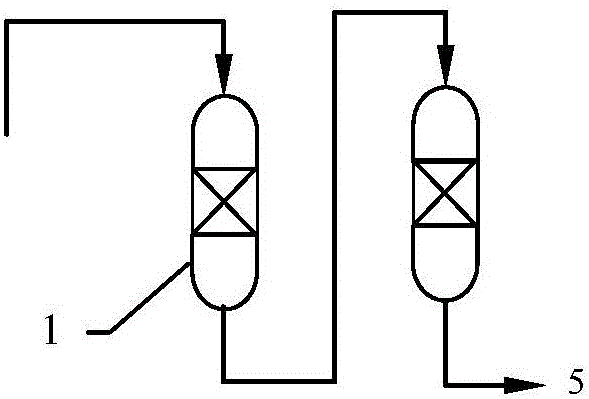
本发明涉及一种适用于C5、C9石油树脂,环戊二烯树脂或共聚石油树脂加氢过程脱硫、脱氯的工业方法。该方法适用于一段或两段石油树脂加氢工艺,采用高温固体脱硫剂、脱氯剂,能够有效地脱除加氢反应过程产生的硫化氢(H2S)和氯化氢(HCl),消除了对后续设备和仪表的腐蚀,避免了采用碱洗脱硫、脱氯工艺导致的高低压汽液分离系统温度下降,能够在高低压汽液分离系统回收更多的溶剂,取消了溶剂和废碱液油水分离过程和溶剂脱水精制过程,简化了加氢石油树脂生产工艺,降低了装置生产能耗和建设投资;由于采用固体脱硫、脱氯剂进行脱硫、脱氯,装置不再产生、排出废碱液等液体废物,只需周期性的更换失效的脱硫、脱氯剂,具有排出固体废物少、处理容易、对环境污染小的特点。
背景技术:
:在以石油馏分裂解生产乙烯、丙稀过程中,会副产大量的裂解C5、C9馏分,可以作为生产石油树脂的原料,采用热聚合或催化聚合方法,经过预处理、聚合、脱溶剂、结片成型等工序(催化聚合还包括脱催化剂、中和、水洗等工序),生产各种不同规格的C5、C9石油树脂或共聚石油树脂(分子量一般在500-2000左右),称为未加氢石油树脂。由于采用的原料与聚合工艺不同,未加氢石油树脂呈浅黄色至红褐色多种色泽,普遍存在颜色深、气味臭、热氧稳定性低、粘结力和相容性较差等缺陷,影响了其在高端领域的应用,主要原因是聚合物链中不饱和双键含量高,以及在聚合过程中形成的不明有色基团。加氢石油树脂就是针对未加氢石油树脂的以上不足,采用催化加氢技术,在催化剂的作用下将由裂解C5、C9聚合得到的未加氢石油树脂中的不饱和成分和有色基团加氢,减少双键含量,并脱除在聚合过程中残留的氯和硫后得到的无色或浅色石油树脂。与未加氢石油树脂相比,加氢石油树脂进一步改善了石油树脂的色度、粘合性、耐候性、光热稳定性和相容性等性能,大大拓宽了石油树脂的应用领域,可广泛用于涂料、油漆、油墨、热熔胶、胶粘剂、压敏胶等领域,尤其是卫生用品和交通涂料上。目前,加氢石油树脂的生产工艺主要有三种:浆态加氢工艺、喷淋式加氢工艺和固定床加氢工艺。浆态加氢工艺通常为间歇釜式反应,适用于较小规模的生产,存在生产工艺繁琐,催化剂损失大等弊端;喷淋式加氢工艺由日本荒川化学公司实现了工业化,但也存在设计要求高、设备投资大、不易控制等缺点:目前石油树脂生产装置主要采用固定床加氢工艺,该工艺适用于大规模的加氢石油树脂生产。石油树脂的固定床加氢工艺分为一段加氢和两段加氢,一段加氢工艺特点在于在不饱和键加氢、有色基团以及氯和硫的脱除在加氢反应器中一步完成;石油树脂两段加氢工艺一般在一段和二段加氢反应器中装填不同的加氢催化加,在第一段反应器中进行不饱和键的初步加氢并进行有色基团以及氯和硫的脱除,在第二段加氢反应器中对石油树脂进行加氢精制。加氢产物经汽液分离,脱除溶剂后进行造粒得到加氢石油树脂产品。由于石油树脂聚合原料中通常含有硫、氯等杂质,而且石油树脂催化聚合过程中通常采用无水AlCl3为催化剂,尽管对聚合过程产物进行碱洗中和、水洗等后处理过程,但加氢原料树脂中残存的氯含量仍然在500~5000ppm,会明显拟制催化剂的加氢活性,同时转化为硫化氢(H2S)和氯化氢(HCl),对后续设备和仪表造成严重腐蚀。