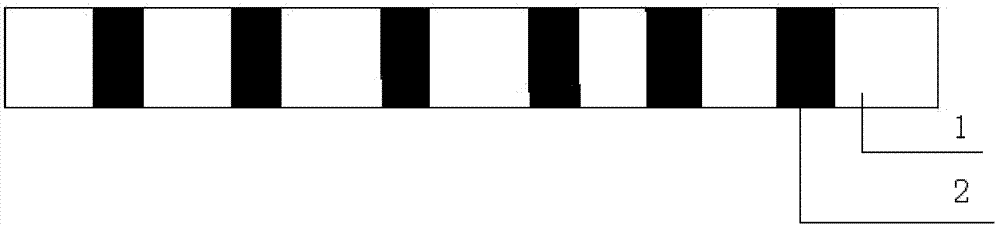
本发明属于建筑材料技术领域,涉及一种芯板及其制造方法和用途。
背景技术:现有技术中的中空芯板主要有:一是高分子发泡中空芯板,其主要缺陷是受力性能很差;二是蜂窝状中空芯板,主要缺陷是耐水性能差、受力性能差,实用性不强。且两种中空芯板一般都只具有隔热、保温、隔音、质轻等基本性能。
技术实现要素:本发明的目的在于针对现有技术的缺陷,提供一种芯板及其制备方法和用途。该方法简单合理,所生产的芯板除了具有隔热、保温、隔音、质轻等基本性能外,还能根据选用聚合物的不同赋予其更多性能。为实现上述目的,本发明采用以下技术方案:一种芯板,由包含以下重量份的组分制成:聚合物100份,助剂20-80份。所述的聚合物选自聚丙烯、聚酰胺、聚乙烯、聚酯、聚苯乙烯、聚甲基丙烯酸甲酯、丙烯腈-苯乙烯-丁二烯共聚物或乙烯/乙烯醇共聚物中的一种或一种以上。所述的助剂选自稀释剂或成孔剂中的一种或一种以上。所述的稀释剂选自石蜡、豆油或二苯醚中的一种或一种以上。所述的成孔剂选自球形活性炭、碳酸钙或人造石墨中的一种或一种以上。一种上述芯板的制备方法,包含步骤如下:(1)首先按上述比例称取聚合物和助剂,将上述原料混合均匀;(2)然后将上述溶液直接涂覆在模板上得到平板膜,经降温冷却,可将平板膜浸入冷却液中冷却,体系发生液-液或是固-液相分离,得到聚合物固化膜;(3)最后将步骤(2)中制得的聚合物固化膜中的助剂除去,使得所制膜表面产生微孔,即得到一种具有微孔结构的夹芯板材的芯板材料。所述的步骤(2)中溶液的涂覆厚度为1-10mm。所述的芯板为任意形状,优选为规则图形,如有实际需要,可将规则图形裁至需要图形。所述的微孔的尺寸为0.1-15μm。所述的芯板的孔隙率为20-80%。所述的芯板的厚度为1-10mm。所述的步骤(2)中的冷却液选自水、乙烷、乙醇、乙二醇或丙二醇。所述的步骤(3)中通过蒸发或萃取除去聚合物固化膜中的助剂,其中萃取剂选自醇、卤代烯烃或卤代烷烃,优选甲醇、甲苯或四氯化碳。所述的醇、卤代烯烃或卤代烷烃是根据助剂的类别来选用的,选用的原则是:①和原溶液中的溶剂互不相溶;②对溶质的溶解度要远大于原溶剂;③易于挥发;④萃取剂不能与原溶液的溶剂反应。芯板表面孔隙率高低可以通过添加或减少稀释剂或成孔剂的用量以及冷却降温的过程来调整;芯板厚度可以在涂膜时控制,如果涂膜时的厚度影响了膜表面的微孔尺寸或孔隙率,可以通过多层聚合物固化膜相互叠加成型的工艺来满足实际需要的厚度。所述的多层聚合物固化膜的相互叠加成型工艺可以通过胶粘的方法来完成。可以是叠前涂胶,也可以是叠后涂胶;可以是涂胶也可以是喷胶等其他上胶方式。该叠加成型工艺可在上述步骤(3)后完成。首先是形成微孔后叠加的,第二叠加的膜就是有微孔的聚合物固化膜,胶黏剂可选择聚氨酯胶,上胶量为200g/m2。一种上述芯板作为中空夹芯板材芯板的应用。所述的应用包含以下步骤:在上述芯板的上下两面通过胶黏剂覆上金属板材或者高分子材料板材,制成中空夹芯板材。所述金属板材为铁板、铝板、铜板、不锈钢板或彩钢板等。所述高分子材料板材为聚丙烯、聚酰胺、聚乙烯、聚酯或连续纤维增强热塑性树脂板材(TPAC)。所述的胶黏剂选择两液混合硬化胶,用量200-300g/m2。本发明的优点在于:本发明采用相分离的方法制备微孔芯板,其孔径分布均匀,孔隙率高,制成的芯板形态和厚度也可以根据需要进行调整,且芯板性能可以根据实际需要选择不同的聚合物材料。用本发明方法制成的芯板制造中空板材,除了具有一般中空板材的隔热、保温、隔音、质轻等基本性能以外,还可以根据选用聚合物的不同赋予其更多性能,比如亲水性能、阻燃性能、抗菌性能、抗静电性能等。除了增加各方面性能以外,同时通过对板材的选择,还可以做成透明、半透明、亚光、色彩等多种样式,可以实现采光、美化等效果。可应用于大型工业厂房、建筑隔断墙、洁净车间、房间门、办公(或家具)用品以及需要保温隔热防火场所的板材等建筑用材。附图说明图1为聚合物固化膜的结构示意图。图2为聚合物固化膜截面的结构示意图。图3为聚合物固化膜上稀释剂或成孔剂蒸发或萃取过程的示意图。图4为聚合物固化微孔膜的结构示意图。