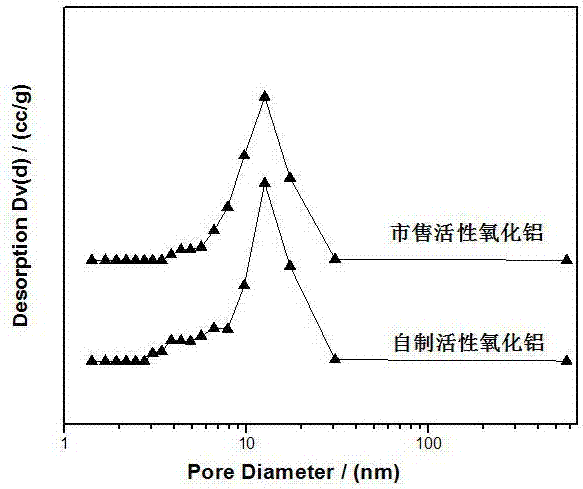
本发明属于化学领域,具体为一种利用废弃蒽醌再生剂制备活性氧化铝的方法。
背景技术:
:活性氧化铝是一种性能优良、结构稳定的两性金属氧化物,具有较大的比表面积、特殊的孔结构、优良的吸附性、较高的热稳定性和机械强度等特点,在很多催化领域有广泛的应用。且活性氧化铝具有结构稳定、不易潮解、抗腐蚀性强及机械强度高等诸多优点,因此活性氧化铝被广泛运用于催化剂、催化剂载体、吸附剂及干燥剂等多方面工业应用。过氧化氢,其水溶液俗称双氧水,是一种强氧化剂,广泛应用在漂白剂、发色剂、无机或有机过氧化物的原料、氧化剂、杀菌剂、消毒剂、防腐剂、电镀液、火箭动力燃料等领域。过氧化氢的工业生产方法主要是蒽醌法,其工艺为烷基蒽醌溶解于有机混合溶剂中配成蒽醌工作液。首先在加氢催化剂及在加压条件下与氢气反应氢化为烷基氢蒽醌,然后与纯o2或空气的反应,烷基氢蒽醌再转化成烷基蒽醌,同时得到过氧化氢。经萃取、精制与浓缩制得质量分数为20%-50%的双氧水产品。但烷基蒽醌在上述氢化阶段和氧化阶段中会生成一些副产物,这些副产物在反应中已失去生产能力,统称为蒽醌降解物。蒽醌降解物的产生不但会降低系统内烷基蒽醌的浓度,影响工业生产效率,而且还会降低双氧水产品质量,严重妨碍了工业生产的正常运转。目前蒽醌法制备过氧化氢工业上普遍使用大量的蒽醌再生剂进行再生,这种再生剂是由活性氧化铝球负载低浓度的碱性金属氧化物构成。但这种再生剂长时间与蒽醌降解物接触后,再生活性下降明显,常出现膨胀开裂及结块现象,使用寿命一般为两个月左右。一个小型的5万t的过氧化氢企业每年可消耗蒽醌再生剂2000~2500t,而废弃的蒽醌再生剂中吸附了大量的重芳烃及蒽酚酮等降解物很难处理,现阶段的处理方式主要是对其高温焙烧来生产瓷砖,但这种方式会产生大量有害的有毒气体,对大气造成极大的污染。因此如何回收利用工厂废弃的蒽醌再生剂具有十分重要的意义。现有的回收技术一般只是对工厂失活的蒽醌再生剂进行清洗,增加碱量后焙烧,但以此方法回收利用的氧化铝再生剂活性降低、使用寿命较短、粉尘及磨耗率增多。中国专利cn103879969a提出活性氧化铝再生处理方法:向废弃再生剂中加入稀酸溶液,混合均匀,制成条状;在室温下阴干后,于600~900k温度下焙烧3~5h得到条状载体;将条状载体经该氢氧化钠溶液浸渍后,取出,干燥后,即得新的蒽醌再生催化剂。但该方法得到的条形再生剂的再生活性与使用寿命还有待验证,条形再生剂因其流动性差也很难被双氧水厂家接受,极大的限制了该发明的应用。技术实现要素:本发明针对上述问题提供一种用水热法制备利用废弃蒽醌再生剂制备活性氧化铝的方法的方法。为达到上述目的,本发明的技术方案如下:本发明的利用废弃蒽醌再生剂制备活性氧化铝的方法,包括以下步骤:a、将废弃的蒽醌再生剂研磨成50~3000目的细粉,然后加入相当于废弃蒽醌再生剂细粉总重量20~50%的重芳烃,混合均匀浸泡1~2后进行固液分离,向滤渣中加入相当于废弃蒽醌再生剂细粉总重量的1~400%的去离子水,充分搅拌后加入到密闭容器中,在加压条件下,加热至80-200℃,继续反应0-72小时后取出,进行固液分离,得滤渣;所述的蒽醌再生剂为活性氧化铝球负载氢氧化钠;b、向步骤a得到的滤渣中加入相当于废弃蒽醌再生剂细粉总重量的1~100%的酸液,混合均匀,反应0.1~72h后,用水洗涤后,得到氧化铝粗品;c、在氧化铝粗品中加入相当于废弃蒽醌再生剂细粉总重量的1~50%的结构稳定剂和1~200%的助挤剂,混合均匀,然后挤压成型;d、在室温下阴干后,于600~1100k温度下焙烧2~5h,即得活性氧化铝载体。