目前用于石油树脂加氢过程脱硫、脱氯的方法主要是碱洗法,例如ZL201010266085.X(一种加氢石油树脂的工业制造方法)公开的合并碱洗工艺,工艺流程见图1,该方法应用在两段固定床加氢工艺中,树脂、溶剂与循环氢气混合加热后进入一段加氢反应器1进行加氢反应,反应后物料进入汽液分离罐2进行汽液分离,分离后的液相和加热后的补充氢气、溶剂混合后进入二段加氢反应器3进行二段加氢反应,二段加氢反应器3反应产物和汽液分离罐2分离出的汽相进入中和反应器17,在泵入碱液的情况下进行碱液中和脱除反应产生的硫化氢和氯化氢,中和反应器17排出的含有碱液的油水混合物进入一级高压汽液分离罐5、汽液分离后气化的溶剂、水蒸气和溶解氢冷凝后进入二级高压汽液分离罐;未气化的液相进入一级低压汽液分离罐6进行汽液分离,气化的溶剂、水蒸气和溶解氢冷凝后进入二级低压汽液分离罐14;未气化的液相进入常压的树脂汽液液分离罐18,物料分为汽相、液相,液相包括碱液水相和树脂有机相两部分,其中的汽相进入溶剂汽液分离罐19,溶剂汽液分离罐19中未气化的溶剂和水进入溶剂液液分离罐23,在此进行溶剂和水相静置分层,上层的粗溶剂进入分子筛脱水罐24脱水后作为循环溶剂去配料,下层的水用于树脂水洗。树脂汽液液分离罐18的液相下层为含碱水相成为废水排出,上层的有机相与来自溶剂液液分离罐23的水进入混合器21混合后进入树脂液液分离罐22,分层后下层水相用于碱液配置,上层含树脂产物的有机相进入一级降膜蒸发器8脱除部分溶剂后进入二级降膜蒸发器9在减压汽提的条件下脱除溶剂和低聚物后的熔体去造粒单元结片造粒得到合格的加氢石油树脂产品。该方法对树脂加氢深度有较高的要求,在树脂汽液液分离罐18和树脂液液分离罐22中存在油水两相物料乳化的可能,对油水两相液体物料的分离方法和设备、脱溶剂系统的设计和操作有更高的要求,而且溶剂液液分离罐23油水分离出的循环粗溶剂中会混入水份,需要对循环粗溶剂进行全部或部分脱水精制处理,使得石油树脂加氢工艺相对复杂。技术实现要素:本发明的目的在于提供了一种适用于C5、C9石油树脂,环戊二烯树脂或共聚石油树脂加氢过程脱硫、脱氯的工业方法。本发明克服了现有技术的缺点,进一步简化了石油树脂加氢装置的工艺,节省了投资和操作费用,保证了装置的稳定运行。本发明的技术方案如下:一种石油树脂加氢过程脱硫、脱氯的工业方法,根据一段和两段不同的工艺,分别说明如下:在石油树脂一段加氢方法中,树脂、溶剂与循环氢气混合加热后进入加氢反应器进行加氢反应,反应后的物料进入装有固体脱硫剂、脱氯剂的高压脱硫、脱氯反应罐组脱除加氢反应过程产生的硫化氢和氯化氢,脱除硫和氯的物料进入一级高压汽液分离罐分离出气化的溶剂和溶解氢,分离的气化的溶剂和溶解氢冷凝后进行氢气回收和溶剂回收,液相进入一级低压汽液分离罐,在低压下分离出气化的溶剂和溶解氢后进入一级降膜蒸发器和二级降膜蒸发器脱除溶剂和低聚物后的熔体经造粒工艺后得到加氢石油树脂产品;在石油树脂两段