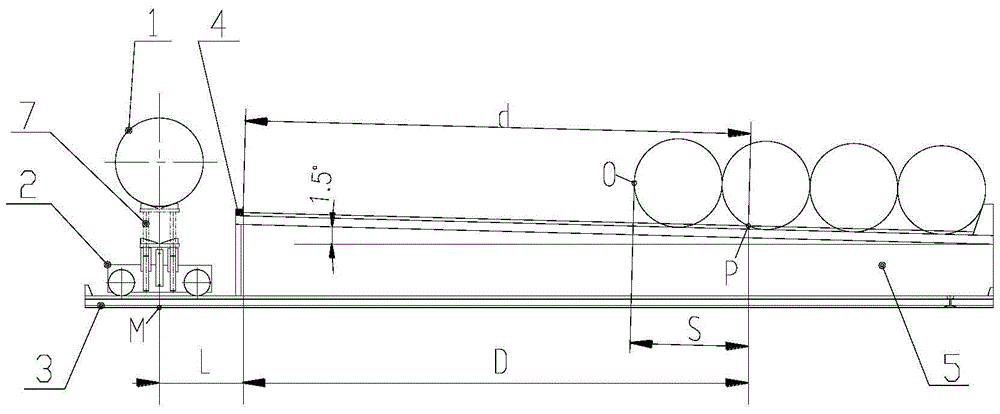
本发明涉及直缝埋弧焊管生产领域,尤其涉及一种直缝埋弧焊管出料控制方法及出料装置。
背景技术:直缝埋弧焊管采用JCOE钢管成型,一条焊缝,埋弧焊接工艺,规格范围从325mm~1626mm。直缝埋弧焊管的生产工艺灵活,可生产范围内的任何规格与壁厚。虽然生产效率较高频直缝焊钢管、螺旋焊钢管要低,但其最大优势就在于可以生产高频钢管、螺旋钢管、甚至无缝钢管都不能生产的规格型号。近年来,直缝埋弧焊管生产线钢管产品趋于大管径化、厚壁、高钢级,钢管最大长度也由原来的12.5m增加到18.4m。对于传统制管生产线采用翻管器加斜台架的出料方式,已经无法适应生产需要,主要由于钢管重量重,斜台架倾角小时,钢管滚动不到位,影响排管效果,斜台架上一次储存的钢管数量较少,增加了来回倒料的工时,降低了生产效率;如果增大斜台架倾角,钢管在滚动时冲击力大,容易互相碰撞造成损伤。
技术实现要素:本发明提供了一种直缝埋弧焊管出料控制方法,能够适应不同管径、不同管长的钢管出料,通过激光测距传感器测定已排钢管距离并计算出后续排管的安全距离,自动控制横移车在最佳位置排放钢管;钢管排管效果好,滚动时冲击力小,生产过程安全可靠,一次存储钢管多,横移车移动动作准确,生产效率高;本发明同时提供了用于实现本方法的出料装置。为了达到上述目的,本发明采用以下技术方案实现:一种直缝埋弧焊管出料控制方法,包括如下步骤:1)在钢管出料段辊道一侧设置1.5°斜台架和横移车导轨,1.5°斜台架顶部设置激光测距传感器,调整其激光束发射角度与1.5°斜台架上表面平行;2)横移车走行机构和激光测距传感器通过PLC控制器相连,激光测距传感器采集1.5°斜台架上最近端钢管测距点距离,将数据传送至PLC控制器;3)PLC控制器编程,计算出距钢管上激光测距点的排管安全距离,计算排管安全距离时,钢管直径默认为¢1626,即以目前所生产最大规格钢管直径进行代入计算;钢管上激光测距点至后排钢管最外端距离为S,排管安全距离为1.5S;激光测距传感器至最近端钢管上激光测距点距离为d,换算后的垂直距离为D=d·cos1.5°;横移车初始位置距激光测距传感器距离为L,则横移车需移动距离为:D+L-1.5S;4)横移车行至出料段辊道内,通过举升装置抬起钢管并回到初始位置,PLC控制器控制横移车向1.5°斜台架方向的移动距离,在距1.5°斜台架上最近端钢管安全距离处排放钢管;5)步骤2)-4)重复进行,将钢管依次排列到1.5°斜台架上,1.5°斜台架上钢管排满后转运,再重复步骤2)-4),直至钢管出料完成。用于实现一种直缝埋弧焊管出料控制方法的出料装置,包括横移车、横移车导轨、1.5°斜台架、激光测距传感器和PLC控制器,所述横移车导轨和1.5°斜台架布设在钢管出料段辊道一侧,其布设方向与钢管输送方向垂直;激光测距传感器安装在1.5°斜台架靠近横移车的其中一个台架顶部,激光测距传感器和横移车走行机构通过PLC控制器相连接,横移车上设有举升装置。所述1.5°斜台架由多个均布的平行台架组成,其布设宽度与钢管最大长度相适应;横移车导轨布设在1.5°斜台架中部。