044a所述浸润剂适用于玄武岩纤维拉丝作业用浸润剂。可见不同专利文件中所述的玻璃纤维和玄武岩纤维所用的浸润剂配方都不同,说明不同的无机类连续纤维,不同用途的纤维都有专门的浸润剂配方与之配合,并不能通用。目前,关于氧化铝连续纤维浸润剂未见报道,将其他纤维浸润剂用于浸润氧化铝连续纤维效果较差,为此,提出本发明。技术实现要素:针对现有技术的不足,本发明提供一种氧化铝连续纤维加捻纱专用浸润剂及其制备方法,该浸润剂能够赋予氧化铝连续纤维一定的集束性,抗静电性,润滑性,耐磨性,目的解决氧化铝连续纤维在加捻过程中产生的静电问题、纤维丝束发生断裂以及纤维不成束问题,提高其在后加工过程中的适用性,同时减少氧化铝连续纤维力学性能在加工过程中的损失。本发明的浸润剂采用一定重量百分比的水性环氧乳液成膜剂、润滑剂、有机硅烷偶联剂、ph值调节剂和水组成,使用该浸润剂在热处理过程中通过涂膜器进行氧化铝连续纤维表面涂层改性,经过烘干加捻后,可制得氧化铝连续纤维成品。本发明的技术方案如下:一种氧化铝连续纤维加捻纱专用浸润剂,按照重量百分比包括以下组分组成:3~6%水性环氧乳液、0.2~0.6%润滑剂、0.1~0.2%抗静电剂、0.3~0.8%有机硅烷偶联剂、0.02~0.05%ph值调节剂,余量为水。根据本发明,优选的,所述的水性环氧乳液为双酚a型水性环氧乳液,进一步优选为环氧当量在160~280克/当量的双酚a型水性环氧乳液;更优选为ex-305型水性环氧乳液、bh-644型水性环氧乳液或bh-653型水性环氧乳液。优选的,所述的双酚a型水性环氧乳液所含环氧树脂分子量为340~560/mol。该分子量范围内的水性环氧树脂(低、中分子量水性环氧树脂)具有强极性,其乳液烘干成膜后可以赋予氧化铝连续纤维原丝优良的集束性。根据本发明,优选的,所述的润滑剂包括润滑剂a和润滑剂b,以及包括或不包括润滑剂c;所述的润滑剂a为酰胺型阳离子型润滑剂,进一步优选牌号为3760b型润滑剂;所述的润滑剂b为脂肪族及非离子复合型润滑剂,进一步优选牌号为3550型润滑剂;所述的润滑剂c为阳离子型润滑剂,进一步优选牌号为3512型润滑剂;优选的,润滑剂a、润滑剂b和润滑剂c的质量比为1:(0.3~1):(0.3~0.8)。所述的润滑剂中可以有两种阳离子型润滑剂,起润滑作用,同时能起到抗静电作用,原理是阳离子型浸润剂可以降低摩擦系数,使氧化铝连续纤维难于产生静电。根据本发明,优选的,所述的抗静电剂为无机氯化锂。原理是无机氯化锂有强烈形成水化合物的趋势,成为带有结晶水的盐类,具有较强的吸潮性,在浸润剂膜上吸收水分的同时本身离解成离子,所以导电效果很好。根据本发明,优选的,所述的有机硅烷偶联剂为γ-氨丙基三乙氧基硅烷或γ-(甲基丙烯酰氧)丙基三甲氧基硅烷。水解后的有机硅烷偶联剂含有的三醇基硅烷中的羟基与纤维表面的羟基形成氢键。烘干过程中,羟基在高温下发生醚化反应,脱去一份水生成醚基,形成牢固的共价键。根据本发明,优选的,所述的ph值调节剂为冰醋酸。根据本发明,优选的,所述的氧化铝连续纤维加捻纱专用浸润剂,按照重量百分比包括以下组分组成:3~5%水性环氧乳液、0.2~0.6%润滑剂、0.1~0.2%抗静电剂、0.3~0.6%有机硅烷偶联剂、0.02~0.05%ph值调节剂,余量为水。