加氢方法中,树脂、溶剂与循环氢气混合加热后进入一段加氢反应器进行加氢反应,反应后的物料进入汽液分离罐进行汽液分离,分离后的液相物料与经加热后的补充溶剂和氢气混合后进入二段加氢反应器进行加氢反应,出自二段加氢反应器的物料和一段加氢反应器后汽液分离罐分离的汽相进入装有固体脱硫剂、脱氯剂的高压脱硫、脱氯反应罐组脱除加氢反应过程产生的硫化氢和氯化氢,脱除硫和氯的物料进入一级高压汽液分离罐,以后步骤同一段加氢脱硫脱氯方法相同;所述高压压力为4~15MPa,低压压力为0.4~4MPa。当采用只对汽相物料脱硫、脱氯的方法,树脂、溶剂与循环氢气混合加热后进入一段加氢反应器进行加氢反应,反应后的物料进入汽液分离罐进行汽液分离,分离后的液相物料与经加热后的补充溶剂和氢气混合后进入二段加氢反应器进行加氢反应,出自二段加氢反应器的汽液混合物料进入一级高压汽液分离罐进行汽液分离,分离的汽相与一段加氢反应器后汽液分离罐分离的汽相一并进入高压脱硫、脱氯反应罐组,脱除加氢反应过程产生的硫化氢和氯化氢后进入二级高压汽液分离罐进行溶剂和氢气的回收;一级高压汽液分离罐分离的液相进入一级低压汽液分离罐进行汽液分离,分离的汽相进入低压脱硫、脱氯反应罐组脱硫、脱氯后去往二级低压汽液分离罐;一级低压汽液分离罐分离的液相进入一级降膜蒸发器,分离的汽相进入常压脱硫、脱氯反应罐组脱硫、脱氯后后去往循环溶剂罐;一级降膜蒸发器脱除部分溶剂的树脂溶液进入二级降膜蒸发器,在二级降膜蒸发器中脱除的溶剂和低聚物进入减压脱硫、脱氯反应罐组去往低聚物分离塔,降膜蒸发器排出的树脂熔体经造粒工艺后得到加氢石油树脂产品。所述加氢的原料石油树脂为由裂解C5、C9馏分聚合得到的C5、C9石油树脂,环戊二烯树脂或共聚石油树脂。所述加氢溶剂包括饱和烷烃类、饱和多烷基环烷烃、芳烃类溶剂,如环己烷、烷基环己烷、庚烷、辛烷、壬烷、癸烷、加氢的芳烃抽余油、加氢裂化的饱和馏分油、以及重芳烃及重芳烃加氢得到的多烷基环己烷。本发明的石油树脂加氢过程脱硫、脱氯的工业装置,根据一段和两段不同的工艺,分别说明如下:在石油树脂一段加氢方法的装置中,加氢反应器出口与高压脱硫、脱氯反应罐组进口连接,高压脱硫、脱氯反应罐组出口连接一级高压汽液分离罐;在石油树脂两段加氢工艺装置中,一段加氢反应器出口连接汽液分离罐进口,汽液分离罐底部液相出口连接二段加氢反应器进口,二段加氢反应器出口管线与汽液分离罐汽相出口管线合并后接到高压脱硫、脱氯反应罐组进口,高压脱硫、脱氯反应罐组出口连接一级高压汽液分离罐;在石油树脂两段加氢方法的装置中,只对汽相物料进行脱硫脱氯时,一段加氢反应器出口连接汽液分离罐进口,汽液分离罐底部液相出口连接二段加氢反应器进口,二段加氢反应器出口连接一级高压汽液分离罐,一级高压汽液分离罐顶部汽相出口管线与汽液分离罐汽相出口管线合并后接到高压脱硫、脱氯反应罐组进口,高压脱硫、脱氯反应罐组出口连接高分冷凝器,一级高压汽液分离罐底部液相出口连接一级低压汽液分离罐,一级低压汽液分离罐顶部汽相出口连接低压脱硫、脱氯反应罐组,低压脱硫、脱氯反应罐组出口与低分冷凝器相连,一级低压汽液分离罐底部液相出口连接加热器,加热器另一物料接口连接一级降膜蒸发器物料进口,一级降膜蒸发器顶部汽相出口与常压脱硫、脱氯反应罐组进口相连,压脱硫、脱氯反应罐组出口连接一级降膜冷凝器,一级降膜蒸发器底部液相出口与二级降膜蒸发器进口相连,二级降膜蒸发器底部熔体出口连接造粒单元设备,二级降膜蒸发器顶部汽相出口连接减压脱硫、脱氯反应罐组,脱硫、脱氯反应罐组出口与低聚物分离塔物料进口相连。