所述横移车导轨铺设长度大于辊道至台架最外侧距离,横移车可沿横移车导轨移动至辊道下方,并通过限位装置限定初始位置,初始位置设在1.5°斜台架外侧靠近辊道处。所述激光测距传感器的激光束发射角度与1.5°斜台架上表面平行。与现有技术相比,本发明的有益效果是:1)能够适应不同管径、不同管长的钢管安全快速出料,满足现有直缝埋弧焊管生产线的出料要求;2)通过激光测距传感器测定已排钢管距离并计算出后续排管的安全距离,自动控制横移车在最佳位置排放钢管;钢管紧挨着依次排列,排管效果好,1.5°斜台架一次存储钢管多;3)排管时滚动时冲击力小,生产过程安全可靠,对钢管无损伤;4)横移车移动动作由PLC控制器控制,行程准确,不必人工调整,生产效率高。附图说明图1是本发明所述装置的结构示意图。图2是本发明所述横移车移动距离计算原理示意图。图中:1.钢管2.出料段辊道3.横移车导轨4.横移车5.1.5°斜台架6.激光测距传感器7.举升装置M.横移车初始位置N.激光测距传感器安装位置P.距激光测距传感器最近端钢管上的激光测距点O.下一根要排放的钢管最外侧点具体实施方式下面结合附图对本发明的具体实施方式作进一步说明:本发明所述一种直缝埋弧焊管出料控制方法,包括如下步骤:1)在钢管出料段辊道2一侧设置1.5°斜台架5和横移车导轨3,1.5°斜台架5顶部设置激光测距传感器6,调整其激光束发射角度与1.5°斜台架5上表面平行;2)横移车4走行机构和激光测距传感器6通过PLC控制器相连,激光测距传感器6采集1.5°斜台架5上最近端钢管测距点距离P,将数据传送至PLC控制器;3)PLC控制器编程,计算出距钢管上激光测距点P的排管安全距离,计算排管安全距离时,钢管1直径默认为¢1626,即以目前所生产最大规格钢管直径进行代入计算;钢管上激光测距点P至后排钢管最外端O距离为S,排管安全距离为1.5S;激光测距传感器6至最近端钢管上激光测距点P距离为d,换算后的垂直距离为D=d·cos1.5°;横移车初始位置M距激光测距传感器N距离为L,则横移车需移动距离为:D+L-1.5S;(如图2所示)4)横移车4行至出料段辊道2内,通过举升装置7抬起钢管1并回到初始位置M,PLC控制器控制横移车4向1.5°斜台架5方向的移动距离,在距1.5°斜台架上最近端钢管安全距离处排放钢管1;5)步骤2)-4)重复进行,将钢管1依次排列到1.5°斜台架5上,1.5°斜台架5上钢管1排满后转运,再重复步骤2)-4),直至钢管1出料完成。见图1,是本发明所述装置的结构示意图。本发明所述用于实现一种直缝埋弧焊管出料控制方法的出料装置,包括横移车4、横移车导轨3、1.5°斜台架5、激光测距传感器6和PLC控制器,所述横移车导轨3和1.5°斜台架5布设在钢管出料段辊道2一侧,其布设方向与钢管1输送方向垂直;激光测距传感器6安装在1.5°斜台架5靠近横移车4的其中一个台架顶部,激光测距传感器6和横移车4走行机构通过PLC控制器相连接,横移车4上设有举升装置7。所述1.5°斜台架5由多个均布的平行台架组成,其布设宽度与钢管1最大长度相适应;横移车导轨3布设在1.5°斜台架5中部。