根据本发明,上述氧化铝连续纤维加捻纱用浸润剂的制备方法,包括步骤如下:(1)在水中加入ph值调节剂,将水的ph值调节为3~4,再加入定量的有机硅烷偶联剂,继续搅拌至水溶液澄清后再加入ph值调节剂,将溶液的ph值调节为4~5;(2)将定量的水性环氧乳液用10~15倍的去离子水进行稀释,搅拌时间为0.5~1h;(3)将定量的润滑剂用10~20倍的去离子水进行稀释,搅拌时间为0.5~1h;(4)将定量的抗静电剂用10~20倍的去离子水进行溶解,搅拌时间为1~2h;(5)将步骤(2)、(3)、(4)中的溶液混合均匀,搅拌0.5~1h;(6)将步骤(1)中水解好的有机硅烷偶联剂及余量的水加入步骤(5)得到的混合溶液中,均匀搅拌1~2h,即得氧化铝连续纤维加捻纱专用浸润剂。本发明的制备方法中所有物料组分,包括水性环氧乳液、润滑剂、抗静电剂、有机硅烷偶联剂、ph值调节剂和水的质量百分比加和为100%。本发明的氧化铝连续纤维加捻纱用浸润剂的制备方法,步骤简单、适于工业化生产,易于推广。本发明的优点在于:1.采用本发明中的浸润剂涂覆过的氧化铝连续纤维能够有效去除纤维加捻过程中纤维丝与丝间的静电,赋予纤维优良的成束性和润滑性,同时赋予纤维良好的力学性能。2.采用本发明浸润剂制备方法简单,容易操作。3.本发明中所述氧化铝连续纤维加捻纱专用浸润剂中各成分都是水溶性的,有很好的粘结性和成膜性,并且可避免挥发性有机物的大量使用,有显著的环保特色和应用价值。附图说明图1为本发明试验例1中未经过浸润剂处理的氧化铝连续纤维照片。图2为本发明试验例1中经过浸润剂处理过的氧化铝连续纤维照片。图3为本发明试验例2中经过对比例1的浸润剂处理过的氧化铝连续纤维照片。图4为本发明试验例2中经过对比例2或对比例3的浸润剂处理过的氧化铝连续纤维照片。图5为本发明试验例2中经过对比例4的浸润剂处理过的氧化铝连续纤维照片。图6为本发明试验例2中经过对比例5的浸润剂处理过的氧化铝连续纤维形态照片。图7为本发明试验例1中经过浸润剂处理过的氧化铝连续纤维形态照片。具体实施方式下面通过具体实施例对本发明作进一步说明,但不限于此。实施例中所用原料如无特殊说明,均为常规市购产品。实施例1一种氧化铝连续纤维加捻纱专用浸润剂,按照重量百分比由以下成分组成:3.0%水性环氧树脂、0.4%有机硅烷偶联剂、0.3%润滑剂a、0.2%润滑剂b、0.1%润滑剂c、0.1%抗静电剂及0.02%ph值调节剂。本实施例中,所述的水性环氧树脂乳液为环氧当量160~180克/当量的双酚a型水性环氧乳液。牌号为ex-305型水性环氧乳液(分子量为340~360/mol),购自上海爱世博有机硅材料有限公司。所述的有机硅烷偶联剂为γ-(甲基丙烯酰氧)丙基三甲氧基硅烷,购自国药集团化学试剂有限公司。所述的润滑剂a是牌号为3760b的酰胺型阳离子型润滑剂,购自西安友基复合材料有限公司。所述的润滑剂b是牌号为3550的脂肪族及非离子复合型润滑剂,购自西安友基复合材料有限公司。所述的润滑剂c是牌号为3512的阳离子型润滑剂,购自西安友基复合材料有限公司。所述的抗静电剂是无机氯化锂。所述的ph值调节剂采用的是冰醋酸。上述氧化铝连续纤维加捻纱用浸润剂的制备方法,根据以上所述的浸润剂配比,并包括以下几个步骤:(1)在水中加入ph值调节剂,将水的ph值调节为3~4,再加入定量的有机硅烷偶联剂,继续搅拌至水溶液澄清后再加入ph值调节剂,将溶液的ph值调节为4~5;(2)将定量的水性环氧乳液用10~15倍的去离子水进行稀释,搅拌时间为0.5~1h;(3)将定量的润滑剂用10~20倍的去离子水进行稀释,搅拌时间为0.5~1h;(4)将定量的抗静电剂用10~20倍的去离子水进行溶解,搅拌时间为1~2h;(5)将步骤(2)、(3)、(4)中的溶液混合均匀,搅拌0.5~1h;(6)将步骤(1)中水解好的有机硅烷偶联剂及余量的水加入步骤(5)得到的混合溶液中,均匀搅拌1~2h,即得氧化铝连续纤维加捻纱专用浸润剂。