装置中的脱硫、脱氯反应罐组适用与石油树脂一段和两段加氢装置,每个脱硫、脱氯反应罐组由两罐、三罐或四罐组成。当原料树脂仅含硫时,只需配备脱硫反应罐组;当原料树脂仅含氯时,只需配备脱氯反应罐组;当原料树脂同时含硫和氯时,脱硫、脱氯反应罐组使用脱硫剂、脱氯剂混装罐时,采用双罐、三罐操作;脱硫、脱氯反应罐组使用单独的脱硫罐和脱氯罐时;需配备两个脱硫罐和两个脱氯罐,进行四罐操作。所述的脱氯反应罐分别配置在一级高压分离罐、一级低压分离罐、一级降膜蒸发器和二级减压汽提降膜蒸发器的排汽管线,实现汽相脱硫、脱氯。具体说明如下:该方法适用于一段和两段固定床式石油树脂加氢工艺中,该工艺采用高温固体脱硫剂、脱氯剂的脱氯(硫)罐,有效的脱除加氢反应过程产生的硫化氢(H2S)和氯化氢(HCl),消除了对后续设备和仪表的腐蚀,特别是高硫、氯含量的石油树脂的加氢过程,固体脱硫剂、脱氯剂可采用市售的各种高温脱氯、脱硫剂。由于取消了碱液中和和水洗步骤,避免了油水两相物料乳化的现象,同时避免了采用碱洗脱硫、脱氯工艺导致的高低压汽液分离系统温度下降,能够在高低压汽液分离系统回收更多的溶剂。因为取消了碱洗、水洗工艺,系统中不再引进水,溶剂脱水精制工序也将取消,简化了加氢石油树脂生产工艺,降低了装置建设投资;由于采用固体脱硫、脱氯剂进行脱硫、脱氯,装置不再产生、排出废碱液等液体废物,具有排出固体废物少、处理容易、对环境污染小的特点。一段石油树脂加氢汽液相物料脱硫、脱氯工艺见图2,其过程为树脂、溶剂与循环氢气混合加热后进入加氢反应器1进行加氢反应,反应后的含硫化氢(H2S)和氯化氢(HCl)的汽液混合物直接进入装有固体脱硫剂、脱氯剂的高压脱硫、脱氯反应罐组4-1脱除加氢反应过程产生的硫化氢(H2S)和氯化氢(HCl),脱除硫和氯的物料进入一级高压汽液分离罐5,分离出气化的溶剂和溶解氢后进行溶剂和氢气的回收,液相进入一级低压汽液分离罐6,在低压下分离出气化的溶剂和溶解氢后进入一级降膜蒸发器8和二级降膜蒸发器9脱除溶剂和低聚物后的熔体经造粒工艺后得到加氢石油树脂产品。两段石油树脂加氢汽液相物料脱硫、脱氯工艺见图3,其过程为树脂、溶剂与循环氢气混合加热后进入一段加氢反应器1进行加氢反应,反应后的汽液混合物直接进入汽液分离罐2进行汽液分离,分离后的液相物料与经加热后的补充溶剂和氢气混合后进入二段加氢反应器3进行加氢反应,出自二段加氢反应器3的含硫化氢(H2S)和氯化氢(HCl)的汽液混合物和汽液分离罐2分离的含硫化氢(H2S)和氯化氢(HCl)的汽相一起进入装有固体脱硫剂、脱氯剂的高压脱硫、脱氯反应罐组4-1,完成气液两相物料的脱硫、脱氯过程,脱除硫和氯的物料进入一级高压汽液分离罐5,以后步骤同一段加氢脱硫脱氯工艺相同。