1为聚合物,2为稀释剂或成孔剂,3为微孔。具体实施方式以下结合附图所示实施例对本发明作进一步的说明。实施例1将聚丙烯100份、石蜡70份的比例混合溶解成均相溶液,直接涂覆在模板上形成厚度为1mm平板膜,将平板膜浸入冷水中冷却,体系发生液-液相分离,形成聚合物固化膜(如图1-2所示)。采用蒸发的方法将石蜡蒸发掉,蒸发温度为35℃±1℃,使得所制膜表面产生微孔(如图3-4所示),即得到一种微孔尺寸为0.1μm,孔隙率为70%,厚度为1mm的夹芯板材的芯板材料。在上述芯板的上下两面覆上彩钢板,即可制成中空夹芯板材。制成夹芯板材选用两液混合硬化胶,用量为200g/m2。实施例2将聚酯100份、豆油60份的比例混合溶解成均相溶液,直接涂覆在模板上形成厚度为3mm平板膜,将平板膜浸入丙二醇中冷却,体系发生液-液相分离,聚合物会固化成膜。采用蒸发的方法将豆油蒸发掉,蒸发温度为22℃±1℃,使得所制膜表面产生微孔,即得到一种微孔尺寸为0.1μm,孔隙率为60%,厚度为3mm的夹芯板材的芯板材料。在上述芯板的上下两面覆上不锈钢板,即可制成中空夹芯板材。制成夹芯板材选用两液混合硬化胶,用量为220g/m2。实施例3将聚甲基丙烯酸甲脂100份、二苯醚50份的比例混合溶解成均相溶液,直接涂覆在模板上形成厚度为5mm平板膜,将平板膜浸入乙烷中冷却,体系发生液-液相分离,形成聚合物固化膜。采用萃取的方法用甲苯将二苯醚萃取掉,使得所制膜表面产生微孔,即得到一种微孔尺寸为1μm,孔隙率为50%,厚度为5mm的夹芯板材的芯板材料。在上述芯板的上下两面覆上聚丙烯板材,即可制成中空夹芯板材。制成夹芯板材选用两液混合硬化胶,用量为240g/m2。实施例4将乙烯/乙烯醇共聚物100份、球形活性炭40份的比例混合溶解成均相溶液,直接涂覆在模板上形成厚度为7mm平板膜,将平板膜浸入水中冷却,体系发生固-液相分离,形成聚合物固化膜。采用萃取的方法用甲醇将球形活性炭萃取掉,使得所制膜表面产生微孔,即得到一种微孔尺寸为10μm,孔隙率为40%,厚度为7mm的夹芯板材的芯板材料。在上述芯板的上下两面覆上聚丙烯板材,即可制成中空夹芯板材。制成夹芯板材选用两液混合硬化胶,用量为260g/m2。实施例5将聚乙烯100份、碳酸钙30份的比例混合溶解成均相溶液,直接涂覆在模板上形成厚度为10mm平板膜,将平板膜浸入水中冷却,体系发生固-液相分离,形成聚合物固化膜。采用萃取的方法用四氯化碳将碳酸钙萃取掉,使得所制膜表面产生微孔,即得到一种微孔尺寸为15μm,孔隙率为30%,
技术实现要素:已经修改完毕,厚度为10mm的夹芯板材的芯板材料。在上述芯板的上下两面覆上TPAC板材,即可制成中空夹芯板材。制成夹芯板材选用两液混合硬化胶,用量为280g/m2。实施例6将聚丙烯100份、石蜡20份的比例混合溶解成均相溶液,直接涂覆在模板上形成厚度为1mm平板膜,将平板膜浸入冷水中冷却,体系发生液-液相分离,形成聚合物固化膜。采用蒸发的方法将石蜡蒸发掉,蒸发温度为35℃±1℃,使得所制膜表面产生微孔,即得到一种微孔尺寸为0.1μm,孔隙率为20%,厚度为1mm的夹芯板材的芯板材料。在上述芯板的上下两面覆上彩钢板,即可制成中空夹芯板材。制成夹芯板材选用两液混合硬化胶,用量为300g/m2。实施例7将聚甲基丙烯酸甲脂100份、二苯醚80份的比例混合溶解成均相溶液,直接涂覆在模板上形成厚度为5mm平板膜,将平板膜浸入乙烷中冷却,体系发生液-液相分离,形成聚合物固化膜。采用萃取的方法用甲苯将二苯醚萃取掉,使得所制膜表面产生微孔,即得到一种微孔尺寸为1μm,孔隙率为80%,厚度为5mm的夹芯板材的芯板材料。在上述芯板的上下两面覆上聚丙烯板材,即可制成中空夹芯板材。制成夹芯板材选用两液混合硬化胶,用量为300g/m2。上述的对实施例的描述是为便于该技术领域的普通技术人员能理解和应用本发明。熟悉本领域技术的人员显然可以容易地对这些实施例做出各种修改,并把在此说明的一般原理应用到其他实施例中而不必经过创造性的劳动。因此,本发明不限于这里的实施例,本领域技术人员根据本发明的揭示,不脱离本发明范畴所做出的改进和修改都应该在本发明的保护范围之内。