实施例2一种氧化铝连续纤维加捻纱专用浸润剂,按照重量百分比由以下成分组成:3.5%水性环氧树脂、0.4%有机硅烷偶联剂、0.3%润滑剂a、0.3%润滑剂b、0.1%抗静电剂及0.02%ph值调节剂。本实施例中,所述的水性环氧树脂乳液为环氧当量160~180克/当量的双酚a型水性环氧乳液。牌号为ex-305型水性环氧乳液(分子量为340~360/mol),购自上海爱世博有机硅材料有限公司。所述的有机硅烷偶联剂为γ-氨丙基三乙氧基硅烷,购自国药集团化学试剂有限公司。所述的润滑剂a是牌号为3760b的酰胺型阳离子型润滑剂,购自西安友基复合材料有限公司。所述的润滑剂b是牌号为3550的脂肪族及非离子复合型润滑剂,购自西安友基复合材料有限公司。所述的抗静电剂是无机氯化锂。所述的ph值调节剂采用的是冰醋酸。上述氧化铝连续纤维加捻纱专用浸润剂的制备方法,根据以上所述的浸润剂配比,并包括以下几个步骤:(1)在水中加入ph值调节剂,将水的ph值调节为3~4,再加入定量的有机硅烷偶联剂,继续搅拌至水溶液澄清后再加入ph值调节剂,将溶液的ph值调节为4~5;(2)将定量的水性环氧乳液用10~15倍的去离子水进行稀释,搅拌时间为0.5~1h;(3)将定量的润滑剂用10~20倍的去离子水进行稀释,搅拌时间为0.5~1h;(4)将定量的抗静电剂用10~20倍的去离子水进行溶解,搅拌时间为1~2h;(5)将步骤(2)、(3)、(4)中的溶液混合均匀,搅拌0.5~1h;(6)将步骤(1)中水解好的有机硅烷偶联剂及余量的水加入步骤(5)得到的混合溶液中,均匀搅拌1~2h,即得氧化铝连续纤维加捻纱专用浸润剂。实施例3一种氧化铝连续纤维加捻纱专用浸润剂,按照重量百分比由以下成分组成:4.5%水性环氧树脂、0.4%有机硅烷偶联剂、0.3%润滑剂a、0.25%润滑剂b、0.1%润滑剂c、0.1%抗静电剂及0.02%ph值调节剂。本实施例中,所述的水性环氧树脂乳液为环氧当量160~180克/当量的双酚a型水性环氧乳液。牌号为ex-305型水性环氧乳液(分子量为340~360/mol),购自上海爱世博有机硅材料有限公司。所述的有机硅烷偶联剂为γ-(甲基丙烯酰氧)丙基三甲氧基硅烷,购自国药集团化学试剂有限公司。所述的润滑剂a是牌号为3760b的酰胺型阳离子型润滑剂,购自西安友基复合材料有限公司。所述的润滑剂b是牌号为3550的脂肪族及非离子复合型润滑剂,购自西安友基复合材料有限公司。所述的润滑剂c是牌号为3512的阳离子型润滑剂,购自西安友基复合材料有限公司。所述的抗静电剂是无机氯化锂。所述的ph值调节剂采用的是冰醋酸。上述氧化铝连续纤维加捻纱专用浸润剂的制备方法,根据以上所述的浸润剂配比,并包括以下几个步骤:(1)在水中加入ph值调节剂,将水的ph值调节为3~4,再加入定量的有机硅烷偶联剂,继续搅拌至水溶液澄清后再加入ph值调节剂,将溶液的ph值调节为4~5;(2)将定量的水性环氧乳液用10~15倍的去离子水进行稀释,搅拌时间为0.5~1h;(3)将定量的润滑剂用10~20倍的去离子水进行稀释,搅拌时间为0.5~1h;(4)将定量的抗静电剂用10~20倍的去离子水进行溶解,搅拌时间为1~2h;(5)将步骤(2)、(3)、(4)中的溶液混合均匀,搅拌0.5~1h;(6)将步骤(1)中水解好的有机硅烷偶联剂及余量的水加入步骤(5)得到的混合溶液中,均匀搅拌1~2h,即得氧化铝连续纤维加捻纱专用浸润剂。