在此过程中一段汽相和二段物料合并后脱氯和脱硫过程一步完成,一段反应器后含硫、氯的汽相和二段反应器汽液混合相合并后进入脱硫脱氯反应罐,脱硫脱氯反应罐操作压力与反应压力相当两段石油树脂加氢汽相物料脱硫、脱氯工艺见图4,其过程为树脂、溶剂与循环氢气混合加热后进入一段加氢反应器1进行加氢反应,反应后的汽液混合物进入汽液分离罐2进行汽液分离,分离后的液相物料与经加热后的补充溶剂和氢气混合后进入二段加氢反应器3进行加氢反应,出自二段加氢反应器的的含硫化氢(H2S)和氯化氢(HCl)的汽液混合物进入一级高压汽液分离罐5进行汽液分离,分离的含硫化氢(H2S)和氯化氢(HCl)的汽相与一段加氢反应器1后汽液分离罐2分离的含硫化氢(H2S)和氯化氢(HCl)的汽相一并进入高压脱硫、脱氯反应罐组4-1脱除加氢反应过程产生的硫化氢(H2S)和氯化氢(HCl)后进入二级高压汽液分离罐13进行循环氢气分离和溶剂回收;一级高压汽液分离罐5分离的液相进入一级低压汽液分离罐6进行汽液分离,分离的含硫化氢(H2S)和氯化氢(HCl)的汽相进入低压脱硫、脱氯反应罐组4-2脱硫、脱氯后去往二级低压汽液分离罐14进行氢气回收和溶剂回收;一级低压汽液分离罐6分离的液相进入一级降膜蒸发器8,分离的汽相进入常压脱硫、脱氯反应罐组4-3后去往循环溶剂罐15用于作为循环溶剂去配料;一级降膜蒸发器8脱除部分溶剂的树脂溶液进入二级降膜蒸发器9,在减压汽提条件下脱除的溶剂和低聚物进入减压脱硫、脱氯反应罐组4-4去往低聚物分离塔16,降膜蒸发器排出的树脂熔体经造粒工艺后得到加氢石油树脂产品。在此过程中作为加氢产物的液相石油树脂物料不进入脱硫、脱氯反应罐组,完全避免了树脂降解等副反应的发生。在此工艺中由脱硫、脱氯反应罐组取代原有工艺中的中和反应器,系统中将不再引进水和碱液,原有的树脂汽液液分离罐18、树脂液液分离罐22、混合器21、分子筛脱水罐24设备将取消,原有剂液液分离罐由于只存在溶剂改为循环溶剂罐15,由二级高压汽液分离罐13、二级低压汽液分离罐14、一级降膜蒸发器8、低聚物分离塔16回收的溶剂回到循环溶剂罐15,作为循环溶剂去配料。对于脱硫、脱氯反应罐组的配置,为保证装置安全运行,正常工况下每组脱硫、脱氯反应罐组必须有两个处于运行状态,主要采用以下配置:当加氢原料为碳五石油树脂时原料氯含量高,不含硫,只用配备脱氯反应罐,当加氢原料为热聚的碳九石油树脂时原料硫含量高,不含氯,只用配备脱硫反应罐。每组脱硫反应罐或脱氯反应罐的配置采用双罐或三罐操作。双罐操作时,正常时为串联运行,需要更换脱硫、脱氯剂时,一罐运行,另一罐切出进行更换脱氯或脱硫剂,更换完成后恢复串联运行;三罐操作时,两罐串联运行,一罐备用,需要更换脱硫、脱氯剂时备用罐投入使用。当加氢原料为冷聚的碳九石油树脂或C5/C9共聚石油树脂时,原料同时含硫和氯,每组罐同时要脱硫脱氯。采用双罐、三罐、四罐操作,其中采用双罐、三罐时,每个罐内分别混装或分层装填脱氯、脱硫剂;采用四罐操作时,两个脱氯反应罐装填脱氯剂,另两个脱硫罐装填脱硫剂。