进一步,所述的步骤a中去离子水的加入量为相当于废弃蒽醌再生剂细粉总重量的10-200%。进一步,所述的步骤a中的细粉为50~3000目的粉末。进一步,所述的步骤a中,所述的加压条件为控制在10个大气压以内。进一步,所述的步骤b中酸液的加入量为相当于废弃蒽醌再生剂细粉总重量的60-100%。进一步,所述的步骤b中,酸液为硝酸、硫酸、盐酸的一种或两种以上的混合。进一步,所述的步骤c中,结构稳定剂为磷酸、硝酸锆、硅酸钠中的一种或两种以上的混合,结构稳定剂的用量为相当于废弃蒽醌再生剂细粉总重量的1~10%。。进一步,所述的步骤c中,助挤剂为硝酸、冰醋酸、柠檬酸、田菁粉、活性炭中的一种或两种以上与去离子水的混合,助挤剂的用量为相当于废弃蒽醌再生剂细粉总重量的1~10%。进一步,所述的步骤c中,挤压成型可将活性氧化铝载体挤压成球形、条形、柱状、三叶草、蜂窝状、片状、类球形或多叶草状。进一步,所述的步骤d中,活性氧化铝载体的晶型为γ型,比表面积为150~300m2·g-1,孔容为0.5~1.5cm3·g-1,粒径为1~10mm。进一步,所述的重芳烃为c9~c12的重芳烃。本发明的有益效果为:1、本发明加入重芳烃作为清洗剂,能够将废弃的蒽醌再生剂表面附着的大部分蒽醌工作液清洗干净,分离出来,便于去离子水进入再生剂内部,为后续充分反应打下良好基础。同时,重芳烃留存于蒽醌再生剂上,与残留在蒽醌再生剂上的蒽醌工作液相互交溶,减小蒽醌再生剂对蒽醌工作液的吸附,在后续的热压反应中,配合去离子水与蒽醌再生剂反应生成薄水铝石,能够在最大程度上实现蒽醌工作液的脱附;2、本发明喷洒去离子水,在加热加压的条件下生成薄水铝石,导致孔结构坍塌,比表面积和孔容都会急剧减少,这是保证蒽醌工作液良好脱附的重要步骤;3、本发明步骤b中进行酸液反应洗涤,一方面能够进一步清洗干净蒽醌再生剂,另一方面实现薄水铝石转变,重新获得活性氧化铝;4、本发明还加入结构稳定剂和助挤剂,使得到的活性氧化铝水热稳定性更好,晶型结构稳定,挤压制成的氧化铝载体更为稳固;5、本发明制备的活性氧化铝具有优良的性能,各项指标与在售的活性氧化铝相当,可应用于催化剂载体、吸附剂及干燥剂等多方面工业用途;制备工艺简单科学合理,原料来源广泛,属变废为宝技术,能减轻过氧化氢企业环保压力,这为新技术的推广提供了广阔的发展空间。附图说明图1为实施例5活性氧化铝及市售的活性氧化铝的吸附-脱附等温线;图2为活性氧化铝孔径分布图;由图1可知,按照iupac分类规则,两个氧化铝的吸脱附曲线近似于iv型,而且吸附和脱附存在滞后现象,在p/p0为0.8-1.0范围内存在一个h2型滞后环,这是由于毛细管凝聚作用造成的,说明样品中有丰富的介孔结构,发生毛细作用的压力较高表明介孔的孔径较大;迟滞环很陡,并且直立部分几乎平行,表明孔道有序性好;通过bjh法计算得到的实施例5活性氧化铝及市售的活性氧化铝的孔径分布曲线如图2所示,可以看出,实施例5活性氧化铝的孔径分布情况与市售的活性氧化铝相差不大,能满足性能要求。具体实施方式下面通过具体实施例对本发明进行详细说明。