实施例4上述氧化铝连续纤维加捻纱专用浸润剂,按照重量百分比由以下成分组成:4.0%水性环氧树脂、0.4%有机硅烷偶联剂、0.3%润滑剂a、0.2%润滑剂b、0.1%润滑剂c、0.1%抗静电剂及0.02%ph值调节剂。本实施例中,所述的水性环氧树脂乳液为环氧当量180~230克/当量的双酚a型水性环氧乳液。牌号为bh-653型水性环氧乳液(分子量为360~460/mol),购自东莞广通化工制品有限公司。所述的有机硅烷偶联剂为γ-(甲基丙烯酰氧)丙基三甲氧基硅烷,购自国药集团化学试剂有限公司。所述的润滑剂a是牌号为3760b的酰胺型阳离子型润滑剂,购自西安友基复合材料有限公司。所述的润滑剂b是牌号为3550的脂肪族及非离子复合型润滑剂,购自西安友基复合材料有限公司。所述的润滑剂c是牌号为3512的阳离子型润滑剂,购自西安友基复合材料有限公司。所述的抗静电剂是无机氯化锂。所述的ph值调节剂采用的是冰醋酸。实施例5一种氧化铝连续纤维加捻纱用浸润剂,按照重量百分比由以下几组分组成:4.5%水性环氧树脂、0.4%有机硅烷偶联剂、0.3%润滑剂a、0.3%润滑剂b、0.1%抗静电剂及0.02%ph值调节剂。本实施例中,所述的水性环氧树脂乳液为环氧当量180~230克/当量的双酚a型水性环氧乳液。bh-653型水性环氧乳液(环氧当量为360~460克/当量),购自东莞广通化工制品有限公司。所述的有机硅烷偶联剂为γ-氨丙基三乙氧基硅烷,购自国药集团化学试剂有限公司。所述的润滑剂a是牌号为3760b的酰胺型阳离子型润滑剂,购自西安友基复合材料有限公司。所述的润滑剂b是牌号为3512的阳离子型润滑剂,购自西安友基复合材料有限公司。所述的抗静电剂是无机氯化锂。所述的ph值调节剂采用的是冰醋酸。制备方法同实施例1。对比例1如实施例1所述,不同的是:所述的润滑剂中仅使用0.6%的润滑剂a。对比例2如实施例1所述,不同的是:所述的润滑剂中仅使用0.6%的润滑剂b。对比例3如实施例1所述,不同的是:所述的润滑剂中仅使用0.3%的润滑剂b和0.3%的润滑剂c。对比例4使用专利文件cn106242320a所述适用于玻璃纤维织造用浸润剂作对比。对比例5使用专利文件cn106587659a所述适用于格子梁制造的玻璃纤维浸润剂作对比。试验例1应用本发明实施例1的浸润剂涂覆过的氧化铝连续纤维形态如图2所示,与未涂覆浸润剂的纤维原丝形态如图1所示,作对比。从图1可看出未经过浸润剂处理的氧化铝连续纤维丝与丝间由于存在静电而不成束,再加上纤维本身柔韧性不好,表面不润滑,纤维没有得到很好地保护造成纤维断裂和产生毛羽,这样的纤维是无法进行加捻生产,同时影响纤维后续加工使用;相对比图2可以看出经过浸润剂处理的纤维几百根纤维丝成一束,表面光滑无毛羽,也不容易断裂,有利于加捻生产及后续加工使用。试验例2应用对比例1的浸润剂涂覆过的氧化铝连续纤维形态如图3所示,与本发明实施例1的浸润剂涂覆过的氧化铝连续纤维形态如图2所示,作对比。从图3可看出,浸润剂中润滑剂成分仅使用润滑剂a处理过的氧化铝连续纤维硬挺度偏大,表面不太光滑,这样的纤维不太适用于现有的加捻生产工艺,纤维容易在加捻过程中折断或出现断丝现象。