双罐操作时,正常时为串联运行,需要更换脱硫、脱氯剂时,一罐运行,另一罐切出进行更换脱氯和脱硫剂,更换完成后恢复串联运行;三罐操作时,两罐串联运行,一罐备用,需要更换脱硫、脱氯剂时,备用罐投入串联运行,需要更换的罐切出,更换完成后备用;四罐操作时,四罐串联运行,当某一罐需要换剂时,该罐切出,其余三罐串联运行,更换完成后恢复四罐串联运行。每个脱硫、脱氯反应罐组采用串联操作,两罐串联操作说明见图5,通过调节阀门开关实现脱硫、脱氯反应罐A26和脱硫、脱氯反应罐B27串联操作及切换。当脱硫脱氯反应罐A进口阀28、脱硫脱氯反应罐A到脱硫脱氯反应罐B串联控制阀31和脱硫、脱氯反应罐B出口阀33开启其他三个阀门关闭时,物料先经过脱硫脱氯反应罐A再经过脱硫脱氯反应罐B完成脱硫脱氯,实现从脱硫脱氯反应罐A到脱硫脱氯反应罐B的串联操作。脱硫脱氯反应罐A内脱硫剂、脱氯剂需要更换时,开启脱硫脱氯反应罐B进口阀29出口阀33,其余阀门关闭,这时物料只经过脱硫脱氯反应罐B,可以切出脱硫脱氯反应罐A对脱硫脱氯反应罐A内脱硫剂、脱氯剂进行更换,更换结束后脱硫脱氯反应罐B进口阀29、脱硫脱氯反应罐B到脱硫脱氯反应罐A串联控制阀30、脱硫脱氯反应罐A出口阀32开启,实现从脱硫脱氯反应罐B到脱硫脱氯反应罐A的串联操作。该方法适用各种烃类加氢溶剂体系,包括饱和烷烃类、饱和多烷基环烷烃、芳烃类溶剂等,如环己烷、烷基环己烷、庚烷、辛烷、壬烷、癸烷、加氢的芳烃抽余油、加氢裂化的饱和馏分油、以及重芳烃及重芳烃加氢得到的多烷基环己烷等。特别指出的是,该方法同样适用于汽相脱硫、脱氯,脱氯反应罐可以分别配置在一级高压分离罐、一级低压分离罐、一级降膜蒸发器(常压脱溶剂罐)和二级减压汽提降膜蒸发器的排汽管线,实现汽相脱硫、脱氯。附图说明图1:石油树脂加氢汽液合并碱洗工艺示意图;图2:一段石油树脂加氢汽液相物料脱硫、脱氯示意图;图3:两段石油树脂加氢汽液相物料脱硫、脱氯示意图;图4:两段石油树脂加氢汽相物料脱硫、脱氯示意图;图5脱硫、脱氯反应罐串联使用示意说明;其中:1一段加氢反应器、2汽液分离罐、3二段加氢反应器、4-1高压脱硫、脱氯反应罐组4-2低压脱硫、脱氯反应罐组、4-3常压脱硫、脱氯反应罐组、4-4减压脱硫、脱氯反应罐组、5一级高压汽液分离罐、6一级低压汽液分离罐、7加热器、8一级降膜蒸发器(常压脱溶剂罐)、9二级降膜蒸发器(减压汽提)、10高分冷凝器、11低分冷凝器、12一级降膜蒸发器冷凝器13二级高压汽液分离罐14二级低压汽液分离罐15循环溶剂罐16低聚物分离塔17中和反应器18树脂汽液液分离罐19溶剂汽液分离罐20减压汽液分离罐21混合器22树脂液液分离罐23溶剂液液分离罐24分子筛脱水罐25真空机组26脱硫、脱氯反应罐A27脱硫、脱氯反应罐B28脱硫、脱氯反应罐A进口阀29脱硫、脱氯反应罐B进口阀30脱硫、脱氯反应罐B到脱硫、脱氯反应罐A串联控制阀31脱硫、脱氯反应罐A到脱硫、脱氯反应罐B串联控制阀32脱硫、脱氯反应罐A出口阀33脱硫、脱氯反应罐B出口阀。