实施例1本发明的利用废弃蒽醌再生剂制备活性氧化铝的方法,包括以下步骤:a、将1000g废弃的蒽醌再生剂研磨成1000目的细粉,然后加入200gc9~c12重芳烃,混合均匀浸泡1h后进行固液分离,向滤渣中加入2000g去离子水,充分搅拌后加入到密闭容器中,在2个大气压力下,加热至120℃,继续反应2小时后取出,进行固液分离,得滤渣;所述的蒽醌再生剂为活性氧化铝球负载氢氧化钠;b、向步骤a得到的滤渣中加入300g硝酸、250g硫酸的混合酸液,混合均匀,反应3h后,用去离子水洗涤,得到氧化铝粗品;c、在氧化铝粗品中加入50g磷酸、30g硝酸锆、20g柠檬酸、30g田菁粉、15g活性炭及450g去离子水,挤压成条形;d、在室温下阴干后,于700k温度下焙烧3h,即得γ型活性氧化铝载体,比表面积为227.4m2·g-1,孔容为0.67cm3·g-1,粒径为4mm,条形的长度为3-5cm。实施例2本发明的利用废弃蒽醌再生剂制备活性氧化铝的方法,包括以下步骤:a、将800g废弃的蒽醌再生剂研磨成400目的细粉,加入400gc9~c12重芳烃,混合均匀浸泡1.2h后进行固液分离,向滤渣中加入1000g去离子水,充分搅拌后加入到密闭容器中,在3个大气压力下,加热至150℃,继续反应3小时后取出,进行固液分离,得滤渣;所述的蒽醌再生剂为活性氧化铝球负载氢氧化钠;b、向步骤a得到的滤渣中加入为350g硝酸、200g盐酸的混合酸液,混合均匀,反应3h后,用去离子水洗涤,得到氧化铝粗品;c、在氧化铝粗品中加入50g磷酸、50g硝酸锆、25g硝酸、20g冰醋酸、25g田菁粉、25g活性炭及400g去离子水、,挤压成类球形;d、在室温下阴干后,于750k温度下焙烧2.5h,即得γ型活性氧化铝载体,比表面积为231.7m2·g-1,孔容为0.58cm3·g-1,粒径为4mm。实施例3本发明的利用废弃蒽醌再生剂制备活性氧化铝的方法,包括以下步骤:a、将900g废弃的蒽醌再生剂研磨成800目的细粉,加入270gc9~c12重芳烃,混合均匀浸泡1.4h后进行固液分离,向滤渣中加入1200g去离子水,充分搅拌后加入到密闭容器中,在3个大气压力下,加热至150℃,继续反应4小时后取出,进行固液分离,得滤渣;所述的蒽醌再生剂为活性氧化铝球负载氢氧化钠;b、向步骤a得到的滤渣中加入650g硫酸,混合均匀,反应4h后,用去离子水洗涤,得到氧化铝粗品;c、在氧化铝粗品中加入50g磷酸、50g硝酸锆、20g硅酸钠、35g硝酸、10g冰醋酸、35g田菁粉、30g活性炭及450g去离子水,挤压成柱状;d、在室温下阴干后,于1073k温度下焙烧2h,即得γ型活性氧化铝载体,比表面积为242.1m2·g-1,孔容为0.65cm3·g-1,粒径为4mm。实施例4本发明的利用废弃蒽醌再生剂制备活性氧化铝的方法,包括以下步骤:a、将950g废弃的蒽醌再生剂研磨成1200目的细粉,加入380gc9~c12重芳烃,混合均匀浸泡1.6h后进行固液分离,向滤渣中加入1900g去离子水,充分搅拌后加入到密闭容器中,在4个大气压力下,加热至180℃,继续反应5小时后取出,进行固液分离,得滤渣;所述的蒽醌再生剂为活性氧化铝球负载氢氧化钠;b、向步骤a得到的滤渣中加入250g硝酸、160g硫酸、180g盐酸的混合酸液,混合均匀,反应2h后,用去离子水洗涤,得到氧化铝粗品;c、在氧化铝粗品中加入165g硝酸锆、50g硝酸、45g田菁粉及550g去离子水,挤压成蜂窝状;d、在室温下阴干后,于923k温度下焙烧3h,即得γ型活性氧化铝载体,比表面积为252.8m2·g-1,孔容为0.68cm3·g-1,粒径为4mm。