所述横移车导轨3铺设长度大于辊道2至台架5最外侧距离,横移车4可沿横移车导轨3移动至辊道2下方,并通过限位装置限定初始位置M,初始位置M设在1.5°斜台架5外侧靠近辊道2处。所述激光测距传感器6的激光束发射角度与1.5°斜台架5上表面平行。以下实施例在以本发明技术方案为前提下进行实施,给出了详细的实施方式和具体的操作过程,但本发明的保护范围不限于下述的实施例。下述实施例中所用方法如无特别说明均为常规方法。【实施例】如图1所示,本实施例中,直线辊道2用于纵向输送钢管1;横移车4用于钢管1的横向输送;1.5°斜台架5固定在地面基础上,用于排列储存钢管1;激光测距传感器6为长距离激光测距传感器,用于检测钢管1的位置,并将检测的数据传送给PLC控制器。钢管1整个出料过程为:直线辊道2将车间生产合格后的钢管1输送到横移车接料工位;横移车4通过PLC控制器程序进行控制,可在导轨3上往复行走,首先移动到辊道2下方并通过举升装置7将钢管1升起实现接料,然后通过PLC控制器内的程序运算计算出横移车4运送钢管到达指定位置需要行走的距离,到达指定位置后举升装置7落下实现排料;钢管1在安全距离处依次传输到1.5°斜台架5上,钢管1沿1.5°斜台架5上表面缓慢滚动并依次排列,从而完成钢管1的安全快速出料。钢管1排放安全距离是指钢管1从横移车4下落到斜台架5上并在自身重力作用向下滚动时,既能滚动到紧挨前面排放钢管1的一侧停止,又不会因滚动速度过快造成对前面排放钢管1的冲击损伤。在经过反复实验验证后,我们得出的经验值是斜台架的最佳倾斜角度为1.5°;如设钢管上激光测距点P至后排钢管最外端O距离为S,则排放后一根钢管1的安全距离为(1~2)S,本实施例中排管安全距离取1.5S。如果想精确控制此安全距离,可根据不同规格钢管1分别在PLC控制器中编程,根据所生产钢管1型号随时调用。本实施例中,作为简化,减少编程工作量,所有有关钢管1的计算默认钢管直径为¢1626,即目前所生产最大钢管直径,因为其自重最大,满足¢1626排管要求的安全距离,其它小管径钢管也可保证不会在排放时发生干涉碰撞现象。图2中,M点为横移车初始位置,N点为激光测距传感器安装位置;P点为距激光测距传感器最近端钢管上的激光测距点,O点为下一根要排放的钢管最外侧点。则OP之间的距离为S,MN之间的距离为L,NP之间的斜向距离为d,垂直距离为D。本实施例中,激光测距传感器6安装后的激光束距1.5°斜台架5上表面中心高度为60mm,可据此计算出S的大小,也可通过在CAD中画图放样直接量取,本实施例中,S=2132mm,排管安全距离为1.5S=3198mm。本实施例中,L=1600mm,实测d=9355mm,则D=9355×cos1.5°=9352mm,横移车4需移动距离为:D+L-1.5S=7754mm。即当横移车4从初始位置M向1.5°斜台架侧移动7754mm时,横移车举升装置7落下将需要出料的钢管1放置到1.5°斜台架5上,钢管1沿1.5°斜台架5向下缓慢滚动后与前一根钢管1并列排放,完成此次钢管1出料过程。依此类推,直至完成全部出料工作。