具体实施方式本实例按照附图工艺4所示意的流程进行加氢试验、采用两段石油树脂加氢汽相物料脱硫、脱氯工艺路线,一段加氢反应器1出口连接汽液分离罐2进口,汽液分离罐2底部液相出口连接二段加氢反应器3进口,二段加氢反应器3出口连接一级高压汽液分离罐5,一级高压汽液分离罐5顶部汽相出口管线与汽液分离罐2汽相出口管线合并后接到高压脱硫、脱氯反应罐组4-1进口,高压脱硫、脱氯反应罐组4-1出口连接高分冷凝器10,一级高压汽液分离罐5底部液相出口连接一级低压汽液分离罐6,一级低压汽液分离罐6顶部汽相出口连接低压脱硫、脱氯反应罐组4-2,低压脱硫、脱氯反应罐组4-2出口与低分冷凝器11相连,一级低压汽液分离罐6底部液相出口连接加热器7,加热器7另一物料接口连接一级降膜蒸发器8物料进口,一级降膜蒸发器8顶部汽相出口与常压脱硫、脱氯反应罐组4-3进口相连,压脱硫、脱氯反应罐组4-3出口连接一级降膜冷凝器12,一级降膜蒸发器8底部液相出口与二级降膜蒸发器9进口相连,二级降膜蒸发器9底部熔体出口连接造粒单元设备,二级降膜蒸发器9顶部汽相出口连接减压脱硫、脱氯反应罐组4-4,脱硫、脱氯反应罐组4-4出口与低聚物分离塔16物料进口相连。实验原料为较低氯含量的C5石油树脂,一、二段加氢反应器分别装填自制的负载型Pd-Al2O3加氢催化剂,脱硫、脱氯反应罐装填惰性瓷球和市售的高温脱氯、脱硫剂,加氢溶剂为环己烷,稳定剂为脱氧剂1010脱溶剂过程采用常压、真空两级脱溶剂过程,回收溶剂循环使用。工艺条件见表1,实验结果见表3。表1工艺条件过程工艺条件一段加氢反应进料浓度:20%,压力:8.0MPa,温度:250℃,体积空速:4.0l/hr,氢油比:200V/V二段加氢反应进料浓度:20%,压力:8.0MPa,温度:250℃,体积空速:4.0l/hr,氢油比:200V/V脱氯、脱硫罐脱氯反应罐、两罐操作低压氢气回收压力:1.2MPa稳定剂注入加氢石油树脂中稳定剂含量控制在20ppm常压脱溶剂温度:160℃减压降膜脱溶剂真空度:-0.06MPa,温度:220℃,汽提蒸汽量:10Kg/100Kg石油树脂实施例2本实施例为两段加氢反应工艺,按照附图工艺3所示意的流程进行汽液相物料脱硫、脱氯工艺路线:自一段石油树脂加氢反应器1排出的含硫化氢(H2S)和氯化氢(HCl)的汽液混合物直接进入气液分离罐2,气液分离罐2含硫化氢(H2S)和氯化氢(HCl)的汽相与从二段加氢反应器排出的含硫化氢(H2S)和氯化氢(HCl)的汽液混合物一起进入脱硫、脱氯反应罐组4-1,完成气液两相物料的脱硫、脱氯过程,设备连接方法为一段加氢反应器1出口连接汽液分离罐2进口,汽液分离罐2底部液相出口连接二段加氢反应器3进口,二段加氢反应器3出口管线与汽液分离罐2汽相出口管线合并后接到高压脱硫、脱氯反应罐组4-1进口,高压脱硫、脱氯反应罐组4-1出口连接一级高压汽液分离罐5.其它条件能与实例1相同。工艺条件见表2,实验结果见表4。