实施例5本发明的利用废弃蒽醌再生剂制备活性氧化铝的方法,包括以下步骤:a、将1500g废弃的蒽醌再生剂研磨成2000目的细粉,加入375gc9~c12重芳烃,混合均匀浸泡1.8h后进行固液分离,向滤渣中加入2000g去离子水,充分搅拌后加入到密闭容器中,在4个大气压力下,加热至160℃,继续反应4小时后取出,进行固液分离,得滤渣;所述的蒽醌再生剂为活性氧化铝球负载氢氧化钠;b、向步骤a得到的滤渣中加入850g硝酸、80g盐酸,混合均匀,反应4h后,用去离子水洗涤,得到氧化铝粗品;c、在氧化铝粗品中加入80g硝酸锆、50g硅酸钠、60g硝酸、18g柠檬酸、25g田菁粉及700g去离子水,挤压成三叶草状;d、在室温下阴干后,于723k温度下焙烧4h,即得γ型活性氧化铝载体,比表面积为238.6m2·g-1,孔容为0.65cm3·g-1,粒径为3mm。实施例6本发明的利用废弃蒽醌再生剂制备活性氧化铝的方法,包括以下步骤:a、将1200g废弃的蒽醌再生剂研磨成1800目的细粉,加入600gc9~c12重芳烃,混合均匀浸泡2h后进行固液分离,向滤渣中加入1200g去离子水,充分搅拌后加入到密闭容器中,在3个大气压力下,加热至140℃,继续反应8小时后取出,进行固液分离,得滤渣;所述的蒽醌再生剂为活性氧化铝球负载氢氧化钠;b、向步骤a得到的滤渣中加入950g盐酸,混合均匀,反应3h后,用去离子水洗涤,得到氧化铝粗品;c、在氧化铝粗品中加入150g硅酸钠、100g冰醋酸、10g柠檬酸、40g田菁粉及600g去离子水,挤压成多叶草状;d、在室温下阴干后,于983k温度下焙烧3h,即得γ型活性氧化铝载体,比表面积为221.7m2·g-1,孔容为0.63cm3·g-1,粒径为4mm。实施例7本发明的利用废弃蒽醌再生剂制备活性氧化铝的方法,包括以下步骤:a、将1300g废弃的蒽醌再生剂研磨成1100目的细粉,加入585gc9~c12重芳烃,混合均匀浸泡1.7h后进行固液分离,向滤渣中加入3200g去离子水,充分搅拌后加入到密闭容器中,在5个大气压力下,加热至110℃,继续反应12小时后取出,进行固液分离,得滤渣;所述的蒽醌再生剂为活性氧化铝球负载氢氧化钠;b、向步骤a得到的滤渣中加入460g硫酸、680g盐酸的混合酸液,混合均匀,反应4h后,用去离子水洗涤,得到氧化铝粗品;c、在氧化铝粗品中加入150g磷酸、130g硅酸钠、400g冰醋酸、50g田菁粉及500g去离子水,挤压成球形;d、在室温下阴干后,于900k温度下焙烧2h,即得γ型活性氧化铝载体,比表面积为240.9m2·g-1,孔容为0.56cm3·g-1,粒径为3mm。实施例8本发明的利用废弃蒽醌再生剂制备活性氧化铝的方法,包括以下步骤:a、将2000g废弃的再生剂研磨成300目的细粉,加入再660gc9~c12重芳烃,混合均匀浸泡1.9h后进行固液分离,向滤渣中加入4000g去离子水,充分搅拌后加入到密闭容器中,在3.5个大气压力下,加热至190℃,继续反应10小时后取出,进行固液分离,得滤渣;所述的蒽醌再生剂为活性氧化铝球负载氢氧化钠;b、向步骤a得到的滤渣中加入700g硝酸、380g硫酸的混合酸液,混合均匀,反应18h后,用去离子水洗涤,得到氧化铝粗品;c、在氧化铝粗品中加入650g磷酸、200g冰醋酸、360g柠檬酸、80g田菁粉及700g去离子水,挤压成三叶草状;d、在室温下阴干后,于673k温度下焙烧5h,即得γ型活性氧化铝载体,比表面积为230.2m2·g-1,孔容为0.59cm3·g-1,粒径为3mm。