应用对比例2或对比例3的浸润剂涂覆过的氧化铝连续纤维形态如图4所示,与本发明实施例1的浸润剂涂覆过的氧化铝连续纤维形态如图2所示,作对比。从图4可看出,浸润剂中润滑剂成分仅使用润滑剂b或者润滑剂b、c混合使用,处理过的氧化铝连续纤维过于柔软,且可以看出纤维集束性效果不是很好,影响整束纤维的技术性能,这样的纤维不太适用于现有的加捻生产工艺,纤维容易在加捻过程中滑落或出现断丝现象。应用对比例4和对比例5的浸润剂涂覆过的氧化铝连续纤维形态如图5、图6所示,与本发明实施例1的浸润剂涂覆过的氧化铝连续纤维形态如图2、图7所示,作对比。从图5可看出,使用专利文件cn106242320a所述适用于玻璃纤维织造用浸润剂或使用专利文件cn106587659a所述适用于格子梁制造的玻璃纤维浸润剂,处理过的氧化铝连续纤维涂覆量过大或某些成分不适合氧化铝连续纤维,使纤维涂覆烘干后变弯曲,而且集束过度,使纤维经过涂膜器将纤维丝束压扁烘干后却无法恢复原形,且将纤维丝束粘到一起无法完整抽出单丝(如图6和图7相比,图7所示的氧化铝连续纤维整束可以集成一束,也可以分开单丝,而图6所示纤维整束集束过度,无法分开单丝),且纤维硬挺度过大,一折就断,影响整束纤维的技术性能,这样的纤维是无法使用的。试验例3应用本发明实施例1-5和对比例1-5的浸润剂涂覆氧化铝连续纤维进行测试,结果如表1所示。表1.氧化铝连续纤维涂浸润剂与未涂浸润剂测试结果测试项目涂覆率(%)硬挺度(cm)整束纤维拉伸断裂强力(n/tex)加捻效果纤维原丝0.001.70.371实施例11.182.00.386优实施例21.542.00.415优实施例31.712.050.402优实施例41.852.10.426优实施例51.792.20.425优对比例11.202.50.389良对比例21.191.80.375良对比例31.231.850.373良对比例42.694.60.392差对比例52.565.20.395差从表1中可以看出,经过本发明浸润剂处理后的的氧化铝连续纤维比没有经过浸润剂处理的纤维硬挺度稍有提高且在适合加捻要求的硬挺度范围内,整束纤维拉伸断裂强力有很大提高,说明经过浸润剂处理对氧化铝连续纤维起到集束保护作用,从硬挺度、润滑性、整束纤维拉伸断裂强力等方面都符合纤维加捻工艺,且加捻效果极佳。将本发明实施例与对比例结合数据进行对比,可以看出浸润剂中润滑剂成分仅使用润滑剂a,经涂覆后氧化铝连续纤维虽然整束纤维拉伸断裂强力有所提高,但是纤维硬挺度稍大,且润滑效果不佳,不适用于现有的加捻工艺,仅使用润滑剂b或者润滑剂b、c混合使用,经涂覆后氧化铝连续纤维整束纤维拉伸断裂强力没有明显提高,且纤维硬挺度过小,润滑稍微过度,连续纤维加捻时容易滑落,也不适用于现有的加捻工艺,必须是几种润滑剂复配使用才能从硬挺度、润滑性、整束纤维拉伸断裂强力等方面很好的达到加捻工艺要求,而使用专利文件cn106242320a所述适用于玻璃纤维织造用浸润剂或使用专利文件cn106587659a所述适用于格子梁制造的玻璃纤维浸润剂,虽然涂覆后整束纤维拉伸断裂强力有所提高,但是涂覆量过大,会导致纤维在使用时经过高温处理后被游离的碳离子损伤严重,影响纤维的整体使用性能,且纤维集束过度,把纤维丝束粘到一起无法分开单丝导致氧化铝连续纤维无法正常使用,且涂覆后纤维硬挺度过大使纤维更不耐折,润滑效果不佳,不适用于现有的加捻工艺且无法生产出合格的氧化铝连续纤维。当前第1页12