表2工艺条件过程工艺条件一段加氢反应进料浓度:20%,压力:8.0MPa,温度:250℃,体积空速:4.0l/hr,氢油比:200V/V二段加氢反应进料浓度:20%,压力:8.0MPa,温度:250℃,体积空速:4.0l/hr,氢油比:200V/V脱氯、脱硫罐脱氯反应罐、两罐操作低压氢气回收压力:1.2MPa稳定剂注入加氢石油树脂中稳定剂含量控制在20ppm常压脱溶剂温度:160℃减压降膜脱溶剂真空度:-0.06MPa,温度:220℃,汽提蒸汽量:10Kg/100Kg石油树脂对比例2本对比例为两段加氢反应工艺,按照附图工艺1所示意的流程进行汽液相物料合并碱洗脱硫、脱氯工艺路线,中和碱液为5%氢氧化钠溶液,实验结果见表4。实施例3:本对比例为一段加氢反应工艺,按照附图工艺2所示意的流程进行汽液相物料脱硫、脱氯工艺路线:加氢反应器1出口与高压脱硫、脱氯反应罐组4-1进口连接,高压脱硫、脱氯反应罐组4-1出口连接一级高压汽液分离罐5;实验原料为较低氯含量的C5石油树脂,加氢反应器装填自制的负载型Pd-Al2O3加氢催化剂,自一段石油树脂加氢反应器1排出的含硫化氢(H2S)和氯化氢(HCl)的汽液混合物直接进入脱硫、脱氯反应罐组4-1,完成气液两相物料的脱硫、脱氯过程,其它条件与实例1相同。工艺条件见表3,实验结果见表4。表3工艺条件过程工艺条件加氢反应进料浓度:20%,压力:8.0MPa,温度:250℃,体积空速:2.0l/hr,氢油比:200V/V脱氯、脱硫罐脱氯反应罐、两罐操作低压氢气回收压力:1.2MPa稳定剂注入加氢石油树脂中稳定剂含量控制在20ppm常压脱溶剂温度:160℃减压降膜脱溶剂真空度:-0.06MPa,温度:220℃,汽提蒸汽量:10Kg/100Kg石油树脂实施例4:本实例实验加氢溶剂为甲基环己烷,其它与实例1相同,实验结果见表4。实施例5:本实例实验原料为高氯含量的C5石油树脂,采用脱氯反应罐、三罐操作,其它与实例1相同,实验结果见表4。实施例6:本实例按照附图4所示的示意流程进行加氢试验,实验原料为催化聚合方法生产的C9石油树脂,常压脱溶剂温度提高到200℃,减压降膜脱溶剂提高到250℃,溶剂为三甲基环己烷,采用脱硫剂脱氯剂混装罐三罐操作,其它与实例1相同。实验结果见表4。实施例7:本实例实验原料为热聚合方法生产的C9石油树脂,采用脱硫罐两罐操,作其它与实例1相同,实验结果见表4。实施例8:本实例按照附图4所示的示意流程进行加氢试验,实验原料为催化聚合方法生产的C5/C9共聚石油树脂,常压脱溶剂温度提高到180℃,减压降膜脱溶剂提高到230℃,溶剂为三甲基环己烷,采用两个脱硫反应罐、两个脱氯反应罐四罐操作,其它与实例1相同。实验结果见表4。表4实验结果工艺过程的工艺指标及计算方法:溴价:gBr/100g加氢石油树脂的测试仪器及方法(执行标准)色值:美国HunterLabColourQuestEX色度分析仪,ASTME313溴价:美国METTLERTOLEDOT50型自动电位滴定仪,ASTMD1159—98软化点:国产SYD—2806F型软化点测定仪,环球法GB/T12007.6—1989氯含量:国产RPA—200A微库仑滴定仪,石科院RIPP64结论从表4中数据可以得出以下结论:在石油树脂加氢过程中采用本方法能有效脱氯、脱硫,所制得的加氢石油树脂具有低溴价,浅颜色,低氯、硫含量的特点。当前第1页1 2 3