实施例9本发明的利用废弃蒽醌再生剂制备活性氧化铝的方法,包括以下步骤:a、将1000g废弃的蒽醌再生剂研磨成50目的细粉,加入440gc9~c12重芳烃,混合均匀浸泡2h后进行固液分离,向滤渣中加入1000g去离子水,充分搅拌后加入到密闭容器中,在1个大气压力下,加热至80℃后,进行固液分离,得滤渣;所述的蒽醌再生剂为活性氧化铝球负载氢氧化钠;b、向步骤a得到的滤渣中加入10g盐酸,混合均匀,反应0.1h后,用去离子水洗涤,得到氧化铝粗品;c、在氧化铝粗品中加入10g磷酸、5g活性炭及5g去离子水,挤压成片状;d、在室温下阴干后,于600k温度下焙烧3h,即得γ型活性氧化铝载体,比表面积为235.3m2·g-1,孔容为0.61cm3·g-1,粒径为3mm。实施例10本发明的利用废弃蒽醌再生剂制备活性氧化铝的方法,包括以下步骤:a、将1000废弃的蒽醌再生剂研磨成3000目的细粉,加入500g重芳烃,混合均匀浸泡1.5h后进行固液分离,向滤渣中加入4000g去离子水,充分搅拌后加入到密闭容器中,在10个大气压力下,加热至200℃,继续反应72小时后取出,进行固液分离,得滤渣;所述的蒽醌再生剂为活性氧化铝球负载氢氧化钠;b、向步骤a得到的滤渣中加入500g硝酸、200g硫酸、300g盐酸的混合酸液,混合均匀,反应72h后,用去离子水洗涤,得到氧化铝粗品;c、在氧化铝粗品中加入400g磷酸、100g硅酸钠、100g硝酸、500g柠檬酸、500g活性炭及900的去离子水,挤压成条形;d、在室温下阴干后,于1100k温度下焙烧5h,即得γ型活性氧化铝载体,比表面积为248.2m2·g-1,孔容为0.63cm3·g-1,粒径为4mm,条形的长度为3cm。实施例11将实施例5制备的三叶草形貌活性氧化铝与在售三叶草形貌活性氧化铝进行对比试验分析,具体过程如下:1实验过程1.1实验原料废弃蒽醌再生剂:工业品,广西柳州化学工业集团有限公司;硝酸:分析纯,国药集团化学有限公司;盐酸:分析纯,国药集团化学有限公司;柠檬酸:分析纯,国药集团化学有限公司;田菁粉:工业品,河南省高丝宝商贸公司;市售活性氧化铝,工业品,淄博恒环铝业有限公司;实施例5制备的三叶草形貌活性氧化铝。1.2活性氧化铝理化性能分析采用美国micromeritics公司tristarii3020型比表面-孔径分布测定仪测定样品的比表面、孔体积及孔径分布等孔结构数据,根据bet方程和bjh模型计算样品比表面数值和孔径分布;采用yhkc-2a型压碎强度测定仪测定压碎强度,随机取50粒测定后取平均值;采用日本岛津xrd-6000型x射线粉末衍射仪(xrd)测定样品的晶体结构。2结果与讨论2.1活性氧化铝理化性能检测再生剂的物理性能检测包括晶型、外观、堆密度、抗压碎强度、吸水率、磨耗率、粉尘、等指标的检测,具体检测结果如表1所示:表1再生剂的物理性能检测检测项目市售的活性氧化铝实施例5活性氧化铝晶型γγ外观(直径/mm)直径3三叶草直径3三叶草堆密度/g.ml-10.610.59抗压碎强度/n54.853.1比表面积/m2.g-1221.5238.6孔容/cm3·g-10.620.65吸水率/%54.155.3磨耗率/%0.130.12粉尘/%0.200.15由表1可知,实施例5制备的活性氧化铝的各项理化性能与现阶段市售的活性氧化铝相差不大,在关键性能比表面积上,实施例5的性能明显优于在售的活性氧化铝,可应用于催化剂载体、吸附剂及干燥剂等多方面工业用途,达到工业应用标准。当前第1页12